脆性材料磨削模式与表面粗糙度
表面粗糙度
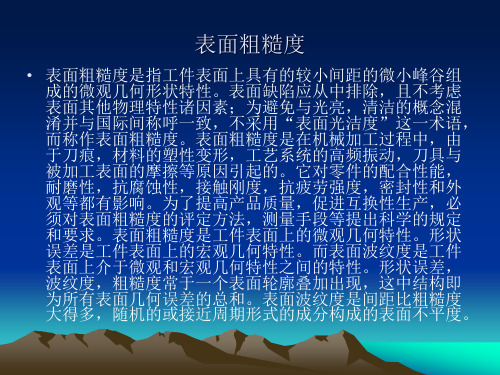
• 表面粗糙度是指工件表面上具有的较小间距的微小峰谷组 成的微观几何形状特性。表面缺陷应从中排除,且不考虑 表面其他物理特性诸因素;为避免与光亮,清洁的概念混 淆并与国际间称呼一致,不采用“表面光洁度”这一术语, 而称作表面粗糙度。表面粗糙度是在机械加工过程中,由 于刀痕,材料的塑性变形,工艺系统的高频振动,刀具与 被加工表面的摩擦等原因引起的。它对零件的配合性能, 耐磨性,抗腐蚀性,接触刚度,抗疲劳强度,密封性和外 观等都有影响。为了提高产品质量,促进互换性生产,必 须对表面粗糙度的评定方法,测量手段等提出科学的规定 和要求。表面粗糙度是工件表面上的微观几何特性。形状 误差是工件表面上的宏观几何特性。而表面波纹度是工件 表面上介于微观和宏观几何特性之间的特性。形状误差, 波纹度,粗糙度常于一个表面轮廓叠加出现,这中结构即 为所有表面几何误差的总和。表面波纹度是间距比粗糙度 大得多,随机的或接近周期形式的成分构成的表面不平度。
• 2表面粗糙度的评定参数: 表面粗糙度的常用评定参 数有5个即: • 轮廓的算术平均偏差Ra • 轮廓单元的平均线高度Rc • 轮廓的最大高度Rz • 轮廓单元的平均宽度RSm • 轮廓的支承长度率Rmr(c) • 与高度特性有关的参数为Ra,Rc,Rz,它们是基本评定参数。 • 与间距特性有关的参数为RSm. • 与形状特性有关的参数为Rmr(c)。
• • • • • • • • •
加工纹理方向的符号有下列几种: ⑴ =:纹理方向平行于注有符号的视图投影面。 ⑵ ⊥:纹理方向垂直于注有符号的视图投影面。 ⑶ X:纹理对注有符号的视图投影面是两个相交的方相。 ⑷ M:纹理呈多方向。 ⑸ C:纹理对于注有符号表面的中心来说是近似同心圆。 ⑹ R:纹理对于注有符号表面的中心来说近似放射形。 ⑺ P:纹理无方向或呈凸起的细粒状。 表面粗糙度在图样的标注示例,如图所示。
《机械制造工艺学》教案 影响加工表面粗糙度的工艺因素及其改善措施
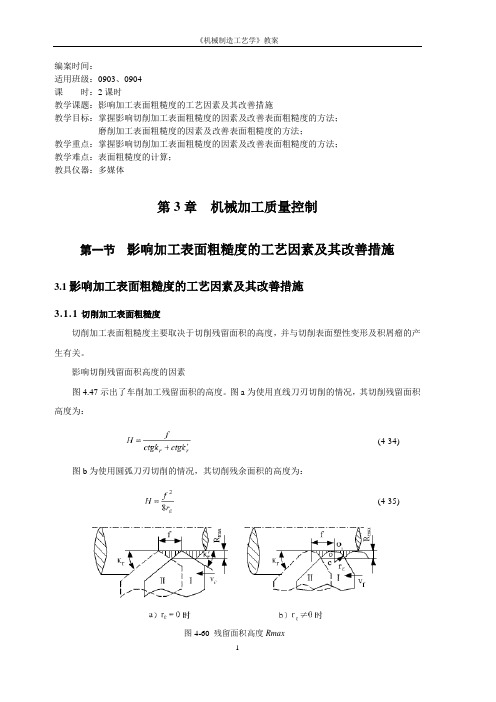
编案时间:适用班级:0903、0904课时:2课时教学课题:影响加工表面粗糙度的工艺因素及其改善措施教学目标:掌握影响切削加工表面粗糙度的因素及改善表面粗糙度的方法;磨削加工表面粗糙度的因素及改善表面粗糙度的方法;教学重点:掌握影响切削加工表面粗糙度的因素及改善表面粗糙度的方法;教学难点:表面粗糙度的计算;教具仪器:多媒体第3章机械加工质量控制第一节影响加工表面粗糙度的工艺因素及其改善措施3.1影响加工表面粗糙度的工艺因素及其改善措施3.1.1切削加工表面粗糙度切削加工表面粗糙度主要取决于切削残留面积的高度,并与切削表面塑性变形及积屑瘤的产生有关。
影响切削残留面积高度的因素图4.47示出了车削加工残留面积的高度。
图a为使用直线刀刃切削的情况,其切削残留面积高度为:(4-34) 图b为使用圆弧刀刃切削的情况,其切削残余面积的高度为:(4-35)图4-60 残留面积高度Rmax从上面两式可知,影响切削残留面积高度的因素主要包括:刀尖圆弧半径、主偏角、副偏角及进给量f等。
影响切削表面塑性变形和积屑瘤的因素图4-61示出了加工塑性材料时切削速度对表面粗糙度的影响。
切削速度v处于20~50m/min 时,表面粗糙度值最大,这是由于此时容易产生积屑瘤或鳞刺。
积屑瘤已在3.4节中介绍,鳞刺是指切削加工表面在切削速度方向产生的鱼鳞片状的毛刺。
在切削低碳钢、中碳钢、铬钢、不锈钢、铝合金、紫铜等塑性金属时,无论是车、刨、钻、插、滚齿、插齿和螺纹加工工序中都可能产生鳞刺。
积屑瘤和鳞刺均使表面粗糙度值加大。
当切削速度超100m/min时,表面粗糙度值下降,并趋于稳定。
在实际切削时,选择低速宽刀精切和高速精切,往往可以得到较小的表面粗糙度值。
图4-61 切削45钢时切削速度与粗糙度关系一般说,材料韧性越大或塑性变形趋势越大,被加工表面粗糙度就越大。
切削脆性材料比切削塑性材料容易达到表面粗糙度的要求。
对于同样的材料,金相组织越是粗大,切削加工后的表面粗糙度值也越大。
平面磨床的加工参数
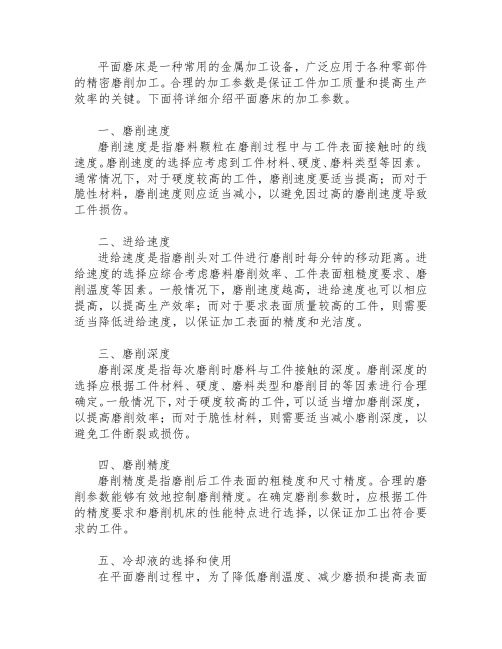
平面磨床是一种常用的金属加工设备,广泛应用于各种零部件的精密磨削加工。
合理的加工参数是保证工件加工质量和提高生产效率的关键。
下面将详细介绍平面磨床的加工参数。
一、磨削速度磨削速度是指磨料颗粒在磨削过程中与工件表面接触时的线速度。
磨削速度的选择应考虑到工件材料、硬度、磨料类型等因素。
通常情况下,对于硬度较高的工件,磨削速度要适当提高;而对于脆性材料,磨削速度则应适当减小,以避免因过高的磨削速度导致工件损伤。
二、进给速度进给速度是指磨削头对工件进行磨削时每分钟的移动距离。
进给速度的选择应综合考虑磨料磨削效率、工件表面粗糙度要求、磨削温度等因素。
一般情况下,磨削速度越高,进给速度也可以相应提高,以提高生产效率;而对于要求表面质量较高的工件,则需要适当降低进给速度,以保证加工表面的精度和光洁度。
三、磨削深度磨削深度是指每次磨削时磨料与工件接触的深度。
磨削深度的选择应根据工件材料、硬度、磨料类型和磨削目的等因素进行合理确定。
一般情况下,对于硬度较高的工件,可以适当增加磨削深度,以提高磨削效率;而对于脆性材料,则需要适当减小磨削深度,以避免工件断裂或损伤。
四、磨削精度磨削精度是指磨削后工件表面的粗糙度和尺寸精度。
合理的磨削参数能够有效地控制磨削精度。
在确定磨削参数时,应根据工件的精度要求和磨削机床的性能特点进行选择,以保证加工出符合要求的工件。
五、冷却液的选择和使用在平面磨削过程中,为了降低磨削温度、减少磨损和提高表面质量,通常需要使用冷却液。
不同的工件材料和磨削条件需要选择不同类型的冷却液,并合理控制冷却液的流量和温度,以达到最佳的磨削效果。
六、磨削轮修整磨削轮的修整对于平面磨床的加工效率和加工质量至关重要。
合理的修整参数能够保持磨削轮的良好状态,延长使用寿命,提高磨削精度和表面质量。
总之,平面磨床的加工参数对于磨削效率、加工质量和工件表面质量都有着重要的影响。
在实际加工中,操作人员需要根据具体的工件材料、形状和加工要求,合理选择和调整磨削参数,以确保磨削过程稳定、高效、精确,从而满足客户对工件加工质量的需求。
磨削工艺的优化与改进

磨削工艺的优化与改进为了适应不断发展的工业需求,磨削技术在制造业中扮演着重要的角色。
磨削是一种通过磨削轮与工件的相对运动,去除工件表面的不规则部分,达到提高工件精度和表面质量的目的。
然而,随着产品复杂性的增加和质量要求的提高,传统的磨削工艺在面对一些新型材料和高精度要求时显得效率低下、技术单一。
传统磨削过程中存在着磨削轮的磨损、加工精度降低、工作效率低下等问题,需要通过改进优化工艺来提高生产效率和产品质量。
首先,在磨削工艺方面,可以通过选择合适的磨削轮来改善加工精度。
磨削轮的选择应根据工件材料和要求来确定。
例如,在对脆性材料的磨削时,选择具有良好自磨削能力和抗冷热疲劳性能的磨削轮,可以减小工件表面的热影响区和热应力区,提高工件表面质量。
此外,为了提高磨削轮的使用寿命,可以在磨削过程中采用适当的冷却液,降低磨削轮的温升和磨削轮与工件的摩擦系数,减少磨损。
其次,磨削工装的设计也是优化磨削工艺的关键之一。
磨削工装的设计应根据工件形状和磨削要求来确定。
例如,对于复杂形状的工件,可以设计出适合的磨具夹具,减少工件因磨具变形而导致的磨削误差。
此外,磨削工装的制造材料也应选择具有良好的刚度和耐磨性能,提高工装的稳定性和寿命。
此外,在磨削参数的选择上也是需要优化的。
磨削参数的选择应根据工件材料、磨削轮材料、磨削轮粒度、工作速度等因素来确定。
过大或过小的磨削压力都会影响磨削效果,而过大的磨削速度可能会产生过高的热量,从而降低磨削质量。
因此,在确定磨削参数时,需要综合考虑各种因素,通过试验和分析来找到最佳的磨削参数组合。
值得一提的是,近年来,随着人工智能和自动化技术的发展,磨削工艺也得到了进一步优化。
通过加入自动感测装置和控制系统,可以实现对磨削过程的自动监测和控制。
例如,通过对磨削力、温度和表面质量等参数的实时监测,可以及时调整磨削参数,提高加工精度和效率。
总之,磨削工艺的优化与改进对于提高产品质量和生产效率至关重要。
机械加工表面质量的影响因素

浅谈机械加工表面质量的影响因素摘要:机械产品的使用性能和使用寿命与组成产品的零件加工质量密切相关,零件的加工质量是保证产品质量的基础。
衡量零件加工质量好坏的主要指标有:加工精度和表面粗糙度。
本文主要对机械加工表面质量的影响因素进行浅析,从而来提高机械加工表面质量。
关键词:机械加工;表面质量;影响因素工艺系统的振动对工件表面质量的影响在机械加工过程中,有时工艺系统会发生振动,即在刀具的切削刃与正在切削的工件表面之间除了名义上的切削运动之外,还会出现一种周期性的相对运动。
振动系统的各种成形运动的干扰和破坏,使被加工表面外观与振纹,增加表面粗糙度,加工表面质量的恶化。
刀具几何参数和材料对加工表面质量的影响切削刀具几何参数,边角,角,主要刀尖半径对表面粗糙度的影响最大。
在某些情况下,减少了边角,角,角半径可以减小表面粗糙度。
在相同的条件下,硬质合金刀具加工表面粗糙度值低于高速钢刀具,金刚石,立方氮化硼刀具优于硬质合金,但由於钻石、铁族材料的亲和力,它不用于处理铁基材料。
此外,耙,刀具,切割边缘本身粗糙度将直接影响加工表面粗糙度,因此,要提高刀具刃磨质量,使刀具和刀片,切割边缘粗糙度值比工件表面粗糙度值低1~2级。
切削液对加工表面质量的影响切削液的冷却和润滑,可减少切削过程界面摩擦,降低切削温度,切削层表面金属塑性变形程度下降,并抑制积屑瘤和规模生产。
在生产中,合理选择切削液对不同材料可以大大降低工件的表面粗糙度。
工件材料对加工表面质量的影响塑料材料,工具,金属挤压产生塑性变形,切削力与工件和芯片分离的撕裂作用,使表面粗糙度值增加。
工件材料的韧性,金属的塑性变形大,加工表面粗糙。
脆性材料,芯片被打破,由于粒状,断屑和左许多坑加工表面和表面粗糙。
对同一材料,较粗粒结构,更大的加工表面粗糙度。
因此,为了降低加工表面粗糙度,往往在切割的材料之前,淬火和回火或正火处理获得均匀,细晶结构,硬度高。
切削条件对工件表面质量的影响与切削条件有关的工艺因素,包括切削用量、冷却润滑情况、进给速度、切削深度等。
单颗磨粒切厚均匀化实现脆性材料延性域磨削技术
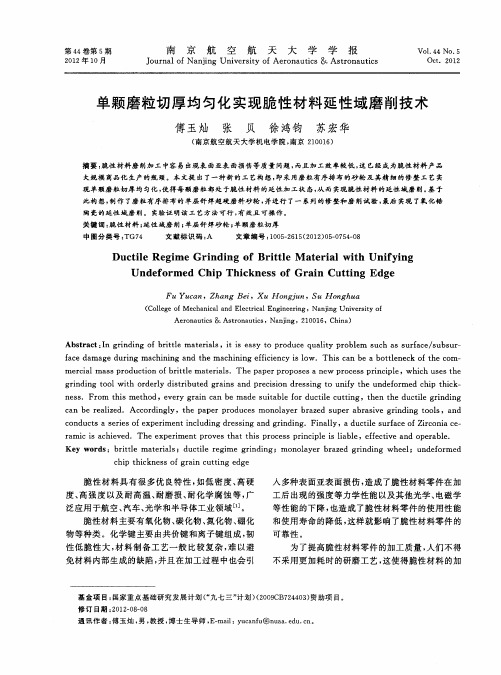
单 颗磨 粒 切 厚 均 匀 化 实 现脆 性材 料 延 性 域磨 削 技术
傅 玉 灿 张 贝 徐 鸿钧 苏 宏 华
( 京 航 空航 天 大 学 机 电学 院 , 京 2 0 1 ) 南 南 1 06
摘 要 : 性 材 料 磨 削 加 工 中容 易 出现 表 面亚 表 面 损 伤 等 质 量 问题 , 且 加 工 效 率 较低 , 已 经成 为脆 性 材 料 产 品 脆 而 这 大 规模 商 品 化 生产 的瓶 颈 。本 文提 出 了一种 新 的 工 艺构 想 , 即采 用磨 粒 有 序 排 布 的砂 轮 及 其 精 细 的修 整 工 艺 实 现 单 颗 磨 粒切 厚 均 匀化 , 得 每 颗 磨 粒 都 处 于脆 性 材 料 的 延 性 加 工 状 态 , 而 实现脆 性材 料 的延 性 域 磨 削 。 于 使 从 基 此 构 想 , 作 了磨 粒 有 序排 布 的单 层 钎 焊 超 硬 磨 料 砂 轮 , 进 行 了一 系列 的 修 整 和 磨 削 试 验 , 制 并 最后 实现 了氧 化 锆 陶瓷 的 延性 域磨 削 。 实验 证 明 该 工 艺 方 法 可行 , 效 且 可 操 作 。 有 关 键 词 : 性 材 料 ; 性 域 磨 削 ; 层 钎 焊 砂 轮 ; 颗 磨 粒切 厚 脆 延 单 单 中 图 分 类 号 : G7 T 4 文献 标 识 码 : A 文 章 编 号 :0 52 1 (0 2 0—7 40 10 —6 52 1) 50 5—8
第 4 第 5期 4卷
21 年 1 02 O月
南
京
航
空
航
天
大
学
学
报
Vo1 44 No.5 .
J u n lo ni gUnv r i fAe o a t s& Asr n u is o r a fNa j ie st o r n u i n y c to a tc
车床工件表面粗糙度的形成原因及解决措施

车床工件表面粗糙度的形成原因及解决措施表面粗糙度是机械加工中衡量加工质量的重要因素,表面粗糙度对零件和机器有着重要的意义。
但由于工件材料、切削加工方式、表面硬化等原因,造成了表面粗糙度值提高。
本文详细分析了车床工件表面粗糙度的形成原因,并提出相应的解决措施。
标签:车床工件:表面:粗糙度:原因:解决措施1.引言在实际的机械加工中,工件表面会存在许多高低不平的微小峰谷,这是因为切屑分离时塑性变形、工艺系统的振动以及刀具与已加工表面问的摩擦等因素的影响。
这些零件被加工表面上的微观几何形状误差称为表面粗糙度。
表面粗糙度对零件的耐磨性、耐腐蚀性、疲劳强度和配合性质都有很大影响。
本文详细分析了车床工件表面粗糙度的形成原因,并提出相应的解决措施,具有一定的实际意义。
2.影响工件表面粗糙度的原因2.1工件材料性能。
塑性金属材料在加工的过程中,刀具挤压金属材料,使其产生塑性变形,切屑和工件分离是由于刀具外力的挤压,表面出现撕裂现象,这严重影响表面粗糙度。
伴随着工件材料韧性的提高,在切屑过程中材料的塑性变形也就越大,加工表面粗糙度也就越差。
脆性材料在加工时,所切削形成的铁屑为颗粒状,在切屑崩碎的过程中,加工表面容易产生细小的坑点,提高表面粗糙度值。
2.2刀具切削加工。
在普通刀具在切屑过程中,切削表面势必会产生残留面积,残留面积的高度则是影响加工表面粗糙度的主要因素。
在整个加工过程中,刀具的进给量、主偏角、副偏角、圆弧半径则是造成切削残留面积的主要因素。
砂轮磨削加工过程中,砂轮上硬质颗粒断裂后形成微刃,其分布情况和外形对表面粗糙度有着直接的影响。
因为磨削加工表面是大量微刃在金属表面切削出细小的切削痕迹构成的,所形成的切削痕迹越细小、越密集则表面粗糙度就越好,相反切削痕迹粗大、分布疏散,则表面粗糙度越差。
2.3表面冷作硬化。
在普通刀具切削或砂轮磨削过程中,表面层金属由于刀具外在切削力和材料本身的塑性,使其晶格产生剪切、滑移、拉长、扭曲、破碎,宏观的表现特点则是材料表面层变硬,屈服点提高,延生率降低。
磨 工

1.3 砂 轮
1.3.1 砂轮的性能
砂轮是磨削用的切削工具,是由磨粒、结合剂和空隙构成的多孔物体,如 图所示。砂轮的性能主要由磨粒的种类和大小、结合剂的种类和砂轮的硬度来 决定。
1.磨粒 磨粒在磨削过程中担任切削工作,每一个磨粒都相当于一把刀具,以切削工件。常见
的磨粒有刚玉和碳化硅两种。其中,刚玉类磨粒适用于磨削钢料和一般刀具;碳化硅磨粒 类适用于磨削铸铁和青铜等脆性材料以及硬质合金刀具等。
1)顶尖安装 磨削轴类零件的外圆时常用前、后顶尖装夹。其安装方法与车削中顶尖
的安装方法基本相同。
2)卡盘安装 工件较长且只有一端有中心孔时应采用卡盘安装。安装方法与车床的安装方法基本 相同,如下左图所示
3)心轴安装 盘套类空心工件常用心轴安装。心轴的安装与车床的安装方法相同,不同的是磨削 用的心轴精度要求更高些,且多用锥度(锥度为1/5 000~1/7 000)心轴,如下右 图所示。
金工实习
1.1 概 述
磨工是指用磨料去除工件表面多余材料的加工方法,是零件精加工的主要方法。 磨工的尺寸等级一般可达到IT6~IT5,表面粗糙度Ra值可达到0.8~0.2 μm。
1.1.1 磨削要素
磨削要素包括主运动、圆周进给运动、纵向进给运动和横向进给运动。 1.主运动及磨削速度
磨削的主运动是砂轮的高速旋转运动。磨削速度是砂轮外圆的线速度,其计算 公式为
内圆磨床主要用于磨削内圆柱面、内圆锥面和孔内端面等。如图所示为 M2110内圆磨床。
1.2.3 平面磨床
平面磨床主要用来磨削平面。平面磨床有立轴式和卧轴式两类。其中,立轴式 平面磨床用砂轮的端面磨削平面;卧轴式平面磨床用砂轮的圆周面磨削平面。如图 所示为M7120D平面磨床
- 1、下载文档前请自行甄别文档内容的完整性,平台不提供额外的编辑、内容补充、找答案等附加服务。
- 2、"仅部分预览"的文档,不可在线预览部分如存在完整性等问题,可反馈申请退款(可完整预览的文档不适用该条件!)。
- 3、如文档侵犯您的权益,请联系客服反馈,我们会尽快为您处理(人工客服工作时间:9:00-18:30)。
Grinding Mode of Brittle Material and Surface Roughness
Meng Jianfeng Li Jianfeng Ge Peiqi
Abstract: The research status about the grinding modes and surface roughness of brittle materials at home and abroad are summarized. The reference for gaining better products and operating precise and ultraprecise grinding brittle materials is provided. Keywords: brittle material, grinding mode, surface roughness
hc = 0 15 ( E Kc 2 )( ) H H ( 1)
通过对光学 玻璃 ( NbF1) 进行超精密
磨削 ( 磨削时砂轮的线速度 v s = 1200m/ min, 工件速 度 vw = 0 5m/ min, 磨 削深 度 a p = 1 m ) 发 现: 当用 W40 型金刚石砂轮磨削时磨削模式为断裂模式, 磨 削后工件表面有大量的磨削条纹 , 表面不透明, 表面 粗糙度 R a 为 5 36 m; 当砂轮为 W20 型时 , 磨削模式 为断裂与塑性模式, 工件表面上的磨削条纹是断续 的 , 表面呈部分透明状, 表面粗糙度 R a 为 0 11 m; 当砂轮为 W10 型时 , 磨削模式为塑 性模式, 表面上 看不到任何微裂纹缺陷 , 表面完全透明。文献[ 8] 的
式中 , E 为材料的弹性模量 ( MPa) ; H 为材料的硬度
2004 年第 38 卷
11
41 的影响大于前者。而文献 [ 14] ~ 文献 [ 16] 中却认 为 : 砂轮速度越大 , 表面粗糙度越小, 因为砂轮速度 增加使得单颗磨粒的未变形切屑厚度减小。其中, 文献 [ 13] 指出, 提高砂轮速度比降低工件横向进给 速度及磨削深度更能有效地降低表面粗糙度。文献 [ 13] 还认为 , 采用高的砂轮速度 , 将使表面粗糙度得 到明显改善 , 其原因有三个: 一是砂轮速度提高, 磨 削力降低, 对于氧化铝砂轮来说 , 可降低磨粒的破碎 和磨损 , 提高磨粒的寿命, 增加与工件表面的摩擦抛 光时间 ; 二是砂轮速度提高, 磨削区的温度升高, 使 材料有可能发生塑性变形 , 促进砂轮对工件表面的 挤压摩擦作用; 三是砂轮速度提高, 单位时间内砂轮 与工件之间的接触次数增多 , 对工件表面的摩擦抛 光作用增强。 ( 2) 砂轮进给量 文献[ 7] 、 [ 9] 、 [ 13] 都认为 , 随着砂轮进给量的 减少 , 表面粗糙度 值减小。图 2 为在塑性磨削模 式下精磨光学玻璃时砂轮进给量与表面粗糙度的关 系。可以看出, 在塑性磨削模式下, 随着砂轮进给量 的减少 , 表面粗糙度值迅速减小。
[ 10]
图 3 工作台速度与 粗糙度的关系
( 1) 砂轮速度 K W Lee 通过陶瓷材料磨削试验认为 : 砂轮 速度越大 , 表面粗糙度越大。因为砂轮速度增加, 虽 然单颗磨粒的未变形切屑厚度减小 , 粗糙度应减小 , 但砂轮速度增加导致磨削系统的振动加剧, 且后者
( 4) 磨削深度 文献 [ 9] 认为 , 在塑性模式条件下进行磨削时, 表面粗糙度不受磨削深度的影响。史兴宽[ 17] 指出, 随着磨削深度的增大, 磨削表面的粗糙度值变大 , 因
3
影响脆性材料表面粗糙度的因素
脆性材料的磨削模式直接影响工件的 表面质 量, 表面质量包括表面粗糙度、 裂纹、 烧伤和残余应 力等。表面粗糙度是描写脆性材料表面质量的参数 之一 , 也是人们在磨削加工中普遍关注的首要问题。 对同一材料, 表面粗糙 度受砂轮磨粒 尺寸、 磨 削用 量, 光磨次数及磨削液等因素的综合影响。 3 1 砂轮磨粒尺寸 图 1 为精磨光学玻璃时砂轮磨粒尺寸与表面粗 糙度的关系[ 7] 。由图可见 , 砂轮磨粒尺寸越小 , 磨削 表面粗糙度 R a 值越小。这是由于砂轮磨粒尺寸越 小, 同时参与磨削的磨粒越多 , 磨刃密度系数 c 1 越 大, 越易形成塑性域磨削 , 所以粗糙度值越低, 文献 [ 7] ~ 文献[ 12] 都得出上述结论。
所示) 。
图 4 磨削深度 与粗糙度的关系
vanced ceramics with slotted diamond wheels. Journal of Mate rials Processing Technology, 2000, 100: 230~ 235 11 Yesha Zheng , Joaquim Manuel Vieira, Filipe Jose Oliveira et al . Relationship between flexural strength and surface rough ness for hot pressed Si3N4 self reinforced ceramics. Journal of the European Ceramic Society, 2000, 20: 1345~ 1353 12 Nobuhide Itoh, Hitoshi Ohmori. Grinding characteristics of hard and brittle materials by fine grain lapping wheels with ELID. Journal of Materials Processing Technology, 1996, 62: 315~ 320 13 胡 军 , 徐燕申 , 谢 艳 等 . 氮化 硅陶 瓷镶 块低 粗糙 度
式中 , h cmax 为单个磨粒的最大切削深度 ( mm) ; Vs 为 砂轮速度( m/ s) ; Vw 为工件进给速度 ( mm/ s) ; a p 为 磨削 深 度 ( mm ) ; N d 为 砂 轮 动 态 有 效 磨 刃 数 ( mm ) ; C 为磨削常数; d e 为砂轮当量直径( mm) 。 考虑金刚石砂轮的磨粒顶角为三角形, 可得砂 轮动态有效磨刃数 [ 6]
[ 7]
作者 通 过 磨 削 Pyrex 玻 璃 ( 砂 轮 的 线 速 度 v s = 1800m/ min, 工件速度 v w = 1 1m/ min, 磨削深度 a p = 2 m) 得出如下结论 : 当磨粒尺寸为 30~ 110 m 时 , 为断裂模式, 加工表面粗糙度 R a 为 471 3~ 867nm; 磨粒尺寸为 12~ 25 m 时, 断裂模式占 95% , 加工表 面粗糙度 R a 为 172nm; 磨粒尺寸为 2~ 6 m 时 , 磨削 模式为塑性, 加工表面粗糙度 R a 为 52 3nm 。
40
工 具技 术
脆性材料磨削模式与表面粗糙度
孟剑峰 李剑峰
山东大学
摘 要 : 对国内外有关脆性材料的磨削模式及表 面粗糙 度的研 究进展进 行了综 述 , 为获得高 质量的 脆性材 料 产品、 实施脆性材料的精密与超精密磨削提供有 益的参考。 关键词 : 脆性材料 , 磨削模式 , 表面粗糙度
葛培琪
[ 分析和 试验证 明, 脆性材料在适当的加工条件下仍能以塑性磨削 模式进行加工, 并得到粗糙度很低的光滑表面。实 现脆性材料塑性域磨削的条件是 : 砂轮单个磨粒的 最大切削深度应小于脆性材料的临界切削深度。T G Bifano [ 4] 应用显微压痕法建立了玻璃材料不产生 裂纹时的临界切削深度。通过应用扫描电镜观察玻 璃的压 痕形貌 发现 , 要使 玻璃 表面的 裂纹 数少 于 10% , 压痕的临界深度满足:
1
引言
( MPa) ; Kc 为材料的断裂韧性( MPa m) 。 通过对磨削过程中砂轮与工件的接触状态进行 分析, 得到砂轮单个磨粒的最大切削深度为[ 5]
h cmax = ( 4vw vsN d C a p/ d e ) 1/ 2 ( 2)
随着尖端科学技术的不断发展, 高质量的脆性 材料产品 , 如航空航天用陶瓷轴承、 工业及民用的石 英玻璃和陶瓷玻璃、 激光与红外光学晶体等的应用 越来越广泛 , 对脆性材料的精密及超精密加工的研 究也日益深入。脆性材料虽然用途十分广泛, 但硬 度高, 脆性大 , 为了获得高质量的脆性材料产品 , 克 服研抛技术生产周期长、 产品成本高的缺点, 近年来 出现了超精密磨削加工技术。对于脆性材料的磨削 加工, 材料的磨削模式对已加工表面质量有很大的 影响 , 根据最新研究 , 脆性材料在选择适当的参数条 件下仍能以塑性磨削模式加工 , 使得磨削表面的质 量等同甚至优于研抛表面[ 1~ 3] 。因此, 研究脆性材 料的磨削模式及表面粗糙度, 以及它们与刀具和加 工工艺参数之间的关系是非常重要的, 将会对脆性 材料的磨削加工起到一定的指导作用。
图 2 砂轮进给量与 粗糙度的关系
( 3) 工件速度
图1 金刚石砂轮磨粒尺寸与粗糙度的关系
如图 3[ 17] 所示, 在不同的光磨 次数下, 磨削表 面的粗糙度值都随工作台速度的降低而降低。因工 件速度减小 , 单颗磨粒的未变形切屑厚度减小, 所以 磨削表面粗糙度降低[ 16, 17] 。
但文献[ 13] 用氧化铝砂轮光磨氮化硅陶瓷镶块 却得出与此相反的结论, 即随着磨粒尺寸的增大, 表 面粗糙度值降低。这是因为砂轮磨削陶瓷表面的加 工过程可分为砂轮磨粒与工件表面凸峰的碰撞、 碰 撞与摩擦共同作用、 摩擦抛光三个阶段 , 当磨粒尺寸 较大时, 磨粒强度较高 , 不易破碎和脱落, 与工件之 间的摩擦抛光作用时间增加; 而当磨粒较小时 , 磨粒 易脱落, 与工件之间的摩擦抛光作用时间减弱。 3 2 磨削用量
N d= A g ( c 1) 2/ 3 2 ks
1/ 3
- 2
vw vs
1/ 3
ap de
1/ 6
( 3)