磨削加工时,影响工件表面粗糙度的因素
砂轮修整磨削加工工件表面粗糙度问题

砂轮修整磨削加工工件表面粗糙度问题
砂轮修整磨削加工工件表面粗糙度问题
一、从技术方面:
1 )磨床砂轮在修整工件的粗糙度达不到要求时,可以试着在砂轮转速范围内,加大砂轮的转速来提高工件的表面粗糙度。
从另一个方面来说,也可以试着将被磨削工件的转速降低。
此举目的就是加大砂轮与工件的相对转速。
2 )当按住第一种方法效果不理想时,还可以将工件的纵向进给量减小,以减少砂轮磨削弓箭的强度,这样也可以防止工件的`大面积烧伤。
3 )对于在磨床砂轮工作过程中,切削液,冷却液的流量也要试着控制,经常换用清洁的切削液、冷却液,以减少碎屑堵塞砂轮气孔。
4 )在上述几个情况都改进后,如工件还是会出现纹路或达不到工件的粗糙度要求是,那就要再对磨床砂轮的平衡精度、磨床主轴的回转精度、工作台的运动平稳性等多方面调整下机床以及整个工艺系统的刚度、消减磨削时的振动。
二、从砂轮选择方面:
因选择合适的砂轮来磨削适应的砂轮工件,一般来讲,
应选择与工件材料亲和力的磨料:工件材料的软、粘时,应选用较硬的磨具;硬、脆时选较软的磨具。
选择使用砂轮直径较大的砂轮,增大砂轮宽度,砂轮粒度越细,皆可降低工件表面粗糙度值。
三、从砂轮修整金刚笔使用方面:
在使用砂轮修整工件的过程中,砂轮的修整修锐时,因采用耐磨性好的金刚笔,合适的刃口形状和安装角度,按照技术科学合理的修磨,能使磨粒切削刃获得良好的等高性,降低表面粗糙度。
根据用户生产车间的不同需求,我司可提供来图来样生产各类磨床用砂轮修整
刀具,您可将砂轮特性参数电话或书面传真给我们,我司会为您择优选择。
影响机械加工表面粗糙度的几个因素及措施

职教类影响机械加工表面粗糙度的几个因素及措施摘要:表面粗糙度是零件表面所具有的微小峰谷的不平程度,它是评价零件的一项重要指标。
一般说来,它的波距和波高都比较小,是一种微观的几何形状误差。
对机械加工表面,表面粗糙度是由切削时的刀痕,刀具和加工表面之间的摩擦,切削时的塑性变形,以及工艺系统中的高频振动等原因所造成的。
表面粗糙度是检验零件质量的主要依据,它的选择直接关系到生产成本、产品的质量、使用寿命。
关键词:机械加工表面粗糙度提高措施随着工业技术的飞速发展,机器的使用要求越来越高,一些重要零件在高压力、高速、高温等高要求条件下工作,表面层的任何缺陷,不仅直接影响零件的工作性能,而且还可能引起应力集中、应力腐蚀等现象,将进一步加速零件的失效,这一切都与加工表面质量有很大关系。
因而表面质量问题越来越受到各方面的重视。
一、机械加工表面粗糙度对零件使用性能的影响表面粗糙度对零件的配合精度,疲劳强度、抗腐蚀性,摩擦磨损等使用性能都有很大的影响。
1、表面质量对零件配合精度的影响(1)对间隙配合的影响由于零件表面的凹凸不平,两接触表面总有一些凸峰相接触。
表面粗糙度过大,则零件相对运动过程中,接触表面会很快磨损,从而使间隙增大,引起配合性质改变,影响配合的稳定性。
特别是在零件尺寸和公差小的情况下,此影响更为明显。
(2)对过盈配合的影响粗糙表面在装配压入过程中,会将相接触的峰顶挤平,减少实际有效过盈量,降低了配合的连接强度。
2、表面质量对疲劳强度的影响零件表面越粗糙,则表面上的凹痕就越深明,产生的应力集中现象就越严重。
当零件受到交变载荷的作用时,疲劳强度会降低,零件疲劳损坏的可能性增大。
3、表面质量对零件抗腐蚀性的影响零件表面越粗糙,则积聚在零件表面的腐蚀气体或液体也越多,且通过表面的微观凹谷向零件表层渗透,形成表面锈蚀。
4、表面质量对零件摩擦磨损的影响两接触表面作相对运动时,表面越粗糙,摩擦系数越大,摩擦阻力越大,因摩擦消耗的能量也越大,并且还影响零件相对运动的灵活性。
浅谈加工表面粗糙度和物理力学性能的影响因素研究
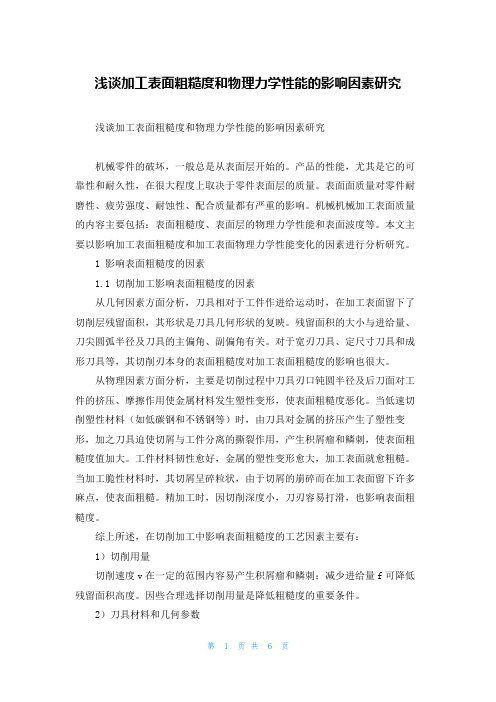
浅谈加工表面粗糙度和物理力学性能的影响因素研究浅谈加工表面粗糙度和物理力学性能的影响因素研究机械零件的破坏,一般总是从表面层开始的。
产品的性能,尤其是它的可靠性和耐久性,在很大程度上取决于零件表面层的质量。
表面面质量对零件耐磨性、疲劳强度、耐蚀性、配合质量都有严重的影响。
机械机械加工表面质量的内容主要包括:表面粗糙度、表面层的物理力学性能和表面波度等。
本文主要以影响加工表面粗糙度和加工表面物理力学性能变化的因素进行分析研究。
1 影响表面粗糙度的因素1.1 切削加工影响表面粗糙度的因素从几何因素方面分析,刀具相对于工件作进给运动时,在加工表面留下了切削层残留面积,其形状是刀具几何形状的复映。
残留面积的大小与进给量、刀尖圆弧半径及刀具的主偏角、副偏角有关。
对于宽刃刀具、定尺寸刀具和成形刀具等,其切削刃本身的表面粗糙度对加工表面粗糙度的影响也很大。
从物理因素方面分析,主要是切削过程中刀具刃口钝圆半径及后刀面对工件的挤压、摩擦作用使金属材料发生塑性变形,使表面粗糙度恶化。
当低速切削塑性材料(如低碳钢和不锈钢等)时,由刀具对金属的挤压产生了塑性变形,加之刀具迫使切屑与工件分离的撕裂作用,产生积屑瘤和鳞刺,使表面粗糙度值加大。
工件材料韧性愈好,金属的塑性变形愈大,加工表面就愈粗糙。
当加工脆性材料时,其切屑呈碎粒状,由于切屑的崩碎而在加工表面留下许多麻点,使表面粗糙。
精加工时,因切削深度小,刀刃容易打滑,也影响表面粗糙度。
综上所述,在切削加工中影响表面粗糙度的工艺因素主要有:1)切削用量切削速度v在一定的范围内容易产生积屑瘤和鳞刺;减少进给量f可降低残留面积高度。
因些合理选择切削用量是降低粗糙度的重要条件。
2)刀具材料和几何参数实践表明,在切削条件相同时,用硬质合金刀具加工的工作表面粗糙度比用高速钢刀具加工的低。
用金钢石车刀加工因不易形成积屑瘤,故可获得粗糙度很低的表面。
刀类圆弧半径rE、主偏角KC和副偏角kcC均影响残留面积的大小。
金属加工表面质量的影响因素及改进措施
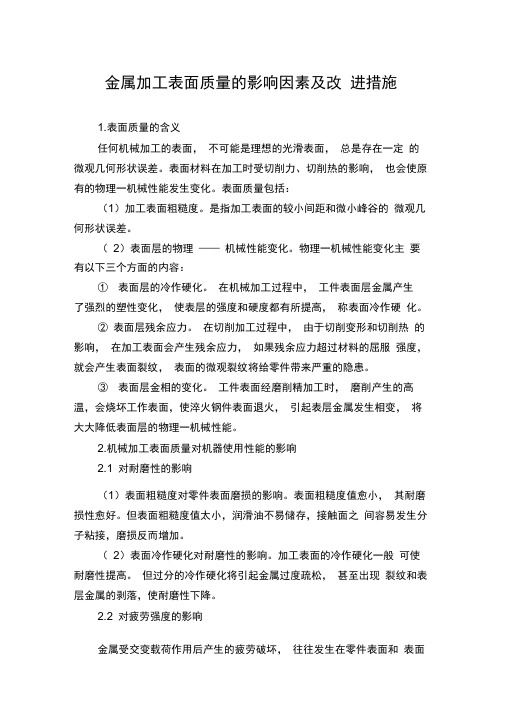
金属加工表面质量的影响因素及改进措施1.表面质量的含义任何机械加工的表面,不可能是理想的光滑表面,总是存在一定的微观几何形状误差。
表面材料在加工时受切削力、切削热的影响,也会使原有的物理一机械性能发生变化。
表面质量包括:(1)加工表面粗糙度。
是指加工表面的较小间距和微小峰谷的微观几何形状误差。
(2)表面层的物理——机械性能变化。
物理一机械性能变化主要有以下三个方面的内容:①表面层的冷作硬化。
在机械加工过程中,工件表面层金属产生了强烈的塑性变化,使表层的强度和硬度都有所提高,称表面冷作硬化。
②表面层残余应力。
在切削加工过程中,由于切削变形和切削热的影响,在加工表面会产生残余应力,如果残余应力超过材料的屈服强度,就会产生表面裂纹,表面的微观裂纹将给零件带来严重的隐患。
③表面层金相的变化。
工件表面经磨削精加工时,磨削产生的高温,会烧坏工作表面,使淬火钢件表面退火,引起表层金属发生相变,将大大降低表面层的物理一机械性能。
2.机械加工表面质量对机器使用性能的影响2.1 对耐磨性的影响(1)表面粗糙度对零件表面磨损的影响。
表面粗糙度值愈小,其耐磨损性愈好。
但表面粗糙度值太小,润滑油不易储存,接触面之间容易发生分子粘接,磨损反而增加。
(2)表面冷作硬化对耐磨性的影响。
加工表面的冷作硬化一般可使耐磨性提高。
但过分的冷作硬化将引起金属过度疏松,甚至出现裂纹和表层金属的剥落,使耐磨性下降。
2.2 对疲劳强度的影响金属受交变载荷作用后产生的疲劳破坏,往往发生在零件表面和表面冷硬层下面,因此零件的表面质量对疲劳强度影响很大。
(1)表面粗糙度对疲劳强度的影响。
在交变载荷作用下,表面粗糙度的凹谷部位容易引起应力集中,产生疲劳裂纹。
表面粗糙度值愈大,表面的纹痕愈深,纹底半径愈小,抗疲劳破坏的能力就愈差。
(2 )残余应力、冷作硬化对疲劳强度的影响。
表面层残余拉应力,将使疲劳裂纹扩大,加速疲劳破坏;而表面层残余压应力,能够阻止疲劳裂纹的扩展,延缓疲劳破坏的产生:表面冷硬化一般伴有残余压应力的产生,可以防止裂纹产生并阻止已有裂纹的扩展,对提高疲劳强度有利。
车床工件表面粗糙度的形成原因及解决措施

车床工件表面粗糙度的形成原因及解决措施表面粗糙度是机械加工中衡量加工质量的重要因素,表面粗糙度对零件和机器有着重要的意义。
但由于工件材料、切削加工方式、表面硬化等原因,造成了表面粗糙度值提高。
本文详细分析了车床工件表面粗糙度的形成原因,并提出相应的解决措施。
标签:车床工件:表面:粗糙度:原因:解决措施1.引言在实际的机械加工中,工件表面会存在许多高低不平的微小峰谷,这是因为切屑分离时塑性变形、工艺系统的振动以及刀具与已加工表面问的摩擦等因素的影响。
这些零件被加工表面上的微观几何形状误差称为表面粗糙度。
表面粗糙度对零件的耐磨性、耐腐蚀性、疲劳强度和配合性质都有很大影响。
本文详细分析了车床工件表面粗糙度的形成原因,并提出相应的解决措施,具有一定的实际意义。
2.影响工件表面粗糙度的原因2.1工件材料性能。
塑性金属材料在加工的过程中,刀具挤压金属材料,使其产生塑性变形,切屑和工件分离是由于刀具外力的挤压,表面出现撕裂现象,这严重影响表面粗糙度。
伴随着工件材料韧性的提高,在切屑过程中材料的塑性变形也就越大,加工表面粗糙度也就越差。
脆性材料在加工时,所切削形成的铁屑为颗粒状,在切屑崩碎的过程中,加工表面容易产生细小的坑点,提高表面粗糙度值。
2.2刀具切削加工。
在普通刀具在切屑过程中,切削表面势必会产生残留面积,残留面积的高度则是影响加工表面粗糙度的主要因素。
在整个加工过程中,刀具的进给量、主偏角、副偏角、圆弧半径则是造成切削残留面积的主要因素。
砂轮磨削加工过程中,砂轮上硬质颗粒断裂后形成微刃,其分布情况和外形对表面粗糙度有着直接的影响。
因为磨削加工表面是大量微刃在金属表面切削出细小的切削痕迹构成的,所形成的切削痕迹越细小、越密集则表面粗糙度就越好,相反切削痕迹粗大、分布疏散,则表面粗糙度越差。
2.3表面冷作硬化。
在普通刀具切削或砂轮磨削过程中,表面层金属由于刀具外在切削力和材料本身的塑性,使其晶格产生剪切、滑移、拉长、扭曲、破碎,宏观的表现特点则是材料表面层变硬,屈服点提高,延生率降低。
影响表面粗糙度的因素

.影响表面粗糙度的因素1.切削加工中影响表面粗糙度的因素1)?几何因素2)物理因素切削加工后表面粗糙度的实际轮廓形状一般都与由纯几何因素形成的理想轮廓有较大的差别。
这是由于存在与被加工材料的性质及切削机理有关的物理因素的缘故。
采用低切削速度加工塑性金属材料(如低碳钢、铬钢、不锈钢、高温合金、铝合金等)时,容易出现积屑瘤与鳞刺,使加工表面粗糙度严重恶化,成为影响加工表面质量的主要因素。
刀具与被加工材料的挤压与磨擦使金属材料发生塑性变形,也会增大表面粗糙度。
切削加工中的振动,使工件的表面粗糙度增大。
从物理因素看,降低表面粗糙度的主要措施是减少加工时的塑性变形,避免产生积屑瘤和鳞刺。
其主要影响因素有切削速度、被加工材料的性质、刀具的几何形状、材料性质和刃磨质量。
适当增大刀具的前角,可以降低被切削材料的塑性变形;降低刀具前刀面和后刀面的表面粗糙度可以抑制积屑瘤的生成;增大刀具后角,可以减少刀具和工件的摩擦;合理选择冷却润滑液,可以减少材料的变形和摩擦,降低切削区的温度;采取上述各项措施均有利于减小加工表面的粗糙度。
2.磨削中影响表面粗糙度的因素三.影响加工表面金属层物理力学性能的因素加工过程中,由于切削力和切削热的作用,工件表面金属层的物理力学性能会发生很大的变化,导致表面层金属和基体材料的性能有很大的差异。
其影响因素主要表现为三个方面。
1.表面层金属材料的加工硬化切削(磨削)过程中产生的塑性变形,会使表层金属的晶格发生畸变,晶粒间产生剪切滑移,晶粒被拉长,甚至破碎,从而使表层金属的硬度和强度提高,这种现象称为加工硬化。
加工硬化的程度取决于塑性变形的程度。
影响加工硬化的因素(1)?切削力越大,塑性变形越大,硬化程度也越大。
因此,当进给量、背吃刀量增大,刀具前角减小时,都会因切削力增大而使加工硬化程度增大。
(2)?切削温度越高,会使加工硬化作用减小。
如切削速度增大,会使切削温度升高,加工硬化程度将会减小。
机械制造中的机械加工表面粗糙度工作原理

机械制造中的机械加工表面粗糙度工作原理机械加工是指通过削、切、磨等工艺将工件原有形状进行改变以满足一定尺寸、形状和粗糙度要求的加工方法。
在机械制造过程中,机械加工表面粗糙度的控制是十分重要的,它直接影响到零件的功能和使用寿命。
本文将介绍机械加工表面粗糙度的工作原理。
一、表面粗糙度的概念表面粗糙度是指工件表面上凹凸不平的程度,通常用Ra(平均粗糙度)来表示。
在机械加工中,我们常常要求工件表面光洁度高、粗糙度小,以确保零件的密封性、运动性和装配性能。
二、机械加工表面粗糙度的影响因素机械加工表面粗糙度受到多种因素的影响,主要包括以下几个方面:1.切削参数:切削速度、进给量、切削深度等切削参数直接影响到工件表面的质量。
一般来说,切削速度越大、进给量越小、切削深度越小,工件表面的粗糙度就越小。
2.切削工具状况:切削工具的磨损情况对工件表面质量有重要影响。
切削工具磨损过度会导致切削力增大、表面粗糙度加大。
所以,及时更换和修磨切削工具能够有效控制表面粗糙度。
3.工件材料:工件材料的硬度、韧性等性质会影响机械加工的精度和表面质量。
例如,硬度较高的材料可能导致切削刀具的磨损,从而影响表面的粗糙度。
4.切削方式:不同的切削方式,如车削、铣削、磨削等,对工件表面粗糙度的影响也有所不同。
三、机械加工表面粗糙度的控制方法为了能够控制机械加工表面的粗糙度,在实际操作中可以采取以下措施:1.选择合适的工艺参数:根据工件材料、形状和要求,合理选择切削速度、进给量、切削深度等参数,以获得较小的粗糙度。
2.使用高质量的切削工具:选择具有良好刚性和耐磨性的切削工具,并保持其锋利度,以便实现更好的切削效果。
3.优化切削方式:根据工件的特点,选择合适的切削方式。
有时候,可以采用一些先进的切削方式,如超声波切削、电火花加工等,以改善表面粗糙度。
4.后续加工工艺:有时候,机械加工的表面粗糙度无法满足要求,可以考虑通过后续加工工艺来改善。
例如,研磨、抛光等方法可以使工件表面更加光滑。
表面粗糙度及其影响因素
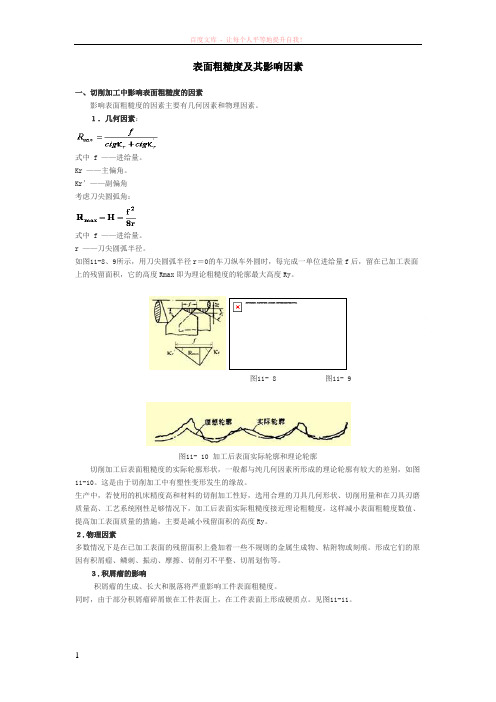
表面粗糙度及其影响因素一、切削加工中影响表面粗糙度的因素影响表面粗糙度的因素主要有几何因素和物理因素。
1.几何因素:式中 f ——进给量。
Kr ——主偏角。
Kr’——副偏角考虑刀尖圆弧角:式中 f ——进给量。
r ——刀尖圆弧半径。
如图11-8、9所示,用刀尖圆弧半径r=0的车刀纵车外圆时,每完成一单位进给量f后,留在已加工表面上的残留面积,它的高度Rmax即为理论粗糙度的轮廓最大高度Ry。
图11- 8 图11- 9图11- 10 加工后表面实际轮廓和理论轮廓切削加工后表面粗糙度的实际轮廓形状,一般都与纯几何因素所形成的理论轮廓有较大的差别,如图11-10。
这是由于切削加工中有塑性变形发生的缘故。
生产中,若使用的机床精度高和材料的切削加工性好,选用合理的刀具几何形状、切削用量和在刀具刃磨质量高、工艺系统刚性足够情况下,加工后表面实际粗糙度接近理论粗糙度,这样减小表面粗糙度数值、提高加工表面质量的措施,主要是减小残留面积的高度Ry。
2.物理因素多数情况下是在已加工表面的残留面积上叠加着一些不规则的金属生成物、粘附物或刻痕。
形成它们的原因有积屑瘤、鳞刺、振动、摩擦、切削刃不平整、切屑划伤等。
3.积屑瘤的影响积屑瘤的生成、长大和脱落将严重影响工件表面粗糙度。
同时,由于部分积屑瘤碎屑嵌在工件表面上,在工件表面上形成硬质点。
见图11-11。
图11- 11 图11- 12鳞刺的影响鳞刺的出现,使已加工表面更为粗糙不平。
鳞刺的形成分为:抹拭阶段:前一鳞刺已经形成,新鳞刺还未出现;而切屑沿着前刀面流出,切屑以刚切离的新鲜表面抹拭刀——屑摩擦面,将摩擦面上有润滑作用的吸附膜逐渐拭净,以致摩擦系数逐渐增大,并使刀具和切屑实际接触面积增大,为这两相摩擦材料的冷焊创造条件,如图11-12(a)。
导裂阶段:由于在第一阶段里,切屑将前刀面上的摩擦面抹拭干净,而前刀面与切屑之间又有巨大的压力作用着,于是切屑与刀具就发生冷焊现象,切屑便停留在前刀面上,暂时不再沿前刀面流出。
- 1、下载文档前请自行甄别文档内容的完整性,平台不提供额外的编辑、内容补充、找答案等附加服务。
- 2、"仅部分预览"的文档,不可在线预览部分如存在完整性等问题,可反馈申请退款(可完整预览的文档不适用该条件!)。
- 3、如文档侵犯您的权益,请联系客服反馈,我们会尽快为您处理(人工客服工作时间:9:00-18:30)。
磨削加工时,影响工件表面粗糙度的因素
1、磨削用量对表面粗糙度的影响
1)砂轮的速度越高,单位时间内通过被磨表面的磨粒数就越多,因而工件表面的粗糙度值就越小。
同时,砂轮速度越高,就有可能使表面金属塑性变形的传播速度大于切削速度,工件材料来不及变形,致使表层金属的塑性变形减小,磨削表面粗糙度值也将减小。
2)工件速度对表面粗糙度的影响刚好与砂轮速度的影响相反,增大工件速度时,单位时间内通过被磨表面的磨粒数减少,表面粗糙度值将增加。
3)砂轮的纵向进给减小,工件表面的每个部位被砂轮重复磨削的次数增加,被磨表面的粗糙度值将减小。
4)磨削液厂家“联诺化工”发现随着磨削深度增大,表层塑性变形将随之增大,被磨表面粗糙度值也会增大。
2、磨削液对表面粗糙度的影响
磨削液对磨削力,磨削温度及砂轮磨损等方面的影响,最终会影响工件表面粗糙度。
高效磨削液是一种水基化学合成液,它含有阴离子表面活性剂,磨削加工时,砂轮与工件间的磨削产生阳离子。
因此,这种磨削液可使砂轮与工件的接触区不产生高热,减少磨粒磨损。
同时它含有润滑性能好,吸附性能强的添加剂,在高温高压下与铁反应形成牢固的润滑膜,减小了磨削阻力。
高效磨削液还含有非离子表面活性剂,它可降低水的表面张力,提高磨削液的浸润性和清洗性,有利于降低工件表面粗糙度。
磨削液厂家“联诺化工”的SCC750B水性环保磨削液属于高效磨削液。
SCC750B选用特制的高性能极压添加剂、防锈剂等其它添加剂复配而成,与水混合时可形成稳定的透明荧光绿色溶液。
SCC750B水性环保磨削液具有良好的极压润滑性、防锈性、冷却性、沉降性和清洗性。
具有极强的抗微生物分解能力,在不同的水硬度条件下,仍可保持其稳定性,是新一代高性能的多用途的无泡磨削液。
SCC750B水性环保磨削液优点:
●含特种极压润滑添加剂,可显著减少砂轮磨损;
●采用高分子水/油溶性防锈剂,对设备及工件(特别是铸铁)有极好的防锈性;
●无泡沫倾向,清洗性能好,比同类产品有更好的金属屑沉降性;透明度高,有利于监察工件的表面加工状态及切削液消耗量,不会刺激皮肤,保护操作者健康;使用寿命长,一年以上更换期,符合环保要求,减少浪费,提高生产效率;
●对操作工人皮肤无伤害、及机台油漆无影响,且有保护作用。
3、砂轮对表面粗糙度的影响
1)砂轮粒度单纯从几何因素考虑,砂轮粒度越细,磨削的表面粗糙度值越小。
但磨削液厂家“联诺化工”发现磨粒太细时,砂轮易被磨屑堵塞,若导热情况不好,反而会在加工表面产生烧伤等现象,使表面粗糙度值增大。
因此,砂轮粒度常取为46~60号。
2)砂轮硬度砂轮太硬,磨粒不易脱落,磨钝了的磨粒不能及时被新磨粒替代,使表面粗糙度值增大。
磨削液厂家“联诺化工”发现砂轮太软,磨粒易脱落,磨削作用减弱,也会使表面粗糙度值增大。
常选用中软砂轮。
3)砂轮组织紧密组织中的磨粒比例大,气孔小,在成形磨削和精密磨削时,能获得较小的表面粗糙度值。
疏松组织的砂轮不易堵塞,适于磨削软金属、非金
属软材料和热敏性材料(磁钢、不锈钢、耐热钢等),可获得较小的表面粗糙度值。
一般情况下,应选用中等组织的砂轮。
4)砂轮材料选择适当,可获得满意的表面粗糙度。
磨削液厂家“联诺化工”提醒氧化物(刚玉)砂轮适用于磨削钢类零件;碳化物(碳化硅、碳化硼)砂轮适于磨削铸铁、硬质合金等材料;用高硬磨料(人造金刚石、立方氮化硼)砂轮磨削可获得很小的表面粗糙度值,但加工成本较高。
5)砂轮修整对表面粗糙度也有重要影响。
精细修整过的砂轮可有效减小被磨工件的表面粗糙度值。