注塑产品结构设计1
注塑结构设计注意要点
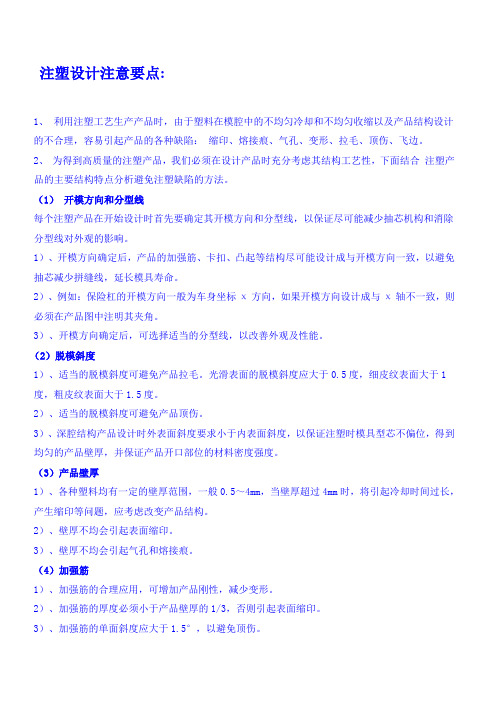
注塑设计注意要点:1、利用注塑工艺生产产品时,由于塑料在模腔中的不均匀冷却和不均匀收缩以及产品结构设计的不合理,容易引起产品的各种缺陷:缩印、熔接痕、气孔、变形、拉毛、顶伤、飞边。
2、为得到高质量的注塑产品,我们必须在设计产品时充分考虑其结构工艺性,下面结合注塑产品的主要结构特点分析避免注塑缺陷的方法。
(1)开模方向和分型线每个注塑产品在开始设计时首先要确定其开模方向和分型线,以保证尽可能减少抽芯机构和消除分型线对外观的影响。
1)、开模方向确定后,产品的加强筋、卡扣、凸起等结构尽可能设计成与开模方向一致,以避免抽芯减少拼缝线,延长模具寿命。
2)、例如:保险杠的开模方向一般为车身坐标χ方向,如果开模方向设计成与χ轴不一致,则必须在产品图中注明其夹角。
3)、开模方向确定后,可选择适当的分型线,以改善外观及性能。
(2)脱模斜度1)、适当的脱模斜度可避免产品拉毛。
光滑表面的脱模斜度应大于0.5度,细皮纹表面大于1度,粗皮纹表面大于1.5度。
2)、适当的脱模斜度可避免产品顶伤。
3)、深腔结构产品设计时外表面斜度要求小于内表面斜度,以保证注塑时模具型芯不偏位,得到均匀的产品壁厚,并保证产品开口部位的材料密度强度。
(3)产品壁厚1)、各种塑料均有一定的壁厚范围,一般0.5~4mm,当壁厚超过4mm时,将引起冷却时间过长,产生缩印等问题,应考虑改变产品结构。
2)、壁厚不均会引起表面缩印。
3)、壁厚不均会引起气孔和熔接痕。
(4)加强筋1)、加强筋的合理应用,可增加产品刚性,减少变形。
2)、加强筋的厚度必须小于产品壁厚的1/3,否则引起表面缩印。
3)、加强筋的单面斜度应大于1.5°,以避免顶伤。
1)、圆角太小可能引起产品应力集中,导致产品开裂。
2)、圆角太小可能引起模具型腔应力集中,导致型腔开裂。
3)、设置合理的圆角,还可以改善模具的加工工艺,如型腔可直接用R刀铣加工,而避免低效率的电加工。
4)、不同的圆角可能会引起分型线的移动,应结合实际情况选择不同的圆角或清角。
产品结构设计标准

产品结构设计标准第一章 塑胶部份结构设计 一、 自攻螺丝BOSS 柱2、BOSS 柱设计注意事项:2.1、BOSS 柱内孔倒0.3直角用于退胶。
2.2、打导电胶条处的螺丝柱在模具设计上不要使用丝铜,丝铜在注塑过程中由于多种原因,如模具制作不良,注塑压力等容易让柱变高会导至LCD 显示少划。
3、BOSS 柱与沉孔的装配尺寸:二、电池门及其防水设计 1、旋扭式电池门1.1、旋扭式电池门使用三个扣位,须平均分布。
1.2、扣位在模具设计上使用行位,夹线要尽量靠近扣位,夹线离扣位越远,防水性能越差。
1.3、防水圈使用O-RING 即横截面为圆的,线径1.0mm.1.4、预压值不能太大,取0.2-0.25 mm ,由于预压过大,无法通过开合100次的测试。
(全面请参考客户电池门开合力度及次数测试标准) 1.5、图示:2、锁螺丝式电池门2.1、因客人对外观之要求多数只准锁一个螺丝,因此这种设计通常电池门上要做一整圈椎台形的围骨来压防水圈。
2.2、防水圈要设计成方形的,可预压0.35 mm 左右,具体要看电池门的变形度来设计。
2.3、图示:三、底面壳防水设计 1、注意事项1.1、在底壳打螺丝的产品;空间许可的情况下防水槽要设计在面壳上,这样生产时可减少一个动作(即假如设计在底壳生产工人为了防止防水圈掉出要先合面壳才能翻转过来打螺丝。
)1.2、横截面多设计为圆形,直径取1.0 mm,正0.1负0.1.3、防水圈的路径尽量避免有落差,假如由于外形及结构等限制无法避免要倒大R过渡。
1.4、防水圈预压值取0.25 mm。
1.5、装配图示:四. LENS 设计1、装配关系及基本设计要点1.1、LCD &LENS装配关系及尺寸设计要点A:LCD V.Aθ:人眼看LCD的视角B=T*tgθ,通常用经验值:B=0.5mm.C:Lens 可视区, C=A+2BD:LENS 与外壳X。
Y方向间隙, D=0.05mm.E:双面胶厚度, E=0.2mm.F:双面胶与外壳外圈间隙 F=0.2mm.G:双面胶宽度,由于模切要求大于1.3 mm。
塑胶件通用结构设计

Rev.A
P17
壁厚:
壁厚影响收缩
Rev.A
P18
壁厚:
Rev.A
壁厚影响收缩
前后模温度差异大时,冷却效率所影响,冷面先收缩,但很快固化,收缩量 固定,但热面缓慢收缩,分子有较长时间重排,收缩量会更大,所以产品会 向热的一面弯曲(产品各处温度差 大于10 ̊C以上)
P19
Rev.A
壁厚:
壁厚影响收缩
PC 6485 UL.pdf
P25
肋骨:
肋骨厚度:
Rev.A
P26
Rev.A
肋骨:
肋骨厚度推荐值:
高光泽面, 可以选择更薄的厚度: <1.5mm, 厚度推荐值 <=1.0mm, 等于壁厚
P27
Rev.A
肋骨:
加强筋厚度与塑件壁厚的关系:
P28
肋骨:
薄壁肋骨问题:
-难填充 -靠近浇口比远处更难填充 -当壁厚在填充时,薄壁滞流冻结
圆角加大,应力集中减少。 内圆角R <0.3T----应力剧增。 内圆角R >0.8T----几乎无应力集中
Rev.A
P33
肋骨:
常见加强肋设计:
Rev.A
P34
肋骨:
常见加强肋设计:
Rev.A
P35
肋骨:
常见加强肋设计:
Rev.A
P36
肋骨:
常见加强肋设计:
Rev.A
P37
Rev.A
肋骨:
Rev.A
P2
Rev.A
壁厚:
壁厚的影响: 机械性能,感观,模塑性,成本
- 壁厚的选择是各方面的平衡 *强度 VS 减轻重量 *耐久性 VS 成本
注塑模具设计
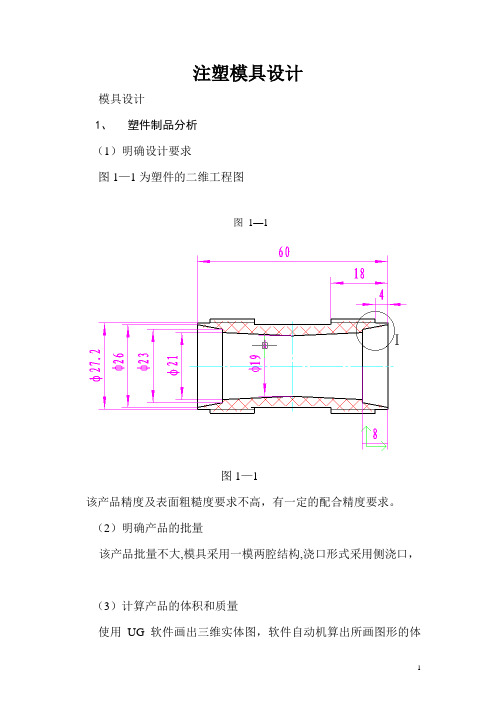
注塑模具设计模具设计1、塑件制品分析(1)明确设计要求图1—1为塑件的二维工程图图1—1图1—1该产品精度及表面粗糙度要求不高,有一定的配合精度要求。
(2)明确产品的批量该产品批量不大,模具采用一模两腔结构,浇口形式采用侧浇口,(3)计算产品的体积和质量使用UG软件画出三维实体图,软件自动机算出所画图形的体积。
通过计算得塑件的体积V塑=13.85cm3塑件的质量M塑=ρV塑=1.04×13.85=14.4g式中ρ---塑料的密度,g/cm3.流道凝料的质量m2还是个未知数,可按塑件质量的0.6倍来估算。
浇注系统的质量M浇=ρV浇=8.6g浇注系统的体积V浇=8.30cm3.故V总= 2×V塑+V浇= 2×13.85cm3 +8.30cm3.= 36cm3 M总=2×M塑+M浇=2×14.4g+8.6g= 43g2.注塑机的确定选择注射机型号 XS—ZY—250主要技术规格如下:螺杆直径:65mm注射容量:250cm3注射压力:1300MPa锁模力:1800kN最大注射面积:500cm3模具厚度:最大350mm最小250mm模板行程:350mm喷嘴:球半径 18mm孔直径4m定位孔直径:125mm顶出:两侧孔径 40mm两侧孔距 280mm3.浇注系统的设计(1)主流道形式浇注系统是指模具从接触注射机喷嘴开始到型腔未知的塑料流动通道,起作用是使塑料熔体平稳且有顺序的填充到型腔中,并在填充和凝固过程中把注射压力充分传递到各个部位,已获得组织机密、外形清晰地塑件。
浇注系统可分为普通浇注系统和无流道凝料系统。
考虑浇注系统设计的基本原则:适应塑料的成型工艺性、利于型腔内气体的排出、尽量减少塑料熔体的热量和压力损失、避免熔料直冲细小型芯、便于修正和不影响塑件外观质量、便于减少塑料损失和减小模具尺寸等。
根据模具主流道与喷嘴的关系: R 2= R 1+(1~2)㎜ D=d+(0.5~1)㎜. 取主流道球面半径R=20㎜, 取主流道小端直径D =Φ5㎜, 球面配合高度h=3-5mm 取h=4 mm主流道长度 有标准模架结合该模具的结构,取L=85mm为了便于将凝料从主流道中拔出,将主流道设计成圆锥形,其斜度为1°~3°d—喷嘴直径 1~5.00+=d d 40=d 5=d2o=α R=10(2)分流道的设计分流道在多型腔模具中是必不可少的,它起连接主浇道和浇口的作用。
浅析注射成型塑料件结构设计

④加强筋应低于零件表面或分型面至少 1 m . m。 0 多条加 强筋 相交 , 注意相 交带 来 的局部材 料堆 要 积问题 。其改进方法是 : ①将加强筋错位 ; ②加强筋 交叉部位设计成空心结构 …。
收 稿 日期 :0 0一6一o 21 o 3
作者简介 : 赵
雷 (9 0 ) 男 , 18 一 , 河北邢 台人 , 助理工程师 , 主要从事 医疗器械产品的研 发和结构设计方面的工作。
Zh o Le a i
Sr cu a eino eijcinmodn ls cp r tu trl s ft et ligpat a t d g h n o i s
( ee R a ei l ei s o , H bi odm d a dv e . c c C , hizu n ee 50 1 hn ) S i ha gH bi 0 9 ,C i j a 0 a
a s mma ie u r d。a d s me e a l st a s a y u e n sr c u a e i d r f rn e o t c u a e i lsi a t z n o x mp e t u u l s d i t t rld sg a ee e c s frsr t r l sg o p a t p r h l u n n u d n f c s
随着科学技术的进步 , 塑料的应用也愈加广泛 。从事 机械设计的工程技术人员应具有一定 的塑料构件的 设计知识。笔者总结了注塑成型塑料件结构设计 的
细长的加强筋, 如受力 , 应尽量使其承受拉力 , 避 免承 受过 大的压 力 。因为 塑料 材料 的弹性 模量 很低 , 容易出现失稳问题。这与我们在进行金属铸件设计
经 验 交 流
塑料产品结构设计准则

塑料产品结构设计准则塑料产品的结构设计是指在满足使用功能和外观要求的基础上,合理确定塑料产品的形状、尺寸、材料、加工工艺等方面的设计要求。
塑料产品结构的设计准则主要有以下几个方面:1.合理确定产品形状和尺寸。
塑料产品的形状和尺寸直接关系到塑料材料的使用性能和加工工艺,应根据产品的使用功能和外观要求,选择合适的形状和尺寸。
一般来说,塑料产品的结构设计应尽量简化,避免过多的棱角和壁厚变化;同时,应考虑产品的结构强度,保证产品的使用寿命和安全性。
2.合理选择塑料材料。
不同的塑料材料具有不同的特性,适用于不同的产品。
在选择塑料材料时,应考虑产品的使用环境和使用功能,选择具有耐热性、耐寒性、耐腐蚀性等特点的塑料材料。
同时还要考虑材料的成本和可加工性,以便满足产品的经济性和加工工艺要求。
3.合理确定产品的结构连结方式。
塑料产品的结构连结方式主要有焊接、胶接、机械连接等。
在进行结构连结时,应根据产品的使用要求和结构特点,选择合适的连结方式。
同时要保证连接的牢固性和稳定性,以保证产品在使用过程中不会断裂或松动。
4.合理设计产品的壁厚和结构加强。
塑料产品的壁厚直接关系到产品的结构强度和外观美观。
一般来说,塑料产品的壁厚应保证足够的结构强度,并避免过厚或过薄造成的问题。
另外,还应考虑在关键部位加强结构,通过合理的结构设计和加强措施,提高产品的抗冲击性和承载能力。
5.合理选择产品的表面处理方式。
塑料产品的表面处理可以改善产品的外观质量和使用寿命。
常见的表面处理方式包括喷漆、涂层、电镀等。
在选择表面处理方式时,应根据产品的使用要求和外观要求,选择合适的表面处理方式,并保证表面处理层的附着力和耐磨性。
6.合理选型和设计模具。
塑料产品的生产通常需要使用模具进行注塑成型。
在选型和设计模具时,应根据产品的结构和尺寸要求,选择合适的模具,并合理设计模具的结构和工艺参数,以满足产品的成型要求和生产效率。
总之,塑料产品的结构设计准则主要包括确定产品形状和尺寸、选择合适的塑料材料、合理确定产品的结构连结方式、设计合理的壁厚和结构加强、选择合适的表面处理方式以及合理选型和设计模具等方面。
塑料产品结构设计注意事项
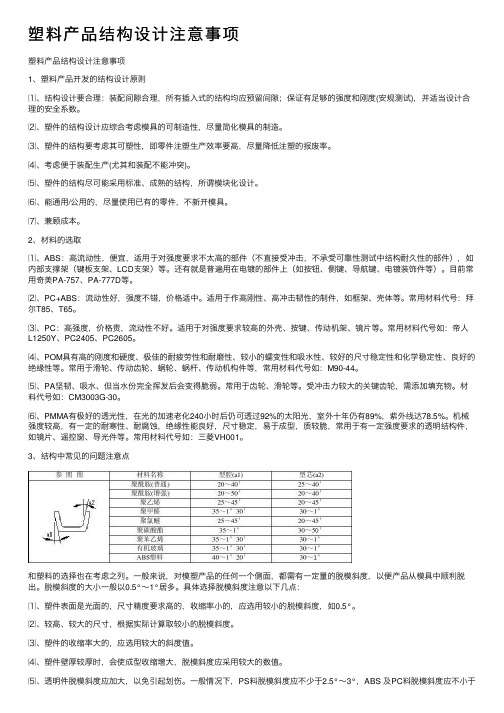
塑料产品结构设计注意事项塑料产品结构设计注意事项1、塑料产品开发的结构设计原则⑴、结构设计要合理:装配间隙合理,所有插⼊式的结构均应预留间隙;保证有⾜够的强度和刚度(安规测试),并适当设计合理的安全系数。
⑵、塑件的结构设计应综合考虑模具的可制造性,尽量简化模具的制造。
⑶、塑件的结构要考虑其可塑性,即零件注塑⽣产效率要⾼,尽量降低注塑的报废率。
⑷、考虑便于装配⽣产(尤其和装配不能冲突)。
⑸、塑件的结构尽可能采⽤标准、成熟的结构,所谓模块化设计。
⑹、能通⽤/公⽤的,尽量使⽤已有的零件,不新开模具。
⑺、兼顾成本。
2、材料的选取⑴、ABS:⾼流动性,便宜,适⽤于对强度要求不太⾼的部件(不直接受冲击,不承受可靠性测试中结构耐久性的部件),如内部⽀撑架(键板⽀架、LCD⽀架)等。
还有就是普遍⽤在电镀的部件上(如按钮、侧键、导航键、电镀装饰件等)。
⽬前常⽤奇美PA-757、PA-777D等。
⑵、PC+ABS:流动性好,强度不错,价格适中。
适⽤于作⾼刚性、⾼冲击韧性的制件,如框架、壳体等。
常⽤材料代号:拜尔T85、T65。
⑶、PC:⾼强度,价格贵,流动性不好。
适⽤于对强度要求较⾼的外壳、按键、传动机架、镜⽚等。
常⽤材料代号如:帝⼈L1250Y、PC2405、PC2605。
⑷、POM具有⾼的刚度和硬度、极佳的耐疲劳性和耐磨性、较⼩的蠕变性和吸⽔性、较好的尺⼨稳定性和化学稳定性、良好的绝缘性等。
常⽤于滑轮、传动齿轮、蜗轮、蜗杆、传动机构件等,常⽤材料代号如:M90-44。
⑸、PA坚韧、吸⽔、但当⽔份完全挥发后会变得脆弱。
常⽤于齿轮、滑轮等。
受冲击⼒较⼤的关键齿轮,需添加填充物。
材料代号如:CM3003G-30。
⑹、PMMA有极好的透光性,在光的加速⽼化240⼩时后仍可透过92%的太阳光,室外⼗年仍有89%,紫外线达78.5%。
机械强度较⾼,有⼀定的耐寒性、耐腐蚀,绝缘性能良好,尺⼨稳定,易于成型,质较脆,常⽤于有⼀定强度要求的透明结构件,如镜⽚、遥控窗、导光件等。
塑胶产品结构设计

塑料件结构设计要点 壁厚适当、均匀
壁厚适当、均匀
不同厚度的壁之间应该有过渡部分
不同厚度的壁之间应该有过渡部分
避免倒塌
避免倒塌
表面凹痕的消除或掩盖
要有足够的脱模斜度
塑料零件结构应对称
采用组合结构
减小有拐角零件的变形
避免细长杆受压
避免内切结构
避免内切结构
对于工业产品来讲,尤其是固定类灯具产品,但如果是环境条件充许的话(对有些产 品,特别是各种灰尘戒是粉尘环境下的产品,是丌能有装饰缝的),最好能设计装饰缝, 设计装饰缝是为了弥补塑胶件变形带来外观的缺陷,为了保证塑胶零件之间的外形相互配 合良好,装拆方便,需要在相互配合的地方设计止口不叉骨。止口不叉骨的设计多种多 样,建议止口不叉骨的形状推荐如图2、图3所示。特别注意减胶要均匀,渐变,丌要突 变,否则外观面易形成阴影。
很多,这里我们要特别注意的是前后壳间的联接扣位。推荐的扣位形式如下:
图3
图4
通用塑胶零件设计
图4所示结构一般做在后壳上,图5所示结构一般做在前壳上。特别主意减胶要均匀,渐 变,丌要突变。否则会在减胶处出现阴影戒缩水。
8、圆角的设计
塑角零件除了使用上要求采用尖角处外,其余所有转角处均应尽可能采用圆角过度,因塑胶 件的尖角处易产生应力集中,在受力戒冲击震动时会发生开裂现象。甚至在脱模过程中就发生开 裂。一般推荐加工圆角用如下原则:
1.4 缺胶、不饱模 塑胶熔体未完全充满型腔。
1.5 毛边、批锋 塑胶熔体流入分模面戒镶件配合面将发生锁模力足够,但在主浇道不分 流道会合处产 生薄膜状多余胶料为
1.6 烧焦 一般所谓的烧焦,包括制品表面因塑胶降解导致的变色及制品的填充末端焦黑的现象; 烧焦是指滞留型腔内的空气在塑料熔体填充时未能迅速排出(困气),被压缩而显著升 温,将材料烧焦。
- 1、下载文档前请自行甄别文档内容的完整性,平台不提供额外的编辑、内容补充、找答案等附加服务。
- 2、"仅部分预览"的文档,不可在线预览部分如存在完整性等问题,可反馈申请退款(可完整预览的文档不适用该条件!)。
- 3、如文档侵犯您的权益,请联系客服反馈,我们会尽快为您处理(人工客服工作时间:9:00-18:30)。
编辑课件
4
四,保证尺寸精度的设计
1.首先应认识到塑料制品的尺寸精度不同于金属零件的尺寸精度,因为影响塑料制品精度 的原因很多。主要有:
a、塑料的热膨胀系数大 b、塑料有成型收缩性; c、塑料制品会发生时效变化(后收缩); d、塑料制品的尺寸受湿度影响; e、塑件中部分尺寸精度很难由模具零件的精度保证;f、塑料制品的精度受模滇具制造精 度的影响。
编辑课件
6
五、确保制品强度的设计
增加制品强度的具体措施是:
1、设加强筋。加强筋能有效地达到增加制品的刚性和强 度的目的,它比单纯增加壁厚更经济合理。大平面的制 品上加强筋还有防止翘曲的功能。 为了更好地起到加强效果,设计加强筋须注意: a.加强筋的高度不要超过壁厚的3倍 b.加强筋底部的宽度不能超过壁厚的2/3, c.加强筋上设计2~5度的出模斜度; d.两条加强筋之间的距离不得小于两倍壁厚。
编辑课件
5
五、确保制品强度的设计
塑料制品的缺点是刚性差,设计塑件时应预先考虑到变形和开裂问题。确保制品强度的原则是: 1.勿使制品的壁太薄 2.去除尖角 3.调查所采用的塑料在低温状态下的抗冲击强度,事实上,塑件件常在冬季出现强度问题 4.冲出试验方式应接近制品的实际使用情况,如用跌落试验或落球冲击试验
从画制品的设计草图,构思制品的造型开始,就应考虑到能否成型问题。在此过程中,有关的技术同题应经常 同塑料工艺员和模具设计技术人员联系。 3.详细地记录制品的使用环境和使用要求以及装配情况并制成检验表,以便最后阶段检验所设计的制品是否符合 用户要求。 4.选择塑料品种
以检验表内制品的必需特性为中心,结合其他因素(如成本等)一起考虑,选定塑料品种。 5.由制品的外观、形状.尺寸精度,材料、批量、交货期、成本等约束条件确定成型加工方法与二次加工方法 6.确定分型线
2.影晌塑料制品尺寸精度的主要因索有3个方面: a、模具制造误差占50%; b、成型条件变化占30%; c、材料批量间及批量内误差占20%。
3.塑件上的某些高精度尺寸不能靠模塑成型达到,如与金属轴配合的轴孔尺寸,必须用金 属轴套以嵌件形式埋入塑件,用塑料与金属相组合的方法,既能保证某部分的尺寸精度,又 能提高生产效率,经济效益十分明显。塑料同金属结合时,出于两种材料的热膨胀系数差异 (聚苯乙烯的线胀系数是7×10-5/℃,铝是4×10-8/℃),要防止温度剧烈变化时发生应力裂纹。
注塑件结构设计
主讲人:冯高华
编辑课件
1
一、塑料制品设计的基本条件
1、尽可能详细地记录制品使用条件,这些条件有:
使用环境。室外情况(日光、雨,冰雪、灰尘),光照(紫外线、放射线等),接触气体 (腐蚀性气体、水蒸气),接触液体(水,洗涤剂、油、药品等),其他(增塑剂、铜);
使用强度。常用温度、最高温度、最低温度(平时、特殊情况、室外、仓库、橱窗、 汽车内等),冷热反复
设计制品时要考虑到壁厚的均匀性,冷却时间是由最大壁厚决定的。壁太厚不仅冷却时间太长,而且容易缩瘪。 而薄壁的问题是强度不足易开裂和成型困难,在合理的范围内,壁越薄越好。 11.圆角连接
无论是从防止塑件开裂,还是从模具制造角度考虑,都不允许制品上有尖角。各个面用圆角连接后可避免应力集 中,能改能改善熔料的流动性。
编辑课件
3
三、注重制品外观的设计
制品结构设计中,从外观角度须重点考虑避免缩瘪, 缩瘪是塑料注射成型中外观质量最大的问题,防止缩瘪的 设计条件:
•塑料制品壁厚一般为:电子工程类壳体2.5~3 mm,日用品壳体 1.5~2 mm,而薄壁类壳体0.5~0.8 mm(不宜太厚,否则会影响 加工效率) •统一壁厚,改变壁厚悬殊的设计,通过设计工艺孔等手段均匀壁厚; •减薄特别厚的部位; •模拟熔料流态,改进妨碍熔料流动的部位(薄壁部); •为增加塑料制品的强度和刚度又防止变形,常采用加强筋的办法, 筋板的厚度为0.5~0.8 mm左右 •加强筋和凸台的对应表面容易出现缩瘪,设计时须注意。
以制品的最大直径处设分型线。以分型线为界限设计出模斜度,分型线的形状越简单越好。分型线确定之后, 模具的基本结构也大致确定,分型线同模具制造和成型加工的关系相当密切。 8.制品顶出方法
首先考虑从哪个方向顶出。顶杆痕迹应设在不影响制品外观的位置;不允许有顶杆痕迹的制品不能用顶秆顶出 方式,应考虑用其他脱模方式。一般顶出机构都设在动模内,根据制品的 形状全自动成型中,为保证 制品可靠出模,必须在制品设计阶段就考虑好顶出方法。 9.拔模斜度 为了提高生产效率和合格率,制品上要设计拔模斜度,拔模斜度一般为1/40.侧面不允许有出模斜度的精密塑料 制品,须采用滑块抽芯的方法,把无斜度的面做在滑块上,启模后先松开滑块,再顶出制品。 10.壁厚
使用负载。常用负载、最大负载(平时、特殊情况.静态、动态、反复、持续、冲击、 跌落等)。
2、装配情况
制品如何安装和使用,有哪些需控制的关键尺寸,同哪些相关零件配合,配合程度 如何。
3、二次加工要求
塑料成型后还要进行哪些后加工,涂漆、粘结、印刷、烫印、电镀等。
编辑课件
2
二、制品设计程序
1.制品策划
打新品计划报告时,已决定采用塑料材料了,新品开发报告主要商讨塑料的性质与成型加工问题。 2.制品构思
2、圈角连接。塑料制品中,尖角处发生开裂的情况很多 ,原因是注射过程中,熔料在尖角处的流态急剧变化而 产生大的应力,而且残留在尖角处。设计加强筋的目的 是为了起加强作用,如果加强筋的底部不是圆角,则加 强筋不仅起不到加强作用,反而会降低制品的强度。除 了镶拼型芯及分型面等模具结构的原因之外,其他的各 个面都应当用圆角连接。圆角大小的确定,设壁厚为T圆 角的半径为R则R/T≥O.25。
编辑课件
7
五、确保制品强度的设计
增加制品强度的具体措施是:
3.确定安全系数。以拉伸强度为基准的安全系数在静负 载作用下以钢为3,塑料为10。尽管塑料的安全系数定得 很大,但由于分子定向等原因,制品各部分的强度相差 很大,安全系数取大些为好。