注塑件结构设计要点
注塑结构设计注意要点
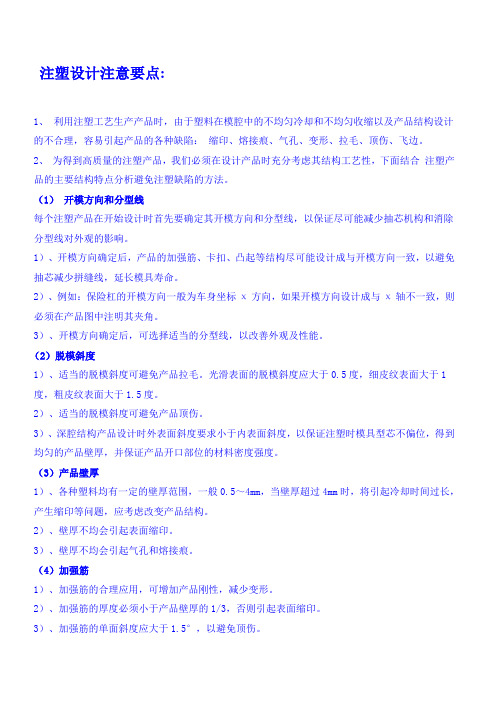
注塑设计注意要点:1、利用注塑工艺生产产品时,由于塑料在模腔中的不均匀冷却和不均匀收缩以及产品结构设计的不合理,容易引起产品的各种缺陷:缩印、熔接痕、气孔、变形、拉毛、顶伤、飞边。
2、为得到高质量的注塑产品,我们必须在设计产品时充分考虑其结构工艺性,下面结合注塑产品的主要结构特点分析避免注塑缺陷的方法。
(1)开模方向和分型线每个注塑产品在开始设计时首先要确定其开模方向和分型线,以保证尽可能减少抽芯机构和消除分型线对外观的影响。
1)、开模方向确定后,产品的加强筋、卡扣、凸起等结构尽可能设计成与开模方向一致,以避免抽芯减少拼缝线,延长模具寿命。
2)、例如:保险杠的开模方向一般为车身坐标χ方向,如果开模方向设计成与χ轴不一致,则必须在产品图中注明其夹角。
3)、开模方向确定后,可选择适当的分型线,以改善外观及性能。
(2)脱模斜度1)、适当的脱模斜度可避免产品拉毛。
光滑表面的脱模斜度应大于0.5度,细皮纹表面大于1度,粗皮纹表面大于1.5度。
2)、适当的脱模斜度可避免产品顶伤。
3)、深腔结构产品设计时外表面斜度要求小于内表面斜度,以保证注塑时模具型芯不偏位,得到均匀的产品壁厚,并保证产品开口部位的材料密度强度。
(3)产品壁厚1)、各种塑料均有一定的壁厚范围,一般0.5~4mm,当壁厚超过4mm时,将引起冷却时间过长,产生缩印等问题,应考虑改变产品结构。
2)、壁厚不均会引起表面缩印。
3)、壁厚不均会引起气孔和熔接痕。
(4)加强筋1)、加强筋的合理应用,可增加产品刚性,减少变形。
2)、加强筋的厚度必须小于产品壁厚的1/3,否则引起表面缩印。
3)、加强筋的单面斜度应大于1.5°,以避免顶伤。
1)、圆角太小可能引起产品应力集中,导致产品开裂。
2)、圆角太小可能引起模具型腔应力集中,导致型腔开裂。
3)、设置合理的圆角,还可以改善模具的加工工艺,如型腔可直接用R刀铣加工,而避免低效率的电加工。
4)、不同的圆角可能会引起分型线的移动,应结合实际情况选择不同的圆角或清角。
塑料件结构设计要点

大略的汇总下结构中常见的问题注意点,期抛砖引玉,共同提高。
1、关于塑料零件的脱模斜度:一般来说,对模塑产品的任何一个侧面,都需有一定量的脱模斜度,以便产品从模具中顺利脱出。
脱模斜度的大小一般以0.5度至1度间居多。
具体选择脱模斜度注意以下几点:●塑件表面是光面的,尺寸精度要求高的,收缩率小的,应选用较小的脱模斜度,如0.5°。
●较高、较大的尺寸,根据实际计算取较小的脱模斜度,比如双筒洗衣机大桶的筋板,计算后取0.15°~0.2°。
●塑件的收缩率大的,应选用较大的斜度值。
●塑件壁厚较厚时,会使成型收缩增大,脱模斜度应采用较大的数值。
●透明件脱模斜度应加大,以免引起划伤。
一般情况下,PS料脱模斜度应不少于2.5°~3°,ABS及PC料脱模斜度应不小于1.5°~2°。
●带皮纹、喷砂等外观处理的塑件侧壁应根据具体情况取2°~5°的脱模斜度,视具体的皮纹深度而定。
皮纹深度越深,脱模斜度应越大。
结构设计成对插时,插穿面斜度一般为1°~3°(见后面的图示意)。
2、关于塑件的壁厚确定以及壁厚处理:合理的确定塑件的壁厚是很重要的。
塑件的壁厚首先决定于塑件的使用要求:包括零件的强度、质量成本、电气性能、尺寸稳定性以及装配等各项要求,一般壁厚都有经验值,参考类似即可确定(如熨斗一般壁厚2mm,吸尘器大体为2.5mm),其中注意点如下:l塑件壁厚应尽量均匀,避免太薄、太厚及壁厚突变,若塑件要求必须有壁厚变化,应采用渐变或圆弧过渡,否则会因引起收缩不均匀使塑件变形、影响塑件强度、影响注塑时流动性等成型工艺问题。
l塑件壁厚一般在1—5mm范围内。
而最常用的数值为2—3mm。
l常用塑料塑件的最小壁厚及常用壁厚推荐值:(mm)l尽量不要将加强筋和螺钉柱设计的太厚,一般建议取本体壁厚的一半较保险,否则容易引起缩影等外观问题●尽量不要将零件设计成单独的平板,尺寸很小另论,否则变形导致零件不平整3、关于塑件的加强:为了确保塑件的强度和刚性,而又不致使塑件的壁厚过厚,可以在塑件的适当部位设置加强筋。
注塑件模具设计应注意的几大要点

注塑件模具设计应注意的几大要点模具工业是制造业中的一项基础产业,是技术成果转化的基础,同时本身又是高新技术产业的重要领域,在欧美等工业发达国家被称为“点铁成金”的“磁力工业”。
美国工业界认为“模具工业是美国工业的基石”;德国则认为它是所有工业中的“关键工业”;日本模具协会也认为“模具是促进社会繁荣富裕的动力”,同时也是“整个工业发展的秘密”,是“进入富裕社会的原动力”。
一、开模方向和分型线每个注塑产品在开始设计时首先要确定其开模方向和分型线,以保证尽可能减少抽芯滑块机构和消除分型线对外观的影响。
1、开模方向确定后,产品的加强筋、卡扣、凸起等结构尽可能设计成与开模方向一致,以避免抽芯减少拼缝线,延长模具寿命。
2、开模方向确定后,可选择适当的分型线,避免开模方向存在倒扣,以改善外观及性能。
二、脱模斜度1、适当的脱模斜度可避免产品拉毛(拉花)。
光滑表面的脱模斜度应≥0.5度,细皮纹(砂面)表面大于1度,粗皮纹表面大于1.5度。
2、适当的脱模斜度可避免产品顶伤,如顶白、顶变形、顶破。
3、深腔结构产品设计时外表面斜度尽量要求大于内表面斜度,以保证注塑时模具型芯不偏位,得到均匀的产品壁厚,并保证产品开口部位的材料强度。
三、产品壁厚1、各种塑料均有一定的壁厚范围,一般0.5~4mm,当壁厚超过4mm时,将引起冷却时间过长,产生缩印等问题,应考虑改变产品结构。
2、壁厚不均会引起表面缩水。
3、壁厚不均会引起气孔和熔接痕。
四、加强筋1、加强筋的合理应用,可增加产品刚性,减少变形。
2、加强筋的厚度必须≤(0.5~0.7)T产品壁厚,否则引起表面缩水。
3、加强筋的单面斜度应大于1.5°,以避免顶伤。
五、圆角1、圆角太小可能引起产品应力集中,导致产品开裂。
2、圆角太小可能引起模具型腔应力集中,导致型腔开裂。
3、设置合理的圆角,还可以改善模具的加工工艺,如型腔可直接用R刀铣加工,而避免低效率的电加工。
4、不同的圆角可能会引起分型线的移动,应结合实际情况选择不同的圆角或清角。
汽车注塑件(塑料件)设计时需要遵循的14个基本原则

(2)拔模角和高度 通常,筋的拔模角在1-1.5度,最小不能小于0.5度,否则会导致零件脱模困
难。越高的筋顶部往往很薄,导致注塑过程中难以充满也就失去了筋的意义。筋 的顶端厚度一般不低于1毫米,高度一般为零件壁厚的2.5-3倍。当然也会有例外, 需要具体分析。
0.5 deg min 筋厚
Байду номын сангаас
1 min 壁厚
D min D min
塑料件中的柱销也是我们常用到的结构,主要用于提供连接和定位。 • 设计要点:
(1)像筋的设计一样要考虑拔模角度、出模方向、根部厚度与基本壁厚的比 例等。
(2)另外,我们还有一个相互矛盾的问题需要考虑。一方面,我们希望销柱 的厚度(B)尽量薄些,以防止表面出现缩痕。另一方面,我们希望其厚度能厚 一些,以增加结构强度。最终,我们要根据产品结构和材料等综合分析确定。
塑料件翻边结构十分重要,它能够明显提高制件的结构刚度控制变形,是很 有用的结构,我们设计时必须尽量考虑增加翻边结构。 • 设计要点:
(1)翻边的厚度应该与基本壁厚一致。 (2)考虑到零件花纹,我们对翻边的拔模角度有特殊的要求,一般在3-6度之 间。但是不同的花纹会有不同的要求,设计时应根据花纹要求及制造和质量要求 选择适当的拔模角。
P/L P/L
8 有许多种类型的花纹可以用于零件表面的装饰。我们设计时需要针对不同的
花纹选择合适的设计结构。 • 设计要点:
(1)拔模角—总的规则是每增加0.025毫米的花纹深度,需要增加至少1度的拔 模角。关于花纹和拔模角需要设计者和花纹供应商共同检查和确认,并得到 OEM的认可。
(2)翻边—对于翻边结构,花纹和拔模角的关系是最突出的。翻边结构就需 要一定的脱摸角度,以便零件从模具内移出。越长的翻边需要越大的脱模角度, 越深的花纹,也需要越大的脱模角度。如果不注意这点就会产生零件脱模困难, 甚至擦伤零件花纹表面。
注塑件结构设计要点

三、塑料的成形方式
一般来说塑料的成型方法有以下几种:注射成型、挤压成型、压铸成型、 发泡、吹塑、真空吸塑、中空成型、机加工等,本文只对注射成型进行分 析。
注塑成型
将颗粒状或粉末状塑料置于注射机料筒内加热,使其熔融后用推杆或旋转 螺杆施加压力,使料筒内的胶料丛喷嘴和模具的浇注系统注射到模具型腔 中冷却成型的方法。详见下图1、图2.
一、什么是塑料
塑料是四大工程材料(钢铁、木材、水泥和塑料)之一,它是以备高注分
子量的合成树脂为主要成份,广泛应用于工业、农业、国防等行业。但是
塑料与其它材料相比又具有自己的一些特有的性能,这些性能决定它的一 些特有的使用场合、加工方法、生产工艺等。
二、塑料的分类
1、塑料按照受热属性分类,分为热固性和热塑性两种,区分两种塑料的 规则一般是在一定温度加热一段时间或加入硬化剂后有无发生化学反应而 硬化,发生化学反应而硬化的叫热固性塑料,反之则叫热塑性塑料。
图7加强筋缩水部位
图6加强筋
从图6的分析中可以看出筋要的厚度应尽量减小,但这也是有限制的。 如筋的厚度太小就必须增加筋的高度以增加刚度。筋太薄受压时筋容易变形、
成型时料不易填满、粘模等问题。当然筋底圆角半径也不能太小,否则就起 不到减小应力集中的作用。
一般来说,筋根圆角半径应不小于筋厚的40%,筋厚应是基料壁厚的 50%~75%之间,高的比值仅限小收缩率的材料。筋的高度应该小于基料厚 的五倍。筋上必须有脱模角且必须置于顺脱模的方向上或者采用活动模具组 件。筋与筋之间的间距必须大于基料厚的两倍。
拔模角的大小没有一个定数,通常是根据经验值确定。一般来说, 高度抛光的外壁可使用1/8度或1/4度的出模角,深入或附有织纹的产品 要求出模角作相应的增加,习惯上每0.025mm深的织纹,便需要额外1度 的出模角。
注塑 零件设计 要点

注塑零件设计要点
1. 嘿,你知道注塑零件设计的要点之一是什么吗?那就是尺寸精度啊!就好比盖房子要把每块砖都放对位置,注塑零件的尺寸精度要是不达标,那可不行呀!想象一下,一个本该严丝合缝的零件,却大了或小了那么一点点,整个产品不就出问题啦!所以尺寸精度可得把握好咯!
2. 注塑零件设计,材料选择超重要的呀!这就像选队友,得选个靠谱的。
比如说,如果你要做个耐磨损的零件,却选了个软趴趴的材料,那不是白搭嘛!不同的材料有不同的特性,咱可不能瞎选,得根据需求来,是不是这个理儿?
3. 哇哦,还有一个要点可不能忽视,那就是结构设计!这就像是搭积木,得有合理的架构。
你想想看,如果一个零件的结构设计得不合理,可能就容易变形、破裂。
比如说设计了个特别薄的地方,那能经得住折腾吗?所以结构设计一定要精心考虑呀!
4. 注塑零件设计的脱模斜度也很关键呐!这就像要让一个东西顺利滑出来一样。
如果脱模斜度不够,零件被卡在里面,那可就麻烦啦!这可不是好玩的,咱得把这个考虑进去,让零件能够轻轻松松地出来,是不是呀?
5. 嘿呀,别忘了表面质量这个要点呀!就像人的脸一样,要干净光滑。
要是一个注塑零件表面粗糙坑洼,那多难看呀,谁会喜欢呢!所以在设计的时候就得想好怎么让它的表面质量漂亮些,这很重要哦!
6. 最后一点哦,注塑零件设计的成本控制也不能马虎呀!这就好像过日子要算计着花钱一样。
如果设计的时候不考虑成本,那最后成本太高,可就得不偿失啦!所以要在保证质量的前提下,尽量降低成本,这才是明智之举呀!
我的观点结论就是:注塑零件设计的这些要点都非常重要,每一个都不能小瞧,得认真对待,这样才能设计出高质量的注塑零件。
塑料件结构设计要点
产品开发的结构设计原则:a、结构设计要合理:装配间隙合理,所有插入式的结构均应预留间隙;保证有足够的强度和刚度(安规测试),并适当设计合理的安全系数。
b、塑件的结构设计应综合考虑模具的可制造性,尽量简化模具的制造。
c、塑件的结构要考虑其可塑性,即零件注塑生产效率要高,尽量降低注塑的报废率。
d、考虑便于装配生产(尤其和装配不能冲突)。
e、塑件的结构尽可能采用标准、成熟的结构,所谓模块化设计。
f、能通用/公用的,尽量使用已有的零件,不新开模具。
g、兼顾成本大略的汇总下结构中常见的问题注意点,期抛砖引玉,共同提高。
1、关于塑料零件的脱模斜度:一般来说,对模塑产品的任何一个侧面,都需有一定量的脱模斜度,以便产品从模具中顺利脱出。
脱模斜度的大小一般以0.5度至1度间居多。
具体选择脱模斜度注意以下几点:a、塑件表面是光面的,尺寸精度要求高的,收缩率小的,应选用较小的脱模斜度,如0.5b、较高、较大的尺寸,根据实际计算取较小的脱模斜度,比如双筒洗衣机大桶的筋板,计算后取0.15 ° ~0.2 °。
c、塑件的收缩率大的,应选用较大的斜度值。
d、塑件壁厚较厚时,会使成型收缩增大,脱模斜度应采用较大的数值。
e、透明件脱模斜度应加大,以免引起划伤。
一•般情况下,PS料脱模斜度应不少于 2.5 °~3°,ABS及PC料脱模斜度应不小于1.5 ° ~2°。
f、带皮纹、喷砂等外观处理的塑件侧壁应根据具体情况取2° ~5°的脱模斜度,视具体的皮纹深度而定。
皮纹深度越深,脱模斜度应越大。
g、结构设计成对插时,插穿面斜度一般为1° ~3°(见后面的图示意)。
2、关于塑件的壁厚确定以及壁厚处理:合理的确定塑件的壁厚是很重要的。
塑件的壁厚首先决定于塑件的使用要求:包括零件的强度、质量成本、电气性能、尺寸稳定性以及装配等各项要求,一般壁厚都有经验值,参考类似即可确定(如熨斗一般壁厚2mm吸尘器大体为2.5mm),其中注意点如下:a、塑件壁厚应尽量均匀,避免太薄、太厚及壁厚突变,若塑件要求必须有壁厚变化,应采用渐变或圆弧过渡,否则会因引起收缩不均匀使塑件变形、影响塑件强度、影响注塑时流动性等成型工艺问题。
注塑结构设计基础知识
注塑结构设计基础知识
嘿,朋友们!今天咱就来好好聊聊注塑结构设计基础知识。
注塑结构设计啊,就好比是搭积木,你得把各种小零件巧妙地组合在一起,才能搭出漂亮又坚固的“城堡”!比如说做一个塑料杯子,这不就得从它的形状、厚度这些方面好好琢磨嘛!
注塑结构设计可不是一件简单的事儿啊!你得考虑材料的特性,就像不同性格的人,得用不同的方式对待。
比如有些塑料很脆,你设计的时候就得小心别让它容易断了呀。
然后呢,还有模具的问题。
模具就像是一个模子,你得把注塑材料倒进去,让它成型。
要是模具设计得不好,那出来的东西可就歪七扭八了!比如说你想做个方方正正的盒子,结果模具不行,出来个奇形怪状的东西,这多糟心啊!
再来说说结构的合理性。
你看那汽车零件,设计得合理才能既轻便又结实,这注塑结构设计不也是一样的道理嘛!你总不能弄个不合理的结构,让东西用着用着就散架了吧?
还有啊,别忘了考虑成本呢!要是成本太高,那做出来的东西谁买得起呀!这就像是去菜市场买菜,你也得货比三家,找个性价比高的呀。
注塑结构设计真的超级重要啊!它能决定一个产品的质量、美观和实用性。
咱可不能小瞧了它!所以啊,朋友们,好好钻研注塑结构设计基础知识吧,让我们一起创造出更多又棒又实用的东西来!这就是我的观点,别犹豫,赶紧行动起来吧!。
注塑件设计要点
注塑件设计要点1 、开模方向和分型线每个注塑产品在开始设计时首先要确定其开模方向和分型线,以保证尽可能减少抽芯机构和消除分型线对外观的影响。
开模方向确定后,产品的加强筋、卡扣、凸起等结构尽可能设计成与开模方向一致,以避免抽芯减少拼缝线,延长模具寿命。
例如:保险杠的开模方向一般为车身坐标χ方向,如果开模方向设计成与χ轴不一致,则必须在产品图中注明其夹角。
开模方向确定后,可选择适当的分型线,以改善外观及性能。
2 、脱模斜度适当的脱模斜度可避免产品拉毛。
光滑表面的脱模斜度应大于0.5度,细皮纹表面大于1度,粗皮纹表面大于1.5度。
适当的脱模斜度可避免产品顶伤。
深腔结构产品设计时外表面斜度要求小于内表面斜度,以保证注塑时模具型芯不偏位,得到均匀的产品壁厚,并保证产品开口部位的材料密度强度。
3 、产品壁厚各种塑料均有一定的壁厚范围,一般0.5~4mm,当壁厚超过4mm时,将引起冷却时间过长,产生缩印等问题,应考虑改变产品结构。
壁厚不均会引起表面缩印。
壁厚不均会引起气孔和熔接痕。
4 、加强筋加强筋的合理应用,可增加产品刚性,减少变形。
加强筋的厚度必须小于产品壁厚的1/3,否则引起表面缩印。
加强筋的单面斜度应大于1.5°,以避免顶伤。
5、圆角圆角太小可能引起产品应力集中,导致产品开裂。
圆角太小可能引起模具型腔应力集中,导致型腔开裂。
设置合理的圆角,还可以改善模具的加工工艺,如型腔可直接用R刀铣加工,而避免低效率的电加工。
不同的圆角可能会引起分型线的移动,应结合实际情况选择不同的圆角或清角。
6 、孔孔的形状应尽量简单,一般取圆形。
孔的轴向和开模方向一致,可以避免抽芯。
当孔的长径比大于2时,应设置脱模斜度。
此时孔的直径应按小径尺寸(最大实体尺寸)计算。
盲孔的长径比一般不超过4。
孔与产品边缘的距离一般大于孔径尺寸。
7 、注塑模的抽芯机构及避免当塑件按开模方向不能顺利脱模时,应设计抽芯机构。
抽芯机构能成型复杂产品结构,但易引起产品拼缝线,缩印等缺陷,并增加模具成本缩短模具寿命。
塑胶模具结构设计要点
塑胶模具结构设计要点1.极坐标原则:塑胶模具结构设计先确定要制作的塑件形状和尺寸,根据塑件的形状和尺寸确定模具的轮廓线形。
轮廓线形可用赫曼H曲线进行设计。
模具的开模方向应尽量与塑件的最大轮廓线形相垂直,以便于塑料注入时的填充和排气。
2.模具的完整性:塑胶模具设计要保证模具结构的完整性,所有零部件安装框架结构要紧凑,布局合理,尽量减少模具的整体尺寸。
模具的底板和基础要够厚实,以便于承受注塑过程中的压力和热应力。
3.模腔的设计:塑胶模具的模腔设计要满足塑件的形状和尺寸要求,注意避免模腔中出现深浅不一的地方,以免造成填充不均匀和塑件变形。
模腔的表面质量要求高,尽量避免切削、铣削等加工,以减少模腔的表面粗糙度。
4.模具的冷却系统设计:塑胶模具在注塑过程中会产生大量的热量,冷却系统的设计对模具的使用寿命和生产效率有重要影响。
冷却系统应尽量覆盖整个模具,确保模腔中的塑料在注塑过程中均匀冷却,防止产生内应力和变形。
冷却水的供给要充分,流速要适宜,冷却水口要布置合理,以确保整个模具的冷却效果。
5.浇口和排气系统设计:浇口的设计应考虑塑料的流动性和塑件的外观要求,浇口位置要选择在模具的最厚点或处于最大壁厚改变处,以保证注塑过程中的充填和射出平稳。
排气系统的设计要保证塑料在充填过程中的排气畅通,避免产生气泡或虚线。
6.抽芯装置设计:塑胶模具中的一些塑件需要采用抽芯装置进行成型,抽芯装置的设计要满足塑件的形状和尺寸要求,确保塑件在脱模过程中不变形或损坏。
抽芯装置的操作要方便,可靠,要考虑到抽芯力和脱模力的大小,以确保抽芯的顺畅和模具的寿命。
7.快速更换系统设计:塑胶模具在生产过程中需要频繁更换不同的模腔,快速更换系统的设计能够极大地提高模具的使用效率和生产效率。
快速更换系统要求模腔结构尽量简单,易于拆卸和装配,以及固定方式的可靠性。
8.模具的加工工艺:塑胶模具的制作工艺要选择合适的材料和加工工艺,以确保模具的成型精度和表面质量。
- 1、下载文档前请自行甄别文档内容的完整性,平台不提供额外的编辑、内容补充、找答案等附加服务。
- 2、"仅部分预览"的文档,不可在线预览部分如存在完整性等问题,可反馈申请退款(可完整预览的文档不适用该条件!)。
- 3、如文档侵犯您的权益,请联系客服反馈,我们会尽快为您处理(人工客服工作时间:9:00-18:30)。
注塑件结构设计要点吕文果塑料是四大工程材料(钢铁、木材、水泥和塑料)之一,它是以高分子量的合成树脂为主要成份,在一定条件下可塑制成一定形状且在常温下保持形状不变的材料。
塑料总体分为热固性和热塑性两种,区分两种塑料的规则一般是在一定温度加热一段时间或加入硬化剂后有无发生化学反应而硬化,发生化学反应而硬化的叫热固性塑料,反之则叫热塑性塑料。
它广泛应用于工业、农业、国防等行业。
但是塑料与其它材料相比又具有自己的一些特有的性能,这些性能决定它的一些特有的使用场合、加工方法、生产工艺等。
一般来说塑料的成型方法有以下几种:注射成型、挤压成型、压铸成型、发泡、吹塑、真空吸塑、中空成型、机加工等。
由于塑料的种类及性能、使用场合、成型工艺等条件的影响,对塑料件的结构设计也就自然会产生一些特殊的要求及方法。
由于热固性塑料与热塑性塑料最终的形态不同,结构设计过程中的好多要求也就不一样,涉及的范围相当之大。
下面我们就针对注射成型的热塑性塑料件的结构设计从胶模斜度、塑件的壁厚、加强筋、支承柱、孔、公差等方面作一些初略的讨论。
一、 壁厚合理确定塑件的壁厚是非常重要的,其它的形体和尺寸如加强筋和圆角等都是以壁厚为参照的。
塑料产品的壁厚主要决定于塑料的使用要求,即产品需要承受的外力、是否作为其他零件的支撑、承接柱位的数量、伸出部份的多少以、选用的塑胶材料、重量、电气性能、尺寸稳定性以及装配等各项要求而定。
如果壁厚不均匀,会使塑料熔体的充模速度和冷却收缩不均匀,由此会引起凹陷、真空泡、翘曲、甚至开裂。
壁厚均匀是塑料件设计的一大原则。
一般的热塑性塑料壁厚设计在1~6mm范围。
最常用的为2~3mm。
大型件也有超过6mm的。
表1是一些热塑性塑料壁厚的推荐值。
在取较小壁厚时,要考虑制品在使用和装配时的强度和刚度。
从经济角度来看,过厚的产品不但增加物料成本,还延长生产周期。
尽量使塑件各处的壁厚均匀,否则会引起收缩不均匀使塑件产生变形和气泡、凹陷的工艺问题。
厚胶的地方比旁边薄胶的地方冷却得慢,因而产生缩痕。
更甚者导致产生缩水印、热内应力、挠曲部份歪曲、颜色不同或不同透明度。
若厚胶的地方渐变成薄胶的是无可避免的话,应尽量设计成渐次的改变,并且在不超过壁厚3:1的比例下,如下图1:图1其实大部份厚胶的设计可使用加强筋来改变总壁厚。
除了可节省物料来节省生产成本外,还可以节省冷却时间,冷却时间大概与壁成正比。
取缔后的设计更可保留和原来设计相近的刚性、强度及功用,关于加强筋我们会在后面的章节中专门讨论。
此外壁厚的设计还要考虑流程,即熔料从浇口起流向型腔各处的距离。
一般工艺参数下流程与壁厚有一定的比例关系,壁厚越大流程越长,如果流程与壁厚的比值太大,离浇口远的地方就会出现缺料也就是常说的打不饱。
因此必要的情况下还需增加壁厚。
表1 热塑性塑料制品的最小壁厚及常用壁厚的推荐值塑料材料 最小壁厚 小型件推荐壁厚 中型件推荐壁厚大型件推荐壁厚尼龙 0.45 0.76 1.5 2.4~3.2聚乙烯 0.6 1.25 1.6 2.4~3.2聚苯乙烯 0.75 1.25 1.6 3.2~5.4 PMMA 0.8 1.5 2.2 4~6.5 PVC 1.2 1.6 1.8 3.2~5.8 PP 0.85 1.54 1.75 2.4~3.2 PC 0.95 1.8 2.3 3~4.5 POM 0.8 1.4 1.6 3.2~5.4 ABS 0.8 1 2.3 3.2~6 尖锐的角位通常会导致部件有缺陷及应力集中,尖角的位置亦常在电镀过程后引起不希望的物料聚积。
集中应力的地方会在受负载或撞击的时候破裂。
较大的圆角提供了这种缺点的解决方法,不但减低应力集中的因素,且令流动的塑料流得更畅顺和成品脱模时更容易。
下图可供叁考之用。
如果内角是圆角,外角是尖角,转角的地方仍比其它地方厚,仍会出现收缩的现象;我们可以使内外都成圆角,来使壁厚均匀,这种情况下外圆角是内圆角加上基本壁厚之和。
转角位的设计准则亦适用于悬梁式扣位。
因这种扣紧方式是需要将悬梁臂弯曲嵌入,转角位置的设计图说明如果转角弧位R 太小时会引致其应力集中系数过大,因此,产品弯曲时容易折断,弧位R太大的话则容易出现收缩纹和空洞。
因此,圆弧位和壁厚是有一定的比例。
一般介乎0.2至0.6之间,理想数值是在0.5左右。
二、脱模方向及拔模斜度每个注塑产品在开始设计时首先要确定其开模方向和分型线,以保证尽可能减少抽芯机构和消除分型线对外观的影响。
如汽车保险杠的脱模方向一般是沿车的长度方向。
开模方向确定后,产品的加强筋、卡扣、凸起等结构尽可能设计成与开模方向一致,以避免抽芯、减少拼缝线,延长模具寿命。
开模方向确定后,可选择适当的分型线,以改善外观及性能。
注塑件从成型模具中脱模运动时,要克服脱模力和开模力。
开模是指塑件外形从型腔中脱出。
模内塑件在冷却过程中产生收缩,孔壁部分对型芯产生包紧力。
开模时塑件与型芯产生摩擦力、孔底密封件开模时产生真空吸附,诸多原因说明脱模力比开模力大得多。
过大的脱模力会使塑件变形、发白、起皱和表面擦伤。
脱模斜度是决定脱模力大小的一大因素。
因注塑件冷却收缩后多附在凸模上,为了使产品壁厚均匀及防止产品在开模后附在较热的凹模上,出模角对应於凹模及凸模是应该相等的。
不过,在特殊情况下若然要求产品于开模后附在凹模的话,可将相接凹模部份的出模角适当减少,或刻意在凹模加上适量的倒扣位。
拔模角的大小没有一个定数,通常是根据经验值确定。
一般来说,高度抛光的外壁可使用1/8度或1/4度的出模角,深入或附有织纹的产品要求出模角作相应的增加,习惯上每0.025mm深的织纹,便需要额外1度的出模角。
出模角度与单边间隙和边位深度之关系表,列出出模角度与单边间隙的关系,可作为叁考之用。
此外在考虑脱模斜度时,原则上越大越有利于脱模,但必须注意保证塑件的尺寸精度,脱模斜造成的尺寸误差必须控制在尺寸精度范围内。
对于收缩较大,形状复杂的塑件应考虑较大的脱模角。
三、 加强筋塑料件的强度并不完全依其壁厚增加而增大。
相反,因为壁厚的增加引起收缩而产生内应力,反而降低其强度。
塑料件的强度以刚度为主,多采用薄壁风格组合结构,在相应部位设置加强筋,以提升截面惯性矩。
但是加了加强筋后,加强筋与主壁的连接处就一定会变厚,这个厚度通常取决于内切的最大圆,也就是取决于筋厚和根部的圆角半径。
如图3中,基料厚均为4mm,左图筋要部厚度为4mm,筋根圆角为R2.4,其最大内切圆直径为φ6.2;右图仅将筋厚变为2mm,筋根圆角半径改成R1.6,则最大内切圆直径变为φ4.9。
如图4由于局部壁厚增加,在其背面就容易产生收缩变形,影响塑件的外观,对于表面要求非常高的零件,如汽车外饰件,此类影响外观的缺陷是非常不允许的。
正确的设计可以减少组件形成表面凹痕的可能,以提高零件的质量。
从图3的分析中可以看出筋要的厚度应尽量减小,但这也是有限制的。
如筋的厚度太小就必须增加筋的高度以增加刚度。
筋太薄受压时筋容易变形、成型时料不易填满、粘模等问题。
当然筋底圆角半径也不能太小,否则就起不到减小应力集中的作用。
一般来说,筋根圆角半径应不小于筋厚的40%,筋厚应是基料壁厚的50%~75%之间,高的比值仅限小收缩率的材料。
筋的高度应该小于基料厚的五倍。
筋上必须有脱模角且必须置于顺脱模的方向上或者采用活动模具组件。
筋与筋之间的间距必须大于基料厚的两倍。
图3图4此外我们通常都希望一个零件在各个方向上都具有同样的刚性,获得这样结果的最简单的方法就是在零件的横向和纵向都加上筋,并使它们垂直相交。
但同时也会出现问题,就是在相交的地方会增加壁厚,增大收缩的机会。
一般这种情况可以在相交处加一圆孔以便形成均匀的壁厚。
如下图:图5四、 孔在塑胶件上开孔使其和其它部件相接合或增加产品功能上的组合是常用的方法,洞孔的大小及位置应尽量不会对产品的强度构成影响或增加生产的复杂性,以下是在设计洞孔时须要考虑的几个因素。
相连洞孔的距离或洞孔与相邻产品直边之间的距离不可少于洞孔的直径,如下图6。
图中尺寸关系原则上要求B≥A,C≥A。
特别靠边的C值应尽可能大一些,否则穿孔位置容易产生断裂的情况。
要是孔内附有螺纹,则螺孔与产品边沿的距离一般来说大于孔径的三倍。
图6孔的类型一般有通孔,盲孔和分级孔等。
从装配的角度来看,通孔的应用远较盲孔为多,而且较盲孔容易生产。
从模具设计的角度来看,通孔的设计在结构上也会方便一些,可以通过固定在动模和定模上的两个型芯结合来形成,也可以只固定在动模或定模上的一根型芯而成型。
前者在流体塑料的作用下形成两个悬臂梁,但力臂较短,变形不大。
后者与动模和定模都有搭接,一般来说形成简支梁,变形也不大。
应用两型芯成型时,两型芯的直径应稍有不同以避免因为两条边钉轴心稍有偏差而引致产品出现倒扣的情况,而且相接的两个端面必须磨平。
而盲孔的型芯则完全是悬臂梁,受到流体塑料的冲击后容易弯曲,成形的孔会变成异形孔,一般来说,盲孔的深度只限於直径的两倍。
要是盲孔的直径只有或小于1.5mm,盲孔的深度更不应大於直径的尺寸。
且盲孔的底部壁厚应不小于孔径的六分之一,否则会出现收缩。
侧孔往往是通过侧抽芯的方法成型,这会增加模具的成本,且如果侧芯太长的话容易断,增加模具维护费用。
如果情况允许的话可采用如下图7的方法加以改善。
图7五、 支柱支柱突出胶料壁厚是用以装配产品、隔开物件及支撑其他零件之用。
空心的支柱可以用来嵌入件、收紧螺丝等。
这些应用均要有足够强度支持压力而不致于破裂。
支柱一般做成圆柱形,因为圆柱易于模具成型,此外具有较好的力学性能。
一般来说支柱尽量不要设计成独立的圆柱外伸,应尽量连接至外壁或与加强筋一同使用,目的是加强支柱的强度及使胶料流动更顺畅,与外壁的连接需做成薄壁连接避免缩水,支柱的底部与基料的连接处需做出0.4到0.6倍基料厚的圆角半径。
支柱的壁厚应在0.5到0.75的基料厚之间,支柱的顶部内孔为方便安装螺钉导向应有倒角。
支柱上需有拔模斜度。
这几点都与加强筋的设计要求相类似,因此也可以说支柱是筋的变种。
以上相应关系请参见如下图8与图9.图8图9许多支柱凸台的作用是用来连接自攻螺钉,装配后支柱上的内螺纹是通过冷流加工形成的,冷流加工不产生料的切削,只是将塑料挤压变形来产生衔接的内螺纹。
螺纹支柱的尺寸要既能承受螺钉的旋入力又能承受附载,支柱上的孔径大小要能保证螺钉在特定扭矩及特定振动下不脱出,支柱的外径要能保证螺钉扭紧过程中承受所产生的周向力而不断裂、不破裂。
此外为了保证在自攻螺钉旋入导向的方便,一般在支柱的顶部开一凹坑,凹坑的直径应略大于螺纹的公称直径。
支柱的尺寸计算是非常繁杂的,在这推荐一种国外网站上的简单估算方法,这个方法的关键是螺钉的公称直径。
首先必须写出所用的材料,然后再从右边查出相应的系数,用螺钉的公称直径乘以相应的系数就能得出相应的尺寸。