喷涂参数要求
等离子喷涂参数的选择
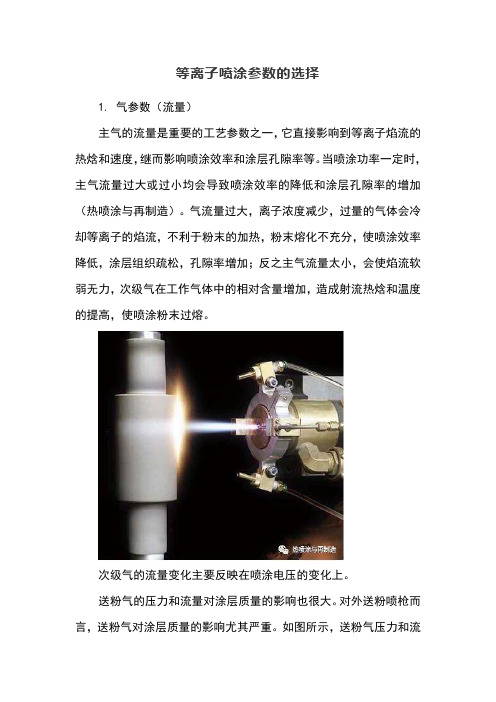
等离子喷涂参数的选择1. 气参数(流量)主气的流量是重要的工艺参数之一,它直接影响到等离子焰流的热焓和速度,继而影响喷涂效率和涂层孔隙率等。
当喷涂功率一定时,主气流量过大或过小均会导致喷涂效率的降低和涂层孔隙率的增加(热喷涂与再制造)。
气流量过大,离子浓度减少,过量的气体会冷却等离子的焰流,不利于粉末的加热,粉末熔化不充分,使喷涂效率降低,涂层组织疏松,孔隙率增加;反之主气流量太小,会使焰流软弱无力,次级气在工作气体中的相对含量增加,造成射流热焓和温度的提高,使喷涂粉末过熔。
次级气的流量变化主要反映在喷涂电压的变化上。
送粉气的压力和流量对涂层质量的影响也很大。
对外送粉喷枪而言,送粉气对涂层质量的影响尤其严重。
如图所示,送粉气压力和流量过小会使粉末难以到达焰流中心,过大则会使粉末穿过射流中心,产生严重的“边界效应”,致使涂层疏松,结合强度降低。
对于内送粉喷枪而言,送粉气压力和流量过大同样不能把粉末送入焰心,若过小,则易造成堵塞喷嘴,严重时则会烧坏喷嘴(热喷涂与再制造)。
若要很大送粉气压力和流量才能把粉末送入焰心,则须检查供粉系统的气密性,是否漏气。
所以送粉气的压力和流量应根据送粉量的大小、粉末的比重、粉末的流动性以及供粉系统的性能、射流的功率和刚性来选取。
(a) 送粉气压力和流量过大(b) 送粉气压力和流量正好(c) 送粉气压力和流量过小送粉气流量大小对送粉效果的影响2. 电参数(1)功率输入功率大小首先要满足能够将粉末熔化良好。
形成涂层的粉末所需的热功率应为:式中:Gf——单位时间的送粉量T0,Tm,Tr——粉末原始温度、粉末熔点和粉末过热的温度;Cs,Cm——粉末固态和熔态的比热;Hr——熔融粉末材料在Tr下的热焓增量。
根据等离子焰流能量利用系数ηf,可估算出喷嘴出口处等离子体的热功率qp:最后按喷枪效率η,可估算出所需输入的功率P:式中:0.24——电能转变为热能的系数一般来说,采用较高的功率值比较好。
喷涂质量标准分区橘皮等级要求

喷涂是一种常见的表面涂装工艺,其质量标准对于产品的外观和性能至关重要。
对于喷涂质量的要求一般包括涂层的厚度、平整度、附着力等多个方面。
而针对不同的产品和行业,对于喷涂质量的要求也有所不同。
本文将围绕喷涂质量标准分区橘皮等级要求展开讨论。
一、喷涂质量标准分区1. 根据产品的使用要求和行业标准,喷涂质量一般分为外观质量和性能质量两个方面。
2. 对于外观质量,喷涂涂层的平整度、色泽、光泽度等是重要的评定标准。
3. 对于性能质量,主要包括涂层的附着力、耐腐蚀性、耐磨性等指标。
4. 根据喷涂质量标准分区,产品可能被划分为不同的等级,如优质等级、一般等级和低质等级。
二、橘皮等级要求1. 在喷涂过程中,由于外部环境条件、涂装工艺等因素的影响,涂层表面可能出现橘皮现象。
2. 橘皮是指喷涂表面出现皱纹状、类似橘子皮纹理的缺陷,影响了涂层的平整度和外观。
3. 对于橘皮现象,通常会根据其程度划分为不同的等级,如轻微橘皮、中等橘皮和严重橘皮等级。
4. 橘皮等级要求会根据产品的使用要求和行业标准进行规定,不同行业可能对橘皮等级有不同的要求。
三、喷涂质量的影响因素1. 喷涂质量受到多种因素的影响,包括涂料的性能、喷涂工艺、喷涂设备、环境条件等多个方面。
2. 涂料的选择对于喷涂质量有着重要的影响,不同的涂料对橘皮现象的抵抗能力不同。
3. 喷涂工艺和设备的参数设置也会直接影响喷涂质量,如喷涂压力、喷涂速度、喷涂距离等。
4. 环境条件也是影响喷涂质量的重要因素,如温度、湿度、风力等都可能对喷涂产生影响。
四、改善喷涂质量的方法1. 选用合适的涂料材料,根据产品的使用要求和行业标准进行选择,确保涂料的性能符合要求。
2. 优化喷涂工艺,合理设置喷涂设备的参数,如调整喷涂压力、速度等,避免喷涂过程中产生橘皮。
3. 控制环境条件,保持喷涂环境的干燥、通风和恒温,避免外部因素对喷涂质量的影响。
4. 加强质量管理,建立健全的质量控制体系,对涂层质量进行全面监控和评定。
涂装工艺技术参数

涂装工艺技术参数一、施工环境条件1. 最佳施工环境条件为环境温度10-40℃,湿度30-70% 。
2. 空气湿度不得大于80%。
在湿度大于80%气候情况下,喷漆前需对工件进行烘烤,温度70-80℃(工件基体温度),保温时间30分钟。
3. 要求在配漆和施工环境中配置温度计和湿度计。
二、涂料调配(指加入固化剂后)1.按涂料技术参数进行调配。
2.涂料调配好后需进行过滤除去涂料中杂质,底漆用180目、中涂用180-240目、面漆用300-320目滤布过滤。
3.涂料调配后放置8-10分钟,使涂料熟化后再喷涂。
(此点需严格执行)4.涂料调配后应在4小时内使用完。
三、喷涂前准备工作1.工件在喷涂前应做到干净、干燥;施工场地保持清洁干净,喷漆室每天进行清扫,定期对喷漆室送风过滤棉清理干净。
2.采用空气喷涂时必须安装冷干机(或油水分离器),每天上午和下午各排放一次油、水,湿度大的季节,还需增加排放油、水次数,保证压缩空气无油和水份等杂质。
3.喷漆工和相关接触人员在工作中应做好劳动安全保护,穿戴防毒口罩、手套、工作服等劳保用品,防止吸入有毒溶剂、尘埃等。
四、底、面漆技术参数1. 大光黄底漆(1)稀释剂:茸康大光黄底漆稀释剂;(2)固化剂:进口固化剂;(3)配比:进口固化剂=4:1(重量比);(4)粘度:16-25秒;2. SPU70815P-Y黄色聚氨酯中涂(1) 稀释剂:RUT-085稀释剂(快干型,在15℃以下气温情况使用)或XPS90018溶剂(慢干型,15℃以上<含15℃>气温情况下使用);(2) 固化剂:GXH63417聚氨酯固化剂;(3) 配比: GXH63417聚氨酯固化剂=7:1(重量比);(4) 粘度:14-25秒;3. SPU70806T-Y聚氨酯面漆(或SPU70807T-GY聚氨酯面漆)(1) 稀释剂:RUT-085稀释剂(快干型,在15℃以下气温情况使用)或XPS90018溶剂(慢干型,15℃以上<含15℃>气温情况下使用);(2) 固化剂:GXH63417聚氨酯固化剂;(3) 配比: GXH63417聚氨酯固化剂=4:1(重量比);(4) 粘度:14-25秒;4.干燥:(1) 烘干温度需达到70-80℃(工件基体温度),保温时间30分钟;(2) 工件进烘干室前需流平8-10分钟;(3) 如常温自然干燥,干燥时间应大于24小时后才能开始涂刮腻子或喷涂面漆;5.漆膜厚度要求:(1) 底漆的干膜厚度应达到20- 35um;(2) 面漆的干膜厚度应达到40- 60um;(3) 涂膜总厚度:70μm≤磷化件≤100μm ,80μm≤抛丸喷砂件≤110μm;五、腻子刮磨1. 腻子桶打开后,观察腻子表面有无结皮,如有则去掉,然后将整桶腻子搅拌均匀;2. 严格按原子灰配比(一般为原子灰:固化剂=100:2-3)要求调配腻子,在气温高情况下,不能减少固化剂用量,而应适当减少每次原子灰调配量,并充分搅拌均匀颜色一致;3. 在刮涂腻子时应以工件表面为基准,刮平凹处,尽量使腻子薄而平整;4. 如存在较大凹坑,应分多次填刮,每次刮涂厚度不应超过1mm,且需在上道腻子干燥后进行;5. 腻子经干燥打磨后,整个表面应平整光滑,线角分明,腻子与涂层表面连接处不得有明显接痕,无漆粒等杂质附在工件表面上;6. 擦净:用压缩空气全面擦吹净后再用粘性纱布按一个方向擦净工件表面;。
喷涂参数要求

查
粒物。
测厚仪、目测
测量漆膜厚度
1、要求喷涂均匀,色差在 4 以内;
车厢外
2、喷涂无流挂、橘皮、颗粒物等缺 部中涂、
目测、采用专用仪器进
测量漆膜厚度、硬度、附
9
陷;
罩光喷
行测试
着力、光泽度
3、要求漆膜厚度、硬度、附着力光
涂
泽度按工艺执行。
1、空压系统压力:0.6-0.8MPa
车架喷
10
喷枪枪头距离工件:10-20cm;
附着力达到 1 级
硬度达到 1H
光泽度:>70Gs
3
小件 喷涂
喷涂完成
漆膜厚度:35±5μm 附着力达应达到 1 级
光泽度:≥50Gs
备注:此表一式二联,由品控课填写。
保存期:二年
3
序号 车型
不合格品记录及处理表
NO.:
问题描述
不合格数 生产总数
量
量
处理情况
责任课室 备注
保存期:二年
4
内部质量信息单
涂装检验规程
1 目的
通过对涂装生产过程各个工序的检验,使车架、车厢、零部件外表涂装质量,符合工艺技术规定。
2 范围
适用于车架、车厢、零部件外表涂装过程中产品质量的检验工作。
3 职责
3.1 品控课负责对公司生产的三轮车车架、车厢、零部件涂装生产过程及化验参数进行检验工作。
3.2 品控课负责对不合格项目进行汇总、分析、提出整改意见并验证整改实施效果。
专用仪器测试、目测
备注:带“★”检验项目为关重工序。
4.2 生产过程控制办法
4.2.1 检查各生产过程的各种测量数据、记录是否准确。
4.2.2 抽查后要如实填写巡检记录表。
喷涂前处理作业指导书

喷涂前处理作业指导书序号作业流程图说明注意事项1 1、除油如加热除油效果更佳。
2、没有锈的工件可以不除锈。
3、除油用料:RS102脱脂剂,RS108脱脂液。
4、技术参数:浓度配比:3-5%(RS102脱脂剂);1-2%(RS104脱脂液);槽液温度:常温-60℃(加温效果更好);除油时间:5-20分钟溶液碱度:18-50溶液PH值:10-14温度:常温时间:1-3分钟溶液PH值:5.5-8.51、经除油清洗后的工件表面挂水均匀,不能有分流及水珠现象。
2、脱脂后经清洗其工件表面无油污、锈蚀等。
3、及时清除浮于液面的油污等脏物。
4、每4小时检查调整一次液位,维持正常液位;每4小时测定一次碱度,按测定的碱度及时补充脱脂剂RS102、RS108脱脂液将碱度控制在规定范围内。
5、当除油槽使用时间太长,添加RS102脱脂剂、RS108脱脂液后,效果改善不大时,应更换。
6、清水洗槽中的水应保持干净,如保持溢流更好,确保溶液PH值在规定范围内。
7、对上述参数检测时,必须做好记录,并填入表格中。
中和槽是0.2%~1.0%纯碱水溶液。
中和的目的是中和掉工件上残留的酸,使清洗更加干净;1 1、表调用料型号:RS105表调剂。
2、技术参数:PH值:7.5-9.5温度:常温时间:0.5-1min浓度配比:2‰1、PH值小于7.5时,用表调剂RS105调整。
2、连续生产时,每处理500-1000m2,补加1-2kgR105表调剂。
3、长期使用后槽液会老化变差、变黄,补加后效果改善不大,应更换。
4、当PH值小于7.5时,胶体钛被沉淀,表调失效,应更换。
5、必须用清水溶解RS105表调后建浴或添加。
6、对上述参数进行检测时,做好记录,填入表格中。
31、磷化用料型号:RS309磷化剂,RS806促进剂。
2、技术参数:温度:常温-45℃;时间:5-12分钟溶液总酸度(TA):23-30溶液游离酸度(FA):1.8-3.5溶液促进剂(AC):1.0-4.01、每2小时测定各点值,及时补充药剂至规定范围,调整液面至规定范围。
油漆喷涂工艺质量控制标准

油漆喷涂工艺质量控制标准油漆喷涂工艺质量控制标准1. 背景介绍油漆喷涂工艺是一种常用的涂装方式,常用于汽车、家具、建筑等行业。
为了保证喷涂质量和客户满意度,需要制定相应的工艺质量控制标准。
2. 喷涂工艺参数喷涂压力:推荐使用压力表进行调节,喷枪出口压力应在指定范围内。
喷涂距离:距离涂装目标物表面应保持恒定的距离,以确保喷涂均匀。
喷涂方式:可采用交叉喷涂、罩面喷涂等方式,根据具体情况进行选择。
喷涂速度:控制喷涂速度,避免过快或过慢造成涂层不均匀。
3. 涂层质量要求厚度:涂层厚度应符合设计要求,需进行测量和记录。
颜色和光泽:涂层颜色应与要求一致,光泽度应均匀。
平整度:涂层应平整、无气泡、无皱纹、无鱼眼等缺陷。
附着力:涂层与基材的附着力要满足相关标准要求。
耐候性:涂层应具有一定的耐候性能,能够抵抗日晒、雨淋等自然环境的侵蚀。
4. 质量控制方法喷涂前准备:确保基材表面干净、光滑,去除杂质和油脂。
喷涂样板:制作涂层样板以作为参照,供比对和质量评估。
定期检查:定期对喷涂过程进行检查,包括喷涂设备、喷涂效果和涂层质量。
检测工具:使用适当的检测工具,如涂层厚度仪、色差仪等,进行涂层质量的检测和评估。
记录和分析:对检测结果进行记录和分析,及时发现问题并进行改进措施。
5. 质量控制责任生产部门:负责制定喷涂工艺标准和控制方法,并进行培训和指导。
质量部门:负责对喷涂过程进行监督和检验,确保符合标准要求。
检测部门:负责对涂层质量进行检测和评估,并及时提供报告。
以上是油漆喷涂工艺质量控制的标准,通过严格执行这些标准,可以保证油漆喷涂的质量和稳定性,提高产品的竞争力和客户满意度。
喷涂机器人的喷涂方法
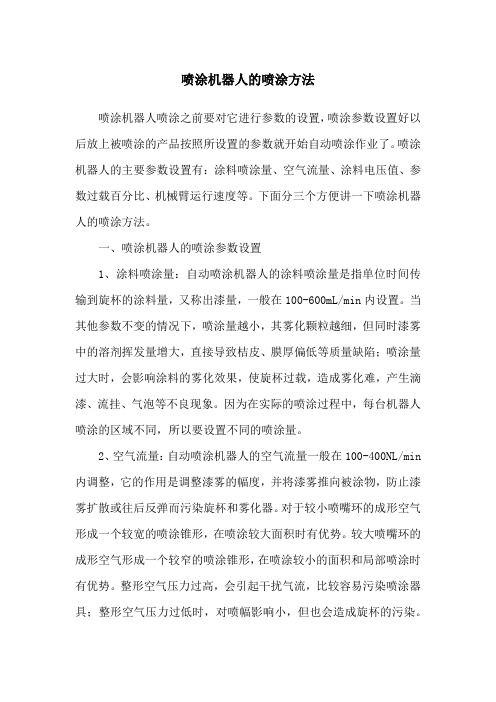
喷涂机器人的喷涂方法喷涂机器人喷涂之前要对它进行参数的设置,喷涂参数设置好以后放上被喷涂的产品按照所设置的参数就开始自动喷涂作业了。
喷涂机器人的主要参数设置有:涂料喷涂量、空气流量、涂料电压值、参数过载百分比、机械臂运行速度等。
下面分三个方便讲一下喷涂机器人的喷涂方法。
一、喷涂机器人的喷涂参数设置1、涂料喷涂量:自动喷涂机器人的涂料喷涂量是指单位时间传输到旋杯的涂料量,又称出漆量,一般在100-600mL/min内设置。
当其他参数不变的情况下,喷涂量越小,其雾化颗粒越细,但同时漆雾中的溶剂挥发量增大,直接导致桔皮、膜厚偏低等质量缺陷;喷涂量过大时,会影响涂料的雾化效果,使旋杯过载,造成雾化难,产生滴漆、流挂、气泡等不良现象。
因为在实际的喷涂过程中,每台机器人喷涂的区域不同,所以要设置不同的喷涂量。
2、空气流量:自动喷涂机器人的空气流量一般在100-400NL/min 内调整,它的作用是调整漆雾的幅度,并将漆雾推向被涂物,防止漆雾扩散或往后反弹而污染旋杯和雾化器。
对于较小喷嘴环的成形空气形成一个较宽的喷涂锥形,在喷涂较大面积时有优势。
较大喷嘴环的成形空气形成一个较窄的喷涂锥形,在喷涂较小的面积和局部喷涂时有优势。
整形空气压力过高,会引起干扰气流,比较容易污染喷涂器具;整形空气压力过低时,对喷幅影响小,但也会造成旋杯的污染。
为防止涂料残留在喷涂器具上,需要根据涂料量和实际经验准确地调整整形空气流量。
3、涂料电压值:机械手静电喷涂的电压一般在40-70kV内调整,在高转速杯式静电涂装场合,旋杯喷枪为负极,接地的被涂物车身为正极,在两极间施加高电压后产生的强电吸引力是将靠离心力机械雾化的漆雾颗粒传输到接地的被涂件上的主要作用力。
因此喷涂电压值的大小,直接影响静电涂装的静电效应、上漆率和涂膜的均匀性。
若雾化器到车身的距离一定时,电压值越高,静电场越强,漆滴的荷电量随电压增高而增大,则吸引力也就越大,上漆率越高。
双组份喷涂系统技术要求:

双组份喷涂系统技术要求:
(1)基本参数:
生产班制:二班制
生产方式:间隙式生产
喷涂道数:底面漆各一道,一次干膜厚度30~40μm
最大工件尺寸(小车及支架高度为1m):16X4X5m(长件)
11X4X5m (短件)
喷漆室净尺寸:18X7X6.5m(长件)
13X7X6.5m(短件)
涂料用量:约30~80kg/h
(2)涂料种类(供参考,投标方应根据自已的经验结合本项目做出切实可行的方案)
A.底漆:环氧富锌底漆(双组份)
比例:9:1(要求机械可调)
粘度:60~120 s
固化时间:~8h
B.面漆:丙烯酸聚氨酯面漆(双组份)
比例:3:1/4:1(要求机械可调)
粘度:<80s
固化时间:4~6h
(3)双组份喷涂系统要求
双组份喷涂系统共4套,均采用一泵两枪配置,每台喷漆室内
底、面漆喷涂系统各1套,底漆喷涂系统应充分考虑到富锌涂料的特点。
喷涂系统管路长度应能满足最大工件的喷涂要求;设备应能满足市场中不同厂家同一类型产品的喷涂要求;整个系统必须考虑工人操作维护方便,清洗方便,喷枪带反吹装置;整个系统安全、环保性能应符合国家相关标准。
- 1、下载文档前请自行甄别文档内容的完整性,平台不提供额外的编辑、内容补充、找答案等附加服务。
- 2、"仅部分预览"的文档,不可在线预览部分如存在完整性等问题,可反馈申请退款(可完整预览的文档不适用该条件!)。
- 3、如文档侵犯您的权益,请联系客服反馈,我们会尽快为您处理(人工客服工作时间:9:00-18:30)。
槽液 PH 值:7.5-9
磷化
游离酸度
1-2Pt(手动)
0.8-1.5Pt(自 动)
槽液总酸度:25-40 点
促进剂浓度:2pt-5pt
电泳
12-16%(手动) 槽液固体份
12-14%(自动)
槽液电导率:1200± 300us/cm
PH 值:6-6.5
烘干
老线烘干温度:170°-180° 新线烘干温度:170°-200°
涂装检验规程
1 目的
通过对涂装生产过程各个工序的检验,使车架、车厢、零部件外表涂装质量,符合工艺技术规定。
2 范围
适用于车架、车厢、零部件外表涂装过程中产品质量的检验工作。
3 职责
3.1 品控课负责对公司生产的三轮车车架、车厢、零部件涂装生产过程及化验参数进行检验工作。
3.2 品控课负责对不合格项目进行汇总、分析、提出整改意见并验证整改实施效果。
10-13 秒(冬季)
泳后漆膜厚度 漆膜厚度 中涂漆膜厚度
成品漆膜厚度
附着力应达到 1 级
成品质量
硬度达到 1H
光泽度:≥50Gs
空压系统压力:0.6-0.8MPa
喷涂车架 喷枪枪头距离工件:10-20cm
电流指示:50μA
2
车架 喷涂
烘干
烘干温度:≥200° 线速:≤300r/min 漆膜厚度:>60μm
2、槽液电导率:1200±300us/cm; 进行测试
进行倒槽。
3、槽液 PH 值:6-6.5。
老线烘干温度:170°-180°。 7 烘干★
新线烘干温度:170°-200°。
仪表显示
检查温度表及线速表记录 数值
喷 涂 前 1、电泳漆膜厚度:15-25μm;
8 表 面 检 2、要求车厢表面无浮尘、油污、颗
专用仪器测试、目测
备注:带“★”检验项目为关重工序。
4.2 生产过程控制办法
4.2.1 检查各生产过程的各种测量数据、记录是否准确。
4.2.2 抽查后要如实填写巡检记录表。
4.2.3 发现异常情况,立即填写“内部质量信息单”上报相关部门,验证处置过程及结果满足工艺技术要求。
5 程序作业记录表
5.1 涂装巡检记录表
喷涂前表 面
修理
要求表面无浮尘、油污、颗 粒物等缺陷
车厢外部 中涂 罩光喷涂
隆鑫红
19-28 秒(夏季) 26-36 秒(冬季)
宝马金
14-23 秒(夏季) 19-28 秒(冬季)
奥兴红 紫光红 欧曼兰 透明兰
10-20 秒(夏季)
备注
2
隆鑫灰 深枣红
青绿 翠绿 小康绿
14-24 秒(冬季)
清漆调漆 9-11 秒(夏季) (室温)
品控课:
车 间:
注:整改措施现场不能确定的,相应课室须明确后续的得出时间,否则视为 1 个工作日内完成。
5
1、检查记录表
动线)/0.8-2Pt(自动线); 5 磷化★
2、促进剂浓度 2pt-5pt; 3、槽液总酸度:25-40 点。
利用酚酞、酚蓝滴定测 2、查看是否按照工艺规定
试
进行倒槽。
1、槽液固体份:12-16%(手动线)
1、检查记录表
/12-14%(自动线); 6 电泳★
烤箱、电导率仪、PH 仪 2、查看是否按照工艺规定
附着力达到 1 级
硬度达到 1H
光泽度:>70Gs
3
小件 喷涂
喷涂完成
漆膜厚度:35±5μm 附着力达应达到 1 级
光泽度:≥50Gs
备注:此表一式二联,由品控课填写。
保存期:二年
3
序号 车型
不合格品记录及处理表
NO.:
问题描述
不合格数 生产总数
量
量
处理情况
责任课室 备注
保存期:二年
4
内部质量信息单
5.2 不合格品记录及处理表
5.3 内部质量信息单
1
涂装巡检记录表
编号:
巡检人:
序号 项目 检查内容 1 车厢 喷涂 脱脂槽液
指标 PH 值:12-14 游离碱度:20pt-40pt
日期: 年 月 日
合格判定(合格打√,不合格打×)
时间 判定
时间
判定
NO.:
时间 判定
酸洗
婆梅氏比重:13-17
表调
3.3 生产部负责对不合格项目进行改进或返修处置。
4 工作程序
4.1 巡检人员具体操作内容如下表:
序 检验 号 项目
检验内容及要求
1 脱脂
1、脱脂槽液的 PH 值:12-14; 2、脱脂槽液游离碱度 20pt-40pt。
所有水 2
洗工序
水洗液 PH 值:6-8
操作方法
备注
1、应用广范试纸对槽液 PH 值进行测试, 2、用酚酞滴定进行测 试。
查
粒物。
测厚仪、目测
测量漆膜厚度
1、要求喷涂均匀,色差在 4 以内;
车厢外
2、喷涂无流挂、橘皮、颗粒物等缺 部中涂、
目测、采用专用仪器进
测量漆膜厚度、硬度、附
9
陷;
罩光喷
行测试
着力、光泽度
3、要求漆膜厚度、硬度、附着力光
涂
泽度按工艺执行。
1、空压系统压力:0.6-0.8MPa
车架喷
10
2、喷枪枪头距离工件:10-20cm;
1、检查记录表 2、查看是否按照工艺规 定进行倒槽。
1、检查记录表
广范试纸进行测试对比 2、查看是否按照工艺规定 进行倒槽。
3 酸洗 4 表调
婆梅氏比重:13-17 表调槽液 PH 值:7.5-9
婆梅氏比重计对比 PH 试纸对比
检查记录表 1、检查记录表 2、查看是否按照工艺规定 进行倒槽。
1、槽液游离酸度(FA):1-2 点(手
发出课室: 质量问题详细情况(/车型、数量或比例、不合格现象及部位):
QR801-01
反馈人: 原因分析:
年月日
在制品处理:
库存品处理:
进一步的分析处理及整改措施:
签名:
审核: 年月日
领导审批:
签名:
年月日
整改验证:
签名:
年月日
处理人:
年
月
日
审核:
签收课室: 品质技术部:
制造部:
物资课:
管 理 课:
涂
3、电流指示:50μA。
指示表
1、烘干温度:≥200°;
1、检查温度表及线速表记
车 架 烘 2、线速:≤300r/min;
专用仪器测试、仪表显 录数值
11 干
3、漆膜厚度、附着力、厚度、光泽
示
2、测量漆膜厚度力、光泽度
12 零部件
1、要求漆膜厚度、光泽度、符合工 艺要求; 2、要求表面质量:无流挂、橘皮、 颗粒物等缺陷。