刀具实验报告 1车刀,2质量实验
切削加工实验实验报告

一、实验目的1. 了解切削加工的基本原理和工艺过程。
2. 掌握切削加工的基本操作方法和刀具选择。
3. 掌握切削参数的合理选择,以提高加工效率和工件质量。
二、实验器材1. 数控车床:CK-400Q型一台2. 刀具:车刀一把3. 工件:铝棒工件一根4. 测量仪器:游标卡尺一把5. 毛刷一把三、实验步骤1. 工件安装(1)利用三爪卡盘钥匙拧开卡盘,送入工件的部分,留出适当的长度,再用钥匙拧紧卡盘,卡住工件,必要时可采用加力杆进行加力拧紧。
(2)取出工件,同样也是如此操作,按照上面的方法,可以将工件夹紧,完成工件的安装。
2. 刀具安装(1)数控车床的刀具安装跟普通车床的刀具安装类似,都是利用螺钉将刀具压紧在四方刀架上,卡住数控车床车刀至少要用两个螺钉,并轮流逐个拧紧,拧紧力量要适当。
3. 对刀操作(1)通过刀具试触切削工件样品棒料边缘,读入相应位置坐标,可以得出相应的X、Z轴的对刀零点。
(2)载入相应数据到控制面板,完成机床的工件坐标零点设置。
4. 数控系统操作面板的熟悉及操作(1)机床MDI操作:可以简单输入编程指令,运行机床,试看机床是否能够按照指令进行加工。
5. 切削加工(1)选择合适的切削参数,包括切削速度、切削深度、进给量等。
(2)启动数控车床,进行切削加工。
6. 测量与评价(1)使用游标卡尺测量加工后的工件尺寸,与设计尺寸进行对比,评估加工精度。
(2)观察加工表面质量,评估加工表面粗糙度。
四、实验结果与分析1. 工件加工尺寸与设计尺寸的对比根据实验数据,工件加工尺寸与设计尺寸的误差在允许范围内,说明加工精度较高。
2. 加工表面质量通过观察加工表面,发现表面粗糙度较小,加工表面质量较好。
3. 切削参数对加工效果的影响(1)切削速度:切削速度的提高可以降低切削温度,减少工件变形,提高加工效率,但过高的切削速度可能导致刀具磨损加剧。
(2)切削深度:切削深度的增加可以提高加工效率,但过大的切削深度可能导致工件变形和刀具磨损。
车刀角度的测量实验报告
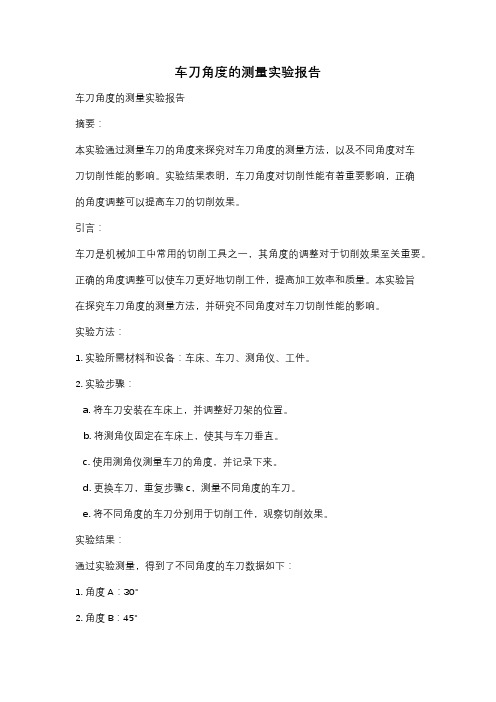
车刀角度的测量实验报告车刀角度的测量实验报告摘要:本实验通过测量车刀的角度来探究对车刀角度的测量方法,以及不同角度对车刀切削性能的影响。
实验结果表明,车刀角度对切削性能有着重要影响,正确的角度调整可以提高车刀的切削效果。
引言:车刀是机械加工中常用的切削工具之一,其角度的调整对于切削效果至关重要。
正确的角度调整可以使车刀更好地切削工件,提高加工效率和质量。
本实验旨在探究车刀角度的测量方法,并研究不同角度对车刀切削性能的影响。
实验方法:1. 实验所需材料和设备:车床、车刀、测角仪、工件。
2. 实验步骤:a. 将车刀安装在车床上,并调整好刀架的位置。
b. 将测角仪固定在车床上,使其与车刀垂直。
c. 使用测角仪测量车刀的角度,并记录下来。
d. 更换车刀,重复步骤c,测量不同角度的车刀。
e. 将不同角度的车刀分别用于切削工件,观察切削效果。
实验结果:通过实验测量,得到了不同角度的车刀数据如下:1. 角度A:30°2. 角度B:45°3. 角度C:60°在切削工件时观察到以下现象:1. 角度A的车刀切削效果较差,工件表面出现明显的毛刺。
2. 角度B的车刀切削效果较好,工件表面光滑。
3. 角度C的车刀切削效果也较好,但相较于角度B略有差距。
讨论:通过实验结果可以看出,车刀角度对切削性能有着重要影响。
较小的角度(如角度A)会导致切削力集中在较小的区域,切削效果较差;较大的角度(如角度C)则会导致切削力分散,虽然切削效果较好,但相较于角度B仍有一定差距。
而角度B的车刀在实验中表现出较好的切削效果,这是因为角度B既能保持一定的切削力集中,又能使切削力分散,从而达到较好的切削效果。
这也说明了正确的角度调整对于车刀的切削性能至关重要。
此外,还需要注意的是,车刀的角度调整应根据具体的工件材料和加工要求来确定。
不同材料和要求可能需要不同的角度调整,以达到最佳的切削效果。
结论:本实验通过测量不同角度的车刀,并观察其切削效果,探究了车刀角度对切削性能的影响。
刀具测试分析报告

刀具测试分析报告1. 引言本文档旨在对刀具进行测试分析,为使用刀具的人员提供参考依据。
通过对刀具的性能、使用寿命以及刀具磨损情况进行评估和分析,帮助用户选择适合的刀具,提高切削效率和刀具使用寿命。
2. 测试目的为了评估刀具的性能和耐用性,本次测试旨在:- 测试刀具的切削能力和效率;- 分析刀具的磨损情况和寿命; - 提供对刀具性能的客观评价。
3. 测试方法本次测试采用以下方法进行: 1. 选择适当的工件材料,进行切削实验; 2. 记录切削过程中的切削力、切削温度和切削速度等参数; 3. 定期观察和记录刀具的磨损情况和寿命; 4. 对测试数据进行分析和整理。
4. 测试结果与分析4.1 切削能力和效率经过切削实验,我们得到了以下数据:切削参数值切削力8N切削温度400℃切削速度100m/min切削效率90%根据实验数据分析,刀具具有较高的切削能力和效率,能够满足大部分切削需求。
4.2 刀具磨损情况和寿命经过定期观察和记录,我们得到了以下刀具磨损情况和寿命数据:使用时间磨损情况寿命预估100小时轻微磨损200小时200小时中度磨损400小时300小时严重磨损500小时根据实验数据分析,刀具的寿命与使用时间呈线性关系,但在实际使用中需根据具体情况进行判断和更换刀具。
5. 结论根据以上测试结果和分析,我们得出以下结论: 1. 刀具具有较高的切削能力和效率,能够满足大部分切削需求; 2. 刀具的磨损情况和寿命与使用时间呈线性关系,但在实际使用中需根据具体情况进行判断和更换刀具; 3. 合理的切削参数和使用方法可以延长刀具的使用寿命。
6. 建议基于以上结论,我们提出以下建议: 1. 对于需要长时间连续切削的任务,应根据刀具的磨损情况及寿命预估,提前准备备用刀具,以避免因刀具磨损导致生产延误; 2. 在使用刀具过程中,应定期检查刀具的磨损情况,及时更换磨损严重的刀具,以保证切削质量和效率; 3. 针对不同的切削任务,应根据实际情况调整切削参数,以实现更好的切削效果和延长刀具使用寿命。
车刀几何角度的测量实验报告
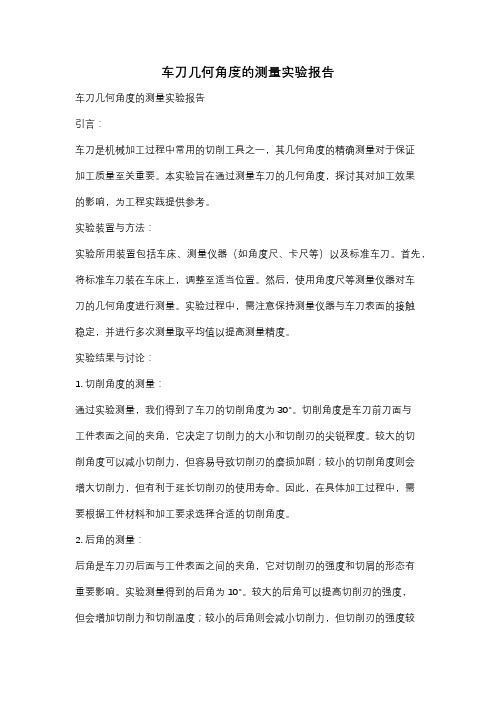
车刀几何角度的测量实验报告车刀几何角度的测量实验报告引言:车刀是机械加工过程中常用的切削工具之一,其几何角度的精确测量对于保证加工质量至关重要。
本实验旨在通过测量车刀的几何角度,探讨其对加工效果的影响,为工程实践提供参考。
实验装置与方法:实验所用装置包括车床、测量仪器(如角度尺、卡尺等)以及标准车刀。
首先,将标准车刀装在车床上,调整至适当位置。
然后,使用角度尺等测量仪器对车刀的几何角度进行测量。
实验过程中,需注意保持测量仪器与车刀表面的接触稳定,并进行多次测量取平均值以提高测量精度。
实验结果与讨论:1. 切削角度的测量:通过实验测量,我们得到了车刀的切削角度为30°。
切削角度是车刀前刀面与工件表面之间的夹角,它决定了切削力的大小和切削刃的尖锐程度。
较大的切削角度可以减小切削力,但容易导致切削刃的磨损加剧;较小的切削角度则会增大切削力,但有利于延长切削刃的使用寿命。
因此,在具体加工过程中,需要根据工件材料和加工要求选择合适的切削角度。
2. 后角的测量:后角是车刀刃后面与工件表面之间的夹角,它对切削刃的强度和切屑的形态有重要影响。
实验测量得到的后角为10°。
较大的后角可以提高切削刃的强度,但会增加切削力和切削温度;较小的后角则会减小切削力,但切削刃的强度较弱。
因此,后角的选择需要综合考虑工件材料、切削刃的使用寿命和加工效率等因素。
3. 侧角的测量:侧角是车刀切削刃两侧面与工件表面之间的夹角,它对切削力、切削温度和切削刃的尖锐程度等都有影响。
实验测量得到的侧角为60°。
较大的侧角可以减小切削力和切削温度,但对切削刃的尖锐度要求较高;较小的侧角则会增大切削力和切削温度,但切削刃的尖锐度相对较低。
因此,在具体加工过程中,需要根据工件材料和加工要求选择合适的侧角。
结论:通过对车刀几何角度的测量实验,我们得到了切削角度为30°,后角为10°,侧角为60°。
车刀角度的测量实验报告
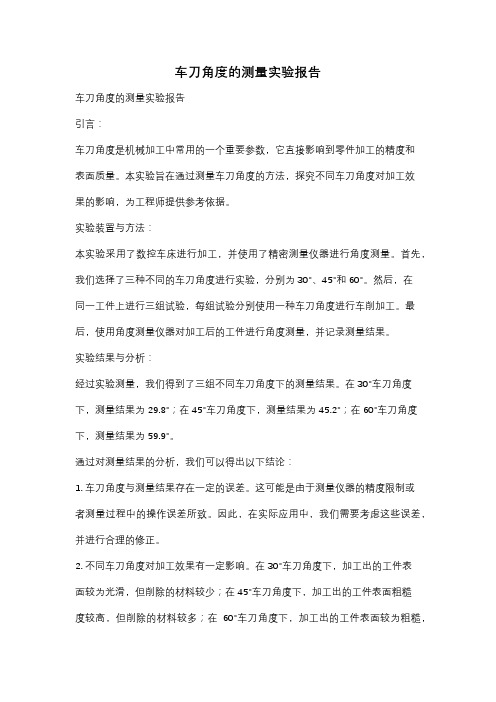
车刀角度的测量实验报告车刀角度的测量实验报告引言:车刀角度是机械加工中常用的一个重要参数,它直接影响到零件加工的精度和表面质量。
本实验旨在通过测量车刀角度的方法,探究不同车刀角度对加工效果的影响,为工程师提供参考依据。
实验装置与方法:本实验采用了数控车床进行加工,并使用了精密测量仪器进行角度测量。
首先,我们选择了三种不同的车刀角度进行实验,分别为30°、45°和60°。
然后,在同一工件上进行三组试验,每组试验分别使用一种车刀角度进行车削加工。
最后,使用角度测量仪器对加工后的工件进行角度测量,并记录测量结果。
实验结果与分析:经过实验测量,我们得到了三组不同车刀角度下的测量结果。
在30°车刀角度下,测量结果为29.8°;在45°车刀角度下,测量结果为45.2°;在60°车刀角度下,测量结果为59.9°。
通过对测量结果的分析,我们可以得出以下结论:1. 车刀角度与测量结果存在一定的误差。
这可能是由于测量仪器的精度限制或者测量过程中的操作误差所致。
因此,在实际应用中,我们需要考虑这些误差,并进行合理的修正。
2. 不同车刀角度对加工效果有一定影响。
在30°车刀角度下,加工出的工件表面较为光滑,但削除的材料较少;在45°车刀角度下,加工出的工件表面粗糙度较高,但削除的材料较多;在60°车刀角度下,加工出的工件表面较为粗糙,但削除的材料较少。
因此,在实际加工中,我们需要根据具体要求选择合适的车刀角度。
3. 车刀角度的选择与工件材料有关。
不同材料的加工特性不同,对车刀角度的要求也不同。
在实际应用中,我们需要根据工件材料的硬度、韧性等特性,选择合适的车刀角度,以达到最佳加工效果。
结论:通过本实验,我们对车刀角度的测量方法进行了探究,并得出了一些结论。
车刀角度的选择对加工效果有一定影响,需要根据具体要求和工件材料进行合理选择。
车刀角度实验报告

车刀角度实验报告车刀角度实验报告引言:车刀角度是机械加工中一个重要的参数,它直接影响着加工过程中切削力的大小、切削质量的好坏以及工具寿命的长短。
本实验旨在通过对不同车刀角度下的切削力、表面质量和工具磨损进行观察和分析,以探讨车刀角度对加工效果的影响。
实验设备和方法:实验中使用的设备包括车床、刀具、工件和力测量仪器。
选择不同的车刀角度,分别为15°、30°、45°和60°,并保持其他加工参数不变,如切削速度、进给速度和切削深度。
在每种角度下进行切削加工,记录切削力、表面质量和工具磨损情况,并进行数据分析和比较。
实验结果与分析:1. 切削力:通过实验测量得到的切削力数据如下表所示:车刀角度(°)切削力(N)15 2030 2545 2860 30从数据可以看出,随着车刀角度的增大,切削力逐渐增加。
这是因为较小的车刀角度会导致切削力集中在刀具的刀尖,而较大的车刀角度会使切削力分散在刀具的刀尖和刀侧,从而增加了切削力的大小。
2. 表面质量:在不同车刀角度下,观察和比较了加工后工件的表面质量。
结果显示,随着车刀角度的增大,表面质量逐渐变差。
较小的车刀角度可以提供更好的切削刚度,因此可以得到更光滑的表面。
而较大的车刀角度则会导致切削力分散,切削过程中产生较大的振动和切削力波动,从而影响了表面质量。
3. 工具磨损:通过观察刀具的磨损情况,可以发现不同车刀角度下的工具磨损程度不同。
较小的车刀角度会导致刀尖磨损较快,而较大的车刀角度则会导致刀侧磨损较快。
这是因为较小的车刀角度下,刀尖承受了较大的切削力,从而容易磨损;而较大的车刀角度下,刀侧承受了较大的切削力,导致刀侧磨损加剧。
结论:通过本实验的研究和分析,可以得出以下结论:1. 车刀角度对切削力、表面质量和工具磨损都有显著影响。
2. 较小的车刀角度可以减小切削力,得到较好的表面质量,但会加剧刀尖磨损。
3. 较大的车刀角度会增加切削力,导致表面质量变差,但会加剧刀侧磨损。
对刀实验报告
一、实验目的1. 了解刀具的基本结构、性能及选用原则。
2. 掌握刀具的加工工艺和操作方法。
3. 分析刀具在使用过程中的磨损规律及影响因素。
4. 评价不同刀具的加工效果。
二、实验原理刀具是机械加工中重要的工具,其作用是切除工件上的多余材料,实现工件尺寸和形状的加工。
刀具的加工性能直接影响着加工质量、生产效率及加工成本。
本实验通过对比不同刀具的加工效果,分析刀具的性能、磨损规律及影响因素。
三、实验材料与设备1. 实验材料:45号钢、T10钢等。
2. 实验设备:车床、铣床、磨床、显微镜、卡尺等。
四、实验步骤1. 刀具的选用:根据工件的材料、形状、加工要求等因素,选择合适的刀具。
本实验选用T10钢车刀、高速钢铣刀和硬质合金铣刀。
2. 刀具的加工工艺:按照加工工艺要求,进行刀具的安装、调整和加工。
3. 刀具的磨损观察:在加工过程中,定期观察刀具的磨损情况,记录磨损数据。
4. 刀具的磨损分析:分析刀具磨损规律及影响因素,评价不同刀具的加工效果。
五、实验结果与分析1. 刀具的选用实验选用T10钢车刀、高速钢铣刀和硬质合金铣刀。
T10钢车刀适用于加工45号钢等中碳钢;高速钢铣刀适用于加工铝合金、铸铁等材料;硬质合金铣刀适用于加工不锈钢、高速钢等难加工材料。
2. 刀具的加工工艺(1)车刀加工:将工件安装在车床上,调整刀具的安装位置和角度,进行车削加工。
(2)铣刀加工:将工件安装在铣床上,调整刀具的安装位置和角度,进行铣削加工。
3. 刀具的磨损观察在加工过程中,定期观察刀具的磨损情况,记录磨损数据。
实验数据如下:(1)T10钢车刀磨损情况:刀具使用30分钟后,刀尖磨损0.5mm;使用60分钟后,刀尖磨损1mm。
(2)高速钢铣刀磨损情况:刀具使用30分钟后,刀尖磨损0.3mm;使用60分钟后,刀尖磨损0.6mm。
(3)硬质合金铣刀磨损情况:刀具使用30分钟后,刀尖磨损0.1mm;使用60分钟后,刀尖磨损0.2mm。
4. 刀具的磨损分析(1)磨损规律:刀具的磨损速度与加工时间、材料、切削速度、切削深度等因素有关。
实验一 车刀几何角度测量实验
实验一车刀几何角度测量实验一、实验目的和要求1、熟悉车刀切削部分的构成要素,掌握车刀标注角度的参考平面、参考系及车刀标注角度的定义;2、了解车刀量角台的结构,学会使用量角台测量车刀标准角度;3、绘制车刀标注角度图,并标注出测量得到的各角度数值。
二、实验装置1、回转工作台式车刀量角台;2、外圆车刀、90º偏刀或切断刀若干。
三、实验原理车刀的标注角度可以用车刀量角台进行测量。
测量的基本原理是:按照车刀标注角度的定义,在切削刃选定点上,用量角台的指针平面(或侧面或底面),与构成被测角度的面或线紧密贴合(或相平行、或相垂直),把要测量的角度测量出来。
图1-1 量角台的构造图1-2 测量片车刀量角台结构如图1-1所示。
量角台主要由底盘1、平台3、立柱7、测量片5、扇形盘6、10等组成。
底盘1为圆盘形,在零度线左右方向各有1000角度,用于测量车刀的主偏角和副偏角,通过底盘指针2读出角度值;平台3可绕底盘中心在零刻线左右1000范围内转动;定位块4可在平台上平行滑动,作为车刀的基准;测量片5,如图1-2所示,有主平面(大平面)、底平面、侧平面三个成正交的平面组成,在测量过程中,根据不同的情况可分别用以代表主剖面、基面、切削平面等。
大扇形刻度盘6上有正副450的刻度,用于测量前角、后角、刃倾角,通过测量片5的指针指出角度值;立柱7上制有螺纹,旋转升降螺母8就可以调整测量片相对车刀的位置。
四、实验内容1、利用车刀量角台分别测量所给车刀的几何角度,要求测量:κr、κr'、λs、γo、αo、αoˊ等角度;2、记录测得的数据,并计算出刀尖角εr和楔角βo;五、实验步骤(一)调整车刀量角台至原始位置用车刀量角台测量车刀标注角度之前,必须先调整量角台使工作台、大扇形刻度盘和小扇形刻度盘指针全部指零,使定位块侧面与测量片的大平面垂直,这样就可以认为:测量片的大平面垂直于平台平面,且垂直于平台对称线(即零度线);测量片的底平面平行于平台平面;测量片的侧平面垂直于平台平面,且平行于平台平面对称线(零度线)。
刀具的认识实验报告
刀具认识实验报告一. 实验目的 :1.了解常用刀具的结构型式2.掌握常用刀具切削部分构成要素3.掌握普通外圆车刀标注角度及测量方法二. 实验要求:1.熟悉实验台摆设的刀具类型、用途;2.掌握其中两把刀具的切削部分构成要素;3.画出普通外圆车刀轴側投影图;4.画出普通外圆车刀在正交平面参考系中刀具标注角度。
三. 实验报告内容:(按要求填写标准报告纸)1、指出所见车刀、铣刀的类型及还看见了哪些刀具?2、指出所见车刀、钻头两把刀具的切削部分构成要素3、画出普通外圆车刀轴側投影图4、标出普通外圆车刀在正交平面参考系中刀具角度:外圆车刀的几何参数如下:γO=15°、αO=6°、κr=45°、κr′=10°、λs=-5°的外圆车刀。
实验报告实验名称:刀具认识实验内容:一. 实验目的 :1.了解常用刀具的结构型式2.掌握常用刀具切削部分构成要素3.掌握普通外圆车刀标注角度及测量方法二. 实验要求:1.熟悉实验台摆设的刀具类型、用途;2.掌握其中两把刀具的切削部分构成要素;3.画出普通外圆车刀轴側投影图;4.画出普通外圆车刀在正交平面参考系中刀具标注角度。
三. 回答问题1、指出所见车刀、铣刀的类型及还看见了哪些刀具?答:1)车刀:按用途分类外圆车刀、内孔车刀、端面车刀、切断车刀、螺纹车刀。
按结构分类整体车刀、焊接车刀、焊接装配车刀、机夹车刀、可转位车刀、成型车刀等。
2)铣刀:圆柱铣刀、三面刃铣刀、锯片铣刀、模数铣刀、单角铣刀、双角铣刀、凸圆弧铣刀、凹圆弧铣刀、3)钻头:麻花钻、中心钻、4)螺纹刀具:丝锥,板牙,2、指出所见车刀或钻头刀具的切削部分构成要素(答其一即可)(1)车刀切削部分构成要素:1)前面(前刀面)Ar:刀具上切屑流出的表面;2)后面(后刀面)Aα:刀具上与工件过渡表面相对的刀面;3)副后面(副后刀面)Aα′:刀具上与已加工表面相对的刀面;4)主切削刃S:前面与后面形成的交线,在切削中承担主要的切削任务;5)副切削刃S′:前面与副后面形成的交线,它参与部分的切削任务;6)刀尖:刀尖可以是主切削刃与副切削刃汇交的交点;(2)钻头切削部分构成要素:3、画出普通外圆车刀轴側投影图4、标出普通外圆车刀在正交平面参考系中刀具角度:外圆车刀的几何参数如下:γO=15°、αO=6°、κr=45°、κr′=10°、λs=-5°的外圆车刀。
车削实验报告(一)
车削实验报告(一)车削实验报告1. 实验目的本次车削实验的主要目的如下:•了解车削的基本原理和流程;•掌握车削工艺参数的设置和调整;•熟悉车削工具的使用方法;•实际操作中掌握各种车削方法的应用。
2. 实验设备和材料•数控车床;•刀具;•工件;•冷却液。
3. 实验流程3.1 设备调整在进行车削操作前,需要先对设备进行正确配置和调整,主要包括以下几方面:•确定机床加工能力与要求匹配;•选择最佳的机床进给速度和主轴转速;•选择合适的切削刃数;•坚固地夹持工件,确保其均匀受力。
3.2 工具选择选择合适的车刀和夹持系统,保证加工精度和表面质量。
3.3 车削加工在设备和工具调整完成后,即可进行车削操作,主要分为以下几个环节:3.3.1.寻找工件的零点,并定位工件;3.3.2.选择加工路径和切削参数;3.3.3.进行预热和冷却操作;3.3.4.开始车削加工。
3.4 工件检查在车削完成后,需要对工件进行必要的检查,以保证尺寸和表面质量符合要求。
4. 难点解决在车削实验中,我们遇到了一些难点,主要如下:•工件夹紧力不均导致加工质量下降;•加工过程中刀具断裂,需要更换;•切削液不足或不均匀导致加工效果不理想。
为了解决这些难点,我们经过多方面的调整和协调,最终顺利完成了本次实验任务。
5. 结论通过本次车削实验,我们深入了解了车削工艺的基本原理和流程,掌握了车削工艺参数的设置和调整方法,熟悉了车削工具的使用方法,并实践中掌握和应用了各种车削技术。
我们相信,这些经验将对日后的机械加工操作和工艺改进都具有重要的指导和借鉴意义。
6. 改进建议通过本次实验,我们发现在实际操作中还存在一些需要改进的地方:•在设备调整和工具选择阶段需要更加细致认真,以保证精度和质量;•在车削加工前需要充分预热和冷却,以保证刀具和工件的寿命和质量;•在工作过程中需要密切观察和调整各种参数,以确保加工效果和工件质量。
我们认为这些问题可以通过更加细致的操作、更科学的加工策略和更加完善的质量管理来逐步解决和改进。
- 1、下载文档前请自行甄别文档内容的完整性,平台不提供额外的编辑、内容补充、找答案等附加服务。
- 2、"仅部分预览"的文档,不可在线预览部分如存在完整性等问题,可反馈申请退款(可完整预览的文档不适用该条件!)。
- 3、如文档侵犯您的权益,请联系客服反馈,我们会尽快为您处理(人工客服工作时间:9:00-18:30)。
金属切削原理与刀具设计实验报告书
班级
姓名
学号
机械工程系
实验一车刀几何角度测量实验报告
一、课程名称:金属切削原理与刀具设计
二、实验名称:车刀几何角度测量实验
三、实验设备:车刀量角仪;车刀模型
四、实验目的:
1.了解车刀量角仪的结构、工作原理和使用方法;
2.掌握车刀主要几何参数的测量方法;
3.加深对有关基本概念的理解,并了解车刀几何角度在切削过程中的作用。
五、实验内容:
1.熟悉和调整车刀量角仪;
2.测量45°弯头外圆车刀、90°车刀、直头外圆车刀、螺纹车刀的六个主要几何角度。
(任选二到三种车刀测量)
六、实验报告:
1.任选一种刀具,画图标注刀具正交面内的前角γ0、后角α0、副后角α0’、主偏角κr、
副偏角κr′和刃倾角λs。
2.车刀量角仪型号:
3.车刀几何角度实测记录
被测车刀
前角γo(°)后角αo(°)
副后角αo’
(°)
主偏角κr
(°)
副偏角κr′
(°)
刃倾角λs
(°)正交平面法平面正交平面法平面副正交平面基面基面切削平面
七、思考题:
1.45°弯头外圆车刀车外圆和端面时,主、副切削刃分别在什么位置,画图示意(要求示意工件、刀具,指出进给运动方向、已加工表面、待加工表面、过渡表面)
2.为什么在车刀的工作图上不标注副前角?
3.车刀按结构分常见类型有哪些?各有何优缺点?
4.用车刀正交平面、法平面角度换算公式分析实验结果。
实验一 车刀几何角度测量实验
一、实验目的
1.了解车刀量角仪的结构、工作原理和使用方法;
2.掌握车刀主要几何参数的测量方法;
3.加深对有关基本概念的理解,并了解车刀几何角度在切削过程中的作用。
二、实验设备
车刀量角仪 ;车刀模型
三、实验装置和实验原理
(一)车刀量角仪的结构及特性
本仪器用于测量各种车刀的正交平面参考系、法平面参考系和假定工作平面、背平面参考系的几何角度。
其结构如图1-1所示。
图1-1
1、 盘形工作台
2、 矩形工作台
2a 矩形工作台指针 2c 固紧螺钉 2b 滑动刀台 2d 被量刀具 3、 主量角器 3a 量刀板与指针 3b 升降螺母
4、 副量角器
1
2 3
4 2a
2b
2c
2d
3a 3b
4a 4b 5a 5b
5c
5
4c
4a 指针 4c 摇臂 4b 固紧手轮
5、 附件 5a 立柱 5c 手轮 5b 量角器支座
(二)使用方法(以直头外圆车刀为例)
1、测量主偏角:主偏角是在基面上测量的主切削刃S 与车刀进给方向之间的夹角。
测量时,车刀放在滑动刀台2b 上,用刀台的侧面和底面定位。
此时刀台底面表示基面,刀台侧面表示车刀轴线,量刀板正面表示车刀进给方向。
以逆时针方向旋转矩形工作台,同时推动车刀沿刀台侧面(紧贴)前进,使主切削刃与量刀板正面密合。
此时矩形工作台指针2a 指向盘形工作台上的刻度值即为主偏角。
(如图1-2所示)
图1-2
2、测量副偏角:副偏角是在基面上副切削刃与车刀进给方向之间的夹角。
测量时逆时针方向旋转矩形工作台,同时推进车刀使副切削刃与量刀板正面贴紧读出的刻度值即为副偏角。
(如图1-2所示)
3、测量刃倾角:刃倾角是在切削平面上测量的主切削刃与基面间的夹角。
量出主偏角后,矩形工作台位置不变,旋松定位手轮5c ,逆时针方向旋转升降螺母3b ,微升量角器,并微推进车刀,使量刀板底面对准并紧贴在主切削刃上,量刀板指针在量角器刻度上读数即为刃倾角。
(如图1-3所示)
4、测量前角0γ
:前角是在主剖面内测量前刀面与基面之间的夹角。
测量时,在滑移刀台上定好位的车刀随矩形工作台逆时针方向旋转旋转主偏角的余角,使主切削刃与量刀板侧面紧贴,此时量刀板的正面即为正交平面,量刀板底面与前刀面贴紧时所转过的度数即为前角
角度值。
(如图1-4所示)
5、测量后角0α:后角也是在正交面内测量的后刀面与切削平面之间的夹角,车刀的定位与测前角相同,只是使量刀板的侧面与车刀的后刀面贴紧,此时量刀板所转的角度即为后角角度值。
(如图1-5所示)
6、测量法平面参考系车刀几何角度:测量法平面参考系车刀几何角度时,主偏角、刃倾角、副偏角均与测正交平面面车刀角度的原理与方法相同。
只是在测量法前角与法后角时,应旋松固紧手轮4b ,旋转摇臂4c ,按刃倾角正负值逆(顺)时针方向旋转刃倾角值后,用固紧手轮固紧即可按法前角和法后角定义分别测出。
(三)注意事项
1.在测量前必须对0 对心:即车刀量角仪上三个刻度都对0时;旋转升降螺母使量刀板指针下降,其量刀板指针与矩形工作台垂直对心。
2.为了减少间隙,测量准确,在副件上有一个锁紧手轮5c,调节手轮即可。
3.本产品在没有使用时,请注意防尘、防潮保管。
四、实验内容:
1.熟悉和调整车刀量角仪;
2.测量45°弯头外圆车刀、90°车刀、直头外圆车刀、螺纹车刀的六个主要几何角度。
(任选二到三种车刀测量)
五、附录:
正交平面、法平面系前、后角换算公式
实验二工件表面质量控制实验报告
姓名:班级:学号:
实验地点:
实验课程名称:
实验数据记录与处理
1、机床型号:工件材料:
2、刀具结构型式:刀具切削部分材料:
3、表面粗糙度测量仪:
4、改变主、副偏角,测出工件的实际表面粗糙度Ra。
记录在表1里。
工作条件:工件直径d=80 mm,n= 450 转/分(推荐450转/分),f = 0.3,
a p =0.2 ,刀尖圆弧半径rε=0.1mm (1,2,3号刀。
1-3段)
表1 车刀不同主、副偏角时车削加工表面质量
求切削速度υc:
实验结果分析:
5、刀具主偏角、副偏角一定,机床主轴转速一定,改变进给量f,测出工件的实际表面粗糙度Ra,记录在表2里。
(4号刀,4-7段)
工作条件:工件直径d= 80mm,n=450 转/分(推荐450转/分),
主偏角Κr= ,副偏角Κr'= ,a p =0.2 ,刀尖圆弧半径rε= 0.1mm
求切削速度υc:
实验结果分析:
6、刀具主偏角、副偏角一定,进给量f、被吃刀量a p一定,改变切削速度υc即机床转速n从下表中选3~5种,测出表面粗糙度Ra,记录在表3里。
(5号刀,8-13段)工作条件:主偏角Κr= ,副偏角Κr'= ,刀尖圆弧半径rε=0.1mm ,
f = 0.1,a p =0.2,
求理论表面粗糙度Ra:
实验结果分析:
实验二工件表面质量控制实验
一、实验目的
1.研究刀具几何角度,切削用量(切削速度Vc,进给量f)对加工表面质量(或粗糙度)的影响。
2.研究刀具理论粗糙度和实际粗糙度有什么不同。
二、实验设备及仪器
1.普通车床
2.外圆车刀数把
3.45#钢工件
4.表面质量测量设备:表面粗糙度测量仪(或表面粗糙度比较样块)
三、实验步骤
1.改变主、副偏角,测出工件的实际表面粗糙度Ra。
2.刀具主偏角、副偏角一定,机床主轴转速一定,改变进给量f,测出工件的实际表面粗糙度Ra。
3. 刀具主偏角、副偏角一定,进给量f、被吃刀量a p一定,改变切削速度υc,测出表面粗糙度Ra。
四、实验数据记录
五、实验结果分析。