刀具实验报告
各种刀具认识实验报告
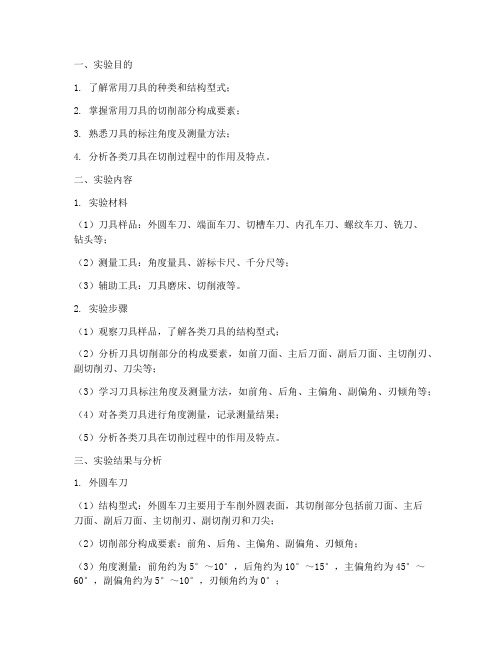
一、实验目的1. 了解常用刀具的种类和结构型式;2. 掌握常用刀具的切削部分构成要素;3. 熟悉刀具的标注角度及测量方法;4. 分析各类刀具在切削过程中的作用及特点。
二、实验内容1. 实验材料(1)刀具样品:外圆车刀、端面车刀、切槽车刀、内孔车刀、螺纹车刀、铣刀、钻头等;(2)测量工具:角度量具、游标卡尺、千分尺等;(3)辅助工具:刀具磨床、切削液等。
2. 实验步骤(1)观察刀具样品,了解各类刀具的结构型式;(2)分析刀具切削部分的构成要素,如前刀面、主后刀面、副后刀面、主切削刃、副切削刃、刀尖等;(3)学习刀具标注角度及测量方法,如前角、后角、主偏角、副偏角、刃倾角等;(4)对各类刀具进行角度测量,记录测量结果;(5)分析各类刀具在切削过程中的作用及特点。
三、实验结果与分析1. 外圆车刀(1)结构型式:外圆车刀主要用于车削外圆表面,其切削部分包括前刀面、主后刀面、副后刀面、主切削刃、副切削刃和刀尖;(2)切削部分构成要素:前角、后角、主偏角、副偏角、刃倾角;(3)角度测量:前角约为5°~10°,后角约为10°~15°,主偏角约为45°~60°,副偏角约为5°~10°,刃倾角约为0°;(4)作用及特点:外圆车刀切削力较大,切削速度较快,适用于粗加工和半精加工。
2. 端面车刀(1)结构型式:端面车刀主要用于车削端面,其切削部分包括前刀面、主后刀面、副后刀面、主切削刃、副切削刃和刀尖;(2)切削部分构成要素:前角、后角、主偏角、副偏角、刃倾角;(3)角度测量:前角约为10°~15°,后角约为10°~15°,主偏角约为45°~60°,副偏角约为5°~10°,刃倾角约为0°;(4)作用及特点:端面车刀切削力较大,切削速度较快,适用于粗加工和半精加工。
刀具实验报告
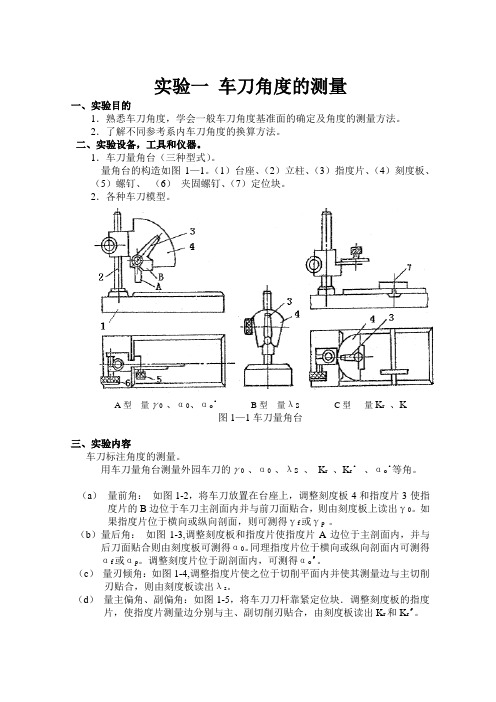
实验一车刀角度的测量一、实验目的1.熟悉车刀角度,学会一般车刀角度基准面的确定及角度的测量方法。
2.了解不同参考系内车刀角度的换算方法。
二、实验设备,工具和仪器。
1.车刀量角台(三种型式)。
量角台的构造如图1—1。
(1)台座、(2)立柱、(3)指度片、(4)刻度板、(5)螺钉、(6)夹固螺钉、(7)定位块。
2.各种车刀模型。
A型量γ0 、α0、αo·B型量λs C型量K r、K图1—1车刀量角台三、实验内容车刀标注角度的测量。
用车刀量角台测量外园车刀的γ0 、α0 、λs 、K r、K r·、αo·等角。
(a)量前角:如图1-2,将车刀放置在台座上,调整刻度板4和指度片3使指度片的B边位于车刀主剖面内并与前刀面贴合,则由刻度板上读出γ0。
如果指度片位于横向或纵向剖面,则可测得γf或γp 。
(b)量后角:如图1-3,调整刻度板和指度片使指度片A边位于主剖面内,并与后刀面贴合则由刻度板可测得α0。
同理指度片位于横向或纵向剖面内可测得αf或αp。
调整刻度片位于副剖面内,可测得αo〃。
(c)量刃倾角:如图1-4,调整指度片使之位于切削平面内并使其测量边与主切削刃贴合,则由刻度板读出λs。
(d)量主偏角、副偏角:如图1-5,将车刀刀杆靠紧定位块.调整刻度板的指度片,使指度片测量边分别与主、副切削刃贴合,由刻度板读出K r和K r〃。
图1—2前角γ0测量图1—3后角量α0的测量图1—4刃倾角λs的测量图1—5主偏角K r、副偏角K r〃的测量实验记录1.主剖面参考系的基本角度(单位:度)计算:3.在所测量刀具中选择刃倾角最大的刀具,计算切深前角γp,进给前角γf。
由tgγp=tgγo cos K r +tgλs sin K r得γp=arctg(tg10.5o cos42o+tg(-6o)sin42o)=3.86o由tgγf=tgγo sin K r -tgλs cos K r得γf=arctg(tg10.5o sin42o-tg(-6o)cos42o)=11.43o实验二车削力的测定及经验公式的建立一、实验目的1.了解切削力动态测量显示系统、YDC-III89型压电式车削测力仪的工作原理和使用方法。
刀具参数测量实验报告
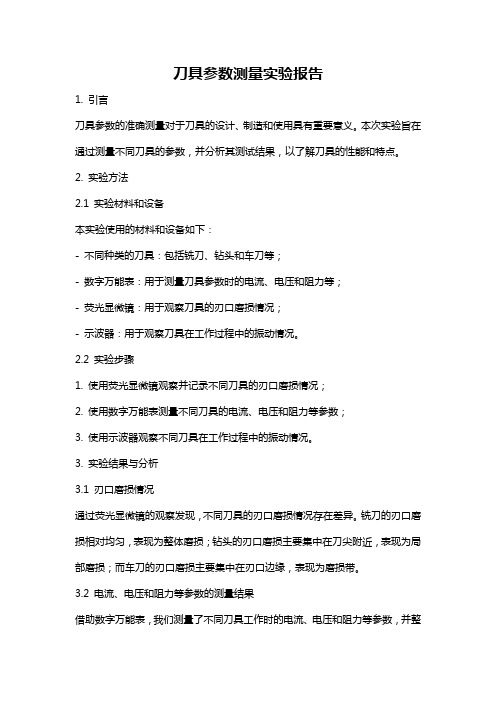
刀具参数测量实验报告1. 引言刀具参数的准确测量对于刀具的设计、制造和使用具有重要意义。
本次实验旨在通过测量不同刀具的参数,并分析其测试结果,以了解刀具的性能和特点。
2. 实验方法2.1 实验材料和设备本实验使用的材料和设备如下:- 不同种类的刀具:包括铣刀、钻头和车刀等;- 数字万能表:用于测量刀具参数时的电流、电压和阻力等;- 荧光显微镜:用于观察刀具的刃口磨损情况;- 示波器:用于观察刀具在工作过程中的振动情况。
2.2 实验步骤1. 使用荧光显微镜观察并记录不同刀具的刃口磨损情况;2. 使用数字万能表测量不同刀具的电流、电压和阻力等参数;3. 使用示波器观察不同刀具在工作过程中的振动情况。
3. 实验结果与分析3.1 刃口磨损情况通过荧光显微镜的观察发现,不同刀具的刃口磨损情况存在差异。
铣刀的刃口磨损相对均匀,表现为整体磨损;钻头的刃口磨损主要集中在刀尖附近,表现为局部磨损;而车刀的刃口磨损主要集中在刃口边缘,表现为磨损带。
3.2 电流、电压和阻力等参数的测量结果借助数字万能表,我们测量了不同刀具工作时的电流、电压和阻力等参数,并整理成下表:刀具电流(A)电压(V)阻力(Ω)-铣刀 2.1 12.5 5.95钻头 1.8 10.2 5.67车刀 2.4 15.8 6.58从上表可以看出,不同刀具工作时的电流、电压和阻力等参数存在一定的差异。
其中,车刀的电流和电压均较高,而阻力相对较大;钻头的电流和电压较低,阻力也相对较小;铣刀的参数处于中等水平。
3.3 刀具振动情况的观察使用示波器观察不同刀具在工作过程中的振动情况。
实验结果显示,不同刀具的振动幅度和频率存在差异。
铣刀的振动幅度较大,频率较高;钻头的振动幅度相对较小,频率也较低;车刀的振动幅度和频率均处于中等水平。
4. 结论通过本次实验,我们对不同刀具的参数进行了测量,并分析了测量结果。
根据实验结果,我们得出以下结论:1. 不同刀具的刃口磨损情况存在差异,其中铣刀的磨损相对均匀,钻头的磨损集中在刀尖附近,车刀的磨损集中在刃口边缘。
刀具几何角度测量实验报告
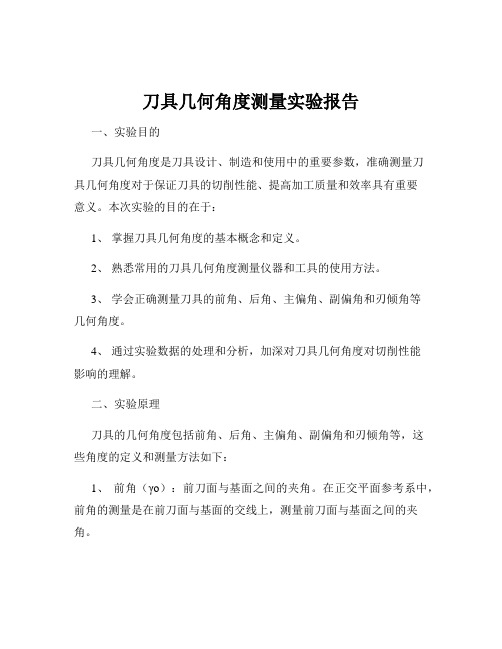
刀具几何角度测量实验报告一、实验目的刀具几何角度是刀具设计、制造和使用中的重要参数,准确测量刀具几何角度对于保证刀具的切削性能、提高加工质量和效率具有重要意义。
本次实验的目的在于:1、掌握刀具几何角度的基本概念和定义。
2、熟悉常用的刀具几何角度测量仪器和工具的使用方法。
3、学会正确测量刀具的前角、后角、主偏角、副偏角和刃倾角等几何角度。
4、通过实验数据的处理和分析,加深对刀具几何角度对切削性能影响的理解。
二、实验原理刀具的几何角度包括前角、后角、主偏角、副偏角和刃倾角等,这些角度的定义和测量方法如下:1、前角(γo):前刀面与基面之间的夹角。
在正交平面参考系中,前角的测量是在前刀面与基面的交线上,测量前刀面与基面之间的夹角。
2、后角(αo):后刀面与切削平面之间的夹角。
在后刀面与切削平面的交线上,测量后刀面与切削平面之间的夹角。
3、主偏角(κr):主切削刃在基面上的投影与进给方向之间的夹角。
4、副偏角(κ'r):副切削刃在基面上的投影与背离进给方向之间的夹角。
5、刃倾角(λs):主切削刃与基面之间的夹角。
测量刀具几何角度通常使用万能角度尺、刀具角度测量仪等工具。
三、实验设备和工具1、实验所用刀具:车刀、铣刀等。
2、测量仪器:万能角度尺、刀具角度测量仪。
3、其他工具:游标卡尺、千分尺、量角器等。
四、实验步骤1、准备工作熟悉实验所用的刀具和测量仪器。
检查测量仪器的精度和零位是否准确。
2、测量前角(γo)将刀具平放在工作台上,使前刀面朝上。
使用万能角度尺或刀具角度测量仪的测量爪与前刀面和基面接触,读取测量仪器上的角度值,即为前角。
3、测量后角(αo)将刀具翻转,使后刀面朝上。
按照测量前角的方法,测量后刀面与切削平面之间的夹角,得到后角。
4、测量主偏角(κr)将刀具的主切削刃平放在工作台上,使主切削刃在基面上的投影清晰可见。
使用量角器或刀具角度测量仪测量主切削刃在基面上的投影与进给方向之间的夹角,即为主偏角。
刀具角度的实验报告
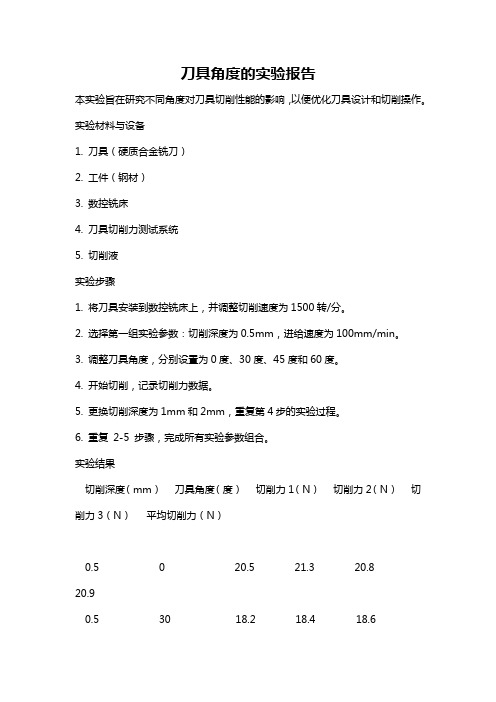
刀具角度的实验报告本实验旨在研究不同角度对刀具切削性能的影响,以便优化刀具设计和切削操作。
实验材料与设备1. 刀具(硬质合金铣刀)2. 工件(钢材)3. 数控铣床4. 刀具切削力测试系统5. 切削液实验步骤1. 将刀具安装到数控铣床上,并调整切削速度为1500转/分。
2. 选择第一组实验参数:切削深度为0.5mm,进给速度为100mm/min。
3. 调整刀具角度,分别设置为0度、30度、45度和60度。
4. 开始切削,记录切削力数据。
5. 更换切削深度为1mm和2mm,重复第4步的实验过程。
6. 重复2-5 步骤,完成所有实验参数组合。
实验结果切削深度(mm)刀具角度(度)切削力1(N)切削力2(N)切削力3(N)平均切削力(N)0.5 0 20.5 21.3 20.820.90.5 30 18.2 18.4 18.618.40.5 45 16.7 16.8 16.6 16.70.5 60 15.2 15.3 15.4 15.31 0 25.1 24.8 25.3 25.11 30 21.6 22.1 21.8 21.81 45 19.8 19.6 19.7 19.71 60 17.9 17.7 18.1 17.92 0 30.3 30.6 30.5 30.52 30 26.7 26.9 26.6 26.72 45 24.5 24.6 24.4 24.52 60 22.1 21.8 22.3 22.1数据分析通过对实验结果的分析,我们可以得出以下结论:1. 随着切削深度的增加,切削力也随之增加。
这是由于加工过程中材料的剪切面积增大,切削力的需要也增加。
2. 在相同切削深度下,刀具角度增加会导致切削力的减小。
这是由于增大的刀具角度可以降低刀具与工件之间的接触面积,减小切削力的需要。
3. 当刀具角度达到一定程度后,再增加刀具角度对切削力的减小作用有限。
这是由于角度过大会导致刀具的切削效率降低,进而增加切削力。
刀具及磨刀实验报告(3篇)
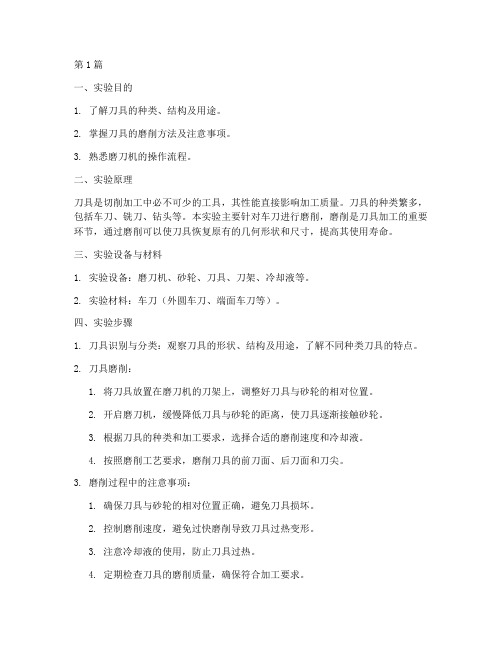
第1篇一、实验目的1. 了解刀具的种类、结构及用途。
2. 掌握刀具的磨削方法及注意事项。
3. 熟悉磨刀机的操作流程。
二、实验原理刀具是切削加工中必不可少的工具,其性能直接影响加工质量。
刀具的种类繁多,包括车刀、铣刀、钻头等。
本实验主要针对车刀进行磨削,磨削是刀具加工的重要环节,通过磨削可以使刀具恢复原有的几何形状和尺寸,提高其使用寿命。
三、实验设备与材料1. 实验设备:磨刀机、砂轮、刀具、刀架、冷却液等。
2. 实验材料:车刀(外圆车刀、端面车刀等)。
四、实验步骤1. 刀具识别与分类:观察刀具的形状、结构及用途,了解不同种类刀具的特点。
2. 刀具磨削:1. 将刀具放置在磨刀机的刀架上,调整好刀具与砂轮的相对位置。
2. 开启磨刀机,缓慢降低刀具与砂轮的距离,使刀具逐渐接触砂轮。
3. 根据刀具的种类和加工要求,选择合适的磨削速度和冷却液。
4. 按照磨削工艺要求,磨削刀具的前刀面、后刀面和刀尖。
3. 磨削过程中的注意事项:1. 确保刀具与砂轮的相对位置正确,避免刀具损坏。
2. 控制磨削速度,避免过快磨削导致刀具过热变形。
3. 注意冷却液的使用,防止刀具过热。
4. 定期检查刀具的磨削质量,确保符合加工要求。
4. 磨削完成后的检查:检查刀具的磨削质量,包括几何形状、尺寸和表面粗糙度等。
五、实验结果与分析1. 通过实验,掌握了刀具的种类、结构及用途。
2. 熟悉了磨刀机的操作流程和磨削方法。
3. 磨削后的刀具符合加工要求,表面光滑、尺寸准确。
六、实验总结1. 本实验加深了对刀具和磨削工艺的认识,提高了实际操作能力。
2. 通过实验,掌握了磨刀机的操作技巧和注意事项,为今后从事相关工作奠定了基础。
七、思考题1. 刀具磨削过程中,如何避免刀具过热变形?2. 如何根据加工要求选择合适的磨削速度和冷却液?3. 如何保证磨削后的刀具质量?第2篇一、实验目的1. 了解刀具的种类、结构及用途。
2. 掌握刀具磨削的基本原理和方法。
刀具几何角度的测量实验报告
刀具几何角度的测量实验报告刀具几何角度的测量实验报告引言:刀具在机械加工领域中起着至关重要的作用。
而刀具的几何角度对于其性能和加工效果有着直接的影响。
因此,准确测量刀具的几何角度是非常重要的。
本实验旨在通过一系列测量实验,探究刀具几何角度的影响以及测量方法的准确性。
实验一:刀具的切削角度测量在切削过程中,刀具的切削角度直接影响着切削力和切削刃的寿命。
本实验使用了专用的角度测量仪器,通过将刀具固定在测量仪器上,准确测量了刀具的切削角度。
实验结果显示,切削角度的大小与切削力呈正相关关系。
较大的切削角度可以减小切削力,但过大的切削角度会导致切削刃的过早磨损。
因此,在实际加工中,需要根据具体情况选择适当的切削角度。
实验二:刀具的前角度测量刀具的前角度是指刀具刃的前面与切削面之间的夹角。
该角度的大小直接影响着切削刃的尖锐度和切削质量。
本实验使用了光学显微镜,通过观察切削刃的形态,测量了刀具的前角度。
实验结果显示,较小的前角度可以使切削刃更加尖锐,提高切削质量。
然而,过小的前角度会导致切削刃容易损坏。
因此,在实际加工中,需要根据材料的硬度和切削条件选择适当的前角度。
实验三:刀具的后角度测量刀具的后角度是指刀具刃的后面与切削面之间的夹角。
该角度的大小对切削刃的排屑性能和切削质量有着重要影响。
本实验使用了扫描电子显微镜,通过观察切削刃的形态,测量了刀具的后角度。
实验结果显示,较小的后角度可以改善切削刃的排屑性能,提高切削质量。
然而,过小的后角度会导致切削刃的容易断裂。
因此,在实际加工中,需要根据切削材料的特性选择适当的后角度。
实验四:刀具的侧后角度测量刀具的侧后角度是指刀具刃的侧面与切削面之间的夹角。
该角度的大小对切削刃的切削力和切削质量有着重要影响。
本实验使用了数字显微镜,通过测量切削刃的形态,准确测量了刀具的侧后角度。
实验结果显示,适当的侧后角度可以减小切削力,提高切削质量。
然而,过大的侧后角度会导致切削刃的易损性增加。
刀具实验报告参考答案
实验一刀具角度的测量一、实验目的1.熟悉车刀切削部分的构造要素, 掌握车刀标注角度的参考平面、参考系及车刀标注角度的定义。
2、了解量角仪的结构, 学会使用量角仪测量车刀标注角度。
3、绘制车刀标注角度图, 并标注出测量得到的各标注角度数值。
二、实验基本原理按照车刀标准角度的定义, 在主切削刃的选定点, 用万能角度尺的尺面或量角仪的指针平面(或侧面、或底面), 与构成被测角度的面或线紧密贴合(或相互平行、或相互垂直), 把要测量的角度测量出来。
三、实验仪器设备及材料车刀量角台、外圆车刀、端面车刀、切断刀及三角形螺纹车刀四、实验步骤1、测量车刀的主偏角松开量角器锁紧螺钉, 调整量角器使其处于水平位置, 拧紧量角器锁紧螺钉;2、松开滑块锁紧螺钉, 旋转滑块定位螺母, 将滑块降到最低位置, 将滑块上90°刻线对准立柱上正对操作者的0°刻线, 拧紧滑块锁紧螺钉;3、转动量角器上的指针, 同时改变刀具在工作台上的位置, 使测量刀口与主切削刃平行或贴合, 读取量角器上的读数a, 主偏角=90°-该读数a, 将主偏角数值计入报告。
4、测量车刀的副偏角5、转动量角器上的指针, 同时改变刀具在工作台上的位置, 使测量刀口与副切削刃平行或贴合, 读取量角器上的读数, 副偏角即为该读数, 将副偏角数值计入报告。
6、测量车刀的刃倾角松开滑块锁紧螺钉, 旋转滑块定位螺母, 将滑块上升到一定位置;松开量角器锁紧螺钉, 将量角器处于垂直位置, 量角器所处平面垂直于基面, 拧紧量角器锁紧螺钉;7、转动滑块, 将滑块上0°刻线对准立柱上正对操作者的0°刻线, 此时量角器处于背吃刀面上, 顺时针将滑块转过a度, 此时量角器即处于主切削平面上, 拧紧滑块锁紧螺钉;8、转动量角器上的指针, 同时改变刀具在工作台上的位置, 上下移动滑块位置, 使测量刀口与主切削刃平行或贴合, 读取量角器上的读数, 即刃倾角, 将刃倾角数值计入报告。
刀具角度测量实验报告
刀具角度测量实验报告一、实验目的。
本实验旨在通过测量刀具角度,探究刀具在不同角度下的切削性能,为工程加工提供理论依据和实际指导。
二、实验原理。
刀具角度是指刀具刃口与工件表面的夹角,常用的刀具角度有刀尖倾角、主偏角、切削刃倾角等。
刀具角度的选择直接影响切削力、切削温度和切削表面质量。
三、实验仪器和材料。
1. 数显卡尺。
2. 数控铣床。
3. 钢材工件。
4. 切削刀具。
四、实验步骤。
1. 将工件夹紧在数控铣床上,调整好刀具的位置和刀具角度。
2. 使用数显卡尺测量刀具角度,记录下各个角度对应的数值。
3. 依次进行不同角度下的切削实验,记录下切削力、切削温度和切削表面质量等数据。
4. 分析实验数据,得出刀具角度对切削性能的影响规律。
五、实验结果与分析。
通过实验数据的分析,我们得出了以下结论:1. 刀具角度对切削力的影响,随着刀具角度的增大,切削力逐渐减小。
这是因为刀具角度增大可以减小切削刃厚度,降低切削力。
2. 刀具角度对切削温度的影响,刀具角度增大会降低切削温度,减小切削表面的热影响区,有利于提高切削表面质量。
3. 刀具角度对切削表面质量的影响,适当增大刀具角度可以提高切削表面质量,但角度过大会增加切削刃厚度,降低切削表面质量。
六、实验结论。
通过本实验,我们得出了以下结论:1. 刀具角度对切削性能有着显著的影响,合理选择刀具角度可以提高切削效率和切削表面质量。
2. 在实际加工中,需要根据工件材料、切削条件等因素综合考虑,选择合适的刀具角度。
七、实验总结。
本实验通过测量刀具角度,探究了刀具角度对切削性能的影响规律,为工程加工提供了重要的理论依据和实际指导。
在今后的工程实践中,我们将继续深入研究刀具角度的影响机理,不断优化切削工艺,提高加工效率和产品质量。
机床刀具认知实验报告(3篇)
第1篇一、实验目的1. 了解机床刀具的基本结构和分类;2. 掌握刀具的几何参数和角度对切削性能的影响;3. 熟悉刀具的选用原则和注意事项;4. 培养动手能力和实际操作技能。
二、实验内容1. 机床刀具的基本结构(1)刀具主体:包括刀杆、刀片和刀柄等部分;(2)刀片:是刀具的切削部分,用于与工件接触,产生切削力;(3)刀柄:连接刀具与机床主轴,传递动力和切削力。
2. 刀具的分类(1)按加工方法分类:车刀、铣刀、刨刀、磨刀等;(2)按加工对象分类:外圆车刀、端面车刀、内孔车刀、螺纹车刀等;(3)按材料分类:高速钢刀具、硬质合金刀具、陶瓷刀具等。
3. 刀具的几何参数和角度(1)前角:刀具前刀面与基面之间的夹角,用于改善切削条件,提高切削效率;(2)后角:刀具后刀面与基面之间的夹角,用于减小切削力,提高刀具寿命;(3)主偏角:刀具主切削刃与基面之间的夹角,用于改善切削条件,提高切削效率;(4)副偏角:刀具副切削刃与基面之间的夹角,用于减小切削力,提高刀具寿命;(5)刃倾角:刀具主切削刃与副切削刃之间的夹角,用于改善切削条件,提高切削效率。
4. 刀具的选用原则(1)根据加工材料和加工方法选择刀具;(2)根据工件形状和尺寸选择刀具;(3)根据机床性能和加工精度要求选择刀具;(4)根据加工条件选择刀具,如切削速度、切削深度等。
5. 刀具的注意事项(1)刀具安装要牢固,防止切削过程中刀具松动;(2)刀具刃磨要正确,确保切削刃锋利;(3)合理选用切削参数,避免刀具过载;(4)注意刀具的磨损和损坏,及时更换刀具。
三、实验步骤1. 观察和了解机床刀具的基本结构和分类;2. 学习刀具的几何参数和角度对切削性能的影响;3. 根据实验要求,选用合适的刀具;4. 安装刀具,调整切削参数;5. 进行切削实验,观察刀具的切削性能;6. 分析实验结果,总结实验心得。
四、实验结果与分析1. 通过实验,掌握了机床刀具的基本结构和分类;2. 理解了刀具的几何参数和角度对切削性能的影响;3. 学会了刀具的选用原则和注意事项;4. 培养了动手能力和实际操作技能。
- 1、下载文档前请自行甄别文档内容的完整性,平台不提供额外的编辑、内容补充、找答案等附加服务。
- 2、"仅部分预览"的文档,不可在线预览部分如存在完整性等问题,可反馈申请退款(可完整预览的文档不适用该条件!)。
- 3、如文档侵犯您的权益,请联系客服反馈,我们会尽快为您处理(人工客服工作时间:9:00-18:30)。
实验一车刀角度的测量一、实验目的1.熟悉车刀角度,学会一般车刀角度基准面的确定及角度的测量方法。
2.了解不同参考系内车刀角度的换算方法。
二、实验设备,工具和仪器。
1.车刀量角台(三种型式)。
量角台的构造如图1—1。
(1)台座、(2)立柱、(3)指度片、(4)刻度板、(5)螺钉、(6)夹固螺钉、(7)定位块。
2.各种车刀模型。
A型量γ0 、α0、αo·B型量λs C型量K r、K图1—1车刀量角台三、实验内容车刀标注角度的测量。
用车刀量角台测量外园车刀的γ0 、α0 、λs 、K r、K r·、αo·等角。
(a)量前角:如图1-2,将车刀放置在台座上,调整刻度板4和指度片3使指度片的B边位于车刀主剖面内并与前刀面贴合,则由刻度板上读出γ0。
如果指度片位于横向或纵向剖面,则可测得γf或γp 。
(b)量后角:如图1-3,调整刻度板和指度片使指度片A边位于主剖面内,并与后刀面贴合则由刻度板可测得α0。
同理指度片位于横向或纵向剖面内可测得αf或αp。
调整刻度片位于副剖面内,可测得αo〃。
(c)量刃倾角:如图1-4,调整指度片使之位于切削平面内并使其测量边与主切削刃贴合,则由刻度板读出λs。
(d)量主偏角、副偏角:如图1-5,将车刀刀杆靠紧定位块.调整刻度板的指度片,使指度片测量边分别与主、副切削刃贴合,由刻度板读出K r和K r〃。
图1—2前角γ0测量图1—3后角量α0的测量图1—4刃倾角λs的测量图1—5主偏角K r、副偏角K r〃的测量实验记录1.主剖面参考系的基本角度(单位:度)计算:3.在所测量刀具中选择刃倾角最大的刀具,计算切深前角γp,进给前角γf。
由tgγp=tgγo cos K r +tgλs sin K r得γp=arctg(tg10.5o cos42o+tg(-6o)sin42o)=3.86o由tgγf=tgγo sin K r -tgλs cos K r得γf=arctg(tg10.5o sin42o-tg(-6o)cos42o)=11.43o实验二车削力的测定及经验公式的建立一、实验目的1.了解切削力动态测量显示系统、YDC-III89型压电式车削测力仪的工作原理和使用方法。
2.了解切削力产生过程。
3.掌握切削深度、进给量等对切削力的影响规律4.通过对实验数据的处理,建立主切削力的经验公式二、实验设备,工具和仪器。
1.工件 60,Q235棒料;2.C6140普通车床;3.YDC-III89型压电式车削测力仪(含外远圆车刀);4.SINOCER YE5850电荷放大器;5.PCI—9118DG/L多功能数据采集卡(A/D转换);6.计算机;7.切削力动态测量显示系统软件。
三、实验原理(一)测试系统框图(二)YDC-III89型压电式车削测力仪1.构成由一个含外圆车刀的整体构件与一个压电石英晶体三维力传感器构成,如图11. 外圆车刀2. 力传感器该测力仪同一些必要的二次仪表组合在一起,可以完成切削力的静、动态测试,可以准确而容易地获得金属切削加工中最重要的参数,既三维切削力。
全属切削理论的研究已由过去的静态测量发展到动态测量,对测力仪有了更高的要求。
Y DC-III89A压电式车削测力仪能以其高刚度、高灵敏度、高固有频率能很好地满足静、动态测试的要求,可测出任意方向力的三个相互正交的分量(FX,Fy,Fz) 。
2.压电石英晶体三维力传感器原理(1)基本原理压电石英晶体三维力传感器的结构如图2这种传感器有三对不同切型的石英晶片装入壳体内构成。
其中一对采用具纵向压电效应的切片,只能测量垂直仪的Z向力;而另外两对晶片由于采用具有切向效应的切型,且相互灵敏度方向成90°放置,因此可测X,Y向的分力。
这样空间任何方向的力作用在传感器上时,传感器便能自动地将力分解为空间相互正交的三个分力。
(2)传感器的特点a、刚性好。
石英的弹性系数E=8000k g∕mm2,而通常石英晶片厚只有约lmm,因此整个传感器的刚度相当于一个实心铸铁块的刚度。
b、灵敏度高。
因为压电传感器属于“无位移”型传感器,理论上电荷量只与应力有关,而与位移无关,这样系统的刚性可以大些,而对灵敏度没有太大的影响。
c、线性好,而且一般情况下几乎没有滞后现象。
d、频率响应宽。
特别适合动态测量,X, Y两向固有频率均在5 kHz以上,而Z 向固有须率可达25KHz以上,若装在合适结构中,频响还可提高。
e、稳定性好。
时间老化低,无热释电现象,对温度敏感性比电阻电感传感器要小得多,因此灵敏度基本保持为常数。
出厂时以标定好。
F、调整、使用方便。
压电系统没有绝对零点,可以选定任意给定的状态作为零点。
在准静态测量中,力的动态部分比稳态部分小很多。
若希望将动态部分放大或只显示动态部分,只需将电荷放大器清零,并且将灵敏度换到高档即可,而不管静态部分的大小。
这一点对自适应控制和用概率论方法进行数据处理十分有意义。
(3)测力仪静、动态标定.静态标定:目的是为了得到静标曲线,以便求得各项灵敏度、线性误差、重复性误差、向间干扰等静态性能参数。
由于该传感器稳定性好,时间老化低,无热释电现象,对温度敏感性比电阻电感传感器要小得多,因此灵敏度基本保持为常数,出厂时已标定好。
实验时将三台电荷放大器的的传感灵敏度旋钮分别调至标定结果中的数值。
动态标定:目前主要有激振法和钢球冲击法两种,主要是用于求得频率响应曲线和固有频率。
详见YDC-III89型压电式车削测力仪使用说明书1]。
(三)SINOCER YE5850电荷放大器;是将测力仪的电荷信号转变为电压信号输出的关键设备,能够测量动态信号和准静态信号。
对于不同测试对象应合理选择电荷放大器的灵敏度数值。
为了保持静态分量的稳定性,特别为了静标需要,要求电荷放大器必须具有极高的输入阻抗(>1013Ω)、极低的下限频率(<10-6Hz)和大的时间常数(>106S)。
详见电荷放大器使用说明书[2](四)P CI—9118DG/L多功能数据采集卡测试系统利用该采集卡可进行低速信号和高速信号采集。
1.低速信号采集对于常规车削、钻削,一般主轴的转速比较低,可选用此功能;对于定性试验或静态刚度试验也可以选用这种信号采集方式,由于采集速率低且采样频率不精确,所得的数据不适合进行频域分析(时频变换)。
2.高速信号采集对于切削速度比较高,转速比较高的切削情况,可以选择高速测量方式,由于采用采集卡自带的CPU,与系统时钟等无关,采集速度取决于卡的采集能力,对于9118,单通道测试时,最高采集速度可达330KH Z,如果是三通道,实际最快的采集频率为110 KH Z。
信号采集操作步骤详见切削力动态测量显示系统软件使用说明书[3]四、实验(一)准备工作1.安装工件、测力仪,刀具对准工件中心高。
2.按测量系统框图连线,参见切削力动态测量系统硬件连接指南[4]。
3.熟悉机床操作手柄及操作指南。
4.确定实验条件。
(二)切削实验用单因数法进行实验,即在固定其他因数,只改变一个因数的条件,测出切削力。
1.固定v、f(v取100m/min左右,f在0.14~0.56mm/r范围内取一个数值),依次改变a p(在0.5~2.5mm范围内取5个数值)进行切削,对应每一个a p,传感器会采集到三组(三个方向分力的)实验数据。
2.固定v、a p(v取100m/min左右,a p在1~2.5mm范围内取一个数值),依次改变f(根据机床进给量表,在0.1~0.6mm范围内取5个数值)进行切削,对应每一个f,传感器会采集到三组(三个方向分力的)实验数据。
3.其他(还可改变v、γ0等实验)(三)实验记录2.固定v、a p,改变f(实验2)p(四)数据处理对应每组切削用量参数,系统采集到一组数据,利用系统的数据处理功能,将其转换成Excel文件,再求出算术平均值,填入上面表中相应位置。
(五)图形处理利用系统的图形处理功能,可进行图形处理,显示、打印、保存图形。
实验1的fx,fy,fz数据图实验2的fx,fy,fz数据图实验数据对数值线性拟合10(六)经验公式建立(主切削力)型式:求出系数f C 、p a C 、z F C ,指数, 、 Fz y 。
由 lgf z =lgc f +y fz lgf 得 y fz =0.756 c f =10^3.499=3155由 lgf z =lgc ap +x fz lgap 得 x fz =1.054 c ap =10^2.765=582由Fz=c fz ap xfz f yfz 取 ap=2 f=0.1 时fz=561.99 解得c fz =1543.27(七)分析讨论分析切削用量a p 、f 对F Z 的影响规律。
由实验得出的计算公式 Fz=c fz ap xfz f yfz 即 Fz=1543.27ap 1.054f 0.756可知 背吃刀量ap 和进给量fap ↑ =>切削力 Fz ↑(增大倍数大致相同) ;f ↑ =>切削力 Fz ↗(增大倍数略小)。
故为提高生产效率,在相同切削力和切削功率条件下,应采用大进给量。
(八)实验心得与总结刀具的这两次实验的都很经典且实用,在帮助我们理解刀具的角度位置和切削力与切削用量的关系有很大的作用。
在处理数据的过程中要抓住主要的关键数据,舍弃与总体数据相差很多的干扰错误数据。
在使用分析软件时要注意其计算精度范围,数据处理得出的结果与理论值相差不多,证明了实验数据处理的正确性。
Fz y f fC Fz =z F p x p a a C Fz =Fz z F y x p z F f a C Fz =z F x。