第五章短纤维后加工设备
短纤维生产工艺

短纤维生产工艺
短纤维是指长度在1.5-4.5毫米之间的纤维,主要用于制作各
种纺织品和非织造布。
下面将介绍短纤维的生产工艺。
首先,短纤维的生产工艺主要分为湿法和干法两种。
湿法生产工艺是将植物纤维或化学纤维通过加工设备处理成湿浆,再通过旋转筛分机将湿浆脱水除杂,得到湿糊状的短纤维。
然后将湿糊状的短纤维进行分散和脱水,使其含水率降低到15%以下。
最后通过烘干设备将湿糊状的短纤维烘干,使其含
水率低于5%。
干法生产工艺则是直接将原纤维送入预处理机械,通过强大的离心力和废气抽吸机的作用,分离出纤维和杂质。
然后通过制粉机将纤维打破成短纤维,最后利用气力输送系统将短纤维输送到后续的加工设备中。
在上述的湿法和干法生产工艺中,还存在着一系列的辅助加工过程。
比如,对植物纤维进行浸渍处理,可以改变其物理性质和纤维结构,提高纤维的柔软性和强度。
同时还可以通过添加化学药剂,对纤维进行漂白和染色加工,使纤维具有更好的颜色和光泽。
此外,为了提高短纤维的加工效率和产品的质量,还需要采用纤维预处理技术。
比如,在短纤维生产过程中可以采用卷曲、撕裂和剥离等预处理技术,以增加纤维的拉伸度和强度,提高产品的稳定性和可靠性。
总的来说,短纤维的生产工艺主要包括湿法和干法两种。
在这两种工艺中,还需要进行一系列的辅助加工和预处理,以提高短纤维的质量和性能。
通过不断的技术创新和工艺改进,短纤维的生产工艺将会越来越高效和环保。
第5章 精梳

一、精梳前准备工序的目的
1.提高条子中纤维平行伸直度。
2.根据喂入的需要,制成均匀的条子或小 卷。
(1)小卷需要定量均匀,容量大,外形好,退 卷时不粘连发毛。
(2)小卷的纵横向结构要均匀,使纤维层能在 很好握持状态下梳理。横向均匀,可使纤维层 在精梳时握持可靠,纵向均匀则能使内外层重 量稳定,可稳定精梳落纤率,以改善精梳条的 重量不匀率。
图中,梳棉机输出的生条以后弯钩为主, 经过生条筒储存后送入下一道工序时,弯钩就 变为前弯钩;经过第一道准备工序储存后送入 第二道准备工序,此时弯钩变为后弯钩;再进 入精梳工序时,又成为前弯钩。
当梳棉机与精梳机之间的准备工艺道数
为偶数时,可使小卷在喂入精梳机构时,被 钳板握持的棉层中,多数弯钩纤维仍然其纤维的损失。
目前纺纱工序还是连续与离散相结合的, 纤维集合体的半制品需要中间存储,比如条 子、粗纱、细纱等。从梳理机到精梳机之间, 每经过一道中间存储就会发生一次弯钩倒向, 即前后弯钩的方向更换,这是因为“先进后 出”的原则所决定的。
由于梳理机出来的纤维弯钩主要是后弯 钩,因此梳理机到精梳机之间的工艺道数必 须是偶数,这样才可以保证精梳工序纤维中 以前弯钩为主体,这就是精梳准备工艺的偶 数法则。
后退喂给:棉层在钳板后摆时喂入。
α2=X2/F
α2 :后退给棉的喂给系数 X2:钳板闭合前已喂给的长度(mm) F:总喂给长度(mm)
在后退给棉过程中,钳板闭合后给出的 棉层将涌皱在钳板后面。
钳板闭合越早, X2越小, α2越小。须丛 涌皱较多,在钳板后退时受锡林梳理的须丛
长度越短。当0≤ X2 ≤ F 时, 0≤ α2 ≤1
不同给棉方式及喂给系数将影响精梳梳理 质量(纤维长度、短纤率、棉结数等)及 落纤率的大小。这些属于精梳工艺调整的 范畴。
短纤生产工艺
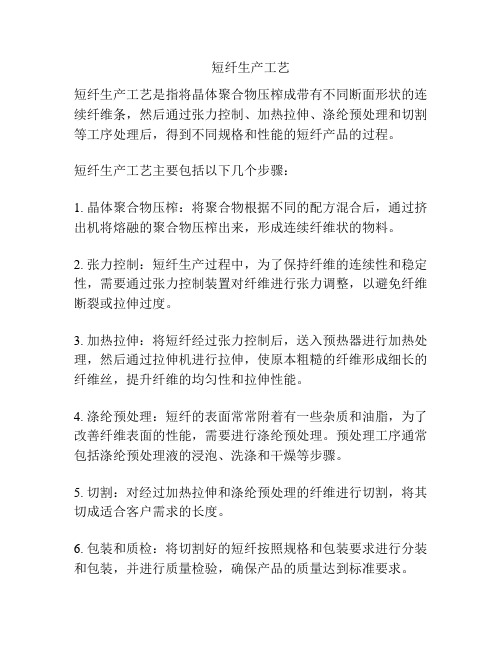
短纤生产工艺
短纤生产工艺是指将晶体聚合物压榨成带有不同断面形状的连续纤维条,然后通过张力控制、加热拉伸、涤纶预处理和切割等工序处理后,得到不同规格和性能的短纤产品的过程。
短纤生产工艺主要包括以下几个步骤:
1. 晶体聚合物压榨:将聚合物根据不同的配方混合后,通过挤出机将熔融的聚合物压榨出来,形成连续纤维状的物料。
2. 张力控制:短纤生产过程中,为了保持纤维的连续性和稳定性,需要通过张力控制装置对纤维进行张力调整,以避免纤维断裂或拉伸过度。
3. 加热拉伸:将短纤经过张力控制后,送入预热器进行加热处理,然后通过拉伸机进行拉伸,使原本粗糙的纤维形成细长的纤维丝,提升纤维的均匀性和拉伸性能。
4. 涤纶预处理:短纤的表面常常附着有一些杂质和油脂,为了改善纤维表面的性能,需要进行涤纶预处理。
预处理工序通常包括涤纶预处理液的浸泡、洗涤和干燥等步骤。
5. 切割:对经过加热拉伸和涤纶预处理的纤维进行切割,将其切成适合客户需求的长度。
6. 包装和质检:将切割好的短纤按照规格和包装要求进行分装和包装,并进行质量检验,确保产品的质量达到标准要求。
短纤生产工艺的关键环节在于加热拉伸和涤纶预处理。
加热拉伸可以改善纤维形态和性能,提高纤维的强度、延伸性和抗断裂性能。
涤纶预处理可以去除纤维表面的杂质和油脂,提高纤维与其他材料的粘附性能,使短纤在后续的加工和应用中更加稳定和可靠。
总之,短纤生产工艺是一个复杂而精细的过程,需要通过严格的工艺控制和质量检验,确保生产出符合客户需求和标准要求的短纤产品。
涤纶短纤维后加工生产工艺流程解析
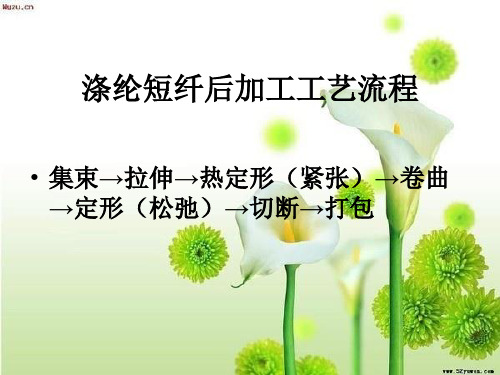
涤纶短纤后加工工艺流程
• 集束→拉伸→热定形(紧张)→卷曲 →定形(松弛)→切断→打包
1、初生纤维的存放和集束
• 存放的目的:刚成形的初生纤维,起结构不 太稳定,需一段时间存放平衡使内应力减 小和消失,并使卷绕时所上的油剂,得到 均匀扩散,从而改善拉伸性能。一般在恒 温恒湿下存放8小时以上。
2、拉伸
短纤维切断长度由纤维品种而定: 棉型纤维:38mm 毛型纤维:90~120mm 中长纤维:51~76mm 打包是涤纶短纤维生产的最后一道工序, 将短纤维打成一定规格和重量的包,以便运 送出厂。
ห้องสมุดไป่ตู้
3、热定型:
消除纤维内应力,提高纤维的尺寸稳定性, 并且进一步改善其物理机 械性能。使拉伸,卷曲效果固定,并使成品 纤维符合要求。
4、卷曲
目的:通过卷曲,增加纤维间的抱合力 方法:在热水或水蒸汽加热下,通过机械 挤压获得卷曲效果。 一般棉型纤维5-7个曲/厘米,毛型3-5个 曲/厘米
5、切断和打包
5.聚酯纤维
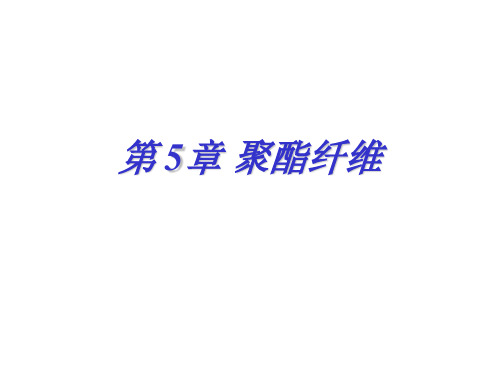
BHET的合成
BHET的合成主要采用以下三种方法: (1)DMT和EG的酯交换法; (2)PTA和EG的直接酯化法; (3)PTA和EO (环氧乙烷)加成法。 在工业上PET的制造采用二种方法:
酯交换法:以DMT为中间体通过酯交换法来制造 直接酯化法:以PTA(高纯度对苯二甲酸)或MTA (中纯度对苯二甲酸)为中间体通过直接酯化法来 制造。
可以达到强化熔体均匀性的目的,同时可以减少 熔体通过弯管时,管壁与管中心温度及停留时间 的差别。
➢ 在较新型的螺杆挤出机中,往往采用特殊设计的 混炼头来代替静态混合器。混炼头的主要作用是 改变螺杆沟槽中挤出的熔体的流线,使熔体进一 步均匀化
聚酯纤维
聚酯短纤
聚酯纤维的分类
• 从应用领域来划分
–服用 –装饰用 –产业用 –2000年的比例68:19:13 –2005年的比例54:33:13
聚酯纤维的生产工艺及技术
❖聚酯纤维原料的生产技术及工艺 ❖聚酯纤维的生产技术及工艺
聚酯纤维原料的生产技术
• PET原料: – 对苯二甲酸 – 乙二醇(或环氧乙烷)
We=KP,式中,K为平衡常数,P为平衡蒸汽压。 升高温度和增加干燥介质的流动有利于干燥过程。
干燥过程
➢干燥分为两个阶段,即预结晶阶段和高温 干燥阶段
➢预结晶温度和时间
– 沸腾床:温度可高至160~180oC,时间8~15min。 – 搅拌式充填:温度120~140oC,时间1~l.5小时。 – 转鼓干燥时,在120℃以下缓慢升温,预结晶时
• PET的制造大致可分为两个阶段 – 第一阶段是由基本原料对二甲苯、甲苯、邻 苯二甲酸酐合成中间体对苯二甲酸二甲酯 (DMT)或对苯二甲酸(PTA)。 – 第二阶段是由DMT或PTA与乙二醇(EG) 进行酯化或酯交换反应,生成聚酯单体对苯 二甲酸双β-羟乙酯(简称BHET或DGT) – 各种工艺路线的区别主要在前一阶段,即单 体的合成阶段。
聚酯纤维生产技术—聚酯短纤维的后加工
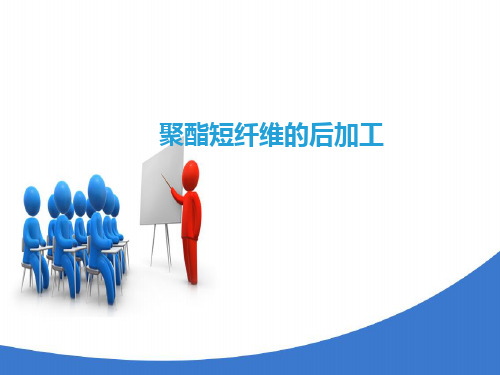
3、湿热拉伸:加热介质(油、热水、蒸汽),聚酯玻璃化温度降低(降低20℃), 有利于拉伸。
第一级拉伸:Ⅰ、Ⅱ段→拉伸应力较小→要求的加热温度较低→热水 含油剂)浴加 热
第二级拉伸:Ⅲ段→拉伸应力较大→要求的加热温度较高→过热蒸汽或沸水加热
拉伸的原理
1、拉伸曲线
• 通过拉伸使纤维的结构单元获得稳定的取向结构,达到提高成品纤维强度 的目的。
• 拉伸过程分子运动单元:链段、分子链
小尺 寸取 向
大尺 寸取 向
拉伸设备:五辊或七辊拉伸机,各道拉伸机之间 设置加热器(油浴加热、水浴加热、热水喷林、 蒸汽喷射)
LVD801型七辊拉伸机为例: 三道七辊拉伸机+一道七辊拉伸或回缩机 二、三道七辊拉伸机的每只拉伸辊上有一个毛 刷(清除毛丝) 每道七辊拉伸机上有1~2只橡皮压辊(可升降) 一道、二道七辊之间有热水(含油剂)浴拉伸 槽(淹没并加热纤维)——一级拉伸
拉伸的工艺条件
单击此处添 加文本具体 内容
单击此处添 加文本具体 内容
单击此处添 加文本具体 内容
单击此处添 加文本具体 内容
单击此处添 加文本具体 内容
拉伸温度
拉伸速度 拉伸倍数及分配 拉伸点的控制 拉伸介质的选用
卷曲工艺控制
04
卷曲目的
增加纺纱时纤维之间的摩擦 力和抱合力
提高纤维和纺织品的弹性, 改善织物的抗皱性;
聚酯短纤维的后加工
CONTENT
07 06
打包 切断
05
热定型工艺控制
04
卷曲工艺控制
03
拉伸工艺控制
02
初生纤维的存放和集束
01
后加工的意义及工艺流程
聚酯纤维后加工

2、工艺 (1)超喂率:变形喷嘴前后速度表征。 超喂提高蓬松性,超喂率提高, 纤度增加,强度下降. 333dtex, 超喂率14.7-30%, 纤度3.9-11.7%, 而强力下降达60%。 :毛圈过大,松散,均匀性和稳定性变差; 过低:不利于丝条的缠结成圈。 (2)热辊温度和拉伸比:变形热辊温度130-150℃,拉伸比1.51.7 (3)定型温度和时间:定型温度越高(190-230),丝圈缠结越紧, 变形丝结构稳定性越好,沸水收缩率越低。 (4)加工速度和张力:原丝线密度愈高,加工速度应愈低。一般 500-700m/min. 变形区较低张力有利于开松、卷曲;稳定区控制较低张力,有利于纤维内应 力松弛,提高变形效果。5.5-8.0cN (5)空气压力:提高,有利于丝圈形成,使变形效果增加,600900kPa. (6)给湿量:变形前给水润湿,吸去丝上部分油剂,并起增塑作 用,每喷嘴0.8-1.0L/h.
PET卷绕丝双折射与存放时间关系
2、拉伸设备 三道七辊拉伸机 湿热拉伸工艺,加热方式——热水喷淋、蒸 汽喷射、油浴、水浴加热
3、拉伸工艺条件 一级和两级拉伸, 间歇集束两级拉伸 拉伸温度: 提高,屈服应力和拉伸应力减小,有利于拉伸, 第一级拉伸——Tg以上,70-90℃; 第二级拉伸——第一级拉伸后,已有一定程度取向和结晶,Tg也随之 提高,进行第二级拉伸时就应有更高温度。150(棉)-180(毛)℃ 拉伸速度: 拉伸速度提高,拉伸应力提高;可提高拉伸温度,降低拉伸应力,提 高拉伸速度;但当拉伸速度超过某一值后,应力又会降低,因为拉伸 过程发热,使纤维实际温度升高,降低拉伸应力。 拉伸丝束喂入速一般30-45m/min,出丝速度一般为140-180m/min(棉), 毛型要低些。
涤纶短纤
打包机
涤纶短纤维后加工工艺与质量控制—集束和拉伸

聚合物结构对应力—应变行为的影响
25
• ④熔纺卷绕丝其它结构因素的影响
• 卷绕丝内含较大的气泡或固体粒子时,
• 卷绕丝内出现裂缝或纤度波动时
可拉伸性↓
• ⑤湿纺冻胶体凝固丝网络结构的影响
• 凝固丝网络骨架越细密
最大拉伸比↑
• 凝固丝的溶胀度↑
最大拉伸比↑
•
可拉伸性先↑后↓
聚丙烯纤维在60℃下拉伸时,密度ρ和熔融热Hc对拉伸比的关系 A—经热处理的试样 b—拉伸前骤冷的试样
34
• (2)强度、拉伸模量和屈 服应力
• 纤维的强度、拉伸模量和 屈服应力随拉伸倍数而↑, 增大速度不同
各种纤维的强度对拉伸倍数R的依赖关系
1—粘胶纤维 2—聚乙烯醇纤维 3—聚甲醛纤维 4—PVA与乙烯基己内酰 5—聚酰胺和聚酯纤维 6—聚丙烯腈纤维 7—乙烯醇与N-乙烯基吡咯烷
(t)
1
2
3
e
E1
e
E2
(1 e t / 2 ) t
3
e
(1)普弹形变1
1=e/E1
• 普弹形变是大分子主链的键角和键长受力后发生形变的反映
• 普弹形变与应力同相位,瞬间发生和瞬间回复
• 普弹形变的弹性模量E1很大,形变量1很小 • 总形变的1%,与时间无关
12
• (2)高弹形变2
2 (t)
初生纤维线密度的影响 线密度↓等效于T ↑ 线密度↑ σ*↑N ↑,等效于T ↓
29
(三) 拉伸过程中纤维结构与性能的变化
• 1. 拉伸过程中纤维超分子结构的变化 • (1) 取向度的提高 • ①不同取向结构单元
非晶态高聚物的拉伸作用 大尺寸取向
- 1、下载文档前请自行甄别文档内容的完整性,平台不提供额外的编辑、内容补充、找答案等附加服务。
- 2、"仅部分预览"的文档,不可在线预览部分如存在完整性等问题,可反馈申请退款(可完整预览的文档不适用该条件!)。
- 3、如文档侵犯您的权益,请联系客服反馈,我们会尽快为您处理(人工客服工作时间:9:00-18:30)。
的影响。
化学纤维的卷曲分三种类型:化学卷曲 (较少采用)、物理卷曲(如复合纤维的 卷曲)和机械卷曲。机械卷曲是一种施加 机械力于已成形纤维而造成卷曲的方法。
目前较为广泛采用的为填塞箱法。这种 方法制得的纤维弯折小,抱合力好,而且 设备紧凑,卷曲效果比较明显。在实际生 产中被广泛采用。
丝束就以基本不
变的形态在两卷
曲刀的刀面上逐
渐向前滑移。
⒊蒸汽预热箱
经过拉伸后的丝束,弹性模量E很大,不 利于丝束的卷曲,即使卷曲也不稳固;又因 丝束含湿低,卷曲不充分,因此在丝束进入
卷曲机前必须先经蒸汽预热箱给湿预热,以
降低丝片的弹性模量和提高其湿度。
二、切断机
涤纶等短纤维通常是与棉、羊毛以及 其他化学纤维混纺的,根据所纺纤维品种 长度的不同,要将涤纶丝束切断成相应的 长度。
压辊系铸造结构,外包丁腈橡胶或聚氨酯橡 胶,以提高对丝束的握持力,减少打滑现象。
压辊安排方式有两种:上压辊和下压辊。上 压辊依靠丝束的张力或气缸的压力使压辊压在牵 伸辊上。下压辊两端两只气缸压力由下向上紧紧 地压住牵伸辊,压紧力可调。
⑷浸渍辊
在第一台牵伸机和第二台牵伸机上分别有一
浸渍辊,浸在水浴槽中,第一台牵伸机的浸渍辊 内可通冷却水,作用是控制丝束的拉伸点,防止 因拉伸潜热的作用使拉伸点前移,从而达到稳定 拉伸的效果。
长边轴传动是用一台电机带动一根长轴 经圆锥齿轮减速箱及多档齿轮减速箱(又 称排档箱)等传递到各台牵伸机等,以达 到同步传动。
长边轴传动的优点: ⑴传动平稳可靠,可以低速起动; ⑵在低速运转或正常运转时都能使各道牵
伸机同步,从而保证拉伸倍数的稳定; ⑶由于长边轴传动能在低速运行,因此便
于生头和除去毛 丝,操作方便。
⑵装设加热器
第一级拉伸温度控制在Tg以上,温度过高过 低都会影响拉伸点。为了稳定拉伸点,一般在第 一、第二台牵伸机之间设有水浴或油浴加热器, 使纤维内部形成一稳定的温度梯度。当纤维的实 际温度上升至所对应的屈服应力时则出现细颈。 此外,纤维在拉伸过程中会放出大量的热能,若 没有合适的加热介质将发出的热量及时地扩散出 去,则会因温度的变化,导致纤维的应力随之变 化,拉伸点产生移动。所以,装设加热器是控制 拉伸点的有效方法。
在拉伸过程中,纤维的形变是一个松弛过 程,需要一定的时间,拉伸速度太快,形变来 不及发展,造成纤维内应力增加;
拉伸速度太低,拉伸取向效果差,纤维 强度不高,所以一是要设定拉伸速度的最 佳值,二是拉伸速度要始终恒定。为此通 常采用长边轴传动方式和提高电气控制元 件的精度,来控制各台牵伸机的速度恒定, 确保拉伸点的固定。
长边轴传动的缺点:长边轴的动力传递 结构复杂,占地面积较大,且不易改变各 道拉伸的工艺参数。
长边轴传动的机台有一、二、三、四道 拉伸机、紧张热定型及上油机。联合机的 运转速度由第三道牵伸机辊筒表面线速度 代表(m/min)。
联合机的加工能力是指成品纤维的总 (特)数。
二、牵伸机
短纤维和长丝一样,纺丝成形得到的初
紧张热定型机
松弛热定型机
圆网松弛热定型机
⒉联合机的传动 联合机(的设计)应能满足下列要求:
⑴前后道机器应能同步运转; 例:牵伸机组各机器间往往用长边轴传动,
各机器可准确地达到同步运转的要求。 ⑵便于操作与维修; ⑶应有很高的可靠性。
联合机是高产的连续生产线,只要一处出 了故障不能及时排除,便可造成全线停产,造 成重大的经济损失。
⑶采用橡胶压辊和增加拉伸辊数目
丝束通过牵伸机上牵伸辊时,纤维与金属 辊表面存在打滑现象。由滑动摩擦引起纤维的 温度升高,影响拉伸点位置的变化。故在牵伸 机上采用橡胶压辊和增加牵伸辊数。一般五辊 牵伸机打滑系数为7%~10%,而七辊牵伸机 打滑系数仅为3%,有利于控制拉伸点和拉伸 倍数。
⑷采用长边轴传动和提高电气控制精度
第五章 短纤维后加工设备
第一节 短纤维后加工联合机 与牵伸机
一、短纤维后加工联合机
⒈联合机的组成
短纤维在纺丝成形后,必须经过一系列 后处理才能成为优良的纺织纤维。短纤维 后加工的工艺路线和设备都与长丝截然不 同,它是将几十万甚至几百万根单丝集合 成一股相当粗的丝束,然后在数台牵伸机 之间进行拉伸,以及进行其他的后处理。
打包机的作用是将松散的纤维打成一定重量、一
定体积的包装。
机械传动打包机国际上早已淘汰,我国也基本不 再生产。目前广泛采用的多为双箱液压打包机,由三 个部分组成,即:打包称量机、皮带输送机和打包主 机。
切断后的短纤维由皮带夹送到打包机顶部,再落 入称量斗分批称量。称量后的纤维送入料仓进行预压 (即将纤维分层压紧),预压的次数和称量数相同。 当纤维达到一定量后提起箱体,并将箱体绕中心轴旋 转1800至主压头下。落箱后,在主压油缸作用下,纤 维被进一步强制压紧至所需大小的体积,用铁丝捆紧, 卸压后由推包汽缸顶出捆紧的纤维包。
生纤维需在恒温恒湿的条件下存放一段时 间,然后再集束浸渍以施加有一定的预张
力后进行拉伸。 短纤维是采用集中拉伸,即把几十万根
单丝集中成粗丝束,在牵伸机上以50~ 300m/min的线速度拉伸成一定细度和均匀 度的纤维,从而获得足够的强度和合适的 伸度,以适应后加工的要求。
⑴丝束进入拉伸机前应具有一定的预张力; ⑵牵伸辊对丝束的握持力尽可能大,防止 打滑; ⑶能够有效的控制拉伸点和拉伸温度; ⑷应配置防绕辊装置; ⑸应确保丝束上油率的均匀稳定。
断刀。随着刀盘的回 转,切断刀正好从沟 槽中通过,将丝束切
断。切断后的纤维顺 着沟轮下的喇叭口落 入风管被吸走。
⑴牵引辊
作用是夹紧丝束、并将其送入切断机内。 主动牵引辊是一金属辊,表面镀硬铬;被 动牵引辊则表面包覆橡胶,依靠气缸压力 夹紧丝束,使其在拉紧状态下喂入沟轮。
⑵沟轮
起着夹紧丝束的作用。由轮辐和外圈组 成,外圈材料为铸钢基体,表面包覆丁腈 橡胶,以增加其握持力。外圈上开有等分 沟槽,常用槽数有45、60、64、69四种, 以适应切断不同长度的纤维时选用。
⒈牵伸机的组成
⑴牵伸箱
牵伸箱通常是铸铁件(也有用钢结构的), 在箱内装有牵伸轴、传动齿轮,还装有润滑油 装置,分别对各轴承及齿轮进行润滑。而牵伸 辊、压辊、缠辊自停装置、浸渍辊等则装在箱 体外侧。
⑵牵伸辊部件
一台牵伸机通常由五个或七个牵伸辊组成 一组,它们直径相同,依靠两台牵伸机的速 度差来完成丝束的拉伸,因此提高牵伸辊对
⑸缠辊自停装置
工作原理是利用空电变换器将压缩空气 讯号转为电讯号。
⒉拉伸点的控制
纤维在拉伸过程中通常把出现细颈的位
置称为拉伸点。为了获得线密度和其他物 理机械性能均匀的纤维,拉伸点位置必须 稳定。如果拉伸点位置移动,则会出现拉
伸不足或毛丝,造成纤维粗细不一,染色 不均。
由拉伸机理可知,拉伸点的位置与拉伸 温度、拉伸倍数、拉伸速度和拉伸张力等
因素密切相关,因此必须从拉伸工艺条件 及拉伸设备方面来严格保证控制拉伸点位 置。
* ⑴配置浸渍辊
丝束通过第一台牵伸机的几个牵伸辊后,
纤维逐渐被张紧,当其张力达到纤维的屈 服应力时则出现细颈。为了使拉伸点不发
生在拉伸辊的张力坡度上,把第一台牵伸 机的最后一辊设定为浸渍辊,浸渍辊内部 通有冷却水,从而降低丝束温度,增大纤 维的屈服应力,拉伸点就不会提前发生在 牵伸辊上。
第一次卷曲:上下卷曲轮夹持丝束向卷曲 箱内推进,此时丝片的下面一边W点紧靠下 辊面,前方则已受阻不能挺直前进,但后方 丝束继续进入箱内,而丝片上方与上辊面间 已有一定的空隙,丝片凸向上辊面开始弯曲, 直到V点碰住为
止。这是弯曲的初步
形成,弯折长度为
1㎜左右。
随着丝片不断前进,两辊面距离逐渐增大,V、 W两点各自紧靠上下辊面前进,当进到位置b时, V点仍与上辊面紧贴,但下边与下辊面也有一定 的空隙,于是下边的U点开始弯曲,凸向下辊面, 直到碰住为止。一上一下形成一个弯折波。当丝 片进到位置c、d时,丝片再发生弯折。这样在两 卷曲轮夹持点前进方向8~11㎜距离内完成了第 一次卷曲。
棉型短纤维切断长度为38㎜,并要求 均匀度好。中长纤维用来与粘胶短纤维或 与其他纤维混纺,切断长度为51~76㎜。 毛型短纤维则要求纤维较长,用于粗梳毛 纺的切断长度为64~76㎜,用于精梳毛纺 的切断长度为89~114㎜。
⒈沟轮式切断机
丝束通过牵引辊 喂入切断机,并由一 对沟轮将丝束夹住。 沟轮上开有许多沟槽, 在两沟轮转动的垂直 平面上有一回转刀盘, 在刀盘上装有数把切
短纤维采用这种集束拉伸的优点是机台效
率高,大大减少机器台数和操作人员,减 少占地面积,并提高了劳动生产率。
除了因纤维品种和具体条件的不同,后 加工的工艺流程和设备基本上都相同。以 高强低伸型涤纶短纤维为例,其工艺流程 如下:
短纤维后加工联合机是由集束架、牵伸机、 紧张热定型机、卷曲机、松弛热定型机、切断 机和打包机等单元组成。
⑶切断刀和刀盘
切断刀刀盘最多能装6把刀,所装刀数要与 纤维切断长度相适应。切断机的刀盘轴倾角一 般取6°,这样在切断过程中,使刀和丝束形 成顺切的情况,以减少丝束对刀口的正面冲击, 降低摩擦热,避免产生超长纤维。
⑷加压系统
⑸传动系统
⒉压轮式切断机(亦称刀盘式)
随着加工速度、丝束总线密度和产品质 量要求的不断提高,上述沟轮式切断机的 缺点变得越来越明显。这种切断机的刀盘 上最多装6把刀,工作效率较低,如用提高 加工速度的办法来提高生产率,则沟轮和 刀盘的转速将增大,
生第二次弯曲。第
一次弯曲时单丝在
弯折,而第二次弯
曲时则是弯折丝片。
第三次卷曲:已形成两次卷曲的弯折丝片, 从25㎜处再往前进,由于两卷曲轮间的间距继续 增大,而且这增大远比以前更为剧烈,丝束的既
成形状已不再能填满新的空间了。而前方丝束 的阻力和后方丝束的推力仍迫使丝束改变自己