PCB生产工艺资料-化学镀金
PCB电镀工艺介绍
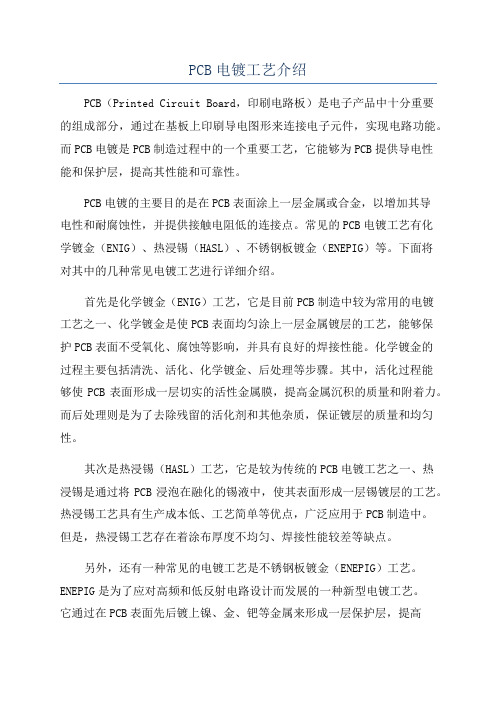
PCB电镀工艺介绍PCB(Printed Circuit Board,印刷电路板)是电子产品中十分重要的组成部分,通过在基板上印刷导电图形来连接电子元件,实现电路功能。
而PCB电镀是PCB制造过程中的一个重要工艺,它能够为PCB提供导电性能和保护层,提高其性能和可靠性。
PCB电镀的主要目的是在PCB表面涂上一层金属或合金,以增加其导电性和耐腐蚀性,并提供接触电阻低的连接点。
常见的PCB电镀工艺有化学镀金(ENIG)、热浸锡(HASL)、不锈钢板镀金(ENEPIG)等。
下面将对其中的几种常见电镀工艺进行详细介绍。
首先是化学镀金(ENIG)工艺,它是目前PCB制造中较为常用的电镀工艺之一、化学镀金是使PCB表面均匀涂上一层金属镀层的工艺,能够保护PCB表面不受氧化、腐蚀等影响,并具有良好的焊接性能。
化学镀金的过程主要包括清洗、活化、化学镀金、后处理等步骤。
其中,活化过程能够使PCB表面形成一层切实的活性金属膜,提高金属沉积的质量和附着力。
而后处理则是为了去除残留的活化剂和其他杂质,保证镀层的质量和均匀性。
其次是热浸锡(HASL)工艺,它是较为传统的PCB电镀工艺之一、热浸锡是通过将PCB浸泡在融化的锡液中,使其表面形成一层锡镀层的工艺。
热浸锡工艺具有生产成本低、工艺简单等优点,广泛应用于PCB制造中。
但是,热浸锡工艺存在着涂布厚度不均匀、焊接性能较差等缺点。
另外,还有一种常见的电镀工艺是不锈钢板镀金(ENEPIG)工艺。
ENEPIG是为了应对高频和低反射电路设计而发展的一种新型电镀工艺。
它通过在PCB表面先后镀上镍、金、钯等金属来形成一层保护层,提高PCB的可靠性和耐腐蚀性。
ENEPIG工艺具有良好的焊接性能、热稳定性和阻焊层附着力,非常适合于高频电路和复杂设计的PCB。
除了上述介绍的几种电镀工艺外,还有很多其他的电镀工艺,例如有机覆盖层镀金(OSIG)、沉金(ENIG)等。
每种电镀工艺都有各自的特点和适用范围,根据PCB设计的要求和产品的特性选择合适的电镀工艺非常关键。
PCB电镀镍金工艺介绍

PCB电镀镍金工艺介绍(一)深圳特区横岗镇坳背村太平电路科技厂李勇成一、PCB电镀镍工艺1、作用与特性P C B上用镀镍来作为贵金属和贱金属的衬底镀层,对某些单面印制板,也常用作面层。
对于重负荷磨损的一些表面,如开关触点、触片或插头金,用镍来作为金的衬底镀层,可大大提高耐磨性。
当用来作为阻挡层时,镍能有效地防止铜和其它金属之间的扩散。
哑镍/金组合镀层常常用来作为抗蚀刻的金属镀层,而且能适应热压焊与钎焊的要求,唯读只有镍能够作为含氨类蚀刻剂的抗蚀镀层,而不需热压焊又要求镀层光亮的PCB,通常采用光镍/金镀层。
镍镀层厚度一般不低于2.5微米,通常采用4-5微米。
PCB低应力镍的淀积层,通常是用改性型的瓦特镍镀液和具有降低应力作用的添加剂的一些氨基磺酸镍镀液来镀制。
我们常说的PCB镀镍有光镍和哑镍(也称低应力镍或半光亮镍),通常要求镀层均匀细致,孔隙率低,应力低,延展性好的特点。
2、氨基磺酸镍(氨镍)氨基磺酸镍广泛用来作为金属化孔电镀和印制插头接触片上的衬底镀层。
所获得的淀积层的内应力低、硬度高,且具有极为优越的延展性。
将一种去应力剂加入镀液中,所得到的镀层将稍有一点应力。
有多种不同配方的氨基磺酸盐镀液,典型的氨基磺酸镍镀液配方如下表。
由于镀层的应力低,所以获得广泛的应用,但氨基磺酸镍稳定性差,其成本相对高。
典型的氨基磺酸镍电镀镀液配方成分克/升高速镀液氨基磺酸镍,Ni(SO3NH2)2280~400 400~500硼酸,H3BO340~50 40g/l阳极活化剂60—100 60—100 润湿剂1~5ml/l 适量去应力剂(添加剂)适量根据需要而定操作条件温度55度C阴极电流密度(A/dm2) 1.5~8搅拌压缩空气加阴极移动加镀液循环PCB电镀镍金工艺介绍(二)深圳特区横岗镇坳背村太平电路科技厂李勇成二、PCB电镀金工艺1、作用与特性PCB上的金镀层有几种作用。
金作为金属抗蚀层,它能耐受所有一般的蚀刻液。
印制电路板化学镀镍金工艺知识

印制电路板化学镀镍金工艺知识在一个印制电路板的制造工艺流程中,产品最终之表面可焊性处理,对最终产品的装配和使用起着至关重要的作用。
综观当今国内外,针对印制电路板最终表面可焊性涂覆表面处理的方式,主要包括以下几种:Electroless Nickel and Immersion Gold (1)热风整平;(2)有机可焊性保护剂;(3)化学沉镍浸金;(4)化学镀银;(5)化学浸锡;(6)锡/ 铅再流化处理;(7)电镀镍金;(8)化学沉钯。
其中,热风整平是自阻焊膜于裸铜板上进行制作之制造工艺(SMOBC采用以来,迄今为止使用最为广泛的成品印制电路板最终表面可焊性涂覆处理方式。
对一个装配者来说,也许最重要的是容易进行元器件的集成。
任何新印制电路板表面可焊性处理方式应当能担当N次插拔之重任。
除了集成容易之外,装配者对待处理印制电路板的表面平坦性也非常敏感。
与热风整平制程所加工焊垫之较恶劣平坦度有关的漏印数量,是改变此种表面可焊性涂覆处理方式的原因之一。
镀镍/金早在70年代就应用在印制板上。
电镀镍/ 金特别是闪镀金、镀厚金、插头镀耐磨的Au-Co 、Au-Ni 等合金至今仍一直在带按键通讯设备、压焊的印制板上应用着。
但它需要“工艺导线”达到互连,受高密度印制板SMT安装限制。
90年代,由于化学镀镍/金技术的突破,加上印制板要求导线微细化、小孔径化等,而化学镀镍/金,它具有镀层平坦、接触电阻低、可焊性好,且有一定耐磨等优点,特别适合打线(Wire Bonding)工艺的印制板,成为不可缺少的镀层。
但化学镀镍/金有工序多、返工困难、生产效率低、成本高、废液难处理等缺点。
铜面有机防氧化膜处理技术,是采用一种铜面有机保焊剂在印制板表面形成之涂层与表面金属铜产生络合反应,形成有机物- 金属键,使铜面生成耐热、可焊、抗氧化之保护层。
目前,其在印制板表面涂层也占有一席之地,但此保护膜薄易划伤,又不导电,且存在下道测试检验困难等缺点。
pcb电镀工艺流程

pcb电镀工艺流程
《PCB电镀工艺流程》
在印刷电路板(PCB)制造过程中,电镀工艺是一个重要的步骤。
它可以增强PCB表面的导电性,提高焊接性能,并保护PCB
免受腐蚀。
下面将介绍PCB电镀工艺的主要流程。
首先,PCB经过表面处理后,会进入清洗环节。
在这一步骤中,PCB表面的污垢、油脂和其他杂质将被清洗干净,以保
证后续的电镀能够顺利进行。
接下来是化学镀铜的工序。
PCB会被浸泡在含有铜盐和其他
化学药剂的溶液中,通过电化学反应使铜层沉积在PCB表面。
这一步骤能够实现PCB表面的化学镀铜,从而增加其导电性。
然后是化学镀镍工序。
在这一步骤中,PCB被浸泡在镍盐和
其他化学物质的溶液中,通过电化学反应使镍层沉积在PCB
表面。
这一步骤可以提高PCB的硬度和耐腐蚀性能。
最后是化学镀金工序。
在这一步骤中,PCB会被浸泡在含有
金盐和其他化学药剂的溶液中,通过电化学反应使金层沉积在PCB表面。
化学镀金可以提高PCB的焊接性能,并增加其耐
腐蚀性能。
总的来说,PCB电镀工艺流程包括清洗、化学镀铜、化学镀
镍和化学镀金等步骤。
这些工序能够增强PCB表面的性能,
保护PCB免受腐蚀,从而提高PCB的可靠性和使用寿命。
pcb镀金常用工艺
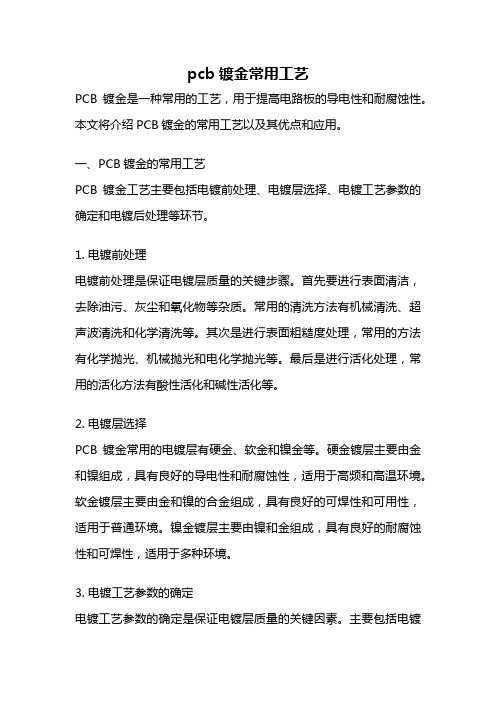
pcb镀金常用工艺PCB镀金是一种常用的工艺,用于提高电路板的导电性和耐腐蚀性。
本文将介绍PCB镀金的常用工艺以及其优点和应用。
一、PCB镀金的常用工艺PCB镀金工艺主要包括电镀前处理、电镀层选择、电镀工艺参数的确定和电镀后处理等环节。
1. 电镀前处理电镀前处理是保证电镀层质量的关键步骤。
首先要进行表面清洁,去除油污、灰尘和氧化物等杂质。
常用的清洗方法有机械清洗、超声波清洗和化学清洗等。
其次是进行表面粗糙度处理,常用的方法有化学抛光、机械抛光和电化学抛光等。
最后是进行活化处理,常用的活化方法有酸性活化和碱性活化等。
2. 电镀层选择PCB镀金常用的电镀层有硬金、软金和镍金等。
硬金镀层主要由金和镍组成,具有良好的导电性和耐腐蚀性,适用于高频和高温环境。
软金镀层主要由金和镍的合金组成,具有良好的可焊性和可用性,适用于普通环境。
镍金镀层主要由镍和金组成,具有良好的耐腐蚀性和可焊性,适用于多种环境。
3. 电镀工艺参数的确定电镀工艺参数的确定是保证电镀层质量的关键因素。
主要包括电镀液的成分和浓度、电流密度、电镀时间和温度等。
电镀液的成分和浓度应根据不同的电镀层选择确定。
电流密度和电镀时间应根据电镀层的厚度和均匀性要求确定。
温度的控制对电镀层的质量也有重要影响,通常要求在一定的范围内保持恒定。
4. 电镀后处理电镀后处理是保证电镀层质量的重要环节。
主要包括清洗、干燥和包装等。
清洗的目的是去除电镀液残留物和杂质,常用的方法有水洗、酸洗和碱洗等。
干燥的目的是除去水分,常用的方法有自然干燥、热风干燥和吸湿剂干燥等。
包装的目的是保护电镀层,常用的方法有真空包装、泡沫包装和气密包装等。
二、PCB镀金的优点PCB镀金具有以下优点:1. 提高导电性:金属电镀层能够提高电路板的导电性,降低导电阻抗,提高信号传输效率。
2. 增强耐腐蚀性:金属电镀层能够有效防止电路板受到氧化、腐蚀和污染等环境因素的侵蚀,延长电路板的使用寿命。
3. 增加可焊性:金属电镀层能够提高电路板与焊接材料之间的附着力,增加焊接的牢固度和可靠性。
pcb工艺镀金和沉金的区别

pcb工艺镀金和沉金的区别镀金和沉金的别名分别是什么?镀金:硬金,电金沉金:软金,化金别名的由来:镀金:通过电镀的方式,使金粒子附着到pcb板上,所有叫电金,因为附着力强,又称为硬金,内存条的金手指为硬金,耐磨,绑定的pcb一般也用镀金沉金:通过化学反应,金粒子结晶,附着到pcb的焊盘上,因为附着力弱,又称为软金工艺先后程序不同:镀金:在做阻焊之前做此工艺,因为镀金需要两个电极,一个是pcb板子,一个是缸槽,如果pcb板做完阻焊,就不能导电了,也就不能镀上金沉金:在做阻焊之后,和沉锡一样,化学方法,有漏铜皮的地方就回附着上金镀金和沉金对贴片的影响:镀金:在做阻焊之前做,做过之后,有可能绿油清洗不干净,不容易上锡沉金:在做阻焊之后,贴片容易上锡镀金和沉金对电器方面的影响:镀金:镀金之前需要先镀一层镍,然后再镀一层金,金属层为铜镍金因为镍有磁性,对屏蔽电磁有作用沉金:直接在铜皮上面沉金,金属层为铜金,没有镍,无磁性屏蔽1. 6镀金和沉金的鉴别:镀金工艺因为pcb含有镍,所以有磁性,鉴别是镀金或者沉金时,可以使用磁铁吸引pcb板子,有吸引力为镀金,无吸引力为沉金另外颜色也有区别,沉金为金黄色,镀金:因为镀金面子大,一般都是镀的很薄,趋向于白色,当然也有镀的很厚的,也是金黄色,此时看焊盘不易分辨,那么就用小刀刮开阻焊层(绿油或者黑油其他颜色),漏出金属层,因为镀金工艺是镀整个pcb板,绿油下面的金属层为金镍铜的叠层,所以看上去是金黄色,如果镀层不厚,黄里透白,但是沉金工艺的层叠方式不同,阻焊层下面为铜,为红色(红铜的颜色)。
2.7如果对你有用请支持一下,您的支持是我的动力,谢谢。
PCB化学镍金及OSP工艺步骤和特性分析
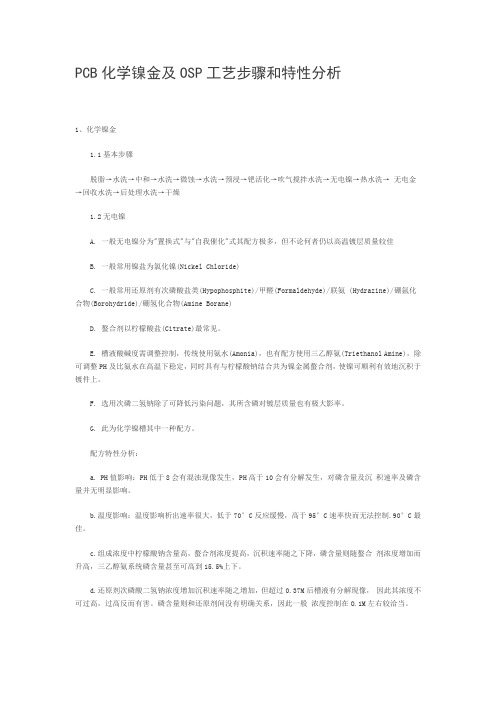
PCB化学镍金及OSP工艺步骤和特性分析1、化学镍金1.1基本步骤脱脂→水洗→中和→水洗→微蚀→水洗→预浸→钯活化→吹气搅拌水洗→无电镍→热水洗→ 无电金→回收水洗→后处理水洗→干燥1.2无电镍A. 一般无电镍分为"置换式"与"自我催化"式其配方极多,但不论何者仍以高温镀层质量较佳B. 一般常用镍盐为氯化镍(Nickel Chloride)C. 一般常用还原剂有次磷酸盐类(Hypophosphite)/甲醛(Formaldehyde)/联氨 (Hydrazine)/硼氩化合物(Borohydride)/硼氢化合物(Amine Borane)D. 螯合剂以柠檬酸盐(Citrate)最常见。
E. 槽液酸碱度需调整控制,传统使用氨水(Amonia),也有配方使用三乙醇氨(Triethanol Amine),除可调整PH及比氨水在高温下稳定,同时具有与柠檬酸钠结合共为镍金属螯合剂,使镍可顺利有效地沉积于镀件上。
F. 选用次磷二氢钠除了可降低污染问题,其所含磷对镀层质量也有极大影率。
G. 此为化学镍槽其中一种配方。
配方特性分析:a. PH值影响:PH低于8会有混浊现像发生,PH高于10会有分解发生,对磷含量及沉积速率及磷含量并无明显影响。
b.温度影响:温度影响析出速率很大,低于70°C反应缓慢,高于95°C速率快而无法控制.90°C最佳。
c.组成浓度中柠檬酸钠含量高,螯合剂浓度提高,沉积速率随之下降,磷含量则随螯合剂浓度增加而升高,三乙醇氨系统磷含量甚至可高到15.5%上下。
d.还原剂次磷酸二氢钠浓度增加沉积速率随之增加,但超过0.37M后槽液有分解现像,因此其浓度不可过高,过高反而有害。
磷含量则和还原剂间没有明确关系,因此一般浓度控制在O.1M左右较洽当。
e.三乙醇氨浓度会影响镀层磷含量及沉积速率,其浓度增高磷含量降低沉积也变慢,因此浓度保持约0.15M较佳。
PCB化学镀镍金工艺介绍(二)

PCB化学镀镍/金工艺介绍(二)二、化学镀金目前化学镀金工艺主要有二种,化学浸金和化学镀金两种。
3.1浸金---浸金就其机理而言应为置换反应即:Ni+2Au+→Ni2++2Au由于金和镍的标准电位相差较大,在合适的溶液中会发生金在镍表面置换沉积出来从反应式我们可以看出,浸金反应要进行必须要有镍层的存在,但随着置换出的金层厚度的增加,镍被完全覆盖后,浸金后反应就停止了。
一般浸金层的厚度较薄,通常为0.1微米,这即可降低成本,也可提高后续电子元件钎焊率。
如果刻意追求较高的浸金层的厚度,不但无益,反而有害,从浸金的原理可知,要想获得较厚的金层,就必须有镍的存在,所以只有在金层孔隙率较大的情况下达到这一点,而这样以后装配电子元件的钎焊性有不良影响。
常用化学浸金的配方与工艺条件:氯化铵————————150克/升柠檬酸氢二铵—————100克/升氰化亚金钾——————2克/升稳定剂————————适量温度—————————大于90度cPH —————————4.03.2化学镀金:化学镀金的原理是利用还原剂,将金还原后均匀沉积在被镀物上,达到所需要的厚度(目前化学镀Ni-P-贵金属Au已进入实用商品化阶段。
这类镀层称多元合金镀层、三合一镀层。
所以金厚度可达15μ″以上)-。
其反应式:Au++Red→Au0+ox 工艺组分如下:金(以氰化亚金钾形式加入)———0.5-2克/升柠檬酸铵————————————40-60克/升氯化铵—————————————70-80克/升偏亚流酸钾(钠)————————10-15克/升次亚磷酸钠———————————10-15克/升PH———————————————4.5-5.8温度——————————————90度c四、化学镀镍/金工艺简介:4.1 工艺流程:阻焊膜后裸铜电路板上板→酸性除油→两级水洗→3%过流酸盐预浸(微蚀)→两级水洗→活化处理→催化→后浸→两级水洗→化学镀镍→两级水洗→化学金→金回收→水洗→热去离子水洗→下架→吹干4.2 除油处理—化学镀镍/金前处理宜采用酸性除油液,主要要求其除油能力强,且容易水洗,不能含有络合能力强的络合剂、护铜剂,更不可加入铜面防氧化剂。
- 1、下载文档前请自行甄别文档内容的完整性,平台不提供额外的编辑、内容补充、找答案等附加服务。
- 2、"仅部分预览"的文档,不可在线预览部分如存在完整性等问题,可反馈申请退款(可完整预览的文档不适用该条件!)。
- 3、如文档侵犯您的权益,请联系客服反馈,我们会尽快为您处理(人工客服工作时间:9:00-18:30)。
其他焊墊表面處理(OSP,化學鎳金,)14.1前言錫鉛長期以來扮演著保護銅面,維持焊性的角色,從熔錫板到噴錫板,數十年光陰至此,碰到幾個無法克服的難題,非得用替代製程不可:A.Pitch太細造成架橋(bridging)B.焊接面平坦要求日嚴C.COB(chip on board)板大量設計使用D.環境污染本章就兩種最常用製程OSP及化學鎳金介紹之14.2OSPOSP是Organic Solderability Preservatives的簡稱,中譯為有機保焊膜,又稱護銅劑,英文亦稱之Preflux,本章就以護銅劑稱之.14.2.1種類及流程介紹A.BTA(苯駢三氯唑):BENZOTRIAZOLEBTA是白色帶淡黃無嗅之晶狀細粉,在酸鹼中都很安定,且不易發生氧化還原反應,能與金屬形成安定化合物。
ENTHON將之溶於甲醇與水溶液中出售,作銅面抗氧化劑(TARNISH AND OXIDE RESIST),商品名為CU-55及CU-56,經CU-56處理之銅面可產生保護膜,防止裸銅迅速氧化。
操作流程如表。
B.AI(烷基咪唑)ALKYLIMIDAZOLE PREFLUX是早期以ALKYLIMIDAZOLE作為護銅劑而開始,由日本四國化學公司首先開發之商品,於1985年申請專利,用於蝕刻阻劑(ETCHING RESIST),但由於色呈透明檢測不易,未大量使用。
其後推出GLICOAT等,係由其衍生而來。
GLICOAT-SMD(E3)具以下特性:-與助焊劑相容,維持良好焊錫性-可耐高熱銲錫流程-防止銅面氧化操作流程如表。
C.ABI(烷基苯咪唑)ALKYLBENZIMIDZOLE由日本三和公司開發,品名為CUCOAT A,為一種耐濕型護銅劑。
能與銅原子產生錯合物(COMPLEX COMPOUND),防止銅面氧化,與各類錫膏皆相容,對焊錫性有正面效果。
操作流程如表。
D.目前市售相關產品有以下幾種代表廠家:醋酸調整系統:GLICOAT-SMD(E3)OR(F1)WPF-106A(TAMURA)ENTEK106A(ENTHON)MEC CL-5708(MEC)MEC CL-5800(MEC)甲酸調整系統:SCHERCOAT CUCOAT AKESTER大半藥液為使成長速率快而升溫操作,水因之蒸發快速,PH控制不易,當PH提高時會導致MIDAZOLE不溶而產生結晶,須將PH調回。
一般採用醋酸(ACETIC ACID)或甲酸(FORMIC ACID)調整。
14.2.2有機保焊膜一般約0.4µm的厚度就可以達到多次熔焊的目的,雖然廉價及操作單純,但有以下缺點:A.OSP透明不易測量,目視亦難以檢查B.膜厚太高不利於低固含量,低活性免洗錫膏作業,有利於焊接之Cu6Sn5IMC也不易形成C.多次組裝都必須在含氮環境下操作D.若有局部鍍金再作OSP,則可能在其操作槽液中所含的銅會沉積於金上,對某些產品會形成問題E.OSP Rework必須特別小心14.3化學鎳金14.3.1基本步驟脫脂→水洗→中和→水洗→微蝕→水洗→預浸→鈀活化→吹氣攪拌水洗→無電鎳→熱水洗→無電金→回收水洗→後處理水洗→乾燥.14.3.2無電鎳A.一般無電鎳分為"置換式"與"自我催化"式其配方極多,但不論何者仍以高溫鍍層品質較佳B.一般常用的鎳鹽為氯化鎳(Nickel Chloride)C.一般常用的還原劑有次磷酸鹽類(Hypophosphite)/甲醛(Formaldehyde)/聯氨(Hydrazine)/硼氬化合物(Borohydride)/硼氫化合物(Amine Borane)D.螯合劑以檸檬酸鹽(Citrate)最常見E.槽液酸鹼度需調整控制,傳統使用氨水(Amonia),也有配方使用三乙醇氨(Triethanol Amine),除可調整PH及比氨水在高溫下穩定,同時具有與檸檬酸鈉結合共為鎳金屬螯合劑,使鎳可順利有效地沉積於鍍件上F.選用次磷二氫鈉除了可降低污染問題,其所含的磷對鍍層品質也有極大影率G.此為化學鎳槽的其中一種配方配方特性分析:a.PH值的影響:PH低於8會有混濁現像發生,PH高於10會有分解發生,對磷含量及沉積速率及磷含量並無明顯影響b.溫度的影響:溫度影響析出速率很大,低於70°C反應緩慢,高於95°C速率快而無法控制.90°C最佳c.組成濃度中檸檬酸鈉含量高,螯合劑濃度提高,沉積速率隨之下降,磷含量則隨螯合劑濃度增加而升高,三乙醇氨系統磷含量甚至可高到15.5%上下d.還原劑次磷酸二氫鈉濃度增加沉積速率隨之增加,但超過0.37M後槽液有分解現像,因此其濃度不可過高,過高反而有害。
磷含量則和還原劑間沒有明確關係,因此一般濃度控制在O.1M左右較洽當e.三乙醇氨濃度會影響鍍層的磷含量及沉積速率,其濃度增高磷含量降低沉積也變慢,因此濃度保持約0.15M較佳。
他除了可以調整酸鹼度也可作金屬螯合劑之用f.由探討得知檸檬酸鈉濃度作通當調整可有效改變鍍層磷含量H.一般還原劑大分為兩類:次磷酸二氫鈉(NaH2PO2H2O,Sodium Hypophosphate)系列及硼氫化鈉(NaBH4,Sodium Borohydride)系列,硼氫化鈉價貴因此市面上多以次磷酸二氫鈉為主一般公認反應為:[H2PO2]-+H2Oa H++[HPO3]2-+2H(Cat)-----------(1)Ni2++2H(Cat)a Ni+2H+---------------------------(2)[H2PO2]-+H(Cat)a H2O+OH-+P------------------(3)[H2PO2]-+H2Oa H++[HPO3]2-+H2-----------------(4)}銅面多呈非活化性表面為使其產生負電性以達到"啟鍍"之目的銅面採先長無電鈀的方式反應中有磷共析故,4-12%含磷量為常見。
故鎳量多時鍍層失去彈性磁性,脆性光澤增加,有利防鏽不利打線及焊接14.3.3無電金A.無電金分為"置換式鍍金"與"無電金"前者就是所謂的"浸鍍金"(lmmersion Gold plating)鍍層薄且底面鍍滿即停止。
後者接受還原劑供應電子故可使鍍層繼續增厚無電鎳。
B.還原反應示性式為:還原半反應:Au++e-+Au0氧化半反應式:Reda Ox+e-全反應式:Au++Red aAu0+Ox.C.化學鍍金配方除提供黃金來源的錯合物及促成還原的還原劑,還必須併用螯合劑、安定劑、緩衝劑及膨潤劑等才能發揮效用D.化學金配方組成及功用:E.部份研究報告顯示化學金效率及品質的改善,還原劑的選用是關鍵,早期的甲醛到近期的硼氫化合物,其中以硼氫化鉀最普遍效果也佳,若與他種還原劑並用效果更理想。
代表反應式如后:還原半反應:Au(CN)-2+e-a Au0+2CN-:氧化半反應式:BH4-+H2O a BH3OH-+H2BH3OH-+30H-a BO2-+3/2H2+2H20+3e-全反應式:BH3OH"+3AU(CN)z"+30H`-,BOz吐+/2Hz+2H,0+3Auo6CN-F.鍍層之沉積速率隨氫氧化鉀及還原劑濃度和槽溫提高而提升,但隨氰化鉀濃度增加而降低G.已商業化的製程操作溫度多為9O℃左右,對材料安定性是一大考驗H.細線路底材上若發生橫向成長可能產生短路的危險I.薄金易有疏孔易形成Galvanic Cell Corrosion K.薄金層疏孔問題可經由含磷後處理鈍化方式解決14.3.4製程重點:A.鹼性脫脂:為防止鈀沉積時向橫向擴散,初期使用檸檬酸系清潔劑。
後因綠漆有疏水性,且鹼性清潔劑效果又較佳,同時為防止酸性清潔劑可能造成的銅面鈍化,故採磷酸鹽系直鍊非離子性清潔劑,以容易清洗為訴求。
B.微蝕:其目的在去除氧化獲得新鮮銅面,同時達到絕對粗度約0.5-1.0µm之銅面,使得鍍鎳金後仍能獲得相當粗度,此結果有助打線時之拉力。
配槽以SPS150g/l加少量鹽酸,以保持氯離子約2OOppm為原則,以提高蝕刻效率。
C.銅面活化處理鈀約3ppm,操作約40℃,一分鐘,由於氯化鈀對銅面鈍化比硫化鈀為快,為得較好的鎳結合力自然是硫化鈀較適當。
由於鈀作用同時會有少量Cu+會產生,它可能還原成Cu也可能氧化成Cu++,若成為銅原子則沉積會影響鈀還原。
為使鈀還原順利須有吹氣攪拌,風量約為0./~O.15M3/M2*min以上,促使亞銅離子氧化並釋出電子以還原鈀,完成無電鎳沉積的動作。
D.活化後水洗:為防止鎳層擴散,清除線路間之殘鈀至為重要,除強烈水洗也有人用稀鹽酸浸漬以轉化死角的硫化鈀防止鎳擴散。
為促進鎳還原,熱水預浸將有助於成長及均勻性,其想法在提高活性使大小面積及高低電壓差皆因提高活性而使差異變小以達到均一的目的。
E.無電鎳:操作溫度85±5℃,PH4.5~4.8,鎳濃度約為4.9~5.1g/l間,槽中應保持鎳濃度低於5.5,否則有氫氧化沉澱的可能,若低於4.5g/l則鍍速會減慢,正常析出應以15µm/Hr,Bath loading則應保持約0.5~1.5)dM2/l,鍍液以5g/l為標準鎳量經過5個Turn即必須更槽否則析出鎳品質會變差。
鎳槽可以316不銹鋼製作,槽體事先以50%硝酸鈍化,並以槽壁外加電解陽極以防止鎳沉積,陰極可接於攪拌葉通以0.2~0.4A/M2(0.018~0.037AS F)低電流,但須注意不能在槳葉區產生氣泡否則代表電流太強或鎳鍍層太厚必須燒槽。
建浴操作應維持在PH=5~4.7間,可用NaOH或H2S04調整,PH低於4.8會出現混濁,槽液老化PH 操作範圍也會逐漸提高才能維持正常析出速度。
因線路底部為死角,易留置反應後所留的殘鹼,因此對綠漆可能產生不利影響,必須以加強攪拌及震動使殘鹼及氣泡去除。
F.無電鎳磷含量:一般無電鎳多以"次磷酸二氫鈉"為還原劑,故鍍層會含有一定量的磷約4~6%,且部份呈結晶狀。
苦含量在6~8%中含量則多數呈非結晶狀,當高達12%的以上則幾乎全呈非結晶組織。
就打線而言,中磷含量及硬度在500~600HV最佳,焊錫性也以9%最好。
一般在添加四回後析出磷含量就會達到10%應考慮換槽,打線用厚度應在130µ以上。
G.無電金:以檸檬酸為錯合劑的化學金槽,含金5g/l,槽體以PP為材質。
PH=5.1~5.3時可與銅作用,PH=4.5~4.8時可與鎳作用實行鍍金,PH可以檸檬酸調整之。
一般操作溫度在85℃,厚度幾乎會停止在2.5µ"左右,大約五分鐘就可達到此厚度,高的溫度固然可加快成長但因結晶粗反而防蝕能力較差。