OSP工艺和化金工艺比较
FPC板界业所用表面处理

一. 目前FPC板界业所用表面处理有以下几种1.OSP2.电镀锡铅3.电镀纯锡4.化学锡5.喷锡6.电镀金7. 化学金8.化学银二.他们之间的比较.1. 就价格讲: OSP<电镀锡铅<电镀纯锡<化学锡<喷锡<电镀金<化学金2. 就电镀原理解:OSP,化学锡,喷锡,化学金,四种表面处理:他们在制作过程中不需要任何导电线,就可以进行表面处理; 电镀锡铅,电镀纯锡,电镀金三种表面处理一定要有电镀线才可以进行电镀.不然形成不了回路就无法形成相应的表面处理.一般化学方式即不需要导电线的表面处理,其镀层一般较薄,镀不厚,他们一般是通过化学的置换反应方式进行的,但OSP 不一样是经过浸泡涂覆而成而一般电镀的表面处理可以根据客户不同要求进行电镀,其厚度分别如下:3 . 无铅制程:OSP,电镀纯锡,化学锡,电镀金,化学金均可以满足无铅制程,并满足欧盟提出的RoHS要求. 而电镀锡铅+喷锡不符合无铅要求,不满足欧盟提出ROHS要求而将逐渐淘汰.4 . 可焊性比较(公司内部实验所得)其实刚刚进行过表面处理后的新的铜面其焊接性最好,但因其在空气中易产生氧化,故在其表面常进行一些保护,就是我们长说的表面处理,从以上表面处理其可焊性比较如下:OSP>喷锡>电镀锡铅>化学金>电金>电镀纯锡>化学锡三. 电镀金一般情况电镀金都需要先镀镍,其作用是作为金层的底层的耐磨性,同时阻挡基体铜向金层扩散,镍层厚度一般不低于2-2.5um镍层目前分为硫酸镍与氨基磺酸镍,氨基磺酸镍内应力小较柔软,硫酸镍内应力大,在FPC行业一般不用硫酸镍.电镀金常分两种,一种是板面镀金和扦头镀金,板面镀金,其金层要求较薄镀层厚度一般为0.03um-0.1um具有良好的导电性和可焊性.扦头镀金俗称金手指镀金.镀的是硬金,这是一种含有CO,Ni,Fb,Sb等金属元素的合金镀层,合金元素的含量约为0.2%其硬度,耐磨性都高于纯金镀层,一般的镀金层要求较厚,当然金层越厚其价格越贵,另外电镀金还有一种金为软金,即是电镀纯金这种金层常用做Bonding用,电镀金是在外界电流的情况下才可以镀故需要每个Pad 均可牵线且允许牵线才可以施镀.四. 化学镍金(EN/IG –Electroless Nikel and Immersion Gold)化学镀镍是利用镍盐溶液在强还原剂次亚硫酸钠的作用下,使镍离子还原成金属镍同时次亚硫酸盐分解析出磷,因而在具有催化表面的镀件上获得Ni-P合金层,浸金是一种无须还原剂的典型置换反应,当化学镍表面进入到浸金槽液中,镍层被溶解抛出两个电子的同时其金属也随即自镍表面取得电子而沉积在镍金层上,一旦镍表面全被金层所盖满后金层的沉积反应逐渐停止,很难得到相当的厚度, 一般化金厚度为0.03-0.1um,化学镍金层中,化学镀镍是主体,化学金只是为了防止镍层纯化,一般化学镀镍层厚度为2-5um沉金层为0.03-0.1um由于无电沉积的化学镀层,镀层厚度均为一致,可以到达施镀的任何部位, 具有可焊,导电,散热功能.五.喷锡(HASL)喷锡学名为热风整平,它的功能原理是印制板浸入熔融的焊料中,再利用热风将印制板表面及孔内多余焊料去掉,剩余的焊料均为涂覆在焊盘及和孔内无阻焊膜的线路,表面焊接,及封装的焊盘上,一般是230-240℃2-3S, 此种表面处理他的缺陷是厚度不均匀,对于FPC板易造成压伤折皱,另外HASL在Pitch 小于o.5mm时无法用HASL,常易造成短路,架桥.六. OSPOSP是(organic solderability preserVatives)的英文缩为,意为有机保焊剂,是在干净的铜面形成的一种保护铜面不生锈的保护膜,但在焊接前又能被稀酸或助焊剂所迅速除去. 而令裸铜表面瞬间仍能展现良好的可焊性一般膜厚为0.35um.优点是焊盘平坦,可平稳的作SMT锡膏印刷与放置芯片,能替代HASL与化镍金.但有以下缺点:1.不耐多次焊接,OSP透明不易测量,目视难以检查.OSP Rework必须特别小心.七. 镀锡铅镀锡铅的原理是在电流的情况下在板面镀上63%锡及37%的铅,其优点是较容易的控制客户要求的镀层厚度且平整,一般情况下的厚度为4-10um,但是为了焊接的可靠度,客户也会将镀层厚度提高,但是厚度越高其在压合时易形成锡短.另锡铅焊接性能优异,因锡与铅是当前锡与任何合金组合熔点最低的一种组合.降低了焊接温度,相应的也降低了与之相配套使用的材料及电子组件的耐温要求.八. 化学锡与电镀锡目前所开发出来的化学锡与电镀锡,是应无欧盟无铅技术的要求产生的, 因铅对于人体及环境有害, 铅在人体内的积累会引起神经系统的紊乱, 对血液系统和肾产生不良影响.化学锡:一般的厚度为0.5um—1um, 化学镀纯锡可以得到精细.致密.纯锡的沉积层.优点:无铅,减少热应力对FPC产生的影响, 可多次焊接,表面平整.缺点:易氧化,应尽快用,不要储存太长时间,焊接时用无铅焊料,温度要求高,REFLOW一般要求260度.电镀纯锡:其厚度可根据客户要求镀厚优点: 无铅,可多次焊接,表面平整.缺点:焊接时用无铅焊料,焊接温度高,REFLOW温度一般要求260度.九.FPC成品表面处理工艺-储存期限储存环境: 温度: 25±5℃相对湿度: 60±5%1. 电镀镍金处理: 储存期限: 12个月(真空包装) 10个月(一般包装)2. 化学镍金处理: 储存期限: 10个月(真空包装) 6个月(一般包装)3. 电镀锡铅处理: 储存期限: 8个月(真空包装) 5个月(一般包装)4. 化学锡处理: 储存期限: 3个月(真空包装) 1个月(一般包装)5. 水性松香(OSP)处理: 储存期限: 3个月(真空包装) 1个月(一般包装)6. 电镀纯锡处理: 储存期限: 10个月(真空包装) 6个月(一般包装。
不同表面处理类型(镀镍金、化镍金、镍钯金-OSP)项目对比表

电镀镍金
不同镀层种类项目对比
化学镀镍金
化学镀镍钯金
华 远 电 OSP
定义
在金属铜上通过电流的作用电镀上镍、 金镀层
化学镍金是通过化学反应在铜的表面置 换钯再在钯核的基础上化学镀上一层镍 磷合金层,然后再通过置换反应在镍的 表面镀上一层金
化学镍钯金是通过化学反应在铜的表面 置换钯再在钯核的基础上化学镀上一层 镍磷合金层,然后在镍层上通过氧化还 原生成一层钯层,再通过置换反应在钯 (透过钯层的微小缝隙与镍层发生置换 反应)的表面镀上一层金
1、制程简单,药水易于管理;
3、可以设计更小的焊盘,在原有的面 积上增加更多的布线区域;
2、生产效率高;
4、钯层既保护了镍层,也为金线互熔 3、焊盘平整度好;
提供了基础,在较薄的金镀层也可以获
4、和焊盘之间无IMC层,锡层直接和 铜进行焊接,具有很高的可靠性,结合
得很好的绑线效果; 5、保存有效期较长;
③化金原理: 亚金离子与镍层发现置换反应: Ni+2Au+=Ni2++2Au
这层膜具有防氧化,耐热冲击,耐 湿性,用以保护铜表面于常态环境中不 再继续生锈(氧化或硫化等);但在后 续的焊接高温中,此种保护膜又必须很 容易被助焊剂所迅速清除,如此方可使 露出的干净铜表面得以在极短的时间内 与熔融焊锡立即结合成为牢固的焊点。
①化镍原理: 步骤1:H2P02- + H2O = H2PO3+2H++2e-,脱氢析出电子 步骤2:H2PO2-+mNi2++(2m+1)e=NimP+2OH-
②镀金原理:
阴极:Au+ + e- →Au,Au+来源于添加 ②化金原理:
各种表面处理优劣性
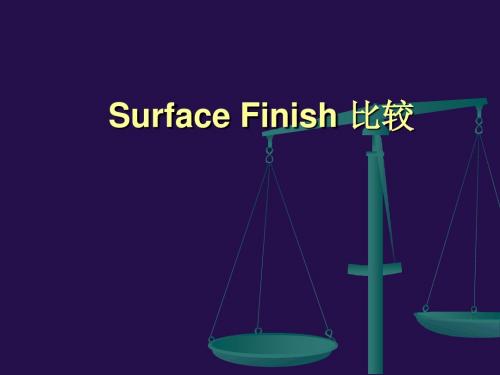
0.8-1.4 um 好 好 中等 16-20 易 差 低 3 3 好 12month 好
0.15-0.4um 好 好 易 16-20 难 中等 低 3 3 好 12month 好
press fit technology
14
使用场合
计算机,消 费性电子 产品,汽车
专用设备如: 欧美客户 PCB测试 产品,如 机,数据库 希捷的硬 交换机,背 盘 板,等
注, 表格说明
:
1.制造成本计算受设备嫁动率影响,以上结果以设备嫁动率至少保证在70%以上计 算。 2.制造成本未将设备折旧,水电,人力成本包含在内因此部分各公司投入成本不同无 法统计。 3.喷锡分垂直喷锡和水平喷锡统计V: 15-20(RMB/M2 )为垂直喷锡成本 H:22-30( RMB/M2 )为水平喷锡成本。)
二. 各种表面处理适用性
1.热风整平: 1.热风整平: 热风整平 A.锡铅合金(63/37)中的铅污染,无法Meet RoHS需求 A.锡铅合金(63/37)中的铅污染,无法Meet RoHS需求 B.凹凸不平的表面不能满足SMT高速贴装需要--B.凹凸不平的表面不能满足SMT高速贴装需要--C.适用于单价较低的低价产品(计算机,消费性电子产品) ) 2.化学镍金(选化板): 2.化学镍金 选化板) 化学镍金( A. 表面平整,可满足高速贴装及RoHS需要,一般条件下使用各种性能稳定好 表面平整,可满足高速贴装及RoHS需要,一般条件下使用各种性能稳定好 如:1m摔落实验,锡球推力测试,且可作为终端产品表面不需再加工。 如:1m摔落实验,锡球推力测试,且可作为终端产品表面不需再加工。 B. 金PAD表面在比较恶劣的环境下如:强酸性气体或腐蚀性气 体中可能会 PAD表面在比较恶劣的环境下如:强酸性气体或腐蚀性气 形成的贾凡尼腐蚀,使接触电阻变高。 C. 中高价位产品一般采用化金(如交换机等,手机,数码相机) 3. 化学银: 化学银: A.易受污染变色影响焊锡性,且生产制造时不可重工。 A.易受污染变色影响焊锡性, B.表面平整,可满足高速贴装及RoHS需要成本较低 B.表面平整,可满足高速贴装及RoHS需要成本较低 B.为欧美客户所钟爱(如希捷的硬盘) B.为欧美客户所钟爱(
PCB表面OSP处理及化学镍金简介

PCB表面OSP处理及化学镍金简介1 引言锡铅长期以来扮演着保护铜面,维持焊性的角色,从熔锡PCB 板到喷锡PCB板,数十年光阴至此,碰到几个无法克服的难题,非得用替代制程不可:A. Pitch 太细造成架桥(bridging)B. 焊接面平坦要求日严C. COB(chip on board)板大量设计使用D. 环境污染本章就两种最常用制程OSP及PCB化学镍金介绍之2 OSPOSP是Organic Solderability Preservatives 的简称,中译为有机保焊膜,又称护铜剂,英文亦称之Preflux,本章就以护铜剂称之。
2.1种类及流程介绍A. BTA(苯骈三氯唑):BENZOTRIAZOLEBTA是白色带淡黄无嗅之晶状细粉,在酸碱中都很安定,且不易发生氧化还原反应,能与金属形成安定化合物。
ENTHON将之溶于甲醇与水溶液中出售,作铜面抗氧化剂(TARNISH AND OXIDE RESIST),商品名为CU-55及CU-56,经CU-56处理之铜面可产生保护膜,防止裸铜迅速氧化。
操作流程如表14.1。
B. AI(烷基咪唑) ALKYLIMIDAZOLE PREFLUX是早期以ALKYLIMIDAZOLE作为护铜剂而开始,由日本四国化学公司首先开发之商品,于1985年申请专利,用于蚀刻阻剂(ETCHING RESIST),但由于色呈透明检测不易,未大量使用。
其后推出GLICOAT等,系由其衍生而来。
GLICOAT-SMD(E3)具以下特性:-与助焊剂相容,维持良好焊锡性-可耐高热焊锡流程-防止铜面氧化C. ABI (烷基苯咪唑) ALKYLBENZIMIDZOLE由日本三和公司开发,品名为CUCOAT A ,为一种耐湿型护铜剂。
能与铜原子产生错合物(COMPLEX COMPOUND),防止铜面氧化,与各类锡膏皆相容,对焊锡性有正面效果。
D.目前市售相关产品有以下几种代表厂家:醋酸调整系统:GLICOAT-SMD (E3) OR (F1)WPF-106A (TAMURA)ENTEK 106A (ENTHON)MEC CL-5708 (MEC)MEC CL-5800(MEC)甲酸调整系统:SCHERCOAT CUCOAT AKESTER大半药液为使成长速率快而升温操作,水因之蒸发快速,PH控制不易,当PH提高时会导致MIDAZOLE不溶而产生结晶,须将PH 调回。
PCB 表面处理工艺
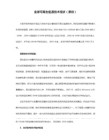
我把目前国内焊料的相关特性及保存时间给你作参考:
HASL热风整平:无法满足细小焊盘间距,厚度不均匀,不环保(含铅),盲埋孔覆盖性差,理论保存时间18个月,
OSP是有机表面保护层
FLASH GOLD 采用的是化学沉积的方法
PLANTING GOLD采用的是电解的原理
【镀金】:整板镀金。
一般是指【电镀金】【电镀镍金板】,【电解金】,【电金】,【电镍金板】,有软金和硬金(一般用作金手指)的区分。其原理是将镍和金 (俗称金盐)溶于化学药水中,将电路板浸于电镀缸中并通上电流而在电路板的铜箔面上生成镍金镀层,电镍金因其镀层硬度高,耐磨损,不易氧化的特点在电子产品名得到广泛的应用。
【化学镍金板】:邦定工艺使用,沉金来说是选择性镀金。
1) 【化金】:通过化学氧化还原反应的方法生成一层镀层,一般厚度较厚,是化学镍金金层沉积方法的一种,可以达到较厚的金层;
2) 【浸金】:也称为【置换金】,也就是【沉金】,一般厚度较薄,1--4微英寸。
【化金】和【浸金】一般用于相对要求较高的板子,平整度要好,化金比浸金要好些,化金一般不会出现组装后的黑垫现象;【镀金】因为镀层纯度较高,焊点强度较上述二者高。
金长很多倍所以大家都乐意采用.再说镀金PCB在度样阶段的成本与铅锡合金板相比相差无几。
但随着布线越来越密,线宽、间距已经到了3-4MIL。因此带来了金丝短路的问题:
随着信号的频率越来越高,因趋肤效应造成信号在多镀层中传输的情况对信号质量的影响越明显:
趋肤效应是指:高频的交流电,电流将趋向集中在导线的表面流动。
OSP工艺和化金工艺比较

• 解决: ① 适当降低温度、浓度和PH值。 ② 加强过滤,最好用5μm的滤芯边疆过滤。 同时加强板子的振动频率和幅度,便于赶 走板面上附着的氢气。 ③ 加强前处理,同 时检查铜面是否粗糙,杜决来料不良
• 露铜
• 原因: ① 反面沾异物 ② 湿膜显影不净和 水洗不净 ③ 钯附着力不够 ④ 活化后水洗 过长 ⑤ 镍槽药水管控失衡。 • 解决: ① 加重刷磨(追踪异物来源) ② 湿膜制程检讨心改善 ③ 控制去脂槽的 Cu2+含量(小于7g/L) ④ 缩短水洗时间 (15SEC) ⑤ 严格按比例添加,同时根据 化验结果结果调整
• OSP 工艺的缺点 OSP当然也有它不足之处,例 如实际配方种类多,性能不一。也就是说供应商 的认证和选择工作要做得够做得好。 OSP工艺的 不足之处是所形成的保护膜极薄,易于划伤(或 擦伤),必须精心操作和运放。同时,经过多次 高温焊接过程的OSP膜(指未焊接的连接盘上 OSP膜)会发生变色或裂缝,影响可焊性和可靠 性。锡膏印刷工艺要掌握得好,因为印刷不良的 板不能使用IPA等进行清洗,会损害OSP层。透 明和非金属的OSP层厚度也不容易测量,透明性 对涂层的覆盖面程度也不容易看出,所以供应商 这些方面的质量稳定性较难评估; OSP技术在焊 盘的Cu和焊料的Sn之间没有其它材料的IMC隔离, 在无铅技术中,含Sn量高的焊点中的SnCu增长 很快,影响焊点的可靠性。
• 2、微蚀 微蚀的目的是形成粗糙的铜面,便 于成膜。微蚀的厚度直接影响到成膜速率, 因此,要形成稳定的膜厚,保持微蚀厚度 的稳定是非常重要的。一般将微蚀厚度控 制在1.0-1.5um比较合适。每班生产前,可 测定微蚀速率,根据微蚀速率来确定微蚀 时间。
• 3、成膜 成膜前的水洗最好采有DI水,以防 成膜液遭到污染。成膜后的水洗也最好采 有DI水,且PH值应控制在4.0-7.0之间,以 防膜层遭到污染及破坏。OSP工艺的关键 是控制好防氧化膜的厚度。膜太薄,耐热 冲击能力差,在过回流焊时,膜层耐不往 高温(190-200°C),最终影响焊接性能, 在电子装配线上,膜不能很好的被助焊剂 所溶解,影响焊接性能。一般控制膜厚在 0.2-0.5um之间比较合适。
OSP表面处理工艺简介
Waste
Easy Difficult Difficult Difficult
Ionic residues Lowest Fair
Fair Highest
PAGE 7
PCB表面处理优点比较
工艺 机理
优点
沉镍金ENIG (Electroless Nickel
Immersion Gold)
先在电路板裸铜表 面反应沉积形成一 层含磷7-9%的镍镀 层,厚度约3-5um, 再于镍表面置换一 层厚度约0.050.15um的纯金层。
通过一种替代咪唑(1,3-二氮杂茂)衍生物的活性组分 与金属铜表面发生的化学反应,Glicoat-SMD F2 在PCB的 线路和通孔等焊接位置会形成均质、极薄、透明的有机涂 覆层。优良的耐热性,能适用于免洗助焊剂和锡膏。
PAGE 10
Glicoat-SMD F2 反应机理
Cu
Cu
Cu
Cu
N
N
N
R N
R N
R N
Cu
Cu
Cu
Cu
N
R N
Cu
N
R N
Cu PCB
N
R N
Cu
N R
N
N R
N
Cu
PAGE 11
OSP制程工艺流程
除油
微蚀
防氧化 PAGE 12
OSP关键流程控制方案
关键流程
微蚀: 微蚀深度及返工次数 防氧化: 膜厚
PAGE 13
为什么需要特殊管制微蚀深度?
H2SO4-H2O2体系
过硫酸盐体系
PAGE 15
微蚀深度管制
1、微蚀深度:1.5-2.5um 2、返工次数:<2次 3、微蚀体系:H2SO4-H2O2体系
PCB表面OSP处理及化学镍金简介
PCB表面OSP处理及化学镍金简介
1 引言
锡铅长期以来扮演着保护铜面,维持焊性的角色,从熔锡板到喷锡板,
数十年光阴至此,碰到几个无法克服的难题,非得用替代制程不可:
A. Pitch 太细造成架桥(bridging)
B. 焊接面平坦要求日严
C. COB(chip on board)板大量设计使用
D. 环境污染本章就两种最常用制程OSP 及化学镍金介绍之
2 OSP
OSP 是Organic Solderability Preservatives 的简称,中译为有机保焊膜,又称护铜剂,英文亦称之Preflux,本章就以护铜剂称之。
2.1
种类及流程介绍
A. BTA(苯骈三氯唑):BENZOTRIAZOLE
BTA 是白色带淡黄无嗅之晶状细粉,在酸碱中都很安定,且不易发生氧
化还原反应,能与金属形成安定化合物。
ENTHON 将之溶于甲醇与水溶液中出售,作铜面抗氧化剂(TARNISH AND OXIDE RESIST),商品名为CU-55 及CU-56,经CU-56 处理之铜面可产生保护膜,防止裸铜迅速氧化。
操作流程如
表14.1。
B. AI(烷基咪唑) ALKYLIMIDAZOLE PREFLUX 是早期以ALKYLIMIDAZOLE 作为护铜剂而开始,由日本四国化学公司首先开发之商品,
于1985 年申请专利,用于蚀刻阻剂(ETCHING RESIST),但由于色呈透明检测不易,未大量使用。
其后推出GLICOAT 等,系由其衍生而来。
PCB表面处理方式一是OSP ,二是HASL,此两种表面处理之区别在那呢收集资料
PCB表面处理方式:一是OSP ,二是HASL,此两种表面处理之区别在那呢?1热风整平(HAL)热风整平(HAL)或热风焊料整平(HASL)是20世纪80年代发展起来的一种先进工艺,到了90年代中、后期,它占据着整个PCB 表面涂(镀)覆层的90%以上。
只是到了90年代的末期,由于表面安装技术(SMT)的深入发展,才使HAL在PCB中的占有率逐步降低下来,但是,目前HAL在PCB表面涂(镀)覆中的占有率仍在50%左右。
尽管SMT的高密度发展会使HAL在PCB中的应用机率不断下降,但是HAL技术在PCB生产中的应用仍有很长的生命力,即使禁用铅的焊料(无铅的绿色焊料),无铅的HAL技术和工艺也会开发和应用起来。
1.1热风整平工艺和应用热风整平技术是指把PCB(一般为在制板 panel)浸入熔融的低共熔点(183℃,如图1所示)Sn/Pb(比例应等于或接近于63/37,操作温度为230∽250℃之间)合金中,然后拉出经热风(控制热风温度、风速和风刀角度,其中风刀结构与PCB板距离等已优化而固定下来)吹去多余的Sn/Pb合金,得到所要求组成和厚度的Sn/Pb合金层。
在热风整平生产过程中要控制和维护好Sn/Pb合金组成的成份比例(一般要定期补充纯锡,因为才锡比铅更易于氧化,加上锡也易于与其它金属形成合金,所以锡消耗比铅要快)。
同时,在高温热风整平的过程中,PCB上的铜也会熔入到Sn/Pb 合金中去,使Sn/Pb合金中含有铜的组分,由于铜和锡会形成高熔点的合金化合物,如Cu6/Sn5、Cu4/Sn3、Cu3/Sn等。
当Sn/Pb合金中的铜含量≥0.3%(重量百分比)时,不仅会是使热风整平温度提高(如超过250℃以上)才能得到平整而光亮的涂覆Sn/Pb合金层,甚至会形成粗糙不平或沙石状的表面。
因此应定期进行分析Sn和Pb含量与比例,以保证其比例处于62∽64/38∽36之间。
同时,由于锡比铅更易于氧化,因此,熔融的锡/铅合金表面应具有耐高温的防氧化剂或耐热助焊剂等加以保护。
电金板和化金板在SMT工艺上有什么区别
电金板和化金板在SMT工艺上有什么区别1.电金板与OSP的润湿性相当,化金板和浸锡板的润湿性是所有PCBfinihing最好的;2.电金的厚度远大于化金的厚度,但是平整度没有化金好;3.电金主要用于金手指(耐磨),做焊盘的也多;4.不知道大家使用的情况怎样,包括形成的IMC之类是否有什么不同?希望您的回答必须是有凭有据的、原理性的,最好带实物举例分析。
请问电金,化金,浸锡,沉金,OPS分别是怎么回事,制作工艺有什么差别,在SMT工艺中又有什么差别呢,谢谢各位电金的厚度远大于化金的厚度?是不是相反了?电金的厚度远大于化金的厚度?是不是相反了?没错!应该是反了,化金的厚度大于电金的厚度才对!镀金不是表面比较不平?所以应该比较厚,化金表面平整。
是不是!镀层厚度:电(电镀)金板:Ni层厚度:2.5--5μmAu层厚度:0.03--0.1μm化(沉浸)金板:Ni层厚度:5--8μmAu层厚度:0.08--0.12μm金手指板(电镀):Ni层厚度:2.5--5μmAu层厚度:0.08--0.12μm就是不知道各PCB生产商的厚度控制在什么范围,如果太薄可能导致露镍或者不耐温请各抒己见!也想了解一下,希望有专家给点建议楼主的问题等待专家指正,不过化金和电金厚度的问题,电金是一定更容易作的比化金厚的,因为电金是个电解过程,而化金是个置换反应,达到一定厚度后反应就很难继续下去了,所以电金更容易作到厚一点。
一般鍍層厚度與6樓說的差不多,而使用電鍍金或化金一般視設計使用情況來決定.1.大家都知道的金手指使用電鍍金因為它金層硬耐磨.2.但wirebond的pad就要使用化金,且Ni層要5um以上.否則Auwire會打不上.因IMC無法生成.3.如基板上既無金手指也無須w/b就可以成本考量使用op了.IMC的生成決定在Ni層的厚度.金層沒有什麼影響.而IMC影響的是焊點可靠度的問題.。
- 1、下载文档前请自行甄别文档内容的完整性,平台不提供额外的编辑、内容补充、找答案等附加服务。
- 2、"仅部分预览"的文档,不可在线预览部分如存在完整性等问题,可反馈申请退款(可完整预览的文档不适用该条件!)。
- 3、如文档侵犯您的权益,请联系客服反馈,我们会尽快为您处理(人工客服工作时间:9:00-18:30)。
• OSP 工艺的缺点 OSP当然也有它不足之处,例 如实际配方种类多,性能不一。也就是说供应商 的认证和选择工作要做得够做得好。 OSP工艺的 不足之处是所形成的保护膜极薄,易于划伤(或 擦伤),必须精心操作和运放。同时,经过多次 高温焊接过程的OSP膜(指未焊接的连接盘上 OSP膜)会发生变色或裂缝,影响可焊性和可靠 性。锡膏印刷工艺要掌握得好,因为印刷不良的 板不能使用IPA等进行清洗,会损害OSP层。透 明和非金属的OSP层厚度也不容易测量,透明性 对涂层的覆盖面程度也不容易看出,所以供应商 这些方面的质量稳定性较难评估; OSP技术在焊 盘的Cu和焊料的Sn之间没有其它材料的IMC隔离, 在无铅技术中,含Sn量高的焊点中的SnC工艺和化金工艺 比较
•
OSP是Organic Solderability Preservatives 的简称,中译为有机保焊膜,又 称护铜剂,英文亦称之Preflux。 简单的说OSP就是在洁净的裸铜表面上,以 化学的方法长出一层有机皮膜,这层膜具有防氧化,耐热冲击,耐湿性,用 以保护铜表面于常态环境中不再继续生锈(氧化或硫化等);但在后续的焊 接高温中,此种保护膜又必须很容易被助焊剂所迅速清除,如此方可使露出 的干净铜表面得以在极短时间内与熔融焊锡立即结合成为牢固的焊点。 其实 OSP并非新技术,它实际上已经有超过35年,比SMT历史还长。OSP具备许 多好处,例如平整面好,和焊盘的铜之间没有IMC形成,允许焊接时焊料和 铜直接焊接(润湿性好),低温的加工工艺,成本低(可低于HASL),加工 时的能源使用少等等。OSP技术早期在日本十分受欢迎,有约4成的单面板使 用这种技术,而双面板也有近3成使用它。在美国,OSP技术也在1997年起 激增,从1997以前的约10%用量增加到1999年的35%。 OSP有三大类的材 料:松香类(Rosin),活性树脂类(Active Resin)和唑类(Azole)。目前 使用最广的是唑类OSP。唑类OSP已经经过了约5代的改善,这五代分别名为 BTA,IA,BIA,SBA和最新的APA。早期的BTA类对湿度敏感,库存寿命很 短(3个月),不能承受多次加热,而且需要较强的焊剂,所以性能不是很好。 一直到70年代有日本开发的第三代BIA类OSP后才有较显著的改善。美国市 场也在80年代开始采用这类OSP,同时被正在发展的SMT所接受。不过BIA 的耐热性仍然是个弱点。目前仍然有供应商提供BIA类的OSP,但逐渐在为 新一代的SBA所取代。 SBA是1997年的研发成果,有美国IBM推出而后得到 在OSP技术上享有盛名的日本“四国化学”公司的改善。在保护性和耐热性 有显著的加强。其耐热性已经可以承受3次的回流处理(但多次加热后需要较 强的焊剂)。SBA是目前OSP供应的主流。成本低于传统的HASL,所以在 锡铅时代已经被大量的使用,尤其是单面板上。在双面回流板以及混装板工 艺应用上却仍然有些顾虑.
OSP的工艺流程
• 除油-->二级水洗-->微蚀-->二级水洗-->酸 洗-->DI水洗-->成膜风干-->DI水洗-->干燥 • 1、除油 除油 除油效果的好坏直接影响到成膜质量。 除油不良,则成膜厚度不均匀。一方面, 可以通过分析溶液,将浓度控制在工艺范 围内。另一方面,也要经常检查除油效果 是否好,若除油效果不好,则应及时更换 除油液。
常见问题的原因及解决方法
• 色差 • 原因: ①镍槽被污染或使用寿命已到,槽 液有机物累积过多。 ②金槽内的镍离子过 多 ③活化槽钯浓度不足。 • 解决: ① 换镍槽,杜决污染源。 ② 分析 金槽镍含量,超过0.5g/L换槽。 ③ 适当提 高钯浓度。
• 镀层粗糙
• 原因: ① 镍槽活性太强。 ② 过滤不够, 板子振动频率幅度不够。 ③ 前处理不良。
化金(化学镀金)
• 化金(化学镀金)不需要通电,是通过溶液内的 化学反应把金沉积到板面上. 对化学镍金制 程本身没有大的问题出现,主要是防焊白 化,是点露铜。而这两项都是湿膜制程品 质隐患而引起。
• 1. 焊自化。防焊油墨的品质破坏是决定因素,但一般的 油墨只要控制好工艺参数,也可将严重程度减至最小。 发前化金板用TARUM TT-9G油墨,该油墨品质十分过硬, 在镍槽镀50mm都未见防焊白化。但是改用太阳4000GF5型油墨,防焊白化有20mil,做试验发现不印文字去 做板,白化程度为15mil,判断是有了文字烤板的缘故, 因此将湿膜后烤参数由150℃ 45min改为150℃ 40min; 文字烤板参板由150℃ 20min(单面文字)改为140℃ 15min,做板后防焊白化只有8mil左右,可允收。说明非 化金板适用油墨在做板时,烤板的时间不宜过长,避免油 墨烘烤过度老化,化金时防焊老化。 2. 星点露铜:这是 最让人头痛的问题,产生的原因主要是湿膜显影及显影后 的水洗烤板时的放板密度(方便有机溶剂、油烟散发)通 风状况及烤箱内的清洁程度。 发现此种情况,严重的退 洗,轻微的采取刷磨两次,延长微蚀时间解决,最有效的 方法是从湿膜制程改善。
• 金脱皮
• 原因: ① 镍层含磷星高 ② 镍层钝化
• 解决: ① 用AA分析磷含量,适当降低还原 剂添加幅度,若不行则换槽。 ② 避免镍层 在空气中暴露时间过长。
• 镍、铜结合力差(镍/铜分层)
• 原因: ① 铜面不洁 ② 前处理失效 • 解决: ① 加强前处理 ② 分析前处理各槽 药液中Cu+含量,如有超标既换之。 (去 脂槽Cu2+<7g/L,微蚀槽Cu2+<15g/L。酸 洗槽Cu2+<0.3g/L)
• 解决: ① 适当降低温度、浓度和PH值。 ② 加强过滤,最好用5μm的滤芯边疆过滤。 同时加强板子的振动频率和幅度,便于赶 走板面上附着的氢气。 ③ 加强前处理,同 时检查铜面是否粗糙,杜决来料不良
• 露铜
• 原因: ① 反面沾异物 ② 湿膜显影不净和 水洗不净 ③ 钯附着力不够 ④ 活化后水洗 过长 ⑤ 镍槽药水管控失衡。 • 解决: ① 加重刷磨(追踪异物来源) ② 湿膜制程检讨心改善 ③ 控制去脂槽的 Cu2+含量(小于7g/L) ④ 缩短水洗时间 (15SEC) ⑤ 严格按比例添加,同时根据 化验结果结果调整
• 2、微蚀 微蚀的目的是形成粗糙的铜面,便 于成膜。微蚀的厚度直接影响到成膜速率, 因此,要形成稳定的膜厚,保持微蚀厚度 的稳定是非常重要的。一般将微蚀厚度控 制在1.0-1.5um比较合适。每班生产前,可 测定微蚀速率,根据微蚀速率来确定微蚀 时间。
• 3、成膜 成膜前的水洗最好采有DI水,以防 成膜液遭到污染。成膜后的水洗也最好采 有DI水,且PH值应控制在4.0-7.0之间,以 防膜层遭到污染及破坏。OSP工艺的关键 是控制好防氧化膜的厚度。膜太薄,耐热 冲击能力差,在过回流焊时,膜层耐不往 高温(190-200°C),最终影响焊接性能, 在电子装配线上,膜不能很好的被助焊剂 所溶解,影响焊接性能。一般控制膜厚在 0.2-0.5um之间比较合适。