普通车床实训报告
金工实习工作报告普通车床加工5篇
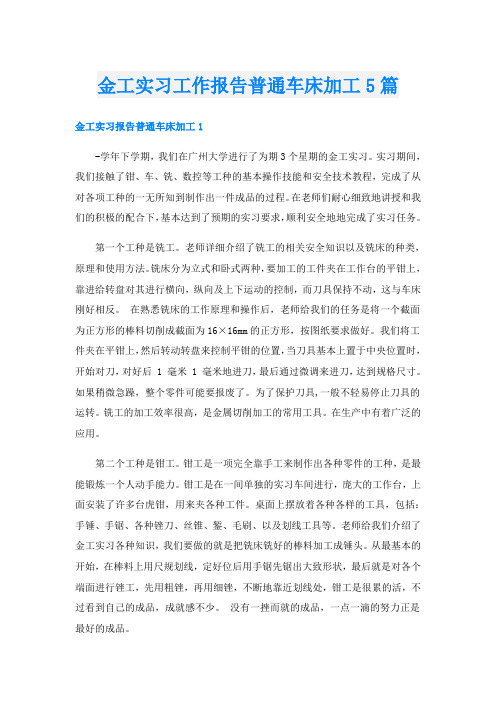
金工实习工作报告普通车床加工5篇金工实习报告普通车床加工1-学年下学期,我们在广州大学进行了为期3个星期的金工实习。
实习期间,我们接触了钳、车、铣、数控等工种的基本操作技能和安全技术教程,完成了从对各项工种的一无所知到制作出一件成品的过程。
在老师们耐心细致地讲授和我们的积极的配合下,基本达到了预期的实习要求,顺利安全地地完成了实习任务。
第一个工种是铣工。
老师详细介绍了铣工的相关安全知识以及铣床的种类,原理和使用方法。
铣床分为立式和卧式两种,要加工的工件夹在工作台的平钳上,靠进给转盘对其进行横向,纵向及上下运动的控制,而刀具保持不动,这与车床刚好相反。
在熟悉铣床的工作原理和操作后,老师给我们的任务是将一个截面为正方形的棒料切削成截面为16×16mm的正方形,按图纸要求做好。
我们将工件夹在平钳上,然后转动转盘来控制平钳的位置,当刀具基本上置于中央位置时,开始对刀,对好后 1 毫米 1 毫米地进刀,最后通过微调来进刀,达到规格尺寸。
如果稍微急躁,整个零件可能要报废了。
为了保护刀具,一般不轻易停止刀具的运转。
铣工的加工效率很高,是金属切削加工的常用工具。
在生产中有着广泛的应用。
第二个工种是钳工。
钳工是一项完全靠手工来制作出各种零件的工种,是最能锻炼一个人动手能力。
钳工是在一间单独的实习车间进行,庞大的工作台,上面安装了许多台虎钳,用来夹各种工件。
桌面上摆放着各种各样的工具,包括:手锤、手锯、各种锉刀、丝锥、錾、毛刷、以及划线工具等。
老师给我们介绍了金工实习各种知识,我们要做的就是把铣床铣好的棒料加工成锤头。
从最基本的开始,在棒料上用尺规划线,定好位后用手锯先锯出大致形状,最后就是对各个端面进行锉工,先用粗锉,再用细锉,不断地靠近划线处,钳工是很累的活,不过看到自己的成品,成就感不少。
没有一挫而就的成品,一点一滴的努力正是最好的成品。
第三个工种是钻床。
主要是为了锤头的攻丝先进行钻孔。
所使用的钻床是摇臂钻床,这个任务比较简单,只需要先定好钻孔的位置就可以进行定位钻孔了。
车床的实习报告8篇
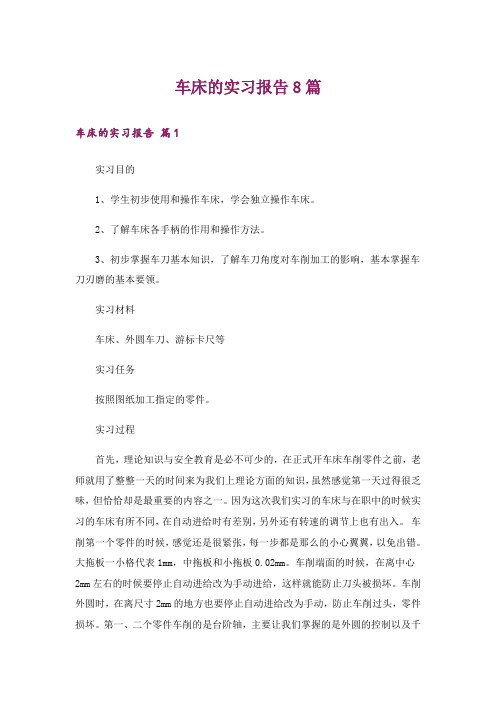
车床的实习报告8篇车床的实习报告篇1实习目的1、学生初步使用和操作车床,学会独立操作车床。
2、了解车床各手柄的作用和操作方法。
3、初步掌握车刀基本知识,了解车刀角度对车削加工的影响,基本掌握车刀刃磨的基本要领。
实习材料车床、外圆车刀、游标卡尺等实习任务按照图纸加工指定的零件。
实习过程首先,理论知识与安全教育是必不可少的,在正式开车床车削零件之前,老师就用了整整一天的时间来为我们上理论方面的知识,虽然感觉第一天过得很乏味,但恰恰却是最重要的内容之一。
因为这次我们实习的车床与在职中的时候实习的车床有所不同,在自动进给时有差别,另外还有转速的调节上也有出入。
车削第一个零件的时候,感觉还是很紧张,每一步都是那么的小心翼翼,以免出错。
大拖板一小格代表1mm,中拖板和小拖板0.02mm。
车削端面的时候,在离中心2mm左右的时候要停止自动进给改为手动进给,这样就能防止刀头被损坏。
车削外圆时,在离尺寸2mm的地方也要停止自动进给改为手动,防止车削过头,零件损坏。
第一、二个零件车削的是台阶轴,主要让我们掌握的是外圆的控制以及千分尺的使用与读数。
在测量零件的时候,一定要用游标卡尺与千分尺配合使用,在离规定尺寸剩余1mm内就要改用千分尺测量,这样就能有效的控制外圆的尺寸。
再有精车的时候,一定要先试切削测量一下,看尺寸是否在范围之内,这样加工出来的零件准确率就比较高。
实习体会通过这四天的实操,我们了解了车刀的种类,常用的刀具材料,刀具材料的基本性能,车刀的组成和主要几何角度。
让我们熟悉了普通车刀的组成、安装与刃磨,了解了车刀的主要角度及作用,刀具切削部分材料的性能和要求以及常用刀具材料,车削时常用的工件装夹方法、特点和应用,常用量具的种类和方法,了解了车外圆、车端面、车内孔、钻孔、车螺纹以及车槽、车断、车圆锥面、车成形面的车削方法和测量方法。
我们开始自己独立实习时,虽然操作技术不怎么熟练,出来的产品都不和规格,不过经过几天的车工实习,最后还是各自独立的完成了规定的工件制造。
普通车床实训报告(5篇)

普通车床实训报告(5篇)第一篇:普通车床实训报告一.目的生产性岗位实习是人才培养方案中的重要组成部分,是理论联系实际的重要实践教学环节,是技术应用能力综合训练和提高的重要阶段。
生产性岗位实习的主要目的是使学生熟悉企业的组织及整体运作模式,掌握普通车床功能、加工操作、设备安装调试和维修的工作程序与专业技能;开阔学生视野,丰富学生的知识结构,培养良好的职业素质与团队精神,进一步提高学生分析问题和解决问题的能力。
为培养适应企事业需要的应用型技术人才奠定坚实的基础。
毕业实习是各专业的一个重要的实践教学环节,是学生把两年来学得的各门课程的理论知识和所受的实践教学课程的技能训练,通过企业单位提供的实战平台,进行融合而形成综合实际能力的过程,是职业生涯开始前的一次全面的预演。
通过毕业实习,在真实的生产实践背景下,使学生在普通车床操作、调试、加工、装配、工艺规程拟订、设备维护、故障排除、营销等不同岗位以及零件机械加工、装配和部件、整机的质量检验等不同岗位上,受到实际的训练,使其上述方面的能力和技能,以及综合素质得到质的提高,毕业后能较好地适应专业工作的需要。
二实习时间于2009年2月至2009年4月期间在日本电产机器装置(浙江)有限公司三实习地点日本电产机器装置(浙江)有限公司第二事业部加工组四实习单位情况简介(一)单位情况简介经单位应聘,本人于2009年2月至2009年4月期间在日本电产机器装置(浙江)有限公司进行岗位实习。
日本电产机器装置(浙江)有限公司是一家外资企业,战地面积50万平方米,一共分五个事业部:第一事业部主要生产精密马达。
第二事业部主要生产精密测定机器及半导体制造装置。
第三事业部生产高速精密自动机器及检查治具。
第四事业部生产小型精密自动制造设备和检查设备。
第五事业部电气回路基板检查装置及检查治具。
公司一共有员工400余人。
公司基本方针是:利用科学,技术,技能的一体化和拥有的一颗诚实的心,生产全世界所需要的产品,向社会作出贡献。
普通车床床拆卸实训报告

一、实训目的本次实训旨在通过实际操作,让学生掌握普通车床床身的拆卸步骤和方法,了解床身各组成部分的结构和功能,提高学生的实际操作技能和机械知识应用能力。
二、实训内容1. 床身拆卸前的准备工作- 熟悉普通车床床身结构,了解其组成部分及各自功能。
- 熟悉拆卸工具和设备,如扳手、螺丝刀、撬棒等。
- 确保安全措施到位,如穿戴防护眼镜、手套等。
2. 床身拆卸步骤- 拆卸床鞍:1. 使用扳手将床鞍固定螺丝拧下。
2. 用撬棒将床鞍从床身中撬出。
- 拆卸床身固定板:1. 使用扳手将床身固定板上的螺丝拧下。
2. 将固定板从床身上拆下。
- 拆卸床身立柱:1. 使用扳手将立柱固定螺丝拧下。
2. 用撬棒将立柱从床身中撬出。
- 拆卸床身底座:1. 使用扳手将底座固定螺丝拧下。
2. 将底座从床身中撬出。
3. 拆卸过程中注意事项- 严格遵守拆卸顺序,避免损坏床身和零部件。
- 注意保护零部件,避免划伤或变形。
- 操作过程中注意安全,防止意外伤害。
三、实训过程1. 床鞍拆卸:- 按照拆卸步骤,顺利地将床鞍从床身中拆卸出来。
- 注意观察床鞍与床身之间的连接方式,了解其结构。
2. 床身固定板拆卸:- 按照拆卸步骤,将床身固定板从床身上拆下。
- 注意观察固定板与床身之间的连接方式,了解其结构。
3. 床身立柱拆卸:- 按照拆卸步骤,将床身立柱从床身中撬出。
- 注意观察立柱与床身之间的连接方式,了解其结构。
4. 床身底座拆卸:- 按照拆卸步骤,将床身底座从床身中撬出。
- 注意观察底座与床身之间的连接方式,了解其结构。
四、实训总结1. 实训收获- 通过本次实训,掌握了普通车床床身的拆卸步骤和方法。
- 加深了对普通车床床身结构及其各组成部分功能的了解。
- 提高了实际操作技能和机械知识应用能力。
2. 存在问题- 在拆卸过程中,对某些零部件的拆卸不够熟练,需要进一步练习。
- 对床身结构及其各组成部分功能的了解还不够深入,需要进一步学习。
3. 改进措施- 加强对床身结构及其各组成部分功能的学习,提高理论知识水平。
普通车床电气实训报告

一、实训目的通过本次普通车床电气实训,使学生了解普通车床的结构、工作原理和操作方法,掌握普通车床电气控制系统的基本原理和故障排除方法,提高学生的实际操作能力和工程实践能力。
二、实训内容1. 普通车床的结构及工作原理(1)普通车床的结构:普通车床主要由床身、主轴箱、进给箱、溜板箱、刀架、尾座等部件组成。
(2)普通车床的工作原理:普通车床通过电动机带动主轴旋转,将工件夹持在卡盘或顶尖上,通过溜板箱带动刀架进行切削加工。
2. 普通车床电气控制系统(1)电气控制系统组成:普通车床电气控制系统主要由电源、主轴电动机、进给电动机、刀架电动机、控制电路、保护电路等组成。
(2)电气控制原理:通过控制电路控制主轴电动机、进给电动机、刀架电动机的启停、转速和方向,实现对普通车床的电气控制。
3. 普通车床电气故障排除(1)故障现象:普通车床在运行过程中,可能出现主轴不转、进给不正常、刀架移动异常等故障。
(2)故障排除方法:①检查电源电压是否正常;②检查控制电路元件是否损坏;③检查电动机及连接线是否正常;④检查保护电路是否起作用。
三、实训过程1. 实训准备(1)了解普通车床的结构、工作原理和电气控制系统;(2)熟悉实训设备,检查设备是否完好;(3)准备实训工具,如万用表、螺丝刀等。
2. 实训操作(1)按照操作规程,启动普通车床;(2)观察主轴、进给和刀架的运行情况,调整速度和方向;(3)进行切削加工,观察加工质量;(4)在实训过程中,注意观察电气控制系统的运行状态,发现异常及时排除。
3. 实训总结(1)总结实训过程中遇到的问题及解决方法;(2)分析普通车床电气故障的原因及排除方法;(3)提高实际操作能力和工程实践能力。
四、实训心得1. 通过本次实训,我对普通车床的结构、工作原理和电气控制系统有了更深入的了解,提高了自己的实际操作能力。
2. 在实训过程中,我学会了如何观察和分析电气故障,提高了自己的故障排除能力。
3. 实训让我认识到理论与实践相结合的重要性,为今后的学习和工作打下了基础。
金工实习实训报告普通车床

一、实习目的本次金工实习实训旨在通过实际操作,使我对普通车床的结构、操作方法及安全规程有更深入的了解,掌握车削加工的基本技能,提高动手能力和工程实践能力。
二、实习时间2023年X月X日至2023年X月X日三、实习地点XX学校机械工程系金工实习车间四、实习内容1. 普通车床的基本结构及原理普通车床是一种常用的金属切削机床,主要用于车削外圆、内孔、端面、螺纹等。
它主要由床身、主轴箱、进给箱、溜板箱、光杠、丝杠、刀架、尾座等部件组成。
2. 普通车床的操作步骤(1)启动车床:首先打开电源开关,然后按下启动按钮,使车床开始运转。
(2)装夹工件:将工件夹紧在卡盘或顶尖上,确保工件定位准确。
(3)安装刀具:根据加工要求选择合适的刀具,将其安装在刀架上,并调整刀具位置。
(4)调整切削参数:根据工件材料和加工要求,调整车床转速、进给量、进给方向等参数。
(5)车削加工:启动进给手柄,使刀具进行切削,加工出所需的形状和尺寸。
(6)停车:完成加工后,关闭进给手柄,使刀具停止切削,然后关闭车床电源。
3. 普通车床的安全操作规程(1)严格遵守车床操作规程,穿戴好安全防护用品。
(2)操作前检查车床各部件是否正常,如有异常,及时报修。
(3)工件装夹牢固,确保加工过程中不会发生脱落。
(4)操作过程中,注意观察刀具与工件的相对位置,避免发生碰撞。
(5)严禁操作过程中闲谈、嬉戏,以免发生意外。
(6)发生紧急情况时,立即停止操作,切断电源,采取必要措施。
五、实习心得通过本次金工实习实训,我对普通车床有了更深入的了解,掌握了车削加工的基本技能。
以下是我在实习过程中的几点心得体会:1. 实践出真知。
在实习过程中,我深刻体会到理论知识与实际操作相结合的重要性。
只有通过实际操作,才能真正掌握车削加工的技能。
2. 安全第一。
在操作过程中,我始终将安全放在首位,严格遵守操作规程,确保自身和他人的安全。
3. 细心操作。
在加工过程中,我注重细节,严格按照工艺要求进行操作,确保加工质量。
普通车床工程实训报告
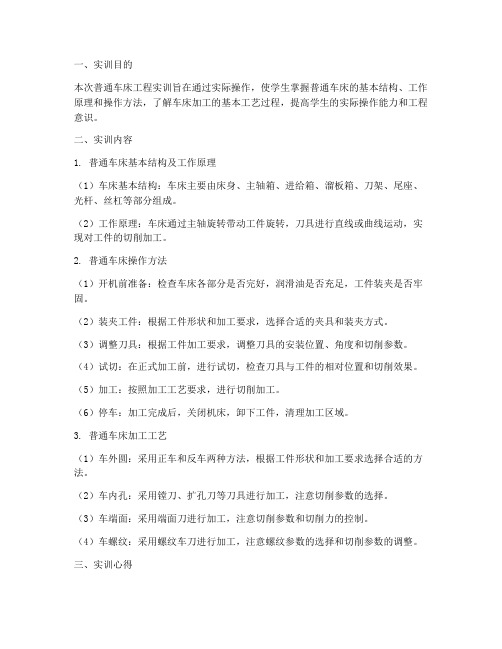
一、实训目的本次普通车床工程实训旨在通过实际操作,使学生掌握普通车床的基本结构、工作原理和操作方法,了解车床加工的基本工艺过程,提高学生的实际操作能力和工程意识。
二、实训内容1. 普通车床基本结构及工作原理(1)车床基本结构:车床主要由床身、主轴箱、进给箱、溜板箱、刀架、尾座、光杆、丝杠等部分组成。
(2)工作原理:车床通过主轴旋转带动工件旋转,刀具进行直线或曲线运动,实现对工件的切削加工。
2. 普通车床操作方法(1)开机前准备:检查车床各部分是否完好,润滑油是否充足,工件装夹是否牢固。
(2)装夹工件:根据工件形状和加工要求,选择合适的夹具和装夹方式。
(3)调整刀具:根据工件加工要求,调整刀具的安装位置、角度和切削参数。
(4)试切:在正式加工前,进行试切,检查刀具与工件的相对位置和切削效果。
(5)加工:按照加工工艺要求,进行切削加工。
(6)停车:加工完成后,关闭机床,卸下工件,清理加工区域。
3. 普通车床加工工艺(1)车外圆:采用正车和反车两种方法,根据工件形状和加工要求选择合适的方法。
(2)车内孔:采用镗刀、扩孔刀等刀具进行加工,注意切削参数的选择。
(3)车端面:采用端面刀进行加工,注意切削参数和切削力的控制。
(4)车螺纹:采用螺纹车刀进行加工,注意螺纹参数的选择和切削参数的调整。
三、实训心得1. 通过本次实训,我对普通车床的基本结构、工作原理和操作方法有了更加深入的了解,提高了自己的实际操作能力。
2. 在实训过程中,我学会了如何根据工件加工要求选择合适的刀具、夹具和切削参数,掌握了车床加工的基本工艺过程。
3. 实训使我认识到,实际操作与理论知识相结合的重要性。
在今后的学习和工作中,我要不断积累实践经验,提高自己的工程意识。
4. 在实训过程中,我遇到了一些困难,如刀具调整、切削参数选择等。
在老师的指导下,我逐渐克服了这些困难,提高了自己的动手能力。
5. 通过本次实训,我深刻体会到团结协作的重要性。
关于普通车床实训报告

一、前言作为一名机械专业的学生,理论知识的学习固然重要,但实践能力的培养同样不可或缺。
为了更好地将所学理论知识与实际操作相结合,提高自己的专业技能,我参加了为期两周的普通车床实训。
通过这次实训,我对普通车床的结构、操作方法以及加工工艺有了更加深入的了解,现将实训过程及心得体会总结如下。
二、实训内容1. 普通车床的基本结构及工作原理在实训初期,我们首先学习了普通车床的基本结构和工作原理。
普通车床主要由床身、主轴箱、进给箱、溜板箱、刀架、尾座等部分组成。
其中,床身是车床的基础,用于支撑其他部件;主轴箱是车床的动力来源,负责驱动主轴旋转;进给箱用于控制刀具的进给速度和方向;溜板箱负责驱动溜板运动,实现车削加工;刀架用于安装刀具,实现切削;尾座用于安装工件,保证加工精度。
2. 普通车床的操作方法在掌握了普通车床的基本结构和工作原理后,我们开始学习普通车床的操作方法。
实训过程中,我们学习了以下操作步骤:(1)开机:首先检查车床各部件是否正常,然后打开电源,启动主轴和进给系统。
(2)装夹工件:根据加工要求,选择合适的夹具,将工件夹紧在尾座上。
(3)安装刀具:根据加工要求,选择合适的刀具,并将其安装在刀架上。
(4)调整刀具位置:根据加工要求,调整刀具位置,确保刀具与工件的位置关系正确。
(5)开车床:启动车床,开始进行车削加工。
(6)停车:完成加工后,关闭电源,停车。
3. 普通车床的加工工艺在实训过程中,我们学习了普通车床的加工工艺,包括外圆加工、端面加工、台阶加工、螺纹加工等。
通过实际操作,我们掌握了以下加工方法:(1)外圆加工:采用直线进给和圆周进给两种方式,加工工件的外圆。
(2)端面加工:采用直线进给和圆周进给两种方式,加工工件的端面。
(3)台阶加工:采用直线进给和圆周进给两种方式,加工工件的台阶。
(4)螺纹加工:采用直线进给和圆周进给两种方式,加工工件的螺纹。
三、实训心得1. 理论与实践相结合的重要性通过这次实训,我深刻体会到理论与实践相结合的重要性。