砖厂生产工艺技术说明
瓷砖生产工艺流程介绍怎么写的呢

瓷砖生产工艺流程介绍怎么写的呢
瓷砖是一种常见的建筑材料,被广泛应用于室内装饰中,其生产过程涉及多个工艺环节。
下面将从原料准备、研磨成型、干燥、装炉烧成和包装出厂等方面介绍瓷砖的生产工艺流程。
首先,瓷砖的生产需要准备各种原料,包括瓷土、石英砂、长石和粘土等。
这些原料需按一定比例混合,经过一系列处理后得到瓷砖的坯体。
接下来是研磨成型的过程。
在这个环节中,原料经过研磨、混合、加水制浆等工序,最终形成了瓷砖的坯体。
坯体经过模具成型后,需要进行干燥处理,以去除多余的水分。
随后是装炉烧成阶段。
坯体放入炉内进行烧结,经过高温处理,使瓷砖坯体结晶硬化,形成坚硬的瓷质。
烧成过程需要控制好温度和时间,确保瓷砖的质量。
最后是包装出厂环节。
烧成后的瓷砖需要经过检查和质量验收,合格的产品进入包装环节。
通常瓷砖会根据规格、颜色等分类包装,并在外包装上标明产品信息和商标。
总的来说,瓷砖生产工艺流程相对复杂,需要严格按照要求操作,保证产品质量。
只有经过每个环节的精心处理,才能生产出质量过硬的瓷砖产品。
希望通过以上介绍,您对瓷砖的生产工艺流程有了更进一步的了解。
1。
瓷砖生产工艺流程介绍怎么写的好

瓷砖生产工艺流程介绍怎么写的好瓷砖是一种常见的装饰材料,被广泛应用于室内和室外的地面和墙面装饰。
瓷砖的生产工艺流程包括原料准备、制胚、干燥、施釉、烧制等多个环节。
下面将详细介绍瓷砖生产的各个环节,以帮助读者更好地了解瓷砖的生产工艺流程。
1. 原料准备瓷砖的主要原料包括粘土、长石、石英和矿物颜料等。
在生产过程中,这些原料需要进行精确配比,以确保瓷砖的质量和色泽稳定。
原料的选择和配比是影响瓷砖品质的关键因素之一。
2. 制胚制胚是瓷砖生产的第一步,主要是将原料按照一定比例混合,在专用的制胚机器上进行压制,形成瓷砖的初步形态。
经过制胚后的瓷砖坯体需要经过充分的挤压和挤出,确保瓷砖的密实度和均匀性。
3. 干燥制胚完成后,瓷砖坯体需要进行干燥处理。
干燥的主要目的是去除水分,使瓷砖坯体具有一定的硬度和强度。
通常采用空气流通的热风干燥方法,可以有效地提高瓷砖的生产效率和质量。
4. 施釉施釉是瓷砖表面处理的关键环节。
施釉可以使瓷砖具有更好的防污性能和装饰效果。
常用的施釉方法包括浸釉和喷釉两种,通过涂覆釉料和经过烘烤处理,使瓷砖表面形成坚硬的瓷釉层。
5. 烧制烧制是瓷砖生产的最后一个环节,也是最关键的一个环节。
瓷砖需要放入窑炉中进行高温烧制,使瓷砖坯体变成坚硬的成品。
烧制过程需要控制温度、时间和气氛等因素,以确保瓷砖的烧结均匀和品质稳定。
总的来说,瓷砖生产的工艺流程需要严谨的操作和精准的控制,每一个环节都影响着最终瓷砖的质量和性能。
只有通过科学合理的生产工艺流程,才能生产出高质量的瓷砖产品,满足人们对于美观、耐用的装饰需求。
希望通过本文的介绍,读者可以更好地理解瓷砖生产工艺流程,为瓷砖生产提供参考和帮助。
瓷砖生产工艺流程详细介绍

瓷砖生产工艺流程详细介绍
1. 原料准备阶段
在瓷砖生产的第一阶段,需要准备各种原料。
主要原料包括粘土、长石、石英、矿渣等。
这些原料需要经过严格的筛分、混合和加工,以保证最终产品的质量和性能。
2. 造粒和成型阶段
在这个阶段,原料会被送入破碎机进行造粒,然后通过挤压成型机或模压机进
行成型。
成型后的瓷砖经过压制,形成一定的厚度和形状。
3. 干燥和烧结阶段
成型后的瓷砖需要先进行干燥,通常会放在干燥室中进行热风干燥,以去除多
余的水分。
接着瓷砖会被送入窑炉进行烧结,将其加热到高温,使其各种物质发生化学变化,形成致密的结晶结构。
4. 釉面处理阶段
在烧结后的瓷砖表面通常会比较粗糙,需要通过涂釉进行表面处理。
涂釉一般
包括釉浆涂覆和烧结。
在烧结的过程中,釉面会与瓷砖基体结合,形成坚固的保护层,提高瓷砖的光亮度和耐磨性。
5. 包装和质检阶段
最后一道工序是将瓷砖进行包装和质检。
包装通常采用纸箱或木箱包装,以防
止瓷砖在运输过程中受到损坏。
质检是确保瓷砖质量符合标准的关键环节,包括外观、尺寸、平整度、色差等指标的检测。
以上是瓷砖生产工艺的基本流程,每个环节都需要严格的控制和管理,以确保
最终产品的质量和性能符合市场需求。
砖厂隧道窑生产工艺

砖厂隧道窑生产工艺砖厂隧道窑生产工艺是一种常用的砖坯烧制工艺,具有高产量、高产能、节能环保等优点。
下面将从原料准备、成型、烧制、冷却等方面介绍砖厂隧道窑的生产工艺。
首先是原料准备。
砖厂隧道窑的原料主要包括黏土、煤粉和水。
首先是黏土选择和配比,要根据砖的种类和要求选择合适的黏土,并进行配比,确保黏土的塑性和稳定性。
同时,还要根据烧制温度和煤粉含量的要求,选择合适的煤粉,并在黏土中加入适量的煤粉以提高砖的燃烧性能。
最后,将黏土和煤粉加入水中,进行充分混合,制成黏土糊状物。
然后是成型过程。
将制成的黏土糊状物通过挤压或模压成型,形成砖坯。
挤压成型是将黏土糊状物通过挤压机挤压成型,成型快速,产量高。
模压成型是将黏土糊状物放入模具中,经过压力和振动成型,成型质量好。
成型后的砖坯应进行适当的养护,保证其强度和稳定性。
接下来是烧制过程。
砖坯放入预热区,在一定的温度下进行预热,使砖坯内部水分慢慢蒸发。
然后进入燃烧区,砖坯在高温下进行燃烧,煤粉与氧气反应生成CO2和水蒸气,燃烧产生的热量使砖坯达到需要的烧结温度。
在高温下,砖坯中的黏土颗粒发生化学反应,形成砖坯的胶结相,使砖坯结实。
最后进入冷却区,通过冷却,使砖坯温度下降,并达到最终的成熟度。
最后是冷却和包装。
经过烧制的砖坯进入冷却区,通过通风和冷却,使砖坯温度逐渐降低。
待砖坯冷却到室温后,进行包装和包装,然后可出厂销售。
总之,砖厂隧道窑生产工艺是一种高效、节能、环保的砖坯生产工艺。
通过合理的原料准备、成型、烧制和冷却等工艺控制,可以生产出质量稳定、强度高的烧结砖,满足市场需求。
同时,隧道窑生产工艺还具有高产量、高产能的特点,能够满足大规模砖坯生产的需求。
砖厂烧砖工艺流程
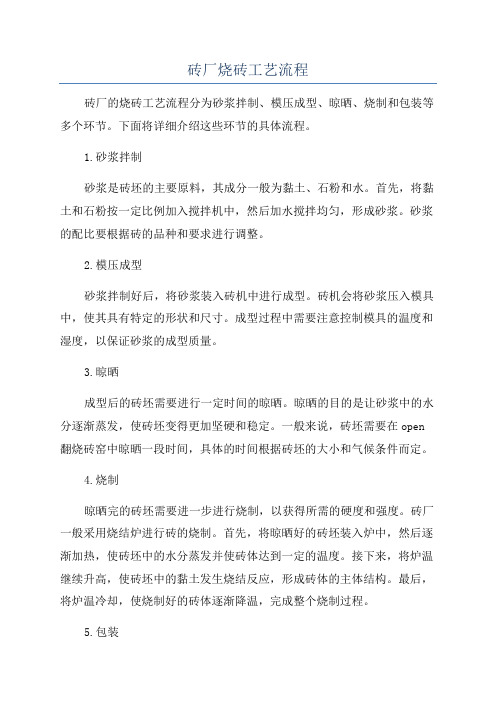
砖厂烧砖工艺流程砖厂的烧砖工艺流程分为砂浆拌制、模压成型、晾晒、烧制和包装等多个环节。
下面将详细介绍这些环节的具体流程。
1.砂浆拌制砂浆是砖坯的主要原料,其成分一般为黏土、石粉和水。
首先,将黏土和石粉按一定比例加入搅拌机中,然后加水搅拌均匀,形成砂浆。
砂浆的配比要根据砖的品种和要求进行调整。
2.模压成型砂浆拌制好后,将砂浆装入砖机中进行成型。
砖机会将砂浆压入模具中,使其具有特定的形状和尺寸。
成型过程中需要注意控制模具的温度和湿度,以保证砂浆的成型质量。
3.晾晒成型后的砖坯需要进行一定时间的晾晒。
晾晒的目的是让砂浆中的水分逐渐蒸发,使砖坯变得更加坚硬和稳定。
一般来说,砖坯需要在open 翻烧砖窑中晾晒一段时间,具体的时间根据砖坯的大小和气候条件而定。
4.烧制晾晒完的砖坯需要进一步进行烧制,以获得所需的硬度和强度。
砖厂一般采用烧结炉进行砖的烧制。
首先,将晾晒好的砖坯装入炉中,然后逐渐加热,使砖坯中的水分蒸发并使砖体达到一定的温度。
接下来,将炉温继续升高,使砖坯中的黏土发生烧结反应,形成砖体的主体结构。
最后,将炉温冷却,使烧制好的砖体逐渐降温,完成整个烧制过程。
5.包装烧制好的砖体经过冷却后,需要进行包装。
一般来说,砖体会经过质检,对砖的尺寸、外观、硬度等进行检查,以保证产品的质量。
之后,砖体会被分类、计量并进行包装。
包装方式一般有捆扎、装袋或装箱等,以便于运输和储存。
总结:以上就是砖厂烧砖工艺流程的主要环节。
从砂浆拌制到包装,每个环节都需要严格控制,以保证砖的质量。
只有在严格的工艺流程控制下,才能生产出高质量的砖产品。
瓷砖制造工艺技术
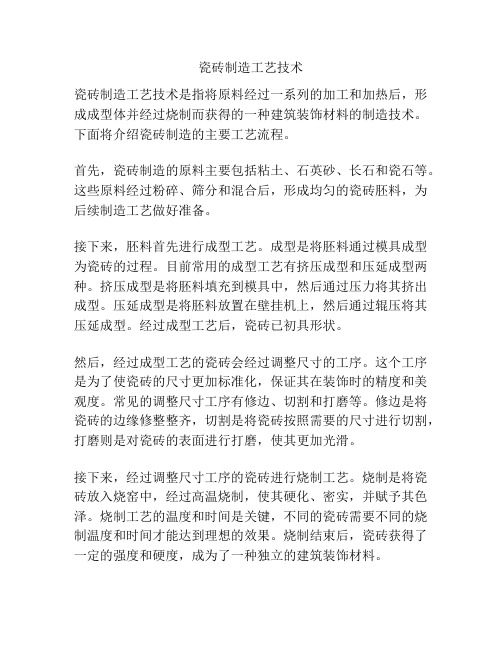
瓷砖制造工艺技术瓷砖制造工艺技术是指将原料经过一系列的加工和加热后,形成成型体并经过烧制而获得的一种建筑装饰材料的制造技术。
下面将介绍瓷砖制造的主要工艺流程。
首先,瓷砖制造的原料主要包括粘土、石英砂、长石和瓷石等。
这些原料经过粉碎、筛分和混合后,形成均匀的瓷砖胚料,为后续制造工艺做好准备。
接下来,胚料首先进行成型工艺。
成型是将胚料通过模具成型为瓷砖的过程。
目前常用的成型工艺有挤压成型和压延成型两种。
挤压成型是将胚料填充到模具中,然后通过压力将其挤出成型。
压延成型是将胚料放置在壁挂机上,然后通过辊压将其压延成型。
经过成型工艺后,瓷砖已初具形状。
然后,经过成型工艺的瓷砖会经过调整尺寸的工序。
这个工序是为了使瓷砖的尺寸更加标准化,保证其在装饰时的精度和美观度。
常见的调整尺寸工序有修边、切割和打磨等。
修边是将瓷砖的边缘修整整齐,切割是将瓷砖按照需要的尺寸进行切割,打磨则是对瓷砖的表面进行打磨,使其更加光滑。
接下来,经过调整尺寸工序的瓷砖进行烧制工艺。
烧制是将瓷砖放入烧窑中,经过高温烧制,使其硬化、密实,并赋予其色泽。
烧制工艺的温度和时间是关键,不同的瓷砖需要不同的烧制温度和时间才能达到理想的效果。
烧制结束后,瓷砖获得了一定的强度和硬度,成为了一种独立的建筑装饰材料。
最后,经过烧制工艺的瓷砖进行表面处理工艺。
表面处理是为了使瓷砖的表面更加美观、光滑,提升质感和耐磨性。
常见的表面处理工艺有釉面处理、喷釉和印花等。
釉面处理是将釉料均匀地涂在瓷砖表面,然后再次进行烧制,使釉料与瓷砖的表面融合,形成一层光滑的釉面。
喷釉是将喷涂的釉料均匀地喷洒在瓷砖表面,然后进行烧制。
印花是将图案印在瓷砖表面,然后通过釉面处理来保护图案。
综上所述,瓷砖制造工艺技术是一个复杂而精细的过程,需要经历原料处理、成型、调整尺寸、烧制和表面处理等多道工序。
通过合理的控制和操作,可以获得质量良好、外观精美的瓷砖,满足人们对建筑装饰材料的需求。
砖厂作业指导书——焙烧车间工艺流程暨作业指导
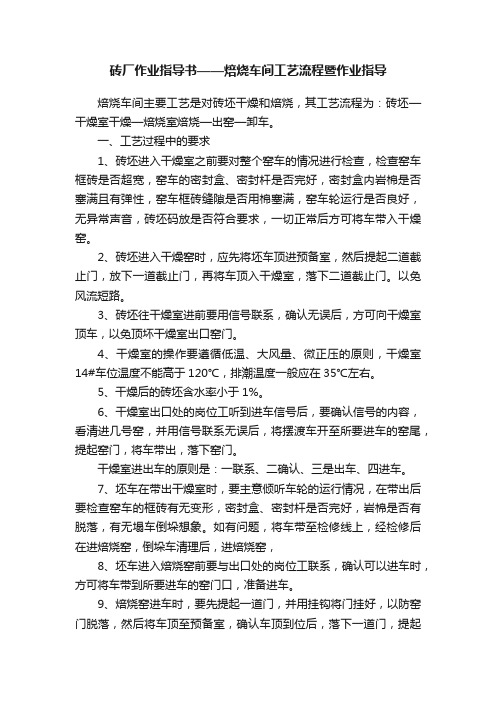
砖厂作业指导书——焙烧车间工艺流程暨作业指导焙烧车间主要工艺是对砖坯干燥和焙烧,其工艺流程为:砖坯—干燥室干燥—焙烧室焙烧—出窑—卸车。
一、工艺过程中的要求1、砖坯进入干燥室之前要对整个窑车的情况进行检查,检查窑车框砖是否超宽,窑车的密封盒、密封杆是否完好,密封盒内岩棉是否塞满且有弹性,窑车框砖缝隙是否用棉塞满,窑车轮运行是否良好,无异常声音,砖坯码放是否符合要求,一切正常后方可将车带入干燥窑。
2、砖坯进入干燥窑时,应先将坯车顶进预备室,然后提起二道截止门,放下一道截止门,再将车顶入干燥室,落下二道截止门。
以免风流短路。
3、砖坯往干燥室进前要用信号联系,确认无误后,方可向干燥室顶车,以免顶坏干燥室出口窑门。
4、干燥室的操作要遵循低温、大风量、微正压的原则,干燥室14#车位温度不能高于120℃,排潮温度一般应在35℃左右。
5、干燥后的砖坯含水率小于1%。
6、干燥室出口处的岗位工听到进车信号后,要确认信号的内容,看清进几号窑,并用信号联系无误后,将摆渡车开至所要进车的窑尾,提起窑门,将车带出,落下窑门。
干燥室进出车的原则是:一联系、二确认、三是出车、四进车。
7、坯车在带出干燥室时,要主意倾听车轮的运行情况,在带出后要检查窑车的框砖有无变形,密封盒、密封杆是否完好,岩棉是否有脱落,有无塌车倒垛想象。
如有问题,将车带至检修线上,经检修后在进焙烧窑,倒垛车清理后,进焙烧窑,8、坯车进入焙烧窑前要与出口处的岗位工联系,确认可以进车时,方可将车带到所要进车的窑门口,准备进车。
9、焙烧窑进车时,要先提起一道门,并用挂钩将门挂好,以防窑门脱落,然后将车顶至预备室,确认车顶到位后,落下一道门,提起二道门,再将车顶至预备室内,确认车顶到位后,将二道门放下,在往焙烧窑进车时,往预备室顶车需4步,如有要停止进车,待整修后在进车。
10、焙烧窑预备室无特殊情况不允许放坯车,以免砖坯回潮,影响烧结质量。
11、焙烧窑排烟管道的操作。
砖厂的生产工艺

砖厂的生产工艺砖厂是一种专门从事砖块生产的企业,其生产工艺是一个复杂而系统的过程。
下面将介绍一个常见的砖厂生产工艺。
首先,砖厂需要准备原材料。
常见的原材料是黏土、砂、水和其他掺合料。
黏土是最主要的原材料,质量的好坏直接影响着砖的质量。
砂用于调节黏土的粘度和增加砖的强度,水是黏土的稀释剂,而其他掺合料则是根据需要添加的,比如一些添加剂用于改变砖的某些性能。
其次,黏土需要经过破碎和混合的工序。
首先,原材料的黏土需要经过破碎机破碎成小块。
然后,黏土块经过细化,以获得更细的颗粒。
接下来,经过搅拌机的搅拌,将黏土均匀混合。
搅拌的时间和速度需要根据黏土的性质和所生产的砖的要求来确定,以确保黏土的质地和黏度得到最佳的调节。
第三,将混合好的黏土制作成砖坯。
这一过程主要是通过模具来完成的。
首先,将黏土均匀地放入模具中。
然后,用压力机对黏土进行压制,使其达到一定的压力和密度。
最后,用切割机将多余的黏土切割,以确保砖坯大小一致。
接下来,砖坯需要进行干燥。
通常,砖坯需要经过自然干燥和人工干燥两个阶段。
在自然干燥阶段,砖坯会被放置在通风良好的地方,以便黏土中的水分慢慢蒸发。
而在人工干燥阶段,砖坯会被放入干燥炉中,通过对炉内温度和湿度的控制,使砖坯在相对较短的时间内达到所需的干燥程度,以便进行下一步的烧制。
最后,进行砖块的烧制。
烧制是整个砖块生产过程中最重要的环节之一。
首先,将砖坯放入窑炉中,并逐渐升高温度。
当温度达到合适的程度后,窑炉内的化学反应开始,砖坯逐渐转化为坚硬的砖。
烧制的时间和温度需要根据砖的种类和规格来确定,以确保砖的强度和质量。
这就是一个常见的砖厂生产工艺。
从准备原材料到最后的砖块烧制,需要经历多个工序和环节,每一步都需要严格的控制和操作,以确保最终生产出的砖具有良好的质量和性能。
- 1、下载文档前请自行甄别文档内容的完整性,平台不提供额外的编辑、内容补充、找答案等附加服务。
- 2、"仅部分预览"的文档,不可在线预览部分如存在完整性等问题,可反馈申请退款(可完整预览的文档不适用该条件!)。
- 3、如文档侵犯您的权益,请联系客服反馈,我们会尽快为您处理(人工客服工作时间:9:00-18:30)。
生产工艺技术说明
生产的产品是煤矸石、黏土烧结多孔砖,利用制成坯体的煤矸石内残留碳的燃烧产生的热量,来供给坯体烧结所需的热量。
为了保证生产线产品质量和产量,根据原料性能特点,本项目采用半硬塑挤出成型,一次码烧工艺,机械化自动码坯,隧道式干燥与焙烧,有利于提高了产品的成品率。
原料处理采用混合料(煤矸石和页岩)集中处理,经过粗碎、细碎、高频振动筛筛选,筛上料再次细碎,筛下料加水搅拌进入陈化,陈化后的原料经搅拌搅拌挤出后,综合性能得到提高,可生产承重、非承重的空心砖或高档砖。
干燥室采用二条内宽4.60m隧道式干燥室,焙烧窑采用二条内宽4.60m隧道窑。
制品的干燥、焙烧过程实现微机监控,焙烧产生的余热用风机送进干燥室供坯体干燥脱水。
在冬季,同时又可以将热风经换热器把冷水加热后用于取暖。
为确保生产高质量的制品和各项工艺性能的可靠,主机及关键设备选用国内最先进的设备,主机选用能适应低塑性原料半硬塑挤出成型的高挤出压力、高真空度的双级真空挤砖机,全自动切条、切坯系统、自动码坯系统、窑车运转系统等。
所有风机选型充分考虑即保证生产需要,又考虑节能环保的要求,主要风机加有变频装置。
表3-1 工作制度
序号工段名称年工作日日工作日班工作日备注
1 原料制备240
2 7.5 有效
工作日
2 成型车间240 2 7.5
3 干燥、焙烧240 3 8.0
4 配电240 3 8.0
生产工艺流程
3.3.1 工艺流程图(如下图)
3.3.2 工艺流程说明(1)原料制备
生产中选用煤矸石全部从周边煤矿运来,煤矸石中若含有大块砂岩、石灰石岩等杂质可人工捡出,以确保产品质量。
可由装载机将煤矸石装入自卸车中,将煤矸石运到原料棚储存。
页岩是委托社会车辆从附近的页岩山运输到厂内原料棚内。
然后由装载机将两种原料按一定比例混合均匀并铲运到板式给料机中,板式给料机按工艺要求定量给料到胶带输送机上,输送到复摆型细碎颚式破碎机处进行破碎,破碎后的原料通过刮板给料机、圆盘给料机均匀喂料,再经反击锤式破碎机进行细碎,粉碎后物经过高频振动筛筛选,筛上料再次回到反击锤式破碎机进行细碎,筛下料输送到搅拌机中加水搅拌、混合,达到陈化的需要。
(2)原料陈化处理
混合料经双轴搅拌机加水搅拌处理后,通过胶带输送机运送到陈化库顶部的可逆移动配仓布料机上,将物料按一定班次规律均匀的堆存到陈化库中,物料的陈化时间应不少于3天。
陈化的作用是使原料中水分均化程度提高,原料颗粒表面和内部性能更加均匀,更趋一致,颗粒变得容易疏解,物料的成型性能得到提高。
(3)挤出成型
经过陈化的混合料,由液压多斗取料机连续装运到胶带输送机上,运到成型车间的箱式给料机处,定量向双轴搅拌挤出机给料。
原料通过再次加水搅拌,其水份控制在16~18%,输送到双级真空挤砖机;挤出成型采用高挤出压力的JKY60/60—40型双级真空挤出机,挤出压力达到4.0MPa,真空度达到≤-0.092MPa。
挤出的泥条经自动切条机、自动切坯机切割成需要规格的砖坯,经翻坯机组进行翻坯、编组后,经砖坯输送机输送到机械码坯处,自动化码坯机将砖坯码放到窑车上,以备干燥。
(4)干燥、焙烧
干燥与焙烧采用一次码烧工艺。
干燥窑采用内宽4.6米的隧道式干燥方式,该生产线采用2条干燥窑。
干燥热源利用隧道窑焙烧的余热。
通过调节系统自动调节送风温度及风量大小,确保砖坯干燥质量。
隧道窑采用内宽为4.6米大断面窑型,窑体结构设计成平吊顶结构。
采用内燃焙烧砖工艺,热源来自砖坯内燃料。
由煤矸石所含热量来满足烧砖工艺要求。
冷却带余热量经换热器换出,可用于车间采暖及生活设施。
隧道窑设有排烟系统、循环系统、余热系统、冷却系统和车底压力平衡系统。
该窑产量高、断面温差小、保温性能好,窑炉设自动控制系统,焙烧热工参数稳定,保证了烧成质量。