化学热处理与表面涂层在工具中的应用
刀具涂层制备方法及应用

刀具涂层制备方法及应用摘要:随着科学技术的发展,难加工材料的使用越来越多,为了适应这一要求,现代机械加工工业正朝着高精度、高速切削、干式切削技术、绿色制造以及降低成本等方向发展,也因为如此,人们对制造用刀具提出了更高的要求。
涂层刀具有高硬度和优良的耐磨性,延长了刀具的寿命。
当前刀具涂层制备方法主要包括化学气相沉积和物理气相沉积,刀具涂层的种类也日益丰富。
涂层刀具的发展呈现涂层成分多元化,涂层结构多层化,涂层基体梯度化和涂层工艺灵活化的趋势。
目前刀具涂层的制备也存在许多不足之处,主要体现在相关技术的研究不够深入方面。
本文就刀具涂层的制备方法、刀具涂层制备问题以及刀具涂层的应用等方面进行了一些论述。
关键词:刀具涂层CVD PVD绿色制造清洁化生产1、前言随着科学技术的进步,难加工材料的使用日益增多,材料的力学性能不断提高,而且,对加工效率的要求也不断提高,传统的未涂层刀具常常不能适应新的要求。
尽管目前常用的刀具如高速钢刀具(硬度66-70HRC)和硬质合金刀具(硬度89-93.5HR C)的硬度都很高,但是对于难加工材料的高效加工已不适用。
虽然可以采取各种措施提高刀具材料的硬度与耐磨性,但同时必然带来刀具材料抗弯强度和冲击韧性的下降,即材料变脆,从而影响刀具的使用性能。
在高速钢刀具基体和硬质合金刀具基体上涂覆一层或多层硬度高、耐磨性好的金属或非金属化合物薄膜(如TiC,TiAIN,Al203等)的涂层刀具,结合了基体高强度、高韧性和涂层高硬度、高耐磨性的优点,降低了刀具与工件之间的摩擦因数,提高了刀具的耐磨性而不降低基体的韧性。
因此,刀具涂层技术是解决刀具材料中硬度、耐磨性与强度、韧性之间矛盾的一个有效措施。
刀具涂层是一种耐磨涂层,其特性要求是:耐磨性好、硬度高、化学稳定性好、摩擦系数低、导热性及稳定性好。
刀具涂层有类似于冷却液的功能,它产生一层保护层,把刀具与切削热隔离开来(因为难熔金属化合物有比刀具基体和工件材料低得多的热传导系数),使热量很少传到刀具,从而能在较长的时间内保持刀尖的坚硬和锋利。
常用材料零件--耐磨零件
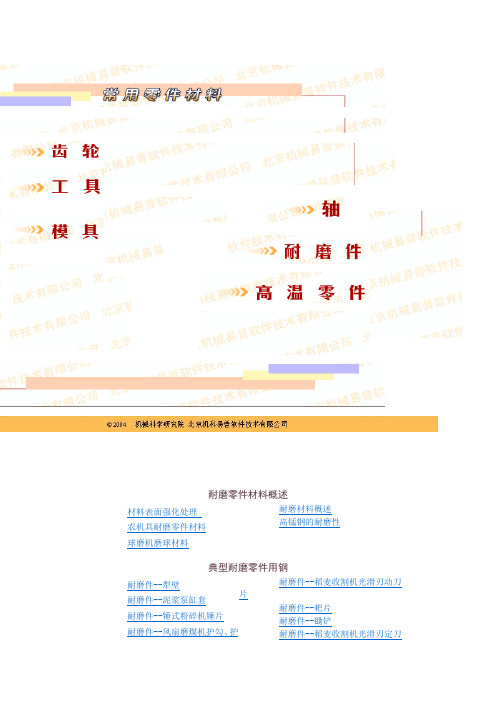
耐磨零件材料概述材料表面强化处理农机具耐磨零件材料球磨机磨球材料耐磨材料概述高锰钢的耐磨性典型耐磨零件用钢耐磨件--犁壁耐磨件--泥浆泵缸套耐磨件--锤式粉碎机锤片耐磨件--风扇磨煤机护勾、护耐磨件--稻麦收割机光滑刃动刀片耐磨件--耙片耐磨件--锄铲耐磨件--稻麦收割机光滑刃定刀甲耐磨件--旋耕机刀片耐磨件--甘蔗粉碎机切片耐磨件--剪羊毛机刀片耐磨件--切草机刀片耐磨件--旋耕机齿轮耐磨件--联合收割机链轮片耐磨件--泥浆活塞杆耐磨件--推土机铲运机铲刀耐磨件--凿岩机耐磨件--钻探机械钻具耐磨件--犁铧耐磨件--覆带板国外工程机械耐磨件用钢及热处理德国挖掘机斗齿日本挖掘机斗齿日本推土机、装载机、行走机构日本推土机、装载机、工作装置美国挖掘机斗齿材料表面强化处理材料表面强化处理是提高耐磨性的重要措施之一。
除了常用的化学热处理(渗碳、渗硼等)和表面淬火方法外,还有表面冶金强化(表面熔化、表面合金化、表面涂层)、气相反应沉积、离子注入等方法都能提高零件表面的耐磨性和疲劳强度等性能。
耐磨堆焊是以提高耐磨性为主要目的的堆焊工艺。
耐磨堆焊材料也就成为一类重要的金属耐磨材料。
常用的耐磨堆焊材料有铁基合金、钴合金、镍合金等。
耐磨堆焊材料的范围很广泛的。
应该在耐磨性、对环境的适应能力和可焊性等几方面综合考虑正确选用堆焊材料。
耐磨材料概述用于制造耐磨零件的金属耐磨材料包括钢、复合钢材和铸铁等。
高锰钢是历史悠久的耐磨材料,在恶劣工况条件下,不容易产生塑性失稳,而具有相当好的耐磨性;但它只有在冲击载荷及单位压力较大的磨料磨损条件下,产生加工硬化效应,才显示出较其他材料具有更优良的耐磨性。
对于冲击载荷不太大的易磨损零部件,目前较广泛选用成本较低的非合金钢(碳素钢)或中高碳合金钢,并采取一定的工艺措施以提高其耐磨性。
选用表面硬化钢或复合钢材制作的零部件,在耐磨、耐冲击等性能方面都具有明显的优点,可提高使用寿命,但成本较高。
化学在机械制造业中的应用
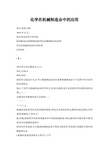
化学在机械制造业中的应用第l3卷第4期1999年l1月新乡师范高等专科学校JOURNALOFXINXIANGTEACHERSCOLLEGE化学在机械制造业中的应用f'安原初,r【_t,'新乡师专化学系新乡s3.∞V0l_13,No.4N0V,1999提要本文通过讨-7e-Z学与机械稍造业的关系和机械稍造业生产过程中有关化学的应用状况,展示了化学与机械制造业的学科交叉,相互渗透,相互促进厦共同发展的美好前菁.,;;~,一关键词化学机械制造交叉渗透…一.一一一一々;÷,?,...j,机械制造业更多涉及的是物理领域,'因为它是利用各种金属材料通过熔化,净却成型,机械加工.热压,冷拔,冲裁,组装等手段将其制戚各种不同的机械制品.然而,随着科学技术的不断发展.化学在机械制造业中的作用日益显现.本文拟就机械制造业中所涉及的化学及其相关同题作以简单的概括和讨论.l机械科遣业的范畴及主要生产工序机械制造业是一个范围广阔,涉及国计民生的产业,通常包括车辆,船舶,航空航天器工程,建筑,农用,轻工,化工,矿山机械.石油采炼设备等数十个领域.机械镪造业的主要生产工艺由于产品不同各有差异,但大都包括以下工艺程序: (1)俦造通过金属及其合金在熔融状态的流动性使其戚型为各种毛胚或直接通过精密铸造得到零件和半成品(2)锻造利用高温下金属及其台金的蘸好塑性施加外力使其改变形状得到零部件和半成品.(3)机械加工利用各种刀具使鼯材料和毛胚改变外部形状,包括锯,切,车,铣.刨,磨,镗,钻,冲压和拉伸等.(4)焊接利用局部界面的融台,使材料成型的工序.(5)热处理利用金属和台金在不同温度的金相组织会导致性能改变的原理进行的淬火,正火,退火,时效等工艺处理(6)表面处理对金属表面进行化学处理,电化学处理,进行金属或合金的沉积,离子注入,掺杂等工艺加工,赋予工件以特殊的性能,如抗蚀,装饰,耐磨,高表面活性,绝壤等.(7)防腐包装对零部件或产品进行的商品化处理2化学在机械制造业中的应用2,l化学在铸造过程中的应用俦遣,叉称金属流体成型工程.俗称翻砂.虽然目前某些铸造过程仍离不开砂箱,但就其工艺而言.已是事过境迁.铸造领域的新技术也紧紧地与化学联系在一起如精密铸造中的蜡型制作,压俦成型的模具及相关的脱膜剂等;更为重要的是:铸造是研削新型台金材料的重要手段铸造过程中的金属及其台金的配方,舍碳量调整,都是化学工作者探索的领域.在熔铸过程中杂质的去脒(磷,氮,硫等)都涉及到高温状态下的各种化学反应,要么使其成为有用的产物参与金属晶体成型,要么通过造渣使之脒去.另外,铸造中的温度参数,如浇俦温度,净却速度,温度梯度等参数的确定都可以直接影响金属晶体的金相组织和晶粒细化程度=2.2在锻造和热处理过程中曲应用(1)各种热处理过程1碇其化学原理热处理是一种与锻造,铸造,焊接等工艺密切相关的加工工艺=它的主要责任不是使金属材料获得一定的形状和R寸,而是以改变金属材料的组织和性能为目的,在铸.煅,焊的过程中,由于种种原因,不可避免的会出现这样或那样的缺陷;如铸造过程中,由于形状复杂,厚薄不均.会造成净却不均匀,组织变化不均匀,产生很大的铸造应力,加之从高温缓慢冷却,晶粒易于粗大;焊接过程中的局部加热与熔化,随后的冷却叉比较快.必然存在在很大的内应力.锻造时由于终煅温度过高或过低也会出现程大的魏氏组织和带状组织.遮些蛙路的存在将重影响工件的使用陛能.必须进行热处理,消除这些缺陷,改善盎相组錾{和材料性能.热处理更重要的意卫在干它是赋于工件最终性能的关键工序,不少零件加工成型后不能直接使用,而必7fJ第-I期寰原韧:化学在机械制造业中的应用须进行热处理,以获得最优的使用性能;如汽车,拖拉机后桥主动齿轮(材料为20CrMnT{),加工成型后要进行渗碳淬火和回火,这样其使用寿命可达到6000小时以上,而未经这种处理的寿命仅为1500小时以下热处理工艺般分为退火,正火,回火,淬火和化学热处理等几种.根据材料性能要求的不同,可以采取不同的工艺或几种工艺组合进行(2)热处理过程中的气氛可控技术由于空气中氡的存在,根据热力学原理,金属与氧的反应速度髓温度的升高而大大加快t对于最后成型的工件,这种氧化造成的尺寸变化是不能接受的,这就需要控制加热环境防止氧化发生;这种环境一般都是采用氮气,氲气,二氧化碳等惰性气体或氢气等还原性气体.这种热处理称为可控气氛热处理有时把粉束冶金制造技术也归于可控气氛热处理,粉末冶金包括体铁系台金,铜系台盘,镍系台盘等许多品种它是将粉末原料用粘结剂通过挤压等手段成型后进行烧结,烧结般在氧气,氧化碳气体中进抒,将一些氧化物如氧化铁,氧化铜等还原戚单质金属并形成舍金,可得到多孔的粉束冶金零件,经渗油和其他辅助处理铷得各种零部件,这种方法具有工序步.成本低,性能独特等优点,特别适台于制造轴承,金属电极等零件.2.3化学在机械加工中的应用机械加工是机械制造业中最重要的生产手段它包括车,铣,刨,磨,钻,镗,冲压,切割,拉伸等多种工艺方法(i)在车,铣,刨,磨加工中的应用在丰,铣,御,磨加工中,化学主要是通过词制台适的润滑冷却液,改善工件与刀具问的接触状况,选到保护刀具,提高其寿命和改善加工表面的目的.这些润滑冷却藏要具有冷却,宿惰,滴洗和防锈多种功能,对某些加工(如攻丝)还要有抗扳压的功能目前使用的普通乳化油系列,水剂透明系列和微乳化系列均有不阿产品的供应,也可以自行谓制它们的主要成分为矿物油,乳化剂,水,防锈添加剂,脱水剂等等的.(2)线切割和电火花加工的化学原理线切割和电业花加工都是模具制造的重要加工手段.线切割和电火花加工的加工环境都需要通过化学方{去调制出耐高温,高绝缘的液体介质,并优化其各项工艺参数.(3)拉伸加工与化学拉伸加工包括管棒材的拉拔和筒状器件的冲压成型及旋压成型=昔通的金属材料次拉深加工变形量都不能超过ioo,对要求大变形量的加工,如豫筒加工就需要进行退火处理以消除产生的应力,这种应力也叫做冷作硬化,它是由于金属的变形f起的晶格错位从而产生的强大应力,如不进行处理,就会出现破裂,造成机件和模具的损坏2.4在焊接过程中化学的应用焊接是两种或两种以上金属材料通过熔融结台在一起的工艺方法.(i)电焊和火焰焊电焊可以看作是局部金属的熔结过程.焊丝与被焊材料由于电场作用产生电弧并在焊缝附近形成高温熔糟,这时熔糟中的金属是液态的,焊料或附着焊条表面的焊药浮于其上茹形成熔渣:玲却后由于收缩系数不同而自动脱落.焊料及附着焊条表面的焊药的配制均是根据无机化学原理完成的火焰焊包括火焰熔焊和火焰钎焊.比如钢铁制品利用氢氧焰和己炔焰将铁丝与焊接机体融舍在一起的过程郢为熔焊熔焊时基体金属也是处于熔融状态.而钎焊时基体金属也是处于熔融状态.而钎焊时基俸金属不发生熔化而是通过钎焊剂的第三种材料的熔化完成焊接,例如钢铁材料的铜钎焊,锯钎焊等等钎焊过程中悍弃町的作用相当大,起着清理保护表面在焊接过程中不被氧化,促进焊接材料与基体进行牢固的结合.这些钎焊剂卫称焊料,也叫做焊药,都属于精细化工产品.研制良好焊剂是焊接工作者的重要工作.(2)特种焊接中的化学应用特种焊接是指非常规方法焊接.它一般包括摩擦焊,爆炸焊,电阻焊,高额焊和塑腔焊接等,摩擦焊是将两种材料进行摩擦使接触面产生高温而熔台在一起;爆炸焊接也是种特殊的焊接方法它是利lq爆炸声生的高温和强大的冲击澈将两种或者两种的材辑焊接在一起=电阻焊是和用金属接台部位存在有一定的电阻,当有强大电流通过时会产生高温使金属融化发生焊台例如点焊和对接焊等.7l新乡师范高等专科学校第13卷25化学在金属表面处理中的应用(1)表面赴理在机械制造业中的地位金属材料的表面处理是化学在机械制造业中最重要的应用通过表面赴理可以赋予工件良好的装饰性的和特殊的工艺性能,可以使本来设有使用价值的材料得以使用t可以使不能进行的工艺加工得以实现蜘如钢铁材料经过电镀获得cuN0复合镀层后,就具有了优异的防腐和装饰性能;铝及铝合金经阳极氧化可以获得具有高硬度和高耐磨性的表面层,使得它可以作为轴承等摩擦零件;经过电刷镀可以使尺寸超差或报废的大型工件蜘如轧辊,汽轮机主轴等等得以重新使用;通过化学腐蚀可以制造出带有精美图案的印刷滚筒这些是其它加工工艺所无法完成的.(2)化学处理与电化学处理化学处理一般包括以下几个方面:金属的化学氧化,磷化,钝化,化学镀层,化学抛光,化学腐蚀等.化学处理得到的膜层一般比较薄,这种方法设备比较简单,欢性的投资比较小.电化学赴理是指在电场作用下,电能和化学能同时作用于工件的处理的方法这种方法般包括如下几个方面:金属和合金的电镀,电化学抛光,电化学氧化等等.(3)化学与电化学腐蚀加工在各种加工手段中,化学与电化学腐蚀加工是种特殊的,不使用刀具和模具的加工手段通过掩胰保护还可以进行局部加工,这种掩膜可以是可剥型橡胶或者塑料,也可以是光敏树脂通过光化学反应得到保护层;通过这种工艺方法可以进行均匀减薄那工和局部减薄加工,也可以进行多层次保护得到深浅不同的浮雕图案.脒r这些掩膜的获得需要化学知识以外,多种化学腐蚀渡和电化学腐蚀液的配方及其工艺参数的选择也是化学工作者的工作范畴.(4)涂料盈涂装在机械制造业中,普通的涂装主要起到一般的防护和装饰作用,而特种I埭装不仅要起到一般的防护装饰作用,还要赋予产品特殊的性能.不论是普通涂装还是特种涂装,都要求涂膜与基体材料很好的结合,所以前处理是不可映少的,对黑色金属般采用踪油,酸洗,磷化工艺,而有色金属的多采用陡油,出光,钝化,化学氧化和电化学阳极氧化等工艺对于涂料的施工,普通溶剂型椽料往往是由底漆,面漆,罩光壤组成,对于电泳漆则为电泳底漆,面漆组成.对于粉末涂料可以次溶装完成特种涂料的施工的比较复杂,要根据基体材料,馀层组戚,使用要求等多种因索进行优化就目前来看,机械制造业涉及的特种涂料通常包括:耐热与烧蚀涂料(用于返回式航天器),防污涂料(用于各种舰船),阻尼涂料(减震),热控涂料(航天器),伪装涂料(军事装备及设施,包括防可见光,防红外,防雷达渡,防紫外等),红外吸收一红外辐射涂料(太阳能设备及军事装备)以及示温涂料(自动灭业设备及感温器材)等等这些颁域是化学与其他高新技术交相辉映,各展风栗的个大舞台.3化学与机械制造业的相互渗透及发展前景机械制造业对化学的要求是多方面.包括无机,有机,物化,分析以及材料化学,电化学和表面化学等.同样,化学对机械制造业的要求也是多方面,如各种化学反应所需要反应器(超高温,超高压,电离辐射,微波辐射等),创造反应条件所需的赴围设备(各种泵类,各种热源,传导器材和控制装置等),对反应过程及反应结果进行检测的装备(各种仪器,仪表)等等化学为机械制造业的发展提供了强有力的支持;机械制造业,特别是化工机械及仪器仪表业的发展也为化学向更高钡域的发展提供了机遇;正如北京大学苏勉曾教授所述:今天和明天的科学技术的本身以及它面临的要解决的国民经济任务,要求各学科的联合,缘合和相互理解.学科的发展也需要改革和开放,而不墨守传统的框架,不能自我孤立的封闭学科之间的交叉,既包括各学科中的概念,理论的融会贯通,也包括实际工作任务中相互支持和合作,以至^虽的交流和新代专多能跨学科^才的培养.正是化学与机械制造业的携手共进.才为我们描绘丁新世纪来临之际二者比翼积E的灿烂辉煌参考文献i鹿J棋.化之继祚束"-大竽化学1jllj£第五卷第五捌-Il2勉曾.'对亿学展"一天学化.】9十卷荦期?:,?E玉仓.《科节{£术史--l:目^畦走学t1版杠1uj:{3f】。
第5章 模具钢料的热处理-模具表面处理技术

第二节模具表面处理工艺概述模具是现代工业之母。
随着社会经济的发展,特别是汽车、家电工业、航空航天、食品医疗等产业的迅猛发展,对模具工业提出了更高的要求。
如何提高模具的质量、使用寿命和降低生产成本,成为各模具厂及注塑厂当前迫切需要解决的问题。
模具在工作中除了要求基体具有足够高的强度和韧性的合理配合外,其表面性能对模具的工作性能和使用寿命至关重要。
这些表面性能指:耐磨损性能、耐腐蚀性能、摩擦系数、疲劳性能等。
这些性能的改善,单纯依赖基体材料的改进和提高是非常有限的,也是不经济的,而通过表面处理技术,往往可以收到事半功倍的效果;模具的表面处理技术,是通过表面涂覆、表面改性或复合处理技术,改变模具表面的形态、化学成分、组织结构和应力状态,以获得所需表面性能的系统工程。
从表面处理的方式上,又可分为:化学方法、物理方法、物理化学方法和机械方法。
在模具制造中应用较多的主要是渗氮、渗碳和硬化膜沉积。
◆提高模具的表面的硬度、耐磨性、摩擦性、脱模性、隔热性、耐腐蚀性;◆提高表面的高温抗氧化性;◆提高型腔表面抗擦伤能力、脱模能力、抗咬合等特殊性能;减少冷却液的使用;◆提高模具质量,数倍、几十倍地提高模具使用寿命。
减少停机时间;◆大幅度降低生产成本与采购成本,提高生产效率和充分发挥模具材料的潜能。
◆减少润滑剂的使用;◆涂层磨损后,还退掉涂层后,再抛光模具表面,可重新涂层。
在模具上使用的表面技术方法多达几十种,从表面处理的方式上,主要可以归纳为物理表面处理法、化学表面处理法和表面覆层处理法。
模具表面强化处理工艺主要有气体氮化法、离子氮化法、点火花表面强化法、渗硼、TD法、CVD化学气相淀积、PVD物理气相沉积、PACVD离子加强化学气相沉积、CVA铝化化学气相沉积、激光表面强化法、离子注入法、等离子喷涂法等等。
下面综述模具表面处理中常用的表面处理技术:一、物理表面处理法:表面淬火是表面热处理中最常用方法,是强化材料表面的重要手段,分高频加热表面淬火、火焰加热表面淬火、激光表面淬火。
第十章-模具表面强化技术

*
表面化学热处理技术
二、渗氮(氮化)
(一)气体渗氮
表2 部分模具钢的气体渗氮工艺规范
牌号
处理 方法
渗氮工艺规范
渗氮层 深度/mm
表面硬度
阶段
渗氮温度/℃
时间/h
氨分解率/%
30CrMnSiA
一段
—
500±5
25~30
20~30
0.2~0.3
(一)气体渗氮
(1) 经过渗氮后钢表面形成一层极硬的合金氮化物,渗氮层的硬度一般可达到68~72HRC,不需要再经过淬火便具有很高的表面硬度和耐磨层,而且还可以保持到600~650℃而不明显下降。
(2) 渗氮后钢的疲劳极限可提高15%~35%。这是由于渗氮层的体积增大,使工件表面产生了残余压应力。
(3) 渗氮后的钢具有很高的抗腐蚀能力。
>58HRC
Cr12MoV
760~800HV
*
表面化学热处理技术
二、渗氮(氮化)
(二)离子渗氮
离子渗氮有如下特点:
(1) 渗氮速度快,生产周期短。
(2) 渗氮层质量高。
(3) 工件的变形小。
(4) 对材料的适应性强。
氮碳共渗
提高硬度、耐磨性、抗粘附性、抗蚀性、耐热疲劳性
冷挤模、拉深模、挤压模穿孔针
渗硼
具有极好的表面硬度、耐磨性、抗粘附性、抗氧化性、热硬性、良好的抗蚀性
挤压模、拉深模
碳氮硼三元共渗
提高硬度、强度、耐磨性、耐疲劳性、抗蚀性
挤压模、冲头针尖
盐浴覆层 (TD处理)
提高硬度、耐磨性、耐热疲劳性、抗蚀性、抗粘附性、抗氧化性
试论热处理工艺在机械制造业中的应用

随后 采取 淬火 以 获得 马 氏体组 织 。高 温形 变淬 火后 再 于适 当 的温度 回 火 ,可 以获 得很 高 的 强韧 性 ,其 强度 一 般 可 以提 高 1 5 ~ 3 5 %,塑性 可 以提 高 3 5 — 5 0 %,而 冲击 韧性 则 可 以大 幅 度 的增长 ,其抗 脆 断 能力 也 较高。
2 . 2相变 中形变 的形变 热处理 相变 中形变 热处 理 中较 经典 的方 式 主要有 等 温形 变处 理 和 马 氏体 相 变 中进行 形 变的 形变 热处 理 。下 面 以马 氏体 相变 中的形变 热处 理 为 例来 阐述 其应 用。 2 . 2 . 1 让 金属 工件 在奥 氏体 下进 行形 变 ,使 奥 氏体加 工硬化 ,诱发 其 部分转 变 为奥 氏体 ,加上 形变 时 马 氏体 加 工硬 化 的作 用 ,将 使 钢获 得显 著 的强化效果 。 2 . 2 . 2 诱发 马 氏体 的室温 形变 ,也 就是 利用 相变 诱发 塑性现 象使 钢 件在使 用 中不断发 生 马氏体转 变 ,从 而兼 有高强 度与超 塑后形 变热 处理 主要 是 针对 奥 氏体转 变 产物 进行 形变 强 化 的工 艺 。在 工 业上 常见 的 主要 是珠 光体 冷形 变 、珠 光体 的温 加 工 、回火 马 氏体 的形 变时 效等 。一般 形变 后 的金 属工 件都 需要 再次 进 行 回火 以消
大 部 分 低 合 金结 构钢 、合 金 工 具 钢 等 的淬 火 加 热 ,真 空 度 一般 选 用 1 . 3 3 — 1 3 . 3 P a ;而 高 合 金 钢 的 高 温 回 火 , 真 空 度 则 一 般 选 用 1 . 3 3 x 1 0 — 2 p a ;对于 高 速 钢等 的 淬 火加 热 ,我 们需 要 考 虑 元素 的蒸 发 效应 和 工件 之 间的相 互作 用 ,一 般选 用的真 空度 为 6 . 6 7 ×1 0  ̄ ' P a 的 高纯氮 。 2 . 真空 热处 理 的应用 真 空热 处 理可 以实现 无 氧化 、无 脱碳 、无渗 碳 等效 果 ,另外 还 可 以去 掉金 属工 件 表 面的 磷屑 ,能 够 达到 表 面光 亮净 化 的效 果 ,因此 近 年来 其应 用 范围 也越 来 越广 ,从 真 空退 火 的应 用延 伸 到真 空渗 碳 等应
刀具表面处理浅谈

切削刀具表面涂层技术浅谈王朋朋摘要:随着材料科学的发展和机械加工技术的进步,我们对切削金属时的刀具的要求也日益提高。
切削刀具向着高切削速度、高可靠性、长寿命和高精度的方向发展。
因此,刀具表面的涂层技术就显得愈加重要。
关键词:刀具表面处理;刀具表面涂层;物理气相沉积Abstract: With the development of Materials Science and Mechanical technology advances, we are metal cutting tool requirement also is increasing day by day. Cutting tool in high cutting speed, high reliability, long life and high precision in the direction of development. As a result, coating on the surface of the cutting tool technology becomes more and more important.Keywords: Tools Surface ; Tools Surface Coating; PVD随着科学技术,工艺生产的进步,对材料的要求愈来愈高,同时对切削材料的刀具的要求愈加复杂,要求切削的速度不断提高,传统的普通刀具往往不能够满足现在的新的要求。
虽然可以采取各种手段,提高刀具材料的硬度和耐磨性,但同时也会使刀具的强度和韧性下降,从而影响切削加工零件的使用性能。
刀具的耐磨性在于表面质量,提高表面质量的主要手段是对刀具表面进行表面处理。
一.刀具表面涂层技术介绍与特点表面涂层技术,就是再刀具基体上涂覆一层或多层硬度高、耐磨性好的金属或非金属化合物薄膜,一般采用TiC、TiAlN等,由于刀具表面涂层具有很高的硬度和耐磨性,同普通刀具相比,在原来的刀具强度的基础上,又可以很好的提高刀具的表面的硬度、耐磨性和刀具的切削性能,因而可以显著的延长刀具的使用寿命。
金属材料、表面处理及热处理概述

2.钢在加热时的转变 在热处理工艺中,钢的加热目的是为了获得奥氏体,奥氏体是钢在 高温状态时的组织,其强度及硬度高,塑性良好,晶粒的大小、成分及 其均匀化程度,对钢冷却后的组织和性能有重要影响。因此,钢在加热 时,为了得到细小均匀的奥氏体晶粒,必须严格控制加热温度和保温时 间,以求在冷却后获得高性能的组织。 3.钢在冷却时的转变 冷却是热处理的关键工序,成分相同的钢经加热获得奥氏体组织后, 以不同的速度冷却时,将获得不同的力学性能,见表2-1。
镀镍的作用:镍可以提高钢的机械性能,增加钢的强度、韧 性、耐热性,增加钢的防腐蚀、抗酸性及其导磁性等。镍 还能够细化晶粒、提高钢的淬透性和增加钢的硬度。 此外,在钢的热加工中,镍又有防止铜对金属表面产生有 害影响之功能。
碳素钢
(2)中碳钢
(3)高碳钢
(碳含量0.25%-0.6%)
(碳含量0.6%-2.11%)
二、铸铁
铸铁中的碳主要以渗碳体和石墨两种形式存在,根据碳的存在 形式不同,铸铁可以分为下列几种:(1)白口铸铁 (2)灰铸铁碳 (3)麻口铸铁 根据铸铁中石墨形态不同,铸铁又可分为:灰铸铁中的石墨呈 片状;可锻铸铁中的石墨呈团絮状;球墨铸铁中的石墨呈球状,蠕 墨铸铁中的石墨呈蠕虫状。
时效
操作方法:将钢件加热到80~200度,保温5~20小时或更长时间,然后随炉 取出在空气中冷却。 目的:1. 稳定钢件淬火后的组织,减小存放或使用期间的变形;2.减轻淬火 以及磨削加工后的内应力,稳定形状和尺寸。 应用要点:1. 适用于经淬火后的各钢种;2.常用于要求形状不再发生变化的 紧密工件,如紧密丝杠、测量工具、床身机箱等。
调质
操作方法:淬火后高温回火称调质,即将钢件加热到比淬火时高10~20度的 温度,保温后进行淬火,然后在400~720度的温度下进行回火。 目的:1.改善切削加工性能,提高加工表面光洁程度;2.减小淬火时的变形 和开裂;3.获得良好的综合力学性能。 应用要点:1.适用于淬透性较高的合金结构钢、合金工具钢和高速钢;2. 不 仅可以作为各种较为重要结构的最后热处理,而且还可以作为某些紧密零件, 如丝杠等的预先热处理,以减小变形。
- 1、下载文档前请自行甄别文档内容的完整性,平台不提供额外的编辑、内容补充、找答案等附加服务。
- 2、"仅部分预览"的文档,不可在线预览部分如存在完整性等问题,可反馈申请退款(可完整预览的文档不适用该条件!)。
- 3、如文档侵犯您的权益,请联系客服反馈,我们会尽快为您处理(人工客服工作时间:9:00-18:30)。
化学热处理与表面涂层在工具中的应用
渗氮
高速钢、基体钢、热模具钢和高碳高铬钢中都含有大量形成氮化物的合金元素,渗氮层的表面硬度高达1000HV以上,大幅度提高了耐磨性,并降低了摩擦系数。
渗氮处理已广泛应用于刀具、冷作模具和热作模具的热处理。
(1)刀具渗氮
高速钢刀具和以高速钢为基的钢结硬质合金刀具都可以在磨刃之后进行渗氮处理。
高速钢中含有大量的Cr、V、W、Mo等形成氮化物元素,渗氮后表面硬度很高,但渗氮层的脆性很大,如果处理不当,易崩刃。
所以高速钢渗氮应采用短时渗氮和低氮势。
一般在560℃渗氮,时间为20~60min,氨分解率在70%~90%范围内调节。
高速钢刀具渗氮不允许出现化合物层,扩散层的总深度控制在0.01~0.03mm之间,对于刃口较厚的连续切削的刀具可取上限,刃口较薄的刀具应取下限。
刀具在使用过程中经过重复磨刃之后,只要前刃面或后刃面之一保留着渗氮层,仍然可以收到提高切削寿命的效果。
(2)冷作模具渗氮
冷挤压凸模、冷镦凸模和冷锻模常用高速钢或基体钢制造,渗氮温度恰好在高速钢和基体钢的回火温度范围内。
在淬火回火并加工至最终形状之后进行短时渗氮,渗层深度只需略大于允许的磨损量,就可以大幅度提高模具寿命。
基体钢或低碳高速钢克服了普通高速钢易开裂、易崩刃的缺点,但耐磨性不如高速钢。
经过短时渗氮后三者的耐磨性则达到同样水平。
所以用基体钢或低碳高速钢制造冷挤压模并进行短时渗氮处理,是大幅度提高其寿命的有效措施。
高碳高铬工具钢制造的冷作模具也可以通过渗氮提高表面耐磨性,但渗氮温度应降至500℃,以减小基体硬度下降的幅度。
高速钢、基体钢、高碳高铬工具钢等高合金工具钢渗氮时间不宜过长,渗氮层深度不宜过深,表面不应出现化合物层,否则会引起崩刃或剥落。
低合金钢制造的冷作模具不宜进行渗氮处理,因低合金工具钢的回火稳定性差,在渗氮温度下硬度已降至40HRC以下。
(3)热作模具渗氮
热作模具钢含有Cr、Mo、W、V等形成氮化物元素,渗氮后表面化合物层
的硬度高于1000HV,扩散层的最高硬度也达到800HV以上。
热作模具钢承受的冲击载荷低于冷作模具,因此热作模具渗氮后一般允许带着化合物层投入使用。
化合物层有很高的耐磨性和低的摩擦系数,并能提高抗粘模的能力。
由于化合物层的热导率很低,减少了工件向模具传播的热量,降低了模面的温度和温度变化的幅度。
化合物层的这些特性有利于提高热作模具的使用寿命。
用于压铸模时,渗氮化合物层还起到提高抗液体金属冲刷和抗粘模的能力。
但是热作模具钢渗氮后化合物层很脆,所以厚度一般控制在3~6μm左右;承受冲击载荷较大的模具,宜控制在1~3μm;承受冲击载荷较低的模具,化合物层可在6~9μm 或8~12μm范围选择。
应根据使用和失效的方式,通过试验加以确定。
热作模具钢所含的合金元素使渗氮的扩散层具有很高的硬度和热强度,明显提高了热挤压模和热锻模抗压塌的能力。
渗氮层的总深度愈深,抗压塌的能力愈高。
但是由于渗氮层热导率低,所以渗氮层过厚,则容易产生热疲劳裂纹。
因此应根据具体模具的失效方式确定渗氮层深度。
热作模具钢的渗氮温度应不高于回火温度,例如3Cr2W8的渗氮温度为560℃,H13钢在500~540℃之间选择。
渗氮时间则根据所要求的渗氮层深度而定。
(4)塑料模、橡胶模、胶木模的渗氮
这类模具一般形状比较复杂,工作时所承受的应力和冲击载荷则很低。
则中、低碳钢或合金钢制造的模具经过短时渗氮处理之后,表面形成致密的化合物层,其耐磨性和抗擦伤能力足以满足使用要求。
而且化合物层有较高的耐腐蚀性,有利于提高塑料模的使用寿命。
渗氮温度一般为560~570℃,对热处理畸变要求很严格的模具,可适当降低渗氮温度。
渗氮时间决定于所要求的化合物层深度,大致在2~5h之间选择。
化合物层>12μm,表面易出现疏松。
对于短时渗氮后直接使用的模具,化合物层宜控制在8~12μm范围。
短时渗氮后经过抛光再使用的模具,化合物层可适当厚一些,但不宜超过20μm。
抛光时将表面疏松层抛掉,保留<12μm的致密化合物。
短时渗氮提高了模具的表面耐磨性,在基体材料选择时就可以着重考虑模具的加工性和经济性。
例如中碳钢正火处理或低碳合金钢退火处理适合于切削加工。
用冷挤压模腔的方法制造模具则可采用经过球化退火的低碳钢或纯铁制造,然后进行短时渗氮。
在历史上气体氮碳共渗和各种盐浴渗氮曾大量应用于模具热处理,但是这两种方法都会产生氰根,污染环境。
随后的研究表明,短时渗氮的效果不亚于盐浴渗氮和气体氮碳共渗。
因此,盐浴渗氮和气体氮碳共渗不应继续应用,可将其提高模具性能的经验移植于无毒的短时渗氮。
渗碳
我国学者戚正风教授开创了无莱氏体制高速钢及其渗碳的研究,无莱氏体高速钢的合金元素含量与高速钢相同,含碳量则降低到不出现莱氏体的范围,用渗碳的方法将表面含碳量提高到甚至超过普通高速钢的水平,形成在奥氏体基体上分布大量碳化物的渗碳层。
渗层中的碳化物并不是在钢液凝固时共晶反应的产物,所以不会成为莱氏体组织。
在渗碳温度下高合金奥氏体中合金元素原子还不可能进行长距离扩散,只可能在比较小的尺寸范围内与碳原子就地结合成细小的颗粒状碳化物。
渗碳温度愈低,渗碳层中的碳化物粒度愈细,在随后的淬火加热时也不易聚集长大。
淬火之后这种高合金渗碳层组织的耐磨性和强韧性都明显优于同样合金元素含量的高速钢,并在生产试验中取得明显提高刀具性能的效果。
目前,无莱氏体高速钢还未能推广的主要妨碍在于供硝渠道难以,以及工具制造厂现有的制造流程和生产线都无法实现无莱氏体刀具的批量生产制造,但不失为技术上合理的长远发展方向。
受无莱氏体高速钢渗碳的启发,李宇进行了Cr13型马氏体不锈钢渗碳试验[11],在渗层中形成密集分布的颗粒碳化物,对比试验结果表明耐磨性比Cr12MoV高3倍,有可能应用于冷作模具。
用低合金钢渗碳的方法制造模具比较少见。
这是因为模具整体所受的应力和冲击载荷都低于动力机械零件,用高碳钢和高碳低合金钢制造的模具,整体淬火、回火之后心部性能足以满足使用要求,而且高碳工具钢淬火温度低于渗碳温度,加热保温时间也远远短于渗碳时间。
相比之下,高碳钢淬火的热处理畸变较小,能耗低,生产效率高,是一种比较合理的技术路线。
只有在一些特殊的情况下,例如承受较大冲击载荷的细长的冲头,整体用高碳钢制造容易折断,用低碳钢渗碳淬火的方案才是合理的。
另外,有一些消耗量大、加工又比较复杂的模具,用冷挤压模腔的方法制造能降低模具制造成本,低碳钢的塑性成形阻力比工具钢低很多,在这种情况下也可以选择低碳钢渗碳的技术路线。
超硬涂层在工具中的应用
如前所述,单纯依赖于改变整体化学成分和整体热处理的途径提高工具的耐磨性是有局限的,而用物理气相沉积、化学气相沉积、离子注入或化学镀等方法在工具表面形成超硬薄膜涂层,可以大幅度提高工具的耐磨性和降低摩擦系数,大幅度提高工具的寿命。
早在20世纪60年代末和70年代初,TiC、TiN、TiC-TiN涂层硬质合金刀片相继面市,70年代和80年代出现性能更好的第二代TiC-Al2O和第三代TiC-Al2O-TiC等多种复合涂层硬质合金刀片,此后气相沉积技术发展迅速。
涂层材料有TiN、ZrN、HfN、TaN、NbN、CrN、CBN、Si3N4、TiC、ZrC、Cr7C3、SiC、Ti(C,N)、TiC(B,N)、Ti(Al,N)、β-C3N4金钢石等以及各种复合涂层,可涂覆在高速钢、模具钢、硬质合金、钢结硬质合金的基体材料上,使刀具、模具寿命提高几倍至几十倍,目前已经在大规模生产上广泛使用,并已成为刀具制造业中的主流。
涂层的种类很多,当前纳米涂层和复合涂层的展也很快。