气辅注塑原理
气辅注塑成型技术介绍
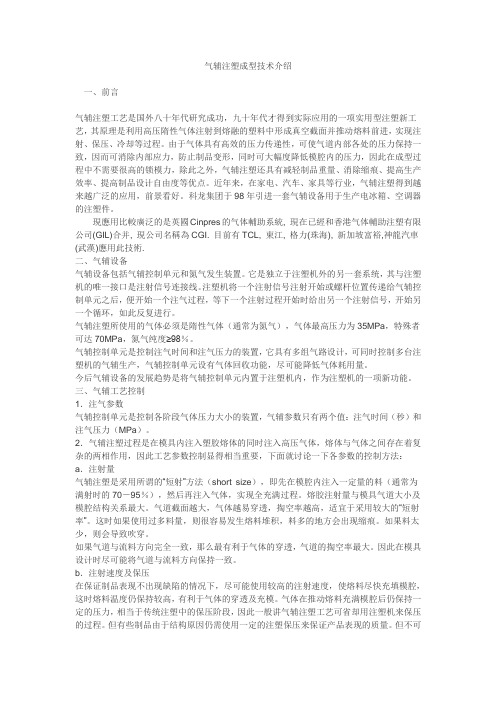
气辅注塑成型技术介绍一、前言气辅注塑工艺是国外八十年代研究成功,九十年代才得到实际应用的一项实用型注塑新工艺,其原理是利用高压隋性气体注射到熔融的塑料中形成真空截面并推动熔料前进,实现注射、保压、冷却等过程。
由于气体具有高效的压力传递性,可使气道内部各处的压力保持一致,因而可消除内部应力,防止制品变形,同时可大幅度降低模腔内的压力,因此在成型过程中不需要很高的锁模力,除此之外,气辅注塑还具有减轻制品重量、消除缩痕、提高生产效率、提高制品设计自由度等优点。
近年来,在家电、汽车、家具等行业,气辅注塑得到越来越广泛的应用,前景看好。
科龙集团于98年引进一套气辅设备用于生产电冰箱、空调器的注塑件。
現應用比較廣泛的是英國Cinpres的气体輔助系統, 現在已經和香港气体輔助注塑有限公司(GIL)合并, 現公司名稱為CGI. 目前有TCL, 東江, 格力(珠海), 新加坡富裕,神龍汽車(武漢)應用此技術.二、气辅设备气辅设备包括气辅控制单元和氮气发生装置。
它是独立于注塑机外的另一套系统,其与注塑机的唯一接口是注射信号连接线。
注塑机将一个注射信号注射开始或螺杆位置传递给气辅控制单元之后,便开始一个注气过程,等下一个注射过程开始时给出另一个注射信号,开始另一个循环,如此反复进行。
气辅注塑所使用的气体必须是隋性气体(通常为氮气),气体最高压力为35MPa,特殊者可达70MPa,氮气纯度≥98%。
气辅控制单元是控制注气时间和注气压力的装置,它具有多组气路设计,可同时控制多台注塑机的气辅生产,气辅控制单元设有气体回收功能,尽可能降低气体耗用量。
今后气辅设备的发展趋势是将气辅控制单元内置于注塑机内,作为注塑机的一项新功能。
三、气辅工艺控制1.注气参数气辅控制单元是控制各阶段气体压力大小的装置,气辅参数只有两个值:注气时间(秒)和注气压力(MPa)。
2.气辅注塑过程是在模具内注入塑胶熔体的同时注入高压气体,熔体与气体之间存在着复杂的两相作用,因此工艺参数控制显得相当重要,下面就讨论一下各参数的控制方法:a.注射量气辅注塑是采用所谓的“短射”方法(short size),即先在模腔内注入一定量的料(通常为满射时的70-95%),然后再注入气体,实现全充满过程。
浅谈气体辅助注塑成型
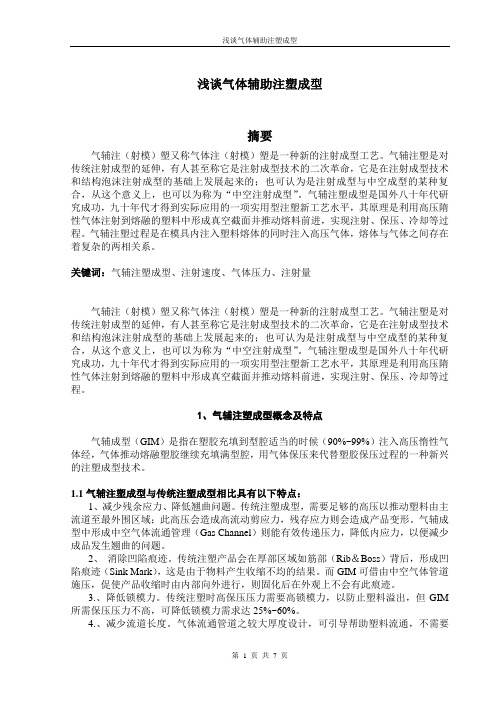
浅谈气体辅助注塑成型摘要气辅注(射模)塑又称气体注(射模)塑是一种新的注射成型工艺。
气辅注塑是对传统注射成型的延伸,有人甚至称它是注射成型技术的二次革命,它是在注射成型技术和结构泡沫注射成型的基础上发展起来的;也可认为是注射成型与中空成型的某种复合,从这个意义上,也可以为称为“中空注射成型”。
气辅注塑成型是国外八十年代研究成功,九十年代才得到实际应用的一项实用型注塑新工艺水平,其原理是利用高压隋性气体注射到熔融的塑料中形成真空截面并推动熔料前进,实现注射、保压、冷却等过程。
气辅注塑过程是在模具内注入塑料熔体的同时注入高压气体,熔体与气体之间存在着复杂的两相关系。
关键词:气辅注塑成型、注射速度、气体压力、注射量气辅注(射模)塑又称气体注(射模)塑是一种新的注射成型工艺。
气辅注塑是对传统注射成型的延伸,有人甚至称它是注射成型技术的二次革命,它是在注射成型技术和结构泡沫注射成型的基础上发展起来的;也可认为是注射成型与中空成型的某种复合,从这个意义上,也可以为称为“中空注射成型”。
气辅注塑成型是国外八十年代研究成功,九十年代才得到实际应用的一项实用型注塑新工艺水平,其原理是利用高压隋性气体注射到熔融的塑料中形成真空截面并推动熔料前进,实现注射、保压、冷却等过程。
1、气辅注塑成型概念及特点气辅成型(GIM)是指在塑胶充填到型腔适当的时候(90%~99%)注入高压惰性气体经,气体推动熔融塑胶继续充填满型腔,用气体保压来代替塑胶保压过程的一种新兴的注塑成型技术。
1.1气辅注塑成型与传统注塑成型相比具有以下特点:1、减少残余应力、降低翘曲问题。
传统注塑成型,需要足够的高压以推动塑料由主流道至最外围区域;此高压会造成高流动剪应力,残存应力则会造成产品变形。
气辅成型中形成中空气体流通管理(Gas Channel)则能有效传递压力,降低内应力,以便减少成品发生翘曲的问题。
2、消除凹陷痕迹。
传统注塑产品会在厚部区域如筋部(Rib&Boss)背后,形成凹陷痕迹(Sink Mark),这是由于物料产生收缩不均的结果。
气体辅助注塑工艺原理及优点.
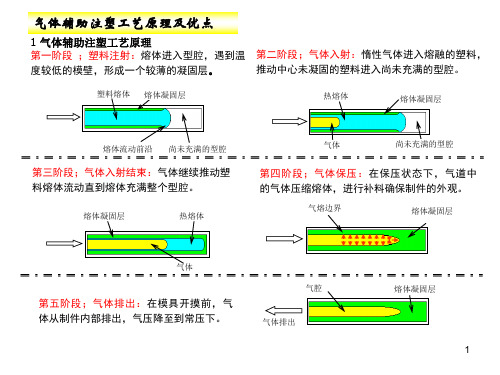
1 气体辅助注塑工艺原理 第一阶段 ;塑料注射:熔体进入型腔,遇到温 第二阶段;气体入射:惰性气体进入熔融的塑料,
度较低的模壁,形成一个较薄的凝固层。
推动中心未凝固的塑料进入尚未充满的型腔。
塑料熔体 熔体凝固层
热熔体
熔体凝固层
熔体流动前沿 尚未充满的型腔
第三阶段;气体入射结束:气体继续推动塑 料熔体流动直到熔体充满整个型腔。
射嘴进气方式,即使用专用的自封闭式或主动式气辅射嘴,在塑料注射结束后,将 高压气体依靠射嘴直接进入塑料内部,按气道形成一个延展的封闭空间-气腔并保持一 定压力,直至冷却,在模具打开之前,通过座台后退使射嘴与制品料道强行分离,使气 体排出制品。
图4自封闭气辅射嘴
图5主动式气辅射嘴 7
(2) 气针进气方式 气针进气方式即在模具的某个特定位置,安装排气装置-气针。当塑料注入型腔后,
2
气辅技术应用
气体辅助注射可以应用在除特别柔软的塑料以外的任何热塑性塑料和部分热 固性塑料。
根据气辅成型制品的结构形状不同,大致分为3类: (1).棒类制品,类似把手之类大壁厚制件; (2).板类制品,容易产生翘曲变形和局部表面收缩的大平面制件; (3).特殊制品,由传统注塑技术难以一次成型的特殊结构的制件。
(5).气道截面尺寸变化应平缓过渡,以免引起收缩不均。 (6).气道入口不应设置在外观面或制件承受机械外力处。
(7).进气口位置应接近浇口,以保证气体与熔体流动方向一致,但两者距离应>30mm, 以避免类制品
气辅注塑成型技术的主要应用之一就是板类制件的成型。因为气体总是沿 着阻力最小的方向前进,容易在较厚的部位进行穿透,因此,在板类制品设计时常 将加强筋作为气道,气道一般设在制品的边缘或壁的转角处。对制品的设计也就是 对加强筋和肋板的设计,即气道的设计。基本原则如下: (1).在设计制作加强筋时,应避免设计又细又密的加强筋。 (2).“手指”效应是大平面制件容易产生的主要问题。 (3).当制件仅由一个气针进气而形成多个加强筋或肋板(气道)时,气道不能形 成回 路。 (4).为避免熔体聚集产生凹陷,气道末端的外形应采用圆角过渡。 (5).采用多点进气时,气道之间的距离不能太近。 (6).气道布置尽量均匀,尽量延伸至制品末端。
气体辅助注塑成型技术简介.
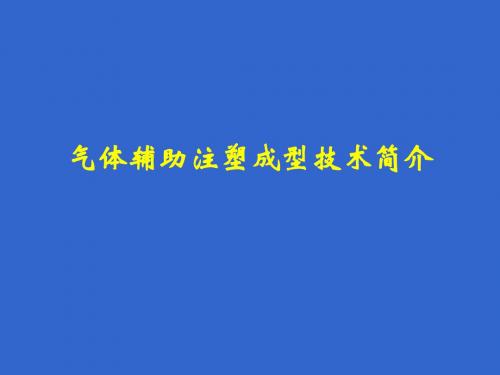
一、气体辅助注塑原理:
气体辅助注塑原理是把高压氮气经气辅 主控制器(分段压力控制系统)直接注射入 模腔内塑化塑料里,使塑件内部膨胀而造成 真空,但仍然保持产品表面的外形完整无缺, 减小产品表面的收缩、产品变形和翘曲,从 而达到提高产品的质量,降低成本的目的。
二、采用气体辅助注塑技术的优点:
应用气辅技术的国内公司:康佳、长虹、创维、科龙、 美的、海信等等;上海延锋伟世通、浙江远翅、上海龙贤汽 配、余姚塑料四厂、宁波国雅汽车内饰件厂以及各类注塑厂 都应用了气辅技术。
四、气体辅助注塑整系统的原理图:
A、整套系统
氮气 发生 器
低压 贮气缸
电动 高压 增压机
高压 贮气缸
气辅 主控 制器
单相电源 压缩空气 三相电源
六、气道形式:
• C、全部中空
七、我厂第一副气辅产品-前门拉手 (LZ111-6402101)
八、前门拉手采用气辅方案:
八、前门拉手采用气辅方案:
谢谢!
——END——
B、简易系统
氮气 缸瓶
气动 高压 增压机
压缩空气
单相电源
高压 贮气缸
气辅 主控 制器
单相——以定量塑化塑料充填入模腔内。所需塑料 份量要通过试验找出来,以保证在充氮期间,气体不 会把成品表面冲破及能有一理想的充氮体积。
2、充气期——注塑期中或后,不同时间注入气体,气体 注入的压力必需大于注塑压力,以达至产品成中空状 态。
模具的工作寿命; 7、降低注塑机的锁模压力,可高达50%; 8、提高注塑机的工作寿命和降低耗电量。
三、气体辅助注塑技术的应用:
基本上所有用于注塑的热塑性塑料及一般的工程材料 (如PS、HIPS、PP、ABS…)都适用于气辅技术。
气体辅助注塑成型的原理及优点

气体辅助注塑成型的原理及优点气体辅助注塑成型具有注射压力低、制品翘曲变形小、表面质量好以及易于加工壁厚差异较大的制品等优点,近年来发展很快。
它在发达国家用于商业化的塑料制品生产差不多已有20多年。
气体辅助注塑成型包括塑料熔体注射和气体(一般采用氮气)注射成型两部分。
与传统的注射成型工艺相比,气体辅助注塑成型有更多的工艺参数需要确定和控制,因而对于制品设计、模具设计和成型过程的控制都有特殊的要求。
气体辅助注射成型过程首先是向模腔内进行树脂的欠料注射,然后把经过高压压缩的氮气导入熔融物料当中,气体沿着阻力最小方向流向制品的低压和高温区域。
当气体在制品中流动时,它通过置换熔融物料而掏空厚壁截面。
这些置换出来的物料充填制品的其余部分。
当填充过程完成以后,由气体继续提供保压压力,将射出品的收缩或翘曲问题降至最低。
气体辅助注塑成型的优点:低的注射压力使残余应力降低,从而使翘曲变形降到最低;低的注射压力使合模力要求降低,可以使用小吨位的机台;低的残余应力同样提高了制品的尺寸公差和稳定性;低的注射压力可以减少或消除制品飞边的出现;成品肉厚部分是中空的,从而减少塑料,最多可达40%;与实心制品相比成型周期缩短,还不到发泡成型的一半;气体辅助注塑成型使结构完整性和设计自由度大幅提高;对一些壁厚差异较大的制品通过气辅技术可以一次成型;降低了模腔内的压力,使模具的损耗减少,提高其工作寿命;减少射入点,气道可以取代热流道系统从而使模具成本降低;沿筋板和凸起根部的气体通道增加了刚度,不必考虑缩痕问题;极好的表面光洁度,不用担心会像发泡成型所带来的漩纹现象。
运用气体辅助注塑成型技术后允许设计人员将产品设计得更加复杂,而模具制造商则能够简化模具结构。
制品功能不断增加和制品组件的减少使得生产周期缩短,无须进行装配和后期修整工作。
在成型CD托盘和机动车电子中心压配层板的生产中表明气体辅助注塑成型能够应用于薄壁制品的生产制造。
尺寸稳定性的提高,制品残余应力的减少以及翘曲量的降低是气体辅助注塑成型技术的一个主要优点。
气辅注塑成型技术介绍

气辅注塑成型技术介绍发布时间:2006-7-14一、前言气辅注塑工艺是国外八十年代研究成功,九十年代才得到实际应用的一项实用型注塑新工艺,其原理是利用高压隋性气体注射到熔融的塑料中形成真空截面并推动熔料前进,实现注射、保压、冷却等过程。
由于气体具有高效的压力传递性,可使气道内部各处的压力保持一致,因而可消除内部应力,防止制品变形,同时可大幅度降低模腔内的压力,因此在成型过程中不需要很高的锁模力,除此之外,气辅注塑还具有减轻制品重量、消除缩痕、提高生产效率、提高制品设计自由度等优点。
近年来,在家电、汽车、家具等行业,气辅注塑得到越来越广泛的应用,前景看好。
科龙集团于98年引进一套气辅设备用于生产电冰箱、空调器的注塑件。
二、气辅设备气辅设备包括气辅控制单元和氮气发生装置。
它是独立于注塑机外的另一套系统,其与注塑机的唯一接口是注射信号连接线。
注塑机将一个注射信号注射开始或螺杆位置传递给气辅控制单元之后,便开始一个注气过程,等下一个注射过程开始时给出另一个注射信号,开始另一个循环,如此反复{TodayHot}进行。
气辅注塑所使用的气体必须是隋性气体(通常为氮气),气体最高压力为35MPa,特殊者可达70MPa,氮气纯度≥98%。
气辅控制单元是控制注气时间和注气压力的装置,它具有多组气路设计,可同时控制多台注塑机的气辅生产,气辅控制单元设有气体回收功能,尽可能降低气体耗用量。
今后气辅设备的发展趋势是将气辅控制单元内置于注塑机内,作为注塑机的一项新功能。
三、气辅工艺控制1.注气参数气辅控制单元是控制各阶段气体压力大小的装置,气辅参数只有两个值:注气时间(秒)和注气压力(MPa)。
2.气辅注塑过程是在模具内注入塑胶熔体的同时注入高压气体,熔体与气体之间存在着复杂的两相作用,因此工艺参数控制显得相当重要,下面就讨论一下各参数的控制方法:a.注射量气辅注塑是采用所谓的“短射”方法(short size),即先在模腔内注入一定量的料(通常为满射时的70-95%),然后再注入气体,实现全充满过程。
气辅注塑工艺介绍L&L

© Yanfeng Visteon Proprietary / All Rights Reserved
© Yanfeng Visteon Proprietary / All Rights Reserved
气辅注塑成型有三种方式:溢料注射工艺,缺料注塑工艺,满料 注射工艺,
我们金桥现在是使用的溢料注射工艺:将模腔全部注满,然后通 过注射气体挤压一些熔体到溢流腔。溢流腔用来控制芯部材料的 流动,从而实现芯部材料的均匀分布。
储料 Screw back
普通注塑
取件 Taking off
顶出 Ejecting
开模 Mold opening
© Yanfeng Visteon Proprietary / All Rights Reserved
气体辅助注塑成型技术 (Gas Assistant Injection Molding, GIM) 是指在注塑 工艺中,熔融塑料充填到型腔 适当的时候(90%~100%)注 入高压气体,推动融熔塑料继 续充填满型腔,使塑件内部膨 胀而形成中空,保持产品完整 表面,用气体保压来代替塑料 保压过程的一种新兴的注塑成 型技术。由于气体具有高效的 压力传递性,可使气道内部各 处的压力保持一致,因而可消 除内部应力,防止制品变形。
图1.9 气辅控制器参数画面
© Yanfeng Visteon Proprietary / All Rights Reserved
气辅注塑工艺介绍 及问题改善
© Yanfeng Visteon Proprietary / All Rights Reserved
一.气辅成型工艺的简单介绍气辅注塑
合模 Mold closing
注射 Injecting
保压 Holding
气辅注塑

1)封闭式气体注射(SEALED INJECTION GAS)方法: * 是把气体直接注入模腔内,使塑料成品中空的方法。无需采用活阀,只是 通过简单模具加工,把气辅气嘴装在模具中。 * 在同一模具上,可有单一或多个注入气体的地方,这视乎同产品的需要, 慕求令产品有良好效果和提供产品设计有较大的灵活性。
太小会使气体流动失去控制 7.冷却要尽量均匀,内外壁温差要尽量小
8.在流道上放置合理流道半径的截流块,辅助注塑设备按工艺需求大致应有以下几类: 1、氮气机:主要用于氮气的制造 2、氮气增压器:主要是将氮气的气压加大,以便于氮气的注入 3、气辅控制器:主要用于控制氮气注入量、气压、时间及排气的控制,是
• 降低生产成本
– 由于减少了壁厚,因此降低了零件成品的总重量. – 由于壁厚较小,因此缩短了冷却时间和循环时间. – 由于降低了锁模力和注塑保压压力,能源消耗成本降低. – 由于零件的集成化,从而降低了装配成本.
• 降低投资成本
– 由于注射压力较低,因此可以降低注塑机的锁模压力,可使用吨位较小的注塑 机.
整个气辅设备的控制中心 4、气辅配件:主要有气针、气管及各种接头等,用于气辅设备与模具的连
接
因各种设备加在一起,占用的空间较大,现有很大一部分已采用一体化的气 辅系统。
END
同传统注射成型工艺相比.应用气体辅助注塑技术,有以下优点:
• 自由设计
– 综合功能较为复杂的塑胶零件可以整装为单一的组件. – 可以在同一零件上结合厚壁和薄壁部分. – 使用空心的"加强筋"部分可以提高其强度.
• 提高零件质量
– 由于减小了微收缩,因此扭曲和变形就减少了. – 消除缩痕. – 由于注射点的数量减少,所以波纹和熔接线也相应减少.
- 1、下载文档前请自行甄别文档内容的完整性,平台不提供额外的编辑、内容补充、找答案等附加服务。
- 2、"仅部分预览"的文档,不可在线预览部分如存在完整性等问题,可反馈申请退款(可完整预览的文档不适用该条件!)。
- 3、如文档侵犯您的权益,请联系客服反馈,我们会尽快为您处理(人工客服工作时间:9:00-18:30)。
气辅注塑原理
气辅注塑原理是指在注塑过程中通过气体辅助将塑料材料填充到模具中。
这种方法可以提高注塑产品的质量和降低生产成本。
下面我们将详细介绍气辅注塑的原理。
气辅注塑的工艺步骤分为四个部分:注塑、充气、冷却、脱模。
下面我们将逐一进行详细介绍。
注塑
注塑是气辅注塑的第一步。
在注塑过程中,塑料颗粒经过加热后熔化,并被注入到模具腔内。
注塑机通过控制注塑速度和压力来确保塑料进入模具腔的质量。
充气
当塑料填充模具腔中时,气体通过气道进入模具。
通过气体的辅助,塑料材料可以充满模具腔。
气体可以使用氮气或者空气等无毒的气体。
在充气过程中,气体通过模具腔的某些部位进入,将塑料向模具的其它部位顺利填充。
冷却
当塑料填充模具腔后,需要对塑料进行冷却,以便使其在脱模前达到精确的尺寸和形状。
模具通常使用水冷却或者油冷却方式。
冷却的持续时间取决于注塑产品的厚度,密度等因素。
脱模
冷却完成后,塑料产品被从模具中取出。
取出时需要注意产品的尺寸和形状不变形。
通常的方法是使用冷却水或者其他方式对产品进行冷却,以防止其变形或损坏。
如果塑料产品不能顺利脱模,需要重新注塑并进行修正。
气辅注塑的优点:
1. 塑料材料的填充更加均匀,从而可以获得更好的注塑产品。
2. 降低产品的塑料材料消耗,缩短生产周期。
3. 由于充气可以控制塑料材料在模具中的压力,因此能够消除产品的表面缺陷和毛刺。
4. 它也可以简化工艺流程,省去一些中间步骤,更加环保。
气辅注塑是一种高效、环保、节能的注塑工艺。
它可以提高生产效率,降低生产成本,同时还能有效改善产品的质量和外观。
近年来,气辅注塑工艺广泛应用于各个领域。
它可以用于制造电子产品、医疗器械、
汽车零配件、家用电器等。
它的灵活性和可塑性极高,满足了市场对产品多样化、品质一
致化、成本低价化等需求。
在汽车零配件的制造中,气辅注塑的运用已成为一种趋势。
由于汽车零配件的尺寸和
数量大,所以制造成本非常高。
而这里正是气辅注塑的优势所在。
利用气辅注塑工艺,能
够更好的控制塑料材料在模具中的填充,从而提高产品的密度、强度和耐用性。
经过加强
后的零配件在安装到汽车中时能够承受高强度的压力和振动,保证了驾驶中的安全性。
在家用电器的制造中,气辅注塑的运用也非常普及。
它能够生产出外形精美、质量优良、重量轻的产品。
这些产品具有良好的绝缘性能和机械性能,能够保证家庭电器的使用
寿命和安全性。
电吹风、电熨斗等产品都采用了气辅注塑工艺,为消费者带来更好的用户
体验。
在医疗器械的制造中,气辅注塑也扮演着重要的角色。
对于医疗器械而言,其质量要
求非常高,对于材料的选择、生产工艺等都有严格的要求。
采用气辅注塑可在控制产品尺
寸和形状精度的同时保证产品的安全性和质量。
气辅注塑工艺的应用已经覆盖到了众多的领域,其广泛的应用体现了气辅注塑作为一
种先进的制造工艺的优势。
未来,气辅注塑将继续发展,更加适应市场需求,为制造业的
繁荣发展作出更大贡献。
随着气辅注塑工艺的不断成熟,一些新的技术也逐渐被引入以提高生产效率和改进生
产质量。
下面将介绍一些与气辅注塑有关的新技术。
1. 超声波振动辅助气辅注塑工艺
超声波振动辅助气辅注塑工艺是指在气辅注塑加工中通过超声波振动的方式实现塑料
混合和填充。
相对于传统的气辅注塑工艺,此工艺的注模速率更快,而且塑料材料的均匀
度提高了。
可以获得更高品质的注塑产品。
2. 电子束辐照技术
电子束辐照技术是一种用高能电子束辐射对食品、医疗材料或塑料制品进行处理的技术。
电子束辐照可以改善塑料材料的物理性能、增强塑料材料的耐热性、抗老化性和抗紫
外线性。
未来,电子束辐照技术有望应用到气辅注塑加工中。
3. 立方体加热技术
立方体加热技术是通过立方体热流对塑料颗粒进行加热的一种技术。
在使用此技术时,可以采用更低的温度来完成注塑工艺,并且可以控制塑料材料在模具中的流动速度,最终
获得更优质的注塑产品。
4. 多项式注塑技术
多项式注塑技术是通过使用多个电磁阀控制注塑机的复杂程度,并通过电子控制系统
对注塑机进行控制,最终实现对注塑产品的质量和控制精度的提高。
采用多项式注塑技术
可以减少塑料材料的浪费,提高生产效率。
以上介绍了一些与气辅注塑工艺有关的新技术。
气辅注塑工艺可以用于生产各种不同
种类的产品,它为制造业带来了更高的效率和质量,同时也为人们提供了更优质、可靠的
产品。
未来,这一技术将不断发展,为各行各业提供更加先进、可靠的制造技术。
除了新技术的引入,气辅注塑工艺还能够通过优化工艺参数来提高注塑产品质量和生
产效率。
下面将介绍一些常见的工艺优化方法。
1. 模具设计优化
优化模具设计可以有效地提高注塑产品的品质。
在模具设计时,应考虑产品的塑料流
动路径、压力分布、模具温度、开模力和脱模力等因素。
如果模具设计合理,可以减少产
品的缺陷,提高产品的耐用性和减少制造成本。
2. 注塑工艺参数优化
在注塑工艺过程中,应根据不同的原材料和产品要求,逐步调整注塑参数。
注入速度、注射压力、模具温度、冷却时间等注塑参数可以影响产品的品质和产量等方面。
必要时,
还可以进行试模实验和模拟优化,以提高生产效率和产品品质。
3. 塑料材料选择优化
在气辅注塑过程中,选择合适的塑料材料非常重要。
选择优质、稳定性高、可回收使
用的塑料原料可以提高注塑产品的品质,降低生产成本,并对环境产生更小的影响。
通过优化模具设计、注塑工艺参数和塑料材料选择等优化方法,可以大大提高气辅注
塑的生产效率和产品质量。
加强质量控制体系和关注产品品质,也对提升注塑产品的竞争
力非常关键。
气辅注塑工艺的实际应用和研究已经得到广泛关注。
适当的技术革新和优化可以提高
气辅注塑加工的生产效率和产品质量,促进制造业的发展,也使消费者获得了更加优质和
可靠的产品。
在未来,它将继续发挥重要作用,推动制造业的前行。