砂芯制造工艺与技术
铸造工艺设计砂型和砂芯的制造
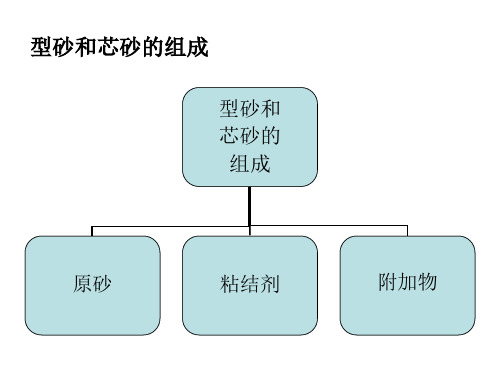
粘土颗粒与砂粒之间的粘结则被解释为:
砂粒因自然破碎及其在混辗过程中产生新的破碎 面而带微弱负电,也能使极性水分子在其周围规 则的定向排列。
粘土颗粒—砂粒之间的公共水化膜,通过其中水 化阳离子“桥”作用,使粘土砂获得湿态强度。
2.“表面联结”机理说
直接吸附在膨润土颗粒表面的极性水分子彼此联 结成六角网格结构,增加水分,逐渐发展成接二 连三的水分子层。粘土颗粒就是靠这种网络水分 子彼此接连,从而产生了湿态粘结力—这种极性 水分子有规则排列网络的联结可称为“表面联 结”。
2-2-1 钠水玻璃及钠水玻璃砂的硬化机理
• 一、钠水玻璃及其质量要求
• 水玻璃—各种聚硅酸盐水溶液的通称。
• 种类:钠水玻璃
•
钾水玻璃
•
季铵盐水玻璃的水溶液
• 钠水玻璃的化学式—Na2O﹒mSiO2﹒nH2O
• 特性:强碱性,PH=11~13
• 直接影响它的化学和物理性质的重要参数:
• 模数,密度,含固量,粘度。
3、原砂的颗粒形状 用光学显微镜或扫描电子显微镜观察原砂的颗粒 形状分类:
圆形砂—O 多角形砂—□ 尖角形砂—△
粒形对型砂性能的影响
①形状越圆—型砂就越易紧实,透气性也就越低; 对于使用树脂等化学粘结剂的型砂和芯砂而言, 粒形对强度的影响尤为显著;粘结剂加入量相同 的条件下,用圆粒砂的试样紧实程度高,而且砂 粒实际比表面小,比尖角砂强度高很多。 ②砂粒表面粗糙度—若有侵蚀沟痕,裂缝和孔洞 存在,粘剂消耗量增大。
受热后,产生大量挥发分,在高温下进行气相分 解,在砂粒表面沉积“光泽碳”—防止铸铁件表 面机械粘砂,提高铸件表面光洁度。
煤粉等附加物的光泽碳含量的测定—可用特殊装 置测出,但湿型砂的光泽碳形成能力较低,很难 直接测量。
砂芯制造工艺与技术

醛树脂作粘结剂,配制的型(芯)砂叫做覆膜砂像干砂一样松散。
其制壳的方法有两种:翻斗法和吹砂法(见图1)。
本帖相关图片如下:图 1 顶吹法和底吹法制造壳芯示意图壳法造型、造芯的优点是混制好的覆膜砂可以较长期贮存(三个月以上);无需捣砂,能获得尺寸精确的型、芯;型、芯强度高,质量轻,易搬运;透气性好,可用细的原砂得到光洁的铸件表面;无需砂箱;覆膜砂消耗量小;型、芯可以长期贮放。
尽管酚醛树脂覆膜砂价格较贵,造型、造芯耗能较高,但在要求铸件表面光洁和尺寸精度甚高的行业仍得到一定应用。
通常壳型多用于生产液压件、凸轮轴、曲轴以及耐蚀泵件、履带板等钢铁铸件上:充芯多用于汽车、拖拉机、液压阀体等部分铸件上。
(二)壳型砂用原材料及混制工艺(1)酚醛树脂壳法采用热线塑性酚醛树脂。
它是在苯酚过量(通常苯酚与甲醛的物质的量之比为1:0.75~0.85)及温度在105℃以下缩合制成的。
常用的硬化剂为乌洛托品,学名六亚甲基四胺,即(CH2)6N4,其加入量一般占树脂质量的10~15%。
(2)原砂壳法一般采用硅砂,对于表面质量要求很高的铸件,特别是壁很厚实、易产生粘砂的铸钢件,也常使用鋯砂、铬铁矿砂。
(3)附加物为了改善覆膜砂的性能,有时在覆膜过程中加入某些附加物。
例如加人硬脂酸钙(为砂量的0.25~0.35%),可防止覆膜砂存放期间结块;增加覆膜妙的流动性,制壳时易于顶出等。
加入石英粉(加入量为砂质量的2%左右),可提高覆膜砂的高温强度。
(4)覆膜砂混制工艺酚醛树脂覆膜砂一般以原砂为 100(质量比),酚醛树脂加入量为:对于壳型是3.5~6.0,壳芯是1.5~4.0,另加入乌洛托品和硬酯酸钙。
覆膜砂的混制工艺可分为冷法、温法和热法三种。
其中热法是一种适于大量制备覆膜砂的方法,需要专门设备。
混制时一般为先将加热到130~160℃的砂加到间歇式混砂机中,再加树脂混匀,熔化的树脂包在砂粒表面,当砂温降到105~110℃时,加入乌洛托品水溶液,吹风冷却,再加入硬脂酸钙混匀,经过破碎、筛分备用。
砂芯材料、工艺及制芯设备对铸造质量的影响

砂芯材料、工艺及制芯设备对铸造质量的影响砂芯主要用来形成铸件的内腔、孔洞和凹坑等部分。
浇注时,砂芯的大部分表面被液态金属包围,经受铁液的热作用、机械作用较强烈,排气条件差出砂、清理困难。
因此,与型砂比较,对芯砂的性能要求更高。
1.砂芯的分级过去很长一段时间,采用植物油(如桐油)等有机黏结剂制备的芯砂应用较多,它使用加热方式使砂芯固化。
但近几十年来,随着化学工业的发展和对铸件产量和精度要求的提高,化学黏结剂已广泛用于砂芯制备。
根据砂芯形状特征及在浇注期间的工作条件和产品质量条件,生产上常将砂芯分为5级,见表1-1。
对各类砂芯的性能要求,取决于砂芯特点和制芯工艺。
如果砂芯在芯盒内硬化成形(Ⅰ、Ⅱ级砂芯),则要求芯砂湿强度较低,以保证有好的流动性和减表1-1 砂芯的形状特征及性能要求分级轻制芯时的劳动强度;如果砂芯脱模后硬化(Ⅲ、Ⅳ、Ⅴ级砂芯),则要求砂芯有高的湿强度。
对于Ⅰ、Ⅱ级砂芯,着重要求砂芯制备时的流动性好,浇注时的发气性低,对砂芯的湿强度要求可低一些。
2.常用砂芯黏结剂及制芯工艺的分类由于对砂芯的要求不同,目前,铸造生产上应用于制芯的黏结剂和制芯工艺种类繁多,见表1-2。
表1-2 常用制芯工艺方法由于各类砂芯黏结剂及制芯工艺相差较大,应根据不同黏结剂的特点和制芯工艺的要求,严格控制工艺参数和制芯过程,才能获得尺寸精确、表面光整强度高、紧实度均匀的高质量砂芯,这也是获得高质量铸件的重要保证之一。
3.制芯设备及模具对铸件质量的影响制芯设备的精度和机械化、自动化程度,很大程度上影响着制芯的生产率砂芯的质量及其稳定性。
在设备工艺参数调定的前提下,制芯设备的机械化自动化程度越高,生产率越高,砂芯质量越容易保障;而人工制芯,砂芯质量受人为因素的影响较多,其稳定性降低。
另外,如果制芯设备出现故障,制芯工艺参数控制不稳定,废品砂芯也会增加。
保证制芯设备正常工作,是获得高质量砂芯的基本条件。
制芯模具或芯盒的精度及表面粗糙度对砂芯的精度及表面粗糙度有直接的影响,因此为了获得合格质量的铸件,必须保障制芯模具或芯盒具有良好的精度和较低的表面粗糙度。
铸造 砂芯

铸造砂芯铸造砂芯是铸造过程中的一项关键技术,它在铸件中起到支撑、定位、冷却等重要作用。
本文将从砂芯的定义、制备方法以及应用领域等方面进行阐述。
一、砂芯的定义砂芯是指将砂料与粘结剂混合后制成的空心砂块,它通常用于铸造过程中形成铸件内部的空腔或复杂形状。
砂芯的形状和尺寸可以根据铸件的要求进行设计和制备。
二、砂芯的制备方法1.湿型砂芯制备方法湿型砂芯是使用含水的砂料和粘结剂混合制备的。
首先将砂料经过筛分、清洗等处理,然后与粘结剂混合搅拌,形成湿性砂料。
接下来,将湿性砂料填充到砂芯模具中,并通过振动、压实等工艺手段使其成型。
最后,经过干燥处理,砂芯变得坚硬可用于铸造。
2.干型砂芯制备方法干型砂芯是使用无水的砂料和粘结剂混合制备的。
首先将砂料加热至一定温度,以去除其中的水分。
然后将无水砂料与粘结剂混合均匀,形成干性砂料。
接下来,将干性砂料填充到砂芯模具中,并通过振动、压实等工艺手段使其成型。
最后,经过加热处理,粘结剂固化,砂芯变得坚硬可用于铸造。
三、砂芯的应用领域砂芯广泛应用于铸造工艺中,特别适用于需要形成内部空腔或复杂形状的铸件。
以下是一些常见的应用领域:1.汽车发动机缸体和缸盖的铸造:砂芯用于形成汽缸体和缸盖内部的冷却通道。
2.工程机械零部件的铸造:砂芯用于形成液压缸、油管等内部结构。
3.锅炉管道的铸造:砂芯用于形成锅炉管道内部的空腔。
4.航空航天零部件的铸造:砂芯用于形成涡轮叶片、火箭喷嘴等复杂形状。
四、砂芯的优势和发展趋势砂芯作为铸造过程中的重要组成部分,具有以下优势:1.灵活性高:砂芯可以根据铸件的要求进行设计和制备,形状和尺寸多样化。
2.成本低:相比于其他制芯方法,砂芯的制备成本较低。
3.应用广泛:砂芯适用于各个行业的铸造工艺,具有广泛的应用前景。
随着科技的发展,砂芯制备技术也在不断进步,出现了一些新的制备方法和材料,如3D打印砂芯技术、陶瓷砂芯等。
这些新技术和材料的出现,使得砂芯制备更加精确、高效,同时也拓宽了砂芯的应用领域。
泥芯、砂芯制作作业指导书
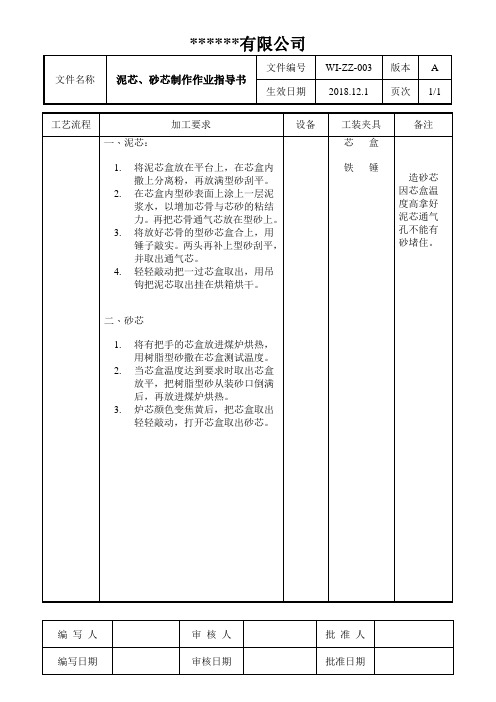
加工要求
设备
工装夹具
备注
1、泥芯:
1.将泥芯盒放在平台上,在芯盒内撒上分离粉,再放满型砂刮平。
2.在芯盒内型砂表面上涂上一层泥浆水,以增加芯骨与芯砂的粘结力。再把芯骨通气芯放在型砂上。
3.将放好芯骨的型砂芯盒合上,用锤子敲实。两头再补上型砂刮平,并取出通气芯。
4.轻轻敲动把一过芯盒取出,用吊钩把泥芯取出挂在烘箱烘干。
2、砂芯
1.将有把手的芯盒放进煤炉烘热,用树脂型砂撒在芯盒测试温度。
2.当芯盒温度达到要求时取出芯盒放平,把树脂型砂从装砂口倒满后,再放进煤炉烘热。
3.炉芯颜色变焦黄后,把芯盒取出轻轻敲动,打开芯盒取出砂芯。
芯盒
铁锤
造砂芯因芯盒温度高拿好泥芯通气孔不能有砂堵住。
铸造工艺流程中的砂芯设计要点

铸造工艺流程中的砂芯设计要点在铸造工艺过程中,砂芯的设计是至关重要的一环。
砂芯的质量和设计合理与否,直接影响着铸件的成型效果和性能。
本文将介绍铸造工艺流程中砂芯设计的要点,并详细解析每个环节的注意事项。
1. 铸造工艺流程概述铸造是一种将熔化金属浇注到模具中,经凝固和冷却后获得所需形状的工艺方法。
在铸造过程中,为了使金属铸件内部为空洞或某些特殊形状而使之成型,需要使用砂芯。
2. 砂芯材料选择砂芯材料的选择应根据铸件的要求来确定。
常用的砂芯材料有石膏砂芯、水玻璃砂芯和硬化砂芯等。
选择适合的砂芯材料,可以提高砂芯的强度和耐高温性能。
3. 砂芯设计要点(1)砂芯形状设计:砂芯的形状设计应根据铸件的形状和几何要求来确定。
砂芯的形状应与铸件配合紧密,确保铸件内部空洞的准确性和一致性。
(2)砂芯结构设计:砂芯的结构设计要考虑铸件的冷却和收缩情况,以及砂芯的支撑和固定方式。
合理的砂芯结构能够提高铸件的冷却效果,避免缺陷的产生。
(3)砂芯通气设计:砂芯内部空洞与铸件之间需要良好的通气,以保证熔融金属充分填充到空洞内。
通气孔的位置和数量需要合理设计,避免砂芯烧结或阻塞通气。
(4)砂芯的涂料选择:砂芯在使用前需要涂覆一层涂料,以提高砂芯的表面质量和耐热性。
根据铸件的要求和砂芯的材料特性,选择合适的涂料进行涂覆。
4. 砂芯制作工艺制作砂芯的工艺流程主要包括模具制作、芯盒装配、砂填充、振动压实、脱模等。
在每个环节中,都需要注意以下几个要点:(1)模具制作:模具的制作应根据砂芯的形状和结构要求进行,确保模具的精度和稳定性。
(2)芯盒装配:芯盒的装配应注意芯盒之间的配合准确性,避免砂芯在装配过程中变形或偏移。
(3)砂填充:砂芯的砂填充应均匀、充实,避免砂芯内部出现空隙或变形。
(4)振动压实:在砂芯振动压实过程中,应注意振动频率和振动时间的控制,以充分压实砂芯,提高其密实度。
(5)脱模:脱模时要注意砂芯的整体性和完整性,避免在脱模过程中产生砂屑或破损。
第2篇砂型和砂芯的制造
密闭系统中加热,测定气体的容积或压力,或称量残留物 的质量,判断发气量大小。
方法二:如图2-1-13所示,称取经过干燥的型砂盛入小舟→推 入850℃的管式加热炉加热→产生的气体经冷凝进入带刻度的 玻璃管中→测量大气压力下型砂的发气体积。
单纯地用湿态抗压强度衡量型砂性能并不太合适,引入劈裂 强度的概念。
劈裂强度(如图2-1-3所示)
在标准圆柱试样的径向加栽,使 试样沿其轴向平面断裂。劈裂强 度可以按照下式计算:
σsF=2F/πdL
σsF—型砂湿态劈裂强度(MPa) F—劈裂载荷(N); d—试样直径,为50mm; L—试样高,为50mm。
第2节 湿型砂的性能要求、检测原理及检测方法
对湿型砂的性能要求取决于铸造条件(包括:合金、浇注 温度、模样、造型方法、铸件结构)。
湿型砂的主要性能:水分、透气性、强度、紧实率、变形 量、破碎指数、流动性、含泥量、颗粒组成、发气性、附 加物含量、抗夹砂性、抗粘砂性等。
检测方法 在线检测:偏重造型性能,如紧实率、水分、抗压强度等,
第二篇 砂型和砂芯的制造
重点:型砂水分、透气性、强度; 难点:型砂变形量的测试。
型砂的分类 按粘接剂的类型:粘土砂、树脂砂、水玻璃砂、油砂等。 按粘结力产生机理不同:如图2-0-1。
物理固结:不含粘结剂,用物理学原理。例如磁型铸造、 V法造型。
化学粘结:在造型(芯)时依靠粘结剂物理化学作用达到 硬化,建立强度,使砂粒结合牢固。
湿型砂试样加压过程中的压力-变形(F-ε )曲线 1)OA段,压力σ与变形ε成线性关系,反映了砂样的粘弹性特
征。 2)AB段,过度阶段,非线性关系,粘塑性变形。压力到达极
砂芯铸造的工艺过程
砂芯铸造的工艺过程
砂芯铸造是一种常见的铸造工艺,它是通过在铸造前制造出砂芯,再在砂芯内注入液态金属,最后冷却凝固形成所需铸件的过程。
下面
将简要介绍砂芯铸造的工艺过程。
首先,选择合适的砂芯材料和适当的砂芯型腔。
根据铸件形状和
尺寸的不同,选择不同的砂芯型腔,并通过设计、调整和测试确认最
佳参数。
然后将选好的砂芯材料,如石英砂、石膏砂、水玻璃砂等,
经过制砂加工处理,得到均匀、致密、稳定的砂芯。
其次,制作砂芯。
将制好的砂芯材料放入砂芯模具中,通过振动、加压、模具开关等操作,将砂芯模具完整地填充好。
然后将砂芯模具
放在干燥室中,靠空气干燥或加热干燥,以使砂芯在模具中稳定形成。
在干燥过程中,还需注意控制温度、湿度、通风等条件,以保证砂芯
质量。
接下来,组装砂芯。
将制好的砂芯硬化后拆下,然后用砂芯粘合
剂或钢丝等连接多个砂芯。
将砂芯组合成一体,形成符合铸件形状的
整体砂芯,再将其放入砂箱内。
最后,注铸液态金属。
将整体砂芯放入铸造设备中,熔化黄铜、
铝合金、铸铁等铸造材料,注入砂芯内,待铸造材料冷却凝固后,拆
开砂芯,得到所需的造型,即铸件。
总之,砂芯铸造是一种将砂芯和铸造材料有机结合的铸造过程,
其优点是可制造出复杂形状、不易变形、表面光滑的铸件。
不过,由
于砂芯制作时间较长,成本较高,因此需要在实际应用中权衡成本与
生产效率。
低压铸造砂芯的工艺措施
低压铸造砂芯的工艺措施低压铸造砂芯是一种常用于铸造过程中用于形成内部空腔的一种工艺。
下面我将从原材料的选择、砂芯制备的工艺要点以及相关参数的控制等方面,详细介绍低压铸造砂芯的工艺措施。
首先,原材料的选择是影响低压铸造砂芯质量的重要因素。
一般来说,砂芯应选择具有良好耐高温性能、适宜砂芯制备的矿物砂粒作为主要原料,如石英砂、石膏等。
此外,还需要添加适量的粘结剂和硬化剂。
粘结剂主要用于粘结砂粒,常用的有冷硬化树脂、酚醛树脂等;硬化剂用于促进粘结剂的固化,常用的有酚醛固化剂、酮醛类固化剂等。
其次,砂芯的制备过程中有几个关键的工艺要点需要注意。
首先是砂芯的密实度控制,密实度的好坏直接影响到砂芯的强度和变形性能。
为了提高砂芯的密实度,可以在制备过程中采取震实法、振动法等措施。
其次是砂芯的形状和几何尺寸的控制,这需要依据铸件的形状和尺寸要求,在模具中设置合适的芯型。
同时,要注意模具的压力和温度的控制,以保证砂芯在形成过程中能够得到充分的填充和固化。
此外,还要注意砂芯表面的光洁度和整体的精度控制,采取合适的模具材料和表面处理手段,确保砂芯的质量符合要求。
最后,参数的控制是低压铸造砂芯过程中必不可少的环节。
一般包括压力、温度等参数的控制。
对于压力控制,需要根据具体的砂芯形状和尺寸,确定适当的压力大小,以保证砂芯能够充分填充模具并固化。
对于温度的控制,需要注意控制模具温度,以防止砂芯在填充模具的过程中过早固化或未能完全固化。
此外,还需要注意控制砂芯和铸件的匹配度,保证二者之间的配合良好,防止出现脱模、损坏等情况。
总之,低压铸造砂芯的工艺措施是一个复杂的过程,需要多方面的因素综合考虑和控制。
只有合理选择原材料,掌握砂芯制备的工艺要点,严格控制相关参数,才能够制备出高质量的砂芯,从而提高铸件的质量和产量。
满满的技术干货,铸造砂芯设计要点汇总
满满的技术干货,铸造砂芯设计要点汇总砂芯主要用于形成铸件的内孔、腔。
某些妨碍起模、不易出砂的外形部分可用砂芯形成。
砂芯的工作条件较为恶劣,因此对砂芯的要求:1)有足够的强度和刚度;2)排气性好;3)退让性好;4)收缩阻力小;5)溃散性好,易出砂。
砂芯设计包括:确定砂芯数量,每个砂芯的形状、尺寸;芯头的个数、形状和尺寸;芯撑、芯骨;排气方式;芯砂种类及造芯方法等。
一、砂芯数量的确定一个铸件所需的砂芯数量,主要取决于铸件结构和铸造工艺方案。
确定砂芯数量的原则是:尽量减少砂芯数量,以减少芯盒、制芯工时费用,降低铸件成本,同时,也应考虑制芯下芯,检查方便,保证铸件质量精度。
1.当内腔或孔的深径比(高度与直径或高度与宽度之比)不很大时,应才用自带砂芯。
自带砂芯的高度和宽度之比不能太大,否则拔模时容易损坏。
自带砂芯尺寸查表。
2.砂芯和分块砂芯整体制造的砂芯,易于保证铸件精度,工装数目少,砂芯强度和刚度较好。
但是,对于尺寸过大、形状复杂的砂芯,仍采用整体砂芯,操作不方便,应分成两个或几个砂芯来制造。
砂芯的分块原是:①填砂面应宽敞;②砂芯支撑面最好是平面,以便于安放和烘干;③分盒面尽量与分型面一致。
④分块应便于下芯、合箱及检查,保证铸件精度。
⑤尺寸精度要求高的部分,尽可能用同一砂芯形成;⑥ 尺寸过大的砂芯,为了便于造芯、下芯解决车间起重量不够的困难,可以分成几个小砂芯。
每个小砂芯需具有足够的强度和刚度。
二、芯头芯头是砂芯的重要组成部分。
芯头的作用是定位、支撑和排气。
芯头在保证定位可靠,支撑牢固、排气通畅的情况下,其数目越少越好。
1.垂直芯头垂直芯头有三种形式,a)上下都作出芯头,定位准确,支撑可靠,排气通畅。
一般常用这种形式。
尤其适于高度大于直径的砂芯;b)只作下芯头,不作上芯头,合箱方便。
适合于横截面积较大而高度不大的砂芯;c)上、下芯头都不作出,可降低砂箱的高度,便于调整砂芯的位置。
适合于比较稳的大砂芯。
当L与D之比≥5倍时,则采取加大的下芯头:D2=(1.5~2.0)D。
- 1、下载文档前请自行甄别文档内容的完整性,平台不提供额外的编辑、内容补充、找答案等附加服务。
- 2、"仅部分预览"的文档,不可在线预览部分如存在完整性等问题,可反馈申请退款(可完整预览的文档不适用该条件!)。
- 3、如文档侵犯您的权益,请联系客服反馈,我们会尽快为您处理(人工客服工作时间:9:00-18:30)。
醛树脂作粘结剂,配制的型(芯)砂叫做覆膜砂像干砂一样松散。
其制壳的方法有两种:翻斗法和吹砂法(见图1)。
本帖相关图片如下:图 1 顶吹法和底吹法制造壳芯示意图壳法造型、造芯的优点是混制好的覆膜砂可以较长期贮存(三个月以上);无需捣砂,能获得尺寸精确的型、芯;型、芯强度高,质量轻,易搬运;透气性好,可用细的原砂得到光洁的铸件表面;无需砂箱;覆膜砂消耗量小;型、芯可以长期贮放。
尽管酚醛树脂覆膜砂价格较贵,造型、造芯耗能较高,但在要求铸件表面光洁和尺寸精度甚高的行业仍得到一定应用。
通常壳型多用于生产液压件、凸轮轴、曲轴以及耐蚀泵件、履带板等钢铁铸件上:充芯多用于汽车、拖拉机、液压阀体等部分铸件上。
(二)壳型砂用原材料及混制工艺(1)酚醛树脂壳法采用热线塑性酚醛树脂。
它是在苯酚过量(通常苯酚与甲醛的物质的量之比为1:0.75~0.85)及温度在105℃以下缩合制成的。
常用的硬化剂为乌洛托品,学名六亚甲基四胺,即(CH2)6N4,其加入量一般占树脂质量的10~15%。
(2)原砂壳法一般采用硅砂,对于表面质量要求很高的铸件,特别是壁很厚实、易产生粘砂的铸钢件,也常使用鋯砂、铬铁矿砂。
(3)附加物为了改善覆膜砂的性能,有时在覆膜过程中加入某些附加物。
例如加人硬脂酸钙(为砂量的0.25~0.35%),可防止覆膜砂存放期间结块;增加覆膜妙的流动性,制壳时易于顶出等。
加入石英粉(加入量为砂质量的2%左右),可提高覆膜砂的高温强度。
(4)覆膜砂混制工艺酚醛树脂覆膜砂一般以原砂为 100(质量比),酚醛树脂加入量为:对于壳型是3.5~6.0,壳芯是1.5~4.0,另加入乌洛托品和硬酯酸钙。
覆膜砂的混制工艺可分为冷法、温法和热法三种。
其中热法是一种适于大量制备覆膜砂的方法,需要专门设备。
混制时一般为先将加热到130~160℃的砂加到间歇式混砂机中,再加树脂混匀,熔化的树脂包在砂粒表面,当砂温降到105~110℃时,加入乌洛托品水溶液,吹风冷却,再加入硬脂酸钙混匀,经过破碎、筛分备用。
五、热芯盒法制芯热芯盒法制芯,是用液态热固性树脂粘结剂和催化剂配制成的芯砂,填入加热到一定温度的芯盒内,贴近芯盒表面的砂芯受热,其粘结剂在很短时间即可缩聚而硬化。
而且只要砂芯的表层有数毫米结成硬壳即可自芯盒内取出,中心部分的砂芯利用余热和硬化反应放出的热量可自行硬化。
它为快速生产尺寸精度高的中小砂芯(砂芯最大壁厚一般为50~75mm。
)提供了一种非常有效的方法,特别适用于汽车、拖拉机或类似行业的铸件生产。
(1)热盒法用粘结剂热芯盒用的树脂有呋喃树脂和酚醛树脂,大多数是以尿醛、酚醛和糠醇改性为础的一些化合物,根据所使用的铸造合金及砂芯的不同以及市场供应情况,进行树脂的选择。
常用的呋喃树脂有:1)脲呋喃(UF/FA)树脂;2)酚呋喃(PF/ FA),树脂此类树脂不含氮,或含极少量的氮,主要用于制造铸钢和球墨铸铁件,硬透性较尿呋喃树脂稍差。
我国的呋喃一2型热芯盒树脂属于这类树脂中的一个品种;3)脲-酚呋喃共聚物(UF/ PF/FA),含氮高的这类树脂主要用于铸铁件.也可用于有色合金铸件。
(2)热芯盒法硬化用催化剂国内对呋喃-1型树脂砂最常用的催化剂是氯化铵和尿素的水溶液,其配比(质量比)为氯化铵:尿素:水=l:3:3。
(3)热芯盒法砂的工艺性能及树脂砂的配制热芯盒法可以使用任何干净、干燥的原砂。
要求砂芯有较好的透气性时,可选用稍粗的原砂;对铸件内表面要求很光洁的,可选用较细的原砂。
热芯盒砂可用一般碾轮式混砂机混碾,混制工艺如下:干砂十附加物—→加催化剂—→加树脂粘结剂—→出砂热芯盒制芯工艺通常采用射芯机射芯,呋喃Ⅰ型树脂砂的固化温度在140~250oC之间,芯盒温度保持在200~250OC较适宜。
一般几十秒即可从芯盒中取出砂芯。
六、气硬冷芯盒法制芯气硬冷芯盒法制芯是将树脂砂填入芯盒,而后吹气硬化制成砂芯。
根据使用的粘结剂和所吹气体及其作用的不同,而有三乙胺法、SO2法、酯硬化法、低毒和无毒气体促硬造芯法等方法。
(一)三乙胺法此法为美国Ashland油脂化学公司研制成功,1968年开始向铸造厂推广并取得应用,国外常称1socure法,或称酚醛一尿烷冷芯盒法,我国叫三乙胺法。
粘结剂由两部分液体组成:组分Ⅰ是酚醛树脂,组分Ⅱ为聚异氰酸酯。
催化剂为液态叔胺,可用三乙胺[(C2H5)3N](TEA)、二甲基乙胺(DMEA)、异丙基乙胶和三甲胺[(CH3)N3](TMA),造芯时,其工艺过程如图2所示。
填砂后向树脂砂中吹入催化剂气雾(压力0.14~0 2MPa)便能在数秒至数十秒内硬化,达到满足脱模搬运的强度。
本帖相关图片如下:图 2 三乙胺法造芯工艺过程采用三乙胺法造芯时,原砂采用干净的AFS细度50~60的硅砂,也可使用锆砂、铬铁矿砂。
原砂必须干燥,水分超过0.l%(质量分数),就会减少芯砂的可使用时间,降低砂芯抗拉强度。
典型的芯砂配方是树脂粘结剂占砂质量的 1.5%,由等质量的组分Ⅰ和组分Ⅱ构成。
(二)SO2法SO2法是继三乙胺法之后开发的一种新型吹气冷芯盒制芯和造型方法,用于铸造生产始1978年,近些年来又开发了一些新型SO2法。
1、呋喃树脂/SO2法此法在 1971年由法国 SaPic公司取得专利权,称Sapici法,直到1978年才用于生产,欧洲大陆称Hardox法,英国称SO2-Fast法,美国叫Insta-Darw法。
其造芯工艺过程类似三乙胺法。
SO2许多优点胜过其他方法,因此从钢铁到有色合金均有应用。
其主要优点如下;①热力度高,使铸件的尺寸精度和表面质量高(高于三乙胶法):②出砂性优良,对给镁合金也极易出砂;③树脂砂有效期特别长,混好的砂不接触SO2气体,决不会硬化;④发气量是有机粘结剂中最低的;⑤强度发展快。
SO2的缺点也很明显,例如:①树脂中游离糠醇汽化易使芯表面结垢;②低碳钢芯盒用于砂芯大量生产时,锈蚀是一个严重问题;③SO2泄漏,将引起严重环境问题;④过氧化物为强氧化剂,易燃烧,要妥善保管。
2、环氧树脂SO2法环氧树脂SO2法于19 8 3年用于生产。
此法与呋喃-SO2法比,芯砂的可使用时间更长(可达5天),而且基本解决了芯盒结垢和粘模问题,很适合大量生产。
环氧树脂SO2法有效地克服了呋喃一SO2法的大部分缺点,但是用于钢铁铸件时,由于易产生冲砂和夹砂,因此需涂敷耐火涂料;浇注系统应有助于平稳层流。
当使用水基涂料时,建议在低于81oC温度下烘干。
3、自由基硬化法自由基硬化法用于铸造生产始于1982年。
此法采用三种组分组成的液态粘结剂,包括:①丙烯基聚氨酯树脂;②少量有机氢过氧化物引发剂(用来激发自由基聚合)③用来提高抗拉强度、延长砂芯保存期的乙烯基硅烷增强剂。
此法用氮稀释的SO2气体促进硬化。
粘结剂的加入量通常为0.9~1.8%。
所用树脂混合物的典型组成是95%的粘结剂、3%的增强剂和2%的过氧化物引发剂。
催化剂气体由1~10%(典型的为2%)的 SO2和情性气体载体(氮)所组成。
每吨芯砂约需 SO2 0.45kg。
用干燥空气或氮清洗是为了充分分散S02气体催化剂,并使SO2随后从硬化好的砂芯或砂型中排出。
(三)乙缩醛硬化法(红硬法)乙缩醛硬化法又称红硬(red-set)法,这是因为该法用树脂砂硬化后变成粉红色而得名。
此法是由原联邦德国开发的,粘结剂是三级分体系。
组分1是树脂,是一种具有高反应的甲阶酚醛树脂水溶液,不合游离酚,含游离甲醛少于0.l%:组分2是活化剂,是不同类型的磷酸在无机酸中的浓缩水溶液;组分3是硬化剂,常用乙缩醛。
此法所配树脂砂在二周内使用仍有好的强度。
硬化时需要的乙醛量理论上占组分40%,实际为60~100%。
所制出的砂芯(型)有好的抗吸湿性,砂芯有强的抗毛刺能力。
但这一方法不宜采用橄榄石砂,高耗酸值砂也减慢硬化过程。
此法的工艺较复杂,对工艺参数要求严格,成本较高,价格为三乙胺法的2~3倍。
树脂自硬砂将砂子、液态树脂及液态催化剂混合均匀后,填充到芯盒(或砂箱)中,稍加紧实、即于室温下在芯盒(或砂箱)内硬化成型,叫自硬冷芯盒法造芯,简称自硬法造芯(型)。
自硬法可大致分为酸催化树脂砂自硬法、尿烷系树脂砂自硬法和酚醛一脂自硬法。
树脂自硬砂不仅用于造芯,亦用于造型,特别适用于单件和小批量生产,可生产铸铁、铸钢及有色合金铸件。
其主要优点是;①提高了铸件的尺寸精度,改善了表面粗糙度;②节约能源,节约车间面积;③砂中的树脂的质量分数,由早期的3~4%降到了0.8~1.2%,这是通过对原砂的处理及对树脂、催化剂、混砂设备、工艺等方面进行改进得到的,从而降低了成本;④大大减轻了造芯、造型、落砂、清理工人的劳动强度,便于实现机械化;⑤旧砂可再生,有利于防止二次公害。
(一)酸催化树脂自硬砂(1)酸催化树脂自硬砂用的树脂常用粘结剂为呋喃树脂和热固性酚醛树脂。
也有采用酮醛树脂与糠醇的混合物(AR/FA)、糠醇—甲醛聚合体(FA/F)、糠醇与其他活性化合物的混和物(FA/C)。
糠醇含量越高,氮和水的含量会愈低,粘结剂的质量也愈好,但价格也高。
(2)酸催化树脂自硬砂用的催化剂通常自硬法用催化剂应符合以下要求:①保证改工艺过程带所规才的硬化速度和强度;②具有低的粘度的液体,不产生沉淀;长期贮存时,性能不变;③如冬季运输引起冷凝,随后加热熔化,性能可回复;④价格合理,经济。
(3)可使用时间和脱模时间可使用时间是指自硬树脂砂混砂后能够制出合格砂芯的那一段时间。
脱模时间是指从混砂结束开始,在芯盒内制的砂芯(或未脱模的砂型)硬化到能满意地将砂芯从芯盒中取出(或脱模),而不致发生砂芯(或砂型)变形所需的时间间隔。
影响可使用时间、脱模时间的因素很多。
实验表明,所采用的原砂、树脂、催化剂的类型、质量和加入量、混砂工艺、环境温度和湿度,均对可使用时间和脱模时间有明显的影响,影响最大的为环境温度和催化剂加入量。
当催化剂量相同,室温不同时,温度低时可使用时间长;温度高时可使用时间短。
其趋势是温度每增加10oC,可使用时间缩短1/2-1/3。
室温相同时,催化剂入量减少,可使用时间明显增长;催化剂增多,可使用时间缩短,但是催化剂加入量超过一定范围后,可使用时间变化不大,但对脱模时间影响显著,温度变化也明显影响脱模时间,其趋势是每增加5 oC,脱模时间缩短1/2-1/3。
(4)混砂工艺合理地选用混砂机,采用正确的加料顺序和恰当的混砂时间有助于得到高质量的树脂砂。
混砂工艺如下:混砂混砂砂十催化剂——→树脂——→出砂砂和催化剂的混合时间的确定,应以催化剂能均匀地覆盖住砂粒表面所需的时间为准。
太短了混合不匀,树脂强度低,个别地方树脂砂型硬化不良或根本不硬化;太长了,影响生产率和使砂温上升。
树脂加入后的混拌时间也不能过短(混拌不均)和过长(砂温升高,可使时间变短),混拌时间一般通过实验确定。