溴化丁基橡胶
溴化丁基橡胶加工工艺

溴化丁基橡胶的基本配合主要由硫化体系、补强体系、增塑体系和防老体系组成。
溴化丁基橡胶的加工工艺主要包括混炼、压延、压出和硫化等工序。
避免产生焦烧和气泡始终是加工过程中的重要内容。
一、混炼溴化丁基橡胶可以用密炼机或开炼机进行混炼。
(一)开炼机混炼采用开炼机混炼溴化丁基橡胶时,辊筒速比宜为1:1.25,前辊(慢辊)辊温宜为40℃左右,后辊辊温稍高,宜为55℃左右。
因为溴化丁基橡胶倾向于包低温辊。
一般混炼加料顺序如下。
①投入部分橡胶,令其包辊,并存有少量堆积胶。
最好使用种子胶,即用少量上批溴化丁基橡胶胶料,以利操作。
②加入防焦剂、酸吸收剂、硬脂酸及1/4补强剂,进行混炼。
③加入剩余溴化丁基橡胶,调整辊距,保留少量堆积胶。
④加入剩余补强剂和填充剂,补强剂须在增塑剂之前加入;增塑剂可与非补强填充剂等一起逐步加入;保持少量堆积胶。
⑤最后加入硫化体系配合,包括氧化锌和促进剂,辊温须控制,以防焦烧。
⑥薄通、下片、冷却。
(二)密炼机混炼一般采用二段混炼工艺,即第一段制备母炼胶,其中不含硫化组分,如氧化锌和促进剂等。
第二段在较低温度下加入硫化体系配合剂。
采用密炼机混炼溴化丁基橡胶时,投料量即填充系数一般高于通用橡胶约5%~10%,以利于配合剂的分散和排除卷入的空气。
溴化丁基橡胶在混炼前的贮存不应过冷,至少在室温下停放,最好能预热,即40℃下预热24h,否则,采用冷橡胶混炼,会导致配合剂分散不良和聚合物结团。
混炼操作要点有以下几项。
①为了提高配合剂混入与分散效果,在投入配合剂之前,先将溴化丁基橡胶在密炼机中塑炼约1.5min,以缩短混炼时间。
②防焦剂,如氧化镁宜在混炼第一阶段加入,有利于安全和混炼。
③补强剂应在混炼早期加入,以增加胶料剪切力,有利于分散。
④增塑剂应在后期加入,以保证胶料在混炼前期维持最大剪切力。
⑤混炼温度要低些。
温度过高,胶料易碎,高于140℃时,会使聚合物脱卤化氢,导致硫化胶性能下降。
第一阶段混炼最高排胶温度一般控制在130℃以下。
溴化丁基橡胶配合及应用手册

图 4 显示了丁基橡胶的结构9。商用丁基橡胶 (IIR) 是异丁烯和少量异戊 二烯(通常摩尔百分比为 2)的共聚物。此图显示了聚合物链的两个不饱和位 置之间的平均分子量。同时还说明了丁基橡胶的有限化学活性。与之相比的是, 天然橡胶或合成聚异戊二烯中的单体链节包含两个不饱和位置。将溴引入丁基 聚合物中时,反应在异戊二烯的碳碳双键位置发生,这可以得到较高的交联反 应活性和新的交联化学性质,同时保持高饱和度、化学惰性结构的特性10。
合反应,生成丁基橡胶 (IIR),然后通过溴化来得到溴化丁基橡胶9。
丁基橡胶 (IIR) 是使用高纯度异丁烯和异戊二烯合成的。聚合机制包含复 杂的阳离子反应。催化剂体系是含引发剂的路易斯酸共引发剂。常见的路易斯 酸共引发剂包括三氯化铝、烷基氯化铝、三氟化硼、四氯化锡和四氯化钛。使 用的引发剂通常是布朗斯特德酸,例如水、盐酸、有机酸或卤代烷。在引发步 骤中,异丁烯单体与路易斯酸催化剂进行反应时会生成带正电荷的碳阳离子 (也称碳正离子)。图 1 是引发步骤的简单示意图,供演示使用。
丁基橡胶的最终分子量主要通过控制引发速度和链转移反应速度来确定。 对进料系统进行提纯,可以最大限度地减少水分和含氧有机化合物,防止这些 物质终止链增长步骤。氯甲烷和未反应的单体将随着蒸汽和热水闪蒸出,经过 干燥和提纯,然后再重新回收到反应釜中。稳定剂(硬脂酸钙)和抗氧化剂 (BHT) 将被输送到热水/聚合物悬浮液中,用来稳定聚合物和防止结块。
表I EXXON™ 溴化丁基橡胶牌号示例1
溴化丁基橡胶的研究
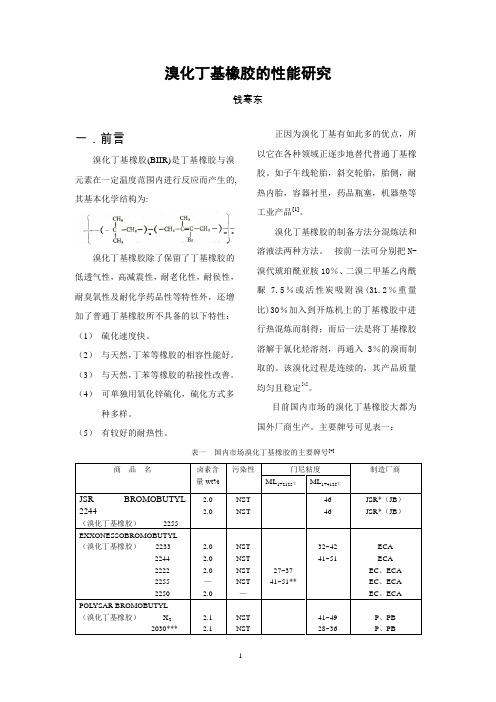
(5)左右开刀各四次后下片。 (6)将辊距放至最小处,薄通 5 次(其 中三次打三角包)。 (7)出片 3mm,冷却,待用。 辊温控制在 50℃一 60℃,混炼时间: 大约 15min 2.3.2 硫化
平板硫化:按测试所得的 t90 来确定 硫化时间,分别做成 100mm×100mm×2mm 的试片进行测试。 2.3.3 操作工艺的注意情况
27.0
11.6 800 20 50
43
11.7 790 35 49
30.4
100℃×72h,%
基本配方:2030 100,DTDM 2,TMTD 1,DM 0.5,氧化锌 2,硬脂酸 1,黑色填料 40 份或白色填料 80 份。
Ó²¶È
³¶¶ÏÇ¿¶È
60
40
16 0
14
12
10
8
6 900 800 0 700 600 500 400 300 200 100 90 80 0 70 60 50 40 30 20 10
溴化丁基橡胶的性能研究
钱寒东
一.前言
溴化丁基橡胶(BIIR)是丁基橡胶与溴 元素在一定温度范围内进行反应而产生的, 其基本化学结构为:
正因为溴化丁基有如此多的优点,所 以它在各种领域正逐步地替代普通丁基橡 胶。如子午线轮胎,斜交轮胎,胎侧,耐 热内胎,容器衬里,药品瓶塞,机器垫等 工业产品[1]。
溴化丁基橡胶的制备方法分混炼法和
氧化锌
硫磺
胺类
吗啡林
1.8
1.8
1.0
0.8
4.5
6.0
14.5
2.5
6.7
6.8
2024年溴化丁基橡胶市场前景分析

溴化丁基橡胶市场前景分析引言溴化丁基橡胶作为一种重要的合成橡胶材料,在许多工业领域拥有广泛的应用。
随着化工行业的快速发展,溴化丁基橡胶市场前景备受关注。
本文旨在对溴化丁基橡胶市场的发展趋势进行分析,为相关行业和投资者提供参考。
市场概况溴化丁基橡胶是一种合成橡胶材料,具有优异的耐候性、耐高温性和耐化学腐蚀性能。
它在建筑、汽车、航空航天、电子等领域有广泛的应用。
目前,全球溴化丁基橡胶市场正呈现稳步增长的趋势。
市场规模根据市场调研数据显示,2019年全球溴化丁基橡胶市场规模达到X亿美元。
随着新兴市场的崛起以及气候变化对橡胶需求的增加,预计市场规模将在未来几年保持平稳增长。
市场驱动因素•建筑行业的快速发展对溴化丁基橡胶的需求持续增加。
溴化丁基橡胶广泛应用于建筑密封材料、防水材料和胶粘剂等方面,随着城市化进程的推进和基础设施建设的加大,溴化丁基橡胶市场将持续增长。
•汽车工业是溴化丁基橡胶的重要应用领域。
随着汽车产量的增加以及对高性能橡胶材料需求的提高,溴化丁基橡胶市场将继续受益于汽车工业的发展。
•环保要求的提升也是溴化丁基橡胶市场增长的推动因素。
溴化丁基橡胶作为一种环保替代材料,可以取代石油基橡胶,满足环境保护要求,因此在一些环保敏感行业中有较高的应用需求。
市场挑战尽管溴化丁基橡胶市场面临广阔的发展空间,但也存在一些挑战。
原材料价格波动溴化丁基橡胶的主要原材料之一是丁基橡胶。
随着原油价格的波动以及全球供应链的变动,原材料价格的不稳定性对溴化丁基橡胶的生产成本和市场价格产生一定影响。
技术创新和竞争随着科技的进步和市场竞争的加剧,溴化丁基橡胶行业需要不断进行技术创新以提升产品性能和质量,以保持竞争力。
市场趋势绿色、环保的发展趋势随着社会对环境保护意识的提高,市场对绿色、环保产品的需求不断增加。
溴化丁基橡胶作为一种环保替代材料,在市场上具有广阔的应用前景。
高性能应用的拓展溴化丁基橡胶具有优良的性能特点,如耐高温、耐候和耐化学腐蚀等。
溴化丁基橡胶的应用研究及市场分析

溴化丁基橡胶的应用研究及市场分析溴化丁基橡胶(BIIR)是IIR的改性产物,改性的目的是提高IIR的活性,改善其与不饱和橡胶的相容性,提高自粘性、互粘性及共交联能力,同时保持IIR的原有特性。
IIR溴化后除增加了交联位置外,同时也增强了双键的反应性。
这是由于C-Br键的键能较小,溴化丁基橡胶的硫化反应活性较高,所以其具有较快的硫化速度和较强的硫化适应性,而且与通用橡胶的共硫化性能较好。
与普通丁基橡胶相比,溴化丁基橡胶增添了以下特性:(1)硫化速度快;(2)与天然橡胶、丁苯橡胶的相容性好;(3)与天然橡胶、丁苯橡胶的粘接性能提高;(4)可单独用氧化锌硫化(BIIR是唯一可单用硫黄或者用氧化锌硫化的弹性体),硫化方式多样化;(5)有较好的耐热性。
溴化丁基橡胶正是凭借如此多的优点,在多种应用领域内正逐步替代普通丁基橡胶,如子午线轮胎、斜交轮胎、胎侧、内胎、容器衬里、药品瓶塞和机器衬垫等工业产品。
溴化丁基橡胶是制造无内胎轮胎和医药用制品不可替代的原材料。
1溴化丁基橡胶的生产方法BIIR的制备方法有干混炼溴化法和溶液溴化法。
干混炼溴化法是在开炼机上将N-溴代琥珀酰亚胺、二溴二甲基乙内酰脲或活性碳吸附溴(质量分数为0.312)与IIR进行热混炼而制得BIIR;溶液溴化法是将IIR溶解于氯化烃溶剂,再通入质量分数约为0.03的溴而制备,该过程是连续的,产品质量均匀稳定。
BIIR中溴的质量分数最佳值为0.017-0.022。
2溴化丁基的应用研究2.1工艺要求溴化丁基橡胶分子链上存在双键,同时含有溴原子,因此可以采用多种方法进行硫化,应根据橡胶制品所要求的物理性能选择硫化体系。
溴化丁基橡胶的混炼、压延和压出操作工艺与门尼粘度相同的普通丁基橡胶相似,但由于溴化丁基橡胶硫化速度较快,容易焦烧,所以应该注意下列情况:1.炼胶温度。
溴化丁基橡胶的混炼温度若超过130℃,有焦烧危险,并且温度过高,胶料容易破碎,导致胶料加工不良。
溴化丁基橡胶的研究.

(6将辊距放至最小处,薄通5次(其中三次打三角包。
(7出片3mm,冷却,待用。
辊温控制在50℃一60℃,混炼时间:大约15min
2.3.2硫化
平板硫化:按测试所得的t90来确定硫化时间,分别做成100mm×100mm×2mm的试片进行测试。
2.3.3操作工艺的注意情况
溴化丁基的混炼、压延和压出操作工艺与门尼粘度相同的普通丁基橡胶相似,但由于溴化丁基橡胶的硫化速度较快,容易焦烧,所以要注意下列情况。
(3与天然,丁苯等橡胶的粘接性改善。
(4可单独用氧化锌硫化,硫化方式多
种多样。
(5有较好的耐热性。
正因为溴化丁基有如此多的优点,所以它在各种领域正逐步地替代普通丁基橡胶。如子午线轮胎,斜交轮胎,胎侧,耐热内胎,容器衬里,药品瓶塞,机器垫等工业产品[1]。
溴化丁基橡胶的制备方法分混炼法和溶液法两种方法。按前一法可分别把N-溴代琥珀酰亚胺10%、二溴二甲基乙内酰脲7.5%或活性炭吸附溴(31.2%重量比30%加入到开炼机上的丁基橡胶中进行热混炼而制得;而后一法是将丁基橡胶溶解于氯化烃溶剂,再通入3%的溴而制取的。该溴化过程是连续的,其产品质量均匀且稳定[4]。
2.1
NST
NST
41~49
28~36
P、PB
P、PB
*只销售不制造**门尼粘度ML1+8(100℃ ***部分交联型
二.实验
为了全面了解溴化丁基橡胶的性能,掌握其应用技术,本文就此进行了配合技术的研究,确定了原材料的配合用量,重点研究了溴化丁基橡胶的多种硫化体系及各自特点;各种补强填料对溴化丁基橡胶性能的影响;通过对胶料的t90,t10,常温拉伸性能,耐热空气老化性能,以及压缩永久变形等性能的测试来反映溴化丁基橡胶的一些性能。此外,还对溴化丁基橡胶的再生利用的性能展开了研究分析。
溴化丁基橡胶的化学结构及溴化合成反应原理

溴化丁基橡胶的化学结构及溴化合成反应原理[-CH2-CH=CH-CH2-CH2-CH2-]n其中,-CH2-CH=CH-为丁二烯单体的重复单元。
乳液聚合是将丁二烯单体溶解在水中,并与乳化剂进行共聚合反应,形成稳定的悬浮液。
在乳液中,乳化剂的疏水部分与丁二烯单体的亲水部分相互作用,形成胶束结构,使得丁二烯单体得以分散在水中。
同时,乳液中会加入催化剂,如过硫酸铵,以促使聚合反应的进行。
通过加热反应体系,可以使得丁二烯单体逐渐聚合成长链的聚合物,即丁基橡胶。
溴化反应是将合成的丁基橡胶与溴化剂进行反应,以在橡胶分子上引入溴原子。
溴化剂常用的有溴气、溴乙烷等。
在反应过程中,溴化剂会与橡胶分子中的一些双键发生加成反应,使得分子链断裂并引入溴原子。
这样,溴化丁基橡胶的分子结构就发生了改变,其中的双键被溴原子所取代。
溴化丁基橡胶的溴化反应原理是根据共轭双键的特性。
共轭双键是指分子中相邻的两个双键之间只隔有一个单键的情况。
在共轭体系中,共轭双键上的π电子能够通过共享形成的π-π分子轨道得到稳定,因此具有较高的反应活性。
溴化反应中,溴化剂攻击共轭双键上的π电子,形成一个高能的中间体,然后与溴化剂发生加成反应。
这样,通过溴化反应引入溴原子,改变了链的结构,使得橡胶的物理性质发生了变化。
溴化丁基橡胶广泛应用于橡胶制品中,具有优良的耐低温性、耐热性和化学稳定性。
同时,由于橡胶分子中引入了溴原子,使得橡胶分子带有极性基团,使得橡胶更容易与其他物质发生反应,从而改善橡胶的加工性能和使用性能。
溴化丁基橡胶制备工艺及研究进展总结分析

溴化丁基橡胶制备工艺及研究进展总结分析第一节溴化丁基橡胶制备工艺分析一、干混炼溴化法我们知道~干混炼溴化法即为干法~是将成品丁基橡胶和卤化剂通过螺杆挤压机~在机械剪切作用下对丁基橡胶进行卤化。
其反应装臵包括进料区、反应区、中和区、洗涤区和出料区等几个操作区。
丁基橡胶和卤化剂通过这几个操作区~生成卤化丁基橡胶。
由于干混卤化法产品质量不稳定~目前较少采用。
二、溶液溴化法溶液溴化法就是湿法~是将丁基橡胶溶解在正己烷中~再与液溴在一定温度范围内反应~溴化后中和、洗涤以及回收。
该溴化过程是连续的~其产品质量均匀稳定。
丁基橡胶的湿法卤化方法很多~丁基橡胶与卤化剂在反应管中进行卤化生成卤化丁基橡胶~是最重要的一种方法。
三、溴化丁基橡胶合成过程中影响因素研究国内一些企业和研究机构重点考察液溴浓度、胶液浓度、停留时间对溴化丁基橡胶的不饱和度、门尼黏度、溴含量、微观结构的影响。
结果表明:随着液溴浓度和反应时间的逐渐增加~溴含量会不断升高~最后逐渐趋于一个理论最大值~同时不饱和度和门尼黏度会随液溴浓度的增加而下降。
并且~在良好的条件下~只需将液溴和丁基橡胶中双键的物质量比值控制在0.85,1范围内~溴化反应时间为30s,60s~所制备的溴化丁基橡胶中的溴元素质量百分比含量就能达到1.5%,2.5%的理想范围内。
溴化丁基橡胶主要存在两种微观结构:溴代仲和溴代伯位烯丙基构型~前者占据了主导地位。
溴化反应过程中存在分子结构重排~即溴代仲位烯丙基构型向溴代伯位烯丙基构型发生转化。
通过对溴化丁基橡胶微观结构的模拟计算~发现溴代仲位烯丙基构型体系的能量要略微低于溴代伯位烯丙基构型~说明在溴化反应中更容易得到溴代仲位烯丙基构型占优势的产物。
还发现在溴代伯位烯丙基构型中的C在溴代仲位烯丙基构型中更短~说明键能更高一些。
第二节溴化丁基橡胶制备与结构表征研究一、实验部分介绍该实验的原材料为:丁基橡胶,Polysar,~301~不饱和度摩尔分数1.8%,液溴~正庚烷和四氢呋喃均为分析纯~北京化学试剂厂生产,硬脂酸钙~工业级~北京化学试剂厂生产,环氧大豆油~工业级~杭州硕亚油脂化工厂提供,3-氯过苯甲酸~工业级~北京有朋精细化工公司提供。
- 1、下载文档前请自行甄别文档内容的完整性,平台不提供额外的编辑、内容补充、找答案等附加服务。
- 2、"仅部分预览"的文档,不可在线预览部分如存在完整性等问题,可反馈申请退款(可完整预览的文档不适用该条件!)。
- 3、如文档侵犯您的权益,请联系客服反馈,我们会尽快为您处理(人工客服工作时间:9:00-18:30)。
前言卤化丁基橡胶的研究与开发始于20世纪50年代以后,目的是提高丁基橡胶硫化性能并改进它与其他橡胶并用的相容性能。
1953年,Morrisay开发出丁基橡胶溴化的方法。
1954年美国Goodrich Chemical公司以工业规模生产出溴化丁基橡胶Hycar2204。
但早期生产的溴化丁基橡胶因溴化工艺不够成熟,产品质量不高,于1969年停产。
1965年以后,Polysar公司成功地开发了一种连续法制造溴化丁基橡胶工艺,并与1971年以工业化产品投放市场。
其后其子公司在比利时的Antwerp 建立装置,与1980年开始生产溴化丁基橡胶。
1980年,Exxon Chemical 公司引进Polysar 技术,在英国Fawley建厂,生产溴化丁基橡胶。
1965年后,原苏联以干法生产溴化丁基橡胶。
溴化丁基橡胶是卤化丁基橡胶一类重要品种,是丁基橡胶经溴化取代反应制得的弹性体,目前它在轮胎、橡胶工业制品和其他橡胶制品等领域中的应用十分广泛。
溴化丁基橡胶(BIIR)是含有活性溴的异丁烯-异戊二烯共聚物弹性体。
由于溴化丁基橡胶拥有丁基橡胶基本饱和的主链,所以其具有丁基聚合物的多种性能特性,如较高的物理强度、较好的减振性能、低渗透性、耐老化以及耐天候老化。
卤化丁基橡胶气密层的发明和使用在许多方面成就了现代子午线轮胎。
在轮胎气密层胶料中使用这类聚合物可以改善保压性能,提高气密层与胎体间的粘合性能以及轮胎的耐久性。
由于溴化丁基聚合物主链高度饱和,所以,其硫化机理要比天然橡胶或聚丁二烯橡胶等通用弹性体复杂得多。
卤化异戊二烯链节的立体化学结构以及常用促进剂的碱性在硫化过程中都起着重要的作用。
所以了解溴化丁基弹性体和溴化丁基弹性体配合的化学机理具有重要意义。
溴化丁基橡胶如果配合得当,在轮胎气密层以外的其他领域也会具有极好的使用性能,如用于轮胎胎侧、汽车发动机减振垫、特种胶带覆盖胶以及医药领域。
溴化丁基橡胶(BIIR)是含有活性溴的异丁烯-异戊二烯共聚物弹性体。
由于溴化丁基橡胶拥有丁基橡胶基本饱和的主链,所以其具有丁基聚合物的多种性能特性,如较高的物理强度、较好的减振性能、低渗透性、耐老化以及耐天候老化。
溴化丁基橡胶相对于丁基橡胶而言,由于卤素的含性较高,所以具有较宽的硫化特性。
溴化丁基橡胶的结构类似于氯化丁基橡胶,与氯化丁基橡胶一样,相对于丁基橡胶,由于卤素的活性较高,所以其也具有较宽的硫化特性。
卤化丁基橡胶与不饱和通用弹性体如天然橡胶(NR)、聚丁二烯橡胶(BR)和丁苯橡胶(SBR)具有较好的共硫化性能,同时又保持了基本饱和的主链结构所拥有的其他性能。
与氯化丁基橡胶相比,由于溴化丁基橡胶中碳-溴键的键能比氯化丁基橡胶中碳-氯键的键能低,所以溴化丁基橡胶的交联活性要高得多,从而使溴化丁基橡胶胶料具有较快的硫化速度,可以使用多种硫化体系硫化。
因此,溴化丁基橡胶与通用弹性体的共硫化匹配性要比氯化丁基橡胶的好。
EXXON™星形支化溴化丁基橡胶是含有支化剂的异丁烯与异戊二烯的溴化共聚物,具有独特的分子量分布,包含部分高分子量的星形支化分子,胶料的加工性能优于普通溴化丁基橡胶。
一、溴化丁基聚合物溴化丁基橡胶是通过溴与丁基橡胶的己烷溶液反应制得的。
BF 固特里奇公司的Crawford 和Morrissey 最早发表了由少量溴,采用分批工艺改性丁基橡胶的研究结果,他们使用溴化剂如N-溴代琥珀酰亚胺,采用分批工艺进行溴化。
在埃克森美孚化工公司,研究人员研究了在丁基橡胶己烷溶液中用元素氯氯化丁基橡胶。
1960年在伦敦发表的一篇论文中介绍了丁基橡胶的氯化和溴化。
除了以前关于交联机理以及硫化胶的物理和化学性能方面的研究外,还有人探讨了卤化机理。
氯化丁基橡胶的工业化生产始于1961 年,其优良的性能和较好的成本效率使其在一些大型工业应用领域如轮胎气密层中的应用受到重视。
按照合同,为BF 固特里奇公司生产了一些溴化丁基橡胶,由BF 固特里奇公司继续销售其溴化丁基橡胶工业牌号大约有5 年时间。
1981 年,凭借21 年卤化弹性体生产经验,埃克森美孚化工公司宣布进入溴化丁基橡胶的生产领域。
1992年,埃克森美孚公司开始工业化生产溴化丁基橡胶牌号中的一个新产品系列,即EXXON™ 星形支化溴化丁基橡胶,设计用于改善胶料在工厂中的加工性能。
与传统溴化丁基橡胶不同,这些产品具有独特的分子量分布,含有部分高分子量星形支化的分子。
溴化丁基橡胶的工业化生产溴化丁基橡胶采用两步法生产。
首先是异丁烯和异戊二烯聚合生成丁基橡胶(IIR),之后再对丁基橡胶进行溴化,制成溴化丁基橡胶。
丁基橡胶(IIR)由高纯度的异丁烯和异戊二烯合成,聚合机理是复合阳离子聚合机理。
催化体系是一种路易斯酸共引发剂和一种引发剂。
典型的路易斯酸共引发剂有三氯化铝,二氯化烷基铝,三氟化硼,四氯化锡和四氯化钛。
布朗斯特酸,如水,盐酸、有机酸或烷基卤化物用作引发剂。
在引发阶段,异丁烯单体与路易斯酸催化剂反应生成带正电的碳阳离子,称为碳正离子。
图1 阳离子聚合引发步骤的简要说明H2 O + BF3H2 O——BF3CH3+ CH3+C = CH2H—O —BF3C—CH3+ H0BF3 CH3CH3H在链增长阶段,单体链节不断地加入分子链中,直到发生链转移或键终止反应为止(下图)。
温度、溶剂极性以及存在的负离子都会影响该放热反应的链增长过程。
CH3CH3CH3CH3C CH3 CH2 = C CH3——C——CH2——C 等CH3CH3CH3CH3在终止大分子链增长的链转移步骤中,聚合物链的碳正离子与异丁烯或异戊二烯单体反应,或与其他物质如溶剂或反离子反应,中断该大分子的增长,并形成新的增长聚合物链,降低聚合温度可以阻碍这种链转移反应,从而可获取更高分子量的的丁基聚合物。
异戊二烯主要是通过1,4 加成的方式进行共聚。
由于从共聚单体上夺取氢、形成稳定的烯丙基碳正离子或与亲核物质如醇或胺反应而产生不可逆破坏后就会使聚合终止。
确定终止点,从而可以控制丁基橡胶的分子量,为下一步的卤化提供非反应性聚合物。
在最广泛使用的丁基橡胶合成工艺中,在反应釜中加入路易斯酸引发剂后,细粒子丁基橡胶分散在氯甲烷中形成淤浆。
反应是高放热反应,通过控制聚合温度(一般为-100 ºC 到-90 °C)就可达到较高的分子量。
最常用的聚合工艺中采用氯甲烷作为反应稀释剂,由沸腾的液体乙烯除去反应热,保持所需的低温。
丁基橡胶的最终分子量主要通过控制引发反应和链转移反应的速度来控制。
对原料体系进行精制可以减少终止链增长过程的水和含氧有机化合物的含量。
氯甲烷和未反应的单体用蒸汽或热水冲洗出来,进行干燥和精制,之后再送回到反应釜中。
稳定剂(硬酯酸钙)和防老剂(BHT丁基化羟基甲苯)加入热水/聚合物淤浆中,以稳定聚合物,防止聚合物结块。
如果是生产卤化丁基橡胶,则在强搅拌条件下将溴加入反应器中。
这些离子卤化反应非常快。
1 摩尔的溴反应后会释放出 1 摩尔的氢溴酸,因此,反应溶液必须用碱溶液如氢氧化钠来中和。
之后用蒸汽和热水将溶剂吹洗分离出来。
也要加入硬脂酸钙来防止聚合物结块。
采用与普通(未卤化)丁基橡胶合成工艺中相同的方法,将获得的聚合物水淤浆过滤、干燥、冷却。
所得干燥产品为碎片状,之后对产品进行称量,并压制成标准34 Kg 胶包,再用EV A 包装膜进行发货包装。
低化学官能度埃克森美孚化工公司在1943年开始工业生产丁基橡胶,推出了化学反应性官能团含量低的高饱和、强惰性聚合物产品4。
但是,官能团的含量足以在硫化后生成具有高强度和高弹性的交联网络。
丁基橡胶的典型粘均分子量为35万–45 万,不饱和基团摩尔百分数(异戊二烯)为0.8% 到2.6%。
二、溴化丁基橡胶性能概述由于溴化丁基橡胶具有丁基橡胶基本饱和的聚异丁烯主链,所以拥有丁基橡胶的多种性能,如空气和湿气的渗透率低。
溴化丁基橡胶和氯化丁基橡胶采用多种硫化体系硫化后都具有类似的硫化胶性能,性能可能优于硫黄硫化的普通丁基橡胶胶料。
溴化丁基橡胶和氯化丁基橡胶之间的差别起因于碳-卤键离解能的不同。
碳-氯键的键能为327 J/mol,耐碳-溴键的键能为209J/mol。
由于溴化丁基橡胶中的碳-卤键键能较低,所以其反应活性要高于氯化丁基橡胶。
因此,溴化丁基橡胶的硫化速度较快,与通用橡胶的共硫化特性好。
另一方面,氯化丁基橡胶具有较长的焦烧时间,对加工条件不敏感。
溴化机理和工艺概述溴化丁基橡胶是采用在约50℃下将元素溴加入丁基橡胶的己烷溶液中的方法制备的。
通过异戊二烯链节上的离子取代反应完成溴化过程。
对溴的加入量进行控制,使弹性体中一个异戊二烯链节大约连接一个溴原子。
反应过程中生成的溴化氢由碱的水溶液中和。
还要加入硬脂酸钙,丁基化羟基甲苯(BHT)和环氧化大豆油(ESBO),以防止在聚合物后处理及贮存阶段发生脱卤化氢和氧化反应。
简言之,硬脂酸钙是一种中度碱,可以与过量的溴化氢(HBr)反应,从而起到了溴化丁基橡胶稳定剂的作用。
硬脂酸钙还会降低胶料的硫化速度,所以要严格控制硬脂酸钙在溴化丁基橡胶中的用量。
ESBO 可以中和橡胶中生成的各种游离酸,如硬脂酸。
在许多弹性体生产中使用的BHT 是一种防老剂,可以阻止降解反应,使聚合物达到规定的贮存寿命。
之后将材料在一系列脱水步骤中进行干燥,压成胶包,最后用塑料薄膜包装。
反应机理主要溴化反应机理是大家公认的溴离子反应机理,反应过程中双键移位,生成一个外亚甲基烯丙基溴化物(图5,结构2)。
之后会进行有限的烯丙位重排和双键的迁移。
图6 展示了所发现的溴化丁基橡胶中含溴官能团的结构9,10,11 。
三、溴化丁基橡胶的硫化用氧化锌交联溴化丁基橡胶时通过烷基化反应机理形成碳-碳键。
溴化丁基橡胶脱去卤化氢形成锌卤催化剂是这种交联机理的关键特点10。
在丁基橡胶类异戊二烯链节的溴化过程中,所形成的带有外亚甲基基团的烯丙基溴结构似乎是主要的反应结构。
存在氧化锌时,通过脱除溴形成烯丙基碳阳离子使该结构发生初步交联,如图3所示。
在未加稳定剂的条件下,溴化丁基橡胶的交联速度和脱卤速度都要比氯化丁基橡胶快许多倍。
加入稳定剂后,两种卤化丁基橡胶的速度常数之间的差别就显著减小了。
通过加入迟延剂,或采用更复杂的硫化体系可以进一步调节溴化丁基橡胶和氯化丁基橡胶表观硫化速度之间的差别。
硫化方法溴化丁基橡胶中含有烯丙位溴原子,使其可以采用多种硫化方法硫化。
以下总结了各种硫化剂对溴化丁基橡胶交联的影响。
氧化锌硫化氧化锌和少量的硬脂酸可以用作溴化丁基橡胶的硫化体系。
氧化锌硫化体系是一种简单的硫化体系,大多用于监控产品质量以及用于一些特殊场合,如要求可抽出材料量极低的药瓶塞。
采用氧化锌硫化溴化丁基橡胶时,要注意一些原则:1. 氧化锌硫化体系对酸性和碱性配合材料较为敏感。