免加热直接轧制技术共42页文档
轧制工艺

---------------------------------------------------------------最新资料推荐------------------------------------------------------轧制工艺Ⅹ第二章轧制生产工艺过程及其制定2.1 轧材产品标准和技术要求 2.2 金属与合金的加工特性 2.3 轧材生产各基本工序及对产品质量的影响下午9时23分1/ 32Ⅹ第二章轧制生产工艺过程及其制定轧制生产工艺过程由锭或坯轧制成符合技术要求的轧材的一系列加工工序的组合。
组织生产工艺过程,确定加工工序,首先要保证生产出的产品符合质量要求(或称技术要求),同时要尽量提高产量、降低消耗,这就是我们常说的“优质、高产、低消耗”,如何“优质、高产、低成本”的生产出符合技术要求的轧材,是制定工艺流程的总任务和总依据。
下午9时23分---------------------------------------------------------------最新资料推荐------------------------------------------------------ 第二章轧制生产工艺过程及其制定轧制生产工艺过程下午9时23分3/ 32Ⅹ2.1 轧材产品标准和技术要求一、轧材的技术要求为了满足使用上的要求,对轧材提出的必须具备的规格和技术性能,包括:形状、尺寸、表面状态、机械性能、物理化学性能,金属内部组织和化学成分等方面的要求。
轧材技术要求是由使用单位按用途的要求提出来的。
我们生产的钢材,都有用户使用。
用户根据使用的要求提出品种规格的要求(如:建筑桥梁需钢梁——工字钢,需要多大的规格),同时还提出其他要求:表面质量(裂纹、结疤、重皮,氧化铁皮),钢材机械性能(强度、塑性、韧性),工艺性能(弯曲、冲压、焊接等),物理化学性能(磁性、抗腐蚀性能等)。
下午9时23分---------------------------------------------------------------最新资料推荐------------------------------------------------------ Ⅹ2.1 轧材产品标准和技术要求二、产品标准钢材技术要求是由使用单位按用途的要求提出来的,使用单位很多,不可能一个用户提一个要求来进行生产,用户提出的要求要根据当时生产的技术水平和经济性来制定成产品的标准,然后钢厂按标准来生产。
第二篇轧制工艺基础

d.采用铸锭的小型生产系统的工艺过程:其 特点是通常在中、小型轧机上用冷的小钢 锭经一次加热轧制成材。 所有采用铸锭的生产工艺都是落后的,已 经或将要遭到淘汰。 不管是哪种类型,其基本工序都是:原料 准备(清理)-加热-轧制-冷却精整处理。
合金钢生产工艺流程
• 可分为冷锭和热锭以及正在发展的连铸坯三种作 业方式。 • 由于对合金钢材的表面质量和物理机械性能等技 术要求比普通碳素钢高,并且钢种特性也较复杂, 故其生产工艺过程一般也比较复杂。 • 除各工序的具体工艺规程会因钢种不同而不同以 外,在工序上比碳素钢多出了原料准备中的退火、 轧制后的热处理、酸洗等工序,以及在开坯中有 时还要采用锻造来代替轧钢等。
2.型钢生产系统:规模往往并不很大。 大型:年产100万t以上; 中型:年产30万-100万t; 小型:年产30万t以下。 3.混合生产系统: 在一个钢铁企业中可同时生产板 带钢、型钢或钢管时,称为混合系统。 • 无论在大型、中型或小型的企业中,混合系统都 比较多,其优点是可以满足多品种的需要。 • 但单一的生产系统却有利于产量和质量的提高。
钢材的冷加工生产工艺流程
• 钢材的冷加工生产工艺流程包括冷轧和冷 拔。 • 其特点是必须有加工前的酸洗和加工后的 退火相配合,以组成冷加工生产线。
有色金属(铜、铝等)及其合金轧 材生产系统及工艺流程
• 铜、铝及其合金的轧材应用比较广泛,其生产系 统规模却不大,一般是以重金属和轻金属分别自 成系统进行生产的,在产品品种上多是板带材、 型线材及管材等相混合,在加工方法上多是轧制、 挤压、拉拔等相混合,以适应于批量小,品种多 及灵活生产的特点和要求。 • 但也有专业化生产的工厂,例如电缆厂、铝箔厂、 板带材厂等。 • 有色金属及合金的轧材主要是板带材,至于型材、 管材乃至棒材则多用挤压及拉拔的方法生产。
带钢无头连铸连轧技术(ESP)简介

带钢无头连铸连轧技术(ESP)简介截止2013年底,我国共有70套热轧宽带钢机组己投产,产能达到2.29亿吨,由此产生的能耗巨大。
近年来,为了节能降耗,欧洲、日本和韩国等国家的钢铁企业在努力实现热轧板带减量化制造技术方面进行了大量的研究开发工作并取得显著效果。
其中,开发和发展热轧板带无头轧制技术,进一步提高板带成材率、尺寸形状精度与薄规格超薄规格比例、实现部分〃以热代冷〃、降低辐耗等方面取得显著成绩。
该项技术是钢铁生产技术的又一次飞跃, 代表了当今世界热轧带钢的前沿技术。
1997年浦项和日立联合着手开始研制采用剪切、焊接工艺,进行中间坯连接的带钢无头轧制新工艺。
1998年4月,日本新日铁大分厂研制成功了利用高能激光器对中间板坯实现对焊的钢板无头轧制生产线。
2006-2007年浦项和日立采用剪切、焊接工艺进行中间坯连接的带钢无头轧制新工艺投入工业化生产,这种基于摆剪概念的新型固态连接工艺,实现了无头轧制连接技术的创新。
2009年意大利钢铁企业阿维迪与西门子公司联手打造的世界第一套ESP无头铸轧带钢生产线投产,当年产量达到45万吨。
本文以阿维迪ESP线为例,简要介绍带钢无头连铸连轧的工艺特点及技术优势。
一、ESP工艺流程及主要特点(一)ESP工艺流程介绍阿维迪ESP生产线如图1所示,该项技术是在德马克公司的ISP技术基础上开发的,其生产线中的连铸机采用平行板式直—弧形结晶器,铸坯导向采用铸轧结构,经液芯压下铸坯直接进入初轧机轧制成中厚板,而后经剪切可下线出售,不下线的板坯经感应加热后, 进入五架精轧机轧制成薄带钢,经冷却后卷曲成带卷。
ESP工艺生产线布置紧凑,不使用长的加热炉或克雷莫纳炉,生产线全长仅190m,是世界上最短的连铸连轧生产线。
ii tt UH 电tt BMr MH 泳冷"口谅、勇矗*图1.意大利阿维迪ESP生产线示意图(二)ESP工艺的主要技术特点1 .较高的浇铸速度。
轧钢新技术

轧钢新技术轧钢新技术近年来,轧钢生产中所涌现的新技术、新工艺主要是围绕节约能源、降低成本、提高产品质量、开发新产品所进行的。
在节能降耗上,主要技术是:连铸坯热送热装技术、薄板坯连铸连轧技术、先进的节能加热炉等;在提高产品性能、质量上,主要技术是:TMCP 技术、高精度轧制技术、先进的板形、板厚控制技术、计算机生产管理技术等;在技术装备上,主要是大型化、连续化、自动化,即热轧带钢、冷轧带钢的连续化,实现无头轧制、酸轧联合机组、连续退火及板带涂层技术等。
这些技术的应用可极大地提高产品的竞争能力。
以节能降耗为目标的新技术1 连铸坯热送热装技术连铸坯热送热装技术是指在400℃以上温度装炉或先放入保温装置,协调连铸与轧钢生产节奏,然后待机装入加热炉。
在轧钢采用的新技术中热送热装效益明显,主要表现在:大幅度降低加热炉燃耗,减少烧损量,提高成材率,缩短产品生产周期等。
我国20 世纪80 年代后期开始首先在武钢进行热送热装试验,90 年代宝钢、鞍钢等在板带轧制中试验,并逐步采用了热送热装技术。
90 年代中期以后我国棒线材大量采用了热送热装技术,但是距日本和一些欧美国家的水平还有较大的差距。
连铸坯热送热装技术的实现还需要以下几个条件:(1)质量合格的连铸板坯;(2)工序间的协调稳定;(3)相关技术设备要求,如采用雾化冷却、在平面布置上尽可能缩短连铸到热轧之间的距离、通过在输送辊道上加设保温罩及在板坯库中设保温坑等;(4)采用计算机管理系统。
根据国内目前的实际情况分析,需要继续推广该技术,己经采用的轧机应当在提高水平上下功夫。
通过加强管理保证该技术的连续使用,不断提高热装率和提高热装温度,同时进行必要的攻关,解决由于采用热装技术以后,产生的产品质量不稳定问题。
2 薄板坯连铸连轧技术薄板坯连铸连轧是20 世纪80 年代末实现产业化的新技术,是钢铁生产近年来最重要的技术进步之一。
采用薄板坯连铸连轧工艺与传统钢材生产技术相比,从原料至产品的吨钢投资下降19%~34%,厂房面积为常规流程的24%。
棒线材MI.DA.无头轧制技术介绍

棒线材MI.DA.无头轧制技术介绍赵辉1,2①(1:北京首钢国际工程技术有限公司 北京100043;2:北京市冶金三维仿真设计工程技术研究中心 北京100043)摘 要 本文主要介绍MI.DA.无头轧制技术以及国内应用现状。
以山西建邦MI.DA.生产线为例,详细介绍了MI.DA.无头轧制的生产工艺和装备,总结了MI.DA.无头轧制技术的优缺点,为今后国内新建类似项目给出建议。
关键词 无头轧制 棒材 线材 MI.DA.中图法分类号 TG333 TG335.1 文献标识码 BDoi:10 3969/j issn 1001-1269 2023 06 025IntroductiontoMI.DA.HeadlessRollingTechnologyofBarandWireZhaoHui1,2(1:BeijingShougangInternationalEngineeringTechnologyCo.,Ltd.,Beijing100043;2:MetallurgicalEngineering3-DSimulationDesignEngineeringTechnologyResearchCenterofBeijing,Beijing100043)ABSTRACT MI.DA.headlessrollingtechnologyanditsdomesticapplicationstatusareintroduced.TakingShanxiJianbangMI.DAproductionlineasanexample,theproductionprocessandequipmentofMI.DAheadlessrollingareintroducedindetail,theadvantagesanddisdvantagesofMI.DAheadlessrollingtechnologyaresummarized,andsuggestionsaregivenfornewsimilarprojectsinChinainthefuture.KEYWORDS Headlessrolling Rod Wire MI.DA.1 前言节能降本一直是我国钢铁企业追求的目标,如何在保证产量的同时,降低生产成本,无头轧制工艺是一个很好的选择。
棒材直接轧制

棒材直接轧制摘要:1.棒材直接轧制的定义和特点2.棒材直接轧制的工艺流程3.棒材直接轧制的应用领域4.棒材直接轧制的优势和局限性正文:棒材直接轧制是一种将金属材料通过轧制设备直接加工成棒材的工艺方法。
这种工艺具有高效、节能、成本低等优点,广泛应用于金属加工领域。
下面将从棒材直接轧制的定义和特点、工艺流程、应用领域以及优势和局限性四个方面进行详细介绍。
一、棒材直接轧制的定义和特点棒材直接轧制是指将金属材料在轧制设备上直接轧制成棒材的加工方法。
这种工艺具有以下特点:1.高效:棒材直接轧制过程连续进行,生产效率高。
2.节能:与其他金属加工工艺相比,棒材直接轧制能耗较低。
3.成本低:棒材直接轧制工艺简化了生产流程,降低了生产成本。
二、棒材直接轧制的工艺流程棒材直接轧制的工艺流程主要包括以下几个步骤:1.准备:将待加工的金属材料进行预热处理,以保证其具有良好的塑性。
2.轧制:将预热后的金属材料送入轧制设备进行连续轧制,使其形状和尺寸发生变化。
3.冷却:轧制后的棒材进行冷却处理,以提高其力学性能。
4.成品:经过冷却处理后的棒材即为成品,可根据需求进行后续加工。
三、棒材直接轧制的应用领域棒材直接轧制广泛应用于以下领域:1.钢铁行业:生产各种规格和形状的钢材,如螺纹钢、圆钢等。
2.有色金属加工:生产铜、铝等有色金属的棒材。
3.矿山、冶金、建筑等领域:用于制作矿山支护材料、建筑钢筋等。
四、棒材直接轧制的优势和局限性棒材直接轧制的优势主要体现在高效、节能、成本低等方面。
但是,这种工艺也存在一定的局限性,如生产出的棒材尺寸和形状精度相对较低,对于高精度要求的产品可能不适用。
因此,在选择棒材直接轧制工艺时,需要综合考虑生产需求和工艺特点。
总之,棒材直接轧制作为一种高效、节能的金属加工工艺,在多个领域得到了广泛应用。
轧制工艺

Ⅹ
2.3 轧材生产各基本工序及其对产品质量的影响
水冷对钢材有要求:对碳素钢,开坯(半成品对性能 不要求)可水冷,某些合金、高合金钢易产生应力和 裂纹不宜水冷。水冷还可清除表面氧化铁皮,提高冷 床生产能力。 钢材放在冷床上,靠辐射和对流冷却,凡是在空气 (2)空冷:
中冷却,不产生热应力裂纹的钢种,都可以空冷, 而且可通过吹风、钢材疏密排列来调整冷却速度。
下午9时23分
Ⅹ
2.3 轧材生产各基本工序及其对产品质量的影响 1.原料的选择及准备
在轧钢生产中,一般常用的原料为钢锭、轧坯 和连铸坯,也有采用压铸坯的。 以上几种原料的优缺点及适用情况见表8—2 P109 要求能够掌握
连铸坯的优点很多,是发展方向,但是还不能完全 说明:
取代铸锭,一个重要的原因就是初轧开坯生产钢锭 的尺寸规格可以灵活, 如:鞍钢有初轧,又生产板坯,又生产方坯(同 时生产),而用连铸则办不到,同时连铸坯受钢 种限制。
下午9时23分
Ⅹ
2.3 轧材生产各基本工序及其对产品质量的影响
若低于Ar3线,在(γ +α )区进行了一定的塑性变形, 将导致加工硬化,塑性降低,变形抗力提高。 (因为在同样温度下,α 易变形,γ 不易变形,导致不同 相变形不均匀,从而引起附加应力;另一方面,在α 基体 上出现γ ,可将γ 看作硬的夹杂物,它将强烈阻止位错的 移动,而在该处形成位错堆积,引起应力集中,在一定条 件下形成断裂。若在γ 基体上出现α ,这将使强固的机体 削弱,同样也引起应力集中易使金属过早断裂。)
下午9时23分
Ⅹ
2.3 轧材生产各基本工序及其对产品质量的影响 2.原料的加热
加热目的:1)提高塑性和降低变形抗力。 2 )改善金属内部组织性能, 如偏析经加热可 减轻或消除。为达到上述目的,加热温度尽量 高一些,但是过高或加热方法不对,都会造成 加热缺陷,影响钢材质量,甚至造成废品。
轧制工艺2
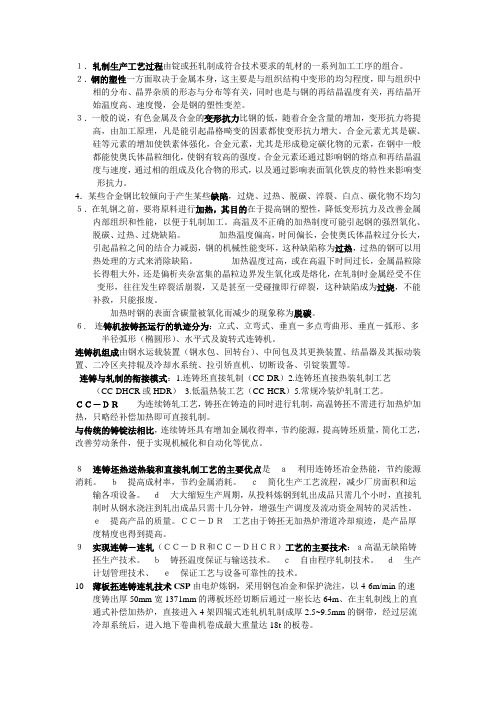
1.轧制生产工艺过程由锭或抷轧制成符合技术要求的轧材的一系列加工工序的组合。
2.钢的塑性一方面取决于金属本身,这主要是与组织结构中变形的均匀程度,即与组织中相的分布、晶界杂质的形态与分布等有关,同时也是与钢的再结晶温度有关,再结晶开始温度高、速度慢,会是钢的塑性变差。
3.一般的说,有色金属及合金的变形抗力比钢的低,随着合金含量的增加,变形抗力将提高,由加工原理,凡是能引起晶格畸变的因素都使变形抗力增大。
合金元素尤其是碳、硅等元素的增加使铁素体强化,合金元素,尤其是形成稳定碳化物的元素,在钢中一般都能使奥氏体晶粒细化,使钢有较高的强度。
合金元素还通过影响钢的熔点和再结晶温度与速度,通过相的组成及化合物的形式,以及通过影响表面氧化铁皮的特性来影响变形抗力。
4.某些合金钢比较倾向于产生某些缺陷,过烧、过热、脱碳、淬裂、白点、碳化物不均匀5.在轧钢之前,要将原料进行加热,其目的在于提高钢的塑性,降低变形抗力及改善金属内部组织和性能,以便于轧制加工。
高温及不正确的加热制度可能引起钢的强烈氧化、脱碳、过热、过烧缺陷。
加热温度偏高,时间偏长,会使奥氏体晶粒过分长大,引起晶粒之间的结合力减弱,钢的机械性能变坏,这种缺陷称为过热,过热的钢可以用热处理的方式来消除缺陷。
加热温度过高,或在高温下时间过长,金属晶粒除长得粗大外,还是偏析夹杂富集的晶粒边界发生氧化或是熔化,在轧制时金属经受不住变形,往往发生碎裂活崩裂,又是甚至一受碰撞即行碎裂,这种缺陷成为过烧,不能补救,只能报废。
加热时钢的表面含碳量被氧化而减少的现象称为脱碳。
6.连铸机按铸抷运行的轨迹分为:立式、立弯式、垂直-多点弯曲形、垂直-弧形、多半径弧形(椭圆形)、水平式及旋转式连铸机。
连铸机组成由钢水运载装置(钢水包、回转台)、中间包及其更换装置、结晶器及其振动装置、二冷区夹持辊及冷却水系统、拉引矫直机、切断设备、引锭装置等。
连铸与轧制的衔接模式:1.连铸坯直接轧制(CC-DR)2.连铸坯直接热装轧制工艺(CC-DHCR或HDR)3.低温热装工艺(CC-HCR)5.常规冷装炉轧制工艺。
- 1、下载文档前请自行甄别文档内容的完整性,平台不提供额外的编辑、内容补充、找答案等附加服务。
- 2、"仅部分预览"的文档,不可在线预览部分如存在完整性等问题,可反馈申请退款(可完整预览的文档不适用该条件!)。
- 3、如文档侵犯您的权益,请联系客服反馈,我们会尽快为您处理(人工客服工作时间:9:00-18:30)。
4、配套技术——1缩短送坯时间
缩短钢坯运送时间的具体做法: • 钢坯切断后,所有涉及钢坯运行的部位提速。 ➢ 切断后辊道提速,移钢机提速,运输辊道提速。 • 减少环节。 ➢ 能直行的就不用横移装置。 ➢ 能用爬坡辊道的不用提坯机 • 减少钢坯启停次数。
。 ➢ 加保保温罩。
• 连铸坯温度的反馈控制,包括凝固终点预报,避免漏钢( ★★★)。
• 钢坯流程(车间平面图)改造:绕过加热炉快速移送。
• 粗轧机配套改造:验算电机能力,优化负荷分配 (★★)。
4、配套技术——1缩短送坯时间
在免加热工艺中缩短从钢坯切断到进轧机的时间至关重要: • 时间就是温度。 • 时间就是直轧率。 • 时间就是效益。
• 钢坯仍需切断,没有无头轧制的优点。 • 无头轧制的DROF技术,已申报专利,将在下步
推出。
4、免加热轧制技术的配套技术
五项配套技术(不一定全部采用): • 缩短钢坯运送时间(★★★★★)。 • 提高钢坯温度(★★★★)。 ➢ 有条件地提高拉速。 ➢ 二冷配水优化:控制钢坯的温度分布,减少温降(★★)
4、配套技术——2提高铸坯温度
4、配套技术——2提高铸坯温度
措施2:二冷区配水参数优化 调整二冷水的压力、流量、分布。 在保证不发生漏钢事故前提下 减少热量散失 提高坯料平均温度 确定凝固终点 优化切断位置(必要并可能时) 对二冷区的温度场进行模拟计算
4、配套技术——2提高铸坯温度
面温度上升。
3、免加热轧制的基本特征
DROF特别适合对现有生产线进行改造,改造的目标 :
• 提高铸坯温度,改善温度分布。 • 缩短送坯时间,减少温降。 • 完全不用加热炉,也完全不用补热装置(特色)。
3、免加热轧制的基本特征
DROF与现有意大利推出的直接轧制技术相比有以 下优点:
• 不需要补热,更加节能。 • 无隧道炉,不需要特殊保温装置。 • 生产线短,设备改造投资少。 • 简单易行,方便对现有生产线进行改造。 缺点
义。 • 通过采用DROF新技术可为企业降低成本,增加效益。
1、技术背景和发展趋势
现有棒线材生产工艺存在的问题: • 能量陷阱(高温坯料冷却下来再加热,带来能量损失) • 热装热送(HCDR)有所改进,仍需加热。 • 加热过程的经济账 1. 燃料消耗(煤、油、气) 2. 氧化损失(~1.0%成材率) 3. 冷却水损失(节省二冷水)。 4. 时间消耗(效率)。 5. 加热炉操作、材料消耗。 6. 总图布置(投资)
棒线材免加热直接轧制技术
Direct Rolling of Free-heating for Bar and Rod Mill
DROF向边际利润要效益的新技术
内容提要
• 技术背景和发展趋势 • 国内外发展状况 • 免加热轧制技术的配套技术 • 经济效益和社会效益 • 结束语
1、技术背景和发展趋势
2、国内外发展状况
• 早期(1980‘~1990’)日本开展了关于直接轧制(CC-DR)大量研究 • 日本、意大利曾经开发出棒线材无头轧制技术,没有大范围推广 • 近期意大利推出捧线材直接轧制生产线流程,特征:隧道炉保温补热
2、国内外发展状况
国内在棒线材节能减排方面做过很多努力,示能取得重大突破性进展 • 一些厂家尝试低温轧制(开轧温度~700℃),有报道,应用面不广。 • 推广蓄热式加热炉取得一定的节能效果,属于局部改进。 • 唐钢、新疆八一曾经引进棒线材无头轧制技术(焊接),问题较多 。 • 棒线材行业进入门槛低,微得生产,竞争激烈。 • 需要在工艺流程上进行重大创新,适应发展要求。 • 东北大学近来对轧钢生产流程创新做了大量的前期研究。
4、配套技术——2提高铸坯温度
提高连铸坯温度的三个措施: ➢ 提高拉速(POSCO薄板坯拉速已达7m/s)。? ➢ 减少冷却水。 ➢ 加保温罩。 前提: ➢ 不能出现漏钢事故。 ➢ 与炼钢产能匹配。 ➢ 与轧钢产能匹配。 技术支撑: ➢ 对凝固过程的数值模拟。
4、配套技术——2提高铸坯温度
措施1:改进结晶器设计(加长、减少水、优化圆角) 优化凝固过程,控制坯壳厚度,避免漏钢。 凝固初期的温度分布的数值模拟计算
国家“十二五规划”提出节能减排目标: • 单位GDP能耗下降16% • 二氧化碳排放降低17% • 主要污染物排放总量减少8~10% 钢铁待业是耗能和排放的大户,节能减排压力巨大 • 现有棒线材生产工艺不做重大变化,节能空间十分有限 • 免加热轧制技术取消现有工艺的加热环节是一项重大革新
,节能减羊效果明显。 • 在产能过剩、市场低迷,竞争激烈的形势下,具有重要意
免加热直接轧制技术
1、纪律是管理关系的形式。——阿法 纳西耶 夫 2、改革如果不讲纪律,就难以成功。
3、道德行为训练,不是通过语言影响 ,而是 让儿童 练习良 好道德 行为, 克服懒 惰、轻 率、不 守纪律 、颓废 等不良 行为。 4、学校没有纪律便如磨房里没有水。 ——夸 美纽斯
5、教导儿童服从真理、服从集体,养 成儿童 自觉的 纪律性 ,这是 儿童道 德教育 最重要 的部分 。—— 陈鹤琴
3、免加热轧制的基本特征
免加热轧制技术的核心是:坯料不经加热炉直接轧制,基本 特征如下:
• 开轧温度在常规轧制和低温轧制之间,终轧温度与常规轧 制相差不大。
• 提高铸坯温度,缩短连铸到轧制的时间,保证较好的开轧 温度。
3、免加热轧制的基本特征
3、免加热轧制的基本特征
表面与中心温差大:
• 钢坯未经加热,表面温度比常规轧制开轧温度低。 • 但是钢坯中心温度比表面温度高得多,有利于变形深透。 • 有利于内部缺陷压合,改进内部质量。 • 粗轧阶段内部高温区温度向外扩散、产生均温作用,使表
二冷区凝固壳厚度变化与切断处温度分布的数值模拟结果
4、配套技术——2提高铸坯温度
措施3:加保温罩减少铸坯的温降,可加保温罩的部位:
✓切断后辊道(留出处理事故空间) 按拉速运行,
✓拉坯机到切割机之间
时间长, 保温效果
✓快速送坯辊道
明显。
4、配套技术——2提高铸坯温度
加保温罩的效果:
平均温度影响