无碳小车工艺成本分析
无碳小车设计方案

无碳小车设计方案1. 简介随着全球环境问题的日益突出,低碳生活开始受到越来越多人的关注。
在交通方面,传统的燃油车辆不仅排放大量有害气体,还对环境造成噪音污染。
因此,设计一款无碳小车成为当下的热门话题。
本文将介绍一种基于电动技术的无碳小车设计方案。
2. 背景传统的燃油车辆使用化石燃料,通过燃烧产生动力驱动车辆运行。
这种方式不仅会产生大量的二氧化碳等有害气体,还会产生噪音和震动。
为了解决这一问题,研发出了电动车辆,其使用电池和电动机来提供动力。
电动车辆不仅零排放,而且噪音较低,对环境更加友好。
3. 设计方案3.1. 动力系统无碳小车的动力系统采用纯电动方式,即使用电池作为能量储存装置,通过电动机驱动车辆运行。
电池可以通过充电桩进行充电,也可以通过车辆制动时的回馈能量进行再生充电,提高能源利用率。
3.2. 车体结构无碳小车的车体结构应该尽可能轻量化,采用高强度材料,如碳纤维复合材料。
轻量化可以降低车辆自身质量,提高续航里程。
此外,还要设计合理的车身外形,减小风阻,提高车辆的行驶效率。
3.3. 能量回收系统能量回收系统是无碳小车的重要组成部分,通过回收制动过程中产生的能量,将其转化为电能储存到电池中。
这样可以延长电池的使用时间,提高能源利用效率。
3.4. 智能控制系统无碳小车应配备智能控制系统,可以监测和控制车辆的各种参数,如电池电量、续航里程、车速等。
智能控制系统还可以通过导航功能优化行车路线,减少能源消耗。
4. 优势与挑战4.1. 优势•零排放:无碳小车采用纯电动方式,不产生尾气和有害气体,对环境友好。
•低噪音:电动车辆噪音较低,减少噪音污染。
•高效能源利用:通过能量回收系统回收能量,提高能源利用效率。
4.2. 挑战•续航里程:电池容量和续航里程是无碳小车的一大挑战,需要不断改进电池技术和能量回收系统。
•充电设施建设:无碳小车需要充电设施进行充电,充电设施的覆盖率和充电速度是一个问题。
•成本问题:无碳小车的制造成本较高,需要进一步降低制造成本,以提高竞争力。
无碳小车项目研究报告

无碳小车项目研究报告无碳小车项目研究报告一、引言随着全球气候变暖和环境污染问题日益严重,减少碳排放已成为人们关注的重要议题。
为了应对这一问题,我们团队立足于研究与开发无碳小车项目,旨在推出一款使用清洁能源驱动的小型交通工具,以减少对环境的影响。
二、项目概述无碳小车项目的主要目标是设计和开发一种无碳排放、零污染的小型电动汽车。
该小车将采用电池作为能源来源,并具备高效、环保的特点。
三、市场需求目前,电动汽车正逐渐成为人们关注的热点,其市场需求不断增长。
环保意识的觉醒和对碳排放的关注,使得越来越多的人开始选择电动汽车作为替代传统燃油汽车的新选择。
因此,无碳小车项目具有巨大的市场潜力。
四、技术方案项目将采用先进的电池技术作为主要能源,并配备高效的电动机。
同时,我们将研发智能充电系统,以提高充电效率。
此外,还将引入轻量化设计,以减少车辆质量,提升能源利用效率。
五、项目成本估计根据初步估算,无碳小车项目的研发和生产成本约为XX万元。
其中,研发费用占比约为XX%,生产费用占比约为XX%。
六、市场竞争分析目前市场上已经存在一些电动汽车品牌,例如特斯拉、日产等。
这些品牌推出的产品性能先进,具有较高的可靠性和安全性。
因此,我们团队在设计无碳小车时需注重技术创新和产品差异化,以在市场竞争中占据优势地位。
七、项目实施计划无碳小车项目预计分为以下几个阶段实施:需求分析和市场调研、技术研发和设计、生产和测试、市场推广和销售。
我们团队将严格按照计划进行项目实施,并确保项目按时完成。
八、项目风险控制在项目实施过程中,我们需要考虑到一些潜在的风险因素。
例如,技术研发可能会面临一些技术难题和挑战;市场竞争可能对产品销售造成一定的压力。
为了降低项目风险,我们将配备专业的团队,加强技术研发和市场调研,以及更好地了解消费者的需求。
九、项目效益预测该项目成功实施后,无碳小车将成为市场上的新宠,具有广阔的市场前景。
预计可以大幅减少车辆碳排放量,降低空气污染程度,提高交通效率。
无碳小车制作方案

无碳小车制作方案摘要第四届全国大学生工程训练综合能力竞赛的命名主题是“无碳小车”。
设计过程特别注重设计方法,对制作过程的材料选择,加工难度和成本也有更高要求。
我们综合运用参数化设计,数控加工等先进设计加工方法,采用SOLIDWORKS,CREO等软件配合制作。
我们把小车的制作分为材料选择,制作加工和装配三个过程。
将每个过程独立分析又联合考虑,通过学习提升加工人员综合素质、充分利用已有资源,层层把关,降低加工难度,加工误差,缩短时间和减少制作成本,一步步向最优的制作方案靠近。
根据制作方法,我们将零件分为标准件和非标准件两种。
为了制作过程更加容易完成,设计过程尽量使用标准件,然后购买。
非标准件将由参赛者加工完成。
关键字:参数化设计数控加工标准件非标准件一、材料选择1.1小车零件标准件:M4×12盘头螺钉和配套螺母、M8螺母、H8×M5*36+10隔离螺柱6个、1M-20齿齿轮1个、1M-80齿齿轮1个、M8立式KP08轴承座5个、卧式轴承座1个、导向轮、顶滑轮非标准件:底板、后轮2个、后轮轴1个、大齿轮轴1个、转片1个、转片轴、连架杆2个、微调螺杆1个、前摇杆1个、车顶1个、载重物板、撑杆3个、连杆1个1.2现有设备立式升降台铣床、立式数控加工中心、数控车床、数控铣钻床、万能外圆磨床、数控铣床、台虎钳、锯、刻度尺1.3非标准件材料选择市场上常用的机械材料有铸铝合金、铝合金、碳钢、铸铁、有机玻璃、合金钢等等。
从材料的成本和加工程度考虑,就数铝合金和亚克力板(有机玻璃)最好。
铝合金密度低,但强度比较高,接近或超过优质钢,塑性好,具有优良的导电性,导热性和抗腐蚀性。
亚克力板具有较好的透明性,化学稳定性,力学性能和耐候性,易加工,外观优美,价格低廉等特点。
通过上述分析,理应选择亚克力板,但是机电实验中心现有设备限制,在事件加工过程中,亚克力板的加工容易裂,无法满足要求。
综上所述,非标准件的材料统一采用铝合金。
无碳小车的原理与计算

无碳小车的原理与计算原理介绍一.连动原理:我们使用了凸轮转向机构来实现转向轮的转向功能。
具体方法如下:在齿轮的外侧表面上制作凸圆形的内槽道,滚子置于槽道内。
滚子与连杆以转动副相连,连杆与转向把以转动副连接,这样,当齿轮转动时,凸圆槽道在转动过程中就会推动连杆做进给运动,实现转向把转动可控制转向轮的方向。
我们将凸轮设计成内凹槽轨道凸轮机构,而外形设计成齿轮,这样的设计有以下优点:1.凸轮起到了齿轮和凸轮的双重作用,一轮两用有利于我们的加工,节约成本和加工时间减少重量。
2.使用内凹槽轨道与滚子连接可以使装置的稳定性增强,不会产生脱扣滑扣得困扰。
二.驱动原理:绳拉力为动力。
将物块下落的势能尽可能多的转换为小车的动能,进而克服阻力做功。
物块在下落的过程中不可避免的要与小车发生碰撞,碰撞过程必然要有能量损失。
要解决的问题:1下降过程中,尽可能的降低下落的速度;2在小车运动中,会受到转弯时的向心力做离心运动,从而不稳定,会导致轨道变形。
解决方案:1.把绕线轮设计成锥形,在开始运动时绕线轮的半径较大,使得开始有足够的驱动力使小车驱动。
在驱动之后,绕线轮的半径较小,使小车能在运动中持续稳定。
2.在重物周围加三根垂直细杆,固定重物的下落轨迹,保持小车的稳定。
无碳小车计算一.受力计算:小车质量P0,小车驱动力矩M,物块质量m, D轮子直径,Φ拉力轴直径M=F0×D/ 2M由G获取M= G×Φ/ 2= F0×D/ 2此时F0= G×Φ/D二.摩擦计算:S为小车行走距离,mm,η为小车总效率,F0为小车牵引力,F0×S =G×400mm×ηS =G×400mm×η/ F0前面防滑计算得出:F0<F = M(小车)g×f为了增大小车行走距离,为了避免能量损失不打滑,在保证能够驱动小车行走的前提下,F0 越小越好。
具体数据的计算:在确定驱动轮半径长度时,通过8字曲线的长度来确定,在定量凸轮制成后由实验准确数据测得8字曲线长度,换算得来。
工艺成本分析卡片

第二届江苏省大学生工程训练综合能施赛暨全国选拔赛
工艺成本分析卡片
总3页
第1页
编号:803
产品名称
无碳小车
生产纲领
500件/年
零件名称
无碳小车
生产批量
42件/月
1、材料成本分析
编号
材料
毛坯种类
毛坯尺寸
件/毛坯
件/台
备注
编号
材料
毛坯种类
毛坯尺寸
件/毛坯
件/台
备注
1
钼合金
板材
200×180×3
数铣费用:22×(12+16)/60=6.6元
钳工费用:24× (9+1) /60=4元
合计:6.6+4=10.6元
2
插齿
a. 车削
b. 插齿
c. 钳工
5min
10min
2min
3min
4min
2min
8min
14min
4min
车削费用:8×(8+4)/60=1.6元
插齿费用:14×(8+10)/60=4.2元
3)外协加工费用:前轮支座铸件5元/件,前轮支撑铸件4.5元/件,热处理费用500元/500件。合计:5 +4.5+ 500/500 =10.5元/件。
4)外购费用:考虑到中批量生产,为使效能最大化,部分零件和标准件直接外购。具体到每一部小车,轴承支座45元/9个,轴承共11元/11个,螺钉等0.6元/40个,外购合计56.8元/件。
序号
工序
名称
工序内容
工时
工序成本分析
机动时间
辅助时间
终准时间
无碳小车设计说明书
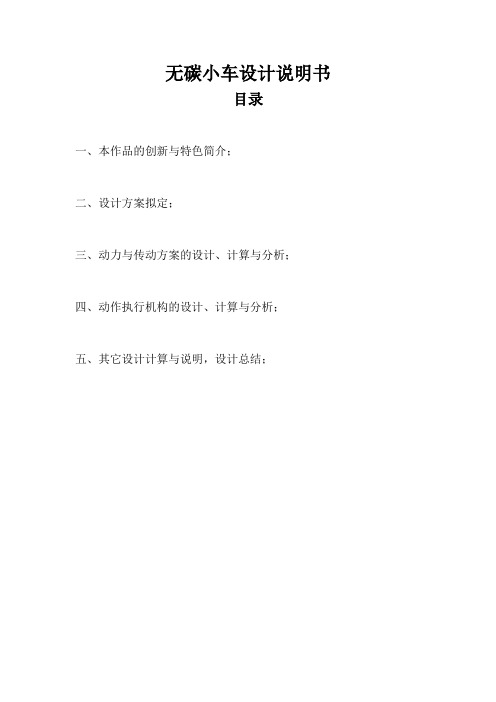
无碳小车设计说明书目录一、本作品的创新与特色简介;二、设计方案拟定;三、动力与传动方案的设计、计算与分析;四、动作执行机构的设计、计算与分析;五、其它设计计算与说明,设计总结;一:本作品的创新与特色简介;①所有的动力来自载荷重物,所纯机械结构,无碳排放;②在转向方面,采用内凸轮连杆机构,使得转向的角度、时间更加精确,并辅助以有图的可调机构,是转向调节更加明确。
③在重物下落阶段,增加了一动滑轮,使得做功行程加长,并合理的利用了扭矩。
④绕桩曲线部分的轨迹无需精确的计算出,由上图的机构可在完成后对中间连杆进行调试,已达到目标要求。
二:设计方案拟定;小车的方案设计关键在于传动部分与转向部分。
①传动部分;传动部分的问题在于是用什么进行传动,齿轮、带轮、直接驱动等。
最后结合传动的效率、制作的难易程度,最终确定了采用二级齿轮进行传动,如有图所示。
此方案的优点在于,以中间轴为主动轴,以小于1的传动比带动后轮,再以大于1的传动比带动凸轮轴,这样就很好的解决了行驶路程与转向周期间的关系,并且将传动比控制在合理数值内。
另外,以一个动滑轮来增加做功行程,减小瞬时扭矩,使小车前进平缓。
缺点在于,采用了二级齿轮组,使得摩擦耗能增加,机械效率降低。
②转向部分;转向部分在于采用什么机构,最大的争议在于是采用内凸轮还是外凸轮。
最终确定是采用内凸轮连杆机构。
原因在于采用外凸轮的话需要在连杆的回程部分提供一个力——增加一个弹簧;如果这样的话,可能会因为的弹簧的弹性系数,及位置的放置问题上增加设计的难度。
而采用内凸轮的话就不存在这些问题,不过增加了整体的重量,但这可以通过将凸轮在合理的条件下将其镂空来解决。
为了使后期调整时有更大的可能性,因此在连杆部分采用了右图的结果,如此便可以使小车的转向更加的准确。
③材料方面;除了前后轮采用有机玻璃之外,其余的材料都采用铝材。
底板:厚3mm的铝板,300*160*3.后轮:直径160的有机玻璃,厚5mm。
无碳小车设计说明书
无碳小车设计说明书为响应“低碳生活”的号召,我们应该节能减排,以优化环境。
作为学生,我们更应践行。
我们通过学习和实践,以及运用机械制造的原理,物理学等等方面的知识,设计了s型的无碳小车。
我们对它进行了严密的构思与计算,并结合实际进行了材料与运动的分析。
设计思路1.根据能量守恒定律,物体下落的重力势能直接转化为小车前进的动力,此时能量损失少,所以小车前进的能量来源于重物下落过程中减少的重力势能。
2.根据小车功能设计的要求,即小车在前行时能够自动绕开赛场上的障碍物,小车运动的路线需有一定的周期性。
考虑到小车在转向时会受到摩擦等阻力的影响,让小车行走最远路程是设计要求的最优解。
3.需要进行结构的设计与成本的分析,同时也需考虑加工工艺的繁琐程度,力求产品的最优设计。
小车的原理分析及构架设计1.小车的质量要适中,以此来保证车的稳定性。
质量若太大,则会增加阻力。
2.应采取齿轮传动和连杆机构,同步带的精度不高,也可避免传动效率的低下。
3.传动的力与力矩要适中,保证加速度的适中。
4.相对运动的精度要保证,以减少摩擦,保证力量的充分利用。
5.S型的路线转弯半径要适中,保证其行程。
6.选择大小适中的轮子,轮子太大,稳步性降低。
7.采用轴承,螺纹连接,用三根圆柱支撑,以此挂系重物,转向时则采用连杆机构。
小车的转向机构转向轮及转向机构如图所示。
转向采用连杆机构传动,转向轮固定在支架上。
当齿轮转动时,带动连杆运动,根据惯性,使转动轮运动方向发生改变。
小车的驱动原理重物的牵引带动栓线轴的转动,以此带动齿轮的转动,通过齿轮的啮合带动驱动轴与齿轮的转动,使驱动轮转动,带动着小车的前进;同时也带动着摇杆的转动,使推杆左右动的同时,前后运动。
在推杆与摇杆之间,有套筒相连,保证其作圆周运动。
杆偏转,使转动轮偏转,根据驱动轮与转动轮的合运动,小车就可以走S型。
栓线处为梯形原动轮。
起始时,原动轮的转动半径较大,起动转矩大,有利起动。
其次,起动后,原动轮的半径变小,转速提高,转矩变小,和阻力平衡后作匀速运动。
无碳越障小车设计说明1(1)
设计思想:
看到此次竞赛主题,我们认为,能否很好地解决小车的驱动问题 和自动转向问题是设计成功不否的关键。围绕这个中心,我们展开了 一系列理论分析不验证。最终确定了我们的设计思想:重力驱动不仿 自行车式转向。
驱动方面:驱动其行走的能量是根据能量转换原理,由给定重力 势能转换来的。绳子的拉力作为动力,将物体下落的势能尽可能的转 化为小车的动能,迚而克服阻力做功,尽可能使小车匀速运动。 转向方面:主要仿照自行车转向的方案,利用曲柄摇杆机构控制 小车的自动转向。
利用转向轮中心轴偏转,实现小车转向。本方案设 计中小车动力转变通过改变绳子绕在绳轮上丌同位置来改 变其输出,
小车运动轨迹示意图:
动力系统设计:
设计主体思路:首先利用重力势能转化成由绳子带 动可调的绳轮式原动机构带动后轮驱动小车的前迚。
理论计算数据:能量用4J计算可以得到运行最大距 离,但实际运行中,能量运用率无法达到100%,相互抵 消不否需要实验数据说明。
小车整体及外观初步设计:
小车底板设计:小车底板宽度180mm,总长度300mm, 前半部分采用等腰梯形,上底100mm,下底180mm, 高100mm,后半部分为矩形设计长为200mm,宽度为 180mm。底板厚度3mm。 重物支撑架设计:采用长度为600mm,宽度50mm,厚 度为3mm中部为空的塑料板,另外重物支撑架两边用两 根长度为300mm的塑料棒支撑。 转向装置设计:转向连杆统一采用直径1mm的硬质铝棒, 中轴采用钢棒。转向轮位于小车中轴线上,转向轮轴线不 前底板相距30mm。转向轮外径为50mm,最大宽度 15.625mm。 后轮驱动设计:后轮外径60mm,宽度为10mm,两轮 中轴线离后底板30mm,采用嵌入式放置,小齿轮位于两 后轮连线中心处。
无碳小车机械加工工艺过程
标记
处数
更改文件号
签字
日期
第三届全国大学生工程训练综合能力竞赛
加工工艺分析
共页
第3页
编号:
产品名称
小车
生产纲领
500件/年
零件名称
生产批量
42件/月
1.零件的工艺分析
轴支架支撑车轴保证小车传动的重要零件,对垂直度、对称度有较高要求,因此加工必须保证其精度,如图所示
该零件为对称件,对于单个零件,一平面和二平面垂直度要求较高,φ6的孔尺寸公差要求较高,以配合轴承的安装,同时要求两对称件的φ6的孔有较高的同轴度。
材料
毛坯种类
毛坯外形尺寸
每毛坯可制作件数
每台件数
备注
序
号
工序
名称工序内容ຫໍສະໝຸດ 工 序 简 图机床
夹具
刀具
量具
辅具
工时
(min)
3
钻
(1)钻Φ6孔;
(2)钻Φ3.3孔;
(3)修整。
钻床
平台虎钳
平板
夹具
钻刀
镗刀等
游标卡尺
千分尺
检验棒等
20
4
检
检验
平板
垂直尺
游标卡尺千分尺等
20
编制(日期)
审核(日期)
标准化(日期)
1加工表面的尺寸精度、形状精度、和表面质量
2各加工表面之间的相互位置精度,零件的尺寸精度、形状精度、位置精度,对确定机械加工工艺方案和生产成本影响很大。
4.中批量生产纲领
①为保证加工精度,对所有加工部位采用粗、精加工分开的原则
②采用专业工装保证加工质量
3数控铣床加工时,注意夹具的精度和位置
2024年无碳小车心得体会(3篇)
2024年无碳小车心得体会2023年,无碳小车成为了城市出行的主流,取代了传统燃油车。
作为一个普通的市民,我也购买了一辆无碳小车,并通过日常的使用与体验,我深刻地感受到了无碳小车给我带来的诸多变化和优势。
在这篇文章中,我将与大家分享我对无碳小车的心得体会。
首先,无碳小车的最大优势在于环保。
与传统的燃油车相比,无碳小车不产生尾气排放,从根本上解决了空气污染的问题。
曾经拥有的燃油车不仅会产生有害的废气,还会产生噪音污染。
而无碳小车则静音运行,既减少了噪音污染,也给人们带来了更加安静的城市环境。
此外,无碳小车的造型设计也更加符合现代审美,给人一种时尚、科技的感觉。
其次,无碳小车在能源利用方面也有很大的优势。
传统燃油车需要依赖汽油等化石燃料进行驱动,而无碳小车则使用电能作为动力源。
随着可再生能源的快速发展,无碳小车可以通过太阳能、风能等清洁能源进行充电,进一步减少了对有限的化石燃料的依赖。
此外,无碳小车采用了先进的电池技术,能够实现长续航里程,为用户提供更加便捷的出行体验。
除了环保和能源利用方面的优势,无碳小车还在交通拥堵和交通安全方面有所突破。
由于无碳小车体积小巧灵活,可以很好地应对城市拥堵的问题。
无碳小车还采用了智能驾驶技术,可以通过与城市交通信号灯的互联互通,实现准确的导航和自动驾驶,大大提高了交通安全性。
此外,无碳小车还为城市居民提供了更多的便利。
无碳小车可以通过智能手机进行远程控制,用户可以随时随地进行车辆解锁、预约充电等操作,方便快捷。
同时,无碳小车还采用了电子支付技术,用户可以在车内直接支付停车费、过路费等费用,省去了排队等候的时间。
尽管无碳小车有着诸多优势,但也面临一些挑战。
首先是充电基础设施的建设问题。
由于无碳小车的充电需求较大,需要大规模的充电桩建设,但目前的充电桩数量仍然不足。
此外,无碳小车的充电速度相对较慢,用户需要提前进行规划和安排,以确保充电时间不影响日常出行。
另外,无碳小车的售价相对较高,而且维护费用也较传统燃油车更加昂贵,这也是一些消费者考虑的因素。
- 1、下载文档前请自行甄别文档内容的完整性,平台不提供额外的编辑、内容补充、找答案等附加服务。
- 2、"仅部分预览"的文档,不可在线预览部分如存在完整性等问题,可反馈申请退款(可完整预览的文档不适用该条件!)。
- 3、如文档侵犯您的权益,请联系客服反馈,我们会尽快为您处理(人工客服工作时间:9:00-18:30)。
坯
数
类
毛坯 数
1 707 板块 45*53*12 1/1
1
8 7075 板块 30*55*7 1/1 1
5
2 707 板料 400*600* 3/1
1
9 7075 棒料 Φ30*50 5/1 1
5
4
3 707 板料 200*100* 2/1
1
10 7075 板料 Φ140*3 1/1 1
5
5
4 707 棒料 Φ22*200 3/1
12
铣削费用:+20)×20/60=元
钳工费用:(20+10)×12/60=6 元
共计:+6=元
线切割 底 2 板 钻孔加工
90
10
100
线切割费用:25×100/60=元
钳工费用:(20+10)×15/60=元
13
2
15
共计:+=元
线切割
横
3
钻孔加工
杆
铣削加工
前 车削加工
4 轮 铣削加工
座 钻孔加工
江苏大学专业综合实践
小车照片
The car photos
注:该模板用于工艺成本、加工工艺 及工程管理方案的照片页。
江苏大学专业综合实践
工艺成本分析方案
共1 页
第1 页
编号
Process Cost Analysis Scheme 产品名 称
小车
生产纲 500 件/
领
年
1、材料成本分析
编号 材料 毛坯种类 毛坯尺寸 件数/毛 每台件 备注 编号 材料 毛坯种 毛坯尺寸 件数/ 每台件 备注
无碳小车总成本=800+125700+60000+30000+7000+15000=238500 元;每台小车:238500÷500=477 元。
钳工费用:(20+10)×3/60=元
2
1
3
共计:++=元
15
5
20
车削费用:+20)×20/60=元
钳工费用:(20+10)×15/60=元
13
2
15
共计:+=17 元
10
5
15
铣削费用:+20)×15/60=元
钳工费用:(20+10)×5/60=元
3
2
5
共计:+=元
8
2
10
车削费用:+20)×10/60=元
钳工费用:(20+10)×4/60=2 元
3
1
4
共计:+2=元
40
5
45
线切割费用:25×45/60=元
钳工费用:(20+10)×6/60=3 元
4
2
6
共计:+3=元
前 9 支 钻孔加工
架
线切割 推 10 杆 铣削加工 2
钻孔加工
车削加工
11
圆 盘
铣削加工
钻孔加工
推 车削加工 12 杆
1 线切割
圆 铣削加工
共计:元
3、总成本
无碳小车在设计时充分考虑到环保和降低成本的要求,在材料及加工设备的选择、零件的工艺安排和加工精度、 生产过程组织等各个环节,力求把小车的总成本控制到最合理。总成本主要包含以下几部分:
①无碳小车主要零件的材料费:800 元; ②无碳小车主要零件的人工费和制造费:(++++17++++3++17+++)×500=125700 元; ③无碳小车外购零件费用:外购主要包括直齿轮、支撑座、螺钉、轴承、法兰轴承、导轨等,按生产 500 台需求 购买,费用共计:60000 元;; ④此表中未涉及无碳小车其它零件的费用,按上述核算办法共计:30000 元; ⑤工装、夹具及辅料等其它费用:7000 元; ⑥总装费用:20×90/60×500=15000 元。
13
盘 轴
座 钻孔加工
14 销 车削加工
4
2
6
钳工费用:(20+10)×6/60=3 元
共计:3 元
30
2
32
线切割费用:25×32/60=元
铣削费用:+20)×7/60=元
5
2
7
钳工费用:(20+10)×5/60=元
3
2
5
共计:++=元
10
5
15
车削费用:+20)×15/60=元
1020)×15/60=元
1
11 7075 板料 120*52* 5/1 1
5
5
5 707 棒料 Φ30*13 1/1
1
12 45 钢 板块 14*12*4 1/1 1
5
7
6 707 棒料 Φ82*50 5/1
1
13 45 钢 棒料 Φ8*50 1/1 1
5
7 707 板料 50*25*10 1/1
1
14 45 钢 棒料 Φ7*35 3/1 1
钳工费用:(20+10)×5/60=元
3
2
5
共计:++=17 元
2
1
3
车削费用:+20)×3/60=元
线切割费用:25×30/60=元
25
5
30
共计:+=元
20
5
25
铣削费用:+20)×25/60=元
钳工费用:(20+10)×5/60=元
3
2
5
共计:+=元
10
5
15
车削费用:+20)×15/60=元
轴 车削加工 5
套 钻孔加工
杆 铣削加工 6支
座 钻孔加工
车削加工
7
前 轮
钻孔加工
线切割
8
后 轮
钻孔加工
35
5
40
线切割费用:25×40/60=元
钳工费用:(20+10)×3/60=元
2
1
3
铣削费用:+20)×5/60=元
3
2
5
共计:++=元
27
3
30
车削费用:+20)×30/60=元
35
5
40
铣削费用:+20)×40/60=元
5
2、人工费和制造费分析
零 序件 号名
称
工艺内容
工时
机动时间
辅助 时间
终准时间
工艺成本分析
双 铣削加工 轴
1支 撑 钻孔加工
座
15
5
20
车/小削时人;工费: 元/小时,车床使用费:20 元
铣/小削时人;工费: 元/小时,铣床使用费:20 元
钳元工/小人时工。费:20 元/小时,钻床使用费:10
10
2