无碳小车设计使用说明(一等奖作品)
无碳小车设计使用说明(一等奖作品)

第二届全国大学生工程训练综合能力竞赛无碳小车设计说明书参赛者:龚雪飞赵鹏飞刘述亮指导老师:朱政强戴莉莉2011-1-16摘要第二届全国大学生工程训练综合能力竞赛命题主题为“无碳小车” 。
在设计小车过程中特别注重设计的方法,力求通过对命题的分析得到清晰开阔的设计思路;作品的设计做到有系统性规范性和创新性;设计过程中综合考虑材料、加工、制造成本等给方面因素。
我们借鉴了参数化设计、优化设计、系统设计等现代设计发发明理论方法;采用了MATLAB 、PROE 等软件辅助设计。
我们把小车的设计分为三个阶段:方案设计、技术设计、制作调试。
通过每一阶段的深入分析、层层把关,是我们的设计尽可能向最优设计靠拢。
方案设计阶段根据小车功能要求我们根据机器的构成(原动机构、传动机构、执行机构、控制部分、辅助部分)把小车分为车架、原动机构、传动机构、转向机构、行走机构、微调机构六个模块,进行模块化设计。
分别针对每一个模块进行多方案设计,通过综合对比选择出最优的方案组合。
我们的方案为:车架采用三角底板式、原动机构采用了锥形轴、传动机构采用齿轮或没有该机构、转向机构采用曲柄连杆、行走机构采用单轮驱动实现差速、微调机构采用微调螺母螺钉。
其中转向机构利用了调心轴承、关节轴承。
技术设计阶段我们先对方案建立数学模型进行理论分析,借助MATLAB分别进行了能耗规律分析、运动学分析、动力学分析、灵敏度分析。
进而得出了小车的具体参数,和运动规律。
接着应用PROE 软件进行了小车的实体建模和部分运动仿真。
在实体建模的基础上对每一个零件进行了详细的设计,综合考虑零件材料性能、加工工艺、成本等。
小车大多是零件是标准件、可以购买,同时除部分要求加工精度高的部分需要特殊加工外,大多数都可以通过手工加工出来。
对于塑料会采用自制的‘电锯'切割。
因为小车受力都不大,因此大量采用胶接,简化零件及零件装配。
调试过程会通过微调等方式改变小车的参数进行试验,在试验的基础上验证小车的运动规律同时确定小车最优的参数。
无碳小车设计项目说明书一等奖作品样本

无碳小车设计项目说明书一等奖作品第二届全国大学生工程训练综合能力竞赛无碳小车设计说明书参赛者:龚雪飞赵鹏飞刘述亮指导老师:朱政强戴莉莉2011-1-16摘要第二届全国大学生工程训练综合能力竞赛命题主题为“无碳小车”。
在设计小车过程中特别注重设计的方法,力求通过对命题的分析得到清晰开阔的设计思路;作品的设计做到有系统性规范性和创新性;设计过程中综合考虑材料、加工、制造成本等给方面因素。
我们借鉴了参数化设计、优化设计、系统设计等现代设计发发明理论方法;采用了MATLAB、PROE等软件辅助设计。
我们把小车的设计分为三个阶段:方案设计、技术设计、制作调试。
通过每一阶段的深入分析、层层把关,是我们的设计尽可能向最优设计靠拢。
方案设计阶段根据小车功能要求我们根据机器的构成(原动机构、传动机构、执行机构、控制部分、辅助部分)把小车分为车架、原动机构、传动机构、转向机构、行走机构、微调机构六个模块,进行模块化设计。
分别针对每一个模块进行多方案设计,通过综合对比选择出最优的方案组合。
我们的方案为:车架采用三角底板式、原动机构采用了锥形轴、传动机构采用齿轮或没有该机构、转向机构采用曲柄连杆、行走机构采用单轮驱动实现差速、微调机构采用微调螺母螺钉。
其中转向机构利用了调心轴承、关节轴承。
技术设计阶段我们先对方案建立数学模型进行理论分析,借助MATLAB分别进行了能耗规律分析、运动学分析、动力学分析、灵敏度分析。
进而得出了小车的具体参数,和运动规律。
接着应用PROE软件进行了小车的实体建模和部分运动仿真。
在实体建模的基础上对每一个零件进行了详细的设计,综合考虑零件材料性能、加工工艺、成本等。
小车大多是零件是标准件、可以购买,同时除部分要求加工精度高的部分需要特殊加工外,大多数都可以通过手工加工出来。
对于塑料会采用自制的‘电锯’切割。
因为小车受力都不大,因此大量采用胶接,简化零件及零件装配。
调试过程会通过微调等方式改变小车的参数进行试验,在试验的基础上验证小车的运动规律同时确定小车最优的参数。
无碳小车设计说明

无碳小车设计说明设计说明:无碳小车设计背景:现在的交通工具使用化石燃料作为能源,不仅对环境造成了严重的污染,还加剧了全球变暖的问题。
为了解决这个问题,设计了一种无碳小车,它使用清洁能源作为驱动力,减少对环境的污染。
设计目标:1.使用清洁能源作为驱动力,减少对环境的污染。
2.提供舒适的乘坐体验和良好的操控性能。
3.具备足够的续航里程和快速充电功能。
4.物理结构紧凑,方便停放和携带。
5.引入智能控制系统,提供高效的安全性和智能交互。
设计特点:1.清洁能源驱动:无碳小车使用电能作为驱动力,充电器可使用太阳能或者风能进行充电,以减少对传统能源的依赖。
2.舒适性和操控性能:小车配备高质量的悬挂系统和减震系统,确保乘坐舒适性。
此外,小车采用电动驱动系统,提供平稳加速和操控性能。
3.续航里程和快速充电功能:小车配备高效的电池系统,提供足够的续航里程,以满足日常通勤需求。
同时,可支持快速充电功能,短时间内充电至80%以上。
4.紧凑的物理结构:小车采用紧凑的物理结构设计,尺寸较小,方便停放和携带,适合城市环境使用。
5.智能控制系统:小车配备智能控制系统,包括导航系统、安全辅助系统和智能交互界面。
导航系统可以提供最佳路线规划和实时交通信息,安全辅助系统可提供驾驶员警示和自动刹车等功能,智能交互界面可以通过语音或手势控制实现乘坐舒适性和便利性。
实施方案:1.动力系统设计:小车采用纯电动驱动系统,电池系统采用高能量密度的锂离子电池,以提供足够的续航里程。
充电器可以使用太阳能充电板或风力充电机,充电时间约为4小时。
2.悬挂系统设计:小车配备高质量的悬挂系统,以提供舒适的乘坐体验。
采用独立悬挂设计,可根据路面情况自动调节减震幅度。
3.控制系统设计:小车配备智能控制系统,包括中央控制单元、传感器和执行器。
中央控制单元接收传感器数据,并将其转换为相应的控制信号,通过执行器实现对小车的控制。
该系统可以提供导航、安全辅助、车辆诊断等功能。
无碳小车
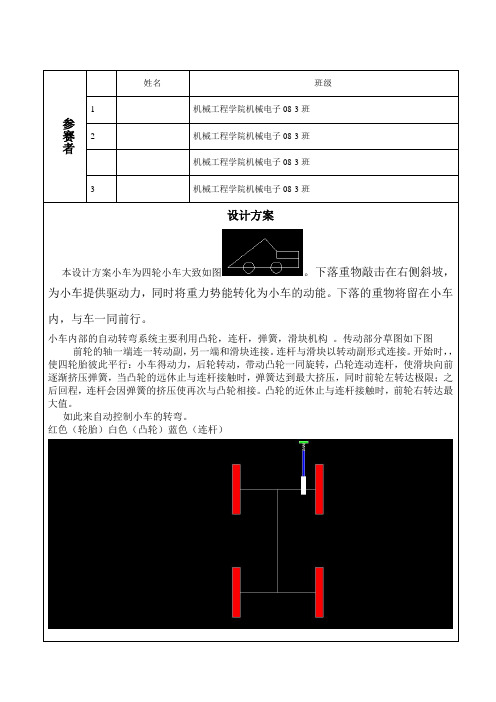
参赛者
姓名班级
1 机械工程学院机械电子08-3班
2 机械工程学院机械电子08-3班
机械工程学院机械电子08-3班
3 机械工程学院机械电子08-3班
设计方案
本设计方案小车为四轮小车大致如图。
下落重物敲击在右侧斜坡,为小车提供驱动力,同时将重力势能转化为小车的动能。
下落的重物将留在小车
内,与车一同前行。
小车内部的自动转弯系统主要利用凸轮,连杆,弹簧,滑块机构。
传动部分草图如下图前轮的轴一端连一转动副,另一端和滑块连接。
连杆与滑块以转动副形式连接。
开始时,,使四轮胎彼此平行:小车得动力,后轮转动,带动凸轮一同旋转,凸轮连动连杆,使滑块向前逐渐挤压弹簧,当凸轮的远休止与连杆接触时,弹簧达到最大挤压,同时前轮左转达极限;之后回程,连杆会因弹簧的挤压使再次与凸轮相接。
凸轮的近休止与连杆接触时,前轮右转达最大值。
如此来自动控制小车的转弯。
红色(轮胎)白色(凸轮)蓝色(连杆)
无碳小车——设计说明书
一、设计结构组成:
滑轮、重物、弹簧、圆锥齿轮,凸轮机构
二、设计图
三、设计图说明
1、驱动部分:如图所示,驱动轮通过小车斜面与重物相连,重物下落驱动小车轮转动,将重物下落的重力势能转化为小车的动能。
2、转向部分:如图所示,与驱动轮同轴的锥齿轮将驱动轮在竖直平面内的圆周转动转换成水平面内的圆周运动,然后再转化成竖直平面内的圆周运动,通过凸轮机构最终实现将圆周运动转化成杆的左右摆动,。
《无碳小车设计说明》-公开课件
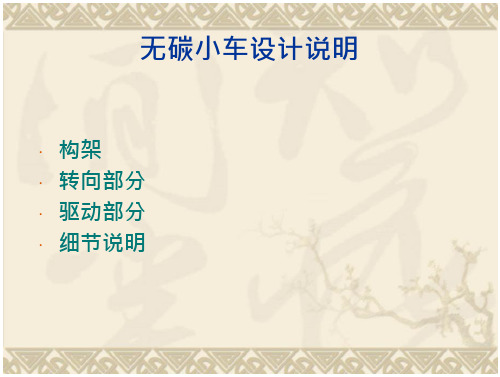
·在整个过程中,重力势能完 全转换为小车运动过程的损
耗。使小车行进的更远.
4.细节设计
· 车身 · 车轮 · 轴承 以减小小车重力和动过程
· 传输功率=转矩X角速度 ,通过一系列的齿 轮,带轮,转轴产生转速比,使作用在后 轮的转矩和阻尼转矩平衡,物块低速匀速 下落。
· 在后轮转轴上安放多个不同半径的带轮, 微调转矩,适应不同的环境下阻力的不同。
· 制作多套后轮,微调转矩。改变后轮时, 也要相应的改变转向传动轮的大小,同时 保持车身水平,适当调整前轮转轴的长度。 (现场可实现)
无碳小车设计说明
· 构架 · 转向部分 · 驱动部分 · 细节说明
1.构架部分
· 小车采用三轮结构(1个转向,2个驱动) · 重物落差0.5米物重1kg.
2.转向
· 转向机构与驱动轴相连
· 小车的转向轮周期性的摆动
· 计算传动机构,使小车行使200厘米时,转 向轮摆动一个周期。
· 确定连杆在转盘有位置,尽量减小转向轮 的摆动角度,从而使小车先驱的实际距离 变大。确定初始位置与摆轮角度的关系。
3.驱动
· 原理:绳拉力为动力。将物块下落的势能 尽可能多的转换为小车的动能,进而克服 阻力做功。物块在下落的过程中不可避免 的要与小车发生碰撞,碰撞过程必然要有 能量损失,所以要解决的问题:1下降过程 中,尽可能的降低下落的速度;2在将要下 降到小车时,改变转速比,使物块减速下 落,进一步减少碰撞损耗。
·
二、小车的起始和结束过程
· 梯形原动轮的设计实现小车的起 动和物块的从低速到减速下落。 减小因碰撞而损失的能量。
梯形原动轮
无碳小车说明书

无碳小车设计说明书学院:行知工学分院班级:机械132班学生姓名:学号:指导老师:完成时间: 2015 年 6 月 15 日1.绪论1.1小车的设计命题设计一种小车,驱动其行走及转向的能量是根据能量转换原理,由给定重力势能转换来的。
给定重力势能为 4 焦耳(取g=10m/s2),设计时统一用质量为1Kg的重块(¢50×65 mm,普通碳钢)铅垂下降来获得,落差400±2mm,重块落下后,须被小车承载并同小车一起运动,不允许从小车上掉落。
如图1.1所示。
图1.1要求小车行走过程中完成所有动作所需的能量均由此重力势能转换获得,不可使用任何其他的能量来源。
要求小车具有转向控制机构,且此转向控制机构具有可调节功能,以适应放有不同间距障碍物的竞赛场地。
要求小车为三轮结构,具体设计、材料选用及加工制作均由学生自主完成。
1.2小车的整体设计要求小车设计过程需要完成:机械设计、工艺方案设计、经济成本分析和工程管理方案设计。
命题中的工程管理项要求综合考虑材料、加工、制造成本等各方面因素,提出合理的工程计划。
设计能力项要求对参赛作品的设计具有创新性和规范性。
命题中的制造工艺能力项要求综合运用加工制造工艺的知识。
1.3小车的设计方法在小车的设计方法上,我们借鉴了参数化设计、优化设计、系统设计等现代设计发明理论方法。
采用CAXA、SolidWorks2012等辅助软件设计。
2.设计方案2.1尺寸设计由于小车实在平面上运行,转弯半径较小,所以定小车的宽度为150mm,长度为150mm,使其能拥有更佳的灵活性。
如图2.1所示。
图2.12.2最大转角因为小车长为150mm,当绕过最大偏移距离为500mm的圆弧时能得到最大转角,如图3.2所示,即可得最大转角位26.897°.如图2.2所示。
.. 图2.2设曲柄长度为10,已知最大转角位26.897°,由图2.3所示可知可得最大偏移距离图2.3偏移距离L=10/tan(26.897°)=19.71mm2.3后轮直径设计传动机构的功能是把动力和运动传递到转弯机构和驱动轮上。
机械设计大赛-无碳小车-设计说明书
目录前言第1章、绪论 (4)1.1 参赛主题 (4)1.2 功能分析 (4)1.3 设计方法 (4)第2章、轨迹和行走机构选型与计算 (6)2.1 轨迹和行走机构选型 (6)2.2 轨迹参数计算 (7)第3章、控制机构选型与计算 (10)3.1 控制机构选型 (10)3.2 放大机构的设计 (12)3.3 凸轮的设计 (13)第4章、传动机构选型与计算 (16)4.1 传动机构选型 (16)4.2 齿轮系的设计 (16)4.2 尺寸参数校核 (17)第5章、动力机构选型与计算 (19)5.1 绕绳轮安装位置分析 (19)5.2 力分析 (20)5.3 前轮转向阻力矩的计算 (23)5.4 弹簧劲度系数的计算 (23)5.5 尺寸参数的获取 (23)5.6 质量属性参数的确定 (26)5.7 参数的计算 (27)5.8 绕绳轮最大半径的确定 (29)第6章、微调机构简介 (30)第7章、误差分析及效率计算 (31)7.1 误差分析 (31)7.1.1 设计误差 (31)7.1.2 参数误差 (31)7.1.3 加工与装配误差 (31)7.2 传动效率的计算 (32)7.2.1 动力机构效率的计算 (32)7.2.2 传动机构效率的计算 (33)7.2.3 控制机构效率的计算 (34)第8章、仿真分析 (35)第9章、综合评价及改进方案 (37)9.1 综合评价 (37)9.2 改进方案 (39)第10章、参考文献 (40)第11章、附录 (40)11.1 机构运动简图及装配图 (40)11.2 小车三维装配图及爆炸图 (42)第1章、绪论1.1 参赛主题第三届全国大学生工程训练大赛的竞赛主题为“无碳小车越障竞赛”。
这次竞赛包含两个竞赛项目。
第一个项目与往届竞赛相同,为小车走“S”形线路绕杆。
竞赛项目二为小车走“8”字形线路绕杆。
通过商量,我们选择的竞赛项目为项目二。
1.2功能分析根据本次竞赛规定,竞赛项目二是小车在半张标准乒乓球台(长1525mm、宽1370mm)上,绕相距一定距离的两个障碍沿8字形轨迹绕行,绕行时不可以撞倒障碍物,不可以掉下球台。
无碳小车说明书
无碳小车设计说明书学院: 行知工学分院班级: 机械132班学生姓名:学号:指导老师:完成时间: 2015 年 6 月 15日1、绪论1、1小车得设计命题设计一种小车,驱动其行走及转向得能量就是根据能量转换原理,由给定重力势能转换来得。
给定重力势能为4焦耳(取g=10m/s2),设计时统一用质量为1Kg得重块(¢50×65 mm,普通碳钢)铅垂下降来获得,落差400±2mm,重块落下后,须被小车承载并同小车一起运动,不允许从小车上掉落。
如图1、1所示。
图1、1要求小车行走过程中完成所有动作所需得能量均由此重力势能转换获得,不可使用任何其她得能量来源。
要求小车具有转向控制机构,且此转向控制机构具有可调节功能,以适应放有不同间距障碍物得竞赛场地。
要求小车为三轮结构,具体设计、材料选用及加工制作均由学生自主完成。
1、2小车得整体设计要求小车设计过程需要完成:机械设计、工艺方案设计、经济成本分析与工程管理方案设计。
命题中得工程管理项要求综合考虑材料、加工、制造成本等各方面因素,提出合理得工程计划。
设计能力项要求对参赛作品得设计具有创新性与规范性。
命题中得制造工艺能力项要求综合运用加工制造工艺得知识。
1、3小车得设计方法在小车得设计方法上,我们借鉴了参数化设计、优化设计、系统设计等现代设计发明理论方法。
采用CAXA、SolidWorks2012等辅助软件设计。
2、设计方案2、1尺寸设计由于小车实在平面上运行,转弯半径较小,所以定小车得宽度为150mm,长度为150mm,使其能拥有更佳得灵活性。
如图2、1所示。
图2、12、2最大转角因为小车长为150mm,当绕过最大偏移距离为500mm得圆弧时能得到最大转角,如图3、2所示,即可得最大转角位26、897°、如图2、2所示。
、、图2、2设曲柄长度为10,已知最大转角位26、897°,由图2、3所示可知可得最大偏移距离图2、3偏移距离L=10 /tan(26、897°)=19、71mm2、3后轮直径设计传动机构得功能就是把动力与运动传递到转弯机构与驱动轮上。
无碳小车设计说明书(一等奖作品)
第二届天下大门生工程训练综合才能竞赛之相礼和热创作无碳小车计划阐明书参赛者:龚雪飞赵鹏飞刘述亮引导老师:朱政强戴莉莉2011-1-16择要第二届天下大门生工程训练综合才能竞赛命题主题为“无碳小车”.在计划小车过程中特别注重计划的方法,力求经过对命题的分析得到明晰开阔的计划思绪;作品的计划做到有零碎性规范性和创新性;计划过程中综合考虑材料、加工、制形成本等给方面要素.我们自创了参数化计划、优化计划、零碎计划等当代计划发发明理论方法;采取了MATLAB、PROE等软件辅助计划.我们把小车的计划分为三个阶段:方案计划、技术计划、制造调试.经过每一阶段的深化分析、层层把关,是我们的计划尽可能向最优计划靠拢.方案计划阶段根据小车功能要求我们根据机器的构成(原动机构、传动机构、执行机构、操纵部分、辅助部分)把小车分为车架、原动机构、传动机构、转向机构、行走机构、微调机构六个模块,进行模块化计划.分别针对每一个模块进行多方案计划,经过综合对比选择出最优的方案组合.我们的方案为:车架采取三角底板式、原动机构采取了锥形轴、传动机构采取齿轮或没有该机构、转向机构采取曲柄连杆、行走机构采取单轮驱动完成差速、微调机构采取微调螺母螺钉.其直达向机构利用了调心轴承、关节轴承.技术计划阶段我们先对方案建立数学模型进行理论分析,借助MATLAB分别进行了能耗规律分析、运动学分析、动力学分析、灵敏度分析.进而得出了小车的具体参数,和运动规律.接着运用PROE 软件进行了小车的实体建模和部分运动仿真.在实体建模的根底上对每一个零件进行了细致的计划,综合考虑零件材料功能、加工工艺、成本等.小车大多是零件是尺度件、可以购买,同时除部分要求加工精度高的部分必要特殊加工外,大多数都可以经过手工加工出来.对于塑料会采取自制的‘电锯’切割.由于小车受力都不大,因而大量采取胶接,简化零件及零件拆卸.调试过程会经过微调等方式改变小车的参数进行实验,在实验的根底上验证小车的运动规律同时确定小车最优的参数.关键字:无碳小车参数化计划软件辅助计划微调机构灵敏度分析目录一绪论本届竞赛命题主题为“无碳小车”.命题与高校工程训练教学内容相衔接,表现综合性工程才能.命题内容表现“创新计划才能、制造工艺才能、实践操纵才能和工程管理才能”四个方面的要求.给定一重力势能,根据能量转换原理,计划一种可将该重力势能转换为机械能并可用来驱动小车行走的安装.该自行小车在前行时可以自动避开赛道上设置的停滞物(每间隔1米,放置一个直径20mm、高200mm的弹性停滞圆棒).以小车前行距离的远近、以及避开停滞的多少来综合评定成绩.给定重力势能为5焦耳(取g=10m/s2),竞赛时一致用质量为1Kg×65 mm,平凡碳钢)铅垂下降来获得,落差500±2mm,重块落下后,须被小车承载并同小车一同运动,不容许掉落.要求小车前行过程中完成的全部动作所需的能量均由此能量转换获得,不成运用任何其他的能量方式.小车要求采取三轮结构(1个转向轮,2个驱动轮),具体结构外型以及材料选用均由参赛者自主计划完成.要求满足:①小车下面×20 mm的实心圆柱型钢制质量块作为载荷,其质量应不小于750克;在小车行走过程中,载荷不容许掉落.②小车计划过程中必要完成:机械计划、工艺方案计划、经济成天职析和工程管理方案计划.命题中的工程管理才能项要求综合考虑材料、加工、制形成本等各方面要素,提出合理的工程规划.计划才能项要求对参赛作品的计划具有创新性和规范性.命题中的制造工艺才能项以要求综合运用加工制造工艺学问的才能为主.小车的计划一定要做到目的明白,经过对命题的分析我们得到了比较明晰开阔的计划思绪.作品的计划必要有零碎性规范性和创新性.计划过程中必要综合考虑材料、加工、制形成本等给方面要素.小车的计划是进步小车功能的关键.在计划方法上我们自创了参数化计划、优化计划、零碎计划等当代计划发发明理论方法.采取了MATLAB、PROE等软件辅助计划.下面是我们计划小车的流程(如图一)图一二方案计划经过对小车的功能分析小车必要完成重力势能的转换、驱动本身行走、自动避开停滞物.为了方便计划这里根据小车所要完成的功能将小车划分为五个部分进行模块化计划(车架、原动机构、传动机构、转向机构、行走机构、微调机构).为了得到令人中意方案,采取扩展性头脑计划每一个模块,寻求多种可行的方案和构思.下面为我们计划图框(图二)图二在选择方案时应综合考虑功能、材料、加工、制形成本等各方面要素,同时尽量防止直接决策,减少决策时的客观要素,使得选择的方案可以综合最优.图三车架不必承受很大的力,精度要求低.考虑到分量加工成本等,车架采取木材加工制形成三角底板式.可以经过回收废木材获得,已加工.原动机构的作用是将重块的重力势能转化为小车的驱动力.能完成这一功能的方案有多种,就服从和简约性来看绳轮最优.小车对原动机构还有别的的具体要求.1.驱动力适中,不至于小车拐弯时速率过大倾翻,或重块晃动厉害影响行走.2.到达尽头前重块竖直方向的速率要尽可能小,防止对小车过大的冲击.同时使重块的动能尽可能的转化到驱动小车行进上,假如重块竖直方向的速率较大,重块本人还有较多动能未释放,能量利用率不高.3.由于分歧的场地对轮子的摩擦摩擦可能纷歧样,在分歧的场地小车是必要的动力也纷歧样.在调试时也不晓得多大的驱动力恰如其分.因而原动机构还必要能根据分歧的必要调整其驱动力.4.机构简单,服从高.基于以上分析我们提出了输入驱动力可调的绳轮式原动机构.如下图四如上图我们可以经过改变绳子绕在绳轮上分歧地位来改变其输入图四的动力.传动机构的功能是把动力和运动传递到转向机构和驱动轮上.要使小车行驶的更远及按计划的轨道精确地行驶,传动机构必须传递服从高、传动波动、结构简单分量轻等.1.不必别的额外的传动安装,直接由动力轴驱动轮子和转向机构,此种方式服从最高、结构最简单.在不考虑别的条件时这是最优的方式.2.带轮具有结构简单、传动颠簸、价格低廉、缓冲吸震等特点但其服从及传动精度其实不高.不得当本小车计划.3.齿轮具有服从高、结构紧凑、工作可靠、传动比波动但价格较高.因而在第一种方式不克不及够满足要求的状况下优先考虑运用齿轮传动.转向机构转向机构是本小车计划的关键部分,直接决定着小车的功能.转向机构也异样必要尽可能的减少摩擦耗能,结构简单,零部件已获得等基本条件,同时还必要有特殊的运动特性.可以将旋转运动转化为满足要求的来回摆动,带动转向轮左右转动从而完成拐弯避障的功能.能完成该功能的机构有:凸轮机构+摇杆、曲柄连杆+摇杆、曲柄摇杆、差速转弯等等.凸轮:凸轮是具有一定曲线轮廓或凹槽的构件,它运动时,经过高副接触可以使从动件获得连续或不连续的恣意预期往复运动.优点:只需计划得当的凸轮轮廓,即可使从动件得到恣意的预期运动,而且结构简单、紧凑、计划方便;缺陷:凸轮轮廓加工比较困难.在本小车计划中由于:凸轮轮廓加工比较困难、尺寸不克不及够可逆的改变、精度也很难包管、分量较大、服从低能量损失大(滑动摩擦)因而不采取曲柄连杆+摇杆优点:运动副单位面积所受压力较小,且面接触便于光滑,故磨损减小,制造方便,已获得较高精度;两构件之间的接触是靠本人的几何封闭来维系的,它不像凸轮机构偶然需利用弹簧等力封闭来坚持接触.缺陷:一样平常状况下只能近似完成给定的运动规律或运动轨迹,且计划较为复杂;当给定的运动要求较多或较复杂时,必要的构件数和运动副数每每比较多,这样就使机构结构复杂,工作服从降低,不但发生自锁的可能性添加,而且机构运动规律对制造、安装偏差的敏感性添加;机构中做立体复杂运动和作往复运动的构件所长生的惯性力难以均衡,在高速时将惹起较大的振动和动载荷,故连杆机构经常运用于速率较低的场合.在本小车计划中由于小车转向频率和传递的力不大故机构可以做的比较轻,可以忽略惯性力,机构其实不复杂,利用MATLAB进行参数化计划其实不困难,加上个链接可以利用轴承大大减小摩擦损耗进步服从.对于安装偏差的敏感性成绩我们可以添加微调机构来处理.曲柄摇杆结构较为简单,但和凸轮一样有一个滑动的摩擦副,其服从低.其急回特性导致难以计划出较好的机构.差速转弯差速拐是利用两个偏爱轮作为驱动轮,由于两轮子的角速率一样而转动半径纷歧样,从而使两个轮子的速率纷歧样,发生了差速.小车经过差速完成拐弯避障.差速转弯,是理论上小车能走的最远的计划方案.和凸轮异样,对轮子的加工精度要求很高,加工出来后也无法根据必要来调整轮子的尺寸.(由于加工和拆卸的偏差是不成防止的)综合下面分析我们选择曲柄连杆+摇杆作为小车转向机构的方案.行走机构即为三个轮子,轮子又厚薄之分,大小之别,材料之分歧必要综合考虑.有摩擦理论晓得摩擦力矩与正压力的关系为.力越小,因而可以走的更远.但由于加工成绩材料成绩安装成绩等等具体尺寸必要进一步分析确定.由于小车是沿着曲线行进的,后轮一定会发生差速.对于后轮可以采取双轮同步驱动,双轮差速驱动,单轮驱动.双轮同步驱动一定有轮子会与地面打滑,由于滑动摩擦远比滚动摩擦大会损失大量能量,同时小车行进遭到过多的约束,无法确定其轨迹,不克不及够无效防止碰到停滞.双轮差速驱动可以防止双轮同步驱动出现的成绩,可以经过差速器或单向轴承来完成差速.差速器触及到最小能耗原理,能较好的减少摩擦损耗,同时可以完成满足要运动.单向轴承完成差速的原理是但其中一个轮子速率较大时便成为从动轮,速率较慢的轮子成为自动轮,这样交替变换着.但由于单向轴承存在侧隙,在自动轮从动轮切换过程中出现偏差导致运动禁尽确,但影响有多大会不会影响小车的功能还需进一步分析.单轮驱动即只利用一个轮子作为驱动轮,一个为导向轮,另一个为从动轮.就如一辆自行车外加一个车轮一样.从动轮与驱动轮间的差速依托与地面的运动约束确定的.其服从比利用差速器高,但行进速率不如差速器波动,传动精度比利用单向轴承高.综上所述行走机构的轮子应有恰当的尺寸,可以假如有条件可以经过实验来确定完成差速的机构方案,假如规则容答应以采取单轮驱动.一台完好的机器包含:原动机、传动机、执行机构、操纵部分、辅助设备.微调机构就属于小车的操纵部分.由于后面确定了转向采取曲柄连杆+摇杆方案,由于曲柄连杆机构对于加工偏差和拆卸偏差很敏感,因而就必须加上微调机构,对偏差进行修正.这是采取微调机构的缘故原由之一,其二是为了调整小车的轨迹(幅值,周期,方向等),使小车走一条最优的轨迹.微调机构可以采取下面两种方式微调螺母式、滑块式如图五图五由于理论分析与实践状况有差距,只能经过理论分析得出较优的方案而不克不及得到最优的方案.因而我们计划了一种机构简单的小车,经过小部分的改动即可以改装成别的方案,再经过实验比较得到最优的小车.三技术计划技术计划阶段的目的是完成细致计划确定个零部件的的尺寸.计划的同时综合考虑材料加工成本等各要素.经过对小车建立数学模型,可以完成小车的参数化计划和优化计划,进步计划的服从和得到较优的计划方案.充分发挥计算机在辅助计划中的作用.为了简化分析,先不考虑小车外部的能耗机理.设小车外部的能小车轮与地面的摩阻系数.则有i个轮子对地面的压力.i个轮子的半径.i个轮子行走的距离为了更片面的理解小车的各个参数变更对小车行进距离的变更下面分别从1.轮子与地面的滚动摩阻系数、2.轮子的半径、3.小车的分量、4.小车能量转换服从.四方面考虑.经过查阅材料晓得一样平常材料的滚动摩阻系数为0.1-0.8间.下图为当车轮半径分别为(222mm,70mm)摩阻系数分别为0.3,0.4,0.5.....mm时小车行走的距离与小车外部转换服从的坐标图(图六)有上图六可知滚动摩阻系数对小车的运动影响非常明显,因而在计划小车时也特别留意考虑轮子的材料,轮子的刚度尽可能大,与地面的摩阻系数尽可能小.同时可看到小车为轮子提供能量的服从进步一倍小车行进的距离也进步一倍.因而应尽可能减少小车外部的摩擦损耗,简化机构,充分光滑.图七为当摩阻系数为0.5mm,车轮半径顺次添加10mm时的小车行走的距离与小车外部转换服从的坐标图图六图七由图可知当小车的半径每添加1cm小车即可多行进1m到2m.因而在计划时应考虑尽可能增大轮子的半径.符号阐明:驱动轮半径R齿轮传动比i驱动轮A驱动轮B驱动轴(轴2曲柄轴(轴1a、驱动:2则曲柄轴(轴1)转过的角度小车挪动的距离为(以A轮为参考)b、转向:c、小车行走轨迹只要A则小车转弯的曲率半径为d、小车其他轮的轨迹以轮A为参考,则在小车的运动坐标系中,BC在地面坐标系中,有整理上述表达式有:为求解方程,把上述微分方程改成差分方程求解,经过设定合理的参数的到了小车运动轨迹如(图六)图六a 、驱动如图:重物以加速率向下加速运动,绳子)(a g m T -=拉力为T ,有122λ⋅⋅=r T M ,(其中1λ发生的扭矩是考虑到摩擦发生的影响而设置的系数.) 驱动轮遭到的力矩A M ,曲柄轮遭到的扭矩1M ,A N 为驱动轮A 遭到的压力,A F 为驱动轮A 提供的动力,有221λ⋅=+M i M M A (其中2λ是考虑到摩擦发生的影响而设置的系数)b 、转向假设小车在转向过程直达向轮遭到的阻力矩恒为C M ,其大小可由赫兹公式求得,)11(1222121E E R B N cc c μμπσ-+-⋅=由于b 比较小,故 对于连杆的拉力c F ,有 c 、小车行走受力分析设小车惯量为I ,质心在则此时对于旋转中心O '的惯量为I '])[(2321a a m I I A +-+='ρ(平行轴定理)整理上述表达式得:小车一旦计划出来在不改变其参数的条件下小车的轨迹就曾经确定,但由于加工偏差和拆卸偏差的存在,拆卸好小车后可能会出现其轨迹与事后计划的轨迹有偏离,必要纠正.其次开始计划的轨迹大概其实不是最优的,必要经过调试实验来确定最优路径,着异样必要改变小车的某些参数.为了得到改变分歧参数对小车运转轨迹的影响,和引导怎样调试这里对小车各个参数进行灵敏度分析.经过MATLAB 编程得到幅值周期方向ibRa1曲柄半径r1d转向杆的长连杆长度单位:m转向轮与曲柄轴轴心距 b=0.15;摇杆长c=0.06;驱动轮直径D=0.355;驱动轮A与转向轮横向偏距驱动轮B与转向轮横向偏距a2=0.08;驱动轴与转向轮的距离d=0.18;曲柄长r1=0.01347;绳轮半径需加工的零件:a.驱动轴6061空心铝合金管.外径6mm 内径3mmb.车轮聚甲醛板(POM板材).厚度:8mm,规格尺寸:600*1200mm2.2可购买的尺度件:a.单向离合器轴承2个b.RBL关节轴承1个:SQ 5-RSc.调心球轴承1个d.深沟球轴承1个d.圆柱直齿轮1对小齿轮:模数=1,齿数=15,外径=17mm,内孔=3mm,大齿轮:模数=1,齿数=45,外径=47mm,内径=10mm,厚度=10mm材质:夹布塑料为了进一步分析本方案的可行性,我们利用了proe和MATLAB 进行了动态仿真,详见视频.四小车制造调试及改进小车制造流程详见工艺分析方案陈述小车调试方法小车的调试是个很紧张的过程,有了大量的理论根据支撑,还必须用大量的理论往验证.小车的调试触及到很多的内容,如车速的快慢,绕过停滞物,小车团体的和谐性,小车行进的距离等.(1)小车的速率的调试:经过小车在指定的赛道下行走,丈量经过指定点的工夫,得到多组数据,从而得出小车行驶的速率,经过实验,发现小车后半程速率较快,团体和谐功能不是太好,于是车小了绕绳驱动轴,减小过大的驱动力同时也增大了小车行进的距离.(2)小车避障的调试:虽然本组小车各个机构绝对来说较简单,损耗能量较少,但是避障不是很好,但与此同时,小车由于计划时采取了多组微调机构,经过观察小车在指定赛道下行走时避障的特点,微调螺母,渐渐小车避障功能改善,并做好标识表记标帜.小车改进方法由于本组小车采取胶水黏贴各处,虽然少了许多的加工成本费用,也防止了能量的过多损耗,但小车会偶然出现脱胶的征象,导致无法行进,于是想法改进,使小车能量损失减少,同时毛病出现的次数减少,波动功能较好,避障多,行进远.另外,本组采取微调机构,但经过计算编程发现要求精度非常高,改变0.001mm都可能使小车偏离原轨道,于是想法改进使小车精度降低,加工成本也减低.五评价分析小车优缺陷优点:(1)小车机构简单,单级齿轮传动,损耗能量少,(2)多处采取微调机构,便于纠正轨迹,避开停滞物,(3)采取大的驱动轮,滚阻系数小,行走距离远,(4)采取磁阻尼,小车波动性进步,不致使车速过快,缺陷:小车精度要求高,使得加工零件成本高,以及微调各个机构都很费时,避障波动行差,时而偏左,时而偏右.自动行走角逐时的前行距离估计经过理论与理论结合,小车行走距离(包含绕开停滞物)约20--25米.改进方向小车最大的缺陷是精度要求非常高,改进小车的精度要求,使能调整简单,小车便能达到很好的行走效果.六参考文献七附录clearclctic%符号定义%重物下降的高度h%小车行驶的路程s%外部能耗系数ypxln=10000;h=0.5;nn=1000;ypxl=linspace(0.5,1,n);R2=111/nn;R1=35/nn;m=1;g=9.8;mz=2;sgm=0.5/nn;for i=1:10% sgm=(0.1*i+0.2)/nn;%mz=1.75-0.2+0.2*i;R1=R1+20/nn;R2=R2+20/nn;s=ypxl*m*h/(mz*(1/R1+2/R2)*sgm); plot(ypxl,s);hold onendplot(0.5,0);tocclearclctic%符号定义%重物下降的高度h%驱动轴转过角度sd2%驱动轴传动比ii%转向轮轴心距b%转向杆的长c%转向轮转过的角度af%驱动轮半径R%驱动轮A与转向轮横向偏距a1 %驱动轮B与转向轮横向偏距a2 %驱动轴与转向轮的距离d%小车行驶的路程s%小车x方向的位移x%小车y方向的位移y%轨迹曲率半径rou%曲柄半径r1%绳轮半径r2%参数输入n=1000;h=linspace(0,0.5,n);ii=3;b=0.15;R=0.111;%驱动轮A与转向轮横向偏距a1 a1=0.08;%驱动轮B与转向轮横向偏距a2 a2=0.08;%曲柄半径r1r1=0.01347;%绳轮半径r2r2=0.006;%驱动轴与转向轮的距离dd=0.18;%转向杆的长cc=0.06;l=sqrt(b^2+r1^2)+(0.351)/1000;g=-10;sd2=h/r2;sd1=sd2/ii+pi/2;C=l^2-2*c^2-r1^2.*(cos(sd1)).^2-(b-r1.*sin(sd1)).^2; A=2.*c.*(b-r1.*sin(sd1));B=-2*c^2;af=asin(C./sqrt(A.^2+B.^2))-atan(B./A);format longrou=a1+(d)./(tan(af));s=sd2*R;ds=s(2)-s(1);dbd=ds./(rou);bd=cumsum(dbd);dy=ds*cos(bd);dx=-ds*sin(bd);x=cumsum(dx);y=cumsum(dy);xb=x-(a1+a2).*cos(bd);yb=y-(a1+a2).*sin(bd);xc=x-a1*cos(bd)-d*sin(bd);yc=y-a1*sin(bd)+d*cos(bd);plot(x,y,'b',xb,yb,'b',xc,yc,'m');hold ongrid onfor i=1:9t=0:0.01:2*pi;xy=0.01.*cos(t)-0.23;yy=0.01.*sin(t)+i;plot(xy,yy);hold onendtocclearclcticn=1000;h=linspace(0,0.5,n);ii=3;b=0.15;R=0.111;%驱动轮A与转向轮横向偏距a1a1=0.08;%驱动轮B与转向轮横向偏距a2%曲柄半径r1r1=0.01347;%绳轮半径r2r2=0.006;%驱动轴与转向轮的距离dd=0.18;%转向杆的长cc=0.06;l=sqrt(b^2+r1^2)+(0.351)/1000;%算法g=-10;sd2=h/r2;sd1=sd2/ii+pi/2;C=l^2-2*c^2-r1^2.*(cos(sd1)).^2-(b-r1.*sin(sd1)).^2; A=2.*c.*(b-r1.*sin(sd1));B=-2*c^2;af=asin(C./sqrt(A.^2+B.^2))-atan(B./A);format longrou=a1+(d)./(tan(af));s=sd2*R;ds=s(2)-s(1);dbd=ds./(rou);bd=cumsum(dbd);dy=ds*cos(bd);dx=-ds*sin(bd);x=cumsum(dx);y=cumsum(dy);xb=x-(a1+a2).*cos(bd);yb=y-(a1+a2).*sin(bd);xc=x-a1*cos(bd)-d*sin(bd);yc=y-a1*sin(bd)+d*cos(bd);toc%动力学分析%参数输入%重物质量m=1;%小车总质量mc=1.6+1;Nc=9.8*mc/3;%小车惯量rc=0.07;I=mc*rc^2;a3=0.05;%传动服从lmd=0.5;%%%%%%%%%%%%%%前轮半径RC=0.05;%前轮宽度B=2/1000;%弹性模量E1=100*1000000000;E2=150*1000000000;mu=0.2;%接触应力sgmc=sqrt((Nc/B/RC)/(2*pi*(1-mu^2)/E1));bc=Nc/sgmc/2/B;%摩擦要素mucmuc=0.1;%摩擦力矩McMc=sgmc*muc*bc*B^2/4;%摩阻系数sgm=0.5/1000;mMN=rou.*(m*9.8*r2*lmd-Nc*sgm)/R;K=rou.*m*r2^2*lmd/R^2;NCNB=Nc*sgm.*sqrt((rou-a1).^2+d^2)/RC+Nc*sgm*(rou-a1-a2); RIA=II./rou;NRA=NCNB*R./rou;aa=(mMN-NCNB)./(K+RIA);plot(y,aa)hold oncleartic%符号定义%重物下降的高度h%驱动轴转过角度sd2%驱动轴与圆柱凸轮轴传动比ii%转向轮与圆柱凸轮轴心距b%转向杆的长c%转向轮转过的角度af%驱动轮半径R%驱动轮A与转向轮横向偏距a1%驱动轮B与转向轮横向偏距a2%驱动轴与转向轮的距离d%小车行驶的路程s%小车x方向的位移x%轨迹曲率半径rou%曲柄半径r1%绳轮半径r2%参数输入n=10000;h=linspace(0,0.5,n);ii=3;b=0.15;R=0.111;%驱动轮A与转向轮横向偏距a1 a1=0.08;%驱动轮B与转向轮横向偏距a2 a2=0.08;%曲柄半径r1r1=0.01347;%绳轮半径r2r2=0.006;%驱动轴与转向轮的距离dd=0.18;%转向杆的长cc=0.06;l=sqrt(b^2+r1^2)+(0.351)/1000; aa=zeros(1,8);kk=zeros(3,8);。
无碳小车设计说明书
S组无碳小车设计说明书目录1、小车的设计要求 (1)2、无碳小车结构方案的设计 (2)2.1整体方案分析 (2)2.2驱动机构 (3)2.3传动机构 (4)2.4转向机构以及轨迹分析与设计 (4)2.4.1小车运行轨迹理论参数分析 (4)2.4.2小车动态力分析 (5)2.4.3传动机构及行走机构参数确定 (7)2.4.4 转向机构参数的确定 (8)2.5微调机构 (9)2.6小车车体整体分析 (9)3、基于SolidWorks motion的仿真分析 (10)3.1 简化模型的建立 (10)3.2 运动副的添加 (10)3.2 仿真计算以及结果分析 (11)参考文献 (12)1、小车的设计要求图1-1 无碳小车示意图图1-2 无碳小车运行轨迹图如上图1-1小车示意图:根据能量守恒定律,给一定重力势能(用⌀mm5065错误!未找到引用源。
普通碳钢的重块,质量为1kg,铅垂下落差为400mm来获得),设计一种“以重力势能驱动具有方向控制功能的无碳小车”,该小车能够在行驶的过程中有规律避开水平的平面上每隔1米设置一个弹性圆棒障碍物(如上图2小车运行轨迹图)。
保证小车行走的过程重物随车平稳的行走而不掉落,要求小车行走的过程中所有的动能均由重物的重力势能获得,不得借用其他形式的能量。
小车底板结构设计采用三轮结构,即2个驱动轮,1个转向轮。
细节上的结构只能根据学校现有材料、机床以及加工工艺的难度进行设计。
2、无碳小车结构方案的设计2.1整体方案分析通过对毕业设计任务要求及目的的剖析,利用发散性思维方式,把实现小车功能的各种可能方案一一列出,为了方便设计,可以将能实现小车功能细分为:驱动机构、传动机构、转向机构、微调机构四个模块。
下图2-1为无碳小车设计的思维导图:图2-1 无碳小车结构方案设计思路在选择各个模块方案时,要从实际情况出发,充分考虑实际学校的机床设备,材料的获取,制造成本以及实际加工工艺的可行性等等。
- 1、下载文档前请自行甄别文档内容的完整性,平台不提供额外的编辑、内容补充、找答案等附加服务。
- 2、"仅部分预览"的文档,不可在线预览部分如存在完整性等问题,可反馈申请退款(可完整预览的文档不适用该条件!)。
- 3、如文档侵犯您的权益,请联系客服反馈,我们会尽快为您处理(人工客服工作时间:9:00-18:30)。
第二届全国大学生工程训练综合能力竞赛无碳小车设计说明书参赛者:龚雪飞赵鹏飞刘述亮指导老师:朱政强戴莉莉2011-1-16摘要第二届全国大学生工程训练综合能力竞赛命题主题为“无碳小车”。
在设计小车过程中特别注重设计的方法,力求通过对命题的分析得到清晰开阔的设计思路;作品的设计做到有系统性规范性和创新性;设计过程中综合考虑材料、加工、制造成本等给方面因素。
我们借鉴了参数化设计、优化设计、系统设计等现代设计发发明理论方法;采用了MATLAB、PROE等软件辅助设计。
我们把小车的设计分为三个阶段:方案设计、技术设计、制作调试。
通过每一阶段的深入分析、层层把关,是我们的设计尽可能向最优设计靠拢。
方案设计阶段根据小车功能要求我们根据机器的构成(原动机构、传动机构、执行机构、控制部分、辅助部分)把小车分为车架、原动机构、传动机构、转向机构、行走机构、微调机构六个模块,进行模块化设计。
分别针对每一个模块进行多方案设计,通过综合对比选择出最优的方案组合。
我们的方案为:车架采用三角底板式、原动机构采用了锥形轴、传动机构采用齿轮或没有该机构、转向机构采用曲柄连杆、行走机构采用单轮驱动实现差速、微调机构采用微调螺母螺钉。
其中转向机构利用了调心轴承、关节轴承。
技术设计阶段我们先对方案建立数学模型进行理论分析,借助MATLAB 分别进行了能耗规律分析、运动学分析、动力学分析、灵敏度分析。
进而得出了小车的具体参数,和运动规律。
接着应用PROE软件进行了小车的实体建模和部分运动仿真。
在实体建模的基础上对每一个零件进行了详细的设计,综合考虑零件材料性能、加工工艺、成本等。
小车大多是零件是标准件、可以购买,同时除部分要求加工精度高的部分需要特殊加工外,大多数都可以通过手工加工出来。
对于塑料会采用自制的‘电锯’切割。
因为小车受力都不大,因此大量采用胶接,简化零件及零件装配。
调试过程会通过微调等方式改变小车的参数进行试验,在试验的基础上验证小车的运动规律同时确定小车最优的参数。
关键字:无碳小车参数化设计软件辅助设计微调机构灵敏度分析目录摘要 (2)一绪论 (6)1.1本届竞赛命题主题 (6)1.2小车功能设计要求 (6)1.3小车整体设计要求 (7)1.4小车的设计方法 (7)二方案设计 (8)2.1车架 (11)2.2原动机构 (11)2.3传动机构 (12)2.4转向机构 (13)2.5行走机构 (15)三技术设计 (17)3.1建立数学模型及参数确定 (18)3.1.1能耗规律模型 (18)3.1.2运动学分析模型 (21)3.1.3动力学分析模型 (26)3.1.4灵敏度分析模型 (28)3.1.5参数确定 (29)3.2零部件设计 (30)3.3整体设计 (33)3.3.1整体装配图 (33)3.3.2小车运动仿真分析 (34)四小车制作调试及改进 (34)4.1小车制作流程 (34)详见工艺分析方案报告 (34)4.2小车调试方法 (34)4.3小车改进方法 (35)五评价分析 (35)5.2自动行走比赛时的前行距离估计 (35)5.3改进方向 (36)六参考文献 (36)七附录 (37)7.1装配图 (37)7.2耗能分析程序 (41)7.3运动学分析程序 (42)7.4动力学分析程序 (44)7.5灵敏度分析程序 (47)一绪论1.1本届竞赛命题主题本届竞赛命题主题为“无碳小车”。
命题与高校工程训练教学内容相衔接,体现综合性工程能力。
命题内容体现“创新设计能力、制造工艺能力、实际操作能力和工程管理能力”四个方面的要求。
1.2小车功能设计要求给定一重力势能,根据能量转换原理,设计一种可将该重力势能转换为机械能并可用来驱动小车行走的装置。
该自行小车在前行时能够自动避开赛道上设置的障碍物(每间隔1米,放置一个直径20mm、高200mm的弹性障碍圆棒)。
以小车前行距离的远近、以及避开障碍的多少来综合评定成绩。
给定重力势能为5焦耳(取g=10m/s2),竞赛时统一用质量为1Kg的重块(φ50×65 mm,普通碳钢)铅垂下降来获得,落差500±2mm,重块落下后,须被小车承载并同小车一起运动,不允许掉落。
要求小车前行过程中完成的所有动作所需的能量均由此能量转换获得,不可使用任何其他的能量形式。
小车要求采用三轮结构(1个转向轮,2个驱动轮),具体结构造型以及材料选用均由参赛者自主设计完成。
要求满足:①小车上面要装载一件外形尺寸为φ60×20 mm的实心圆柱型钢制质量块作为载荷,其质量应不小于750克;在小车行走过程中,载荷不允许掉落。
②转向轮最大外径应不小于φ30mm。
1.3小车整体设计要求小车设计过程中需要完成:机械设计、工艺方案设计、经济成本分析和工程管理方案设计。
命题中的工程管理能力项要求综合考虑材料、加工、制造成本等各方面因素,提出合理的工程规划。
设计能力项要求对参赛作品的设计具有创新性和规范性。
命题中的制造工艺能力项以要求综合运用加工制造工艺知识的能力为主。
1.4小车的设计方法小车的设计一定要做到目标明确,通过对命题的分析我们得到了比较清晰开阔的设计思路。
作品的设计需要有系统性规范性和创新性。
设计过程中需要综合考虑材料、加工、制造成本等给方面因素。
小车的设计是提高小车性能的关键。
在设计方法上我们借鉴了参数化设计、优化设计、系统设计等现代设计发发明理论方法。
采用了MATLAB、PROE等软件辅助设计。
下面是我们设计小车的流程(如图一)图一二方案设计通过对小车的功能分析小车需要完成重力势能的转换、驱动自身行走、自动避开障碍物。
为了方便设计这里根据小车所要完成的功能将小车划分为五个部分进行模块化设计(车架、原动机构、传动机构、转向机构、行走机构、微调机构)。
为了得到令人满意方案,采用扩展性思维设计每一个模块,寻求多种可行的方案和构思。
下面为我们设计图框(图二)图二在选择方案时应综合考虑功能、材料、加工、制造成本等各方面因素,同时尽量避免直接决策,减少决策时的主观因素,使得选择的方案能够综合最优。
图三2.1车架车架不用承受很大的力,精度要求低。
考虑到重量加工成本等,车架采用木材加工制作成三角底板式。
可以通过回收废木材获得,已加工。
2.2原动机构原动机构的作用是将重块的重力势能转化为小车的驱动力。
能实现这一功能的方案有多种,就效率和简洁性来看绳轮最优。
小车对原动机构还有其它的具体要求。
1.驱动力适中,不至于小车拐弯时速度过大倾翻,或重块晃动厉害影响行走。
2.到达终点前重块竖直方向的速度要尽可能小,避免对小车过大的冲击。
同时使重块的动能尽可能的转化到驱动小车前进上,如果重块竖直方向的速度较大,重块本身还有较多动能未释放,能量利用率不高。
3.由于不同的场地对轮子的摩擦摩擦可能不一样,在不同的场地小车是需要的动力也不一样。
在调试时也不知道多大的驱动力恰到好处。
因此原动机构还需要能根据不同的需要调整其驱动力。
4.机构简单,效率高。
基于以上分析我们提出了输出驱动力可调的绳轮式原动机构。
如下图四如上图我们可以通过改变绳子绕在绳轮上不同位置来改变其输出的动力。
图四2.3传动机构传动机构的功能是把动力和运动传递到转向机构和驱动轮上。
要使小车行驶的更远及按设计的轨道精确地行驶,传动机构必需传递效率高、传动稳定、结构简单重量轻等。
1.不用其它额外的传动装置,直接由动力轴驱动轮子和转向机构,此种方式效率最高、结构最简单。
在不考虑其它条件时这是最优的方式。
2.带轮具有结构简单、传动平稳、价格低廉、缓冲吸震等特点但其效率及传动精度并不高。
不适合本小车设计。
3.齿轮具有效率高、结构紧凑、工作可靠、传动比稳定但价格较高。
因此在第一种方式不能够满足要求的情况下优先考虑使用齿轮传动。
2.4转向机构转向机构是本小车设计的关键部分,直接决定着小车的功能。
转向机构也同样需要尽可能的减少摩擦耗能,结构简单,零部件已获得等基本条件,同时还需要有特殊的运动特性。
能够将旋转运动转化为满足要求的来回摆动,带动转向轮左右转动从而实现拐弯避障的功能。
能实现该功能的机构有:凸轮机构+摇杆、曲柄连杆+摇杆、曲柄摇杆、差速转弯等等。
凸轮:凸轮是具有一定曲线轮廓或凹槽的构件,它运动时,通过高副接触可以使从动件获得连续或不连续的任意预期往复运动。
优点:只需设计适当的凸轮轮廓,便可使从动件得到任意的预期运动,而且结构简单、紧凑、设计方便;缺点:凸轮轮廓加工比较困难。
在本小车设计中由于:凸轮轮廓加工比较困难、尺寸不能够可逆的改变、精度也很难保证、重量较大、效率低能量损失大(滑动摩擦)因此不采用曲柄连杆+摇杆优点:运动副单位面积所受压力较小,且面接触便于润滑,故磨损减小,制造方便,已获得较高精度;两构件之间的接触是靠本身的几何封闭来维系的,它不像凸轮机构有时需利用弹簧等力封闭来保持接触。
缺点:一般情况下只能近似实现给定的运动规律或运动轨迹,且设计较为复杂;当给定的运动要求较多或较复杂时,需要的构件数和运动副数往往比较多,这样就使机构结构复杂,工作效率降低,不仅发生自锁的可能性增加,而且机构运动规律对制造、安装误差的敏感性增加;机构中做平面复杂运动和作往复运动的构件所长生的惯性力难以平衡,在高速时将引起较大的振动和动载荷,故连杆机构常用于速度较低的场合。
在本小车设计中由于小车转向频率和传递的力不大故机构可以做的比较轻,可以忽略惯性力,机构并不复杂,利用MATLAB进行参数化设计并不困难,加上个链接可以利用轴承大大减小摩擦损耗提高效率。
对于安装误差的敏感性问题我们可以增加微调机构来解决。
曲柄摇杆结构较为简单,但和凸轮一样有一个滑动的摩擦副,其效率低。
其急回特性导致难以设计出较好的机构。
差速转弯差速拐是利用两个偏心轮作为驱动轮,由于两轮子的角速度一样而转动半径不一样,从而使两个轮子的速度不一样,产生了差速。
小车通过差速实现拐弯避障。
差速转弯,是理论上小车能走的最远的设计方案。
和凸轮同样,对轮子的加工精度要求很高,加工出来后也无法根据需要来调整轮子的尺寸。
(由于加工和装配的误差是不可避免的)综合上面分析我们选择曲柄连杆+摇杆作为小车转向机构的方案。
2.5行走机构行走机构即为三个轮子,轮子又厚薄之分,大小之别,材料之不同需要综合考虑。
有摩擦理论知道摩擦力矩与正压力的关系为δ⋅=N M对于相同的材料δ为一定值。
而滚动摩擦阻力R N R Mf δ⋅==,所以轮子越大小车受到的阻力越小,因此能够走的更远。
但由于加工问题材料问题安装问题等等具体尺寸需要进一步分析确定。
由于小车是沿着曲线前进的,后轮必定会产生差速。
对于后轮可以采用双轮同步驱动,双轮差速驱动,单轮驱动。
双轮同步驱动必定有轮子会与地面打滑,由于滑动摩擦远比滚动摩擦大会损失大量能量,同时小车前进受到过多的约束,无法确定其轨迹,不能够有效避免碰到障碍。