微细加工技术概述
微细加工技术概述及其应用

2011 年春季学期研究生课程考核(读书报告、研究报告)考核科目:微细超精密机械加工技术原理及系统设计学生所在院(系):机电工程学院学生所在学科:机械设计及理论学生姓名:杨嘉学号:10S008214学生类别:学术型考核结果阅卷人微细加工技术概述及其应用摘要微细加工原指加工尺度约在微米级范围的加工方法,现代微细加工技术已经不仅仅局限于纯机械加工方面,电、磁、声等多种手段已经被广泛应用于微细加工,从微细加工的发展来看,美国和德国在世界处于领先的地位,日本发展最快,中国有很大差距。
本文从用电火花加工方法加工微凹坑和用微铣削方法加工微小零件两方面描述了微细加工技术的实际应用。
关键词:微细加工;电火花;微铣削1微细加工技术简介及国内外研究成果1.1微细加工技术的概念微细加工原指加工尺度约在微米级范围的加工方法。
在微机械研究领域中,从尺寸角度,微机械可分为1mm~10mm的微小机械,1μm~1mm的微机械,1nm~1μm的纳米机械,微细加工则是微米级精细加工、亚微米级微细加工、纳米级微细加工的通称。
广义上的微细加工,其方式十分丰富,几乎涉及现代特种加工、微型精密切削加工等多种方式,微机械制造过程又往往是多种加工方法的组合。
从基本加工类型看,微细加工可大致分为四类:分离加工——将材料的某一部分分离出去的加工方式,如分解、蒸发、溅射、切削、破碎等;接合加工——同种或不同材料的附和加工或相互结合加工方式,如蒸镀、淀积、生长等;变形加工——使材料形状发生改变的加工方式,如塑性变形加工、流体变形加工等;材料处理或改性和热处理或表面改性等。
微细加工技术曾广泛用于大规模集成电路的加工制作,正是借助于微细加工技术才使得众多的微电子器件及相关技术和产业蓬勃兴起。
目前,微细加工技术已逐渐被赋予更广泛的内容和更高的要求,已在特种新型器件、电子零件和电子装置、机械零件和装置、表面分析、材料改性等方面发挥日益重要的作用,特别是微机械研究和制作方面,微细加工技术已成为必不可少的基本环节。
微细加工技术
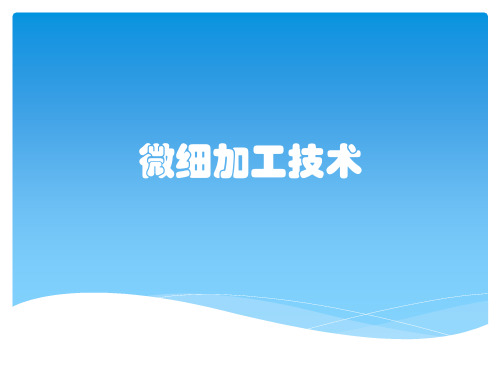
(b)
各向同性刻蚀
(a)各向同性刻蚀(搅拌);(b)各向同性刻蚀(不搅拌)
2)各向异性刻蚀
各向异性刻蚀是指某个方向上的刻蚀速率远大于另 一方向。刻蚀速度与基底材料的结晶取向密切相关;硅 材料是一种各向异性材料,在3个晶面上表现出不同的性 质。对于特定的刻蚀剂,硅的[100]晶面的腐蚀速度最快, [110]晶面次之,[111]晶面的腐蚀速度最慢。硅各向异性 刻蚀在几何形状控制上具有许多优点,可以制作出许多 具有垂直侧壁的微机械零件。
随着微/纳米科学与技术的发展,以形状尺寸微小或操 作尺度极小为特征的微机械成为人们在微观领域认识和 改造客观世界的一种高新技术。
一般认为,微机械依其特征尺寸可以划分为:小型机 械(1mm-10mm),微型机械(1um-1mm)以及纳米机 械(1nm-1um)。从广义来讲,微机械包括微小型机械 和纳米机械。
微细加工是由多项技术构成的一个技术群体,主要 包括:
(1)由IC工艺技术发展起来的硅微细加工技术;
(2)在特种加工和常规切削加工基础上发展形成的微 细制造技术;
(3)由上述两种技术集成的新方法,如LIGA、准 LIGA技术等。
微细加工与常规尺寸加工的区别:
(1)加工精度的表示方法不同:一般尺度加工,加工精 度常用相对精度表示,微细加工用绝对精度表示;
所谓牺牲层技术就是在微结构层中嵌入一层牺牲 材料,在后续工序中有选择地将这一层材料腐蚀掉 而不影响结构层本身。这种工艺的目的是使结构薄 膜与衬底材料分离,得到各种所需的表面微结构。 常用的衬底材料为单晶硅片,结构层材料沉积的多 晶硅、氮化硅等,牺牲层材料多为二氧化硅。
(2)加工机理存在很大的差异:微细加工中加工单位急 剧减小,必须考虑晶粒在加工中的作用;
微细电火花加工技术

微细电火花加工技术微细电火花加工技术是一种高精度加工方法,它通过利用电火花放电的瞬间高温和高压能量,将工件表面的金属材料溶解、熔化、蒸发和喷射等效应,实现对工件进行微细加工的一种技术。
微细电火花加工技术具有加工精度高、表面质量好、加工效率高等优点,在模具制造、航空航天、医疗器械等领域有着广泛的应用。
微细电火花加工技术的原理是利用电火花放电过程中产生的高温等效应来加工工件。
在微细电火花加工过程中,工件和电极通过一个电解液隔开,当施加足够的电压时,电极上会产生高频率的电火花放电。
电火花放电瞬间产生的高温和高压能量会使电解液中的金属离子快速聚集在工件表面,形成微小的气泡,同时气泡瞬间爆破产生的压力将工件表面的金属材料冲击下来。
通过不断重复这个过程,就可以实现对工件表面的微细加工。
微细电火花加工技术的加工精度非常高,可以达到亚微米级别。
这是因为在电火花放电过程中,由于高温和高压能量的局部聚集作用,使得工件表面的金属材料局部熔化和蒸发,从而实现微细加工。
此外,微细电火花加工技术还可以实现对工件表面的复杂形状、小孔和细槽等微细结构的加工,具有很高的灵活性。
微细电火花加工技术的应用非常广泛。
在模具制造领域,微细电火花加工技术可以用于制造高精度的模具零件,如模具芯、模具腔等。
在航空航天领域,微细电火花加工技术可以用于制造航空发动机的涡轮叶片、航天器的结构零件等。
在医疗器械领域,微细电火花加工技术可以用于制造高精度的医疗器械零件,如人工关节、牙科种植体等。
微细电火花加工技术虽然有很多优点,但也存在一些限制。
首先,由于加工过程中电火花放电会产生高温,工件表面容易产生热应力,从而导致表面质量下降。
其次,微细电火花加工技术只适用于导电材料的加工,对于非导电材料的加工效果不佳。
此外,微细电火花加工技术的加工效率相对较低,加工速度较慢。
微细电火花加工技术是一种高精度加工方法,具有广泛的应用前景。
随着科技的不断进步和发展,微细电火花加工技术将会进一步提高加工精度和效率,为各个领域的微细加工需求提供更好的解决方案。
东南大学--材料学院--表面微细加工技术简介
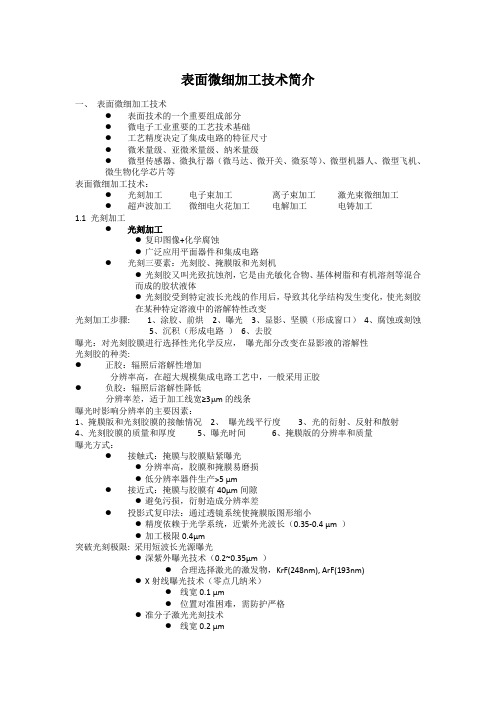
表面微细加工技术简介一、表面微细加工技术●表面技术的一个重要组成部分●微电子工业重要的工艺技术基础●工艺精度决定了集成电路的特征尺寸●微米量级、亚微米量级、纳米量级●微型传感器、微执行器(微马达、微开关、微泵等)、微型机器人、微型飞机、微生物化学芯片等表面微细加工技术:●光刻加工电子束加工离子束加工激光束微细加工●超声波加工微细电火花加工电解加工电铸加工1.1 光刻加工●光刻加工●复印图像+化学腐蚀●广泛应用平面器件和集成电路●光刻三要素:光刻胶、掩膜版和光刻机●光刻胶又叫光致抗蚀剂,它是由光敏化合物、基体树脂和有机溶剂等混合而成的胶状液体●光刻胶受到特定波长光线的作用后,导致其化学结构发生变化,使光刻胶在某种特定溶液中的溶解特性改变光刻加工步骤: 1、涂胶、前烘2、曝光3、显影、坚膜(形成窗口)4、腐蚀或刻蚀5、沉积(形成电路)6、去胶曝光:对光刻胶膜进行选择性光化学反应,曝光部分改变在显影液的溶解性光刻胶的种类:●正胶:辐照后溶解性增加分辨率高,在超大规模集成电路工艺中,一般采用正胶●负胶:辐照后溶解性降低分辨率差,适于加工线宽≥3 m的线条曝光时影响分辨率的主要因素:1、掩膜版和光刻胶膜的接触情况2、曝光线平行度3、光的衍射、反射和散射4、光刻胶膜的质量和厚度5、曝光时间6、掩膜版的分辨率和质量曝光方式:●接触式:掩膜与胶膜贴紧曝光●分辨率高,胶膜和掩膜易磨损●低分辨率器件生产>5 μm●接近式:掩膜与胶膜有40μm间隙●避免污损,衍射造成分辨率差●投影式复印法:通过透镜系统使掩膜版图形缩小●精度依赖于光学系统,近紫外光波长(0.35-0.4 μm )●加工极限0.4μm突破光刻极限: 采用短波长光源曝光●深紫外曝光技术(0.2~0.35μm )●合理选择激光的激发物,KrF(248nm), ArF(193nm)●X射线曝光技术(零点几纳米)●线宽0.1 μm●位置对准困难,需防护严格●准分子激光光刻技术●线宽0.2 μm●精确控制剂量方面有待进一步提高腐蚀/刻蚀:●湿法刻蚀:利用酸碱溶液作为腐蚀剂化学反应●优点:选择性好、重复性好、设备简单、成本低●缺点:钻蚀严重、对图形的控制性较差●干法刻蚀:●等离子体腐蚀:利用强电场下气体辉光放电产生的活性基与被腐蚀胶膜发生化学反应,产生挥发性气体而去除选择性好、对衬底损伤较小,但各向异性较差●离子腐蚀:利用具有一定动能的惰性气体的离子轰击集体表面,离子束腐蚀和溅射腐蚀(物理过程)●反应离子刻蚀(RIE:Reactive Ion Etching):离子轰击的物理效应和活性离子的化学效应结合具有前两者优点,同时各向异性和选择性应用最广泛的主流刻蚀技术新一代光刻技术:●接触-接近式→反射投影式→步进投影式→步进扫描式●436nm ~365nm(汞弧灯)→248nm (KrF准分子激光源)●利用光刻印刷细微图形已接近极限,50nm及以下,光学光刻将被其它新技术取代:●X射线光刻技术(XRL)●极紫外光刻技术(EUVL)●电子束投影光刻技术●离子束投影光刻技术●激光辅助直接刻印法(LADI)X射线光刻技术(XRL)●解决100nm以下光刻节点最现实的技术●光源波长0.7-1.3nm●缺点:掩膜衬底的机械性能(已获得较大突破)极紫外光刻技术(EUVL)——软X射线光刻●极紫外光源波长:10-14nm●物质吸收严重,反射光学系统●Mo、Si组成多层膜对13nm有较高的反射系数●若能得到应用,有可能解决≤50nm的光刻技术激光辅助直接刻印法(LADI)●2002年6月,美国普林斯顿大学研制的一种在硅片上制造出更精细结构的新技术●带有待压印线路图的石英压印模●将模子直接压印在硅片上,施加五千万分之一秒的大功率激光脉冲,使硅熔化后,按照模子的图案凝固,●可印出10nm的线路图,四百万分之一秒●《Science》杂志评论:该工艺可维持芯片小型化进程,摩尔定律在接下来的20年里可能仍然有效1.2 电子束加工工作原理:真空条件下,利用电流加热阴极发射电子束,经控制栅极初步聚焦后,由加速阳极加速,通过透镜聚焦系统进一步聚焦,使能量密度集中在直径1~10μm斑点内。
微细加工工艺技术

微细加工工艺技术微细加工工艺技术是一种应用于微电子、光学、纳米学等领域的高精度加工技术,该技术能够实现对微细结构的精密加工。
在微细加工工艺技术中,常常采用的加工方法有激光刻蚀、化学蚀刻、光刻以及微电子束等。
激光刻蚀是一种应用激光照射,通过激光束的高能量将材料表面局部蚀刻的加工方法。
与传统的机械刻蚀相比,激光刻蚀具有高精度、高效率的优点。
在激光刻蚀中,光束的聚焦度和光斑直径是影响加工精度的重要参数。
化学蚀刻是一种利用特定的化学反应,在材料表面选择性地产生化学蚀刻产物,并将其去除的加工方法。
化学蚀刻通常需要制备特定的蚀刻溶液,通过控制溶液的浓度和温度,来影响化学反应的速率和选择性。
化学蚀刻可以实现微细结构的高精度加工,并被广泛应用于光学元件和微流控芯片等领域。
光刻是一种基于光化学反应的加工方法,通过光阻的选择性暴露和去除,来形成所需的图案结构。
在光刻过程中,首先在材料表面涂敷一层光刻胶,然后利用光刻机的紫外光照射和显影等步骤,实现图案的转移。
光刻具有高精度、高分辨率和高重复性的优点,是微细加工中不可或缺的工艺之一。
微电子束也是一种实现微细结构加工的重要方法。
微电子束利用高能电子束在材料表面定向照射,经过准直、聚焦和偏转等步骤,将电子束的能量转化为对材料的加工作用。
通过控制电子束的参数,如能量、聚焦度和扫描速度等,可以实现对微细结构的精密加工。
微电子束在高精度加工领域具有很大的应用潜力,尤其在微电子器件、光电器件以及半导体器件等方面,具有广阔的发展前景。
总的来说,微细加工工艺技术是一种实现高精度加工的重要方法,包括激光刻蚀、化学蚀刻、光刻和微电子束等。
这些加工方法在微电子、光学、纳米学等领域发挥着重要作用,推动了相关技术的进步和应用的发展。
未来随着科学技术的不断进步,微细加工工艺技术将继续发展壮大,为人类社会带来更多的科技成果和应用产品。
微细加工技术的研究与应用
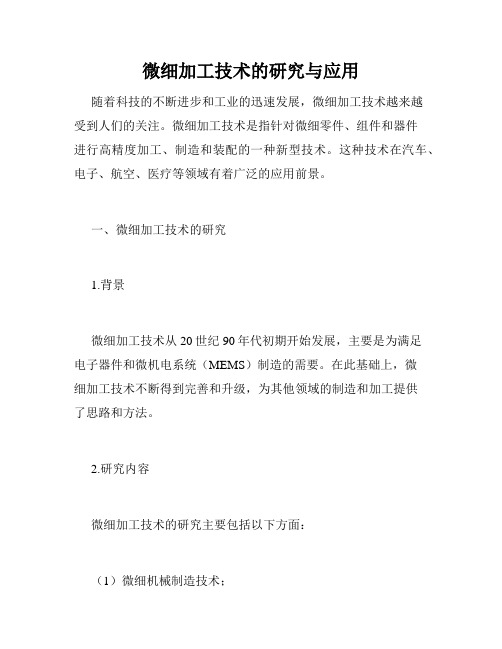
微细加工技术的研究与应用随着科技的不断进步和工业的迅速发展,微细加工技术越来越受到人们的关注。
微细加工技术是指针对微细零件、组件和器件进行高精度加工、制造和装配的一种新型技术。
这种技术在汽车、电子、航空、医疗等领域有着广泛的应用前景。
一、微细加工技术的研究1.背景微细加工技术从20世纪90年代初期开始发展,主要是为满足电子器件和微机电系统(MEMS)制造的需要。
在此基础上,微细加工技术不断得到完善和升级,为其他领域的制造和加工提供了思路和方法。
2.研究内容微细加工技术的研究主要包括以下方面:(1)微细机械制造技术;(2)微细电子制造技术;(3)微细光学制造技术;(4)微细生物制造技术。
其中,微细机械制造技术是应用最为广泛的一项技术,主要针对微型零部件、机械组件和器件等进行加工和制造。
3.研究难点微细加工技术的研究面临着许多难点,其中最主要的难点是如何实现高精度加工。
微细零部件的尺寸通常都在数微米至数百微米之间,而传统加工技术所能达到的精度却远远不够。
因此,如何在微小尺度下进行高精度加工,是微细加工技术研究的核心问题。
二、微细加工技术的应用1.汽车制造领域汽车制造领域是微细加工技术应用的主要领域之一。
在汽车制造中,许多零部件的尺寸都很小,而且对加工精度要求很高。
例如,发动机的火花塞、气门、燃油喷嘴等部件;车身的紧固件、密封件和缝合件等,都需要采用微细加工技术进行加工和制造。
2.电子制造领域电子制造领域也是微细加工技术应用的重要领域之一。
在电子制造中,许多IC芯片、闪存和存储器等器件的结构都非常微小,需要采用微细加工技术进行精密加工和制造。
同时,电子制造领域还需要采用微细加工技术进行导电薄膜的制造、微型电极的加工等工作。
3.医疗领域医疗领域也是微细加工技术应用的一个新兴领域。
在医疗领域中,微细加工技术可以用于制造微型手术器械、医用传感器、微型分析芯片等器件,从而为医疗诊断和治疗提供了新的手段和方法。
微细加工

1.精度表示方法
一般加工,其精度用误差尺寸与加工尺寸比值表示;微细加工,其精度用误 差尺寸绝对值表示。
在微细加工时,由于加工尺寸很小,引入了加工单位尺寸的概念。加工单位 尺寸简称加工单位,它表示去除材料的大小。例如,原子加工单位表示能去除一 个原子。显然,加工单位越小,可获得的精度就越高。
第三章 现代制造工程加工技术
SPM探针
介质中的分子 电化学作用区
偏置电压
电致刻蚀原理
第三章 现代制造工程加工技术
到目前为止,利用电脉 冲诱导氧化方法,已经在多 种半导体和金属(如Si,Cr, Nb,GaAs,Au和Ti等)表 面上,制备了所需的纳米结 构或器件。中国科学院分子 结构与纳米技术重点实验室 在氢钝化的p型Si(111)表 面上,利用此法刻蚀出了图 案清晰的中国科学院院徽。
第三章 现代制造工程加工技术
②微细加工刀具 微细切削加工一般采用单晶金刚石刀具。
各种单晶金刚石刀具
单晶金刚石铣刀刃形
第三章 现代制造工程加工技术
2. 微细车削加工
日本通产省工业技术院机械工程实验室(MEL)于1996年开发了世界上第 一台微型化的机床——微型车床。
世界第一台微细车床
车削轴的直径: 0.02mm
高的定位精度和重复定位精度,高平稳性的进给运动。
低热变形结构设计。
刀具的稳固夹持和高的安装精度。
高的主轴转速及动平衡。
稳固的床身构件并隔绝外界的振动干扰。
具有刀具破损检测的监控系统。
第三章 现代制造工程加工技术
C轴回转工作台 刀具 空气涡轮主轴 B轴回转工作台 X导轨 C 工件 Z导轨
B
空气油减振器
移动 完成
提取
放置
微细加工技术概述

微小机械学发展
• 微机械涉及的基本技术主要有:微机械 设计;微机械材料;微细加工;集成技术; 微装配和封接;微测量;微能源;微系统 控制等。 • 微机来自的制造和生产离不开微细加工技 术。
机械的微型化及相关的制造技术
传统机械
微小型机械 微细制造技术 MEMS技术 纳米机械 纳米制造技术
传统制造技术
所谓微细加工技术就是指能够制造微小尺寸零件 的加工技术的总称。 • 广义地讲,微细加工技术包含了各种传统精密加 工方法和与其原理截然不同的新方法,如微细切削 磨料加工、微细特种加工、半导体工艺等; • 狭义地讲,微细加工技术是在半导体集成电路制 造技术的基础上发展起来的,微细加工技术主要是 指半导体集成电路的微细制造技术,如气相沉积、 热氧化、光刻、离子束溅射、真空蒸镀等。
切削厚度与材料剪切应力关系在微切削时切削往往在晶粒内进行切削力一定要超过晶体内部的分子原子结合力其单位面积的切削阻力nmm2急剧增大刀刃上所承受的剪切应力增大刀刃上所承受的剪切应力变得非常大从而在单位面积上会产生很大的热量使刀刃尖端局部区域的温度极高因此要求采用耐热性高高温硬度高耐磨性强高温强度好的刀刃材料即超高硬度材料最常用的是金刚石等
微细加工的概念
目前微细加工领域的几大流派: •以美国为代表的硅基MEMS技术 以美国为代表的硅基MEMS技术 以美国为代表的硅基MEMS •以德国为代表的LIGA技术 以德国为代表的LIGA 以德国为代表的LIGA技术 •以日本为代表的机械加工方法的微细化 以日本为代表的机械加工方法的微细化 他们的研究与应用情况基本代表了国际微细 加工的水平和方向,应密切关注。
三、微细加工机理
微细切削加工为微量切削,又可称之为极薄切削。机 理与一般普通切削有的很大区别。 在微细切削时,由于工件尺寸很小,从强度和刚度上 不允许有大的吃刀量,同时为保证工件尺寸精度的要求, 最终精加工的表面切除层厚度必须小于其精度值,因此切 屑极小,吃刀量可能小于晶粒的大小,切削就在晶粒内进 行,晶粒就被作为一个一个的不连续体来进行切削,这时 切削不是晶粒之间的破坏,切削力一定要超过晶体内部非 常大的原子、分子结合力,刀刃上所承受的切应力就急速 地增加。
- 1、下载文档前请自行甄别文档内容的完整性,平台不提供额外的编辑、内容补充、找答案等附加服务。
- 2、"仅部分预览"的文档,不可在线预览部分如存在完整性等问题,可反馈申请退款(可完整预览的文档不适用该条件!)。
- 3、如文档侵犯您的权益,请联系客服反馈,我们会尽快为您处理(人工客服工作时间:9:00-18:30)。
1、电子束微细加工技术
电子束加工的原理
电子束加工是在真空条件下, 利用聚焦后能量密度极高(106~ 109W/cm2)的电子束,以极高的 速度冲击到工件表面极小的面 积上,在很短的时间(几分之一 微秒)内,其能量的大部分转变 为热能,使被冲击部分的工件 材料达到几千摄氏度以上的高 温,从而引起材料的局部熔化 和气化,被真空系统抽走。
微细加工的特点
微细加工作为精密加工领域中的一个极重要的关键技术, 目前有如下的几个特点: 1. 微细加工和超微细加工是多学科的制造系统工程; 2. 微细加工和超微细加工是多学科的综合高新技术; 3. 平面工艺是微细加工的工艺基础; 4. 微细加工技术和精密加工技术互补; 5. 微细加工和超微细加工与自动化技术联系紧密; 6.微细加工检测一体化。
所谓微细加工技术就是指能够制造微小尺寸零件 的加工技术的总称。 • 广义地讲,微细加工技术包含了各种传统精密加 工方法和与其原理截然不同的新方法,如微细切削 磨料加工、微细特种加工、半导体工艺等; • 狭义地讲,微细加工技术是在半导体集成电路制 造技术的基础上发展起来的,微细加工技术主要是 指半导体集成电路的微细制造技术,如气相沉积、 热氧化、光刻、离子束溅射、真空蒸镀等。
电子束切割
利用电子束在磁场中偏转的原理,使电子束在工 件内部偏转,还可以利用电子束加工弯孔和曲面。
电子束微细焊接
电子束焊接是利用电子束作为热源的一种焊接工艺,在 焊接不同的金属和高熔点金属方面显示了很大的优越性, 已成为工业生产中的重要特种工艺之一。 电子束焊接具有以下的工艺特点: (1)焊接深宽比高。 (2)焊接速度高,易于实现高速自动化。 (3)热变形小。 (4)焊缝物理性能好。 (5)工艺适应性强。 (6)焊接材料范围广。
应用二:电子束化学微细加工
第二类为电子束化学微细加工,电子束的能量较小, 一般小于30keV,主要用于大规模集成电路(LSI)和超大 规模集成电路(VLSI)复杂图形的制备以及光刻掩膜图形 的制备。 它利用电子束流的非热效应,功率密度较小的电子 束流与电子胶(又称电子抗蚀剂)相互作用,电能转化为 化学能,产生辐射化学或物理效应,使电子胶的分子链 被切断或重新组合而形成分子量的变化以实现电子束曝 光。包括电子束扫描曝光和电子束投影曝光。 电子束曝光微细加工技术,已经成为生产集成电路 元件的关键性加工手段。
微小机械学发展
微机械或微电子机械系统(MEMS)是20 世纪80年代后期发展起来的一门新兴学 科。它给国民经济、人民生活和国防、 军事等带来了深远的影响,被列为21世 纪关键技术之一。
微小机械学发展
随着微/纳米科学与技术的发展,以形状尺寸 微小或操作尺度极小为特征的微机械已成为人 们在微观领域认识和改造客观世界的一种高新 技术。 微机械由于具有能够在狭小空间内进行作业 而又不扰乱工作环境和对象的特点,在航空航 天、精密仪器、生物医疗等领域有着广阔的应 用潜力,受到世界各国的高度重视。
二、微细加工的概念及其特点
微细加工技术的产生和发展一方面是加工技 术自身发展的必然,同时也是新兴的微型机械 技术发展对加工技术需求的促进。超精加工在 20世纪的科技发展中做出了巨大的贡献。 东京工业大学的谷口纪男教授首先提出了纳 米技术术语,明确提出以纳米精度为超精密加 工的奋斗目标。
微细加工的概念
微细加工机理
1.切削厚度与材料剪切应力关系 在微切削时,切削往往在晶粒内 进行,切削力一定要超过晶体内 部的分子、原子结合力,其单位 面积的切削阻力(N/mm2)急剧 增大,刀刃上所承受的剪切应力 变得非常大,从而在单位面积上 会产生很大的热量,使刀刃尖端 局部区域的温度极高,因此要求 采用耐热性高、高温硬度高、耐 磨性强、高温强度好的刀刃材料, 即超高硬度材料,最常用的是金 刚石等。
三、微细加工机理
微细切削加工为微量切削,又可称之为极薄切削。机 理与一般普通切削有的很大区别。 在微细切削时,由于工件尺寸很小,从强度和刚度上 不允许有大的吃刀量,同时为保证工件尺寸精度的要求, 最终精加工的表面切除层厚度必须小于其精度值,因此切 屑极小,吃刀量可能小于晶粒的大小,切削就在晶粒内进 行,晶粒就被作为一个一个的不连续体来进行切削,这时 切削不是晶粒之间的破坏,切削力一定要超过急速 地增加。
四、高能束流微细特种加工技术
高能束流
高能束流加工是利用能量密度很高的电子束、 激光束或离子束等去除工件材料的特种加工方 法的总称。
高能束流微细特种加工技术
特点与应用:属于非接触加工,无成形工具, 而且几乎可以加工任何材料,在精微加工、航 空航天、电子、化工等领域中应用极广。 多学科交叉:其研究内容极为丰富,涉及光学、 电学、热力学、冶金学、金属物理、流体力学、 材料科学、真空学、机械设计和自动控制以及 计算机技术等多种学科,是一种典型的多学科 交叉技术。
微细加工机理
不同微细加工方法的加工机理
根据各种方法的加工机理的不同,微细加工可大致分为3大类: 分离加工将材料的某一部分分离出去的加工方式,如切削、分 解、刻蚀、溅射等。大致可分为切削加工、磨料加工、特种加 工及复合加工等。 结合加工同种或不同种材料的附加或相互结合的加工方式,如 蒸镀、沉积、生长、渗入等。可分为附着、注入和接合三类。 附着是指在材料基体上附加一层材料;注入是指材料表层经处 理后产生物理、化学、力学性能的改变,也可称之为表面改性; 接合则是指焊接、粘接等。 变形加工使材料形状发生改变的加工方式,如塑性变形加工、 流体变形加工等。
电子束加工装置
1)电子枪
电子枪是获得电子束的装置。它主要包括电子发 射阴极、控制栅极和加速阳极等。发射阴极一般用 钨或钽制成。小功率时用钨或钽做成丝状阴极;大 功率时用钽做成块状阴极。控制栅极为中间有孔的 圆筒形,其上加以较阴极为负的偏压,既能控制电 子束的强弱,又有初步的聚焦作用。加速阳极通常 接地,而阴极接很高的负电压。
电子束打孔
目前电子束打孔的最小直径已经可达 φ0.001mm左右,而且还能进行深小孔加工, 如孔径在0.5-0.9mm时,其最大孔深已超过 10mm,即孔的深径比大于15:1。 与其它微孔加工方法相比,电子束的打 孔效率极高,通常每秒可加工几十至几万个 孔。利用电子束打孔速度快的特点,可以实 现在薄板零件上快速加工高密度孔,这是电 子束微细加工的一个非常重要的特点。电子 束打孔已在航空航天、电子、化纤以及制革 等工业生产中得到实际应用。
微细加工的概念
微细加工与常规尺寸的加工的机理是截然不同的。微 细加工与一般尺度加工的主要区别体现在: 1. 加工精度的表示方法不同。在一般尺度加工中,加 工精度常用相对精度表示;而在微细加工中,其加工 精度则用绝对精度表示。加工单位概念的引入。 2. 加工机理存在很大的差异。由于在微细加工中加工 单位的急剧减小,此时必须考虑晶粒在加工中的作用。 3.加工特征明显不同。一般加工以尺寸、形状、位置 精度为特征;微细加工则由于其加工对象的微小型化, 目前多以分离或结合原子、分子为特征。
电子束加工装置
电子束加工装置主要由 电子枪、真空系统、控制系 统和电源等部分组成。 阴极经电流加热发射电 子,带负电荷的电子高速飞 向阳极,在飞向阳极的过程 中,经过加速极加速,又通 过电磁透镜聚焦而在工件表 面形成很小的电子束束斑, 完成加工任务。
1、工作台系统 2、偏转线圈 3、电磁透镜 4、光阑 5、加速阳极 6、发射电子的阴极 7、控制栅极 8、光学观察系统 9、带窗真 空室门 10、工件
微小机械学发展
• 微机械涉及的基本技术主要有:微机械 设计;微机械材料;微细加工;集成技术; 微装配和封接;微测量;微能源;微系统 控制等。 • 微机械的制造和生产离不开微细加工技 术。
机械的微型化及相关的制造技术
传统机械
微小型机械 微细制造技术 MEMS技术 纳米机械 纳米制造技术
传统制造技术
电子束加工原理
1-工件 2-电子束 3-偏转线圈 4-电磁透镜
电子束微细加工的特点
1)束径小、能量密度高。能聚焦到0.1µm,功率密度可达 109W/cm2量级。 2)可加工材料的范围广。对非加工部分的热影响小,对脆 性、韧性、导体、非导体及半导体材料都可加工。 3)加工效率高。每秒钟可以在2.5mm厚的钢板上钻50个直 径为0.4mm的孔。 4)控制性能好。 5)电子束加工温度容易控制。 6)污染小。 电于束加工的缺点是必须在真空中进行,需要一整套 专用设备和真空系统,价格较贵。
电子束微细加工的分类
应用一:电子束热微细加工
第一类为电子束热微细加工,电子束的能量 较大(30keV∼几百keV),又称为高能量密度电子束 加工,它是利用电子束的热效应,将电子束的动 能在材料表面转换成热能而对材料实施加工的。
应用一:电子束热微细加工
高能量密度电子束加工因工件表面束流斑点的功率 密度的不同又分为几种不同的加工方法: 1)当束流斑点功率密度为(10∼102)w/mm2 时,工件 表面不熔化,主要用于电子束热处理; 2)当束流斑点功率密度为(102∼105)w/mm2 时,工件 表面熔化,也有少量气化,主要用于电子束焊接和熔炼; 3)当束流斑点的功率密度为(105∼108)w/mm2 时,工 件产生气化,主要用于电子束打孔、刻槽、切缝、镀膜 和雕刻。
2)真空系统
真空系统是为了保证在电子束加工时维持 (1.33×10-2∼1.33×10-4)Pa的真空度。因为只有在高 真空中,电子才能高速运动。
3)控制系统和电源
电子束加工装置的控制系统包括束流聚焦控制、 束流位置控制、束流强度控制以及工作台位移控制 等。 电子枪 1、发射电子的阴极 2、控制 栅极 3、加速阳极 4、工件
电子束微细加工的应用
根据其功率密度和能量注入时间的不同,电子束加工可用于打孔、 切割、蚀刻、焊接、热处理和光刻加工等。归纳起来,电子束在微细 加工领域中的应用分为两大类:电子束热微细加工和电子束化学微细 加工。
电子束打孔 分离加工 焊接 热微细加工 电 子 束 微 细 加 工 化学微细加工 化学 光刻 应 电子束 光 电子束 光 电子束切割