转炉煤气回收工艺
转炉煤气回收方法
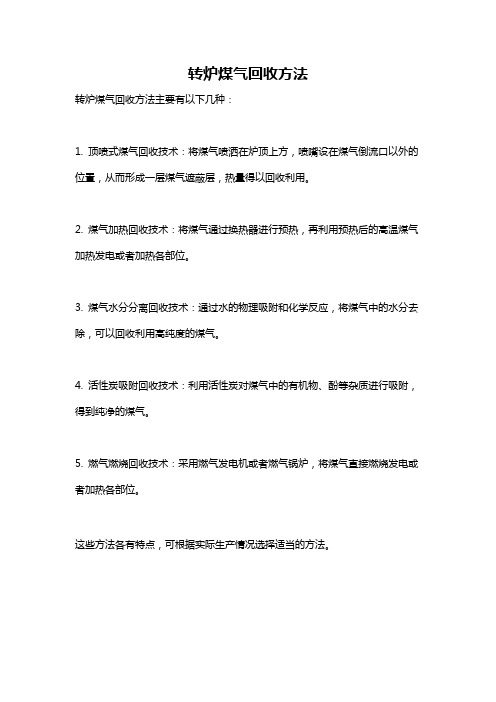
转炉煤气回收方法
转炉煤气回收方法主要有以下几种:
1. 顶喷式煤气回收技术:将煤气喷洒在炉顶上方,喷嘴设在煤气倒流口以外的位置,从而形成一层煤气遮蔽层,热量得以回收利用。
2. 煤气加热回收技术:将煤气通过换热器进行预热,再利用预热后的高温煤气加热发电或者加热各部位。
3. 煤气水分分离回收技术:通过水的物理吸附和化学反应,将煤气中的水分去除,可以回收利用高纯度的煤气。
4. 活性炭吸附回收技术:利用活性炭对煤气中的有机物、酚等杂质进行吸附,得到纯净的煤气。
5. 燃气燃烧回收技术:采用燃气发电机或者燃气锅炉,将煤气直接燃烧发电或者加热各部位。
这些方法各有特点,可根据实际生产情况选择适当的方法。
转炉煤气回收工艺简述

转炉煤气回收工艺简述伴随冶炼能力提升和技术发展,煤气从冶炼副产品变成富产品。
因为在过程所产生炉气中含量有大量一氧化碳,经过对炉气搜集、储存,又将这些一氧化碳作为燃气应用于生产之中。
高炉炼铁生产出铁水中有大量碳,当转炉温度>1700℃时,有大量碳被氧化,生成一氧化碳和二氧化碳,每一吨铁水可产生100m3一氧化碳,因为设备、技术等方面原因,只有60%-80%一氧化碳被回收。
在转炉炼钢前5分钟里,因为顶吹氧,大量纯氧气和高温铁水接触,在高温和充足氧气情况下,铁水中硅和氧气反应,燃烧生成氧化硅,这个反应有两个作用:一、铁水中大部分硅被氧化,生成钢渣脱离铁水。
二、硅燃烧放出大量热,提升了铁水温度。
(在这5分钟里所产生气体,不能回收)铁水温度升高后,氧气和碳反应生成一氧气化碳和二氧化碳,因为烟道几乎是密封,一氧化碳不会和外界氧气发生反应,所以烟道内一氧化碳保持它原状,铁水液面上气体温度可达成1700多度,高温气体进入一文,二文,然后进入旋流塔,在旋流塔中,高温气体上升,旋流塔上方有转炉浊环水向下喷淋,和煤气中灰尘凝结下落,达成洗涤煤气目标,同时使气体温度下降,40度气体进入一次除尘风机,对于进入一次除尘风机煤气,是用往返收还是放散,在线分析仪能够在一秒钟之内分析出结果,假如当初一氧化碳含量大于等于25%,且氧含量小于2%,那么就可回收,此时PLC自动控制打开旋转水封阀门,再打开三通阀(此时放散阀门被关闭)同时通往煤气柜阀门打开,开始回收煤气。
出了旋转水封煤气顺着管道进入预防回气水封(这里有四道,在正常回收情况下,为了减小对煤气阻力,这个水封没有水,当检修时,为了预防煤气柜内煤气回返,在水封里面注入适量水)再进入防沉降水封,(防沉降水封作用相当于膨胀节,起到管道伸缩作用,在管道变形时,相互不影响,不至于拉裂管道。
)当煤气进入煤气柜后,临时在里面存放,煤气柜容量大小决定了气柜内气体存留时间。
“断续回收,连续使用”是煤气回收基础状态。
转炉炼钢煤气回收

“LT”法系统主要是由蒸发冷却塔、静电除尘器、除尘风机、切换站、煤气冷却器等几部分组成。 转炉1500℃的高温烟气经汽化冷却烟道冷却至800~1000℃后,然后进入烟气净化系统。烟气净化系统
由蒸发冷却塔和圆筒型静电除尘器组成,烟气温度通过蒸发冷却器后降至170~200℃,同时通过调质处理, 降低了烟尘的电阻率,收集了粗粉尘。烟气经过这一初步处理后,进入圆筒型静电除尘器,进行进一步净 化,使其含尘质量浓度降至15mg/m3以下,从而达到最佳的除尘效率。
2.2 主要设备及工作原理
汽化冷却烟道:
转炉汽化烟道(也称为余 热锅炉)是转炉炼钢的主要配 套设备之一,该设备在工作时 要最大限度地收集高温烟气, 高温烟气的温度在1400摄氏度1600摄氏度,这些烟气在循环 泵产生的负压作用下,在汽化 烟道内流通,带有火星未燃烧 尽的钢渣进入燃烧室,之后烟 道内的温度在800摄氏度左右, 然后烟气随着烟道出口进入蒸 发冷却塔。
莱钢从2002年底开始酝酿转炉采用干法除尘技术。2003年完成施工图设计和控制系统的软件编程。 2004年7月建成投产, 对3*120t转炉使用了干法除尘,而投产后10天就达到设计能力,并持续稳定地生产。 至今三套“LT”系统均已通过了考核验收。
2) 缺点: (1)系统复杂,从而要求设备、仪表仪器质量高,以满足生 产要求;对施工质量要求也高; (2)要求管理和操作水平高,必须对管理和操作人员进行较 完善的培训,并在实际生产中达到熟练操作和维护;并且要 与炼钢工艺操作紧密配合和协调,杜绝野蛮操作; (3)一次投资高。
“OG”法工艺系统缺点:
由于该系统全过程采用湿法处理,技术存在以下几个缺点: 一是处理后的煤气含尘量较高,高达100mg/m3,要利用此煤气,需进一步净化方能使用; 二是系统存在二次污染,其污水需进行处理; 三是系统阻损大,所以能耗大,占地面积大,环保治理及管理难度较大。
转炉煤气干法净化回收技术

转炉煤气干法(LT)净化回收技术的国产化应用我国现有600多座转炉,年产钢超过4亿吨,节能减排潜力巨大。
目前我国绝大多数转炉的转炉煤气净化采用较为落后的湿法(以下简称老OG)除尘,耗水耗电量大,是钢铁工业节能减排的薄弱环节。
除了老OG除尘之外,近年来我国新建转炉采用了第四代湿法(以下简称新OG法),以及引进的千法(以下简称LT法):使转炉煤气净化技术取得了突破性进展。
在转炉煤气净化技术引进的同时,国内多家设计研究单位进行了吸收开发,目前转炉煤气净化的LT法、新OG法除引进少量关键技术和部件,大量的设备设计、系统设计立足于国内,甚至新OG法基本实现全国产化。
对我国转炉炼钢节能减排、实现负能炼钢起到了积极的推动作用。
但是我们仍清醒看到,转炉煤气净化发展到今天,这些技术包括引进技术都不同程度的存在一些问题、或有值得改之处,这是我国钢铁工业节能减排要追求和持续研究的新目标和新课题。
正是由于目前各种除尘方式的利弊所在,使新建转炉除尘设计选择LT法还是新OG法似乎难以确定。
本文就两种除尘方式进行比较,提出自己的建议。
1.国内外转炉烟气除尘技术的发展和现状当前,转炉烟气净化及煤气回收技术主要有两大类型:即日本的湿法系统(OG法)和德国的干法系统(LT法)。
1.1 湿法系统图1 OG法工艺流程OG法是以双级文氏管为主,抑制空气从转炉炉口流入,使转炉煤气保持不燃烧状态,经过冷却而回收的方法,因此也叫未燃法,又称湿法。
在湿法方面,日本从60年代起开发了OG法,这是世界上普遍采用的流程。
1962年,日本新日铁公司的转炉首次成功地应用该法对转炉烟气进行除尘并回收,合理地利用废气中的化学能和显能及含铁粉尘。
目前己成为世界上最广泛采用的转炉烟气处理方法,在保护环境、回收能源方面发挥了积极作用。
OG法装置主要由烟气冷却系统、烟气净化系统及附属设备组成(见图1)。
在冶炼中生成高一氧化碳浓度且含150~200mg/m3粉尘的煤气,温度达1600℃。
转炉负能炼钢与煤气回收技术
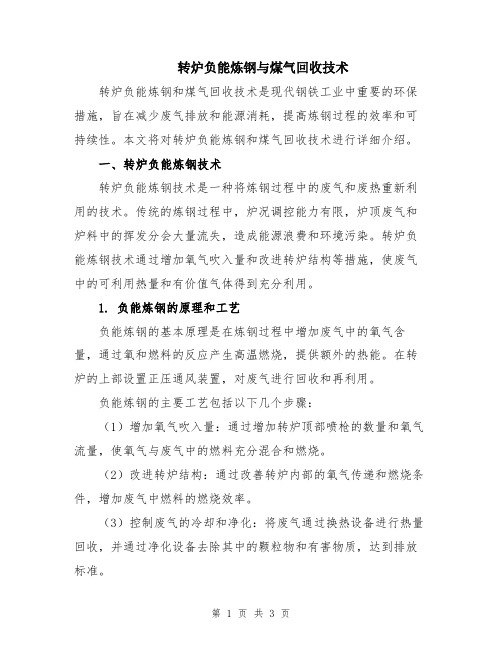
转炉负能炼钢与煤气回收技术转炉负能炼钢和煤气回收技术是现代钢铁工业中重要的环保措施,旨在减少废气排放和能源消耗,提高炼钢过程的效率和可持续性。
本文将对转炉负能炼钢和煤气回收技术进行详细介绍。
一、转炉负能炼钢技术转炉负能炼钢技术是一种将炼钢过程中的废气和废热重新利用的技术。
传统的炼钢过程中,炉况调控能力有限,炉顶废气和炉料中的挥发分会大量流失,造成能源浪费和环境污染。
转炉负能炼钢技术通过增加氧气吹入量和改进转炉结构等措施,使废气中的可利用热量和有价值气体得到充分利用。
1. 负能炼钢的原理和工艺负能炼钢的基本原理是在炼钢过程中增加废气中的氧气含量,通过氧和燃料的反应产生高温燃烧,提供额外的热能。
在转炉的上部设置正压通风装置,对废气进行回收和再利用。
负能炼钢的主要工艺包括以下几个步骤:(1)增加氧气吹入量:通过增加转炉顶部喷枪的数量和氧气流量,使氧气与废气中的燃料充分混合和燃烧。
(2)改进转炉结构:通过改善转炉内部的氧气传递和燃烧条件,增加废气中燃料的燃烧效率。
(3)控制废气的冷却和净化:将废气通过换热设备进行热量回收,并通过净化设备去除其中的颗粒物和有害物质,达到排放标准。
2. 负能炼钢的优势和应用负能炼钢技术在炼钢过程中有以下优势:(1)能源利用率高:通过回收废气中的热能,提供额外的热能供应,减少能源消耗。
(2)降低CO2排放:负能炼钢可以减少废气中CO2的排放量,降低对气候变化的影响。
(3)减少污染物排放:通过净化设备去除废气中的颗粒物和有害物质,减少对环境的污染。
负能炼钢技术已经得到广泛应用,特别是在大型钢铁企业中。
它不仅可以提高炼钢过程的效率和品质,还能降低环境污染和能源消耗。
二、煤气回收技术煤气回收技术是指将炼铁过程中产生的高温煤气进行净化和回收利用的技术。
传统的高炉炼铁过程中,高温煤气被大量排放到大气中,造成能源浪费和环境污染。
煤气回收技术通过煤气净化和能量回收,提高高炉炼铁过程的效率和可持续性。
转炉煤气回收工艺技术参数及操作方式
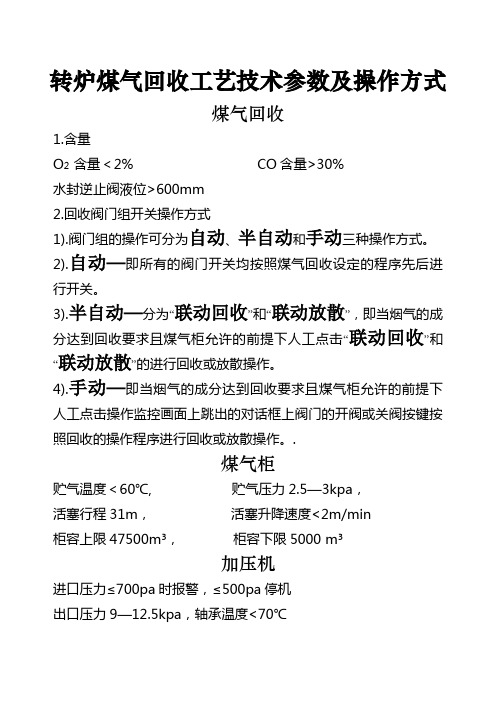
转炉煤气回收工艺技术参数及操作方式
煤气回收
1.含量
O2 含量<2%CO含量>30%
水封逆止阀液位>600mm
2.回收阀门组开关操作方式
1).阀门组的操作可分为自动、半自动和手动三种操作方式。
2).自动—即所有的阀门开关均按照煤气回收设定的程序先后进行开关。
3).半自动—分为“联动回收”和“联动放散”,即当烟气的成分达到回收要求且煤气柜允许的前提下人工点击“联动回收”和“联动放散”的进行回收或放散操作。
4).手动—即当烟气的成分达到回收要求且煤气柜允许的前提下人工点击操作监控画面上跳出的对话框上阀门的开阀或关阀按键按照回收的操作程序进行回收或放散操作。
.
煤气柜
贮气温度<60℃, 贮气压力2.5—3kpa,
活塞行程31m,活塞升降速度<2m/min
柜容上限47500m³,柜容下限5000 m³
加压机
进口压力≤700pa时报警,≤500pa停机
出口压力9—12.5kpa,轴承温度<70℃。
转炉煤气回收流程
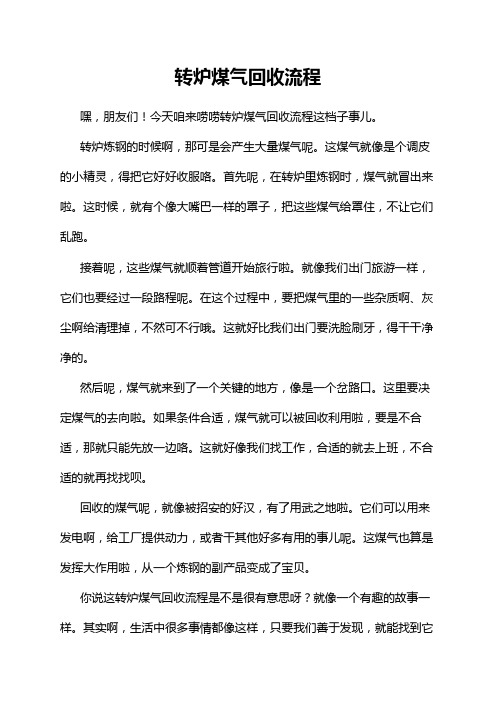
转炉煤气回收流程嘿,朋友们!今天咱来唠唠转炉煤气回收流程这档子事儿。
转炉炼钢的时候啊,那可是会产生大量煤气呢。
这煤气就像是个调皮的小精灵,得把它好好收服咯。
首先呢,在转炉里炼钢时,煤气就冒出来啦。
这时候,就有个像大嘴巴一样的罩子,把这些煤气给罩住,不让它们乱跑。
接着呢,这些煤气就顺着管道开始旅行啦。
就像我们出门旅游一样,它们也要经过一段路程呢。
在这个过程中,要把煤气里的一些杂质啊、灰尘啊给清理掉,不然可不行哦。
这就好比我们出门要洗脸刷牙,得干干净净的。
然后呢,煤气就来到了一个关键的地方,像是一个岔路口。
这里要决定煤气的去向啦。
如果条件合适,煤气就可以被回收利用啦,要是不合适,那就只能先放一边咯。
这就好像我们找工作,合适的就去上班,不合适的就再找找呗。
回收的煤气呢,就像被招安的好汉,有了用武之地啦。
它们可以用来发电啊,给工厂提供动力,或者干其他好多有用的事儿呢。
这煤气也算是发挥大作用啦,从一个炼钢的副产品变成了宝贝。
你说这转炉煤气回收流程是不是很有意思呀?就像一个有趣的故事一样。
其实啊,生活中很多事情都像这样,只要我们善于发现,就能找到它们的价值。
就像那些看似普通的东西,经过一番加工处理,可能就会变得非常有用。
我觉得啊,转炉煤气回收流程是个很了不起的事情。
它让我们在炼钢的同时,还能把产生的煤气利用起来,既节约了资源,又减少了污染。
这就像是我们过日子,要学会精打细算,把每一样东西都用到刀刃上。
这样我们的生活才能越来越好,我们的环境也才能越来越美。
所以啊,大家可别小瞧了这个转炉煤气回收流程,它可是有着大作用呢!。
转炉煤气干法净化回收系统

★拨叉振打仿真视频
★拨叉振打现场视频
六、关键技术及创新点
六、关键技术及创新点
六、关键技术及创新点
六、关键技术及创新点
七、系统性能保证
主要指标 煤气回收值 排放指标 排放指标
指标值 铁水冶炼不低于90m3/h(标) 回收煤气含尘浓度≤10mg/m3(标) 放散煤气含尘浓度≤15mg/m3(标)
回收煤气温度指标
≤70℃
八、经典工程实例
莱钢3座120吨转炉工程
太钢2座180吨转炉工程
八、经典工程实例
天铁2座190吨转炉工程
邯钢2座250吨转炉工程
八、经典工程实例
江阴兴澄2座150吨转炉工程
首钢迁安2座210吨转炉工程
八、经典工程实例
的目的,灰尘聚积在蒸发冷却器底部,由链式输送机送至贮灰仓。
三、系统关键设备及功能(电除尘器)
转炉煤气干法电除尘器是整个转炉煤气干法回收与净化系统中最为关键的
设备之一,也是所有电除尘器当中结构最为复杂的,对设计,制造和安装的要求 很高,转炉生产所产生的烟气中含有大量的煤气,为了使电除尘器内烟气具有较 好的空气动力学特性,避免在除尘器内形成煤气和空气的可燃性混合气体,必须 要防止电除尘器内产生回流和死区,最佳的流动方式是以塞状流动通过电除尘器 内部,基于上述观点,将电除尘器断面设计成圆筒型是最理想的,其主要结构及 特点如下: 电除尘器断面为圆形,因此也称为“圆筒型电除尘器”,有良好的动力学特性。 圆形壳体耐压能力达0.3MPa 壳体上安装有减压泄爆装置(泄爆阀),有效保证了除尘系统的安全运行
三、系统关键设备及功能(蒸发冷却器)
蒸发冷却器位于汽化冷却烟道下游,主要用于 烟气降温,烟气调质和预除尘。 主要由冷却器本体,喷雾系统,温度检测系统, 粗灰捕集系统四个系统组成。
- 1、下载文档前请自行甄别文档内容的完整性,平台不提供额外的编辑、内容补充、找答案等附加服务。
- 2、"仅部分预览"的文档,不可在线预览部分如存在完整性等问题,可反馈申请退款(可完整预览的文档不适用该条件!)。
- 3、如文档侵犯您的权益,请联系客服反馈,我们会尽快为您处理(人工客服工作时间:9:00-18:30)。
转炉煤气回收工艺
转炉煤气回收工艺是一种重要的环保技术,可以大量减少工业生
产过程中的废气排放,这对于保护环境、减少污染、节约能源具有非
常重要的意义。
转炉煤气回收工艺是将高温炼钢废气中的一部分可燃气体重新利用,使其燃烧后产生的热能可以继续用于炼钢工艺中。
这种自给自足
的方式在钢铁行业中具有显著的优势,因为钢铁生产需要大量的热能
来保持高温状态。
在传统的炼钢工艺中,高温炼钢废气中的大部分热能和可燃气体
都是被浪费掉了,直接排放到大气中造成了严重的环境污染。
而采用
转炉煤气回收工艺后,这些废气中的可燃气体可以被有效回收利用,
从而达到节约能源、减少排放的目的。
转炉煤气回收工艺主要分为两个步骤:收集和利用。
首先,需要在炉膛的废气口处设置一个废气管道,将所有的高温
炼钢废气收集起来。
在这个过程中,应该对废气管道进行良好的密封,避免废气的泄漏和外泄,从而确保废气能够稳定地流向后续的工艺流
程中。
其次,将收集到的废气送入热风炉或燃烧炉中进行燃烧利用,将
废气中的可燃气体转换成热能。
这个过程需要使用一些特殊的设备来
控制废气的流量、温度和压力等参数,以确保废气燃烧的效果达到最
佳状态。
通过这样的转炉煤气回收工艺,可以大大提高炼钢过程中的能效,降低工业生产过程中的废气排放,从而达到环保减排的目的。
不仅如此,这种技术还可以大幅降低企业的用能成本,减少经营成本,提高
企业的经济效益,具有非常积极的社会和经济意义。
总之,转炉煤气回收工艺是一项非常重要的绿色技术,可以促进
钢铁产业的可持续发展,实现环保减排、节约能源的目标。
随着环保
意识的提高和技术的不断进步,相信这种技术在未来的发展中将会得到更广泛的应用和推广。