薄壁钢管弯曲模具设计
触臂冷挤压模设计

施 蚺删 曩
触 臂 冷 挤 压 模 设 计
天水长城 电工器材厂 ( 甘肃 7 4 0 ) 冯宏明 10 0
触臂产 品如 图 1 ,材料 为 T Y 2 。该产 品是 V 1 内 S户 高压真空断路器 的关键零件 ,我 国电器产 品中 ,它 占有 相 当的市场份额。开关类导 电产 品,电器性 能除设计 因 素外 ,主要取决于触头的材质和加工质量 。
两个台阶 ,当液压机下缸 工作 时,顶杆  ̄ 1 m部分 先 2m 将 活动芯轴顶出工件 3 m, 时 ,工件与 芯轴 已分离 ; a r 此 继续 向上运动 ,顶杆  ̄4 m部分将工件从 凹模 中顶出 , 3m 顶杆长度按照液压机顶缸高度互配。
4 模具工作过程 .
图 2 挤压工艺 图 图 3 毛坯 图
如图2 所示 ,由弯管模块 、滚动压轮和导轮组成 。滚 动 压轮和导轮安装于滚轮座 中,并可在转盘 的滑槽 中上下 移动 。弯管时,扳动手柄带动转盘绕轴转 动,由导 轮向 管子施加压力 , 使其发生弯 曲变形 。同时滚动压轮 在钢 管弯 曲部位施加一定压力 ,通过轮上弧槽使之产 生一反 向预压力 ,以抵消钢管 弯曲时产生 的椭 圆变形 , 管子 使
2 冷挤压工艺分析 .
该零 件断 面缩减率 为 e 4 .% ,经查 阅:有 色金 = 75
属许用变形程度 e= 0 ~ 5 f 9 % 9%,可以一次挤出;P=
27 K , 用 35 Kl 60 N 选 10 b四柱液压机 。
1 工艺设计 .
()国内触臂生产企业 1 采用数控车床加工 , 原材料
内缘与弯管模块弧槽紧密贴合,以强化弯曲部位管壁,
消除内壁皱褶 。
下端面加工 03  ̄ 5 4 1)啪 心轴导入孔 节模用压板固定 在液压机工作台上。模套 9与凹模 8热装,过盈量取
简易U型弯曲模设计

简易 U型弯 曲模设计
王 智 文 全 兴
( 北华航 天工业学院 材料 工程 系,河北 廊坊 050 ) 600
摘 要 :本文介绍 了一种 简易的 U型弯曲模具 的设计方法 ,具有结构 简单 、制造容 易、节约材料 、重量轻 的特
点 ,在小批量生产 中有借鉴意义。 关键词 :弯 曲模 ;简易模 ;小批量 中图分类号:T 2 1 G 4 文献标识码 :A 文章编号 :17 —7 3 (0 7 0 — 0 1 2 6 3 9 8 20 ) 1 0 0 —0
WA h NG Z i WE a 。ig N Qunxn
管 中间穿过固定于两侧连接板上 , 连接板采用 9 × 0 9 角钢制成。这样用四根钢管解决 了凸、 O 凹模 的圆
角加工的问题 。同时由于凹模在弯曲模工作时可以 绕着芯轴转动, 使得工件毛坯容易进入凹模中, 不容 易产生划伤现象。下模 中的顶板用通用弹顶器提供
顶出力, 对工件起 到底部压平和顶 出工件 的作用 0 工件毛坯定位采用外加定位板的方法, 不和模具制
偿 施。 模具 用在凸、 模 放橡 板的 措 本 采 凹 之间 胶
社 . 0 0. 20
『]中国模具设计 大典 编委会 . 2 中国模 具设计 大典 [ ・ M]南
昌: 江西科学技术 出版社 ,0 3 20 .
De i n fLo Co tu- y eBe d n e s g o w- s T p n i g Di
大相对弯曲半径的 U型件的生产有借鉴意义。
:
由于 U型弯 曲模 需要保证 凸、 凹模 之间 的间
『]钟毓斌 冲压工艺与模具 l J j : L 工业 出版 M] 北尿 冲压工艺与模具设计 .匕 移械 ・ 慨上业 出瞅 1
弯管原理和弯管模具设计

冷弯管原理和弯管模具设计一.弯管原理弯管机标准模具包括:弯管模、夹紧块、导板(或滚轮)。
多节活芯、防皱块为选件D管件外径t管件壁厚R弯曲半管件外径D仅反映管件大小,管件弯曲加工的易难程度取决于管件的壁厚和弯曲半径,管件壁厚越小,半径越小加工难度越大。
一般我们用相对壁厚,相对弯曲半径作为弯管的工艺参数相对壁厚tx=t/D,相对弯曲半径Rx=R/D弯管机对于Rx>3D,tx>0.04的管件使用标准模具即可,对于Rx<3D,tx<0.04D 的管件弯管机可加上防皱板, 多节芯头等工艺措施来保证管件弯曲质量弯管机主要采用缠绕弯管工艺,缠绕弯管工艺可以比较容易在弯管模具加上各种措施以得到较好的管件质量。
弯管工艺弯管工艺,口径从DN25~DN104,壁厚1~2mm,其弯曲半径一般为1D,即是管子口径。
弯管最难处理的就是内圆弧,弯径小了容易起皱,上述工艺主要是消皱器起作用,所以能弯小半径的工件那消皱器的材料很讲究,太硬了,磨伤工件,太软了,不起作用。
是一种铜合金。
弯管芯棒的选取和使用摘要:介绍了管子在冷态弯制时的变形情况,以及通过合理选择芯棒及掌握其正确的使用方法,达到弯制出理想小半径管件的方法。
键词:应力;芯棒;相对弯曲半径;相对壁厚一、引言弯管技术广泛应用于锅炉及压力容器行业,中央空调制造业、汽车工业、航空航天工业、船舶制造业等多种行业,弯管质量的好坏,将直接影响到这些行业的产品的结构合理性,安全性、可靠性等。
因此,为了弯制出高质量的管件,就应该掌握管件在不同工艺条件下的加工技巧。
对于冷态弯管,合理选择芯棒的形成及掌握其正确的使用方法非常必要。
二、工艺分析在纯弯曲的情况下,外径为D、壁厚为S的管子受外力矩M的作用发生弯曲时,中性层外侧的管壁受拉应力σ1的作用而减薄,内侧管壁受压应力σ2的作用而增厚(见图1a)。
同时,合力F1和F2又使管子弯曲处的横截面发生变形而成为近似椭圆形(见图1b),内侧管壁在σ2的作用下还可能出现失稳而起皱(见图1c),为弯制出理想的管件,就应采取相应的措施来防止上述这些缺陷的产生,其中有芯弯管就是最常用的有效方法之一。
有芯弯管模具设计

当 R D较 大时弯 曲模 胎半 径 取小 值 ;当 R D较 / /
小 时弯 曲模胎 半径取 大值 ,最终 靠试模 进行修 正 。
( ) 导板 2 导 板 ( 图 4 是有 弯管 装 置 中 见 )
3 .模 具 设 计 ( )弯 曲模 胎 和镶块 1 弯 曲模 胎 和 镶 块 ( 图 见
锻 压
t a!Fo m i g r n
栏目 持 王 建 宏 主
有芯弯管模具设计
陕西 北 方 动 力 有 限 责 任公 司 ( 鸡 宝 7 10 ) 2 30 王娟侠 刘永林 李俊梅 刘 振 林 1 .有 芯 弯 管 原理
有芯 弯管是 在 弯 管 机 上利 用 芯 棒 使 管 材 沿 弯 曲 模绕 弯 的工 艺方 法 ( 图 1 。弯 管胎 膜 固定 在 机 床 见 )
管 子直径 的 2倍 。芯 棒 常 用 3 rW8 材料 制 造 ,热 C2 V
图 8 链节式 多球芯棒
五是 软轴 式 多球 芯 棒 如 图 9示 ,是 用 一 根 软 轴
把多个 碗 状 球体 串 接 而 成 ,可 实 现 空 间 任 意 方 向的 摆 动 ,适用 于 薄 壁 管 单 一 、多 次 和 空 间 弯 曲 成形 的
力 、物力及 财力 ,而且 易破裂 、起皱 及椭 圆度超差 。
当 R D为 3~4时 ,合金 钢管 R / 取 0 9 R;碳 素 .4 钢管 取 ( . 6~ . 8 0 9 0 9 )R。其 中 尺 为弯 曲模 胎 的 半径 ;R为弯 管 中心 层弯 曲半径 ;D为管子外 径 。
一
是 圆头 式 : ,其 形 状 简单 ,制 造 方 便 ( 芷棒 见
图 5 。但 由于 芯棒 与 管 壁 接触 面积 少 ,因此 防截 面 )
桥架30度上下爬坡弯头制作方法

桥架30度上下爬坡弯头制作方法桥架30度上下爬坡弯头制作方法一、前言桥架是一种用于支撑电缆、管道等设备的金属构件,常用于建筑物内部或室外。
在实际工程中,由于地形和场地限制,桥架需要进行弯曲处理以适应不同的路线和角度。
本文将介绍如何制作30度上下爬坡弯头。
二、材料准备1. 钢管:直径为3英寸(约76.2毫米),壁厚为4毫米的无缝钢管。
2. 弯头模具:根据所需角度定制的弯头模具。
3. 焊接设备:包括氩弧焊机、切割机等。
4. 手工工具:包括锤子、扳手、千斤顶等。
三、制作过程1. 制作模板首先,根据所需角度和半径,在木板上画出相应的图案,并按照图案切割出合适大小的木板。
然后,将木板固定在平整的工作台上,并用锤子和千斤顶将其塑形成所需角度和半径的模板。
2. 切割钢管根据所需长度和角度,在钢管上用钢笔或铅笔标出切割线。
然后,用切割机将钢管沿着标记线切割成所需长度。
注意,切割时需要保证切口平整、无毛刺。
3. 弯曲钢管将切好的钢管放入弯头模具中,并用千斤顶将其压制成所需角度和半径的形状。
注意,弯曲时需要均匀施力,避免出现变形或裂纹。
4. 焊接将弯曲好的钢管与模板对齐,并用扳手固定在模板上。
然后,在焊接前,先用氩弧焊机进行预热处理。
最后,将焊接点进行打磨和涂漆处理。
四、注意事项1. 制作过程中需要注意安全,避免发生意外事故。
2. 切割和弯曲钢管时要保证精度和质量,避免出现偏差或损坏。
3. 焊接时要保证焊缝牢固、美观,并进行防腐处理。
4. 制作完成后要进行检查和测试,确保符合设计要求并能够正常使用。
五、总结本文介绍了制作桥架30度上下爬坡弯头的方法,包括材料准备、制作过程、注意事项等方面。
制作过程中需要注意安全、精度和质量,确保制作出符合设计要求和实际使用的优质产品。
小R弯管挤压精整工艺及模具设计
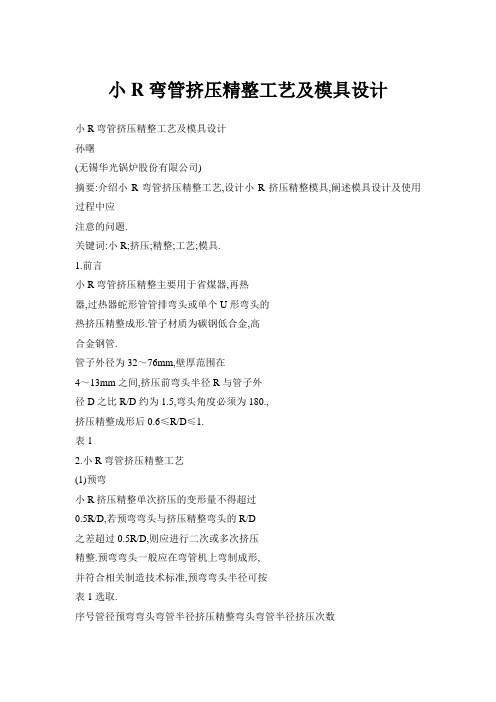
小R弯管挤压精整工艺及模具设计小R弯管挤压精整工艺及模具设计孙曙(无锡华光锅炉股份有限公司)摘要:介绍小R弯管挤压精整工艺,设计小R挤压精整模具,阐述模具设计及使用过程中应注意的问题.关键词:小R;挤压;精整;工艺;模具.1.前言小R弯管挤压精整主要用于省煤器,再热器,过热器蛇形管管排弯头或单个U形弯头的热挤压精整成形.管子材质为碳钢低合金,高合金钢管.管子外径为32~76mm,壁厚范围在4~13mm之间,挤压前弯头半径R与管子外径D之比R/D约为1.5,弯头角度必须为180.,挤压精整成形后0.6≤R/D≤1.表12.小R弯管挤压精整工艺(1)预弯小R挤压精整单次挤压的变形量不得超过0.5R/D,若预弯弯头与挤压精整弯头的R/D之差超过0.5R/D,则应进行二次或多次挤压精整.预弯弯头一般应在弯管机上弯制成形,并符合相关制造技术标准,预弯弯头半径可按表1选取.序号管径预弯弯头弯管半径挤压精整弯头弯管半径挤压次数132R45R32一次挤压2击38R55R38一次挤压338R55R25二次挤压442R6OR42一次挤压542R60R26二次挤压6由5lR76R51一次挤压75lR76R34二次挤压8击57R86R57一次挤压9击57R86R45二次挤压1063.5R95R63.5一次挤压(2)模具安装调试在挤压机上装好挤压模,精整模,背模,挤压模和精整模上应安装定位销,这样在挤压和精整过程中上下模块可以准确合拢,在制造和安装过程中也能准确定位.在挤压弯头前调整挤压模左,右开档尺寸,使挤压后的管子节距符合精整模的要求.调整精整模上下模中心线,空载运行数次.检查油压,加热炉,测温仪等,无异常情况.清理挤压精整模具,型腔内无异物,每次挤压精整后,亦应清理模具型腔.一22—(3)弯头加热根据管子材质的不同,加热温度从800~lIO0"C.加热时应尽量控制在温度范围的上限, 以保证精整时弯头的温度仍在规范规定的温度范围内.弯头的整个弧长及不少于lOmm的直段应得到可靠的加热,弯头弧长中间内侧的加热温度应略低于其它部位.加热温度应用测温仪监测,严格控制加热时间,并予以记录,不得仅凭肉眼估测.弯头加热必须控制加热均匀,现场不得使用任何影响弯头温度的器具,否则挤压后弯头成形会比较差,易造成过烧,氧化皮严重,精整后弯头外表面粗糙,压痕,"尖头","方头"等缺陷.(4)挤压挤压流程见图l(a),挤压时应将加热的弯头推入挤压模,顶进背模圆弧槽中.挤压模上下合拢夹住管子,左右挤压模从外向内横向运动,弯头顶住背模纵向往后退.弯头是在左右挤压模及背模内靠作用力下挤压成形的. (5)精整成形精整流程见图l(b),合模前应使弯头准确地落人精整模下模内,弯头与精整模的中心线偏移不得超过0.5.,上下合模精整成形.精整是利用挤压后的余热,挤压后应将小R弯头立即放人精整模进行整形,精整的行动要及时, 控制好终压温度,挤压后弯头的温度若低于所要求的温度时,应对弯头重新加热.精整后弯管用空气冷却至室温,不得用水或其他方法加速冷却.(6)检验:挤压精整后弯头应按相关制造技术标准进行外形,表面,椭圆度,减薄量等检验.弯头必须平滑,无损伤,皱纹和波浪起伏.3.小R挤压精整模具小R挤压精整模具由挤压模和精整模组成见图l.a)挤压(b)精整图1管子挤压精整流程图1.背模上板2.背模下板3.左上挤压模4.左下挤压模5右上挤压模6.右下挤压模7.上精整模8.下精整模9.定位销(1)挤压模挤压模采用三个分片式模具,由左右挤压模和背模组成.挤压模的型腔根据管子外径设计与弯曲半径无关,可分为直段,圆滑过渡区和收缩直段三部分.背模上下板后部碰紧,中前部的圆弧槽根据预弯弯头直径及弯头伸人长度设计.尽量减小挤压模和背模的接触角度,使挤压过程模具运行更加平稳.保证挤压模收缩段上下面和背模板圆弧槽上下面在同一平面上,避免挤压模和背模接触面出现高度差,防止挤压过程中模具在弯头上造成压痕.模具的型面边缘都应修磨圆角.一23—./,\f.L挤压前的弯头挤压后的弯头图2弯头挤压前后示意图R一一挤压前的弯曲半径r一一挤压后的弯曲半径X一一弯头起弯点位移量L一一弯头直段(2)精整模精整模采用上,下二片分开模具,每种管径或每种弯曲半径需要设计一套模具.图3下精整模精整模型腔直段直径Dl和弯头半径R1尺寸即挤压管子管径和弯头半径.直段长度L1 <L,当管子直段焊缝离管子弯头较近时,以免管子焊缝伸到模具里.型腔直段和弯头部分要圆滑过渡,过渡段长度KX=1.57(R—r)(见图2).在弯头预弯及弯头挤压过程中,弯头会发生拉伸减薄,型腔弯头部分直径D2 约为管径D一(1~2)mm.由于管子材质及弯管设备能力的不同,即使是相同弯管半径弯头在弯管过程中拉伸减薄也各有不同,因此在下精整模上可开一个l~2mm浅长方形浅槽,根据精整的实际情况可在槽中放入不同厚度的板, 增加上下精整模的间隙来调节上下模的型腔, 使精整弯头达到最好的成形效果(见图3).精整模型腔边缘采用倒角加倒圆的设计,以免弯头精整过程中模具在管子上造成切痕.(3)模具材料热挤压精整模具模腔直接接触高温管子,模腔受热温度较高,模具在高温条件下必须有良好得高温强度,较高的硬度和韧性以及良好的耐热疲劳性能根据以上要求,热挤压模具材料一般可选W18Cr4V和W6Mo5Cr4V2,其代用材料可用5CrMnMo或5CrNiMo.一般模具钢的淬火硬度可达HRC58~62,作为热模具钢,如果硬度太高,模具冷却时会引起表层炸裂,因此模具热处理后的硬度可以为HRC52~56,这样使用性能更好,寿命更长.4.结束语经过生产实践证明,小R挤压精整模具结构合理,操作简便,性能可靠.小R弯管挤压精整工艺能满足我公司小R弯头批量生产要求, 产品符合相关技术要求,质量稳定.一24—。
钢管弯曲工艺分析及模具设计

弯 曲件宽度 ( m m);
卜 _ _弯 曲材料 厚 度 ( r n m) ;
弯 曲件 内弯曲半径 ( m m);
— —
材料抗拉强度 ( MP a )。
将七 =1 . 3,6 =1 1 4 mm ,t = 5 mm,R= 3 4 3 mm ,
譬
7 9
WI V I  ̄ . I I I Ct OI WO f l C I N RI 9 .  ̄ o . c o m J
( 2 )钢管压模弯 曲力计算 弯 曲力计算是设计
弯 曲模 和 选择 压 力设 备 吨 位 的重 要 依据 。根据 弯 曲
压模最小壁厚及宽度设计。通过对钢管 受力分析计算 ,并考虑滚压模的经济性 ,最 弯管压模壁厚取1 0 am,宽度取2 r 8 0 mm。
应变分量 ( 见图2 ) ,一种应变状态只有一组主应
变。
一
点的应变状态也可分解成 两部 分 ,如 图3 所
示 。第一部分以平均应变 为各 向应变的三 向等 应变状态 E = ( +5 : +6 )/ 3 ,表示 了单元体 体积的变化 。第二部分是以各 向主变应与 的差 值为变应值构成的应变状态 ,表示了单元体形状的
( 1 )模具材料的基本要求 根据工作部分对模 具硬度的要求 ,硬度要达 ̄ I J 5 8  ̄ 6 4 HR C,具 有高耐 磨性 和足够 韧度 ,以及 良好 的使用性能和 工艺性
图 1
能 ,故该弯管压模选用Z G 3 1 0 —5 7 0 材质。
参磊 工 热 加 工 热
= 4 6 0 MP a 代入上式 ,计算得F 自 = 3 4 2 8 N,现车间
选用功率为4 0 k W 的 三辊 卷 板 机 进 行 滚 压 生 产 ,完 全能 满 足所 需 弯 曲力 的要 求 。
摩托车管件—模双腔弯曲工艺简介
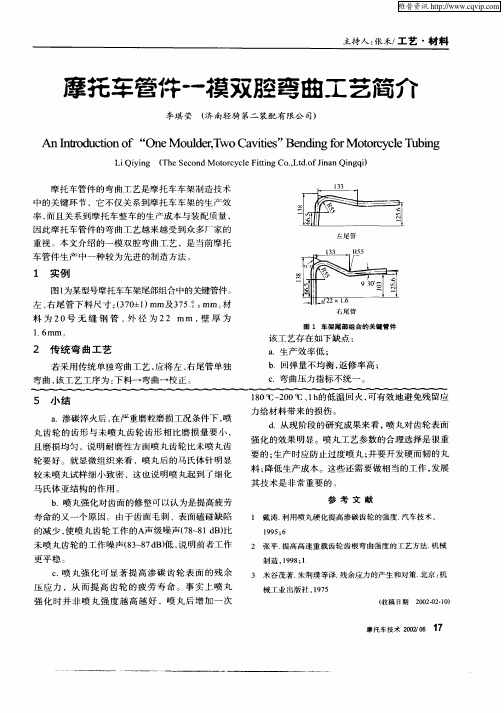
/
R变\ l变 j 不
考 虑 回弹
更平稳。
2 张平. 提高高速重载齿 轮齿 根弯曲强度的工艺方法. 机械
制 造 ,9 8 1 19 ;
C 喷 丸强化可显 著提高渗碳 齿轮表 面的残余 . 压 应力 .从 而提高齿 轮的疲劳 寿命 。事实 上喷丸
强 化 时 并 非 喷 丸 强 度 越 高 越 好 ,喷 丸后 增 加 一 次
定 回弹 余 量 。 实 例 根 据 实 践 确 定 的 回弹余 量 为 : 该 △ △ 2 , = 。 凸模 圆角 不变 , 。△ I, 值 凹模 圆角 R 值 取 下偏 差 一05 , . 。因该处 变 形剧 烈 , 回弹较 小 。 以右 尾 管 为例 , 弯 曲 回弹 分析 图 见 图3 其 。
该 工 艺存 在 如 下缺 点 : a .生 产 效率 低 ;
2 传统 弯 曲工艺
若 采 用 传统 单 独弯 曲工艺 , 将 左 、 应 右尾 管单 独 弯曲 . 该工 艺 工 序 为 : 料一 弯 曲一 校 正 。 下
b .回弹量 不 均衡 , 修 率 高 ; 返
C .弯 曲压力 指标 不 统 一 。 1 0 c 2 0 c、 h 8 ~ 0 l 的低 温 回火 , c c 可有 效地 避 免残 留应 力 给 材料 带 来 的损 伤 。 d .从 现 阶段 的研 究成 果 来 看 , 丸对 齿 轮表 面 喷
1 95; 9 6
b .喷丸强 化对 齿 面 的修 整可 以认 为是提 高疲 劳
寿命 的又 一个 原 因 。 由于 齿 面毛 刺 、表面磕 碰 缺 陷
的减少 , 喷 丸齿 轮 工 作 的A声级 噪 声(8 8 B I 使 7 - d )L 1  ̄ 未 喷 丸齿 轮 的工 作 噪声 (3 8 B 低 , 明前 者工 作 8~7 ) 说 d
- 1、下载文档前请自行甄别文档内容的完整性,平台不提供额外的编辑、内容补充、找答案等附加服务。
- 2、"仅部分预览"的文档,不可在线预览部分如存在完整性等问题,可反馈申请退款(可完整预览的文档不适用该条件!)。
- 3、如文档侵犯您的权益,请联系客服反馈,我们会尽快为您处理(人工客服工作时间:9:00-18:30)。
薄壁钢管弯曲模具设计(图)
弯管在制冷、机械、化工等行业中的应用十分广泛,薄壁钢管弯管的批量生产,一般是在弯管机上冷弯成形,由于薄壁钢管管壁支撑失稳临界力较低,弯曲部位常出现瘪皱等变形缺陷。
这些缺陷不但削弱钢管的强度,降低其承载能力,而且容易造成管内流动介质速度不均、产生涡流和弯曲部位积聚污垢等,影响弯管的正常使用,因此消除弯管缺陷成了弯管过程中最大难点,必须高度重视。
一、薄壁钢管弯曲受力与变形分析
薄壁钢管弯曲时,管子在外力作用下弯曲变形,其弯曲部分的外缘在拉应力作用下管壁变薄,而管子内缘在压应力作用下管壁增厚。
由于在管子弯曲过程中,外缘拉应力和内缘压应力的合力都向中部作用,导致管子弯曲部位在水平面上的直径变大,垂直面上的直径减小,出现椭圆形。
同时,如果弯曲模具弧槽参数选择不当,不能起到强化弯曲部位管壁的作用,则管子内缘在压应力作用下,因管壁失稳临界力较低而产生波浪形皱褶。
由以上分析可知:薄壁钢管弯曲时极易产生瘪皱缺陷。
因此设计薄壁钢管弯曲模具时,必须合理确定其结构参数,以便钢管弯曲时,在模具作用下使管子产生一预加反应力,以抵消薄壁钢管弯曲时产生的椭圆变形,对弯曲部位的瘪皱缺陷进行合理控制。
二、薄壁钢管弯曲模具设计
简易薄壁钢管弯管机的结构如图1所示,弯管模具如图2所示,由弯管模块、滚动压轮和导轮组成。
滚动压轮和导轮安装于滚轮座中,并可在转盘的滑槽中上下移动。
弯管时,扳动手柄带动转盘绕轴转动,由导轮向管子施加压力,使其发生弯曲变形。
同时滚动压轮在钢管弯曲部位施加一定压力,通过轮上弧槽使之产生一反向预压力,以抵消钢管弯曲时产生的椭圆变形,使管子内缘与弯管模块弧槽紧密贴合,以强化弯曲部位管壁,消除内壁皱褶。
1.弯曲模块
钢管弯曲后的半径和形状取决于弯管模块,因此,必须合理确定其结构参数,弯管模块如图3所示:
(1)弯管模块直径D由于外力取消后,被弯曲的钢管会产生回弹,所以弯管模块直径应小于两
倍的弯管曲率半径,数值按下面的经验公式计算
(2)圆弧槽半径r与倒圆半径r1因相对弯曲半径ε(ε=R0/d)的不同而有所不同,其目的是为了强化钢管弯曲部分管壁,避免皱褶,数值可按下式计算:
r=Kd/2,其中K为按相对弯曲半径ε大小确定的系数,当ε≥3.5时,K=1;当ε<3.5时,K=1-0.1/(10ε3)
倒圆半径r1可取1~2mm,ε小时,r1取小值。
当ε≥3.5,钢管直径d小时,r1取小值;钢管直径d大时,r1取大值。
(3)材料与表面粗糙度值选择弯管模块可选用45钢或50钢制造,直径较大时,也可选用
HT200制造。
为了给弯管内缘均匀压缩创造有利条件,弯管模块弧槽面表面粗糙度值取R a≤3.2μm为好。
2.滚动压轮
滚动压轮如图4所示,为防止弯曲过程中划伤钢管表面,需对弧槽边缘倒圆,一般取倒圆半径r1=0.5~1 mm,以不划伤钢管表面为宜。
导向轮如图5所示,为减小摩擦阻力,圆弧槽中心离开导轮外缘表面1~1.5mm,圆弧半径r=d/2,材料与热处理同滚动压轮。
4.滚动压轮与导轮相对位置
导向轮对钢管提前压弯角度α也是一个重要参数。
为使滚动压轮所处位置恰好是钢管弯曲塑性变形的受力部位,应使α等于被弯钢管的回弹角。
滚动压轮中心线与弯管模块中心线的距离δ可取5~15 mm。