机械类数控外文翻译外文文献英文文献数控.doc
机械设计及其自动化外文翻译数控机床
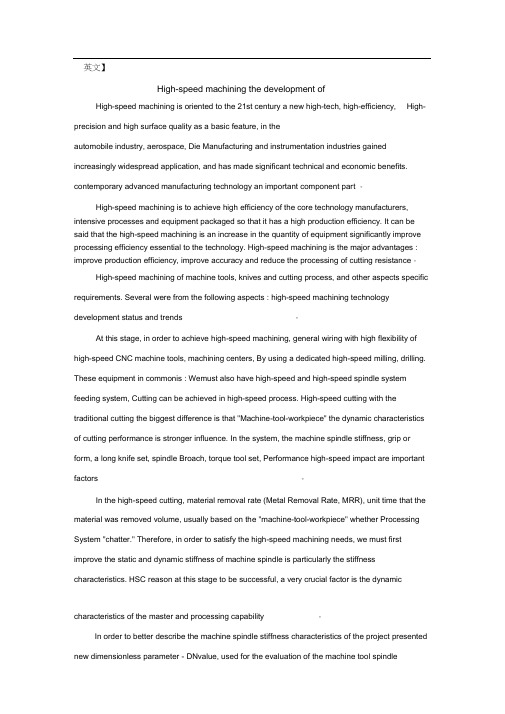
英文】High-speed machining the development ofHigh-speed machining is oriented to the 21st century a new high-tech, high-efficiency, High-precision and high surface quality as a basic feature, in theautomobile industry, aerospace, Die Manufacturing and instrumentation industries gained increasingly widespread application, and has made significant technical and economic benefits. contemporary advanced manufacturing technology an important component part 。
High-speed machining is to achieve high efficiency of the core technology manufacturers, intensive processes and equipment packaged so that it has a high production efficiency. It can be said that the high-speed machining is an increase in the quantity of equipment significantly improve processing efficiency essential to the technology. High-speed machining is the major advantages : improve production efficiency, improve accuracy and reduce the processing of cutting resistance。
机械数控专业--外文资料及翻译

外文资料及译文原文:Television Video SignalsAlthough over 50 years old , the standard television signal is still one of the most common way to transmit an image. Figure 8.3 shows how the television signal appears on an oscilloscope. This is called composite video, meaning that there are vertical and horizontal synchronization (sync) pulses mixed with the actual picture information.These pulses are used in the television receiver to synchronize the vertical and horizontal deflection circuits to match the video being displayed. Each second of standard video contains 30 complete images, commonly called frames , A video engineer would say that each frame contains 525 lines, the television jargon for what programmers call rows. This number is a little deceptive because only 480 to 486 of these lines contain video information; the remaining 39to 45 lines are reserved for sync pulses to keep the television’s circuits synchronized with the video signal.Standard television uses an interlaced format to reduce flicker in the displayed image. This means that all the odd lines of each frame are transmitted first, followed by the even lines. The group of odd lines is called the odd field, and the group of even lines is called the even field.Since each frame consists of two fields, the video signal transmits 60 fields per second. Each field starts with a complex series of vertical sync pulses lasting 1.3 milliseconds. This is followed by either the even or odd lines of video. Each line lasts for 63.5 microseconds, including a 10.2 microsecond horizontal sync pulse, separating one line from the next. Within each line, the analog voltage corresponds to the gray scale of the image, with brighter values being in the direction away from the sync pulses. This place the sync beyond the black range. In video jargon, the sync pulses are said to be blacker than black..The hardware used for analog-to-digital conversion of video signals is called a frame grabber. This is usually in the form of an electronics card that plugs into a computer, and connects to a camera through a coaxial cable. Upon command from software, the frame grabber waits for the beginning of the next frame, as indicated by the vertical sync pulses. During the following two fields,each line of video is sampled many times, typically 512,640 or 720 samples per line, at 8bits per sample. These samples are stored in memory as one row of the digital image.This way of acquiring a digital image results in an important difference between the vertical and horizontal directions. Each row in the digital image corresponds to one line in the video signal, and therefore to one row of wells in the CCD. Unfortunately, the columns are not so straightforward. In the CCD, each row contains between about 400 and800 wells (columns), depending on the particular device used. When a row of wells is read from the CCD, the resulting line of video is filtered into a smooth analog signal, such as in Figure 8.3. In other words, the video signal does not depend on how many columns are present in the CCD. The resolution in the horizontal direction is limited by how rapidly the analog signal is allowed to change. This is usually set at 3.2 MHz for color television, resulting in a rise time of about 100 nanoseconds, i.e, about 1/500th of the 53.2 microsecond video line.When the video signal is digitized in the frame grabber, it is converted back into columns, However, these columns in the digitized image have no relation to the columns in the CCD. The number of columns in the digital image depends solely on how many times the frame grabber samples each line of video. For example, a CCD might have 800 wells per row, while the digitized image might only have 512 pixels (i.e , columns) per row.The number of columns in the digitized image is also important for another reason. The standard television image has an aspect ratio of 4 to 3, i.e. , it is slightly wider than it is high. Motion pictures have the wider aspect ratio of 25 to 9. CCDs used for scientific applications often have an aspect ratio of 1 to 1, i.e , a perfect square. In any event, the aspect ratio of a CCD is fixed by the placement of the electrodes, and cannot be altered. However, the aspect ratio of the digitized image depends on thenumber of samples per line. This becomes a problem when the image is displayed, either on a video monitor or in a hardcopy. If the aspect ratio isn’t properly reproduced, the image looks squashed horizontally or vertically.The 525 line video signal described here is called NTSC (National Television Systems Committee), a standard defined way back in 1954. This is the system used in the United States and Japan. In Europe there are two similar standards called PAL (Phase Alternation by Line) and SECAM (Sequential Chrominance And Memory). The basic concepts are the same , just the numbers are different. Both PAL and SECAM operate with 25 interlaced frames per second, with 625 lines per frame. Just as with NTSC, some of these lines occur during the vertical sync, resulting in about 576 lines that carry picture information. Other more subtle differences relate to how color and sound are added to the signal.The most straightforward way of transmitting color television would be to have three separate analog signals, one for each of the three colors the human eye can detect: red, green and blue. Unfortunately, the historical development of television did not allow such a simple scheme. The color television signal was developed to allow existing black and white television sets to remain in use without modification. This was done by retaining the same signal for brightness information , but adding a separate signal for color information. In video jargon, the brightness iscalled the luminance signal, while the color is the chrominance signal. The chrominance signal is contained on a 3.58 MHz carrier wave added to the black and white video signal. Sound is added in this same way, on a 4.5 MHz carrier wave. The television receiver separates these three signals, processes them individually, and recombines them in the final diplay.译文:关键词:核心,合成信号,电压耦合电视信号尽管已经拥有50年的历史了,电视信号依然是常用的传递信息的途径之一。
机械类数控车床外文翻译外文文献英文文献数控
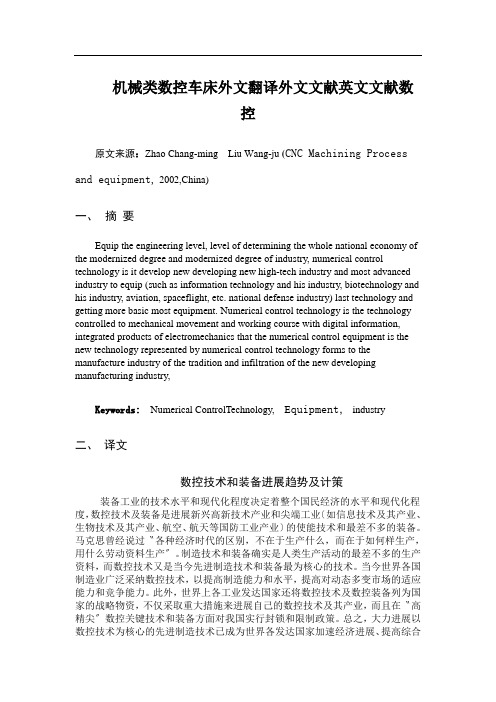
机械类数控车床外文翻译外文文献英文文献数控原文来源:Zhao Chang-ming Liu Wang-ju (CNC Machining Process and equipment, 2002,China)一、摘要Equip the engineering level, level of determining the whole national economy of the modernized degree and modernized degree of industry, numerical control technology is it develop new developing new high-tech industry and most advanced industry to equip (such as information technology and his industry, biotechnology and his industry, aviation, spaceflight, etc. national defense industry) last technology and getting more basic most equipment. Numerical control technology is the technology controlled to mechanical movement and working course with digital information, integrated products of electromechanics that the numerical control equipment is the new technology represented by numerical control technology forms to the manufacture industry of the tradition and infiltration of the new developing manufacturing industry,Keywords:Numerical ControlTechnology, E quipment,industry二、译文数控技术和装备进展趋势及计策装备工业的技术水平和现代化程度决定着整个国民经济的水平和现代化程度,数控技术及装备是进展新兴高新技术产业和尖端工业〔如信息技术及其产业、生物技术及其产业、航空、航天等国防工业产业〕的使能技术和最差不多的装备。
数控技术外文文献翻译

数控技术外文文献翻译(含:英文原文及中文译文)英文原文The development trend of numerical control technology AbstractThe current trends in the development of numerical control technology and equipment in the world and the status quo of the development and industrialization of CNC equipment technology in China are briefly introduced. On this basis, we discuss the development of CNC technology and equipment in China under the new environment of China's accession to the WTO and further opening to the outside world. The importance of improving the level of China's manufacturing informatization and international competitiveness, and put forward some views on the development of China's CNC technology and equipment from both strategic and strategic aspects.The technological level and degree of modernization of the equipment industry determine the level of the entire national economy and the degree of modernization. Numerical control technology and equipment are the development of emerging high-tech industries and cutting-edge industries (such as information technology and its industries, biotechnology and its industries, aviation, aerospace, etc.) (Defense Industry Industry) enabling technology and basic equipment. Marx oncesaid that “the difference between various economic times is no t what is produced but how it is produced and what labor data it is used to produce”. Manufacturing technology and equipment are the most basic production materials for human production activities, and numerical control technology is the core technology of today's advanced manufacturing technologies and equipment. In the manufacturing industry of the world today, CNC technology is widely used to improve manufacturing capabilities and levels, and to improve the adaptability and competitiveness of dynamic markets. In addition, various industrialized countries in the world have also listed numerical control technology and numerical control equipment as strategic materials of the country. They not only take significant measures to develop their own numerical control technologies and their industries, but also have the key technology and equipment of “high-precision” numerical control. Our country adopts a policy of blockade and restriction. In short, the vigorous development of advanced manufacturing technologies centered on numerical control technology has become an important way for all developed countries in the world to accelerate economic development and improve their overall national strength and national status.Numerical control technology is a technology that uses digital information to control mechanical movement and work process. Numerical control equipment is a mechatronic product formed by thepenetration of new technologies represented by numerical control technology into traditional manufacturing industries and emerging manufacturing industries, namely, so-called digital equipment. Its technical scope covers many fields: (1) machinery manufacturing technology; (2) information processing, processing, and transmission technology; (3) automatic control technology; (4) servo drive technology;(5) sensor technology; (6) software Technology and so on. Keywords: CNC technology, machinery manufacturing, information processing, sensors1 Development Trends of Numerical Control TechnologyThe application of numerical control technology has not only brought about revolutionary changes in the traditional manufacturing industry, but also made manufacturing a symbol of industrialization. With the continuous development of numerical control technology and the expansion of application fields, he has made important contributions to the national economy and people's livelihood (IT, automotive The development of light industry, light industry, medical care, etc. is playing an increasingly important role, because the digitalization of the equipment required by these industries is a major trend of modern development. From the current trend of numerical control technology and its equipment development in the world, its main research hotspots are the following aspects [1~4].1.1 New trends in high-speed, high-precision processing technology and equipmentEfficiency and quality are the mainstays of advanced manufacturing technology. High-speed, high-precision machining technology can greatly improve efficiency, improve product quality and grade, shorten production cycle and increase market competitiveness. To this end, the Japanese Advanced Technology Research Institute will list it as one of the five major modern manufacturing technologies. The International Association of Production Engineers (CIRP) has identified it as one of the central research directions for the 21st century.In the passenger car industry, the production cycle of 300,000 vehicles per year is 40 seconds per vehicle, and multi-species processing is one of the key issues that must be addressed for car equipment. In the aviation and aerospace industries, the parts processed by them are mostly thin-walled. With thin ribs, the rigidity is poor, and the material is aluminum or aluminum alloy. These ribs and walls can be processed only when the high cutting speed and cutting force are small. Recently, the method of “hollowing out” large-size aluminum alloy billets has been used to manufacture large parts such as wings and fuselage to replace multiple parts and assembled by numerous rivets, screws, and other coupling methods to obtain strength, stiffness, and reliability of components. improve. All of these require high-speed, high-precision andhigh-flexibility for processing equipment.From the standpoint of EMO2001, the feed rate of high-speed machining centers can reach 80m/min, or even higher, and the airspeed can reach around 100m/min. At present, many automobile plants in the world, including China's Shanghai General Motors Corporation, have adopted a part of the production line consisting of a high-speed machining center to replace the combined machine tools. The HyperMach machine tool feed rate of CINCINNATI, USA is up to 60m/min, the speed is 100m/min, the acceleration is 2g, and the spindle speed has reached 60,000r/min. It takes only 30 minutes to machine a thin-walled aircraft part, and the same part takes 3h for general high-speed milling and 8h for normal milling; the spindle speed and acceleration of the twin-spindle lathe of DMG, Germany, reach 12*!000r/mm respectively. And 1g.In terms of machining accuracy, in the past 10 years, the machining accuracy of ordinary CNC machine tools has increased from 10μm to 5μm, precision machining centers have increased from 3~5μm to 1~1.5μm, and ultra-precision machining precision has begun to enter the nanometer level. (0.01μm).In terms of reliability, the MTBF value of foreign numerical control devices has reached more than 6000 hours, and the MTBF value of the servo system has reached more than 30,000 hours, showing very highreliability.In order to achieve high-speed, high-precision machining, the supporting functional components such as electric spindles and linear motors have been rapidly developed and the application fields have been further expanded.1.2 Rapid development of 5-axis simultaneous machining and compound machiningThe use of 5-axis simultaneous machining of 3D surface parts allows cutting with the best geometry of the tool, resulting in not only a high degree of finish, but also a significant increase in efficiency. It is generally considered that the efficiency of a 5-axis machine tool can be equal to 2 3-axis linkage machines. Especially when using ultra-hard material milling tools such as cubic boron nitride for high-speed milling of hardened steel parts, 5-axis simultaneous machining can be compared with 3-axis linkage. Processing to play a higher efficiency. In the past, due to the complexity of the 5-axis linkage CNC system and the host machine structure, the price was several times higher than that of the 3-axis linkage CNC machine tool, and the programming technology was more difficult, which restricted the development of 5-axis linkage machine tools.At present, due to the emergence of electric spindles, the structure of the composite spindle head that realizes 5-axis simultaneous machining isgreatly simplified, its manufacturing difficulty and cost are greatly reduced, and the price gap of the numerical control system is reduced. As a result, the development of composite spindle head type 5-axis linkage machine tools and compound machine tools (including 5-sided machine tools) has been promoted.At the EMO2001 exhibition, the new 5-axis machine tool of Nippon Machine Tool Co., Ltd. adopts a compound spindle head, which can realize the processing of four vertical planes and processing at any angle, so that 5-sided machining and 5-axis machining can be realized on the same machine tool. It can realize the processing of inclined surface and inverted cone. Germany DMG company exhibited DMUV oution series machining center, which can be processed in five-face machining and five-axis linkage in a single clamping. It can be directly or indirectly controlled by CNC system control or CAD/CAM.1.3 Intelligentization, openness, and networking have become major trends in the development of modern digital control systemsThe 21st century CNC equipment will be a certain intelligent system. The intelligent content is included in all aspects of the CNC system: in order to pursue the processing efficiency and processing quality in the intelligent, such as the process of adaptive control, process parameters automatically Generated; To improve the driving performance and the use of convenient connection intelligent, such as feed-forward control,adaptive calculation of motor parameters, automatic identification load automatic selection model, self-tuning, etc.; simplify the programming, simplify the operation of intelligent, such as smart The automatic programming, intelligent man-machine interface, etc.; as well as the contents of intelligent diagnosis, intelligent monitoring, convenient system diagnosis and maintenance.In order to solve the problems of traditional CNC system closure and industrial application of CNC application software. At present, many countries have conducted research on open numerical control systems such as NGC of the United States, OSACA of the European Community, OSEC of Japan, and ONC of China. The openness of numerical control systems has become the future of CNC systems. The so-called open CNC system is the development of CNC system can be in a unified operating platform, for machine tool manufacturers and end users, by changing, adding or cutting structure objects (CNC function), to form a series, and can be convenient to the user's special The application and technology are integrated into the control system to quickly realize open numerical control systems of different varieties and different grades to form brand-name products with distinctive personality. At present, the architecture specification, communication specification, configuration specification, operation platform, numerical control system function library and numerical control system function software development toolof open CNC system are the core of current research.Networked CNC equipment is a new bright spot in the international well-known machine tool exposition in the past two years. The networking of CNC equipment will greatly satisfy the requirements of information integration for production lines, manufacturing systems, and manufacturing companies. It is also the basic unit for realizing new manufacturing models such as agile manufacturing, virtual enterprise, and global manufacturing. Some famous domestic and foreign CNC machine tools and numerical control system manufacturing companies have introduced relevant new concepts and prototypes in the past two years. For example, at the EMO 2001 exhibition, the “Cyber Production Center” exhibited by Japan's Mazak company Mazak Production Control Center (CPC); Okuma Machine Too l Company, Japan exhibited “ITplaza” (Information Technology Plaza, IT Plaza); Open Manufacturing Environment (Open Manufacturing Environment, OME), exhibited by Siemens, Germany Etc., reflecting the trend of the development of CNC machine tools to the direction of the network.1.4 Emphasizing the Establishment of New Technology Standards and Specifications1.4.1 About Design and Development of CNC SystemsAs mentioned above, the open CNC system has better versatility, flexibility, adaptability, and expandability. The United States, theEuropean Community, and Japan have implemented strategic development plans one after another, and have conducted the open architecture system specification (OMAC). , OSACA, OSEC) research and development, the world's three largest economies in the short term carried out almost the same set of scientific plans and norms, indicating that the arrival of a new revolution in digital technology. In 2000, China began to conduct research and development of the regulatory framework for China's ONC numerical control system.1.4.2 About CNC StandardsCNC standards are a trend in the development of manufacturing informatization. The information exchange in the 50 years since the birth of CNC technology was based on the ISO 6983 standard. That is how the G and M codes describe how to process. The essential feature is the processing-oriented process. Obviously, he has been unable to meet the high speed of modern CNC technology. The need for development. For this purpose, a new CNC system standard ISO14649 (STEP-NC) is being researched and developed internationally. Its purpose is to provide a uniform data model that can describe the entire life cycle of a product without relying on a neutral mechanism of a specific system. , in order to achieve the entire manufacturing process, and even the standardization of product information in various industrial fields. The emergence of STEP-NC may be a revolution in CNC technology. It will have aprofound impact on the development of CNC technology and even the entire manufacturing industry. First, STEP-NC proposes a brand-new manufacturing concept. In the traditional manufacturing concept, NC machining programs are concentrated on a single computer. Under the new standard, NC programs can be distributed on the Internet. This is the direction of open and networked CNC technology. Secondly, STEP-NC CNC system can also greatly reduce the processing drawings (about 75%), processing program preparation time (about 35%) and processing time (about 50%).At present, European and American countries attach great importance to the research of STEP-NC, and Europe has initiated STEP-NC's IMS plan ( Participation in this program comes from 20 CAD/CAM/CAPP/CNC users, vendors and academic institutions in Europe and Japan. STEPTools of the United States is the developer of global manufacturing data exchange software. He has developed a SuperModel for the information exchange of CNC machine tools. Its goal is to describe all machining processes with a unified specification. This new data exchange format has now been validated on prototype prototypes equipped with SIEMENS, FIDIA and European OSACA-NC numerical control systems.2 Basic Estimates of China's CNC Technology and Its Industrial DevelopmentCNC technology in China started in 1958. The development process in the past 50 years can be roughly divided into three stages: the first stage from 1958 to 1979, which is the closed development stage. At this stage, the development of numerical control technology is relatively slow due to the limitations of foreign technology and China's basic conditions. The second stage is the introduction of technology during the “sixth and fifth” periods of the country, the “seventh five-year plan” period, and the “eighth five-year plan period,”and it will be digested and absorbed to initially establish the stage of the national production system. At this stage, due to the reform and opening up and the country’s attention, as well as the improvement of the research and development environment an d the international environment, China’s CNC technology has made great progress in research, development, and localization of products. The third stage is the implementation of industrialization research in the later period of the "Eighth Five-Year Plan" and the "Ninth Five-Year Plan" period of the country, entering the stage of market competition. At this stage, the industrialization of domestically-manufactured CNC equipment has achieved its essenceSexual progress. At the end of the “Ninth Five-Year Plan” period, the domestic market share of domestic CNC machine tools reached 50%, and the number of domestically-manufactured numerical control systems (pervasive models) also reached 10%.Looking at the development process of CNC technology in China in the past 50 years, especially after four five-year plans, the overall results are as follows:a. It lays the foundation for the development of CNC technology and basically masters modern CNC technology. China has now basically mastered the basic technologies from numerical control systems, servo drives, numerical control mainframes, special planes and their accessories. Most of these technologies already have the basis for commercial development. Some technologies have been commercialized and industrialized.b. Initially formed a CNC industrial base. Based on the research results and the commercialization of some technologies, we have established numerical control system production plants such as Huazhong Numerical Control and Aerospace Numerical Control which have mass production capabilities. Lanzhou Electric Machinery Factory, Huazhong Numerical Control and a number of servo systems and servo motor manufacturers, as well as a number of CNC machine manufacturers such as Beijing No. 1 Machine Tool Plant and Jinan No. 1 Machine Tool Plant. These production plants have basically formed China's CNC industrial base.c. Established a basic team of CNC research, development and management talents.Although significant progress has been made in the research, development, and industrialization of numerical control technology, we must also soberly realize that the research and development of high-end numerical control technologies in China, especially the status quo of the technological level of industrialization and the actual needs of China There is a big gap. Although our country's development speed is very fast in the vertical direction, the horizontal ratio (compared with foreign countries) not only has a gap in the level of technology, but also has a gap in the development speed in certain aspects, that is, the gap in the technological level of some highly sophisticated numerical control equipment has expanded. From the international point of view, the estimated level of China's numerical control technology and industrialization is roughly as follows:a. On the technical level, it will be about 10 to 15 years behind the advanced level in foreign countries, and it will be even bigger in terms of sophisticated technology.b. At the industrialization level, the market share is low, the variety coverage is small, and scale production has not yet been established; the specialized production level of functional components and the complete set capacity are low; the appearance quality is relatively poor; the reliability is not high, and the degree of commercialization is insufficient; The domestic CNC system has not established its own brand effect, andthe user's confidence is insufficient.c. On the ability of sustainable development, the research and development and engineering capabilities of pre-competitive numerical control technology are weak; the application of numerical control technology is not strong; the research and formulation of related standard specifications is lagging behind.The main reasons for analyzing the above gaps are as follows:a. Awareness. Insufficient understanding of the arduous, complex and long-term characteristics of the domestic CNC industry process; Insufficient estimates of market irregularities, foreign blockades, killings, and systems; and insufficient analysis of the application level and capabilities of CNC technology in China.b. Systematic aspects. From the point of view of technology, attention has been paid to the issue of CNC industrialization. It has been a time to consider the issue of CNC industrialization from the perspectives of system and industry chain; there is no complete supporting system of high-quality supporting systems, perfect training, and service networks. .c. Mechanisms. Bad mechanisms have led to brain drain, which in turn has restricted technological and technological route innovations and product innovations, and has constrained the effective implementation of planning. It is often planned to be ideal and difficult to implement.d. Technical aspects. Enterprises have little ability to independentlyinnovate in technology, and the engineering ability of core technologies is not strong. The standard of machine tools is backward, the level is low, and the new standard of CNC system is not enough.3 Strategic Thinking on the Development of CNC Technology and Industrialization in China3.1 Strategic ConsiderationsChina is a manufacturing country, and we must try to accept the transfer of the front-end rather than the back-end in the industrial transfer of the world. That is to master the advanced manufacturing core technologies, otherwise, in the new round of international industrial restructuring, China's manufacturing industry will further “empty core”. At the expense of resources, the environment, and the market, we may obtain only the international "processing centers" and "assembly centers" in the world's new economic structure, rather than the status of manufacturing centers that master core technologies. This will seriously affect our country. The development of modern manufacturing.We should pay attention to numerical control technology and industrial issues from the perspective of national security strategy. First of all, we must look at social security because manufacturing industry is the industry with the largest number of employed people in China. Manufacturing industry development can not only improve the people’s living standards, but also ease the country’s The pressure of employmentguarantees social stability. Secondly, from the perspective of national defense security, Western developed countries classify high-precision numerical control products as national strategic materials and implement embargoes and restrictions on China. The “Toshiba Incident” and the “Cox Report” "This is the best illustration.3.2 Development StrategyFrom the perspective of China’s basic national conditions, taking the country’s strategic needs and the market demand of the national economy as the guide, and aiming at improving the comprehensive competitiveness and industrialization le vel of China’s manufacturing equipment industry, we can use systematic methods to choose to dominate the early 21st century in China. The key technologies for the development and upgrade of the manufacturing equipment industry and supporting technologies and supporting technologies for supporting industrialization development are the contents of research and development and the leap-forward development of the manufacturing equipment industry. Emphasizing the market demand as the orientation, that is, taking CNC terminal products as the mainstay, and driving the CNC industry with complete machines (such as large-scale CNC lathes, milling machines, high-speed, high-precision and high-performance CNC machine tools, typical digital machines, key equipment of key industries, etc.). development of. The focus is on the reliability and production scale of CNC systems andrelated functional components (digital servos and motors, high-speed spindle systems and accessories for new equipment, etc.). Without scale, there will be no high-reliability products; without scale, there will be no cheap and competitive products; of course, CNC equipment without scale in China will be difficult to come to the fore. In the research and development of high-precision equipment, we must emphasize the close integration of production, learning, research, and end-users, and aim at “doing, using, and selling off” as a goal, and implement national research on the will of the country to solve the urgent need of the country. . Before the competition, CNC technology emphasizes innovation, emphasizes research and development of technologies and products with independent intellectual property rights, and lays a foundation for the sustainable development of China's CNC industry, equipment manufacturing industry, and even the entire manufacturing industry.中文译文数控技术的发展趋势摘要本文简要介绍了当今世界数控技术及装备发展的趋势及我国数控装备技术发展和产业化的现状, 在此基础上讨论了在我国加入WTO 和对外开放进一步深化的新环境下, 发展我国数控技术及装备、提高我国制造业信息化水平和国际竞争能力的重要性, 并从战略和策略两个层面提出了发展我国数控技术及装备的几点看法。
数控车床主轴部件机械外文文献翻译、中英文翻译、外文翻译
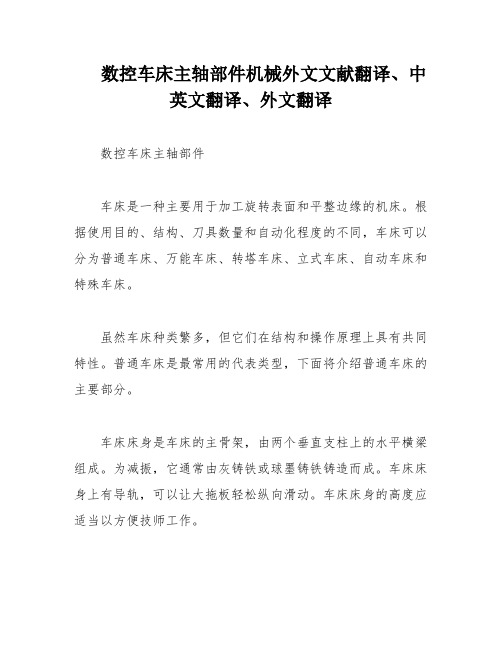
数控车床主轴部件机械外文文献翻译、中英文翻译、外文翻译数控车床主轴部件车床是一种主要用于加工旋转表面和平整边缘的机床。
根据使用目的、结构、刀具数量和自动化程度的不同,车床可以分为普通车床、万能车床、转塔车床、立式车床、自动车床和特殊车床。
虽然车床种类繁多,但它们在结构和操作原理上具有共同特性。
普通车床是最常用的代表类型,下面将介绍普通车床的主要部分。
车床床身是车床的主骨架,由两个垂直支柱上的水平横梁组成。
为减振,它通常由灰铸铁或球墨铸铁铸造而成。
车床床身上有导轨,可以让大拖板轻松纵向滑动。
车床床身的高度应适当以方便技师工作。
主轴箱固定在车床床身的左侧,包括轴线平行于导轨的主轴。
主轴通过齿轮箱驱动,齿轮箱可以提供多种不同的速度(通常是6到18速)。
现代车床有些采用无级调速主轴箱,采用摩擦、电力或液压驱动。
主轴往往是中空的,纵向有一通孔,可以通过此孔进给棒料。
同时,此孔为锥形表面,可以安装普通车床顶尖。
主轴外表面是螺纹,可以安装卡盘、花盘或类似的装置。
尾架总成包括底座、尾架体和套筒轴。
底座是能在车床床身上沿导轨滑动的铸件,有定位装置,可以让整个尾架根据工件长度锁定在任何需要位置。
使用手轮和螺杆,与螺杆啮合的是一固接在套筒轴上的螺母。
套筒轴开口端的孔是锥形的,能安装车床顶尖或诸如麻花钻和镗杆之类的工具。
套筒轴通过定位装置能沿着它的移动路径被锁定在任何点。
大拖板的主要功能是安装刀具和产生纵向和/或横向进给。
它实际上是一由车床床身V形导轨引导的、能在车床床身主轴箱和尾架之间滑动的H形滑块。
大拖板可以手动或通过溜板箱和光杆(进给杆)或丝杆(引导螺杆)机动。
本文介绍了在传统普通车床上进行的各种机加工作业。
但是,需要注意的是现代计算机数控车床具有更多的功能,并且可以进行其他操作,例如仿型。
圆柱面车削是所有车床操作中最简单也是最常见的。
工件旋转一整圈产生一个圆心落在车床主轴上的圆;由于刀具的轴向进给运动,这种动作重复许多次。
(数控加工)机械类数控外文翻译外文文献英文文献数控
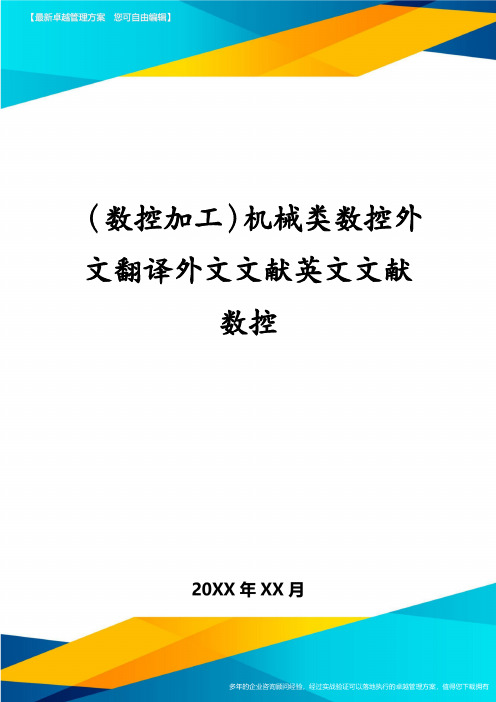
(数控加工)机械类数控外文翻译外文文献英文文献数控NumericalControlOneofthemostfundamentalconceptsintheareaofadvancedmanufacturingte chnologiesisnumericalcontrol(NC).PriortotheadventofNC,allmachinetools weremanualoperatedandcontrolled.Amongthemanylimitationsassociatedwith manualcontrolmachinetools,perhapsnoneismoreprominentthanthelimitation ofoperatorskills.Withmanualcontrol,thequalityoftheproductisdirectlyre latedtoandlimitedtotheskillsoftheoperator.Numericalcontrolrepresentst hefirstmajorstepawayfromhumancontrolofmachinetools.Numericalcontrolmeansthecontrolofmachinetoolsandothermanufacturin gsystemsthoughtheuseofprerecorded,writtensymbolicinstructions.Rathert hanoperatingamachinetool,anNCtechnicianwritesaprogramthatissuesoperat ionalinstructionstothemachinetool,Foramachinetooltobenumericallycontr olled,itmustbeinterfacedwithadeviceforacceptinganddecodingthep2ogramm edinstructions,knownasareader.Numericalcontrolwasdevelopedtoovercomethelimitationofhumanoperato r,andithasdoneso.Numericalcontrolmachinesaremoreaccuratethanmanuallyo peratedmachines,theycanproducepartsmoreuniformly,theyarefaster,andthe long-runtoolingcostsarelower.ThedevelopmentofNCledtothedevelopmentofs everalotherinnovationsinmanufacturingtechnology:1.Electricaldischargemachining.sercutting.3.Electronbeamwelding.Numericalcontrolhasalsomademachinetoolsmoreversatilethantheirmanuallyoperatedpredecessors.AnNCmachinetoolcanautomaticallyproduceawidev arietyofpar4s,eachinvolvinganassortmentofundertaketheproductionofprod uctsthatwouldnothavebeenfeasiblefromaneconomicperspectiveusingmanuall ycontrolledmachinetoolsandprocesses.Likesomanyadvancedtechnologies,NCwasborninthelaboratoriesoftheMas sachusettsInstituteofTechnology.TheconceptofNCwasdevelopedintheearly1 950swithfundingprovidedbytheU.SAirForce.Initsearlieststages,NCmachine swereabletomakestraightcutsefficientlyandeffectively.However,curvedpathswereaproblembecausethemachinetoolhadtobeprogra mmedtoundertakeaseriesofhorizontalandverticalstepstoproduceacurve.The shorteristhestraightlinesmakingupthestep,thesmootheris4hecurve.Eachli nesegmentinthestepshadtobecalculated.Thisproblemledtothedevelopmentin1959oftheAutomaticallyProgrammedT ools(APT)languageforNCthatusesstatementssimilartoEnglishlanguagetodef inethepartgeometry,describethecuttingtoolconfiguration,andspecifythen ecessarymotions.ThedevelopmentoftheAPTlanguagewasamajorstepforwardint hefurtherdevelopmentofNCtechnology.TheoriginalNCsystemwerevastlydiffe rentfromthoseusedpunchedpaper,whichwaslatertoreplacedbymagneticplasti ctape.Atapereaderwasusedtointerprettheinstructionswrittenonthetapefor themachine.Together,all/fthisrepresentedgiantstepforwardinthecontrolo fmachinetools.However,therewereanumberofproblemswithNCatthispointinit sdevelopment.Amajorproblemwasthefragilityofthepunchedpapertapemedium.Itwascomm onforthepapercontainingtheprogrammedinstructionstobreakortearduringam achiningprocess,Thisproblemwasexacerbatedbythefactthateachsuccessivet imeapartwasproducedonamachinetool,thepapertapecarryingtheprogrammedin structionshadtorerunthoughtthereader.Ifitwasnecessarytoproduce100copi esofagivenpart,itwasalsonecessarytorunthepapertapethoughtthereader100 separatetimes.Fragilepapertapessimplycouldnotwithstandtherigorsofshop floorenvironmentandthiskindofrepeateduse.Thisledtothedevelopmentofaspecialmagnetictape.Whereasthepapertape carriedtheprogrammedinstructionsasaseriesofholespunchedinthetape,theT hismostimportantofthesewasthatitwasdifficultorimpossibletochangethein structionsenteredonthetape.Tomakeeventhemostminoradjustmentsinaprogra mofinstructions,itwasnecessarytointerruptmachiningoperationsandmakean ewtape.Itwasalsostillnecessarytorunthetapethoughtthereaderasmanytimes astherewerepartstobeproduced.Fortunately,computertechnologybecomearea lityandsoonsolvedtheproblemsofNC,associatedwithpunchedpaperandplastic tape.Thedevelopmentofaconceptknownasnumericalcontrol(DNC)solvethepaper andplastictapeproblemsassociatedwithnumericalcontrolbysimplyeliminati ngtapeasthemediumforcarryingtheprogrammedinstructions.Indirectnumeric alcontrol,machinetoolsaretied,viaadatatransmissionlink,toahostcompute randfedtothemachinetoolasneededviathedatatransmissionlinkage.Directnumericalcontrolrepresentedamajorstepforwardoverpunchedtapeandplasticta pe.However,itissubjecttothesamelimitationasalltechnologiesthatdependo nahostcomputer.Whenthehostcomputergoesdown,themachinetoolsalsoexperie ncedowntime.Thisproblemledtothedevelopmentofcomputernumericalcontrol.Thedevelopmentofthemicroprocessorallowedforthedevelopmentofprogra mmablelogiccontrollers(PLC)andmicrocomputers.Thesetwotechnologiesallo wedforthedevelopmentofcomputernumericalcontrol(CNC).WithCNC,eachmachi netoolhasaPLCoramicrocomputerthatservesthesamepurpose.Thisallowsprogr Csolvedtheproblems associateddowntimeofthehostcomputer,butitintroducedanotherproblemknow nasdatamanagement.Thesameprogrammightbeloadedontendifferentmicrocompu terswithnocommunicationamongthem.Thisproblemisintheprocessofbeingsolv edbylocalareanetworksthatconnectDigitalSignalProcessorsTherearenumeroussituationswhereanalogsignalstobeprocessedinmanywa ys,likefilteringandspectralanalysis,Designinganaloghardwaretoperformt hesefunctionsispossiblebuthasbecomelessandpractical,duetoincreasedper formancerequirements,flexibilityneeds,andtheneedtocutdownondevelopmen t/testingtime.Itisinotherwordsdifficultpmdesignanaloghardwareanalysis ofsignals.Theactofsamplingansignalintothehatarespecialisedforembeddedsignal processingoperations,andsuchaprocessoriscalledaDSP,whichstandsforDigi talSignalProcessor.TodaytherearehundredsofDSPfamiliesfromasmanymanufacturers,eachonedesignedforaparticularprice/performance/usagegroup.Man yofthelargestmanufacturers,likeTexasInstrumentsandMotorola,offerboths pecialisedDSP’sforcertainfieldslikemotor-controlormodems,andgeneralh igh-performanceDSP’sthatcanperformbroadrangesofprocessingtasks.Devel opmentkitsan`softwarearealsoavailable,andtherearecompaniesmakingsoftw aredevelopmenttoolsforDSP’sthatallowstheprogrammertoimplementcomplex processingalgorithmsusingsimple“drag‘n’drop”methodologies.DSP’smoreorlessfallintotwocategoriesdependingontheunderlyingarch itecture-fixed-pointandfloating-point.Thefixed-pointdevicesgenerallyo perateon16-bitwords,whilethefloating-pointdevicesoperateon32-40bitsfl oating-pointwords.Needlesstosay,thefixed-pointdevicesaregenerallychea per.Anotherimportantarchitecturaldifferenceisthatfixed-pointprocessor stendtohaveanaccumulatorarchitecture,withonlyone“generalpurpose”reg ister,makingthemquitetrickytoprogramandmoreimportantly,makingC-compil ersinherentlyinefficient.Floating-pointDSP’sbehavemorelikecommongene ral-purposeCPU’s,withregister-files.TherearethousandsofdifferentDSP’sonthemarket,anditisdifficulttas kfindingthemostsuitableDSPforaproject.Thebestwayisprobablytosetupacon straintandwishlist,andtrytocomparetheprocessorsfromthebiggestmanufact urersagainstit.The“bigfour”manufacturersofDSPs:TexasInstruments,Motorola,AT&Ta ndAnalogDevices.Digital-to-analogconversionInthecaseofMPEG-Audiodecoding,digitalcompresseddataisfedintotheDS Pwhichperformsthedecoding,thenthedecodedsampleshavetobeconvertedbacki ntotheanalogdomain,andtheresultingsignalfedanamplifierorsimilaraudioe quipment.Thisdigitaltoanalogconversion(DCA)isperformedbyacircuitwitht hesamename&DifferentDCA’sprovidedifferentperformanceandquality,asmea suredbyTHD(Totalharmonicdistortion),numberofbits,linearity,speed,filt ercharacteristicsandotherthings.TheTMS320familyDQPofTexasInstrumentsTheTLS320familyconsistsoffixed-point,floating-point,multiprocesso rdigitalsignalprocessors(D[Ps),andfoxed-pointDSPcontrollers.TMS320DSP haveanarchitecturedesignedspecificallyforreal-timesignalprocessing.Th e’F/C240isanumberofthe’C2000DSPplatform,andisoptimizedforcontrolapp lications.The’C24xseriesofDSPcontrollerscombinesthisreal-timeprocess ingcapabilitywithcontrollerperipheralstocreateanidealsolutionforcontr olsystemapplications.ThefollowingcharacteristicsmaketheTMS320familyth erightchoiceforawiderangeofprocessingapplications:---Veryflexibleinstructionset---Inherentoperationalflexibility---High-speedperformance---Innovativeparallelarchitecture---CosteffectivenessDeviceswithinagenerationoftheTMS320familyhavethesameCPUstructure butdifferenton-chipmemoryandperipheralconfigurations.Spin-offdevicesu senewcombinationsofOn-chipmemoryandperipheralstosatisfyawiderangeofne edsintheworldwideelectronicsmarket.Byintegratingmemoryandperipheralso ntoasinglechip,TMS320devicesreducesystemcostsandsavecircuitboardspace .The16-bit,fixed-pointDSPcoreofthe‘C24xdevicesprovidesanalogdesi gnersadigitalsolutionthatdoesnotsacrificetheprecisionandperformanceof theirsystemperformancecanbeenhancedthroughtheuseofadvancedcontrolalgo rithmsfortechniquessuchasadaptivecontrol,Kalmanfiltering,andstatecont rol.The‘C24xDSPcontrollerofferreliabilityandprogrammability.Analogco ntrolsystems,ontheotherhand,arehardwiredsolutionsandcanexperienceperf ormancedegradationduetoaging,componenttolerance,anddrift.Thehigh-speedcentralprocessingunit(CPU)allowsthedigitaldesignert oprocessalgorithmsinrealtimeratherthanapproximateresultswithlook-upta bles.TheinstructionsetoftheseDSPcontrollers,whichincorporatesbothsign alprocessinginstructionsandgeneral-purposecontrolfunctions,coupledwit htheextensivedevelopmenttimeandprovidesthesameeaseofuseastraditional8 -and16-bitmicrocontrollers.Theinstructionsetalsoallowsyoutoretainyour softwareinvestmentwhenmovingfromothergeneral-purpose‘C2xxgeneration, sourcecodecompatiblewiththe’C2xgeneration,andupwardlysourcecodecompa tiblewiththe‘C5xgenerationofDSPsfromTexasInstruments.The‘C24xarchitectureisalsowell-suitedforprocessingcontrolsignal s.Itusesa16-bitwordlengthalongwith32-bitregistersforstoringintermedia teresults,andhastwohardwareshiftersavailabletoscalenumbersindependent lyoftheCPU.Thiscombinationminimizesquantizationandtruncationerrors,an dincreasesp2ocessingpowerforadditionalfunctions.Suchfunctionsmightinc ludeanotchfilterthatcouldcancelmechanicalresonancesinasystemoranestim ationtechniquethatcouldeliminatestatesensorsinasystem.The‘C24xDSPcontrollerstakeadvantageofansetofperipheralfunctions thatallowTexasInstrumentstoquicklyconfigurevariousseriesmembersfordif ferentprice/performancepointsorforapplicationoptimization.Thislibraryofbothdigitalandmixed-signalperipheralsincludes:---Timers---Serialcommunicationsports(SCI,SPI)---Analog-to-digitalconverters(ADC)---Eventmanager---Systemprotection,suchaslow-voltageandwatchdogtimerTheDSPcontrollerperipherallibraryiscontinuallygrowingandchanging tosuittheoftomorrow’sembeddedcontrolmarketplace.TheTMS320F/C240isthefirststandarddeviceintroducedinthe‘24xserie sofDSPcontrollers.Itsetsthestandardforasingle-chipdigitalmotorcontrol ler.The‘240canexecute20MIPS.Almostallinstructionsareexecutedinasimpl ecycleof50ns.Thishighperformanceallowsreal-timeexecutionofverycomple8controlalgorithms,suchasadaptivecontrolandKalmanfilters.Veryhighsampl ingratescanalsobeusedtominimizeloopdelays.The‘240hasthearchitecturalfeaturesnecessaryforhigh-speedsignalp rocessinganddigitalcontrolfunctions,andithastheperipheralsneededtopro videasingle-chipsolutionformotorcontrolapplications.The‘240ismanufac turedusingsubmicronCMOStechnology,achievingalogpowerdissipationrating.A lsoincludedareseveralpower-downmodesforfurtherpowersavings.Someapplic ationsthatbenefitfromtheadvancedprocessingpowerofthe‘240include: ---Industrialmotordrives---Powerinvertersandcontrollers---Automotivesystems,suchaselectronicpowersteering,antilockbrake s,andclimatecontrol---ApplianceandHVACblower/compressormotorcontrols---Printers,copiers,andotherofficeproducts---Tapedrives,magneticopticaldrives,andothermassstorageproducts---RoboticandCNCmillingmachinesTofunctionasasystemmanager,aDSPmusthaverobuston-chipI/Oandotherp eripherals.Theeventmanagerofthe‘240isunlikeanyotheravailableonaDSP.T hisapplication-optimizedperipheralunit,coupledwiththehighperformanceD SPcore,enablestheuseofadvancedcontroltechniquesforhigh-precisionandhi gh-efficiencyfullvariable-speedcontrolofallmotortypes.Includeintheeve ntmanagerarespecialpulse-widthmodulation(PWM)generationfunctions,suchasaprogrammabledead-bandfunctionandaspacevectorPWMstatemachinefor3-ph asemotorsthatprovidesstate-of-the-artmaximumefficiencyintheswitchingo fpowertransistors.Thereindependentupdowntimers,eachwithit’sowncompareregister,sup portthegenerationofasymmetric(noncentered)aswellassymmetric(centered) PWMwaveforms.Open-LoopandClosed-LoopControlOpen-loopControlSystemsThewordautomaticimpliesthatthereisacertainamountofsophistication inthecontrolsystem.Byautomatic,itgenerallymeansThatthesystemisusually capableofadaptingtoavarietyofoperatingconditionsandisabletorespondtoa classofinputssatisfactorily.However,notanytypeofcontrolsystemhastheau ually,theautomaticfeatureisachievedbyfeed.gthefeedbackstructure,itiscalledanopen-loopsystem,whichisthesimp lestandmosteconomicaltypeofcontrolsystem.inaccuracyliesinthefactthato nemaynotknowtheexactcharacteristicsofthefurther,whichhasadefinitebear ingontheindoortemperature.Thisalcopointstoanimportantdisadvantageofth eperformanceofanopen-loopcontrolsystem,inthatthesystemisnotcapableofa daptingtovariationsinenvironmentalconitionsortoexternaldisturbances.I nthecaseofthefurnacecontrol,perhapsanexperiencedpersoncanprovidecontr olforacertaindesiredtemperatureinthehouse;butidthedoorsorwindowsareop enedorclosedintermittentlyduringtheoperatingperiod,thefinaltemperatureinsidethehousewillnotbeaccuratelyregulatedbytheopen-loopcontrol.Anelectricwashingmachineisanothertypicalexampleofanopen-loopsyst em,becausetheamountofwashtimeisentirelydeterminedbythejudgmentandesti mationofthehumanoperator.Atrueautomaticelectricwashingmachineshouldha vethemeansofcheckingthecleanlinessoftheclothescontinuouslyandturnitse dtoffwhenthedesireddegisedofcleanlinessisreached.Closed-LoopControlSystemsWhatismissingintheopen-loopcontrolsystemformoreaccurateandmoread aptablecontrolisalinkorfeedbackfromtheoutputtotheinputofthesystem.Ino rdertoobtainmoreaccuratebontrol,thecontrolledsignalc(t)mustbefedbacka ndcomparedwiththereferenceinput,andanactuatingsignalproportionaltothe differenceoftheoutputandtheinputmustbesentthroughthesystemtocorrectth eerror.Asystemwithoneormorefeedbackpat(slikethatjustdescribediscalled aclosed-loopsystem.humanbeingareprobablythemostcomplexandsophisticate dfeedbackcontrolsysteminexistence.Ahumanbeingmaybeconsideredtobeacont rolsystemwithmanyinputsandoutputs,capableofcarryingouthighlycomplexop erations.Toillustratethehumanbeingasafeedbackcontrolsystem,letusconsidert hattheobjectiveistoreachforanobjectonaperformthetask.Theeyesserveasas ensingdevicewhichfeedsbackcontinuouslythepositionofthehand.Thedistanc ebetweenthehandandtheobjectistheerror,whichiseventuallybroughttozeroa sthehandreachertheobject.Thisisatypicalexampleofclosed-loopcontrol.However,ifoneistoldtoreachfortheobjectandthenisblindolded,onecanonlyrea chtowardtheobjectbyestimatingitsexactposition.ItisAsantherillustrativ eexampleofaclosed-loopcontrolsystem,showstheblockdiagramoftherudderco ntrolsystemofThebasicalementsandtheblocadiagramofaclosed-loopcontrols ystemareshowninfig.Ingeneral,theconfigurationofafeedbackcontrolsystem maynotbeconstrainedtothatoffig&.Incomplexsystemstheremaybemultitudeof feedbackloopsandelementblocks.数控在先进制造技术领域最根本的观念之壹是数控(NC)。
数控机床的组成部分外文翻译、中英文翻译、外文文献翻译
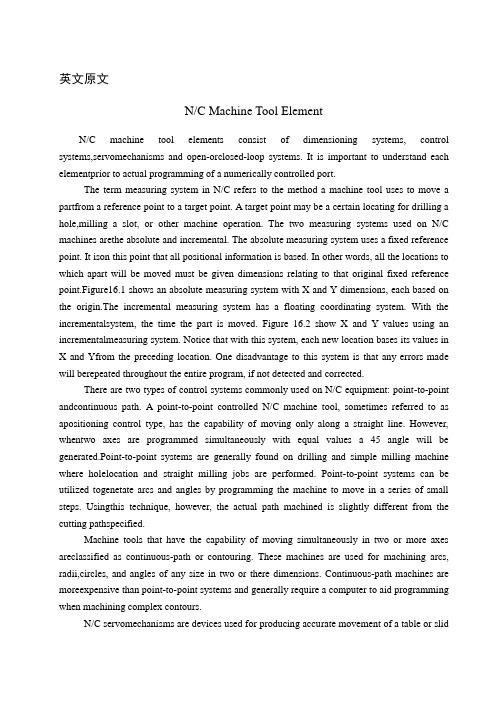
英文原文N/C Machine Tool ElementN/C machine tool elements consist of dimensioning systems, control systems,servomechanisms and open-orclosed-loop systems. It is important to understand each elementprior to actual programming of a numerically controlled port.The term measuring system in N/C refers to the method a machine tool uses to move a partfrom a reference point to a target point. A target point may be a certain locating for drilling a hole,milling a slot, or other machine operation. The two measuring systems used on N/C machines arethe absolute and incremental. The absolute measuring system uses a fixed reference point. It ison this point that all positional information is based. In other words, all the locations to which apart will be moved must be given dimensions relating to that original fixed reference point.Figure16.1 shows an absolute measuring system with X and Y dimensions, each based on the origin.The incremental measuring system has a floating coordinating system. With the incrementalsystem, the time the part is moved. Figure 16.2 show X and Y values using an incrementalmeasuring system. Notice that with this system, each new location bases its values in X and Yfrom the preceding location. One disadvantage to this system is that any errors made will berepeated throughout the entire program, if not detected and corrected.There are two types of control systems commonly used on N/C equipment: point-to-point andcontinuous path. A point-to-point controlled N/C machine tool, sometimes referred to as apositioning control type, has the capability of moving only along a straight line. However, whentwo axes are programmed simultaneously with equal values a 45 angle will be generated.Point-to-point systems are generally found on drilling and simple milling machine where holelocation and straight milling jobs are performed. Point-to-point systems can be utilized togenetate arcs and angles by programming the machine to move in a series of small steps. Usingthis technique, however, the actual path machined is slightly different from the cutting pathspecified.Machine tools that have the capability of moving simultaneously in two or more axes areclassified as continuous-path or contouring. These machines are used for machining arcs, radii,circles, and angles of any size in two or there dimensions. Continuous-path machines are moreexpensive than point-to-point systems and generally require a computer to aid programming when machining complex contours.N/C servomechanisms are devices used for producing accurate movement of a table or slidalong an axis. Two types of servos are commonly used on N/C equipment: electric stepping motors and hydraulic motors. Stepping motor servos are frequently used on less expensive N/C equipment. These motors are generally high-torque power servos and mounted directly to a lead screw of a table or tool slide. Most stepping motors are actuated by magnetic pulses from the stator and rotor assemblies. The net result of this action is that one rotation of the motor shaft produces 200 steps. Connection the motor shaft to a 10-pitch lead screw allows 0.0005-in. movements to be made. Hydraulic servos produce a fluid pressure that flows through gears or pistons to effect shaft rotation. Mechanical motion of lead screws and slides is accomplished through various values and controls from these hydraulic motors. However, they are more expensive and noisy. Most larger N/C machines use hydraulic servos.N/C machines that use an open-loop system contain no-feedback signal to ensure that a machine axis has traveled the required distance. That is, if the input received was to move a particular table axis 1.000 in, the servo unit generally moves the table 1.000 in. There is no means for comparing the actual table movement with the input signal, however, The only assurance that the table has actually moved 1.000 in. is the reliability of the servo system used.Open-loop systems are, of course, less expensive than closed-loop systems. A closed-loop system compares the actual output with the input signal and compensates for any errors. A feedback unit actually compares the amount the table has been moved with the input signal. Some feedback units used on closed-loop systems are transducers, electrical or magnetic scales, and synchros. Closed-loop systems greatly increase the reliability of N/C machines. Machining CentersMany of today’s more sophisticated lathes are called machining centers since they are capable of performing, in addition to the normal turning operations, certain milling and drilling operations. Basically, a machining center can be thought of as being a combination turret lathe and milling machine. Additional features are sometimes included by manufacturers to increase the versatility of their machines.Numerical ControlOne of the most fundamental concepts in the area of advanced manufacturing technologies is numerical control (NC). Prior to the advent of NC, all machine tools were manually operated and controlled .Among the many limitations associated with manual control machine tools, perhaps none is more prominent than the limitation of operator skills. With manual control, the quality of the product is directly related to and limited to the skills of the operator. Numerical control represents the first major step away from human control of machine tools.Numerical control means the control of machine tools and other manufacturing systems through the use of prerecorded, written symbolic instructions. Rather than operating a machine tool, an NC technician writes a program that issues operational instructions to the machine tool. For a machine tool to be numerically controlled, it must be interfaced with a device for accepting and decoding the programmed instructions, known as a reader.Numerical control was developed to overcome the limitation of human operators, and it has done so. Numerical control machines are more accurate than manually operated machines, they can produce parts more uniformly, they are faster, and the long-run tooling costs are lower. The development of NC led to the development of several other innovations in manufacturing technology:1. Electrical discharge machining.2. Laser cutting.3. Electron beam welding.Numerical control has also made machine tools more versatile than their manually operated predecessors. An NC machine tool can automatically produce a wide variety of parts, each involving an assortment of widely varied and complex machining processes. Numerical control has allowed manufacturers to undertake the production of products that would not have been feasible from an economic perspective using manually controlled machine tools and processes. Like so many advanced technologies, NC was born in the laboratories of the Massachusetts Institute of Technology. The concept of NC was developed in the early 1950s with funding provided by the U. S. Air force. In its earliest stages, NC machines were able to make straight cuts efficiently and effectively.However, curved paths were a problem because the machine tool had to be programmed to undertake a series of horizontal and vertical steps to produce a curve. The shorter is the straight lines making up the steps, the smoother is the curve. Each line segment in the steps had to be calculated.This problem led to the development in 1959 of the Automatically Programmed Tools (APT) language. This is a special programming language for NC that uses statements similar to English language to define the part geometry, describe the cutting tool configuration, and specify the necessary motions. The development of the APT language was a major step forward in the further development of NC technology. The original NC systems were vastly different from those used today. The machines had hardwired logic circuits. The instructional programs were written on punched paper, which was later to be replaced by magnetic plastic tape. A tape reader was used to interpret the instructions written on the tape for the machine. Together, all of this represented a giant step forward in the control of machine tools. However, there were a numberof problems with NC at this point in its development.A major problem was the fragility of the punched paper tape medium. It was common for the paper tape containing the programmed instructions to break or tear during a machining process. This problem was exacerbated by the fact that each successive time a part was produced on a machine tool, the paper tape carrying the programmed instructions had to be rerun through the reader. If it was necessary to produce 100 copies of a given part, it was also necessary to run the paper tape through the reader 100 separate times. Fragile paper tapes simply could not withstand the rigors of a shop floor environment and this kind of repeated use.This led to the development of a special magnetic plastic tape. Whereas the paper tape carried the programmed instructions as a series of holes punched in the tape, the plastic tape carried the instructions as a series of holes punched in the tape, the plastic tape carried the instructions as a series of magnetic dots. The plastic tape was much stronger than the paper taps, which solved the problem of frequent tearing and breakage. However, it still left two other problems.The most important of these was that it was difficult or impossible to change the instructions entered on the tape. To make even the most minor adjustments in a program of instructions, it was necessary to interrupt machining operations and make a new tape .It was also still necessary to run the tape through the reader as many times as there were parts to be produced. Fortunately, computer technology became a reality and soon solved the problems of NC associated with punched paper and plastic tape.The development of a concept known as direct numerical control (DNC) solved the paper and plastic tape problems associated with numerical control by simply eliminating tape as the medium for carrying the programmed instructions. In direct numerical control .machine tools are tied, via a data transmission link, to a host computer. Programs for operating the machine tools are stored in the host computer and fed to the machine tool as needed via the data transmission linkage. Direct numerical control represented a major step forward over punched tape and plastic tape. However, it is subject to the same limitations as all technologies that depend on a host computer. When the lost computer goes down, the machine tools also experience downtime. This problem led to the development of computer numerical control.The development of the microprocessor allowed for the development of programmable logic controllers (PLCs) and microcomputers. These two technologies allowed for the development of computer numerical control (CNC).With CNC, each machine tool has a PLC or a microcomputer that serves the same purpose. This allows programs to be input and stored at each individual machine tool. It also allows programs to be developed off-line and downloaded at the individual machine tool. CNC solved the problems associated with downtime of the hostcomputer, but it introduced another known as data management. The same program might be loaded on ten different microcomputers with no communication among them. This problem is in the process of being solved by local area networks that connect microcomputers for better data management.Cutting Tool GeometryShape of cutting tools, particularly the angles, and tool material are very important factors. Angles determine greatly not only tool life but finish quality as well. General principles upon which cutting tool angles are based do not depend on the particular tool, Basically, the same considerations hold true whether a lathe tool, a milling cutter, a drill, or even a grinding wheel are being designed. Since, however the lathe tool, depicted in Fig. 18.1, might be easiest to visualize, its geometry is discussed.Tool features have been identified by many names. The technical literature is full of confusing terminology. Thus in the attempt to cleat up existing disorganized conceptions and nomenclature, this American Society of Mechanical Engineers published ASA Standard B5-22-1950. What follows is based on it.A single-point tool is a cutting tool having one face and one continuous cutting edge, Tool angles identified in Fig. 18.2 are as follows:Tool angle 1, on front view, is the back-rank angle. It is the angle between the tool face and a line parallel to the tool base of the shank in a longitudinal plane perpendicular to the tool base. When this angle is downward from front to rear of the cutting edge, the rake is positive; when upward from front to black, the rake is negative. This angle is most significant in the machining process, because it directly affects the cutting force, finish, and tool life.The side-rake angle, numbered 2, measures the slope of the face on a cross plane perpendicular to the tool base. It, also, is an important angle, because it directs chip flow to the side of the tool post and permits the tool to feed more easily into the work.The end-relief angle is measured between a line perpendicular to the base and the end flank immediately below the end cutting edge; it is numbered 3 in the figure. It provides clearance between work and tool so that its cut surface can flow by with minimum rubbing against the tool. To save time, a portion of the end flank of the tool may sometimes be lest unground, having been previously forged to size. In such case, this end-clearance angle, numbered 4, measured to the end flank surface below the ground portion, would be larger than the relief angle.Often the end cutting edge is oblique to the flank. The relief angle is then best measured in a plane normal to the end cutting edge angle. Relief is also expressed as viewed from side andend of the tool.The side-relief angle, indicated as 5, is measured between the side flank, just below the cutting edge, and a line through the cutting edge perpendicular to the base of the tool. This clearance permits the tool to advance more smoothly into the work.Angle 6 is the end-cutting-edge angle measured between the end cutting edge and a line perpendicular to the side of the tool shank. This angle prevents rubbing of the cut surface and permits longer tool file.The side-cutting-edge angle, numbered 7, is the angle between the side cutting edge and the side of the tool shank. The true length of cut is along this edge. Thus the angel determines the distribution of the cutting forces. The greater the angle, the longer the tool life; but the possibility of charter increases. A compromise must, as usual, be reached.The nose angle, number 8, is the angle between the two component cutting edges. If the corner is rounded off, the arc size is defined by the nose radius 9. The radius size influences finish and chatter.Sand CastingThe first stage in the production of sand castings must be the design and manufacture of a suitable pattern. Casting patterns are generally made from hard word and the pattern has to be made larger than the finished casting size to allow for the shrinkage that takes place during solidification and cooling. The extent of this shrinkage varies with the type of metal or alloy to be cast. For all but the simplest shapes the pattern will be made in two or more pieces to facilitate moulding. If a hollow casting is to be made the pattern design will include extension pieces so that spaces to accept the sand core are moulded into sand. These additional spaces in the mould are termed core prints.Sand moulds for the production of small and medium-sized castings are made in a moulding box. The mould is made in two or more parts in order that the pattern may be removed.The drag half of the mould box is placed on a flat firm board and the drag half of the pattern placed in position. Facing sand is sprinkled over the pattern and then the mould box is filled with moulding sand. The sand is rammed firmly around the pattern. This process of filling and ramming may be done by hand but mould production is automated in a large foundry with the mould boxes moving along a conveyor, firstly to be filled with sand from hoppers and then to pass under mechanical hammers for ramming. When ramming of the sand is complete, excess sand is removed to leave a smooth surface flush with the edges of the moulding box.The completed drag is now turned over and the upper, or cope, portion of the moulding box positioned over it. The cope half of the pattern is placed in position, correct alignment beingensured by means of small dowel pins. Patterns for the necessary feeder, runner and risers are also placed so as to give an even distribution of metal into the mould cavity. The risers should coincide with the highest readily escape from the mould. The sizes of risers should be such that the metal in them does not freeze too rapidly. An important function of a riser is to act as reservoir of liquid metal to feed solidification within the mould. A thin coating of dry parting sand is sprinkled into mould at this stage. This is to prevent the cope and drag sticking together when the cope half is moulded. The cope is now filled with moulding sand and this is rammed firmly into shape in the same manner as in the making of the drag.After the ramming of sand in the cope is completed the two halves of the moulding box are carefully separated. At this stage venting of the moulding box are carefully separated. At this stage venting of the mould can be done, if necessary, to increase the permeability of the mould. After venting the patterns are carefully removed from both cope and drag, and a gate or gates are carefully cut to connect the runner channel with the main cavity. Gates should be sited to allow or entry into mould with a minimum of turbulence. Any loose sand is gently blown away and if a core is to be used it the cope upon the drag and it is then ready for use. Liquid metal is poured smoothly into the mould via the feeder. Pouring ceases when liquid metal appears at the top of the risers and the feeder channel is also full.When the metal that has been poured into a sand mould has fully solidified the mould is broken and casting is removed. The casting still has the runner and risers attached to it and there will be sand adhering to portions of the surface. Runners and risers are cut off and returned to the melting furnace. Sand cores are broken and adherent sand is cleaned from the surface by vibration or by sand blasting with dry sand. Any fins or metal flash formed at mould parting lines are removed by grinding and the castings are then ready for inspection.The main Elements of Horizontal Milling MachinesColumn and baseThe column and base form the foundation of the complete machine. Both are made from cast iron, designed with thick sections to ensure complete rigidity and freedom form vibration. The base, upon which the column is mounted, is also the cutting-fluid reservoir and contains the pump to circulate the fluid to cutting area.The column contains the spindle, accurately located in precision bearings. The spindle id driven through a gearbox from a vee-belt drive from the electric motor housed at the base of column. The gearbox enables a range of spindle speeds to be selected. In the model shown, twelve spindle speeds from 32 to 1400rev/min are available. The front of column carries the guideways upon which the knee is located and guided in a vertical direction.KneeThe knee, mounted on the column guideways, provides the vertical movement of the table. Power feed is available, through a gearbox mounted on the side, from a separate built-in motor, providing a range of twelve feed rates from 12 to 250mm/min. Drive is through a leadscrew, whose bottom end is fixed to machine base. Provision is made to raise and lower the knee by hand through a leadscrew and nut operates by a handwheel at the front. The knee has guideways on its top surface giving full-width support to the saddle and guiding it in a transverse direction. lock is provided to clamp the knee in any vertical position on the column.SaddleThe saddle, mounted on the knee guideways, providers the transverse movement of the table. Power feed is provided through the gearbox on the knee. A range of twelve feeds is available, from 12 to 500mm/min. Alternative hand movement is provided through a leadscrew and nut by a hand heel at the front of the knee.Camping of saddle to the knee is achieved by two clamps on the side of the saddle.The saddle has dovetail gun its upper surface, at right angles to the knee guideways, to provide a guide to the table in a longitudinal direction.TableThe table provides the surface upon which all workpieces and workholding equipment are located and clamped. A series of tee slots is provided for this purpose. The dovetail guides on undersurface locate in the guideways on the saddle, giving straight-line movement to the table in longitudinal direction at right angles to the saddle movement.Power feed is provided from the knee gearbox, through the saddle, to the table leadscrew. Alternative hand feed is provided by a handwheel at each end of the table. Stops at the front of the table can be set to disengage the longitudinal feed automatically in each direction.SpindleThe spindle, accurately mounted in precision bearings, provides the drive for the milling cutters. Cutters can be mounted straight on the spindle nose or in curter-holding devices which in turn are mounted in the spindle, held in position by a drawbolt passing the hold spindle. Spindles of milling machines have a standard spindle nose to allow for easy interchange of cutters and cutter-holding devices. The bore of the nose is tapered to provide accurate location, the angle of taper being 1. The diameter of the taper depends on the size of the machine and may be 30,40,or 50 IST. Due to their steepness of angle, there tapers –known as non-stick or self-releasing- cannot be relied upon to transmit the drive to the cutter or cutter-holding device. Two driving keys are provided to transmit the drive.Overarm and arbor supportDue to the length of arbors used, support is required at the outer end to prevent deflection when cutting takes place. Support is provided by an arbor-support bracket, clamped to an overarm which is mounted on top of the column in a dovetail slide. The overarm is adjustable in or out for different lengths of arbor, or can be fully pushed in when arbor support is not required. Two clamping bolts are support is located in the overarm dovetail and is locked by which the arbor runs during splindle rotation.中文译文数控机床的组成部分数控机床的组成部分包括测量系统、控制系统、伺服系统及开环或闭环系统,在对数控零件进行实际程序设计之前,了解各组成部分是重要的。
关于数控车床编程外文文献翻译中英文翻译外文翻译

关于数控车床编程外文文献翻译、中英文翻译、外文翻译英文原文On the NC latheCNC machine tool numerical control machine tools (Computer numerical control machine tools) abbreviation, is provided with a program control system of automatic machine tools. The logic control system can deal with the control code or other symbolic instruction specified program, and decoding the digital code, said information carrier, through the numerical control device input. After processing by CNC device control signals, control the machine movements, by drawing the shape and size requirements, will be automatically processed by the parts.Features: CNC machine tool operation and monitoring of all completed inthe numericalcontrol unit, it is the brain of CNC machine tools. Compared with the general machine tools, CNC machine tools has the following characteristics:● the processing object adaptability, adapt to the characteristics of mold products such as a single production, provide the appropriate processing method for die and mould manufacturing; ● high machining accuracy, processing with stable quality; ● can coordinate linkage, processing complex shape parts;● machining parts change, only need to change the program, can save the preparation time of production;● the machine itself high precision, rigidity, can choose the am ount of processing good, high productivity (3~5 times as common machine);The machine is a high degree of automation, reducing labor intensity;● conducive to the production management modernization. The use of CNC machine tools and the standard code of digital information processing, information transmission, the use of computer control method, has laid the foundation for the integration of computer aided design, manufacturing and management;● on the operators of higher quality, higher demands for the repair ofthe technical staff;● high reliability.Composition: CNC machine tools in general by the input medium, man-machine interactive equipment, CNC equipment, feed servo drive system, spindle servo drive system, the auxiliary control device, feedback apparatus and adaptive control device etc.. [4] in NC machining, NC milling processing is the most complex, need to solve most problems. NC programming of NC line in addition to CNC milling, cutting, CNC EDM, CNC lathe, CNC grinding, each with its own characteristics, servo system is the role of the motion signal is convertedinto the machine moving parts from the numerical control device of pulse. Concrete has the following parts: the structure of CNC machine tools.Driver: he is driving parts of CNC machine tools, actuator, including spindle drive unit, feeding unit, spindle motor and feed motor. He through the electric or electro-hydraulic servo system to realize the spindle and feeddrive under the control of numerical control device. When several feed linkage, can complete the positioning, processing line, plane curve and space curve.The main performance (1) the main dimensions. (2) the spindle system. (3) feed system. (4) tool system.(5) electrical. Including the main motor, servo motor specifications and power etc.. (6) cooling system. Including the cooling capacity, cooling pump output. (7) dimensions. Expressed as length * width * height.Development trend of CNC lathe:High speed, precision, complex, intelligent and green is the general trend in the development of CNC machine tool technology, in recent years, made gratifying achievements in practicality and industrialization. Mainly in the:1 machine tool composite technology to further expand with the CNC machine tool technology, composite processing technology matures, including milling - car compound, car millingcompound, car - boring - drill - gear cutting compound, composite grinding, forming, composite processing, precision and efficiency of machining isgreatly improved. \processing factory\the development of compound processing machine tool is the trend of diversified.Intelligent technology 2 CNC machine tools have a new breakthrough, in the performance of NC system has been reflected more. Such as: automaticallyadjust the interference anti-collision function, after the power of workpiece automatically exit safety power-off protection function, machining parts detection and automatic compensation function of learning, high precisionmachining parts intelligent parameter selection function, process automatic elimination of machine vibration functions into the practical stage, intelligent upgrade the function of machine and quality.The 3 robots enable flexible combination of flexible combination of higher efficiency of robot and the host are widely used, make flexible line more flexible, extending the function, flexible line shorten further, more efficient. Robot and machining center, milling composite machine, grinder, gear processing machine tool, tool grinding machine, electric machine, sawing machine, punching machine, laser cutting machine, water cutting machine etc. various forms of flexible unit and flexible production line has already begun the application.4 precision machining technology has the machining precision of CNC metal cutting machine tools from the yarn in the original (0.01mm) up to micronlevel (0.001mm), some varieties has reached about 0.05 μ M. Micro cutting and grinding machining of ultra precision CNC machine tools, precision can reach about 0.05 μ m, shape precision can reach about 0.01 μ M. Special processing precision by using optical, electrical, chemical, energy can reach nanometer level (0.001 μ m). By optimizing the design of machine tool structure, machine tool parts of ultra precision machining and precision assembly, using high precision closed loop control andtemperature, vibration and other dynamic error compensation technology, improve the geometric accuracy of machine tool processing, reduce the shape of error, surface roughness, and into the submicron, nano super finishing tiThe 5 functional component to improve the performance of functional components are at a high speed, high precision, high power and intelligent direction, and obtain the mature application. A full digital AC servo motor and drive device, high technology content of the electric spindle, linear motor, torque motor, linear motion components with high performance, application of high precision spindle unit and other function parts, greatly improving the technical level of CNC machine tools.The feed drive system of CNC lathe: Effect of feed drive system,The feed drive system of CNC machine tools will be received pulse command issued by the numerical control system, and the amplification and conversion machine movements carry the expected movement.Two, the feeding transmission system requirementsIn order to guarantee the machining accuracy of NC machine tool is high,the feed drive system of transmission accuracy, sensitivity high (fast response), stable work, high stiffness and friction and inertia small, service life, and can remove the transmission gap. Category three, feed drive system 1, stepping motor servo system Generally used for NC machine tools. 2, DC servo motor servo systemPower is stable, but because of the brush, the wear resulting in use needto change. Generally used for middle-grade CNC machine tools. 3, AC servomotor servo systemThe application is extremely widespread, mainly used in high-end CNC machine tools. 4, the linear motor servo systemNo intermediate transmission chain, high precision, the feed speed, no length limit; but the poor heat dissipation, protection requirements are particularly high, mainly used for high-speed machine.Driving component four, feed system 1, the ball screw nut pairNC machining, the rotary motion into linear motion, so the use of screwnut transmissionmechanism. NC machine tools are commonly used on the ball screw, as shownin Figure 1-25, it can be a sliding friction into rolling friction, meet the basic requirements of the feed system to reduce friction. The transmissionside of high efficiency, small friction, and can eliminate the gap, no reverse air travel; but the manufacturing cost is high, can not lock, size is not too big, generally used for linear feed in small CNC machine tool. 2, rotary tableIn order to expand the scope of the process of NC machine tools, CNC machine tools in addition to make linear feed along the X, Y, Z three coordinate axes, often also need a circumferential feed movement around Y or Z axis. Circular feed motion of CNC machine tools in general by the rotary table to realize, for machining center, rotary table has become an indispensablepart of. Rotary table of commonly used CNC machine tools in the indexing table and NC rotary table. (1) indexing tableIndexing table can only finish dividing movement, not circular feed, it is in accordance with the instructions in the NC system, when indexing will work together with the workpiece rotation angle. When indexing can also use manual indexing. Provisions of indexing table is generally only rotary angle (such as 90, 60 and 45 degree). (2) NC rotary tableNC rotary table appearance similar to the indexing table, but the internal structure and function is not the same. The main function of the NC rotary table is based on the numerical control device sends command pulse signal, complete circumferential feed movement, various arc processing and surface processing, it can also be graduation work. 3, guideRail is an important part of feed drive system, is one of the basic elements of the structure of machine tool, rigidity, precision and accuracy of NC machine tool which determines to a large extent retention. At present, guide the NC machine tool are sliding rail, rolling guideway and hydrostatic guideway. (1) sliding guideSliding guide rail has the advantages of simple structure, easy manufacture, good stiffness, vibration resistance and high performance, widely used in CNC machine tools, the use of most metal plastic form, known as the plastic guide rail, as shown in figure 1-26.On characteristics of the plastic sliding guide: friction characteristicis good, good wear resistance, stable movement, good manufacturability, low speed. (2) rolling guideRolling guide is placed in the rail surface between the ball, roller or needle roller, roller, the rolling friction instead of sliding surface of the guide rail between wipe.Rolling guide rail and the sliding rail, high sensitivity, small friction coefficient, and the dynamic, static friction coefficient is very small, so the motion is uniform, especially in the low speed movement, the stick-slip phenomenon is not easy to occur; high positioning accuracy,repeatability positioning accuracy is up to 0.2 μ m; traction force is small, wear small, portable in movement; good precision, long service life. But the vibration of rolling guide, high requirements on protection, complicated structure, difficult manufacture, high cost.Automatic tool changer:One, the function of automatic tool changerAutomatic tool changing device can help save the auxiliary time of CNC machine tools, and meet in an installation completed procedure, stepprocessing requirements. Two, on the requirement of automatic tool changerNumerical control machine tool for automatic tool changer requirement is: tool change quickly, time is short, high repetitive positioning accuracy, tool storage capacity is sufficient, small occupation space, stable and reliable work. Three, change the knife form 1, rotary cutter replacementIts structure is similar to the ordinary lathe turret saddle, according to the processing of different objects can be designed into square or six angle form, consists of the NC system sends out the instruction to the rotary cutter.2, the replacement of the spindle head tool changeThe spindle head pre-loaded required tools, in order to machining position, the main motor is switched on, drives the cutter to rotate. The advantage of this method is that eliminates the need for automatic clamping, cutting tool, clamping and cutting tool moving and a series of complex operation, reducetool change time, improve The ATC reliability. 3, the use of changing toolThe processing required tools are respectively arranged in the standard tool, adjust the size of the machine after certain way add to the knife, the exchange device from the knife and the spindle take knife switch.感谢您的阅读,祝您生活愉快。
- 1、下载文档前请自行甄别文档内容的完整性,平台不提供额外的编辑、内容补充、找答案等附加服务。
- 2、"仅部分预览"的文档,不可在线预览部分如存在完整性等问题,可反馈申请退款(可完整预览的文档不适用该条件!)。
- 3、如文档侵犯您的权益,请联系客服反馈,我们会尽快为您处理(人工客服工作时间:9:00-18:30)。
Numerical ControlOne of the most fundamental concepts in the area of advanced manufacturing technologies is numerical control (NC).Prior to the advent of NC, all machine tools were manual operated and controlled. Among the many limitations associated with manual control machine tools, perhaps none is more prominent than the limitation of operator skills. With manual control, the quality of the product is directly related to and limited to the skills of the operator . Numerical control represents the first major step away from human control of machine tools.Numerical control means the control of machine tools and other manufacturing systems though the use of prerecorded, written symbolic instructions. Rather than operating a machine tool, an NC technician writes a program that issues operational instructions to the machine tool, For a machine tool to be numerically controlled , it must be interfaced with a device for accepting and decoding the p2ogrammed instructions, known as a reader.Numerical control was developed to overcome the limitation of human operator , and it has done so . Numerical control machines are more accurate than manually operated machines , they can produce parts more uniformly , they are faster, and the long-run tooling costs are lower . The development of NC led to the development of several other innovations in manufacturing technology:1.Electrical discharge machining.ser cutting.3.Electron beam welding.Numerical control has also made machine tools more versatile than their manually operated predecessors. An NC machine tool can automatically produce a wide variety of par4s , each involving an assortment of undertake the production of products that would not have been feasible from an economic perspective using manually controlled machine tools and processes.Like so many advanced technologies , NC was born in the laboratories of the Massachusetts Institute of Technology . The concept of NC was developed in the early 1950s with funding provided by the U.S Air Force .In its earliest stages , NC machines were able to make straight cuts efficiently and effectively.However ,curved paths were a problem because the machine tool had to be programmed to undertake a series of horizontal and vertical steps to produce a curve. The shorter is the straight lines making up the step ,the smoother is 4he curve . Each line segment in the steps had to be calculated.This problem led to the development in 1959 of the Automatically Programmed Tools (APT) language for NC that uses statements similar to English language to define the part geometry, describe the cutting tool configuration, and specify the necessary motions. The development of the APT language was a major step forward in the further development of NC technology. The original NC system were vastly different from those used punched paper , which was later to replaced by magnetic plastic tape .A tape reader was used to interpret the instructions written on the tape for the machine .Together, all /f this represented giant step forward in the control of machine tools . However ,there were a number of problems with NC at this point in its development.A major problem was the fragility of the punched paper tape medium . It was common for the paper containing the programmed instructions to break or tear during a machining process, This problem was exacerbated by the fact that each successive time a part was produced on a machine tool, the paper tape carrying the programmed instructions had to rerun thought the reader . If it was necessary to produce 100 copies of a given part , it was also necessary to run the paper tape thought the reader 100 separate times . Fragile paper tapes simply could not withstand the rigors of shop floor environment and this kind of repeated use.This led to the development of a special magnetic tape . Whereas the paper tape carried the programmed instructions as a series of holes punched in the tape , theThis most important of these was that it was difficult or impossible to change the instructions entered on the tape . To make even the most minor adjustments in a program of instructions, it was necessary to interrupt machining operations and make a new tape. It was also still necessary to run the tape thought the reader as many times as there were parts to be produced . Fortunately, computer technology become a reality and soon solved the problems of NC, associated with punched paper and plastic tape.The development of a concept known as numerical control (DNC) solve the paper and plastic tape problems associated with numerical control by simply eliminating tape as the medium for carrying the programmed instructions . In direct numerical control, machine tools are tied, via a data transmission link, to a host computer and fed to the machine tool as needed via the data transmission linkage. Direct numerical control represented a major step forward over punched tape and plastic tape. However ,it is subject to the same limitation as all technologies that depend on a host computer. When the host computer goes down , the machine tools also experience down time . This problem led to the development of computer numerical control.The development of the microprocessor allowed for the development of programmable logic controllers (PLC) and microcomputers . These two technologies allowed for the development of computer numerical control (CNC).With CNC , each machine tool has a PLC or a microcomputer that serves the same purpose. This allows programs to be input and stored at each individual machine tool. CNC solved the problems associated downtime of the host computer , but it introduced another problem known as data management . The same program might be loaded on ten different microcomputers with no communication among them. This problem is in the process of being solved by local area networks that connectDigital Signal ProcessorsThere are numerous situations where analog signals to be processed in many ways, like filtering and spectral analysis , Designing analog hardware to perform these functions is possible but has become less and practical, due to increased performance requirements, flexibility needs , and the need to cut down on development/testing time .It is in other words difficult pm design analog hardware analysis of signals.The act of sampling an signal into thehat are specialised for embedded signal processing operations , and such a processor is called a DSP, which stands for Digital Signal Processor . Today there are hundreds of DSP families from as many manufacturers, each one designed for a particular price/performance/usage group. Many of the largest manufacturers, like Texas Instruments and Motorola, offer both specialised DSP’s for certain fields like motor-control or modems ,and general high-performance DSP’s that can perform broad ranges of processingtasks. Development kits an` software are also available , and there are companies making software development tools for DSP’s that allows the programmer to implement complex processing algorithms using simple “drag ‘n’ drop” methodologies.DSP’s more or less fall into t wo categories depending on the underlying architecture-fixed-point and floating-point. The fixed-point devices generally operate on 16-bit words, while the floating-point devices operate on 32-40 bits floating-point words. Needless to say , the fixed-point devices are generally cheaper . Another important architectural difference is that fixed-point processors tend to have an accumulator architecture, with only one “general purpose” register , making them quite tricky to program and more importantly ,making C-compilers inherently inefficient. Floating-point DSP’s behave more like common general-purpose CPU’s ,with register-files.There are thousands of different DSP’s on the market, and it is difficult task finding the most suitable DSP for a project. The best way is probably to set up a constraint and wishlist, and try to compare the processors from the biggest manufacturers against it.The “big four” manufacturers of DSPs: Texas Instruments, Motorola, AT&T and Analog Devices.Digital-to-analog conversionIn the case of MPEG-Audio decoding , digital compressed data is fed into the DSP which performs the decoding , then the decoded samples have to be converted back into the analog domain , and the resulting signal fed an amplifier or similar audio equipment . This digital to analog conversion (DCA) is performed by a circuit with the same name & Different DCA’s provide different performance and quality , as measured by THD (Total harmonic distortion ), number of bits, linearity , speed, filter characteristics and other things.The TMS320 family DQP of Texas InstrumentsThe TLS320family consists of fixed-point, floating-point, multiprocessor digital signal processors (D[Ps) , and foxed-point DSP controllers. TMS320 DSP have an architecture designed specifically for real-time signal processing . The’ F/C240 is a number of the’C2000DSP platform , and is optimized for control applications. The’C24x series of DSP controllers combines this real-time processing capability with controller peripherals to create an ideal solution for control system applications. The following characteristics make the TMS320 family the right choice for a wide range of processing applications:--- Very flexible instruction set--- Inherent operational flexibility---High-speed performance---Innovative parallel architecture---Cost effectivenessDevices within a generation of the TMS320 family have the same CPU structure but different on-chip memory and peripheral configurations. Spin-off devices use new combinations of On-chip memory and peripherals to satisfy a wide range of needs in the worldwide electronics market. By integrating memory and peripherals onto a single chip , TMS320 devices reduce system costs and save circuit board space.The 16-bit ,fixed-point DSP core of the ‘C24x devices provides analog designers a digital solution that does not sacrifice the precision and performance of their system performance can be enhanced through the use of advanced control algorithms for techniquessuch as adaptive control , Kalman filtering , and state control. The ‘C24x DSP controller offer reliability and programmability . Analog control systems, on the other hand ,are hardwired solutions and can experience performance degradation due to aging , component tolerance, and drift.The high-speed central processing unit (CPU) allows the digital designer to process algorithms in real time rather than approximate results with look-up tables. The instruction set of these DSP controllers, which incorporates both signal processing instructions and general-purpose control functions, coupled with the extensive development time and provides the same ease of use as traditional 8-and 16-bit microcontrollers. The instruction set also allows you to retain your software investment when moving from other general-purp ose‘C2xx generation ,source code compatible with the’C2x generation , and upwardly source code compatible with the ‘C5x generation of DSPs from Texas Instruments.The ‘C24x architecture is also well-suited for processing control signals. It uses a 16-bit word length along with 32-bit registers for storing intermediate results, and has two hardware shifters available to scale numbers independently of the CPU . This combination minimizes quantization and truncation errors, and increases p2ocessing power for additional functions. Such functions might include a notch filter that could cancel mechanical resonances in a system or an estimation technique that could eliminate state sensors in a system.The ‘C24xDSP controllers take advantage of an set of peripheral functions that allow Texas Instruments to quickly configure various series members for different price/ performance points or for application optimization.This library of both digital and mixed-signal peripherals includes:---Timers---Serial communications ports (SCI,SPI)---Analog-to-digital converters(ADC)---Event manager---System protection, such as low-voltage and watchdog timerThe DSP controller peripheral library is continually growing and changing to suit the of tomorrow’s embedded control marke tplace.The TMS320F/C240 is the first standard device introduced in the ‘24x series of DSP controllers. It sets the standard for a single-chip digital motor controller. The ‘240 can execute 20 MIPS. Almost all instructions are executed in a simple cycle of 50 ns . This high performance allows real-time execution of very comple8 control algorithms, such as adaptive control and Kalman filters. Very high sampling rates can also be used to minimize loop delays.The ‘ 240 has the architectural features necessary for high-speed signal processing and digital control functions, and it has the peripherals needed to provide a single-chip solution for motor control applications. The ‘240 is manufactured using submicron CMOS technology, achieving a log power dissipation rating . Also included are several power-down modes for further power savings. Some applications that benefit from the advanced processing power of the ‘240 include:---Industrial motor drives---Power inverters and controllers---Automotive systems, such as electronic power steering , antilock brakes, and climatecontrol---Appliance and HV AC blower/ compressor motor controls---Printers, copiers, and other office products---Tape drives, magnetic optical drives, and other mass storage products---Robotic and CNC milling machinesTo function as a system manager, a DSP must have robust on-chip I/O and other peripherals. The event manager of the ‘240 is unlike any other available on a DSP . This application-optimized peripheral unit , coupled with the high performance DSP core, enables the use of advanced control techniques for high-precision and high-efficiency full variable-speed control of all motor types. Include in the event manager are special pulse-width modulation (PWM) generation functions, such as a programmable dead-band function and a space vector PWM state machine for 3-phase motors that provides state-of-the-art maximum efficiency in the switching of power transistors.There independent up down timers, each with it’s own compare register, suppo rt the generation of asymmetric (noncentered) as well as symmetric (centered) PWM waveforms.Open-Loop and Closed-Loop ControlOpen-loop Control SystemsThe word automatic implies that there is a certain amount of sophistication in the control system. By automatic, it generally means That the system is usually capable of adapting to a variety of operating conditions and is able to respond to a class of inputs satisfactorily . However , not any type of control system has the automatic feature. Usually , the automatic feature is achieved by feed.g the feedback structure, it is called an open-loop system , which is the simplest and most economical type of control system.inaccuracy lies in the fact that one may not know the exact characteristics of the further ,which has a definite bearing on the indoor temperature. This alco points to an important disadvantage of the performance of an open -loop control system, in that the system is not capable of adapting to variations in environmental conitions or to external disturbances. In the case of the furnace control, perhaps an experienced person can provide control for a certain desired temperature in the house; but id the doors or windows are opened or closed intermittently during the operating period, the final temperature inside the house will not be accurately regulated by the open-loop control.An electric washing machine is another typical example of an open-loop system , because the amount of wash time is entirely determined by the judgment and estimation of the human operator . A true automatic electric washing machine should have the means of checking the cleanliness of the clothes continuously and turn itsedt off when the desired degised of cleanliness is reached.Closed-Loop Control SystemsWhat is missing in the open-loop control system for more accurate and more adaptable control is a link or feedback from the output to the input of the system . In order to obtain more accurate bontrol, the controlled signal c(t) must be fed back and compared with the reference input , and an actuating signal proportional to the difference of the output and the input must be sent through the system to correct the error. A system with one or more feedback pat(s like that just described is called a closed-loop system. human being are probably the most complex and sophisticated feedback control system in existence. A humanbeing may be considered to be a control system with many inputs and outputs, capable of carrying out highly complex operations.To illustrate the human being as a feedback control system , let us consider that the objective is to reach for an object on aperform the task. The eyes serve as a sensing device which feeds back continuously the position of the hand . The distance between the hand and the object is the error , which is eventually brought to zero as the hand reacher the object. This is a typical example of closed-loop control. However , if one is told to reach for the object and then is blindolded, one can only reach toward the object by estimating its exact position. It isAs anther illustrative example of a closed-loop control system, shows the block diagram of the rudder control system ofThe basic alements and the bloca diagram of a closed-loop control system are shown in fig. In general , the configuration of a feedback control system may not be constrained to that of fig & . In complex systems there may be multitude of feedback loops and element blocks.数控在先进制造技术领域最根本的观念之一是数控(NC)。