采购控制程序中英文版本
采购控制程序-中英文版本

Page : 1/4Status:PROCEDURE 程序文件Procurement Management Procedure 采购控制程序目的OBJECTIVE 2 范围SCOPE2 职责RESPONSIBILITY2 正文PROCEDURAL ELEMENTS3 流程FLOW CHART3 任务描述TASKS DESCRIPTION4 参考文件REFERENCE DOCUMETS4 定义与缩写DEFINITIONS/ ABBREVIATIONS 4 记录RECORDS4________________________________________________________________Page : 2/4Status:PROCEDURE 程序文件Procurement Management Procedure 采购控制程序Objective 目的This document is to define the procedure how the procurement should be handled in the factory. 本文件用于定义公司之采购流程。
__________________________________________________________Scope 范围This procedure is applicable for all the procurement orders issued by QF. 此流程适用于所有发出的采购订单。
__________________________________________________________Responsibility 职责Procurement department should provide all the specification of the material according to PD dept’s BOM.Procurement dept is responsible for issuing and following the necessary procurement to ensure production in QF factory. QF Procurement is responsible for providing the information to Finance department on the material which need to be paid.采购部,根据开发部的《物料用量表》From_PR_008_003,提供所有生产大货的物料规格即《生产制造单》From_PR_008_005。
英文采购管理制度及流程

英文采购管理制度及流程1. IntroductionThe procurement management system (PMS) and process are critical components of any organization's operations. It involves the acquisition of goods, services, and resources required to run the business. A well-designed and efficient PMS and process can help an organization achieve cost savings, quality improvements, and timely delivery of goods and services. This document outlines the procurement management system and process for our organization.2. ObjectivesThe primary objectives of the procurement management system and process are as follows: - To ensure the timely acquisition of goods and services required for the organization's operations.- To obtain goods and services of the right quality at the best possible price.- To promote transparency, fairness, and accountability in the procurement process.- To establish and maintain good relationships with suppliers and vendors.3. Policy and ProceduresThe procurement management system and process are governed by a set of policies and procedures that are designed to ensure that all procurement activities are carried out in a transparent, fair, and effective manner. The key policies and procedures include:- Supplier selection and evaluation: A comprehensive list of pre-approved suppliers and vendors is maintained, and new suppliers are evaluated based on their reputation, experience, quality standards, and pricing. This ensures that the organization works with reliable and competent suppliers.- Request for Proposals (RFP): When significant purchases are required, the organization sends out RFPs to potential suppliers, outlining the specifications and requirements for the goods or services required. This allows the organization to compare proposals from different suppliers and select the one that offers the best value for money.- Contract management: Once a supplier is selected, a contract is drawn up that outlines the terms and conditions of the purchase, including price, delivery schedule, quality standards, and payment terms. The contract is managed throughout its duration to ensure that the supplier delivers the goods or services as per the agreed-upon terms.- Purchase orders: For routine purchases, purchase orders are issued to suppliers, specifying the type and quantity of goods required, the agreed-upon price, and the deliveryschedule. This ensures that the procurement process is standardized and that all purchases are authorized and tracked.- Supplier performance evaluation: The performance of suppliers is monitored and evaluated on an ongoing basis, using criteria such as delivery timeliness, product quality, responsiveness to issues, and compliance with contractual terms. This allows the organization to identify any issues with suppliers and take corrective action as required.4. Roles and ResponsibilitiesThe procurement management system and process involve the participation of various stakeholders within the organization, each with specific roles and responsibilities:- Procurement manager: The procurement manager oversees the entire procurement process, including supplier selection, contract management, and supplier performance evaluation. They are responsible for ensuring that all procurement activities are carried out in accordance with the organization's policies and procedures, and that the best possible value is obtained from suppliers.- Requisitioner: The requisitioner is the individual within the organization who identifies the need for goods or services and initiates the procurement process. They are responsible for providing the procurement manager with all the necessary information about the goods or services required, including specifications, quantity, and desired delivery schedule.- Approver: The approver is the individual within the organization who has the authority to approve purchase orders, contracts, and other procurement documents. They ensure that all procurement activities are authorized and comply with the organization's budget and procurement policies.5. Technology and ToolsThe procurement management system and process are supported by various technology tools that help streamline procurement activities and improve efficiency. These include:- Procurement software: Many organizations use specialized procurement software that automates various aspects of the procurement process, including supplier management, RFPs, contract management, and purchase orders. This software can help reduce manual paperwork, improve record-keeping, and provide valuable data and analytics on procurement activities.- Supplier portals: Some organizations use supplier portals, which are online platforms that allow suppliers to submit their proposals, receive purchase orders, and interact with the organization's procurement team. This can help streamline communication with suppliers and provide transparency in the procurement process.- E-procurement systems: E-procurement systems allow organizations to conduct procurement activities electronically, including sourcing, ordering, and payment. This canhelp reduce delays, errors, and administrative costs associated with traditional paper-based procurement processes.6. Performance MeasurementThe effectiveness of the procurement management system and process is measured through various performance indicators, including:- Cost savings: This measures the amount of money saved through efficient procurement practices, such as negotiating lower prices with suppliers, consolidating purchases, and reducing waste and excess inventory.- Supplier performance: This measures the performance of suppliers in terms of delivery timeliness, product quality, responsiveness to issues, and compliance with contractual terms. This can help identify areas for improvement in supplier relationships and ensure that the organization is working with the best suppliers.- Process efficiency: This measures the efficiency of the procurement process in terms of lead times, cycle times, and paperwork reduction. This can help identify opportunities for process improvement and streamlining.7. ConclusionThe procurement management system and process are critical to the success of any organization, as they ensure that the organization has the goods and services required to operate efficiently and effectively. By following clear policies and procedures, leveraging technology tools, and measuring performance, organizations can achieve cost savings, quality improvements, and supplier relationships. This can help the organization maintain a competitive edge in the marketplace and achieve its strategic goals.。
iso9001:2015采购控制程序英文版
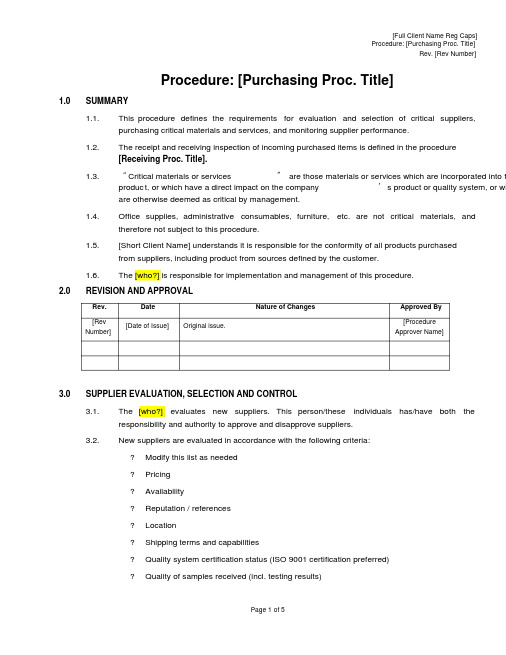
Procedure: [Purchasing Proc. Title]1.0SUMMARY1.1.This procedure defines the requirements for evaluation and selection of critical suppliers,purchasing critical materials and services, and monitoring supplier performance.1.2.The receipt and receiving inspection of incoming purchased items is defined in the procedure[Receiving Proc. Title].1.3.“Critical materials or services” are those materials or services which are incorporated into fproduc t, or which have a direct impact on the company’s product or quality system, or whare otherwise deemed as critical by management.1.4.Office supplies, administrative consumables, furniture, etc. are not critical materials, andtherefore not subject to this procedure.1.5.[Short Client Name] understands it is responsible for the conformity of all products purchasedfrom suppliers, including product from sources defined by the customer.1.6.The [who?] is responsible for implementation and management of this procedure.2.0REVISION AND APPROVALRev. Date Nature of Changes Approved By[Rev Number] [Date of Issue] Original issue.[ProcedureApprover Name]3.0SUPPLIER EVALUATION, SELECTION AND CONTROL3.1.The [who?] evaluates new suppliers. This person/these individuals has/have both theresponsibility and authority to approve and disapprove suppliers.3.2.New suppliers are evaluated in accordance with the following criteria:?Modify this list as needed?Pricing?Availability?Reputation / references?Location?Shipping terms and capabilities?Quality system certification status (ISO 9001 certification preferred)?Quality of samples received (incl. testing results)?On-site audit results?Telephone interview results?Written survey results?Customer mandate?Sole source / OEM status3.3.Where a customer mandates a special process source, both [Short Client Name] and anysuppliers must use the required supplier; this usage may override [Short Client Name]status rules.3.4.In some cases a formal risk assessment may be conducted as part of the evaluation andselection of a potential supplier, or in order to determine if a problematic supplier should be retained; see [Risk Management Proc. Title].[Use this next section if the ASL is a spreadsheet, database or document – NOT if the ASL is part of an ERP system.]3.5.The [who?] will maintain an Approved Supplier List (modify name if needed) which lists allevaluated and approved suppliers, and their approval status.3.6.Suppliers who meet any of the evaluation criteria, in the judgment of the person conducting theevaluation, may then be entered into the purchasing system and items may be purchased.However, the supplier is entered into the Approved Supplier List (ASL) on a CONDITIONAL basis, pending inspection or review of products or services rendered.3.7.Upon successful receipt or review of products or services, the manager may then advance thesupplier’s status to APPROVED.3.8.If the results of review of product or service received are insufficient or otherwise lacking, thestatus to DISAPPROVED, or to leave it at buyer may then elect to change the supplier’sCONDITIONAL until further orders are received and reviewed.3.9. A supplier may also be listed as RESTRICTED, where certain purchasing restrictions are placed onthe supplier. This may be useful to limit what products may be purchased from a supplier, or toplace other conditions.3.10.The Approved Supplier List indicates the supplier, location, approval status (Approved,Conditional, Disapproved, Restricted), and the scope of approval (typically commodity type orproduct family). Re-approval of suppliers is continual and ongoing based on the suppliers abilityto meet the criteria of paragraph 3.2. For Restricted status, a note of the restriction must alsobe included.3.11.Suppliers used for at least six months prior to [Date of Issue], have been grandfathered into thesystem as Approved, provided they have no outstanding quality issues on record, and only uponthe decision by [who?] to do so.[Use this next section if the ASL is part of the ERP system]。
Purchasing Management采购管理程序(中英文)
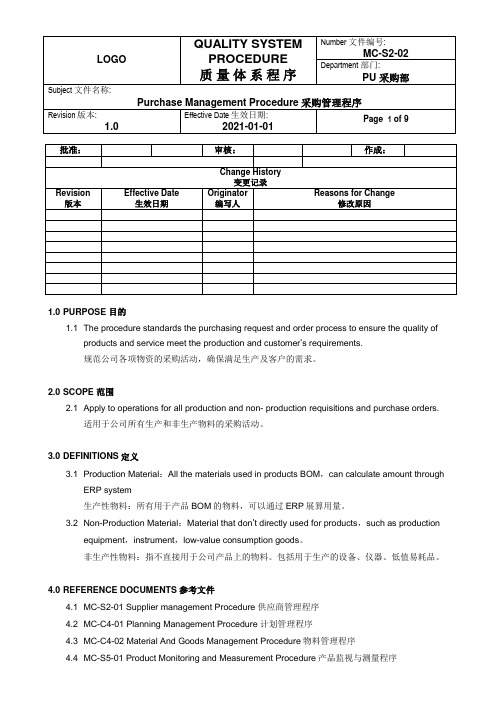
1.0 PURPOSE 目的1.1 The procedure standards the purchasing request and order process to ensure the quality ofproducts and service meet the production and customer’s requirements.规范公司各项物资的采购活动,确保满足生产及客户的需求。
2.0 SCOPE 范围2.1 Apply to operations for all production and non- production requisitions and purchase orders.适用于公司所有生产和非生产物料的采购活动。
3.0 DEFINITIONS定义3.1 Production Material:All the materials used in products BOM,can calculate amount throughERP system生产性物料:所有用于产品BOM的物料,可以通过ERP展算用量。
3.2 Non-Production Material:Material that don’t directly used for products,such as productionequipment,instrument,low-value consumption goods。
非生产性物料:指不直接用于公司产品上的物料。
包括用于生产的设备、仪器、低值易耗品。
4.0 REFERENCE DOCUMENTS参考文件4.1 MC-S2-01 Supplier management Procedure 供应商管理程序4.2 MC-C4-01 Planning Management Procedure 计划管理程序4.3 MC-C4-02 Material And Goods Management Procedure物料管理程序4.4 MC-S5-01 Product Monitoring and Measurement Procedure产品监视与测量程序4.5 MC-S6-01 Nonconforming Product Control Procedure 不合格品控制程序5.0 RECORDS 记录5.1 FN-PU-012 Purchase Order 采购订单5.2 FN-PU-013 Capital approval Form 固定资产审批单5.3 FN-PU-014 Purchasing Requisition Form 采购申请单5.4 FN-PU-015 Purchasing Inquiry Form 询价单5.5 FN-PU-016 Urgency Purchasing Requisition Audit Form紧急需求申请审批单5.6 FN-PU-017 Purchasing Inquiry Record 采购询价记录表5.7 FN-PU-018 Notice of Deductions 供应商扣款单5.8 FN-PU-019 Purchasing Change Application Form 采购变更申请审批单6.0 RESPONSIBILITY职责6.1 Purchasing department: Purchasing for productive materials and non- productive, such asequipments, tooling and fixtures, measuring instruments, and etc.采购部:负责生产性物料和非生产性物料的采购,非生产性物料如设备、工装、量具等。
采购流程 英文

采购流程英文The procurement process is a critical aspect of any business, as it involves the purchasing of goods and services that are essential for the operation of the organization. Effective procurement management is crucial for ensuring that the right products are obtained at the right time and at the right cost. In this document, we will discuss the key steps involved in the procurement process and how it can be effectively managed to achieve optimal results.1. Identify the Need。
The first step in the procurement process is to identify the need for a particular product or service. This may be initiated by various departments within the organization, such as production, marketing, or administration. It is important to clearly define the specifications and requirements for the desired item to ensure that the procurement process is aligned with the organization's objectives.2. Supplier Identification and Selection。
采购程序(中英文含流程图)

采购程序(中英⽂含流程图)采购程序PURCHASING PROCEDURE采购程序PURCHASING PROCEDURE1. Purpose⽬的Provide a consistent method for assuring purchased material meet XXXX and customer requirements and optimize purchasing cost and efficiency.为了确保所采购的物料满⾜xxxx公司及客户的需要,优化采购成本及效率。
2. Scope范围Apply to all direct and indirect material used for finish goods and non-production material.所有⽤于成品或⽣产当中的直接或间接物料。
3. Reference Document参考⽂件4.1 Purchasing control flow chart (Direct Material) OP-PU-FC-01采购控制流程图(直接物料)4.2 Purchasing control flow chart (Indirect Material) OP-PU-FC-02采购控制流程图(间接物料)4.3 RTV control flow chart OP-PU-FC-03退货流程图4.4 Approval Vendor List (Direct Material) OP-PU-FO-01合格供应商清单4.5 Lead Time Summary (Direct Material) OP-PU-FO-02交货周期汇总4.6 Sorting Cost monthly report OP-PU-FO-05挑选费⽤⽉报表4.7 Purchase Request OP-MC-FO-03采购申请表5. Definition定义5.1 MPS - Master Production Schedule主⽣产计划5.2 MRB – Material Review Board物料评审会5.3 MRP – Material Request Plan物料需求计划5.4 PO - Purchase Order采购单5.5 PR - Purchase Request采购申请表6. General procedure⼀般程序6.1 Responsibilities 责任⼈6.1.1 Buyer is responsible for creating PO, issuing PO to supplier and following up delivery.采购员负责下订单,分发订单及跟踪交期。
采购控制程序

4.2对供方的开发导入、调查评价The development of the supplier, import, investigation, assessment
4.2.1对新供应商开发导入首次调查评价,必须确保样件得到批准,试产结论合格的前提下进行调查、评价。总分为100分,调查评价项目如下:
For the first survey and evaluation of new supplier development, it is necessary to ensure that the sample is approved and the survey and evaluation are conducted on the premise that the trial production is qualified. The total score is 100 points, and the survey evaluation items are as follows:
4.1.3 B类:不直接影响产品质量或即使略有影响,但可采取措施予以纠正的采购产品,如电线、电缆、硅钢片、有色金属;模压壳体;按钮配件;弹簧;印刷电路板、电阻、电容、二极管、三极管、发光器件等电子元器件;
Class B: not directly affect the quality of the product or even a slight impact, but can take measures to correct the procurement of products such as wires, cables, silicon steel, non-ferrous metals; moldedshell; button accessories; spring; printed circuit boards, Capacitors, diodes, transistors, light-emitting devices and other electronic components;
采购部流程英语
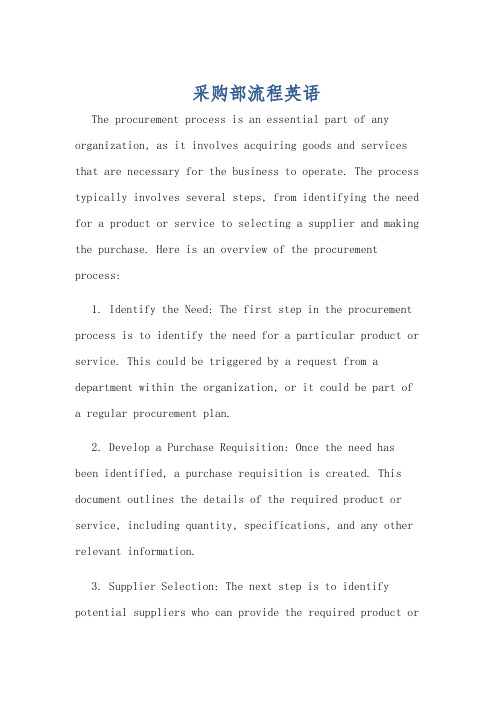
采购部流程英语The procurement process is an essential part of any organization, as it involves acquiring goods and services that are necessary for the business to operate. The process typically involves several steps, from identifying the need for a product or service to selecting a supplier and making the purchase. Here is an overview of the procurement process:1. Identify the Need: The first step in the procurement process is to identify the need for a particular product or service. This could be triggered by a request from a department within the organization, or it could be part ofa regular procurement plan.2. Develop a Purchase Requisition: Once the need has been identified, a purchase requisition is created. This document outlines the details of the required product or service, including quantity, specifications, and any other relevant information.3. Supplier Selection: The next step is to identify potential suppliers who can provide the required product orservice. This may involve issuing a request for proposal (RFP) or a request for quotation (RFQ) to solicit bids from potential suppliers.4. Evaluate Bids: Once the bids have been received, they are evaluated based on various criteria, such as price, quality, delivery time, and supplier reputation. The goalis to select the supplier that offers the best overallvalue for the organization.5. Negotiate Terms: After selecting a supplier, negotiations may take place to finalize the terms of the purchase, including price, delivery schedule, payment terms, and any other relevant details.6. Purchase Order: Once the terms have been agreed upon,a purchase order is issued to the selected supplier. This document serves as a formal contract between theorganization and the supplier, outlining the details of the purchase.7. Receipt and Inspection: When the goods or servicesare delivered, they are received and inspected to ensure they meet the requirements outlined in the purchase order. Any discrepancies or issues are addressed with the supplier.8. Invoice and Payment: After the goods or services have been received and accepted, the supplier issues an invoice, and payment is made according to the agreed-upon terms.9. Record Keeping: Throughout the procurement process, detailed records are maintained to track the purchases, payments, and supplier performance. This information is essential for financial and performance analysis, as wellas for compliance and audit purposes.采购流程是任何组织的重要组成部分,因为它涉及获取业务运营所需的货物和服务。
- 1、下载文档前请自行甄别文档内容的完整性,平台不提供额外的编辑、内容补充、找答案等附加服务。
- 2、"仅部分预览"的文档,不可在线预览部分如存在完整性等问题,可反馈申请退款(可完整预览的文档不适用该条件!)。
- 3、如文档侵犯您的权益,请联系客服反馈,我们会尽快为您处理(人工客服工作时间:9:00-18:30)。
XX有限公司文件编号:版本版次:制定部门:制定日期:修定日期:总页次:会签:1.0 目的Purpose建立公司采购过程的管理程序,对产品采购的过程及价格进行有效控制,以确保所采购的物品/服务质量能符合和满足公司的各项生产需求。
To establish a management procedure for purchasing process control, ensure to control the product purchasing process and price effectively, in order to ensure the products/service purchased can satisfy the company’s requirements and needs.2.0 范围Scope本文件适用于公司内部所有采购过程(指满足公司最终产品所需要的各种原材料、辅助材料、设备及维修材料、外协加工服务、工具以及其它物品的采购)。
This procedure apply to all purchase process happen in our company (all kinds of rawmaterial, auxiliary material, equipments and maintain material, outside machining service, tooling and all other goods needed by the company’s production or work.)3.0 适用文件Applicable documents以下文件的最新版本有效The latest issue of the following documents are effect.COP037 《供应商管理程序》<Suppliers management procedure>COP028 《仓储管理程序》<Storage Management Procedure>COP010《测量仪器校正与管理程序》<Measuring Equipment Calibration and Management Procedure> COP002《质量环境记录控制程序》< Quality and environment Records control procedure>COP038《不合格品控制程序》<Control procedure for Unsatisfactory Products>QCI002 《IQC来料检验作业指导书》<Working Instruction for Incoming Material Inspection>PMI014《产品搬运包装防护作业指导书》<Products Conveying, Packing and Protecting Work Instruction>4.0 职责Responsibilities4.1 采购部负责制定物料的采购计划、采购以及价格控制。
Purchasing department is responsible to arrange the material purchase plan, purchaseprocess and price control.4.2 品保部负责公司成品委外检验和试验,仪器校正的作业。
QA department is responsible for the finished product’s third-party inspection and testing,and the job of equipment calibration.4.3 维修部负责制定生产设备配件、水电材料采购计划。
MA department is responsible for arrange purchase plan for production equipmentfittings, water and electricity materials.4.4 工艺部负责工程使用物料的申购,与生产有关设备的评估选择、设备改造项目的计划。
ME departments is responsible to apply to purchase the engineering probationmaterials, evaluate and choose the equipments related to production, and the projectplan of equipment alteration.4.5 各部门负责本部门生产消耗性配件、常用工具以及与生产消耗无关物品的采购申请。
Other departments are responsible for purchase application of production consumptivefittings, normal tools and products not related to production consume.4.6 其它与生产有关的消耗性辅料、劳动保护用品等,由各部门制定月消耗标准,由仓库出采购申请采购。
The other products such as consumptive auxiliary material related to production, laborprotection appliance, shall make a monthly consume standards by use department, andthen hand into storehouse to apply to purchase.4.7 网络设备及其消耗性材料(除生产设备附属之电脑及零部件)由电脑部统一申请采购。
MIS department shall apply to purchase the network equipments and their consumptivematerial (exclude the computer and parts attached on production equipments)5.0程序内容Procedure content5.1 生产物料的采购Production material purchasing5.1.1 采购计划Purchase plan5.1.1.1采购计划制定的依据为历史产量及物料用量、当月的销售订单的状况。
The purchase plan is prepare base on the past output and materials dosage, the salesorder of this month.5.1.1.2采购部将物料采购分为单项控制和批量控制。
其中主要原材料和特殊物料实行单项控制,其他物料可实行批量控制。
Purchase department separate the material purchase as monomial control and batchcontrol. And the important raw material and special material will carry the monomialcontrol, the other material will carry batch control.5.1.1.3单项控制的物料,对于每一份订单,采购员应先查询生产制作指示并结合物料消耗定额标准,计算其需求量,在ERP里生成采购请求单。
Materials which take monomial control, for each order, buyer shall query theproduction fabricate instruction firstly and combine with material consume rationstandards, calculate theirneeds, create the purchase application in ERP system.5.1.1.4 批量控制的物料,采购员可根据预计月产量、该物料的订货周期,制定安全库存、最低库存的订购点以及计划采购量。
Materials which take batch control, buyer can make the safety storage,theminimum inventory reorder point and planed purchase quantity base on theguesstimate monthly output and order cycle.5.1.1.5 采购计划量需考虑库存数量、采购周期、已订购在途数量、最低库存量以及物料的有效期限及月末库存金额等因素。
单项控制物料还需考虑订单的生产周期,批量控制物料则还需考虑订单的平均消耗量等。
Purchase plans need to consider the factors such as amount of storage, purchasecycle, ordered amount in-transit, the minimum storage, the material’s useful-lifeand the stocks value in the end of the month. The production cycle of the ordershall also take into consideration for monomial control, and the average consumeof each order shall be take into consideration for batch control.5.1.1.6 完成采购计划后,可汇总采购批量,生成采购申请单。
Summarize the purchase batch after finished the purchase plan, create purchaseapplication.5.1.2 送货计划Deliver plan5.1.2.1采购请求单经采购部经理、财务部成本中心、总裁审批后,可向供应商发出正式的订购单。
Send the formal order form to supplier after the purchase application approvedby purchase department manager, cost center principal and the president.5.1.2.2所有采购单需明确材料名称、规格、数量、交货时间、币种、税率、价格、包装、运输及交付方式、付款方式等其它必要条件。