锂电设备生产工艺全解析
锂电池制造工艺全解析
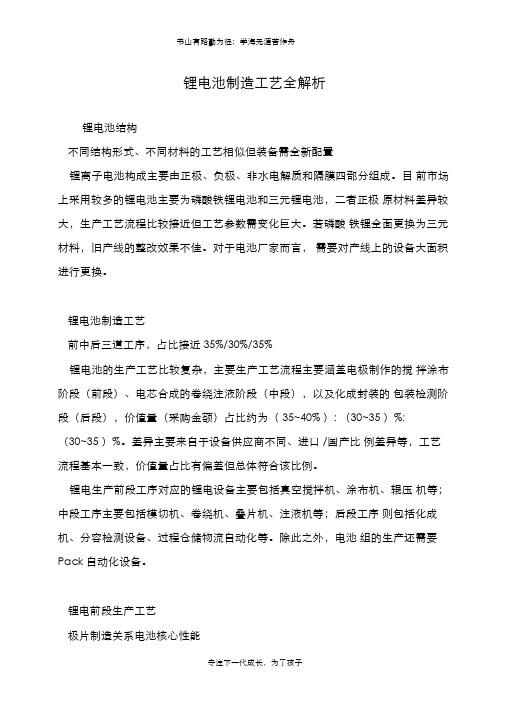
书山有路勤为径;学海无涯苦作舟
锂电池制造工艺全解析
锂电池结构
不同结构形式、不同材料的工艺相似但装备需全新配置
锂离子电池构成主要由正极、负极、非水电解质和隔膜四部分组成。
目前市场上采用较多的锂电池主要为磷酸铁锂电池和三元锂电池,二者正极原材料差异较大,生产工艺流程比较接近但工艺参数需变化巨大。
若磷酸铁锂全面更换为三元材料,旧产线的整改效果不佳。
对于电池厂家而言,需要对产线上的设备大面积进行更换。
锂电池制造工艺
前中后三道工序,占比接近35%/30%/35%
锂电池的生产工艺比较复杂,主要生产工艺流程主要涵盖电极制作的搅拌涂布阶段(前段)、电芯合成的卷绕注液阶段(中段),以及化成封装的包装检测阶段(后段),价值量(采购金额)占比约为(35~40% ): (30~35 )%:
(30~35 )%。
差异主要来自于设备供应商不同、进口/国产比例差异等,工艺流程基本一致,价值量占比有偏差但总体符合该比例。
锂电生产前段工序对应的锂电设备主要包括真空搅拌机、涂布机、辊压机等;中段工序主要包括模切机、卷绕机、叠片机、注液机等;后段工序则包括化成机、分容检测设备、过程仓储物流自动化等。
除此之外,电池组的生产还需要Pack 自动化设备。
锂电前段生产工艺
极片制造关系电池核心性能
专注下一代成长,为了孩子。
锂电池生产工艺流程及参考设备项目2
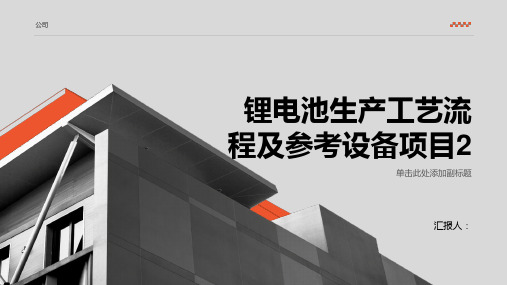
切割:将辊压后的负极材料 切割成所需的尺寸
电解液工艺流程图解
原料准备:锂盐、有机 溶剂、添加剂等
混合搅拌:将原料混合 均匀搅拌至溶液
过滤:去除杂质保证溶 液纯净度
灌装:将溶液灌装到电 池壳中
封口:密封电池壳防止 溶液泄漏
检测:检测电池性能确 保质量合格
电池组装工艺流程图解
电池组装:将 电池芯、电池 壳、电池盖等 部件组装成电
添加标题
粉碎:将烧结后的 负极材料进行粉碎 处理得到最终负极 材料
电解液的制备工艺
原料选择:选择合适的电解液原料如锂盐、溶剂等 混合搅拌:将原料混合在一起进行搅拌使原料充分混合 过滤:将混合后的原料进行过滤去除杂质 包装:将过滤后的电解液进行包装便于运输和使用
电池的组装工艺
电池组装:将 电池芯、电池 壳、电池盖等 部件组装成电
原料处理:粉碎、研 磨、筛分等
配料混合:按照一定 比例混合原料
烧结:在高温下烧结 形成正极材料
粉碎:将烧结后的正 极材料粉碎成粉末
筛分:将粉碎后的粉 末进行筛分得到不同
粒径的正极材料
包装:将筛分后的正 极材料进行包装准备
进入下一道工序
负极材料工艺流程图解
原料准备:选择合适的负极 材料如石墨、硅等
添加标题
公司
锂电池生产工艺流 程及参考设备项目2
单击此处添加副标题
汇报人:
目录
单击添加目录项标题
01
锂电池生产工艺流程
02
锂电池生产设备介绍
03
锂电池生产工艺流程图解
04
ห้องสมุดไป่ตู้
锂电池生产设备参数及选型建议
05
01
添加章节标题
01
锂电池生产工艺及参数

锂电池生产工艺及参数锂电池是一种高能量密度、长寿命、环保的电池,被广泛应用于移动设备、电动汽车、储能系统等领域。
下面将介绍锂电池的生产工艺及参数。
一、正极材料制备工艺1. 混合材料:将锂铁磷酸、碳酸锂、氧化镍、氧化钴等按一定比例混合,加入适量的粘合剂和溶剂,搅拌均匀。
2. 涂布:将混合材料涂布在铝箔或铜箔上,形成正极片。
3. 干燥:将正极片放入烘箱中,进行干燥处理。
4. 压片:将干燥后的正极片放入压片机中,进行压片处理。
5. 切割:将压片后的正极片切割成适当大小。
二、负极材料制备工艺1. 混合材料:将石墨、聚丙烯、碳黑等按一定比例混合,加入适量的粘合剂和溶剂,搅拌均匀。
2. 涂布:将混合材料涂布在铜箔上,形成负极片。
3. 干燥:将负极片放入烘箱中,进行干燥处理。
4. 压片:将干燥后的负极片放入压片机中,进行压片处理。
5. 切割:将压片后的负极片切割成适当大小。
三、电解液制备工艺1. 配制电解液:将碳酸二甲酯、乙二醇、丙二醇、氟化锂等按一定比例混合,搅拌均匀。
2. 过滤:将配制好的电解液过滤,去除杂质。
四、电池组装工艺1. 组装:将正极片、负极片和隔膜按一定顺序叠放,形成电池芯。
2. 注液:将电解液注入电池芯中。
3. 封口:将电池芯封口,形成成品电池。
五、电池参数1. 电压:锂电池的电压一般为3.6V或3.7V。
2. 容量:锂电池的容量一般以毫安时(mAh)为单位,表示电池能够供应的电流量。
3. 充放电倍率:锂电池的充放电倍率表示电池能够承受的最大充放电电流。
4. 循环寿命:锂电池的循环寿命表示电池能够进行多少次充放电循环。
以上是锂电池的生产工艺及参数,锂电池的制备工艺和参数不断改进和提高,以满足不同领域的需求。
【干货】锂离子电池工序大全详细解读

【干货】锂离子电池工序大全详细解读来源:新能源时代锂电池生产制造流程,凡在新能源领域的从业人员都能“信手拈来”。
但是,简单的流程能表达出锂电池制造工艺技术的种种艰辛吗?下面新能源时代(欢迎关注)公众号为大家介绍主要锂电池制程管控的要点。
(抛砖引玉)一部分正极配料(正极由活性物、导电剂、粘结剂组成)1、首先是对来料确认和烘烤,一般导电剂需≈120℃烘烤8h,粘结剂PVDF需≈80℃烘烤8h,活性物(LFP、NCM等)视来料状态和工艺而定是否需要烘烤干燥。
当前车间要求温度:≤40℃,湿度:≤25%RH。
2、干燥完成后,(湿法工艺)需要提前配好PVDF胶液(溶质PVDF,溶液NMP)。
PVDF胶液好坏对电池的内阻、电性能影响至关重要。
影响打胶的因素有温度、搅拌速度。
温度越高胶液配出来泛黄,影响粘结性;搅拌的速度太高容易将胶液打坏,具体的转速需要看分散盘的大小而定,一般情况下分散盘线速度在10-15m/s(对设备依赖性较高)。
此时要求搅拌罐需要开启循环水,温度:≤30℃.3、接下来是配正极浆料。
此时需要注意加料的顺序(先加活性物和导电剂慢搅混合、再加入胶液)、加料时间、加料比例,要严格按工艺执行。
其次需要严格控制设备公转和自转速度(一般分散线速度要在17m/s以上具体要看设备性能,不同厂家差别很大),搅拌的真空度、温度。
在此阶段需要定期检测浆料的粒度和粘度,而粒度和粘度跟固含量、材料性能、加料顺序和制程工艺关系紧密(此次不叙述,欢迎讨论)。
此时常规工艺要求温度:≤30℃,湿度:≤25%RH,真空度≤-0.085mpa。
4、浆料配完后就要将浆料转出至中转罐或涂布车间,浆料转出时需要对其过筛,目的就是过滤大颗粒物、沉淀和去除铁磁性等物质。
大颗粒影响涂布到最后可能导致电池自放过大或短路的风险;浆料铁磁性物质过高会导致电池自放电过大等不良。
此时的工艺要求是温度:≤40℃,湿度:≤25%RH,筛网≤100目,粒度≤15um(参数仅供参考)。
锂电池生产线产品方案设备设施及工艺流程

锂电池生产线产品方案设备设施及工艺流程一、锂电池生产线的产品方案二、锂电池生产线的设备设施1.电池材料配料和预处理设备:主要包括配料系统、混料机、球磨机、筛分机等设备,用于将电池所需的原材料按照一定比例混合、球磨、筛分。
2.涂敷设备:用于将正极、负极活性材料涂敷在铝箔或铜箔上,形成正负极片。
3.胶合设备:用于将正负极片与隔膜进行胶合,形成电芯。
4.折叠成型设备:将电芯进行折叠成型,常见的形式包括蛇形、Z形等。
5.包装设备:用于对电芯进行密封封装,通常包括壳体、端子和电芯贴片等部分。
6.电池测试设备:主要包括电芯充放电测试设备、电池性能测试设备等,用于对电池进行性能测试和质检。
7.组装设备:用于将电芯与保护板、电池管理系统等组装在一起,形成最终的锂电池产品。
8.包装设备:对锂电池产品进行包装,通常采用塑料或铝膜包装。
9.分选设备:对锂电池进行分类,通常根据电压、容量等指标进行分拣。
三、锂电池生产线的工艺流程1.材料配料和预处理:将电池所需的正负极活性材料、导电剂、粘结剂等按照一定比例进行配料。
部分材料需要进行预处理,如球磨、干燥等。
2.涂敷:将正负极活性材料涂敷在铝箔或铜箔上,形成正负极片。
通常采用刮涂或测厚涂覆的方法。
3.预烘干:对涂敷好的正负极片进行预烘干,去除涂层中的溶剂。
4.胶合:将正负极片与隔膜进行胶合,形成电芯。
胶合的过程需要控制温度和湿度。
5.折叠成型:将胶合好的电芯进行折叠成型,形成蛇形或Z形的电芯结构。
6.密封封装:将折叠成型好的电芯进行密封封装,通常采用铝膜或塑料封装。
7.充放电测试:对封装好的电池进行充放电测试,检测电池的性能和质量。
8.组装:将电芯与保护板、电池管理系统等组装在一起,形成最终的锂电池产品。
9.包装:对锂电池产品进行包装,通常采用塑料或铝膜包装,以保证产品的安全运输。
10.分选:对电池进行分类,根据电压、容量等指标进行分拣,确保产品质量和性能。
这是一种典型的锂电池生产线工艺流程,具体的工艺流程和设备设施会根据实际情况而有所不同。
揭秘!锂电池制造工艺设计全解析

---------------------------------------------------------------最新资料推荐------------------------------------------------------ 揭秘!锂电池制造工艺设计全解析WORD 格式-可编辑揭秘!锂电池制造工艺全解析锂电池结构锂离子电池构成主要由正极、负极、非水电解质和隔膜四部分组成。
目前市场上采用较多的锂电池主要为磷酸铁锂电池和三元锂电池,二者正极原材料差异较大,生产工艺流程比较接近但工艺参数需变化巨大。
若磷酸铁锂全面更换为三元材料,旧产线的整改效果不佳。
对于电池厂家而言,需要对产线上的设备大面积进行更换。
锂电池制造工艺锂电池的生产工艺比较复杂,主要生产工艺流程主要涵盖电极制作的搅拌涂布阶段(前段)、电芯合成的卷绕注液阶段(中段),以及化成封装的包装检测阶段(后段),价值量(采购金额)占比约为(35~40%):(30~35)%:(30~35)%。
差异主要来自于设备供应商不同、进口/国产比例差异等,工艺流程基本一致,价值量占比有偏差但总体符合该比例。
专业知识--整理分享1/ 7WORD 格式-可编辑锂电生产前段工序对应的锂电设备主要包括真空搅拌机、涂布机、辊压机等;中段工序主要包括模切机、卷绕机、叠片机、注液机等;后段工序则包括化成机、分容检测设备、过程仓储物流自动化等。
除此之外,电池组的生产还需要 Pack 自动化设备。
锂电前段生产工艺锂电池前端工艺的结果是将锂电池正负极片制备完成,其第一道工序是搅拌,即将正、负极固态电池材料混合均匀后加入溶剂,通过真空搅拌机搅拌成浆状。
配料的搅拌是锂电后续工艺的基础,高质量搅拌是后续涂布、辊压工艺高质量完成的基础。
涂布和辊压工艺之后是分切,即对涂布进行分切工艺处理。
如若分切过程中产生毛刺则后续装配、注电解液等程序、甚至是电池使用过程中出现安全隐患。
因此锂电生产过程中的前端设备,如搅拌机、涂布机、辊压机、分条机等是电池制造的核心机器,关乎整条生产线的质量,因此前端设备的价值量(金额)占整条锂电自动化生产线的比例最高,约35%。
锂电池生产工序完全手册

锂电池生产工序完全手册锂离子电池是一个复杂的体系,包含了正极、负极、隔膜、电解液、集流体和粘结剂、导电剂等,涉及的反应包括正负极的电化学反应、锂离子传导和电子传导,以及热量的扩散等。
锂电池的生产工艺流程较长,生产过程中涉及有 50 多道工序。
锂电池按照形态可分为圆柱电池、方形电池和软包电池等,其生产工艺有一定差异,但整体上可将锂电制造流程划分为前段工序(极片制造)、中段工序(电芯合成)、后段工序(化成封装)。
由于锂离子电池的安全性能要求很高,因此在电池制造过程中对锂电设备的精度、稳定性和自动化水平都有极高的要求。
锂电设备是将正负极材料、隔膜材料、电解液等原料通过有序工艺,进行制造生产的工艺装备,锂电设备对锂电池性能和成本有重大影响,是决定因素之一。
按照不同工艺流程可将锂电设备分为前段设备、中段设备、后段设备,在锂电产线中,前段、中段、后段设备的价值占比约为4:3:3。
锂电池制造流程机器设备前段工序的生产目标是完成(正、负)极片的制造。
前段工序主要流程有:搅拌、涂布、辊压、分切、制片、模切,所涉及的设备主要包括:搅拌机、涂布机、辊压机、分条机、制片机、模切机等。
浆料搅拌(所用设备:真空搅拌机)是将正、负极固态电池材料混合均匀后加入溶剂搅拌成浆状。
浆料搅拌是前段工序的始点,是完成后续涂布、辊压等工艺的前序基础。
搅拌流程图涂布(所用设备:涂布机)是将搅拌后的浆料均匀涂覆在金属箔片上并烘干制成正、负极片。
作为前段工序的核心环节,涂布工序的执行质量深刻影响着成品电池的一致性、安全性、寿命周期,所以涂布机是前段工序中价值最高的设备。
转移式涂布机原理挤压式涂布机原理辊压(所用设备:辊压机)是将涂布后的极片进一步压实,从而提高电池的能量密度。
辊压后极片的平整程度会直接影响后序分切工艺加工效果,而极片活性物质的均匀程度也会间接影响电芯性能。
辊压机原理分切(所用设备:分条机)是将较宽的整卷极片连续纵切成若干所需宽度的窄片。
锂电池生产工艺流程及参考设备项目

锂电池生产工艺流程及参考设备项目一、引言:锂电池是一种通过将锂离子在正负极之间进行移动来储存和释放电能的装置。
随着电动汽车、智能手机等电子产品的普及,锂电池的需求量迅速增长,因此锂电池的生产工艺流程和相应的设备项目也越来越受到关注。
本文将介绍锂电池的生产工艺流程以及一些参考的设备项目。
二、锂电池生产工艺流程:1.材料准备:锂电池的主要材料包括锂合金、电解质、正负极材料等。
在制造锂电池之前,需要对这些材料进行处理和准备,确保其符合生产要求。
2.电池槽装配:将正负极板等材料按照一定的层次码放在电池槽里。
正负极板之间需要使用隔膜进行隔离,以防止短路。
3.浸渍和封装:将电池槽通过浸渍设备浸入电解液中,使电解液能够充分渗透到正负极材料之间。
然后,将浸渍后的电池槽进行封装,防止电解液的外泄。
4.真空充注:将封装好的电池槽通过真空充注设备进行充注。
真空充注可以确保电解液完全充满正负极之间的空隙,并排除其中的气泡。
5.焊接和连接:通过焊接设备将电池槽内的正负极板与电池盖连接起来,为电池提供电流通道。
6.容量测试:对焊接好的电池进行容量测试,以确保其符合相关标准和要求。
7.外壳组装:将容量测试合格的电池装入外壳,并进行外壳组装,包括密封、连接和固定等工作。
8.包装和检验:对组装好的锂电池进行包装和检验,确保产品的质量和安全性。
三、参考设备项目:1.浸渍设备:用于将电池槽浸入电解液中,确保电解液能够充分渗透到正负极材料之间。
常见的浸渍设备有浸液槽、浸渍机等。
2.真空充注设备:用于将封装好的电池槽进行充注,确保电解液完全充满正负极之间的空隙,并排除其中的气泡。
常见的真空充注设备有真空充注机、真空充注罐等。
3.焊接设备:用于将电池槽内的正负极板与电池盖连接起来,为电池提供电流通道。
常见的焊接设备有点焊机、搪焊机等。
4.容量测试设备:用于对焊接好的电池进行容量测试,以确保其符合相关标准和要求。
常见的容量测试设备有容量测试仪器、电池充放电测试系统等。
- 1、下载文档前请自行甄别文档内容的完整性,平台不提供额外的编辑、内容补充、找答案等附加服务。
- 2、"仅部分预览"的文档,不可在线预览部分如存在完整性等问题,可反馈申请退款(可完整预览的文档不适用该条件!)。
- 3、如文档侵犯您的权益,请联系客服反馈,我们会尽快为您处理(人工客服工作时间:9:00-18:30)。
目录索引
一、锂电设备行业全景 (2)
(一)锂电生产工艺及设备 (2)
(二)前段设备:生产效率提升,市场份额加速集中 (4)
(三)中段设备:电池形态迭代,卷绕+叠片成核心工艺设备 (9)
(四)后段设备:电池品质升级,化成分容设备重要性提升 (20)
一、锂电设备行业全景
(一)锂电生产工艺及设备
锂电池设备作为生产工艺设备,直接决定了锂电池的品质和一致性。
锂电池按照形
态可分为圆柱电池、方形电池和软包电池等,其生产工艺有一定差异,但大体上其
工艺流程可分为前端工序(极片制作)、中端工序(电芯制作)以及后端工序(化
成分容及电池组装)。
图1:锂电池生产工艺流程图
数据来源:高工锂电,钜大锂电,广发证券发展研究中心
锂电前段工艺的内容是极片制作,主要工序包括搅拌、涂布、辊压、分切、制片、
模切等过程,对应的主要设备包括真空搅拌设备、涂布设备、辊压设备、分切设备、
制片设备、模切设备等。
中段工艺的内容是电芯制作,主要工序包括卷绕/叠片、入
壳、点焊、烘烤、注液、封口、清洗等过程,对应的主要设备包括卷绕设备、叠片
设备、入壳设备、滚槽设备、封口设备、焊接设备等。
后段工艺的内容是电池组装,
主要工序包括化成分容、pack组装等过程,对应的主要设备包括化成分容柜、激光
点焊机等。
表1:锂电生产主要工艺、对应设备和国内相关企业
数据来源:赢合科技招股说明书,高工锂电,钜大锂电,广发证券发展研究中心
锂电前、中、后段设备的价值量占比分别约为35%、30%、35%。
其中前、中、后
段工艺最核心、价值量也最高的设备分别为涂布机、卷绕/叠片机、化成分容柜。
由
于锂离子电池的安全性能要求很高,因此在电池制造过程中对锂电设备的精度、稳定性和自动化水平都有极高的要求。
图2:锂电设备投资占比(2018)
图3:孚能科技生产设备价格(万元)
数据来源:高工锂电,广发证券发展研究中心 数据来源:孚能招股说明书,广发证券发展研究中心
(二)前段设备:生产效率提升,市场份额加速集中
锂电前段工艺的内容是极片制作,主要工序包括搅拌、涂布、辊压、分切、制片、模切等过程,对应的主要设备包括真空搅拌设备、涂布设备、辊压设备、分切设备、制片设备、模切设备等。
锂电前段工艺是后续生产工艺的基础,例如一旦分切过程中产生毛刺则后续装配、注电解液等程序、甚至是电池使用过程中都可能出现安全隐患。
因此锂电前段设备是电池制造的核心设备,影响到整条生产线的质量。
根据钜大锂电数据,前段设备的价值量占比约为35%。
图
4:锂电生产前段工艺
数据来源:高工锂电,广发证券发展研究中心
搅拌机10%
涂布机20%
辊压分切机
10%
制片模切机10%
卷绕/叠片机
20%
组装设备5%
干燥设备5%化成分容及检测设备20%
表2:锂电前段生产主要工艺、对应设备及国内相关企业
数据来源:赢合科技招股说明书,高工锂电,钜大锂电,广发证券发展研究中心
1.搅拌设备
图5:锂电生产搅拌工艺图6:先导智能搅拌机
数据来源:高工锂电,广发证券发展研究中心数据来源:公司官网,广发证券发展研究中心
浆料搅拌是指将正、负极固态电池材料混合均匀后加入溶剂搅拌成浆状。
根据起点锂电数据,目前锂电搅拌设备的国产率已超过95%,基本实现国产化。
同时,锂电搅拌设备领域逐渐形成两极分化的格局,尾部企业逐渐出清,市场份额向龙头集中的趋势愈发明显。
根据高工锂电数据,2018年搅拌设备行业排名前十企业已经占据90%的市场份额。
目前锂电搅拌领域的上市企业主要有先导智能、赢合科技、北方华创、金银河等。
2.涂布设备
极片涂布指将搅拌后的浆料均匀涂覆在金属箔片上并烘干制成正、负极片。
涂布是锂电生产前段工艺中的核心环节,直接决定锂电池的电芯容量、一致性、安全性等关键性能。
根据钜大锂电数据,在电池失效的所有原因中,涂布工艺不当的占比超过10%。
图7:锂电生产涂布工艺
数据来源:高工锂电,广发证券发展研究中心
涂布设备在前段工序中占地面积最大、价值量最高。
根据钜大锂电数据,2019年涂布设备领域国产化程度不断提升,国产涂布设备占比已超过80%。
但目前国内真正掌握涂布核心技术的企业较少,因此涂布设备高端市场仍无法完全实现国产替代。
同时,涂布设备领域市场集中化态势明显,根据钜大锂电数据,国内前五大涂布企业市场份额占国产总量达到60%以上。
目前,行业内产品口碑较好、排名靠前的涂布设备厂商包括先导智能、赢合科技(雅康精密)、璞泰来(新嘉拓)、科恒股份(浩能科技)、金银河等。
表3:锂电生产涂布设备主要企业及产品特性
双层狭缝式挤压涂布
双层宽幅高速挤压涂
新型高速宽幅双层挤
并联式双面同时挤压
数据来源:各公司官网,钜大锂电,广发证券发展研究中心
辊压工艺是指将涂布后的极片进一步压实,改变涂料物质的电化学性能来提高电池
的能量密度。
分切工艺是指将较宽的整卷极片连续纵切成若干所需宽度的窄片。
辊
压分切工艺的关键是极片表面光滑平整,无毛刺无翘曲,因此对设备的精度性能提
出了较高要求。
图8:锂电生产辊压工艺图9:锂电生产分切工艺
数据来源:高工锂电,广发证券发展研究中心数据来源:高工锂电,广发证券发展研究中心
我国锂电设备企业在辊压分切领域处于世界领先地位,部分技术指标优于日韩同类
企业。
同时,设备一体化、自动化升级是必然趋势,先导智能、科恒股份等企业已
经推出辊压分切一体机等产品,在提高一致性、生产效率、数据闭环等方面效果明
显。
根据钜大锂电预测,未来1-2年市场上集涂布辊压分条于一体的设备将得到广泛
应用。
图10:先导智能辊压分条一体机图11:赢合科技全自动分切机
数据来源:公司官网,广发证券发展研究中心数据来源:公司官网,广发证券发展研究中心
制片工艺是指对分切后的极片焊接极耳、贴保护胶纸、极耳包胶或使用激光切割成
型极耳等。
模切工艺是指将分切后的间隙涂布或连续涂布(单侧出极耳)的极片冲
切成型,用于后续的叠片工艺。
收卷式模切是指将成卷的连续涂布(两侧出极耳)
的极片,通过五金模完成极耳成型,然后收卷,用于后续的卷绕工艺。
传统的极耳成型设备主要为五金模切机,通过机械结构设计使用模具刀进行刚性裁
切。
随着激光应用扩展和成本下降,五金模切机已逐渐被激光极耳成型机取代。
其
工作原理是激光光束聚焦能量,按照设定程序,高速切割电极箔材。
与传统五金工
艺相比,其具备无耗材,速度快,切割质量稳定,设计灵活性高等优势。
图12:先导智能激光式极耳成型机图13:吉阳智能激光式极耳成型机
数据来源:公司官网,广发证券发展研究中心数据来源:公司官网,广发证券发展研究中心
目前制片、模切设备领域主要参与企业为先导智能、赢合科技、大族激光、吉阳智
能,以及日本西村、浅田、韩国PNT公司等。
与海外企业相比,国产设备具备性价
比高、售后服务成本低、元器件价格低廉、生产规模大、自动化少人化程度高等优
势,但在品牌知名度和高性能参数方面仍存在一定提升空间。
(三)中段设备:电池形态迭代,卷绕+叠片成核心工艺设备
锂电中段工艺的内容是电芯制作,主要工序包括卷绕/叠片、入壳、点焊、烘烤、注
液、封口、清洗等过程,对应的主要设备包括卷绕设备、叠片设备、入壳设备、滚
槽设备、封口设备、焊接设备等。
根据钜大锂电数据,中段设备的价值量占比约为
30%,主要集中于卷绕/叠片环节。
图
14:锂电生产中段工艺
表4:锂电中段生产主要工艺、对应设备及国内相关企业
1.卷绕设备
锂电生产的前段工序将极片制作完成后,下一步是制作电芯。
电芯制作方式可以分
为卷绕式和叠片式两种。
卷绕工艺是将原材料按负极、隔膜、正极、隔膜的顺序叠
在一起,把分条后的极片固定在卷针上,随着卷针转动将正极极片、负极极片以及
隔膜卷成电芯的工艺方式。
在这里极片的大小、卷绕的圈数等参数根据电池设计容
量来进行确定。