产品出厂检验控制流程精华版(样本)
产品出厂检验管理制度模版(三篇)

产品出厂检验管理制度模版一、目的和适用范围1. 本制度旨在规范和管理产品出厂检验的流程和要求,确保产品质量符合相关标准和要求。
2. 本制度适用于所有涉及产品出厂检验的部门和人员。
二、相关定义1. 产品出厂检验:指对产品进行全面检验,以确保产品的质量符合相关标准和要求。
2. 出厂检验报告:指对产品进行检验后所形成的文件,记录了产品的质量状况和检验结果。
三、检验依据1. 检验依据包括但不限于国家和行业相关标准、技术规范、合同要求等。
四、检验流程1. 产品制造完成后,由生产部门通知质量控制部门进行产品出厂检验。
2. 质量控制部门收到检验通知后,安排专人进行产品出厂检验,并填写出厂检验报告。
3. 出厂检验报告完成后,由质量控制部门提交给生产部门。
4. 生产部门按照检验报告中的检验结果,决定是否允许产品出厂。
5. 如产品未通过出厂检验,生产部门需按照质量控制部门的要求进行整改,并重新进行出厂检验。
五、检验要求1. 在产品出厂前,必须进行全面的出厂检验,确保产品质量符合相关标准和要求。
2. 检验过程中,应按照相关标准和要求进行检验项目的选择和抽样,并对产品进行严格的检验。
3. 检验要求包括但不限于外观质量、尺寸精度、功能性能等项。
4. 出厂检验报告应在检验完成后及时填写,并记录详细的检验项目和检验结果。
六、检验记录1. 出厂检验报告应包括以下内容:(1) 产品名称、型号、批次等基本信息。
(2) 检验项目和标准。
(3) 检验方法和仪器设备。
(4) 检验结果和评定。
(5) 不合格项的具体描述和处理意见。
(6) 检验日期和检验人员签名。
七、不合格品处理1. 如出现不合格项,生产部门应按照质量控制部门的指示进行处理,包括但不限于整改、返工、报废等。
2. 不合格品处理完成后,生产部门应重新进行出厂检验,直至合格为止。
八、培训和意识提升1. 公司应定期组织产品出厂检验相关知识的培训和学习,提高相关人员的技能和意识。
2. 公司应鼓励员工积极参与产品出厂检验实践,并进行经验分享和总结。
出厂检验操作规程
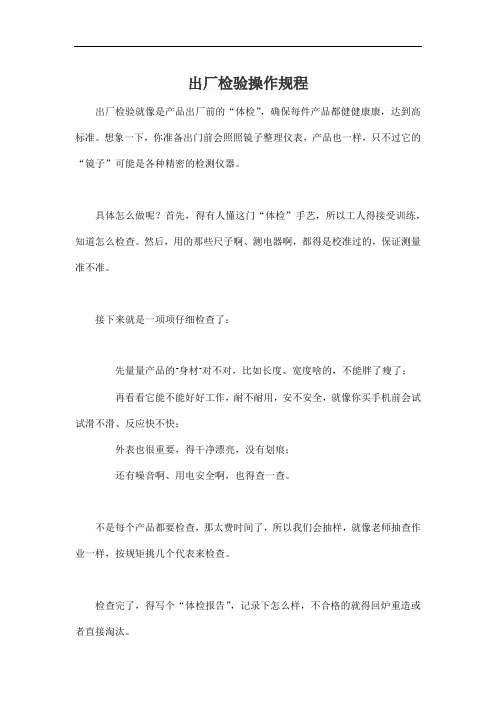
出厂检验操作规程
出厂检验就像是产品出厂前的“体检”,确保每件产品都健健康康,达到高标准。
想象一下,你准备出门前会照照镜子整理仪表,产品也一样,只不过它的“镜子”可能是各种精密的检测仪器。
具体怎么做呢?首先,得有人懂这门“体检”手艺,所以工人得接受训练,知道怎么检查。
然后,用的那些尺子啊、测电器啊,都得是校准过的,保证测量准不准。
接下来就是一项项仔细检查了:
先量量产品的“身材”对不对,比如长度、宽度啥的,不能胖了瘦了;
再看看它能不能好好工作,耐不耐用,安不安全,就像你买手机前会试试滑不滑、反应快不快;
外表也很重要,得干净漂亮,没有划痕;
还有噪音啊、用电安全啊,也得查一查。
不是每个产品都要检查,那太费时间了,所以我们会抽样,就像老师抽查作业一样,按规矩挑几个代表来检查。
检查完了,得写个“体检报告”,记录下怎么样,不合格的就得回炉重造或者直接淘汰。
最后,只有拿到“健康证”的产品,就是合格的,才能打包出厂。
而且啊,每个产品的“身份”咱们都得记清楚,万一以后发现问题,能马上找到它是哪批生产的。
这样持续做,还能从中学到东西,下次生产时做得更好,这就是出厂检验的大致流程,挺像咱们平时做事的逻辑,一步步来,确保万无一失。
产品出厂检验制度范本

产品出厂检验制度一、总则1.1 为了确保本企业生产的产品质量符合国家法律法规、标准和顾客的要求,预防和控制产品质量风险,特制定本产品出厂检验制度。
1.2 本制度适用于企业所有产品的出厂检验工作,包括原材料、半成品、成品等。
1.3 企业应建立健全质量管理体系,确保产品出厂检验工作的有效实施。
二、职责与权限2.1 质检部门负责产品出厂检验工作的组织与实施,对产品质量负责。
2.2 检验人员负责按照检验规程对产品进行检验,并对检验结果的真实性、准确性和及时性负责。
2.3 其他相关部门应协助质检部门做好产品出厂检验工作,确保产品质量。
三、检验流程3.1 产品检验3.1.1 检验人员应按照检验规程对产品进行逐项检验,包括但不限于外观、尺寸、性能、安全等项目。
3.1.2 检验过程中发现的异常情况,应及时报告给质检部门负责人。
3.1.3 检验合格的产品应贴上合格标签,并做好检验记录。
3.2 不合格产品处理3.2.1 不合格产品应隔离存放,并做好标识,防止误用或误入生产线。
3.2.2 质检部门应组织对不合格产品进行原因分析,制定纠正和预防措施,并跟踪实施效果。
3.2.3 对严重不合格的产品,应立即通知顾客,并按照《不合格品控制程序》进行处理。
四、检验记录与追溯4.1 检验记录应真实、完整、准确地反映产品出厂检验过程,包括检验日期、检验人员、检验项目、检验结果等信息。
4.2 检验记录应妥善保存,以便追溯和查询。
4.3 质检部门应定期对检验记录进行汇总和分析,持续改进产品质量。
五、检验设备与方法5.1 企业应配备满足产品出厂检验要求的设备、仪器和工具,确保其正常运行和准确性。
5.2 检验设备应按照相关规定进行定期检定和校准,保证检验结果的准确性。
5.3 企业应根据产品特点和标准要求,选择合适的检验方法,确保检验的有效性。
六、质量改进与培训6.1 企业应持续关注产品质量,针对存在的问题进行质量改进。
6.2 企业应定期对检验人员进行培训,提高其业务水平和素质。
出厂检验管理制度模版(2篇)

出厂检验管理制度模版制度目录第一章总则第二章组织与职责第三章出厂检验的程序第四章出厂检验的内容与要求第五章出厂检验的记录与报告第六章出厂检验的结果与处理第七章监督与评价第八章附则第一章总则第一条为加强对产品质量的控制,提高公司产品的质量水平,依据《中华人民共和国质量法》及相关法规文件,制定本出厂检验管理制度。
第二条出厂检验是指公司自行出厂前对产品的质量进行检验和评估的活动。
第三条出厂检验的目的是确保产品符合国家标准和客户的要求,并为公司决策提供可靠的质量数据。
第四条所有出厂的产品都必须经过出厂检验,并获得经过检验合格的证明。
第五条出厂检验工作由质量管理部负责组织实施,并得到公司领导的支持和监督。
第二章组织与职责第六条质量管理部是公司出厂检验工作的主要组织单位,负责出厂检验的计划制定、实施和监督。
第七条质量管理部应设立专门的出厂检验小组来负责具体的出厂检验工作,由质量管理部负责人指定。
第八条出厂检验小组的成员应具备相关专业知识和工作经验,并参加公司组织的出厂检验培训。
第九条出厂检验小组负责制定出厂检验计划、执行出厂检验、编制检验记录和报告、对不合格产品进行处理、跟踪产品质量问题等。
第三章出厂检验的程序第十条出厂检验工作按照以下程序进行:(一)接到产品出厂申请后,质量管理部组织出厂检验小组制定出厂检验计划。
(二)根据出厂检验计划,出厂检验小组进行必要的准备和安排。
(三)执行出厂检验计划,按照相关标准和要求对产品进行检验。
(四)对检验结果进行评估和判断,编制检验记录和报告。
(五)将检验结果和报告提交给相关部门,由质量管理部负责跟踪处理不合格产品。
(六)根据出厂检验结果,确定产品是否合格,并进行相应的处理。
(七)对出厂检验工作进行总结和评价。
第四章出厂检验的内容与要求第十一条出厂检验的内容包括但不限于以下方面:(一)外观检查:对产品的外观进行检查,判断是否存在明显的缺陷或瑕疵。
(二)尺寸与数量检验:按照产品规格要求,对产品的尺寸和数量进行检验。
产品检验控制程序-一稿

产品检验控制程序1. 目的规范产品的检验流程,提高检验的工作质量,确保原料质量满足生产要求,确保产品质量在生产过程中得到有效控制,预防不合格的原料或产品流入下一工序或者客户。
2. 适用范围本程序适用来料检验、工序检验、最种产品及出货检验活动的控制。
3. 职责3.1品管部负责产品的检验;3.2 品管部负责人负责检验报告的审核,生产总监对产品放行负责。
4. 术语和定义4.1来料检验:对于公司的外购原料及辅料,原料包括化学品,电子品单晶;辅料包括:溶剂,吸附剂,包材等。
4.1.1 IQC:Incoming Quality Control,来料质量控制。
FQC/OQC: Final/Outgoing Quality Control最终/出货质量控制4.1.2 抽样检测:按既定的抽样规则从一批待检样品抽出一部分用来检测,检测结果与判定标准作比较,继而判定该批产品是否合格的过程。
4.2工序检验:产品在制造过程中的检测。
4.2.1 IPQC:In Process Quality Control,过程控制。
4.2.2 过程巡检员:负责生产过程巡回检查的人员,一般由QA负责。
4.3产品检验:产品生产完成后,对产品进行入库前品质检验。
4.4出货检验:发货前对产品进行发货指标要求的项目进行检验。
5.流程5.1来料检验:5.1.1 供应商交货时,须附带《送货单》,交仓管员清点数量、核对品名、型号、规格、重量后暂收并放置于“待检区”。
5.1.2仓管员通知品质部作进料检验,免检材料直接入库。
5.1.3品质部依相应的《IQC管理制度》的相关规定对物料实施检验,将检验情况记录于检验结果中。
5.1.4无法作检验之物料或物料检验项目,供应商必须附出公司证明及检验合格证明文件作为凭据或提供质量保证协议/合同。
5.1.5质检员有独立判定权,但必须以《检验标准》的相关规定和材料样品作为检验依据。
5.1.6 检验合格,贴标识,由仓管员将材料移至仓库对应的区域备用,检验不合格,则依《不合格品控制程序》处理。
产品出厂检验流程详解

产品出厂检验流程详解1. 预检准备:检验人员根据产品的企业标准或合同规定准备好相应的检验仪器设备,确认其准确性和有效性。
按照企业标准中的试验方法设置和校准检测设备,并确保所有检验所需的工装器具齐全。
2. 首件检验(FAI):对批量生产的第一件产品进行全面的尺寸、性能、外观等各项指标的检验,以验证生产工艺的正确性。
3. 过程控制与自检互检:在生产过程中实行“三检制”,即操作者进行自检、班组间进行互检、专职质检员进行专检,保证每一道工序的产品质量都得到监控。
执行首件必检、巡回抽检以及必要时的全检制度,对生产线上发现的不合格品及时隔离并记录。
4. 最终检验:外观检查:检验产品的表面质量、颜色、纹理、标志、包装等是否符合标准,无划痕、变形、破损等问题。
性能测试:按照产品技术规格书要求,对产品的电气性能、机械性能、环境适应性、安全性等进行严格的实验室测试。
尺寸测量:使用卡尺、测膜仪、检测平台等工具对产品关键部位的尺寸、厚度、直线度等进行精确测量。
功能验证:对于电子产品、机械设备等需要确保其功能正常,进行实际操作验证。
5. 质量判定:根据检验结果与规定的质量标准进行比较,判断产品是否合格。
对不合格项目记录详细信息,并分析原因。
对于质量问题严重的产品,需填写《不合格报告》,并由质量管理部组织评审,决定是否返修或报废。
6. 记录与反馈:记录所有的检验数据、结果及处理措施,形成完整的检验记录。
反馈给相关部门,用于持续改进工艺流程和产品质量。
7. 放行与签发合格证:经过最终检验合格的产品,由质检部门出具产品质量合格证明或标签,并办理出厂放行手续。
仓储部门在收到合格证后安排发货,并确保包装完好,避免运输过程中造成二次损伤。
8. 批次管理与追溯:对出厂产品实施批次管理和条码追踪系统,确保任何质量问题发生时能够快速定位到具体批次,便于召回和追溯。
产品出厂检验方法
产品出厂检验方法我司应用工程控制理念实时监测产品制造的品质,从半成品控制到成品检验入库,我们设置了多道生产控制检验程序。
当产品的各项性能指标符合国家标准或者客户需求时,公司品质管理部方批准入库。
故我司产品在出厂之前经历层层把关,严格检验,在保证品质的前提之下,建立完善的成品检验标准。
我司产品及其附着落料检验标准程序如下:1.目的保证出厂产品进行了规定的检验和试验,达到有关国家标准和客户的要求。
2.范围适用于公司生产的车牌级产品成品的最终检验。
3.职责1)品管部负责产品出厂测试,编制出厂检验报告,如实记录测试结果,并对测试结论负责。
技术部现场监督,确保检验报告真实有效。
2)总经理对产品检验报告有最终审核权。
工作程序1)检验准备按《成品检验标准》备好相应的检验仪器,确保其可靠、齐全、有效。
成品检验按《成品检验标准》全检,并执行零缺陷的规定。
每一批次的产品,入库发放前都要进行成品检定。
2)检验与记录测试人员严格按国家行业标准GA36-2018《中华人民共和国机动车号牌》、GA 666-2008《机动车号牌用产品》和《成品检验标准》和检验项目和方法逐项检验,不得漏项漏检。
成品检验报告字迹清晰、工整,填写内容完整、齐全。
检验报告作为该批次产品的质量技术档案要长期保存,以保持其可追溯性。
车牌级产品一般保留期为5年,顾客有要求的或特殊使用的产品检验报告,要长期保留或按顾客要求保留。
3)合格成品的处理成品检验合格后,发放合格证,并入库保管。
每一产品入库时出具产地说明、出厂检验报告和产品质量合格证,并在产品外包装上标明产品名称,规格,数量,生产日期,批次等信息。
4)不合格品成品的处理成品经检验判定为不合格的,返技术部整改,技术总监执检验报告,负责产品整改的组织工作。
产品整改完成后,按本规程要求重新进行产品检验。
若仍不能通过产品检验,则进入产品报废申请程序。
产品品质检验流程标准模板(完整版)
XXX实业有限公
司
产品品质检验流程指导书
检验流程指导图异常处理责任人说明
鑫
素
材
生
分班终抽检I NG
操作员
半
成
品
加
外发加工回]
半成品组
装)抽样检验标准
操作员分班终抽检,
抽样检验标准
成品出货库存成品检验I
包装检验
产品标签核对
首件检验:首件是产品
能不能生产的根本要
求,切勿马虎导致整批
产品报废!无论是调机
技术员还是品管,都对
首件的检验附有不可
推卸的责任;
巡检检验:理论上品管
负责巡检,但是实际生
产参入中,操作员参入
在生产中,对产品的巡
检也附有不可推卸的
责任,产品都是从操作
员手中流出,在有多余
的操作时间时,应该予
以巡检广品,在无多余
时间时,对产品的外观
应予以实时目测初步
判定;
抽检:抽检分班次的抽
检,合格后方能倒入一
起;出货时抽检严格依
照抽样标准判定,做好
出货检验报告;
送货单核对
I
品
质
记
录
包装员
发货员
异常处理:遵循追求
零缺陷的方针进行管
控,发现异常即进行
返工全检,最后出货
时由出货检验员进行
抽检OK出货。
产品检验控制程序
精心整理1目的为验证原材料、半成品、成品的质量特性是否符合规定要求,确保经检验合格的原材料、半成品、成品投入使用。
2适用范围适用于进料、制程及最终成品的检验。
3职责3.1仓库3.23.33.43.544.14.24.34.44.5特采:质量不完全合乎标准的原材料或器件,其缺陷不对最终产品质量产生决定性影响,经技术部和相关部门评估风险后,或征得客户意见,同意采用选别、让步接收等方法进行处理。
4.6原材料:指生产过程所需要的原料,包括主要材料、辅助材料、外购半成品、委外加工半成品、修理用备件、包装材料等。
4.7在制品:从一个生产工序转给另一个生产工序继续加工的自制半成品以及不能单独计算成本的自制半成品。
4.8半成品:指经过一定生产过程并已检验合格,但尚未制造完工成为成品,仍需进一步加工的中间产品。
4.9成品:指已完成全部生产过程,按规定标准检验合格,可供销售的产品。
4.10紧急放行:生产急需来不及验证就发放生产部使用。
5作业程序5.1进料点收、送检:委外/供应厂商交货时仓管直接带供应商将货交至“暂收区”,并需随货附《送货单》,仓库依本公司《物料需求单》之规格、数量点收,核对无误后在供应商《送货单》上盖本公司5.25.2.2A.B.5.2.3后收5.2.45.2.5ICP5.35.3.1生产部在每批生产前均需制作首件,填写《首件确认记录表》通知品质部和PIE工程师确认。
5.3.2品质部以BOM、《IPQC检验作业指导书》等为依据对生产部在制品进行检验或测试。
a.首件检验:生产部每条生产线开始生产或更换产品品种,或调整工艺后生产的第一件产品,经生产自检合格后,由IPQC根据相应的检验标准进行检验,填写《首件确认记录表》;如不合格应要求返工或重新生产,直到检验合格,品质部签字确认后才能批量生产。
b.巡检:生产过程中,IPQC应对生产部操作员完成该工序后的产品进行抽检,并将结果及时反馈给生产部;发现不合格应执行《不合格品控制程序》。
出厂检验制度流程
成品出厂检验制度1、总则1.1成品出厂检验员,业务上由技术部负责指导、负责原料验收、工序监测、卫生控制、出厂检验的监督、检查工作。
1.2检验员应坚持原则,责任心强,熟悉产品性能,技术标准及生产工艺要求,了解主要产品的加工方法,技术要求,营养特性等作用,掌握一般测量基础知识,专用量具试验设备的使用方法。
2、检验工作2. 1严格执行“成品出厂检验规则”和“不合格品管理制度”,督促车间生产是否按工艺、、技术文件和标准进行生产和进行自检、互检、送检。
2.2随时巡检各生产工序,对关键工序重点检查,发现违反生产制度和不合格品时,有权制止和责令责任人返修,及时向上级反映问题。
2. 3产品加工完入库前,按成品出厂检验细则的项目要求进行全检和抽查,经检验合格后方可判该批产品合格,并签发产品合格证和在交库单上签章。
2. 4检验工作应严肃认真,测量准确、数据真实、结论正确,主动配合车间进行全部出厂检验。
2. 5销售回退产品及时进行检验,将检验结论通知销售部门。
3、不合格品的处理3.1在生产中发现的质量问题,应及时分析原因,向技术部及车间反映,经技术、生产部门确定,属一般不合格还是严重不合格的质量问题,分别办理回收处理或是报废手续。
3.2协助车间、仓库做好回收产品和报费产品的隔离工作。
4、按要求作好各项检测原始记录,项目齐全、数据准确,并且做好归档工作。
5、检验用原始记录和工艺技术资料不得遗失,检测设备器具应正确使用,使用前应检查其是否准确。
6、保持工作场地整洁,原始记录不得涂改,检测器具妥善保管,坚持文明生产,安全生产。
4.2组织召开质量工作分析会,提出整改措施,检查生产执行情况。
5、生产部质量责任5.1对生产组织过程中的质量工作负责,制定年、度、季、月生产计划,行使生产指挥调度权,严守工艺纪律和质量管理制度。
5.2参加组织质量分析会监督实施整改措施情况。
6、技术部质量责任6.1对新产品研制,工艺实施及工艺技术资料的正确统一,完整性负责,组织解决产品生产过程中出现的质量问题。
- 1、下载文档前请自行甄别文档内容的完整性,平台不提供额外的编辑、内容补充、找答案等附加服务。
- 2、"仅部分预览"的文档,不可在线预览部分如存在完整性等问题,可反馈申请退款(可完整预览的文档不适用该条件!)。
- 3、如文档侵犯您的权益,请联系客服反馈,我们会尽快为您处理(人工客服工作时间:9:00-18:30)。
产品出厂检验控制流程
1目的
确保公司内部加工生产的整机或组件产品的出厂检验处于受控状态。
2适用范围
公司内部生产的用于销售的整机或组件产品,以及XX产品。
3术语和定义
出厂检验:包括安全测试、FQC检验和OQC检验。
4职责与权限
4.1FQC/OQC:负责整机或组件产品的检验。
4.2质量控制部:经理或由其授权人员负责销售整机或模块产品合格入库的批准放行。
4.3物流部:负责每月统计成品库存并将需重工机器送检。
4.4计划部:负责开出对成品库整机复检的重工单。
4.5XXXX检验人员:负责XXX产品的检验。
5内容及流程
5.1FQC检验:
5.1.1送检
5.1.1.1组件产品送检:产品线装配组或调试组填写《产品送检/入库交接单》随组件产品送
至FQC•工序。
5.1.1.2整机送检:调试组将经检测合格的整机及所有涉及整机追溯的信息(如追溯表、整
机故障技术分析报告等)随机送至FQC工序。
5.1.2检验
5.1.2.1组件产品检验:按相应检验规范检验,检验合格后流到下工序,检验过程中发现的
不合格品处理按《制程不合格品处理规范》执行。
检验记录应予以保持。
5.1.2.2整机检验:
A、整机安全检验:按《通用各机型整机批量安全检验规范》的要求检验。
检验合格后流
到下工序,检验过程中发现的不合格品处理按《制程不合格品处理规范》执行。
检验记
录应予以保持。
B、整机常规检验:按各机型对应整机FQC检验规范或结合各产线通用FQC检验操作指
南进行检验作业,整机外观参照《XX产品通用整机外观检验规范》的要求检验。
检验
合格后流到下工序,检验过程中发现的不合格品处理按《制程不合格品处理规范》执行。
检验记录应予以保持。
C、整机配置、标识检验:按各订单要求配置逐一确认,对机器标贴、专利标贴以及特殊
的标贴、语言和丝印、硬件配置等需特别关注,具体可根据各生产线自行制定的《____
工序检查表》内容进行并保持记录。
监护产品FQC按《通用监护产品FQC扫描检验工
艺》执行。
检验合格后流到下工序,不合格品的处理按《制程不合格品处理规范》执行。
5.1.2.3整机批量性能外观检验
a)FQC检验员按《通用产品整机批量性能外观检验抽样规范》(Q-T-123 )从合格整机中
抽取样本进行整机性能外观的批量检验,检验记录由质量控制部相关授权人员进行审核,
给出是否合格放行的处理意见。
b)当出现不合格时,按《制程不合格品处理规范》处理,待原因分析出来后,需经过评审
决定本批产品的处理。
c)如果涉及整批机器的返工或让步放行,需由产品工程师组织相关人员讨论处理方案,不
良处理后复检合格并经质量控制部审核批准后方可放行。
d)各检验过程需检查和复核“产品追溯表”的相关信息。
5.1.2.4检验记录归档:检验合格与不合格的记录都要予以保持并归档,包括《产品送检/入
库交接单》、《FQC检验记录表》、《XX类产品整机检验记录》、《整机抽检记录》以及
《整机故障技术分析报告》等。
原则上《产品送检/入库交接单》必须与质量记录一
起归档,并保证其对应关系,记录的归档应便于查询。
5.1.2.5填写交接单:FQC根据检验记录填写《产品送检/入库交接单》并登记台帐。
《产品
送检/入库交接单》质检编号栏填写《FQC检验记录表》编号。
5.1.3标识:产品的标识按《生产过程标识管理规范》的要求执行。
5.1.4审核:《产品送检/入库交接单》及《FQC检验记录表》、《XX类产品整机检验记录》、《整
机抽检记录》由FQC送质量控制部审核,以确认产品的最终检验结果,并由质量控制部相关授权人员依据提供的记录判断检验过程是否正确选用了DMR要求的检验标准、合格的验收设备以及提供的验收记录是否齐全、记录填写是否正确等决定是否准予合格放行。
5.2OQC检验
5.2.1送检:对于组件产品由包装作业员填写《产品送检/入库交接单》,整机则直接使用FQC
提供的《产品送检/入库交接单》送OQC检验。
5.2.2检验审核及标识:包装OQC按《通用XX整机包装检验规范》对包装进行检验,检验过
程中发现的不合格品处理按《制程不合格品处理规范》执行。
检验记录应予以保持。
5.2.3检验记录归档:检验合格与不合格的记录都要予以保持并归档,《XX产品追溯表》由OQC
归档保存并按照《产品电子档案管理规范》的要求转化成“产品电子档案”。
5.3XXC产品检验
5.3.1生产检验:按《XXXX生产检验规范》的要求对试剂进行检验。
检验合格后流到下工序,
检验过程中发现的不合格品处理按《试剂不合格品处理规范》执行。
检验记录应予以保持。
5.3.2出厂检验:按《XXXX出厂检验规范》的要求对试剂进行检验,并按照《XX包装标志、
标签和说明书检验规范》对试剂包装进行检验。
检验合格后出货,检验过程中发现的不合格品处理按《XX不合格品处理规范》执行。
检验记录应予以保持。
5.3.3留样检验:按《XX留样检验规范》的要求对留样试剂进行检验,且每周需对留样稀释液
本底进行跟踪。
检验过程中发现的不合格情况处理按《XX不合格品处理规范》执行。
检验记录应予以保持。
5.3.4型式检验:根据《XXXX型式检验规范》的要求视实际情况(如新产品、重大工艺变更、
原材料变更等情况)需对试剂进行型式检验。
检验合格后流到下工序,检验过程中发现的不合格品处理按《XX不合格品处理规范》执行。
检验记录应予以保持。
5.3.5检验记录归档:检验合格与不合格的记录都要予以保持并归档,包括《XXXX生产检验记
录表》、《XXXX型式检验记录表》、《XXXX出厂检验记录表》、《XX包装标志、标签和说明书检验记录表》、《XX留样检验记录表》、《样本底跟踪记录表》以及《不合格品处理记录表》等。
记录的归档应便于查询。
5.3.6审核:《XXXX生产检验记录表》、《XXXX出厂检验记录表》、《XX试剂包装标志、标签和
说明书检验记录表》由试剂厂送质量控制部审核,以确认产品的最终检验结果,并由质量控制部相关授权人员依据提供的记录判断检验过程是否正确选用了DMR要求的检验标准、合格的验收设备以及提供的验收记录是否齐全、记录填写是否正确等决定是否准予合格放行。
试剂生产的具体控制流程内容即流程图参见《XX生产控制程序》()的说明。
6流程图
6.1流程图生产送检/入库流程(不适用于XX产品)7相关文件记录
7.1《产品送检/入库交接单》QW/R11N02.02.01 7.2《制程不合格品处理规范》QW/S12N01-02 7.3《品质异常报告》QW/R13.02.01 7.4《生产过程标识管理规范》QW/S14-08
7.5《产品电子档案管理规范》QW/S15N04-01 7.6 《XX生产控制程序》QW/P11N08
7.7 《XX不合格品处理规范》QW/S16-21-SJ
流程图生产送检/入库流程。