晶间腐蚀性能弯曲评价影响实证探讨
铝合金晶间腐蚀报告范本

铝合金晶间腐蚀报告范本
报告背景:近期,我们的铝合金零件出现了晶间腐蚀现象,导致部分产品质量问题。
为了解决这一问题,我们进行了调查并制作了该报告,以便更好地了解问题根源并采取相应的措施。
调查方法:通过对受影响的铝合金零件进行实际观察及实验分析,我们发现晶间腐蚀主要发生在铝合金的晶界处。
同时,我们还分析了铝合金材料的成分、制造过程及使用环境等方面的因素。
调查结果:我们的调查结果表明,铝合金零件出现晶间腐蚀的原因主要是由于材料中含有较高的铜元素,这种元素会使得晶界处形成脆性相,从而导致晶间腐蚀的发生。
此外,制造过程中的热处理不当也会加重此类问题的发生。
另外,使用环境中的氯离子也是晶间腐蚀的加速因素。
解决方案:为了解决晶间腐蚀问题,我们需要采取以下措施:
1. 优化材料成分,减少铜等对晶间腐蚀的影响。
2. 改进铝合金的制造工艺,避免热处理不当引起的问题。
3. 在使用环境中注意去除氯离子等有害物质,从而减少晶间腐
蚀的发生。
结论:晶间腐蚀是铝合金零件质量问题的一个重要方面,需要我们在制造、使用等方面都密切注意。
通过本次调查,我们对该问题有了更深入的了解,并提出了相应的解决方案,以期更好地保障铝合金零件的质量和可靠性。
- 1 -。
材料化学失效与控制实验:晶间腐蚀
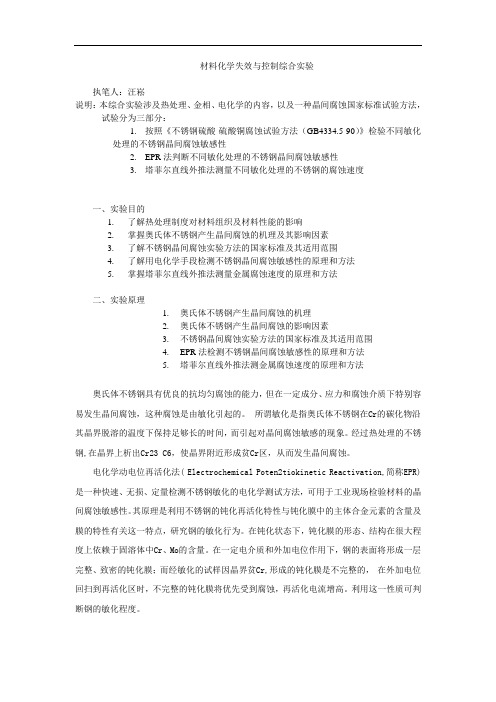
材料化学失效与控制综合实验执笔人:汪崧说明:本综合实验涉及热处理、金相、电化学的内容,以及一种晶间腐蚀国家标准试验方法,试验分为三部分:1.按照《不锈钢硫酸-硫酸铜腐蚀试验方法(GB4334.5-90)》检验不同敏化处理的不锈钢晶间腐蚀敏感性2.EPR法判断不同敏化处理的不锈钢晶间腐蚀敏感性3.塔菲尔直线外推法测量不同敏化处理的不锈钢的腐蚀速度一、实验目的1.了解热处理制度对材料组织及材料性能的影响2.掌握奥氏体不锈钢产生晶间腐蚀的机理及其影响因素3.了解不锈钢晶间腐蚀实验方法的国家标准及其适用范围4.了解用电化学手段检测不锈钢晶间腐蚀敏感性的原理和方法5.掌握塔菲尔直线外推法测量金属腐蚀速度的原理和方法二、实验原理1.奥氏体不锈钢产生晶间腐蚀的机理2.奥氏体不锈钢产生晶间腐蚀的影响因素3.不锈钢晶间腐蚀实验方法的国家标准及其适用范围4.EPR法检测不锈钢晶间腐蚀敏感性的原理和方法5.塔菲尔直线外推法测金属腐蚀速度的原理和方法奥氏体不锈钢具有优良的抗均匀腐蚀的能力,但在一定成分、应力和腐蚀介质下特别容易发生晶间腐蚀,这种腐蚀是由敏化引起的。
所谓敏化是指奥氏体不锈钢在Cr的碳化物沿其晶界脱溶的温度下保持足够长的时间,而引起对晶间腐蚀敏感的现象。
经过热处理的不锈钢,在晶界上析出Cr23 C6,使晶界附近形成贫Cr区,从而发生晶间腐蚀。
电化学动电位再活化法( Electrochemical Poten2tiokinetic Reactivation,简称EPR)是一种快速、无损、定量检测不锈钢敏化的电化学测试方法,可用于工业现场检验材料的晶间腐蚀敏感性。
其原理是利用不锈钢的钝化再活化特性与钝化膜中的主体合金元素的含量及膜的特性有关这一特点,研究钢的敏化行为。
在钝化状态下,钝化膜的形态、结构在很大程度上依赖于固溶体中Cr、Mo的含量。
在一定电介质和外加电位作用下,钢的表面将形成一层完整、致密的钝化膜;而经敏化的试样因晶界贫Cr,形成的钝化膜是不完整的,在外加电位回扫到再活化区时,不完整的钝化膜将优先受到腐蚀,再活化电流增高。
不锈钢晶间腐蚀试验与分析

不锈钢晶间腐蚀试验与分析一、实验目的1.掌握影响奥氏体不锈钢晶间腐蚀的因素;2.掌握不锈钢晶间腐蚀试验的方法;二、实验原理18-8 型奥氏体不锈钢在许多介质中具有高的化学稳定性,但在400-800℃范围内加热或在该温度范围内缓慢冷却后,在一定的腐蚀介质中易产生晶间腐蚀。
晶间腐蚀的特征是沿晶界进行浸蚀。
使金属丧失机械性能,致使整个金属变成粉末。
1.晶间腐蚀产生的原因一般认为在奥氏体不锈钢中,铬的碳化物在高温下溶入奥氏体中,由于敏化(400-800℃)加热时,铬的碳化物常于奥氏体晶界处析出,造成奥氏体晶粒边缘贫铬现象,使该区域电化学稳定性下降,于是在一定的介质中产生晶间腐蚀。
为提高耐蚀性能,常采用以下两种方法。
(1)将 18-8 型奥氏体不锈钢碳含量降至 0.03%以下,使之减少晶界处碳化物析出量,而防止发生晶间腐蚀。
这类钢成称为超低碳不锈钢,常见的有00Cr18Ni10。
(2)在 18-8 型奥氏体不锈钢中加入比铬更易形成碳化物的元素钛或铌,钛或铌的碳化物较铬的碳化物难溶于奥氏体中,所以在敏化温度范围内加热时,也不会于晶界处析出碳化物,不会在腐蚀性介质中产生晶间腐蚀。
为固定18-8 型奥氏体不锈钢中的碳,必须加入足够数量的钛或铌,按原子量计算,钛或铌的加入量分别为钢中碳含量的4-8 倍。
2.晶间腐蚀的试验方法晶间腐蚀的试验方法有 C 法、 T 法、 L 法、 F 法和 X 法。
这里介绍容易实现的 C法和 F法。
试样状态:(1)含稳定化元素( Ti 或 Nb)或超低碳( C≤ 0.03%)的钢种应在固溶状态下经敏化处理的试样进行试验。
敏化处理制度为 650℃保温 1 小时空冷。
(2)含碳量大于 0.03%不含稳定化元素的钢种,以固溶状态的试样进行试验;用于焊接钢种应经敏化处理后进行试验。
(3)直接以冷状态使用的钢种,经协议可在交货状态试验。
(4)焊接试样直接以焊后状态试验。
如在焊后要在 350℃以上热加工,试样在焊后要进行敏化处理。
焊道晶间腐蚀研究报告
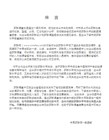
0Cr18Ni9与1Cr18Ni9Ti、00Cr18Ni10N、00Cr19Ni10的化学成分比较见表1(参考标准GB 4239-1991 不锈钢和耐热钢冷轧钢带)。
表1 常见奥氏体不锈钢化学成分
含量% 元素 C Mn Si P S Cr Ni N
国内牌号 美国
牌号
铬是决定不锈钢耐腐蚀性能的最基本元素,使其有耐腐蚀性能。在氧化性介质中,铬能使钢的表面很快形成一层实际为腐蚀介质不能透过和不溶解的富铬的氧化膜,这层氧化膜很致密,并与金属基本结合得很牢固,保护钢免受外界介质进一步氧化浸蚀(钝化的机理);铬还能有效地提高钢的电极电位,当含铬量不低于12%原子时,可使钢的电极电位发生突变,由负电位升到正的电极电位,可显著提高钢的耐蚀性。
2) 降低碳的含量,选用超低碳的不锈钢,如00Cr18Ni10N、00Cr19Ni10、00Cr17Ni14Mo2、00Cr17Ni13Mo2N等,从根本上减弱形成碳铬化合物的机会,从而消除晶间腐蚀。
奥氏体不锈钢经固溶处理后,其力学性能比较如表2(参考标准GB 4239-1991 不锈钢和耐热钢冷轧钢带)所示,可见其强度和塑性非常接近,而所有的奥氏体不锈钢均不能热处理强化,只能通过冷作硬化以提高强度、硬度,在产品性能允许的情况下选用适当的材料,同时避免在晶间腐蚀的敏感温度区间的停留时间,这是避免晶间腐蚀最有效的办法。
1) 加入与碳亲和力比铬还要强的元素钛和铌,钛和铌常用来固定钢中的碳,提高不锈钢抗晶间腐蚀的能力,但是由于钛和铌都是稀有金属,实际不锈钢中钛和铌的含量都不高,如0Cr19Ni10NbN、1Cr18Ni9Ti、0Cr18Ni10Ti、0Cr18Ni11Nb等即使均含有钛和铌,但从实际工艺应用中发现,依然有晶间腐蚀,特别是国产材料晶间腐蚀较严重,这也是GB 4239-1991、GB 1220-1992等国家标准中特别注明不推荐使用1Cr18Ni9Ti的原因,而在最新的GB/T 3280-2007、GB/T 4237-2007、GB/T 1220-2007等国家标准中均取消了1Cr18Ni9Ti这一奥氏体不锈钢牌号;
《微量La的添加对薄壁TU1纯铜管高温退火后退火孪晶及弯曲和耐蚀性能的影响》范文

《微量La的添加对薄壁TU1纯铜管高温退火后退火孪晶及弯曲和耐蚀性能的影响》篇一微量La的添加对薄壁TU1纯铜管高温退火后退火孪晶及弯曲与耐蚀性能的影响一、引言在金属材料的研究中,微量元素的添加对材料性能的改善具有重要作用。
本文以TU1纯铜管为研究对象,探讨微量La的添加对其在高温退火后孪晶结构、弯曲性能及耐蚀性能的影响。
通过实验分析,期望为铜及铜合金的优化设计和应用提供理论依据。
二、实验材料与方法1. 材料准备实验选用TU1纯铜管作为基体材料,通过向其中添加微量La元素,制备出含有La的纯铜合金管材。
2. 实验方法(1)退火处理:将试样在高温下进行退火处理,观察其孪晶结构的变化。
(2)弯曲性能测试:对退火后的试样进行弯曲测试,分析其弯曲性能。
(3)耐蚀性能测试:通过电化学腐蚀测试,分析试样的耐蚀性能。
三、微量La的添加对孪晶结构的影响经过高温退火处理后,含有微量La的纯铜管材表现出更稳定的孪晶结构。
La元素的添加有助于提高铜的晶格稳定性,减少晶界迁移和再结晶过程,从而在退火过程中形成更细小的孪晶结构。
这一现象表明,微量La的添加有助于提高纯铜的力学性能和耐热性能。
四、微量La的添加对弯曲性能的影响La元素的添加显著提高了薄壁TU1纯铜管的弯曲性能。
实验结果表明,含有微量La的纯铜管在弯曲过程中表现出更好的塑性变形能力和抗裂性能。
这主要是由于La元素能够有效地细化晶粒,提高材料的韧性,从而改善了纯铜管的弯曲性能。
五、微量La的添加对耐蚀性能的影响电化学腐蚀测试结果表明,微量La的添加显著提高了薄壁TU1纯铜管的耐蚀性能。
La元素能够与铜基体形成稳定的化合物,提高材料表面的致密性和均匀性,从而增强其抗腐蚀能力。
此外,La元素还能细化晶粒,减少晶界处的缺陷和杂质,进一步提高纯铜管的耐蚀性能。
六、结论通过实验分析,我们可以得出以下结论:1. 微量La的添加有助于改善薄壁TU1纯铜管的高温退火后孪晶结构,使其更加稳定和细小。
晶体硅太阳电池片弯曲度研究进展
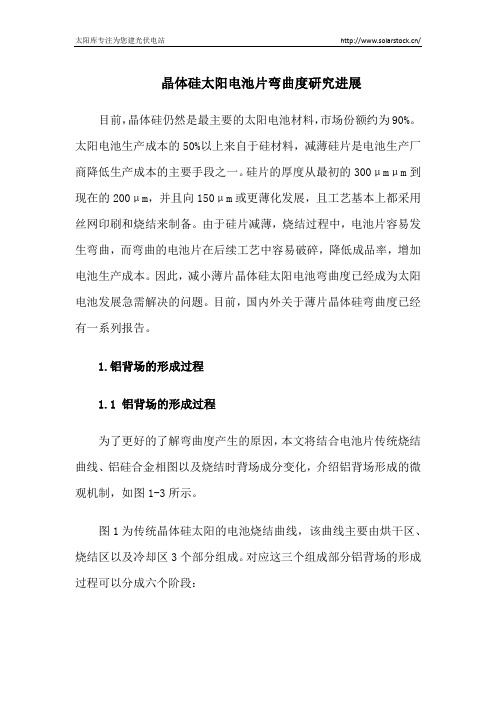
晶体硅太阳电池片弯曲度研究进展目前,晶体硅仍然是最主要的太阳电池材料,市场份额约为90%。
太阳电池生产成本的50%以上来自于硅材料,减薄硅片是电池生产厂商降低生产成本的主要手段之一。
硅片的厚度从最初的300μmμm到现在的200μm,并且向150μm或更薄化发展,且工艺基本上都采用丝网印刷和烧结来制备。
由于硅片减薄,烧结过程中,电池片容易发生弯曲,而弯曲的电池片在后续工艺中容易破碎,降低成品率,增加电池生产成本。
因此,减小薄片晶体硅太阳电池弯曲度已经成为太阳电池发展急需解决的问题。
目前,国内外关于薄片晶体硅弯曲度已经有一系列报告。
1.铝背场的形成过程1.1 铝背场的形成过程为了更好的了解弯曲度产生的原因,本文将结合电池片传统烧结曲线、铝硅合金相图以及烧结时背场成分变化,介绍铝背场形成的微观机制,如图1-3所示。
图1为传统晶体硅太阳的电池烧结曲线,该曲线主要由烘干区、烧结区以及冷却区3个部分组成。
对应这三个组成部分铝背场的形成过程可以分成六个阶段:第一阶段,有机溶剂溶剂挥发,如图3(1)所示,温度范围100~200℃。
生产晶体硅太阳电池的铝浆通常由1到10μm的超细铝粉、玻璃粉、有机粘合剂以及有机溶剂四部分组成。
在烘干阶段,铝浆中的有机溶剂大量挥发,从而使印刷在硅片表面的铝浆成为一种多孔的结构,该多孔的结构由有机粘合剂粘结在硅片的表面,铝浆的印刷量一般在0.7mg/cm2,厚度在40μm左右;第二阶段,铝融化侵蚀硅片表面,如图3(2)所示,温度在铝的熔点660℃,如图1中的第一个平台。
此时,接触硅片表面的液态铝沿着相图中的红线即液相线随着温度的升高由2点开始向上移动,在硅片的局部区域形成液态铝硅合金;第三阶段,铝硅的质量传输,随着温度由相图中的2点移至3点,合金中的硅的含量逐渐升高,铝硅进行着质量的传输,其传输线路为硅由基体向铝传输,而铝由铝浆向基体传输,两者的传输路线相反,见图3(3)所示。
图1:传统太阳能电池片烧结曲线图2:铝硅二元相图第四阶段,峰值温度阶段,在此阶段,铝硅液态合金相中硅的含量达到最高,接近30%,且液态相贯穿整个硅片表面;第五阶段,冷却阶段,此时合金中铝硅的质量传输方向和第三阶段相反,合金的成分沿液态线由4点向3点移动,液态合金中的硅向硅片表面传输,在硅片表面外延生长,含有少量的铝,形成硅的铝掺杂;图3:铝背场的形成过程图4:铝背场的扫描电镜照片第六阶段,凝固阶段,温度在铝硅共晶温度577℃,对应相图中的6点,此时,铝硅合金中硅的成分达到共晶成分,约占12%,形成完整的铝背场,同时在铝硅合金前表面外延生长了一层再结晶的铝。
评定焊接材料的晶间腐蚀敏感性应注意的问题
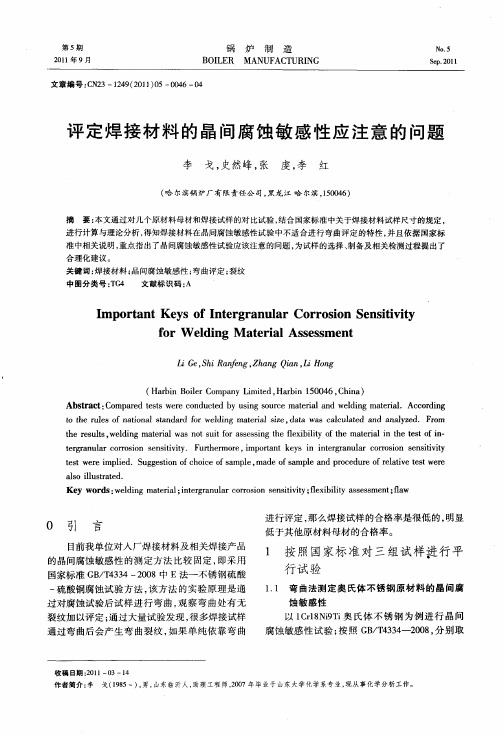
I p r a y f I t r r n l r Co r so e stv t m o t ntKe s o n e g a u a r o i n S n i i i y
f r W ed n a e i lAs e s e t o l i g M t ra s s m n
G ,h afn Z a gQa ,i eS i neg, h n i L R n ( abnB i rC m a yLm t , ab 5 0 6 C ia H ri o e o p n i i d H ri 10 4 , hn ) l e n
Ab ta t C mp rd t s r o d ce y u ig s u c t r la d w l ig mae i1 sr c : o a e e t we e c n u td b s o re mae i n ed n tra .Ac o d n s n a c rig
tr r n l rc ro i n e st i . F t e mo e, mp ra t k y n i tr r n l r c ro in s n i vt e g a u a or so s n ii t vy urh r r i o tn e s i n e g a u a o r so e st iy i ts r mp id.S g e to fc o c fs mp e, d fs mp e a d p o e ur fr ltv e twe e e twe e i le u g sin o h ie o a l ma e o a l n r c d e o e aie ts r
第 4期
李
戈, : 等 评定焊接材料的晶问腐蚀敏感性应注意的问题
不锈钢晶间腐蚀试验方法的改进

不锈钢晶间腐蚀试验方法的改进标题:不锈钢晶间腐蚀试验方法的改进引言:不锈钢是一种具有优异耐腐蚀性能的金属,广泛应用于许多领域。
然而,存在着一种特殊腐蚀形式,即不锈钢晶间腐蚀。
晶间腐蚀极大地影响了不锈钢的性能和使用寿命。
因此,改进不锈钢晶间腐蚀试验方法至关重要。
本文将深入探讨当前不锈钢晶间腐蚀试验方法的局限性,并提出一种改进方法,旨在提高试验准确性和可重复性。
第一部分:不锈钢晶间腐蚀试验方法的现状1.1 不锈钢晶间腐蚀的定义和机理晶间腐蚀是指在高温或腐蚀介质中,不锈钢晶粒边界处发生的一种腐蚀形式。
它通常与不锈钢的化学成分、微观组织以及使用环境等因素密切相关。
1.2 目前常用的不锈钢晶间腐蚀试验方法目前,最常用的不锈钢晶间腐蚀试验方法是敏感化试验和铜硫酸盐铵试验。
这些方法在一定程度上能够模拟真实使用环境下的晶间腐蚀情况,但存在一些局限性。
第二部分:不锈钢晶间腐蚀试验方法的局限性2.1 敏感化试验的局限性敏感化试验是通过在一定的温度和时间条件下进行加热处理,使晶界处形成偏析元素的化合物,进而引发晶间腐蚀。
然而,该方法存在试验结果不可重复、试验时间较长、成本较高等问题。
2.2 铜硫酸盐铵试验的局限性铜硫酸盐铵试验是使用铜硫酸盐溶液对不锈钢试样进行浸泡,然后通过观察试样表面的腐蚀情况来判断晶间腐蚀的程度。
然而,该方法的试验结果易受试样形状、试验条件等因素的影响,导致结果的可靠性有待提高。
第三部分:改进的不锈钢晶间腐蚀试验方法3.1 新的实验设计基于对现有方法的局限性的理解,我们提出了一种改进的不锈钢晶间腐蚀试验方法。
该方法综合考虑了现有方法的优点,并针对其缺点进行了改良。
3.2 试样制备和实验步骤在新的试验方法中,我们建议使用更具代表性的试样形状,并采取严格的试验步骤,以确保试验结果的准确性和可重复性。
第四部分:改进方法的实验结果和讨论4.1 试验结果通过使用改进的不锈钢晶间腐蚀试验方法,我们得到了一系列试验结果。
- 1、下载文档前请自行甄别文档内容的完整性,平台不提供额外的编辑、内容补充、找答案等附加服务。
- 2、"仅部分预览"的文档,不可在线预览部分如存在完整性等问题,可反馈申请退款(可完整预览的文档不适用该条件!)。
- 3、如文档侵犯您的权益,请联系客服反馈,我们会尽快为您处理(人工客服工作时间:9:00-18:30)。
晶间腐蚀性能弯曲评价影响实证探讨引言目前在国内不锈钢晶间腐蚀敏感性的评价过程中采用最为广泛的是硫酸-硫酸铜-铜屑沸腾溶液浸泡法,对应的标准为GB4334-2008E《不锈钢硫酸-硫酸铜腐蚀试验方法》。
在GB 4334-2008 E法中,通常是用直径为5mm的压头将腐蚀后的试样弯曲到180°后观察是否产生裂纹来判定材料对晶间腐蚀的敏感性。
用这一弯曲方法评定材料的晶间腐蚀的倾向性,实际是用适量的变形来加速晶间腐蚀裂纹的暴露,使晶间腐蚀微裂纹扩大,以弯曲后拉伸面是否有宏观裂纹来判定试样是否产生了晶间腐蚀。
这一方法可行的前提是弯曲拉伸面的变形量不超过试样允许的不发生塑性开裂的变形量。
实际上,在试样弯曲拉伸面上出现裂纹不一定能代表其有晶间腐蚀倾向,当弯曲变形量超过了塑性开裂的极限,也可能引起开裂。
不同材料的塑性开裂极限是不同的,在既定的标准下,很难保证所有的材料在弯曲过程中拉伸面的塑性变形都不超过材料本身允许的塑性开裂变形量。
因此在实际的检验过程中,对于不同的材料评价标准的准确性和可靠性需要考虑。
尤其是对于塑性较差的焊接接头材料, 按标准用直径为5mm的压头将试样弯曲到180°时, 即使没有晶间腐蚀裂纹,也可能发生开裂[引用文献]。
为此,需要研究材料力学性能(强度,塑性及断裂阻力等)对于晶间腐蚀评价方法的影响。
由于核电焊接接头材料在高温高压水环境中容易发生由晶间腐蚀引起的应力腐蚀开裂, 对核电设备的安全可靠性产生很大影响。
因此,对GB 4334-2008 E法对核电焊接接头材料的适用性尤其需要进行研究。
本章用ABAQUS软件通过三维有限元对晶间腐蚀性能评价方法中的弯曲试验进行了模拟计算,研究不同材料力学性能对于晶间腐蚀评价方法的影响,讨论了GB 4334-2008 E法标准对核电焊接接头材料试样的适用性,为研究核级焊材晶间腐蚀性能评价方法奠定基础,对开展核级焊接材料的国产化研究工作,并掌握核级焊接材料焊接腐蚀性能评价技术具有重要意义。
1.1有限元模型及分析方法为了探究晶间腐蚀裂纹弯曲评价方法的影响因素,模拟计算了三点弯曲试验过程,分析弯曲试样的应变分布和起裂以及裂纹的扩展情况。
1.1.1 模型结构和尺寸模拟的试样尺寸与标准中实际的三点弯曲试样相同:长度L=100mm,厚度t=4mm,宽度B=20mm。
根据GB2653-2008《焊接接头弯曲试验方法》中的规定,三点弯下支承辊的直径D至少为20mm,辊间的距离应为D+2h和D+3h之间,压头直径依据相关标准确定。
故在模拟中取支承辊直径D =20mm,辊距L0=D+2.5h。
上压头直径d依据GB 4334-2008 E法的规定,取d=5mm。
构建的三维三点弯曲模型如图3.1所示。
压头和支承辊均设置为刚体。
图3.1三点弯曲有限元(FEM)模型Fig.3.1 Three-point bending FEM model1.1.2 材料参数试样材料参数选用常温下实测的316L不锈钢(核电主管道材料)的性能参数,弹性模量E=156150MPa,泊松比μ=0.3,真应力-应变曲线如图3.3所示。
T r u e s t r e s s (M P a )True strain图1.1 316L 材料真应力-应变曲线 1.1.3 GTN 延性损伤断裂模型{对于金属材料的延性断裂,现已发现其断裂机理包括同时发生并相互作用的几个过程[3.1]:①通过第二相,夹杂物的断裂或剥离形成微孔洞;②在塑性应变和三向应力作用下的微孔长大;③微孔聚合而导致断裂。
为了从力学上描述这一微孔型的细观损伤演化和断裂过程,Gurson 在总结前人经验的基础上对含有圆柱形和球形空穴的材料(多孔质体)的塑性变形情况进行了研究,提出了基于材料刚塑性行为和塑性上边界定理的多孔塑性材料的本构模型[1.1]。
基于材料开裂行为的详细现象研究,Tvergaard 考虑了材料的加工硬化、变形以及特殊情况下生产剪切变形带等情况,通过纳入三个额外的参数(q 1,q 2,q 3)修正了Gurson 提出的本构模型[3.3],使得Gurson 模型的预测精度大大提高,其提出的方程如下:2*2*2123232c o s h ()(1)02e h q f q q f σσσσΦ=+-+=, (3-1)其中ζe =(3S ij S ij /2)1/2是宏观Mises 等效应力;ζh =ζkk /3是宏观静水应力(宏观平均应力);S ij =ζij -ζkk δij /3表示Cauchy 应力的偏应力分量;δij 为Kronecker delta 符号;σ是基体材料的屈服应力,f ∗是有效孔洞体积分数。
当ƒ=0时,表示均质,不可压缩材料的Mises 屈服表面,当ƒ趋近于1/q 1时,屈服表面聚合成一个点。
通常,取q 1=1.5,q 2 =1,q 3= q 12。
当q 1=q 2 =q 3=1时,GTN 模型退化为最初的Gurson 模型。
在修正的模型中,考虑了微孔之间的相互作用和材料应变硬化的协同作用,并把微孔聚合引入了模型。
根据等效塑性功原理将宏观和细观两尺度量联系起来,得到基体等效塑性应变的演化方程:(1−f ) ζm dεm pl =ζdεp (3-2)其中εm pl 为基体材料的累积等效塑性应变。
损伤变量f ∗是总的等效孔洞体积分数,它是孔洞体积分数f 的函数,由Tvergaard 和Needleman [3.4-3.5]引入以解释由于孔洞聚合导致材料承载能力逐渐下降的现象。
当f ∗ =0 时,表明材料没有损伤,上述屈服方程退化为标准的von Mises 形式。
f ∗ 定义为:**()/()()c u c f c c f f f f f f f f f ⎧⎪=⎨+---⎪⎩,,c c f f f f ≤>,, (3-3) 其中fc 为孔洞开始发生聚合时的临界孔洞体积分数;f f 是材料破裂时的孔洞体积分数;fu 表示应力承载能力为零时的极限孔洞体积分数。
当材料的孔洞体积分数f 达到临界值f c 时,孔洞开始聚合;当孔洞体积分数f 达到临界值f F 时,材料断裂。
损伤的演化包含两部分:原有孔洞长大和新孔洞形核引起的损伤变化: d f = d f growth + d f nucleation (3-4)由于假设基体材料是不可压缩的,根据质量守恒定律,d fg 只与宏观塑性应变的静水分量有关:d fg = (1−f ) dεp I (3-5)其中:ε p 为宏观塑性应变张量;I 是二阶单位张量。
新孔洞形核造成的孔洞体积分数变化率可由下式表示:d fn =A dεm pl (3-6)其中,212p e N N A s εε⎧⎫⎡⎤-⎪⎪=-⎨⎬⎢⎥⎣⎦⎪⎪⎩⎭这里A 为孔洞形核系数;f N 为可形核粒子的体积分数大小;εN 为孔洞形核时的平均应变;S N 为形核应变的标准差。
公式3-1至3-6构成了GTN 模型,在目前的研究中用GTN 模型中的9个参数(εN ,S N ,f N ,f 0,f c ,f f ,q 1,q 2 ,q 3)来模拟断裂损伤和失效。
}GTN 模型及材料参数这部分计划在绪论中介绍,这一节着重讲为何用GTN 模型以及几个参数的确定(可以)。
在绪论中已经详细介绍了GTN 延性损伤断裂模型,在许多研究中[3.6-3.11]已应用ABAQUS 软件内含的GTN 模型模拟了多种实际金属材料和结构的弯曲和拉伸延性断裂过程,模拟结果和试验结果均十分吻合,说明GTN 模型和对延性断裂过程的模拟是很可靠的。
本文将GTN 模型用于三点弯曲试样的变形和延性开裂模拟,通过改变模型中的材料参数,分析研究材料力学性能对晶间腐蚀性能弯曲评价方法的影响。
在GTN模型中需要确定的参数有模型系数q1、q2、q3,初始孔洞体积分数f0,孔洞形核参数f N、εn、S N,临界孔洞聚合体积分数f c和失效孔洞体积分数f F。
其中q1、q2、q3三个参数对于含有夹杂物和碳化物的钢一般分别取为1.5、1、2.25[3.12],在大多数研究中εn、S N均取为0.3、0.1[3.13-1.11]。
不同材料损伤断裂性能的不同主要体现在初始孔洞体积分数f0、临界孔洞聚合体积分数f c、失效孔洞体积分数f F以及孔洞形核分数f N上。
故本文在研究不同材料的GTN参数时实际上也是以f0、f c、f F以及f N四个参数作为变量,保持其他参数不变。
1.1.4 FEM模型由于弯曲过程中试样应变较大,为了防止变形率过大,保证分析收敛,利于沙漏控制,综合考虑采用C3D8R八节点线性六面体减缩积分单元对试样进行网格划分。
整体网格单元尺寸为0.8×0.8mm,与压头和支承辊接触区域有作用力集中,为减小其对模型计算结果的影响,进行局部网格细化,最小单元边长为0.2mm。
整个试样共有56250个单元。
图1.1显示了试样网格划分情况。
(a)(b)图1.1 试样全模型(a)和前表面局部(b)的有限元网格边界条件与载荷的设置为: 试样与压头及支承辊之间定义为表面与表面接触,两个支承辊完全固定,压头除竖直方向的自由度外全部约束。
载荷通过对压头竖直方向的位移控制来施加。
如图3.3所示。
图3.3 模型的边界条件为便于探究试样弯曲过程中的应变分布情况,分别设置两条路径来求取试样的应变分布,如图3.4和图3.5所示(用文字说明)。
图3.4 沿试样中心区拉伸表面图3.5 沿试样中心平面的厚度方向(起裂点在最下方)3.3弯曲角度对晶间腐蚀弯曲试样中应变分布的影响无论对于什么样的材料,弯曲角度不同,试样的应变会不同。
为了深入、清晰地探讨弯曲角度对于弯曲试样应变分布和裂纹起裂及裂纹扩展的影响,在给定一种材料参数的条件下,进行模拟计算。
使用的材料为316L实验测得的真应力-应变曲线(图1.1)。
为了确定弯曲到180度可以开裂的GTN参数,进行了许多不同GTN参数的试算。
取典型的GTN参数为q1=1.5,q2=1,q3=2.25,εN =0.3,S N=0.1,f N =0.002,f0=0.008,f c=0.01,f F=0.2,用这些参数计算分析弯曲角度对于试样应变分布和裂纹起裂及扩展的影响。
计算的弯曲到60°后,试样中的等效塑性应变PEEQ、沿试样长度方向主应变PE11及GTN损伤变量(孔洞体积分数VVF)的分布云图如图3.6所示。
(a) (b)(c)图3.6 弯曲试样的等效塑性应变PEEQ(a),主应变PE11(b)和空洞体积分数VVF(c)的分布云图图3.6(a)显示试样的上下表面中间区域的等效塑性应变PEEQ较大,这是由于试样在中间处受弯所致。
在弯曲过程中试样上部分受压应力作用,下部分受拉应力作用。