钣金加工技术要求模板
钣金加工技术要求大全
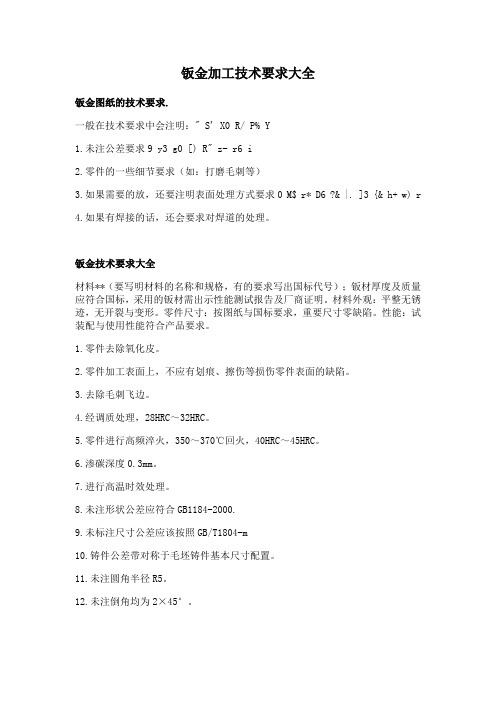
钣金加工技术要求大全钣金图纸的技术要求.一般在技术要求中会注明:" S' X0 R/ P% Y1.未注公差要求9 y3 g0 [) R" z- r6 i2.零件的一些细节要求(如:打磨毛刺等)3.如果需要的放,还要注明表面处理方式要求0 M$ r* D6 ?& |. ]3 {& h+ w) r4.如果有焊接的话,还会要求对焊道的处理。
钣金技术要求大全材料**(要写明材料的名称和规格,有的要求写出国标代号);钣材厚度及质量应符合国标,采用的钣材需出示性能测试报告及厂商证明。
材料外观:平整无锈迹,无开裂与变形。
零件尺寸:按图纸与国标要求,重要尺寸零缺陷。
性能:试装配与使用性能符合产品要求。
1.零件去除氧化皮。
2.零件加工表面上,不应有划痕、擦伤等损伤零件表面的缺陷。
3.去除毛刺飞边。
4.经调质处理,28HRC~32HRC。
5.零件进行高频淬火,350~370℃回火,40HRC~45HRC。
6.渗碳深度0.3mm。
7.进行高温时效处理。
8.未注形状公差应符合GB1184-2000.9.未标注尺寸公差应该按照GB/T1804-m10.铸件公差带对称于毛坯铸件基本尺寸配置。
11.未注圆角半径R5。
12.未注倒角均为2×45°。
13.锐角倒钝。
14.各密封件装配前必须浸透油。
15.装配滚动轴承允许采用机油加热进行热装,油的温度不得超过100℃。
16.齿轮装配后,齿面的接触斑点和侧隙应符合GB10095和GB11365的规定。
17.装配液压系统时允许使用密封填料或密封胶,但应防止进入系统中。
18.进入装配的零件及部件(包括外购件、外协件),均必须具有检验部门的合格证方能进行装配。
19.规定拧紧力矩要求的紧固件,必须采用力矩扳手,并按规定的拧紧力矩紧固。
20.圆锥销装配时应与孔应进行涂色检查,其接触率不应小于配合长度的60%,并应均匀分布。
21.平键与轴上键槽两侧面应均匀接触,其配合面不得有间隙。
钣金件技术要求

钣金件通用技术标准本标准为产品设计者提供本公司一般的设计要求,也为质检员提供检验与判定的参考依据,同时也作为供应商产品加工的标准。
此标准按钣金制作,也适合其他金属件加工的零配件和产品。
一.材料要求:除图纸特别说明外,一般材料采用优质A3冷板(Q235A)。
材料厚度符合GB709-88标准,其力学性能符合GB2975-82标准,化学成分符合GB222-84,并由供应商提供相关原材料检测报告。
二.表面要求:1.外观:光洁平整,去除毛刺、锐边,无变形等缺陷;2.喷涂:颜色与图纸要求或样件及色板一致,喷涂前必须经过酸洗和磷化处理(参考GB8923-88),无挂滴、条纹、起泡、桔皮、剥落、划伤等缺陷,附着力性能可靠,划格试验不大于1级,具体标准参考表一。
一般情况下涂层厚度在39~120μm之间;3.电镀:表面镀锌结晶细致,色泽均匀,结合牢固,不允许有生锈、表层不干净、划伤、凹坑等缺陷(参考钢铁制作机械镀锌标准要求JB/T8928-1999);4.耐蚀性:中性盐雾实验(GB/T 1771-1991)车身内配件外表面500h后划叉处单边扩蚀宽度≤2mm,未划叉区域无起泡、开裂、剥落、掉粉、明显变色、明显失光等涂膜病态现象内腔中性盐雾120h后红锈面积小于10%.;车身外配件1000h后基体无锈蚀。
5.丝印:文字、图案及颜色依据图纸要求,无偏斜、模糊、重影、针孔等缺陷,具体检验标准参考附表二。
6.对于外观分为A 、B、C、D四个等级。
三.加工:1.下料:非模具开料时必须打磨尖角和毛刺,模具落料时,未注圆角半径取料厚;2.折弯:未注折弯内圆角半径取材料厚度,3.焊接:牢固、平整,无虚焊、夹渣、气孔、堆积、变形等缺陷,影响到装配及外观的部分必须打磨平整;4.精度:未注尺寸公差按GB/T1800.3-1998中的IT14级精度制制作,同时图纸上所标注的尺寸均为表面处理后的状态,具体数据参见表三。
附表一划格试验GB/T 9286-1998系等效采用国际标准ISO 2409:1992《色漆和清漆——划格试验》(第二版),代替等效采用ISO 2409:1972的GB 9286-88。
钣金加工技术要求汇总

时磊5说-钣金加工技术要求汇总钣金:技术要求:1折弯半径R2;2、锐边倒钝,去毛刺;3、脱脂洗净;4、零件表面喷塑处理,颜色:新威XW9256HS50。
技术要求:1折弯半径R2 ;2、锐边倒钝,去毛刺;3、零件表面镀白锌处理;4、脱脂洗净。
技术要求:1折弯半径R2 ;2、未注公差参照ISO-2768-m ;3、锐边倒钝,去毛刺;4、加工完脱脂洗净。
技术要求:1未注公差参照ISO-2768-m ;2、锐边倒钝,去毛刺;3、加工完脱脂洗净。
技术要求:1锐边倒钝,去毛刺;2、零件表面镀白锌处理(厚度15微米);3、脱脂洗净。
1折弯半径R1.5;技术要求:1锐边倒钝,去毛刺;2、脱脂洗净。
技术要求:1材料采用镜面板加工;2、折弯半径R1 ;3、锐边倒钝,去毛刺;时磊忖呎…4、脱脂洗净。
技术要求:1锐边倒钝,去毛刺;2、表面喷塑处理(颜色:新威1294HF10);3、脱脂洗净。
技术要求:1、零件1与零件2压铆连接,压平、压牢;2、注意避免表面划伤。
盒体:技术要求:1、折弯半径R1.5;2、锐边倒钝,去毛刺;3、脱脂洗净。
技术要求:1、零件1与零件2、3、4、5、6压铆连接,压平、压牢;2、表面喷塑,颜色:新威1294HF10 ;3、喷塑时注意保护螺纹,喷塑后回丝。
技术要求:1、零件1与零件2、3、4压铆连接,压平、压牢;2、表面喷塑,颜色:新威1294HF10 ;3、喷塑时注意保护螺纹,喷塑后回丝。
技术要求:1、折弯半径R1.5;2、锐边倒钝,去毛刺;3、表面喷塑处理(颜色:新威1294HF10);4、脱脂洗净。
技术要求:1、折弯半径R1.5;2、锐边倒钝,去毛刺;时磊5说-3、零件表面镀白锌处理,厚度15微米;4、图中尺寸为机加尺寸,不包括镀锌厚度;5、脱脂洗净。
技术要求:1、折弯半径R1.5;2、未注公差参照ISO-2768-m ;3、锐边倒钝,去毛刺;4、零件表面不得划伤。
技术要求:1、未注凸部倒角C0.5,凹部倒角R0.3以下;2、零件表面镀白锌处理,厚度15微米;3、图中尺寸为机加尺寸,不包括镀锌厚度;4、脱脂洗净。
钣金技术要求
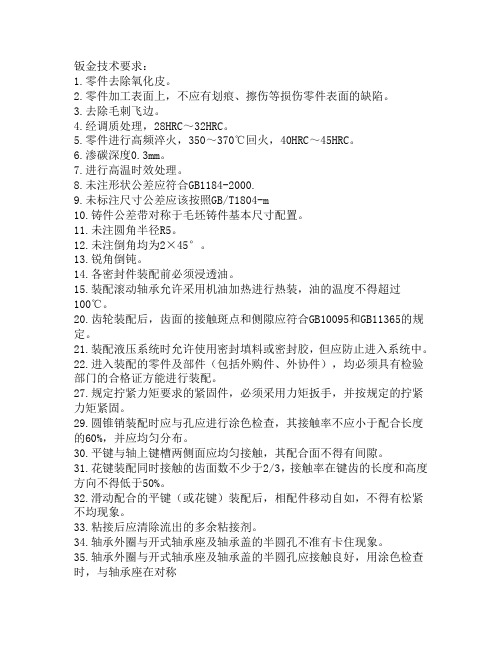
钣金技术要求:1.零件去除氧化皮。
2.零件加工表面上,不应有划痕、擦伤等损伤零件表面的缺陷。
3.去除毛刺飞边。
4.经调质处理,28HRC~32HRC。
5.零件进行高频淬火,350~370℃回火,40HRC~45HRC。
6.渗碳深度0.3mm。
7.进行高温时效处理。
8.未注形状公差应符合GB1184-2000.9.未标注尺寸公差应该按照GB/T1804-m10.铸件公差带对称于毛坯铸件基本尺寸配置。
11.未注圆角半径R5。
12.未注倒角均为2×45°。
13.锐角倒钝。
14.各密封件装配前必须浸透油。
15.装配滚动轴承允许采用机油加热进行热装,油的温度不得超过100℃。
20.齿轮装配后,齿面的接触斑点和侧隙应符合GB10095和GB11365的规定。
21.装配液压系统时允许使用密封填料或密封胶,但应防止进入系统中。
22.进入装配的零件及部件(包括外购件、外协件),均必须具有检验部门的合格证方能进行装配。
27.规定拧紧力矩要求的紧固件,必须采用力矩扳手,并按规定的拧紧力矩紧固。
29.圆锥销装配时应与孔应进行涂色检查,其接触率不应小于配合长度的60%,并应均匀分布。
30.平键与轴上键槽两侧面应均匀接触,其配合面不得有间隙。
31.花键装配同时接触的齿面数不少于2/3,接触率在键齿的长度和高度方向不得低于50%。
32.滑动配合的平键(或花键)装配后,相配件移动自如,不得有松紧不均现象。
33.粘接后应清除流出的多余粘接剂。
34.轴承外圈与开式轴承座及轴承盖的半圆孔不准有卡住现象。
35.轴承外圈与开式轴承座及轴承盖的半圆孔应接触良好,用涂色检查时,与轴承座在对称于中心线120°、与轴承盖在对称于中心线90°的范围内应均匀接触。
在上述范围内用塞尺检查时,0.03mm的塞尺不得塞入外圈宽度的1/3。
36.轴承外圈装配后与定位端轴承盖端面应接触均匀。
37.滚动轴承装好后用手转动应灵活、平稳。
钣金技术要求大全
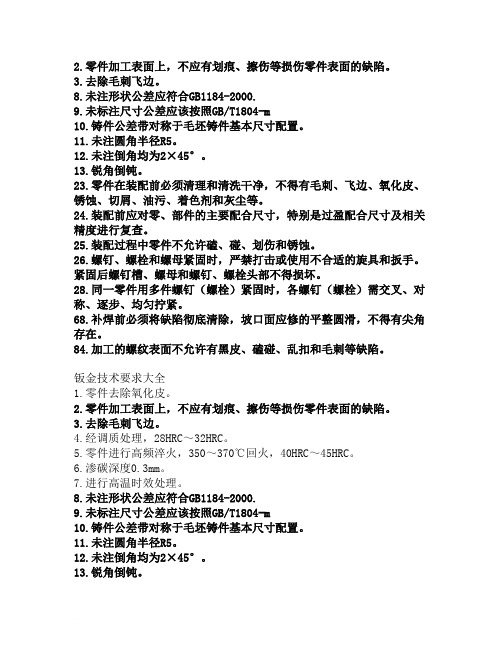
2.零件加工表面上,不应有划痕、擦伤等损伤零件表面的缺陷。
3.去除毛刺飞边。
8.未注形状公差应符合GB1184-2000.9.未标注尺寸公差应该按照GB/T1804-m10.铸件公差带对称于毛坯铸件基本尺寸配置。
11.未注圆角半径R5。
12.未注倒角均为2×45°。
13.锐角倒钝。
23.零件在装配前必须清理和清洗干净,不得有毛刺、飞边、氧化皮、锈蚀、切屑、油污、着色剂和灰尘等。
24.装配前应对零、部件的主要配合尺寸,特别是过盈配合尺寸及相关精度进行复查。
25.装配过程中零件不允许磕、碰、划伤和锈蚀。
26.螺钉、螺栓和螺母紧固时,严禁打击或使用不合适的旋具和扳手。
紧固后螺钉槽、螺母和螺钉、螺栓头部不得损坏。
28.同一零件用多件螺钉(螺栓)紧固时,各螺钉(螺栓)需交叉、对称、逐步、均匀拧紧。
68.补焊前必须将缺陷彻底清除,坡口面应修的平整圆滑,不得有尖角存在。
84.加工的螺纹表面不允许有黑皮、磕碰、乱扣和毛刺等缺陷。
钣金技术要求大全1.零件去除氧化皮。
2.零件加工表面上,不应有划痕、擦伤等损伤零件表面的缺陷。
3.去除毛刺飞边。
4.经调质处理,28HRC~32HRC。
5.零件进行高频淬火,350~370℃回火,40HRC~45HRC。
6.渗碳深度0.3mm。
7.进行高温时效处理。
8.未注形状公差应符合GB1184-2000.9.未标注尺寸公差应该按照GB/T1804-m10.铸件公差带对称于毛坯铸件基本尺寸配置。
11.未注圆角半径R5。
12.未注倒角均为2×45°。
13.锐角倒钝。
14.各密封件装配前必须浸透油。
15.装配滚动轴承允许采用机油加热进行热装,油的温度不得超过100℃。
20.齿轮装配后,齿面的接触斑点和侧隙应符合GB10095和GB11365的规定。
21.装配液压系统时允许使用密封填料或密封胶,但应防止进入系统中。
22.进入装配的零件及部件(包括外购件、外协件),均必须具有检验部门的合格证方能进行装配。
钣金技术要求大全
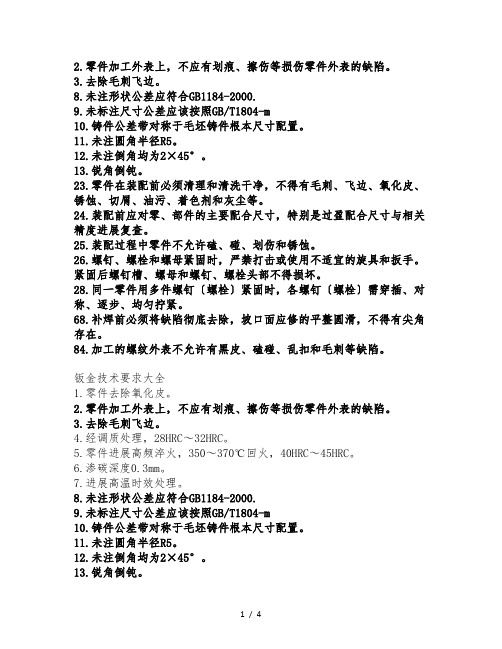
2.零件加工外表上,不应有划痕、擦伤等损伤零件外表的缺陷。
3.去除毛刺飞边。
8.未注形状公差应符合GB1184-2000.9.未标注尺寸公差应该按照GB/T1804-m10.铸件公差带对称于毛坯铸件根本尺寸配置。
11.未注圆角半径R5。
12.未注倒角均为2×45°。
13.锐角倒钝。
23.零件在装配前必须清理和清洗干净,不得有毛刺、飞边、氧化皮、锈蚀、切屑、油污、着色剂和灰尘等。
24.装配前应对零、部件的主要配合尺寸,特别是过盈配合尺寸与相关精度进展复查。
25.装配过程中零件不允许磕、碰、划伤和锈蚀。
26.螺钉、螺栓和螺母紧固时,严禁打击或使用不适宜的旋具和扳手。
紧固后螺钉槽、螺母和螺钉、螺栓头部不得损坏。
28.同一零件用多件螺钉〔螺栓〕紧固时,各螺钉〔螺栓〕需穿插、对称、逐步、均匀拧紧。
68.补焊前必须将缺陷彻底去除,坡口面应修的平整圆滑,不得有尖角存在。
84.加工的螺纹外表不允许有黑皮、磕碰、乱扣和毛刺等缺陷。
钣金技术要求大全1.零件去除氧化皮。
2.零件加工外表上,不应有划痕、擦伤等损伤零件外表的缺陷。
3.去除毛刺飞边。
4.经调质处理,28HRC~32HRC。
5.零件进展高频淬火,350~370℃回火,40HRC~45HRC。
6.渗碳深度0.3mm。
7.进展高温时效处理。
8.未注形状公差应符合GB1184-2000.9.未标注尺寸公差应该按照GB/T1804-m10.铸件公差带对称于毛坯铸件根本尺寸配置。
11.未注圆角半径R5。
12.未注倒角均为2×45°。
13.锐角倒钝。
14.各密封件装配前必须浸透油。
15.装配滚动轴承允许采用机油加热进展热装,油的温度不得超过100℃。
20.齿轮装配后,齿面的接触斑点和侧隙应符合GB10095和GB11365的规定。
21.装配液压系统时允许使用密封填料或密封胶,但应防止进入系统中。
22.进入装配的零件与部件〔包括外购件、外协件〕,均必须具有检验部门的合格证方能进展装配。
钣金技术要求大全

钣金技术要求大全1.零件去除氧化皮。
2.零件加工表面上,不应有划痕、擦伤等损伤零件表面的缺陷。
3.去除毛刺飞边。
4.经调质处理,28HRC~32HRC。
5.零件进行高频淬火,350~370℃回火,40HRC~45HRC。
6.渗碳深度0.3mm。
7.进行高温时效处理。
8.未注形状公差应符合GB1184-2000.9.未标注尺寸公差应该按照GB/T1804-m10.铸件公差带对称于毛坯铸件基本尺寸配置。
11.未注圆角半径R5。
12.未注倒角均为2×45°。
13.锐角倒钝。
14.各密封件装配前必须浸透油。
15.装配滚动轴承允许采用机油加热进行热装,油的温度不得超过100℃。
20.齿轮装配后,齿面的接触斑点和侧隙应符合GB10095和GB11365的规定。
21.装配液压系统时允许使用密封填料或密封胶,但应防止进入系统中。
22.进入装配的零件及部件(包括外购件、外协件),均必须具有检验部门的合格证方能进行装配。
23.零件在装配前必须清理和清洗干净,不得有毛刺、飞边、氧化皮、锈蚀、切屑、油污、着色剂和灰尘等。
24.装配前应对零、部件的主要配合尺寸,特别是过盈配合尺寸及相关精度进行复查。
25.装配过程中零件不允许磕、碰、划伤和锈蚀。
26.螺钉、螺栓和螺母紧固时,严禁打击或使用不合适的旋具和扳手。
紧固后螺钉槽、螺母和螺钉、螺栓头部不得损坏。
27.规定拧紧力矩要求的紧固件,必须采用力矩扳手,并按规定的拧紧力矩紧固。
28.同一零件用多件螺钉(螺栓)紧固时,各螺钉(螺栓)需交叉、对称、逐步、均匀拧紧。
29.圆锥销装配时应与孔应进行涂色检查,其接触率不应小于配合长度的60%,并应均匀分布。
30.平键与轴上键槽两侧面应均匀接触,其配合面不得有间隙。
31.花键装配同时接触的齿面数不少于2/3,接触率在键齿的长度和高度方向不得低于50%。
32.滑动配合的平键(或花键)装配后,相配件移动自如,不得有松紧不均现象。
钣金件技术要求
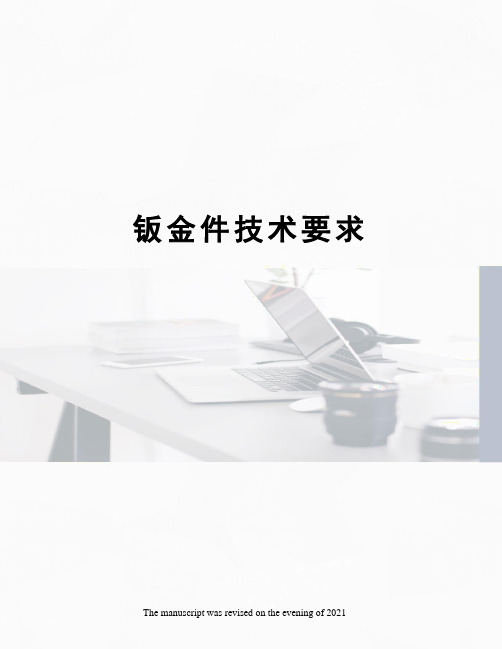
钣金件技术要求 The manuscript was revised on the evening of 2021钣金件通用技术标准本标准为产品设计者提供本公司一般的设计要求,也为质检员提供检验与判定的参考依据,同时也作为供应商产品加工的标准。
此标准按钣金制作,也适合其他金属件加工的零配件和产品。
一.材料要求:除图纸特别说明外,一般材料采用优质A3冷板(Q235A)。
材料厚度符合GB709-88标准,其力学性能符合GB2975-82标准,化学成分符合GB222-84,并由供应商提供相关原材料检测报告。
二.表面要求:1.外观:光洁平整,去除毛刺、锐边,无变形等缺陷;2.喷涂:颜色与图纸要求或样件及色板一致,喷涂前必须经过酸洗和磷化处理(参考GB8923-88),无挂滴、条纹、起泡、桔皮、剥落、划伤等缺陷,附着力性能可靠,划格试验不大于1级,具体标准参考表一。
一般情况下涂层厚度在39~120μm之间;3.电镀:表面镀锌结晶细致,色泽均匀,结合牢固,不允许有生锈、表层不干净、划伤、凹坑等缺陷(参考钢铁制作机械镀锌标准要求JB/T8928-1999);4.耐蚀性:中性盐雾实验(GB/T 1771-1991)车身内配件外表面500h后划叉处单边扩蚀宽度≤2mm,未划叉区域无起泡、开裂、剥落、掉粉、明显变色、明显失光等涂膜病态现象内腔中性盐雾120h后红锈面积小于10%.;车身外配件1000h后基体无锈蚀。
5.丝印:文字、图案及颜色依据图纸要求,无偏斜、模糊、重影、针孔等缺陷,具体检验标准参考附表二。
6.对于外观分为A 、B、C、D四个等级。
三.加工:1.下料:非模具开料时必须打磨尖角和毛刺,模具落料时,未注圆角半径取料厚;2.折弯:未注折弯内圆角半径取材料厚度,3.焊接:牢固、平整,无虚焊、夹渣、气孔、堆积、变形等缺陷,影响到装配及外观的部分必须打磨平整;4.精度:未注尺寸公差按GB/中的IT14级精度制制作,同时图纸上所标注的尺寸均为表面处理后的状态,具体数据参见表三。
- 1、下载文档前请自行甄别文档内容的完整性,平台不提供额外的编辑、内容补充、找答案等附加服务。
- 2、"仅部分预览"的文档,不可在线预览部分如存在完整性等问题,可反馈申请退款(可完整预览的文档不适用该条件!)。
- 3、如文档侵犯您的权益,请联系客服反馈,我们会尽快为您处理(人工客服工作时间:9:00-18:30)。
非标配电箱柜结构加工标准
1、配电箱接地要求:箱体、箱门左下角相应位置采用内丝型接地8*15mm,要求满焊焊接均匀。
安装板采用外丝型接地8*15mm,接地螺丝由后向前穿过安装板焊点在板后。
喷塑前做好保护措施,接地柱表面不得有残留塑粉。
□
2、安装板调节螺丝采用背板焊支架固定如下图,要求固定牢固配齐所需平垫、弹垫、螺母。
安装板固定安装孔采用上下长孔11*20mm。
配电箱安装板、支架均采用喷塑处理。
□
3、配电柜安装梁为花梁(即:冲满10*50mm长孔),安装梁、支架等其他结构件配电柜安装梁均采用喷塑处理。
□
4、配电箱箱门结合处做减震处理,配电柜门结合处加减震胶条,应牢固不易脱落。
□
5、配电箱门边缝隙应均匀,单边不大于2mm,箱门开度不小于90度。
□
6、明装配电箱背板四角冲挂墙安装孔Φ13,距直角两边各30mm不得被安装板覆盖。
□
7、配电柜背面板与底面板为可拆卸式,配电柜顶端底端焊角铁圈梁,顶部四角配吊环,底部相应位置冲17*30mm固定安装孔。
□
8、配电柜门单扇宽度≥600mm时做“T”型加强措施。
□
9、配电箱配锁(AB-303-1)配电柜配锁(AB-301)参考:海坦锁具。
□
10、板材要求:配电箱任意一边≥600mm,箱体、箱门、安装板均采用2.0mm,≯600mm 采用1.5mm冷轧钢板制作。
(有特殊注明的除外)□
备注:制作厂家须严格按照我方提供的图纸生产,满足图纸说明的各项要求。
对图纸如有异议,请及时与我方沟通。