制程首件检验报告(装配)
装配制程检验规范

乐清市莱恩科技有限公司文件编号WI/LE-PZ-03-2009版 / 次 A / 1制程检验规范页码 1 / 81、目的为了严格执行ISO9001-2008质量体系管理要求、确保制造产品符合本公司使用要求,保证生产顺利进行,特制订本规范。
2、范围公司自行生产的半成品及成品检验指导。
3、职责制程检验(IPQC检验员)负责执行检验、指导及判定,负责品质异常开立《品质异常处理单》、负责客户抱怨及制程不良的内容分析及不良查核、处理并记录。
品质部经理负责对处理结果进行核准。
4、工作内容4.1检验依据:检验图、制程检验规范4.2检验制程检验(IPQC)员首检,巡检,完工检应快速对产品进行外观、尺寸、结构、性能等的检验、试验,并做出合理合理判定。
4.3判定/标示A、 制程中产品所有检验、试验项目无任何缺陷,或存在缺陷但在允收范围内,应判定合格状态并签名确认,报部门经理核准通过后方可进行批量生产,完工产品判定合格进行标识后将物料移至QC待检区。
B、制程所有检验、试验项目存在任何一项质量缺陷,在允收范围外,应判定为不合格状态并签名确认,报部门经理核准通过后责令整改.完工品不合格进行标识后进行封样,并将物料移至不合格区或立即通知车间返工.4.5信息反馈制程所有检验、试验项目存在任何一项质量缺陷,在允收范围外,由制程检验(IPQC)员开立《品质异常处理单》报部门经理进行审批。
常规状况下,产品出现异常时品质部经理直接批准不合格处理,转发生产部、技术部,由巡检跟进处理进度及效果,特殊情况可由相关部门提出评审。
4.6质量评审制程中发现产品出现异常,但由于特殊原因有必要提出评审的参照《不合格品控制程序》.4.7检验记录制程中所有检验项目应得到真实,完好记录,并得到审批,记录保存周期为24个月。
电子公司首件及制程检验办法

电子公司首件及制程检验办法背景在电子生产流程中,原材料的选择、制造、设备的装配和测试等环节必须要经过严格的检验流程,确保产品的品质和可靠性。
电子公司的首件及制程检验管理是制造高品质电子产品不可缺少的环节。
本文将介绍电子公司首件及制程检验的办法和注意事项。
首件检验首件检验是制造实施装配、生产线及工装的第一批部件的调试,以保证生产的整个流程将顺利进行。
它是确保所有设备和零件能够可靠工作的重要步骤,它的目的是发现并纠正在制造装配过程中可能出现的问题。
检验内容首先,需要对制造过程的关键节点进行检测与评估,以确保产品符合标准和规定的质量要求。
其中关键节点包括:•零件、组件和部件的型号和规格。
•线路板和丝印,以及布局和尺寸。
•引脚和焊点的位置和尺寸。
•安装和调试工艺的制定(如固定和中心校正)。
•原材料的质量和可靠性。
检验方法•应用合适的测试设备进行测试,以确保其符合设计要求和性能规格。
•对制造过程进行深入分析,并确定可能出现的问题的根源。
•实施适当的改进,确保所有组件和部件都具有可靠的性能和质量。
•将生产前审查结果和结果记录在相关的文件中,以备将来检查。
首件检验的结果应该清晰或者标准化的记录下来,以便在生产过程中进行比对和校准。
要求制定详细的首件检验报告,以便做出必要的调整和不断改进质量标准。
制程检验制程检验是在产品制造过程的不同阶段进行的检验和测试,以确保产品符合质量和性能要求。
制程检验通常由自动化测试设备运行,所有数据都是由电子测试仪器进行采集和记录的。
可以通过每个测试阶段的结果来提供实时反馈,以及衡量产品制造过程的质量、效率和可靠性。
在制程中持续的检验可以提前发现问题,防止产品缺陷在数量不断堆积的情况下产生后果,从而减少问题的发生率。
检验内容制程检验应关注以下问题:•每个生产阶段的关键节点。
•每个阶段的产品质量要求,以确保所有产品在整个流程中保持一致性。
•产品的所有测试和检测标准。
检验方法制程检验应该采用以下方法:•采用基于规格书的自动测试设备检测和测试产品。
IPQC首件制程检验程序
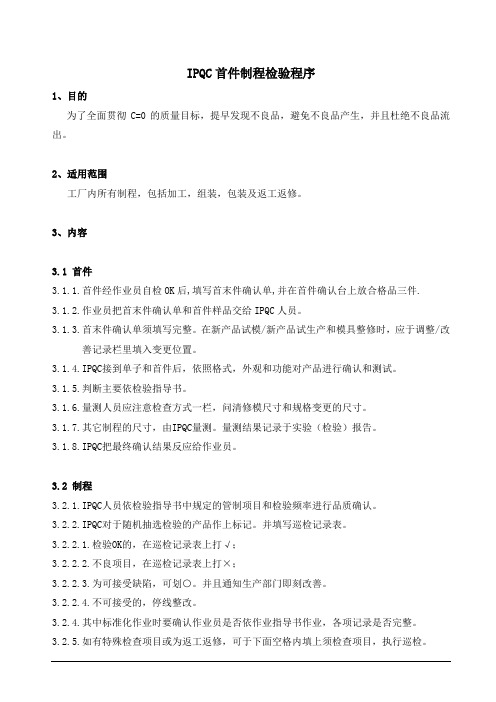
IPQC首件制程检验程序1、目的为了全面贯彻C=0的质量目标,提早发现不良品,避免不良品产生,并且杜绝不良品流出。
2、适用范围工厂内所有制程,包括加工,组装,包装及返工返修。
3、内容3.1 首件3.1.1.首件经作业员自检OK后,填写首末件确认单,并在首件确认台上放合格品三件.3.1.2.作业员把首末件确认单和首件样品交给IPQC人员。
3.1.3.首末件确认单须填写完整。
在新产品试模/新产品试生产和模具整修时,应于调整/改善记录栏里填入变更位置。
3.1.4.IPQC接到单子和首件后,依照格式,外观和功能对产品进行确认和测试。
3.1.5.判断主要依检验指导书。
3.1.6.量测人员应注意检查方式一栏,问清修模尺寸和规格变更的尺寸。
3.1.7.其它制程的尺寸,由IPQC量测。
量测结果记录于实验(检验)报告。
3.1.8.IPQC把最终确认结果反应给作业员。
3.2 制程3.2.1.IPQC人员依检验指导书中规定的管制项目和检验频率进行品质确认。
3.2.2.IPQC对于随机抽选检验的产品作上标记。
并填写巡检记录表。
3.2.2.1.检验OK的,在巡检记录表上打√;3.2.2.2.不良项目,在巡检记录表上打×;3.2.2.3.为可接受缺陷,可划○。
并且通知生产部门即刻改善。
3.2.2.4.不可接受的,停线整改。
3.2.4.其中标准化作业时要确认作业员是否依作业指导书作业,各项记录是否完整。
3.2.5.如有特殊检查项目或为返工返修,可于下面空格内填上须检查项目,执行巡检。
3.2.6.发生品质异常时按品质异常处理办法处理。
备注一栏可填上开出的不可格品单号3.2.7.巡回检验和重点工序质量控制点,由检验人员进行监督,发现异常立即通知操作者停止生产并向生产部门和工程部门报告.3.2.8.IPQC组长应对首件和巡检的执行情况作稽核,稽核结果填写于备注栏。
频率至少1PCS/4H。
3.3 末件3.3.1.批量加工完成后,对最后一件或和几件进行检验,并填写《首(末)件确认书》.3.3.2.末件检验不合格时,由出现末件检验责任部门或岗位,应对前面加工的产品进行追踪复核,分析原因,并及时将信息反馈至有关部门,制订纠正措施,其原因分析和纠正措施可填写在《纠正预防措施实施表》.3.4 工序入库检验3.4.1.检验人员按检验作业指导书要求对工序完工的产品进行检验,检验合格在《批量管制卡》上本道工序栏内签名,包装箱上贴上标识,方可流入下道工序.3.4.2.检验不合格的产品由生产员工重新自检自分再提交检验.3.4.3.在过程出现不合格的产品控制见《不合格控制程序》和《纠正和预防措施控制程序》.3.5现场工艺纪律巡检3.5.1、检验人员必须针对员工的标准化作业应随时监督,并及时填写现场工艺纪律巡查表;3.5.2、工艺纪律巡查内容:员工严格按WI操作、物料搬运防护标识按要求到位;4、附录4.1 IPQC巡检记录表 (QP-12-R04-A0)4.2 产品的 IPQC控制计划4.3 首件检验报告 (QP-12-R03-A0)。
首件检验报告
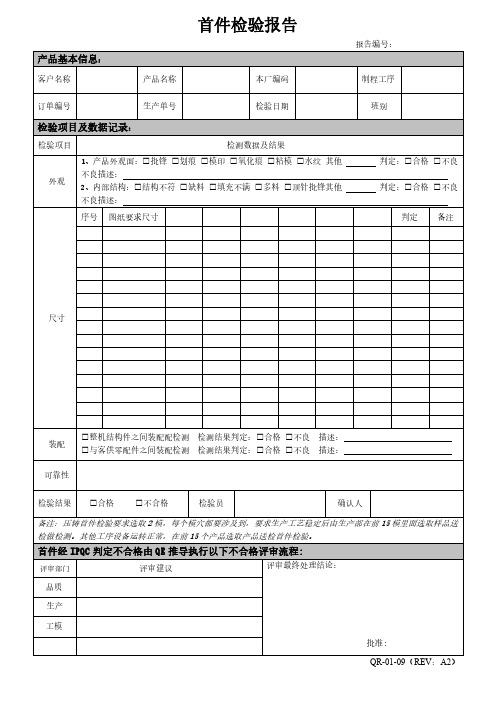
序号 图纸要求尺寸
ห้องสมุดไป่ตู้班别
判定:□合格 □不良 判定:□合格 □不良
判定 备注
尺寸
装配
□整机结构件之间装配配检测 检测结果判定:□合格 □不良 描述: □与客供零配件之间装配检测 检测结果判定:□合格 □不良 描述:
可靠性
检验结果 □合格 □不合格
检验员
确认人
备注:压铸首件检验要求选取 2 模,每个模穴都要涉及到,要求生产工艺稳定后由生产部在前 15 模里面选取样品送
检做检测。其他工序设备运转正常,在前 15 个产品选取产品送检首件检验。
首件经 IPQC 判定不合格由 QE 推导执行以下不合格评审流程:
评审部门
评审建议
评审最终处理结论:
品质
生产
工模
批准:
QR-01-09(REV:A2)
产品基本信息:
客户名称
首件检验报告
产品名称
本厂编码
报告编号: 制程工序
订单编号
生产单号
检验日期
检验项目及数据记录:
检验项目
检测数据及结果
外观
1、产品外观面:□批锋 □划痕 □模印 □氧化痕 □粘模 □水纹 其他 不良描述: 2、内部结构:□结构不符 □缺料 □填充不满 □多料 □顶针批锋其他 不良描述:
制程检验规范

产品(半成品、成品).3.2全检:对制程中的产品或产品的某些检验项目进行100%检验。
3.3巡检:指对生产过程中影响产品品质的因素进行随机抽样检验、确认。
4.职责4.1品管部4。
1.1 负责制程中产品外观、检验流程、检验标准、检验规范、检验站的编制和设置.4.1。
2 IPQC:负责对产品、物料首件确认的主导工作,并对产品首件做出合格与否的判定;制程品质检控,品质异常之追踪与确认;主导不合格品或异常品管问题的提出、跟进、落实、效果确认.4。
1.3 FQC:负责制程中产品外观、产品指定项目的全检。
4.1.4 测试员:负责制程中产品接地、耐压、点亮的全检4。
2工程部4.2.1 参与新产品、试产、设计变更首件的确认,负责制程中产品电气、结构、功能、测试标准,品质异常、不合格品原因的分析及改善对策的提出。
4.2.2 负责制程中产品SOP的制定,工装夹具制作,工艺跟进改善,产能效率的提升,结构性能异常的跟进与落实。
4。
2。
3 负责制程中仪器、设备测试规范的制定;机器、设备、仪器、仪表、治夹具、工具运行状况的监控,设备的正常运转的巡视及日常保养工作监管。
4。
3 业务部:参与新客户第一次生产及客户要求变更后首次生产时首件的确认.4.4 生产部4。
4.1 负责首件的制作与送样确认,自验互检。
4.4.2 制程中5M1E 的落实及制造过程的监控,配合IPQC与PIE的工作;品质异常的受理与改善,改善对策的具体实施。
5.作业内容5.1生产、检验前作业准备5.1.1生产部门5。
1.1.1生产部门在开拉生产前进行自我核查,发现不合格品及异常,采取措施立即纠正,再行生产。
5.1.1。
2 生产部门开拉生产前需查核领用物料是否与制令工单相符,是否有相应的BOM、或样品,工作环境是否符合产品生产需求,各作业工站是否悬挂相应的SOP,人员对作业方法、产品品质是否清楚了解。
【首件确认报告】、【耐压/极性测试记录表】5。
1.1.3 机器、设备、作业工具是否处于正常状态,风批、电批扭力设置是否正确符合作业需求.5。
制程检验程序(含表格)

制程检验程序(ISO9001:2015)1.0目的为规范制程检验,预防产出批量不合格的产品,减少(杜绝)制程异常的发生。
不断降低生产制程不良率,提升产品品质,确保产品品质符合客户要求。
2.0范围适用于本公司生产制程品质检验控制。
3.0定义3.1首件:指生产制程中加工生产的产品,判定符合要求后,拟批量生产前的第一台(个)产品(半成品,成品)。
3.2全检:对制程中的产品或产品的某些检验项目进行100%检验。
3.3巡检:对生产过程中影响产品品质的因素(工位)进行随机抽样检验,确认。
4.0权责4.1品质部4.1.1负责制程中产品外观,检验流程,检验标准,检验规范,检验工位的编制和设置。
4.1.2IPQC:负责对产品,物料首件确认的主导工作,并对产品首件做出合格与否的判定;制程品质检控,品质异常的确认与追踪;主导不合格品或品质异常问题的提出,跟进,落实及改善效果确认。
4.2项目部4.2.1新产品首件的确认,负责制程中电气/结构性能测试流程,测试工位的编制和设置;品质异常,不合格品原因的分析及改善对策的提出。
4.2.2负责制程中设备,仪器的使用规范的制订;机器,设备,仪器,仪表,治夹具,工具运行状况的监控,正常运转的巡视及点检/保养工作的监督。
4.3生产部4.3.1负责首件的制作与送样确认;全检工位的人员配置。
4.3.2制程中4M1E的落实及制程过程的监控,配合IPQC与PE的工作;品质异常的受理与改善,改善对策的具体实施。
4.3.3负责制程中设备,仪器,仪表,治夹具,工具的日常点检/保养工作。
5.0程序5.1生产,检验前作业准备5.1.1生产部5.1.1.1在开拉生产前进行自我核查,发现不符合项及异常,采取措施,立即纠正。
5.1.1.2在开拉生产前须查核领用物料是否与[生产计划排程表]相符,是否有相应的BOM,技术规范;生产环境是否符合产品需求,各作业工位是否悬挂对应的SOP,作业人员对作业方法,产品品质是否清楚了解。
产品首件尺寸检测报告

产品首件尺寸检测报告概述本报告旨在对产品首件尺寸进行全面检测和评估。
尺寸检测是产品质量控制中的重要环节,通过对产品尺寸的精确测量,可以确保产品符合设计要求,提供高质量的产品给客户。
检测对象:产品首件本次尺寸检测的对象是一款新产品的首件,该产品为某公司新研发的电子设备外壳。
由于这是首次生产该产品,为了确保产品质量和性能的稳定,需要对其尺寸进行全面检测。
检测方法本次尺寸检测采用了以下检测方法:1. 数字测量仪:使用高精度的数字测量仪进行各个部件尺寸的测量,可精确到0.01毫米。
2. 三坐标测量仪:对产品整体尺寸进行测量,可以快速准确地获取产品各个方向的尺寸数据。
3. 光学投影仪:对产品的主要外观尺寸进行测量,可以观察和比较产品在不同角度下的尺寸变化。
检测内容外形尺寸首先对产品的外形尺寸进行检测。
测量的内容包括产品的长度、宽度、高度、重量等。
内部尺寸接下来对产品内部的关键部件进行尺寸检测。
该部分检测主要关注与产品功能紧密相关的零部件。
连接尺寸在产品制造过程中,连接处的尺寸通常要求非常精确,因为连接的好坏直接影响产品的性能。
因此,本次检测中也会对连接尺寸进行严格检测。
附件尺寸产品的配件和附件通常需要与产品相匹配,以确保产品能够正常使用。
因此,本次检测还将测量附件的尺寸和相对位置。
检测结果经过全面的尺寸检测,得出以下结果:1. 外形尺寸符合设计要求,产品长度为X毫米,宽度为Y毫米,高度为Z毫米,重量为W克。
2. 内部尺寸符合设计要求,关键部件尺寸均满足规格。
3. 连接尺寸符合设计要求,连接部位尺寸精度高,连接紧固可靠。
4. 附件尺寸与产品相匹配,各附件尺寸准确,配对完善。
结论根据对产品首件的尺寸检测结果,可以得出以下结论:1. 产品首件的尺寸符合设计要求,满足产品生产和使用的需要。
2. 产品的外形尺寸、内部尺寸、连接尺寸和附件尺寸均符合标准要求,各部件尺寸精确,连接紧固可靠,并且配件相对位置准确。
3. 经过尺寸检测,产品的质量得到了验证和保证,可以进行批量生产,以满足市场需求。
QC首件制程巡检规范

文件制修订记录1、目的规范QC对制程的巡检过程,确保公司的生产制程过程,在有效的管制状态下稳定地进行,生产出满足品质要求及客户要求的产品。
2、适用范围本程序适用于与适用于公司制程全过程。
3、定义IPQC:(In-Process Quality Control)制造过程质量控制。
SOP:(Standard Operation Procedure)即标准作业程序。
4、工作程序4.1 QC每班必须对生产首件进行检查确认:4.1.1 QC每班必须按BOM核对物料的规格与描述使用是否正确;4.1.2 QC需确认机型的软件、配色、TAC是否正确;4.1.3 QC对于首件的过程与结果负责。
从物料、操作、QA的首件检测结果都属于QC的监察范围。
4.1.4 QC对点胶或热泥胶进行称重确认点胶的胶量和胶路是否合格。
4.2 QC每天需要对产线的生产设备及ESD防护进行检查:4.2.1 QC每班需要对设备和静电环的点检记录进行核查,并将检查结果记录在《QC制程巡检表》中;4.2.2 QC每班需监督生产部对电烙铁温度和电批扭力的点检情况,并将检查结果记录在《QC制程巡检表》中;4.3 QC每天需要根据生产工艺文件中要求,依照生产工艺文件中细则对产线的工艺纪律进行考核,并将考核结果记录在《QC制程巡检表》中。
4.4 QC每班至少监察产线制程四次,检查各工位员工是否严格依照SOP要求进行操作,并将监察结果记录于《QC制程巡检表》。
4.5物料/产品的标识与摆放监察:4.5.1 物料摆放必须正确,叠放层数不能超出原包装叠放的层数,防止物料受压后导致损坏元器件;4.5.2 半成品摆放必须正确, 叠放层数不能超过8层(60pcs/箱),防止单机头受压后导致外观或功能故障;4.5.3 工位如出现堆机或有半成品,必须有状态标识来区分不同;4.5.4 焊接工位不能将PCBA摆放于电烙铁架与操作工位之间,预防电烙铁嘴的锡渣掉落于PCBA上;4.5.5 QC检测工位,必须对不合格品进行状态标识,并有专用的存放区域,防止因摆放混乱而导致未测试或不良品作为良品流入下一工序。
- 1、下载文档前请自行甄别文档内容的完整性,平台不提供额外的编辑、内容补充、找答案等附加服务。
- 2、"仅部分预览"的文档,不可在线预览部分如存在完整性等问题,可反馈申请退款(可完整预览的文档不适用该条件!)。
- 3、如文档侵犯您的权益,请联系客服反馈,我们会尽快为您处理(人工客服工作时间:9:00-18:30)。
线材尺寸(长度要求
材料(料号、规格、品名、)与BOM一致; 物料用量、位置、方向正确; 雷雕LOGO内容 ,丝印LOGO内容 确认OK; 缺陷,缺陷描述 、提示音 MA; 。 确认OK; 确产品颜色 外观 蓝牙显示名
性能测试
样机或者销售单 主板静态电流
灯光模式与样品一致性OK
包装确认
东莞市**实业有限公司
制程首件检验报告(装配) 生产部填写栏
送检日期 生产线别 首件类型 时 间 口新产品 预计转拉时间: 确认项目 物料核对 自检结果 外观确认 性能测试 包装确认 型号/规格 订单数量 口新订单 口设计变更 首件制作时间: 确认描述 客户名称 首件数量 口转产 口制造条件变更 交销售时间:
送检日期:
制造单号 送检人 口其他( 交品质时间: 确认结果 备注 )
品质部填写栏
检验项目 检验依据 重点控制项检验描述
材料上线检验状态、主板料号 喇叭料号 ,供应商 3.8 V, 电池容量 确认OK; ,规格 MA,供应商 、扎线方式)合格; Ω W。 。
完成时间:
判定 备注
物料核对
BOM
电池电压
样机
附件清单准确性确认OK; 包装方式与样机的一致性OK。
其他 综合判定: 口通过可正常生产
品质部意见:
口NG需重新送检
口NG需停线改善
品质组长签名: 销售部意见:
时间:
销售签名: 审核意见:
时间:
品质主管/经理签名:
时间:
表格编号:QF-LF2*-01
版本:18-01