装配制程检验规范
RF装配工艺规范
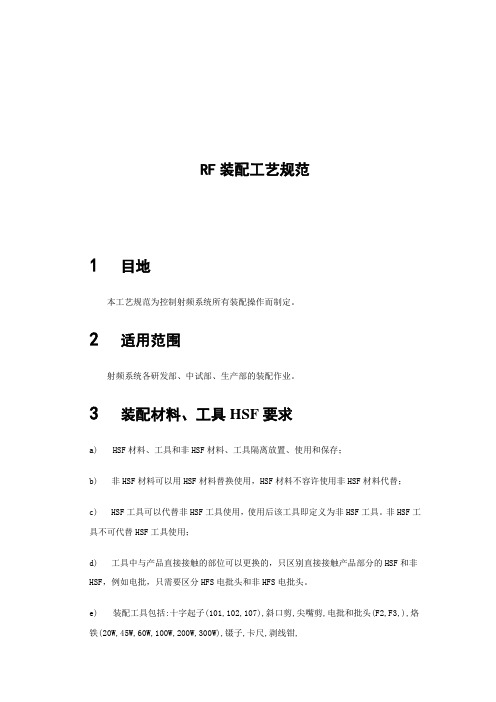
RF装配工艺规范1目地本工艺规范为控制射频系统所有装配操作而制定。
2适用范围射频系统各研发部、中试部、生产部的装配作业。
3装配材料、工具HSF要求a)HSF材料、工具和非HSF材料、工具隔离放置、使用和保存;b)非HSF材料可以用HSF材料替换使用,HSF材料不容许使用非HSF材料代替;c)HSF工具可以代替非HSF工具使用,使用后该工具即定义为非HSF工具。
非HSF工具不可代替HSF工具使用;d)工具中与产品直接接触的部位可以更换的,只区别直接接触产品部分的HSF和非HSF,例如电批,只需要区分HFS电批头和非HFS电批头。
e)装配工具包括:十字起子(101,102,107),斜口剪,尖嘴剪,电批和批头(F2,F3,),烙铁(20W,45W,60W,100W,200W,300W),镊子,卡尺,剥线钳,4装配的要求装配是指一个操作过程,是将产品的全部零件按一定顺序合成部件或将零件和部件合成产品的过程。
在装配过程中,依据装配内容的不同,合理的选择装配工具,装配工具的选用参照<<RF工具使用规范>>.为了保证装配质量,提高工作效率,提高工具的使用寿命,为此,每天要定期对生产工具和设备进行校准.4.1装配有以下几种形式:1)固定式有两种:①集中装配式:有几个人完成一件工作。
适合少量试生产。
②分散装配式:平行作业。
适合个人独立完成一件工作。
2)移动式有两种:①自由移动:无速度限制。
适合于修配工作量较多的装配②强制移动:有速度限制。
适合流水线。
4.2装配有以下几种方法:①完全互换法:不经任何选择和修整就可以进行装配并能达到装配要求和指标。
适合大批量生产。
②选配法:装配精度要求相对比较高,零件的公差范围小。
需要进行选择性装配。
适应生产中高精度的产品要求。
③修配法:将零件按经济公差加工,留有修配量,以满足装配精度要求。
适合小批量生产。
④调整法:用调整办法来改变补偿尺寸,以满足装配精度要求。
5PQC检验操作指导书

编号
版本
A
日期
2023.2.18
制定
审核
批准
一、适用范围:公司装配PQC检验。
二、目的:规范装配PQC作业流程,早期预防批量性的异常。三、详细流程如下:
序号
工序流程
操作照《客户需求信息表》、BoM表、设变单、留样、《成品检验规范》、内部联络单、色样以及相关的标准对生产首样进行首件检验;
c.不良品责任单位是否正确(打标产品:划伤、打标不良退打标,来料不良退电镀Γ;多道工序加工的零件:按责任退给供应商);
d.核对无误后,在《退料单》上签字确认。
10
产线返工方案确认
PQC抽检不良需产线返工的,返工流程按技术提供的方案。PQC将返工的结果填写于《成品检验报告》上。
a.检查牙管是否旋到底,钢套不能往下掉
b.锁住后牙管不能倒转;
C.注意是否会划伤。
塞芯子
a.芯子至少2个台阶塞到内管里,不能全部塞进.
装喇叭接头和螺母
a.两端外牙要朝外,六角螺母装在打字套子端;
尺寸检验
a.按成品检验各项尺寸是否符合标准要求;
b.螺纹要求通规通,止规符合标准要求,螺纹小径需要符合要求;
1.5密封测试:70度热水,动压至0.5MPa,保持5分钟。
1.6低压测试:动压水压0.DIPa,转动缠绕接头,不可产生可见的渗漏。
2
首件不合格处理
反馈产线班长,追溯产线的不合格品并要求产线进行隔离标识,避免混料。按《不合格品控制程序》执行。
3
巡检
检验外观
a.巡查物料是否混料;
b.查看产线检验人员操作方式是否存在碰划伤问题;
C.接头与螺母的尺寸深度要注意管控,不可超出标准要求;
成品检验标准规范.
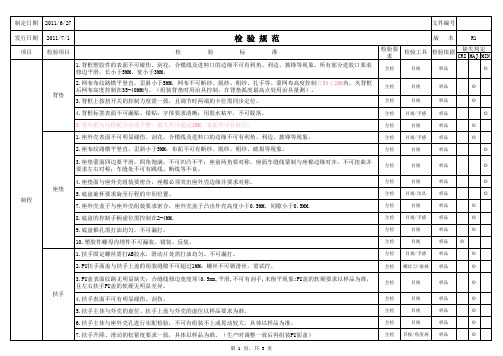
◎ ◎ ◎ ◎ ◎ ◎ ◎ ◎ ◎ ◎ ◎ ◎ ◎ ◎ ◎ ◎ ◎ ◎ ◎ ◎ ◎
第 2 页,共 4 页
1.检查外箱及唛文是否正确,所有的部件和配件是否正确完整。 2.对产品进行跌落测试,检查包装防护是否合格,测试标准依据产品跌落测试要求。 3.成品组装:各部件装配要吻合,组装顺畅.不可漏装/少装/错装/装反,组装螺丝要求全部拧紧。具体参考产品组装说明书 作业。 4.外观检验:座外壳;椅脚不可有破损,刮花等现象;底盘防护罩不可掉落;其它部件参考各部件检验标准。 5.成品椅测量:产品尺寸符合技术资料要求; 5.1 扶手的垂直度需控制在86.5°-89°; 5.2 底盘后仰角度控制在17.5°-20°; 5.3 背垫网布高度控制在35-40MM; 5.4 背垫虚位(调节至最后一档)需控制在4CM以下; 5.5 扶手前后左右晃动的虚位为±1.5MM; 5.6 背角度需控制在75.5-78.5°(测量部位:参照样品要求); 5.7 背转动关节间隙需控制在0.5MM以内。 5.8 成椅尺寸:椅高标准尺寸为(885-1000)±5MM;(参照图纸检验) 5.9 座高标准尺寸为(420-535)±5MM;(参照图纸检验) 5.10 扶手高标准尺寸为(610-670)±5MM;(参照图纸检验) 5.11 扶手内宽标准尺寸为(400-490)±5MM;(参照图纸检验) 5.12 座深标准尺寸为440±10MM;(参照图纸检验) 5.13 气压棒离地标准尺寸为40±5MM;参照图纸检验) 5.14 椅宽标准尺寸:650±5MM;参照图纸检验) 5.15 椅深标准尺寸:570±5MM;参照图纸检验) 5.16 座垫参考尺寸:490*470±5MM;参照图纸检验) 5.17 背垫参考尺寸:445*440±5MM;参照图纸检验) 6.结构功能检验:升降要顺畅;后仰功能正常,且倾仰100次底盘无异声,四档锁定功能正常,椅轮组立成椅走势成直线, 且不能有声音,滑动正常、顺畅;背垫前后调节的松紧度需控制与样品一致。 1.拉背强度测试:施力200磅持续一分钟,功能无异常,结构无变化,测试背角度变化小于2°;施力300磅持续一分钟,允 许功能有异常但结构无变化,测试背角度变化小于5°。 2.扶手垂直强度测试:垂直施力200磅持续一分钟,功能无异常,结构无变化;垂直施力300磅持续一分钟,允许功能异常但 结构无变化。 3.扶手水平强度测试:水平施力100磅持续一分钟,功能无异常,结构无变化;水平施力150磅持续一分钟,允许功能异常但 结构无变化。 强度 测试 4.背关节疲劳测试:施力100磅,测试5万次,螺丝无松动,关节缝隙变化小于1MM。 5.开关疲劳测试:用治具测试5万次,测试后开关需回弹。 6.背疲劳拉背测试:施力100磅,测试6万次,固定关节螺丝无松动,关节间隙变化小于1MM。 7.疲劳冲击:施力100磅,测试10万次,气压棒能自动升降,产品结构不可出现失去效用的现象。 8.成椅冲击测试:气压棒上升至最高和最底时,施力225磅跌落一次,功能性须无异常方可接受。施力300磅跌落一次,允许 功能异常但结构无变化。 9.其它测试项目按BIFMA标准进行测试。 1.来料抽检频率为:100PCS以下抽检1PCS;100-1000PCS抽检2PCS;1000PCS以上抽检4PCS。(小配件及有特殊要求配件除外) 备注 1.本检验标准为R1版,变更蒙网布尺寸,追加背垫项目5、成椅尺寸项目、座背组装项目11,取消原扶手项目7. 2.其它配件请按常规检验标准检验。
WI-B0-003弯管工序品质检验规范与检验标准

5.4试装配性能良好。
5.5缺点等级划分
主要缺点
次要缺点
R弧度不符合设计要求,影响装配,表面严重拉伤,起皱,断裂,部件受压后两边有梭形突出
表面轻度划伤,起皱不明显R弧度稍有变化,但不影响装配。
8、相关记录:
8.1《首件标签》保存期当天
8.2《巡检日报表》保存期3年
5.6处理方法:
5.6.1尺寸测量、破坏性测试按特殊抽样水平S-1抽样;其它按正常检验水平Ⅱ抽样
5.6.2检验的弯管产品缺点等级在标准以内的判定为合格批,超出标准的判定为不合格批,不合格按《不合格控制程序》执行。
6、参考文件或标准:
引用GB/T2828.1-2003
7、附件:
《WI-C7-003AQL抽样方案表(GB2828-2012)》
1、目的:
为确保弯管工序的产品符合本公司之品质要求,特制定本检验规范作为检验依据对弯管工序产品进行质量检验,以确保品质并防止不合格品流入下一道工序。
2、范围:
本标准适用于超杰生产的所有弯管工序的产品质量检验及判定。
3、职责:
制程(金工)品管员负责按照本标准对弯管工序产品进行检验。
4、定义:无
5、作业标准:
零件加工过程检验规程
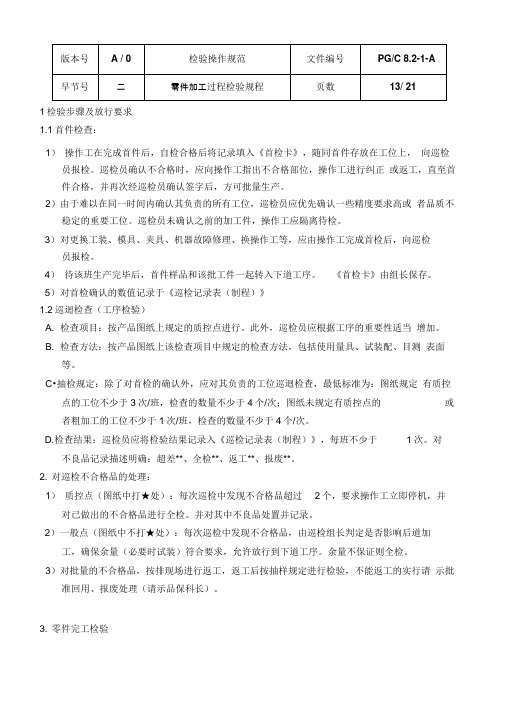
1检验步骤及放行要求1.1首件检查:1)操作工在完成首件后,自检合格后将记录填入《首检卡》,随同首件存放在工位上,向巡检员报检。
巡检员确认不合格时,应向操作工指出不合格部位,操作工进行纠正或返工,直至首件合格,并再次经巡检员确认签字后,方可批量生产。
2)由于难以在同一时间内确认其负责的所有工位,巡检员应优先确认一些精度要求高或者品质不稳定的重要工位。
巡检员未确认之前的加工件,操作工应隔离待检。
3)对更换工装、模具、夹具、机器故障修理、换操作工等,应由操作工完成首检后,向巡检员报检。
4)待该班生产完毕后,首件样品和该批工件一起转入下道工序。
《首检卡》由组长保存。
5)对首检确认的数值记录于《巡检记录表(制程)》1.2巡迴检查(工序检验)A. 检查项目:按产品图纸上规定的质控点进行。
此外,巡检员应根据工序的重要性适当增加。
B. 检查方法:按产品图纸上该检查项目中规定的检查方法,包括使用量具、试装配、目测表面等。
C•抽检规定:除了对首检的确认外,应对其负责的工位巡迴检查,最低标准为:图纸规定有质控点的工位不少于3次/班,检查的数量不少于4个/次;图纸未规定有质控点的或者粗加工的工位不少于1次/班,检查的数量不少于4个/次。
D.检查结果:巡检员应将检验结果记录入《巡检记录表(制程)》,每班不少于1次。
对不良品记录描述明确:超差**、全检**、返工**、报废**。
2. 对巡检不合格品的处理:1)质控点(图纸中打★处):每次巡检中发现不合格品超过2个,要求操作工立即停机,并对已做出的不合格品进行全检。
并对其中不良品处置并记录。
2)一般点(图纸中不打★处):每次巡检中发现不合格品,由巡检组长判定是否影响后道加工,确保余量(必要时试装)符合要求,允许放行到下道工序。
余量不保证则全检。
3)对批量的不合格品,按排现场进行返工,返工后按抽样规定进行检验,不能返工的实行请示批准回用、报废处理(请示品保科长)。
3. 零件完工检验车间加工零件完工后,放在仓库待检区,由品检员进行完工检验,合格后方可入半成品库。
装配车间的规章制度5篇
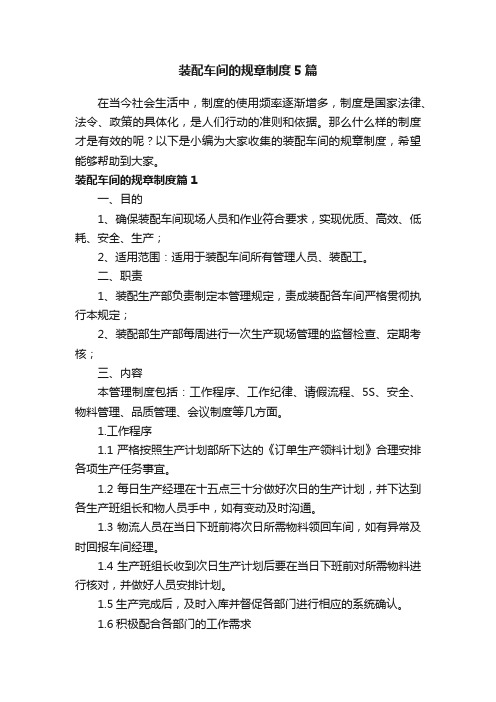
装配车间的规章制度5篇在当今社会生活中,制度的使用频率逐渐增多,制度是国家法律、法令、政策的具体化,是人们行动的准则和依据。
那么什么样的制度才是有效的呢?以下是小编为大家收集的装配车间的规章制度,希望能够帮助到大家。
装配车间的规章制度篇1一、目的1、确保装配车间现场人员和作业符合要求,实现优质、高效、低耗、安全、生产;2、适用范围:适用于装配车间所有管理人员、装配工。
二、职责1、装配生产部负责制定本管理规定,责成装配各车间严格贯彻执行本规定;2、装配部生产部每周进行一次生产现场管理的监督检查、定期考核;三、内容本管理制度包括:工作程序、工作纪律、请假流程、5S、安全、物料管理、品质管理、会议制度等几方面。
1.工作程序1.1严格按照生产计划部所下达的《订单生产领料计划》合理安排各项生产任务事宜。
1.2每日生产经理在十五点三十分做好次日的生产计划,并下达到各生产班组长和物人员手中,如有变动及时沟通。
1.3物流人员在当日下班前将次日所需物料领回车间,如有异常及时回报车间经理。
1.4生产班组长收到次日生产计划后要在当日下班前对所需物料进行核对,并做好人员安排计划。
1.5生产完成后,及时入库并督促各部门进行相应的系统确认。
1.6积极配合各部门的工作需求2.工作纪律2.1遵守作业时间,上下班不准迟到、早退、旷工。
迟到早退一次罚款10元,连续三次或一月内累计四次按旷工一天处理;旷工一天扣除两日工资,连续三次或三月内累计四次旷工者辞退。
2.2上班应着装整洁,穿工作服并正确佩戴厂牌。
违者罚款10元。
2.3严禁穿拖鞋着背心、短裤上班。
违者一律不准上班,更换好服装后方可上班。
2.4工作时间严禁谈笑、打瞌睡、吃零食等。
违者罚款10元。
2.5车间范围内,严禁乱丢果皮、纸屑等杂物。
违者罚款10元。
2.6工作时间严禁看书、玩手机等与工作无关的事;违者罚款10元。
2.7严禁在车间内吵闹、打架斗殴;违者罚款10元,打架斗殴者一律辞退。
fpc检验规范 ()
1. 目的明确与规范手机的FPC来料外观和功能检验标准,使FPC满足既定质量要求。
2. 适用范围本规程适用于本公司所有手机FPC的检验。
注:若新产品不断出现或本标准中的项目涉及不到,应根据公司要求在本标准中加入未涉及到的项目或修正本标准。
3. 职责工程:确定产品的技术要求,向质量部提供相关技术要求以及测量测试方法、设备、夹具。
质量:与工程部确定质量标准,质量和生产部门按照要求进行检验。
4. 样品样品应从正常生产的产品里随机挑选。
产品在研发阶段应该通过试验验证,对不符合项进行改进;量产阶段,工厂按照GB/T 2828.1 正常检验二级水平一次抽样计划,AQL取:Cr=0,Maj=0.4,Min=1.0,从大货里随机抽取样品进行测试。
Cr、Maj、Min的定义:Cr:使用本产品时,影响的客户的安全性,包括人身安全、环境安全,或其它引起较大事故责任的。
Maj:会引起客户对产品的满意度甚至投诉、退换货,例如本产品功能、性能失效,导致产品部分或全部功能无法使用,但不涉及重大责任事故。
Min:会引起客户对产品的满意度,但功能仍能使用,并不会导致客户的投诉、退换货,例如轻微外观问题、包装问题等。
5 . 检验条件及环境5.1、在60—100W日光灯的照明条件下,样品离检查者眼睛约30-40cm处进行检查。
检验方向以垂直线前后左右45°(以时钟3点、6点、9点、12点).5.2、检验者需戴手指套防护。
5.3、检测条件照度: 800-1200 LUX fluorescent lamps. 日光灯照度为:800-1200 LUX环境:22 ±3℃5.4、外观检验者以目视检查,尺寸用卡尺测量。
5.5、电性测试使用夹具,检验功能标准请依样品。
5.6、若标准与规格书不符时,以产品发行之规格书特殊检验规格、工程变更为准。
6. 包装要求6.1 包装检验6.2包装要求⑴、产品外包装为纸箱包装,内包装须用指定的袋子和盘;⑵、现品票应粘在纸箱的右上角,其内容包括:物料名称、物料编码、规格、机型、数量、生产日期、QA检验合格章和特殊标示要求。
航空箱制程检验标准01
(2)不合格批须在本工序完成返检.
(3)不良品须在本工序完成返修后才能流入下一工序.
5.0 各工序检验方法及判定标准:
5.1 铝材加工.
项目 数量 检验内容 检验工具
检验标准
缺点 检验时机 类别 首件 巡检 终检
直角、圆角、腰带铝
规格 P/
目视核对 生产图纸、任务单
等铝材规格
ISO检验规范
工作职责:①严格按图、按工艺文件、按质量标准进行工序检验,使工序质量进一步提高.②负责进料检验、制程检验、成品检验。
对关键零件的主要项次进行重点抽验。
③负责填写各类抽查记录表,搜集质量异常情况,并报告主管领导,共同分析处理质量问题。
进料检验:①对板料的外形尺寸、厚度、数量按采购要求抽检。
②对材质的检定以供货商提供的质量保单为准。
③对外加工零部件按提供的图样抽检或根据装配的实际使用效果判定。
制程检验:①对关键零部件、主要技术项目进行重点首检和巡检并记录于表.②下料、冲剪、折弯工序的上下公差以“0。
5”毫米内为合格;对角线误差在“1”毫米以内为合格。
③孔类工序的上下公差在“0.2”毫米以内为合格,位置尺寸在“0.5”毫米内为合格.④焊接工序要求焊点牢固、平整。
焊接后的座标尺寸在“1”毫米内为合格。
⑤磷化工序以无锈斑,磷化层清晰均匀为合格。
⑥喷涂工序外观平整光泽,膜厚在0.5~0.7毫米内为合格。
耐冲击性、柔韧性、表面硬度、固化条件以供货商提供品质保单为准。
成品检验:①外观平整、整洁、无伤痕、涂膜无脱落现象。
②活动部位缝隙匀称,开合时无阻尼现象。
③各类“五金"配件、工厂商标齐全。
④外包装必须牢靠。
⑤检验合格后,附上合格标签。
一、目的制定进料检验施行的规范,确定来料的品质,数量等符合公司的要求,防止不合格的物料流入厂内。
二、适用范围2。
1原材料2。
2原物料2.3外加工品三、检验规范:3.1对“板料"的外形尺寸、厚度、数量等进行检验,对材质的检验由供应商提供的质量证书为参考。
3。
2“磷化”原料的材质检验以供应商提供的质量证书为参考.3.3“木制家具”按本厂提供的图纸技术要求检验.3.4“塑粉”检验按供应商提供的样板及质量指标证书为参考。
3.5外加工的“密集书架传装置"按本厂提供的图纸和技术要求检验。
一、目的制定最终检验施行的方式,防止不合格的货品流出厂外。
二、适用范围柜子的成品检验三、检验规范3.1外观平整、整洁、无伤痕、涂膜无脱落现现象。
品质检验制度
品质检验制度品质抽样办法1.总则1.1制定目的为节省检验成本,有效管制原物料、产成品之品质,特制定本办法。
1.2适用范围本公司品管单位执行各种抽样检验作业,悉依本办法执行。
1.3权责单位(1)品管部负责本办法制定、修改、废止之起草工作。
(2)总经理负责本办法制定、修改、废止之核准。
2.作业规定2.1抽样计划本公司品质检验之抽样计划采用GB2828(等同MIL-STD-105D)单次抽样,一般检验II级水准及特殊检验S-2水准。
2.2检验原则(1)本公司品质检验之抽样计划采用特别规定,均使用单次正常检验方式。
(2)检验方式如需调整,应由品管部经理(含)以上之人员批准方可变更。
2.3检验方式转换说明2.3.1转换核准程序(1)由品管部提出加严、放宽或恢复正常检验之申请,经品管部经理(含)以上人员批准。
(2)由交验单位提出放宽或恢复正常检验之申请,经品管部经理(含)以上人员批准。
(3)由品管部经理(含)以上人员指示对某些检验采用加严、放宽或恢复正常检验方式,由品管部实施。
2.3.2由正常检验转换为加严检验的条件在正常检验过程中,连续检验十批(不包括两次交验复检批)中,有五批以上被判定不合格(拒收)时,品管部可以申请改用加严检验。
2.3.3由加严检验转换为正常检验的条件在加严检验过程中,连续检验十批均判定合格(允收)时,品管部可以改用正常检验方式。
2.3.4由正常检验转换为放宽检验的条件在正常检验过程中,连续检验十批均判定合格(允许),且在所抽取之样本中,无主要缺陷(MA)及致命缺陷(CR)时,品管部或交验单位可以提出放宽检验的申请。
2.3.5由放宽检验转换为正常检验的条件在放宽检验过程中,只要有一批被判定不合格(拒收)时,品管人员应报请品管部经理恢复正常检验方式。
2.4全数检验时机有下列情形时,经品管部经理(含)以上人员核准,应采用全数检验:(1)交验物料(成品)有致命缺陷(CR)时。
(2)有安全上缺陷或隐患之品质问题时。
- 1、下载文档前请自行甄别文档内容的完整性,平台不提供额外的编辑、内容补充、找答案等附加服务。
- 2、"仅部分预览"的文档,不可在线预览部分如存在完整性等问题,可反馈申请退款(可完整预览的文档不适用该条件!)。
- 3、如文档侵犯您的权益,请联系客服反馈,我们会尽快为您处理(人工客服工作时间:9:00-18:30)。
乐清市莱恩科技有限公司文件编号WI/LE-PZ-03-2009
版 / 次 A / 1
制程检验规范
页码 1 / 8
1、目的
为了严格执行ISO9001-2008质量体系管理要求、确保制造产品符合本公司使用要求,保证生产顺利进行,特制订本规范。
2、范围
公司自行生产的半成品及成品检验指导。
3、职责
制程检验(IPQC检验员)负责执行检验、指导及判定,负责品质异常开立《品质异常处理单》、负责客户抱怨及制程不良的内容分析及不良查核、处理并记录。
品质部经理负责对处理结果进行核准。
4、工作内容
4.1检验依据:
检验图、制程检验规范
4.2检验
制程检验(IPQC)员首检,巡检,完工检应快速对产品进行外观、尺寸、结构、性能等的检验、试验,并做出合理合理判定。
4.3判定/标示
A、 制程中产品所有检验、试验项目无任何缺陷,或存在缺陷但在允收范围内,应判定合格状态并签名确认,报部门经理核准通过后方可进行批量生产,完工产品判定合格进行标识后将物料移至QC待检区。
B、制程所有检验、试验项目存在任何一项质量缺陷,在允收范围外,应判定为不合格状态并签名确认,报部门经理核准通过后责令整改.完工品不合格进行标识后进行封样,并将物料移至不合格区或立即通知车间返工.
4.5信息反馈
制程所有检验、试验项目存在任何一项质量缺陷,在允收范围外,由制程检验(IPQC)员开立《品质异常处理单》报部门经理进行审批。
常规状况下,产品出现异常时品质部经理直接批准不合格处理,转发生产部、技术部,由巡检跟进处理进度及效果,特殊情况可由相关部门提出评审。
4.6质量评审
制程中发现产品出现异常,但由于特殊原因有必要提出评审的参照《不合格品控制程序》.
4.7检验记录
制程中所有检验项目应得到真实,完好记录,并得到审批,记录保存周期为24个月。