热模锻压力机设计说明书
第十二章 压力机模锻工艺及模具设计

(2)锻件图的制订 确定锻件图的原则和内容与锤上模锻相同,不同点如下: 1)热模锻压力机有顶出装置,锻件能方便地从深型腔内取出,分模面可 以灵活地选择。 2)锻件拔模斜度一般比锤上模锻件小一级。外斜度为3°~7°,内斜度 为7°~10°,或视孔的相对深度而定。当h>0.75d时,采用两级拔模 斜度。
5)飞边槽的型式与锤上模锻相似,不同之处在于 仓部是开通的。如图12-4
图12-4 飞边槽的形式 a) 用于形状较复杂锻件 b)用于形状较简单锻件
(2)预锻工步设计:预锻工步设计原则与锤上模锻相似。设计时应着 重考虑以下几点:
1)预锻工步图的高度尺寸相应要比终锻大2~5mm,宽度尺寸比 终锻要小0.5~1mm,对高筋和凸出部分,取较大差值。
之比大于1.6~2时,应增加压扁工步。 (2)对断面有一定变化的锻件:断面变化不超过10%~15%时,采用压
肩~终锻或压肩~预锻~终锻。 (3)对截面变化大的锻件:采用其它设备制坯(辊锻、平锻、楔横轧、
空气锤等)或采用成型毛坯。 (4)对弯曲类锻件,是否需要采用弯曲工步与锤上模锻相同。 在热模锻压力机上模锻质量和尺寸较小的锻件时,可以采用多件模锻。
图12-18 整体式模锻
组合式锻模或镶块锻模结构,便于实现模具零件的标准化,中小批 量的生产多用此种形式。
图12-19 镶块式锻模
图12-20 用楔紧固模块
摩擦压力机上模锻,上下模的导向方式见图12-21、图12-22。
图12-21用导销导向
图12-22 凸凹模导向的结构型式 a) 圆柱面导向 b) 圆锥面导向 c) 喇叭形导向
(1)终锻工步设计:根据热锻件图设计的。与锤 上模锻相似,不同之处有以下几点:
1)上下模充满的难易程度差别不大,应考虑锻件 的定位和取出方便。
压力机设计说明书
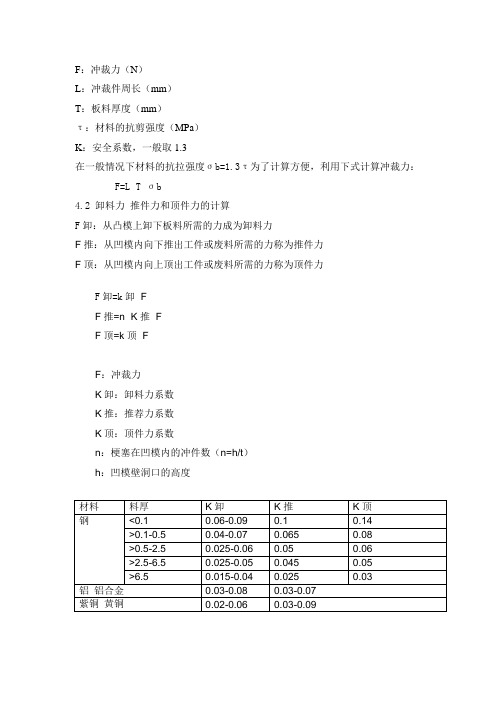
F:冲裁力(N)L:冲裁件周长(mm)T:板料厚度(mm)τ:材料的抗剪强度(MPa)K:安全系数,一般取1.3在一般情况下材料的抗拉强度σb=1.3τ为了计算方便,利用下式计算冲裁力: F=L×T×σb4.2 卸料力推件力和顶件力的计算F卸:从凸模上卸下板料所需的力成为卸料力F推:从凹模内向下推出工件或废料所需的力称为推件力F顶:从凹模内向上顶出工件或废料所需的力称为顶件力F卸=k卸×FF推=n×K推×FF顶=k顶×FF:冲裁力K卸:卸料力系数K推:推荐力系数K顶:顶件力系数n:梗塞在凹模内的冲件数(n=h/t)h:凹模壁洞口的高度材料料厚K卸K推K顶钢<0.1 0.06-0.09 0.1 0.14>0.1-0.5 0.04-0.07 0.065 0.08>0.5-2.5 0.025-0.06 0.05 0.06>2.5-6.5 0.025-0.05 0.045 0.05>6.5 0.015-0.04 0.025 0.03铝铝合金0.03-0.08 0.03-0.07紫铜黄铜0.02-0.06 0.03-0.094.3 压力机所需总冲压力的计算计算冲裁所需的总冲压力时,应先根据模具结构的具体情况,分析总冲压力究竟包含上述冲裁力和卸料力,推件力和顶件力中的哪几项。
采用弹压卸料装置和下初件模具时,上模在冲裁的同时还需克服卸料弹簧阻力和推动梗塞在凹模的材料的推力,于是FQ=F+F卸+F推采用弹压卸料装置和上初件模具时:FQ=F+F卸+F顶采用刚性卸料装置和下出模具时:FQ=F+F推。
80MN热模锻压力机控制系统设计

80MN热模锻压力机控制系统设计热模锻压力机是借助模具实现金属热成型的锻压设备。
它广泛应用于汽车、拖拉机、机车、石化、军工等行业,是进行大批量、高精度模锻件生产的首选设备。
它可以进行镦粗、预锻、终锻、切边、冲孔等工序。
热模锻压力机的用途非常广泛,在热模锻压力机上可以完成开式模锻、闭式模锻、挤压等各种型材的热模锻工艺。
在热模锻压力机上进行锻造的典型零件有:(1)通过镦粗形式成型的锻件,如法兰盘和齿轮毛坯等。
(2)通过挤压方式成型的锻件如一些筒型零件。
(3)通过预先引伸方式成型的锻件,如汽车发动机的曲轴、前梁等。
1 热模锻压力机工作原理热模锻压力机主要由压平机的主机本体、辅助设备、液压系统、润滑系统、气动系统和电气控制系统组成。
压力机本体采用整体实心铸造机身,“X”型滑块导轨,双点支撑结构,具有刚性好、导向精度高、抗偏载能力强等特点。
主电机拖动小飞轮旋转,小飞轮通过皮带传动带动大飞轮,与大飞轮同轴的小齿轮与大齿轮啮合,而大齿轮最终为滑块提供动力,为了增加惯性,所以大齿轮的尺寸非常大,以保证有足够的惯性。
当电机经过四级启动1/ 8电阻启动完毕后,此时转速达到额定转速,通过离合器与制动器的配合,使滑块上下运动,滑块从上死点运动至下死点再回到上死点为一个工作循环,上死点也就是滑块的上极限位,下死点既为滑块下极限位。
压力机滑块有两种工作方式:调整与单次,调整工作方式时,滑块可以点动的停在任何位置;单次工作方式时,踩下脚踏开关,滑块完成一个工作循环。
由于机械构造的原因,润滑对热模锻压力机尤为重要,在压机本体上有多处干油及稀油润滑监测点和温度监测点,如:曲轴干油润滑、高速轴稀油润滑、曲轴温度等,这些监测点将开关量信号传入PLC控制系统,实时反映各个监测点的状态,以防止润滑不到位导致机械设备损坏。
2 工艺流程该热模锻压力机采用KUKA机械手上料,棒料经过传送带进入中频加热炉进行加热,当温度达到900℃左右时,棒料从加热炉中送出,此时上料机械手抓起热棒料送入压力机第一个工位,机械手撤出等待锻压,压力机滑块向下动作时,滑块动力是靠电机的带动,在上下模具接触到之后,也就是到达下死点后,滑块是靠惯性向上动作,在向上运行的过程中,上下顶料器顶出,将工件顶出模具。
热模锻压力机封闭高度调节机构优化设计

随着汽车行业的飞速发展,特别是乘用车的车型多元化、关键部件轻量化等发展趋势,对关键零部件锻坯质量的要求越来越高,国内的锻造行业落后的技术水平已很难匹配我国汽车行业的发展脚步。
相比而言,热模锻压力机具有动作精确可控,打击能量大,运行速度高,锻件精度好,适合于使用步进式机械手实现多工位自动化作业等特点,在国内外锻造行业的应用越来越广泛,具有广阔的市场前景和卓越的经济效益。
热模锻压力机是引进世界先进技术生产的系列产品,因其生产效率高、易于实现自动化、噪声和振动小等优点,因而在现代锻压生产中的应用日趋广泛,是现代锻造生产中不可缺少的高精锻设备。
扬力集团是国内较早研制中小型热模锻压力机的厂家之一,通过对现有技术进行改进与优化,现已开发出HGP4000以下全套系列产品,填补了公司在这一领域的空白。
为了适应不同模具对封闭高度的要求,在热模锻压力机上必须设有封闭高度调节装置[1],扬力在现有技术的基础上对封闭高度的调节装置进行了优化设计。
1传统热模锻压力机1.1封闭高度调节系统热模锻压力机封闭高度调整装置一般通过改变连杆长度A 来实现封闭高度调整。
如图1所示,在压力机正常工作时压紧杆6把偏心压力销1锁死,当需要调节封闭高度时,由油缸控制把压紧杆与偏心压力销1形成一定间隙[2],从而达到调节封闭高度所需的条件;偏心压力销1上加工有涡轮,涡轮是偏心的并与连杆小头和滑块的内圆弧面相接,滑块与连杆3的连接通过连杆销2和偏心压力销1实现。
由于偏心压力销1与连杆销2不同心,所以当电机3通过万向连轴器4、伞齿轮副5、由蜗杆6驱动偏心压力销转动时,偏心压力销1的中心发生变化,从而可以实现连杆长度A 的调节,最终实现压力机封闭高度的调整。
1.2封高调节装置缺点在压力机在工作过程中,滑块需要做上下往复运动,由于电机固定在导轨上,导致万向节连轴器的花键轴与花键套必须跟着上下往复运动。
如图2所示,万向节主要有花键轴、花键套、叉头组成,当花键收稿日期:2020-02-25;修订日期:2020-03-28作者简介:潘地磊(1989-),男,硕士,工程师,从事压力机机械设计。
第五章热模锻曲柄压力机上模锻

分模优点:毛边体积小。可锻深孔。用挤压、墩粗替代拔长、滚挤。
2.形状较复杂的长轴、弯曲类锻件分模面与锤上模锻,以纵向最大剖面分模。
二、余量与公差 和压力机吨位有关。与锤上模锻相比余量和公差相应减少。余量小30~50%,公差小一个等级。
曲柄压力机模锻件公差及其余量
三、锻模斜度、圆角半径、冲孔连皮 锻模斜度:无顶出机构时与锤上模锻相同。有顶出结构时斜度可显著的减少。 曲柄压力机模锻斜度(º) 圆角半径:和锤上模锻相比,圆角半径要增加。 冲孔连皮:设计同锤上模锻。
5-5 锻模结构 一、锻模结构形式 曲柄压力机工作时滑块速度低,工作平稳,装有顶出 机构,锻时上下模不压靠,锻模承受过剩能量少,不考虑 锻模承击面。 压力机模具大多数采模座+内带型槽镶块的组合形式 结构。 模架主要组成有: 模座; 导柱、导套; 顶出结构; 镶块紧固件; 镶块垫板等组成。
锤上模锻分模面
曲柄压力机模锻分模面
(2)终锻型槽有较深的孔时,应在金属最后充型的部位增加通气孔。
2.镶块的形状与尺寸 镶块的形式随锻件的形状和镶块的紧固方式而定。 镶块的种类:圆形和矩形。用压板或斜度匹配进行紧固。 镶块模壁厚度S0 S0=(1~1.5)h ≥ 40mm 镶块闭合状态的高度不大于(0.3~0.4)H(模具闭合高度)
连杆工作原理图
(2)系统构成 工作系统:称曲柄连杆机构。它由曲轴、连杆、滑块等零件组成,其作用是将曲柄的旋转运动转变为滑块的直线往复运动,由滑块带动模具工作。 传动系统:包括齿轮传动、皮带传动等机构,起能量传递作用和速度转换作用。 操纵系统:包括离合器、制动器等零部件,用以控制工作机构的工作和停止。 能源系统:包括电动机、飞轮。 支撑部分:主要指机身,它把压力机所有部分连接成一个整体。 辅助系统:如润滑系统、保护装置等。
MP-1600热模锻压力机精锻齿轮自动化锻造生产线技术方案
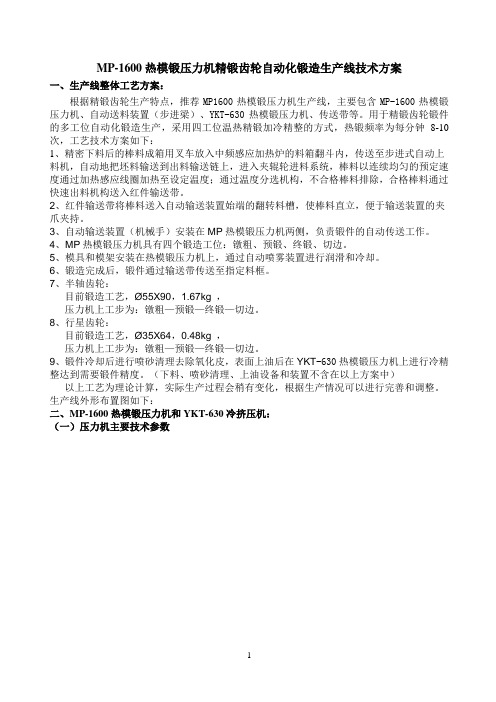
MP-1600热模锻压力机精锻齿轮自动化锻造生产线技术方案一、生产线整体工艺方案:根据精锻齿轮生产特点,推荐MP1600热模锻压力机生产线,主要包含MP-1600热模锻压力机、自动送料装置(步进梁)、YKT-630热模锻压力机、传送带等。
用于精锻齿轮锻件的多工位自动化锻造生产,采用四工位温热精锻加冷精整的方式,热锻频率为每分钟8-10次,工艺技术方案如下:1、精密下料后的棒料成箱用叉车放入中频感应加热炉的料箱翻斗内,传送至步进式自动上料机,自动地把坯料输送到出料输送链上,进入夹辊轮进料系统,棒料以连续均匀的预定速度通过加热感应线圈加热至设定温度;通过温度分选机构,不合格棒料排除,合格棒料通过快速出料机构送入红件输送带。
2、红件输送带将棒料送入自动输送装置始端的翻转料槽,使棒料直立,便于输送装置的夹爪夹持。
3、自动输送装置(机械手)安装在MP热模锻压力机两侧,负责锻件的自动传送工作。
4、MP热模锻压力机具有四个锻造工位:镦粗、预锻、终锻、切边。
5、模具和模架安装在热模锻压力机上,通过自动喷雾装置进行润滑和冷却。
6、锻造完成后,锻件通过输送带传送至指定料框。
7、半轴齿轮:目前锻造工艺,Ø55X90,1.67kg ,压力机上工步为:镦粗—预锻—终锻—切边。
8、行星齿轮:目前锻造工艺,Ø35X64,0.48kg ,压力机上工步为:镦粗—预锻—终锻—切边。
9、锻件冷却后进行喷砂清理去除氧化皮,表面上油后在YKT-630热模锻压力机上进行冷精整达到需要锻件精度。
(下料、喷砂清理、上油设备和装置不含在以上方案中)以上工艺为理论计算,实际生产过程会稍有变化,根据生产情况可以进行完善和调整。
生产线外形布置图如下:二、MP-1600热模锻压力机和YKT-630冷挤压机:(一)压力机主要技术参数MP-1600(二)MP热模锻压力机主要特点1、机架:采用整体式铸造机身。
机架两侧开有侧窗口,方便横向送料。
6000kN热模锻压力机模架结构设计

加
9
图1 模架结构
1 8
最大合模高/ mm
能力发生点/ mm
60 5
5
滑块面积 ( . . ) LR XFB/ Xml mm T l
6 0X6 0 9 3
工作台面积 ( - FB / m X m LRX - ) m m
侧 窗 口尺 寸/ Xmm mm 上 顶 料 能 力一 程/ m n 行 t l - 下 顶 料 能 力一 程/ ml 行 t n —
,
m et M ol o w r
n O. m fl S co g
热 碧 置 蕉 参 .热。 倦 锈 ’ 一 … 工 磊 … 加 一
上 下 模 板 是 上 模 架 的主 体 ,必 须 能 经 受 长 期 使 用 而 不 失 效 ,即具 有 一 定 的 抗 冲 击性 、较 高 强 度 及 耐 磨 性 。 因此 模板 材 质不 宜 选 用铸 钢 ,此 模 架 模板 采 用4 CMo 钢 ,热 处理 后 硬 度 3~ 6 R 2r 锻 2 3 H C。
定位 ,所 以其硬度 尽量高 点 ,在 锻打过 程 中不易
变 形 。 材 质 选 用 4 C M o 钢 ,热 处理 后 硬 度4 ~ 2r 锻 0
4 HRC 。 4
要有好的冲击韧度 ,材质选 用H1 ,热处理后硬度 3
60k 热模锻压力机模架结构设计 00 N
浙江德美轴 承有限公 司 ( 嵊州 32 0 ) 董 1 5 0 雷
1 设计 要求 .
— —
模架是热模锻压力机上锻模 的通用部分 ,不 同 锻件按工序单独设计的模块安装在模架上。模架作 为紧固锻模和传力构件 ,设计时必须考虑模 架的强
度及 生 产过 程 中的 安 全性 ,并 且 在保 证 锻 件生 产 效
如何设计热模锻压力机制动器以及离合器
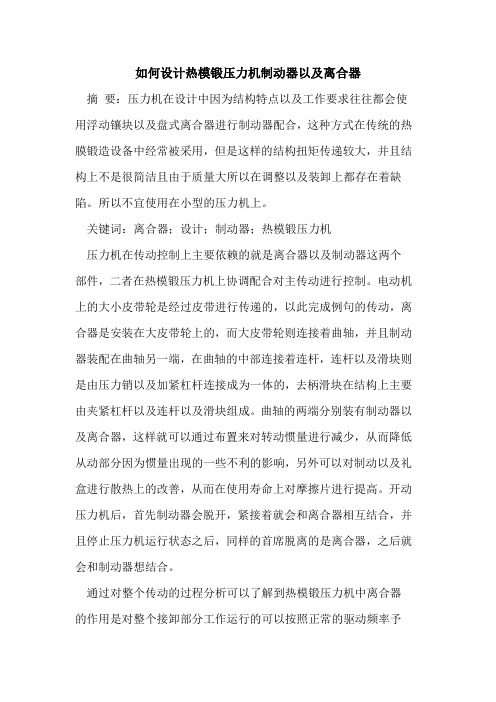
如何设计热模锻压力机制动器以及离合器摘要:压力机在设计中因为结构特点以及工作要求往往都会使用浮动镶块以及盘式离合器进行制动器配合,这种方式在传统的热膜锻造设备中经常被采用,但是这样的结构扭矩传递较大,并且结构上不是很简洁且由于质量大所以在调整以及装卸上都存在着缺陷。
所以不宜使用在小型的压力机上。
关键词:离合器;设计;制动器;热模锻压力机压力机在传动控制上主要依赖的就是离合器以及制动器这两个部件,二者在热模锻压力机上协调配合对主传动进行控制。
电动机上的大小皮带轮是经过皮带进行传递的,以此完成例句的传动,离合器是安装在大皮带轮上的,而大皮带轮则连接着曲轴,并且制动器装配在曲轴另一端,在曲轴的中部连接着连杆,连杆以及滑块则是由压力销以及加紧杠杆连接成为一体的,去柄滑块在结构上主要由夹紧杠杆以及连杆以及滑块组成。
曲轴的两端分别装有制动器以及离合器,这样就可以通过布置来对转动惯量进行减少,从而降低从动部分因为惯量出现的一些不利的影响,另外可以对制动以及礼盒进行散热上的改善,从而在使用寿命上对摩擦片进行提高。
开动压力机后,首先制动器会脱开,紧接着就会和离合器相互结合,并且停止压力机运行状态之后,同样的首席脱离的是离合器,之后就会和制动器想结合。
通过对整个传动的过程分析可以了解到热模锻压力机中离合器的作用是对整个接卸部分工作运行的可以按照正常的驱动频率予以转动的保证,并且对工作扭矩进行传递,而制动器的工作则是对曲轴进行停止的,对其停止的时间进行保证,而且,还低滑块和与滑块相关的零件进行精确的定位,使得在电气以及气动系统因故障停止后得以保证设备安全。
1 结构在目前所使用的热模锻压力机中多采用的是启动摩擦结构的离合以及制动设备,而浮动镶块以及盘式优势气动摩擦的两种形式,而从摩擦盘数目上面又能够分成多盘以及单盘两种形式,而目前所用的mp热模锻压力机就是采用的浮动镶块的气动摩擦,在离合以及制动系统上具有紧凑简单的构造,并且质量也较小,转动惯量在冲动部分影响也不大,对离合器的散热功能较为有利,并且由于结构简单,因此拆装便捷,又能够延长摩擦块的寿命,并且易于保养,摩擦材料的更换也很容易,无论是制造还是使用成本都相对较低。
- 1、下载文档前请自行甄别文档内容的完整性,平台不提供额外的编辑、内容补充、找答案等附加服务。
- 2、"仅部分预览"的文档,不可在线预览部分如存在完整性等问题,可反馈申请退款(可完整预览的文档不适用该条件!)。
- 3、如文档侵犯您的权益,请联系客服反馈,我们会尽快为您处理(人工客服工作时间:9:00-18:30)。
热模锻压力机设计说明书
课程名称:现代设计
学院:机械工程学院
专业:机自
姓名:苏军
学号:1008030355
年级:机自107 班
任课教师:何玲
20013年 11 月20 日
设计任务书
小组成员:丁万飞韦晓光苏军王清鹤指导教师:何玲
一.题目:设计连杆式热模锻压力机。
压力机工作平稳,其中热模锻压力机由一般规模厂中小批量生产。
热模锻压力机传动系统简图
二.设计内容:
一)设计计算
1.传动零件的设计;
2.轴的设计;
二)图纸的绘制
热模锻压力机装配图绘制;零件图绘制
三)编写课程设计说明书
内容包括:目录、设计题目、设计内容、终结、参考文献。
三.设计要求
热模锻压力机装配图1张(A1)。
2、零件图一张(A4)
3、详细设计计算说明书1份(含标准封面、正文并装订)。
目录
一、设计说明 (1)
二、轴设计…………………………………………………………
1.偏心轴设计……………………………………………………
2.细长轴设计……………………………………………………
三、连杆设计………………………………………………………
四、齿轮设计………………………………………………………
五、设计优缺点分析………………………………………………
六、终结……………………………………………………………
七、参考文献………………………………………………………
一、设计说明
热模锻压力机在汽车、拖拉机、内燃机、船舶、航空、矿山机械、石油机械、五金工具等制造业中,用于进行成批大量的黑色和有色金属的模锻和精整锻件,
锻造出的锻件精度高,材料的利用率高,生产率高,易于实现自动化,对工人的操作技术要求低,噪声和振动小等优点。
设计一个连杆式两级传动热模锻压力机。
二、轴设计
1.偏心轴
轴总长d=1000mm
偏心轴效果图
2.细长轴
轴总长d=1000mm
细长轴效果图
三、连杆设计
效果图
四、齿轮设计
传动比i=3,模数m=4
z1=23,d1=270,B1=82,z2=68 ,d2=92,B2=80。
小齿轮效果图
大齿轮效果图
五、设计优缺点分析
装配图
优点:工作平稳,效率高,结果简单。
缺点:没有离合器,一旦工作无法及时停止,没有设计顶出工件装置。
六、总结
此次设计基本掌握了Solidworks软件的基本操作,更进一步理解设计的理念,本次设计加强了自己的动手能力,让我们知道设计一个机器的基本步骤,为今后的学习和工作都起到了很好的理论和实践作用。