公差分析简介及实例分析
公差分析报告基本知识
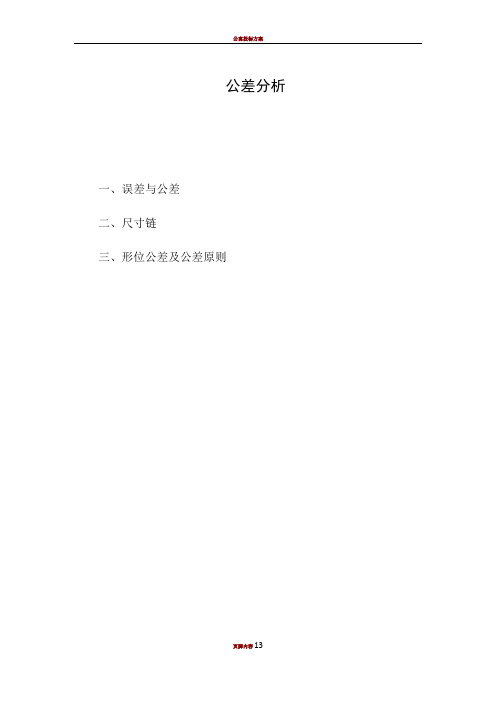
公差分析一、误差与公差二、尺寸链三、形位公差及公差原则一、误差与公差(一)误差与公差的基本概念1. 误差误差——指零件加工后的实际几何参数相对于理想几何参数之差。
(1)零件的几何参数误差分为尺寸误差、形状误差、位置误差及表面粗糙度。
尺寸误差——指零件加工后的实际尺寸相对于理想尺寸之差,如直径误差、孔径误差、长度误差。
形状误差(宏观几何形状误差)——指零件加工后的实际表面形状相对于理想形状的差值,如孔、轴横截面的理想形状是正圆形,加工后实际形状为椭圆形等。
相对位置误差——指零件加工后的表面、轴线或对称面之间的实际相互位置相对于理想位置的差值,如两个面之间的垂直度,阶梯轴的同轴度等。
表面粗糙度(微观几何形状误差)——指零件加工后的表面上留下的较小间距和微笑谷峰所形成的不平度。
2. 公差公差——指零件在设计时规定尺寸变动范围,在加工时只要控制零件的误差在公差范围内,就能保证零件的互换性。
因此,建立各种几何公差标准是实现对零件误差的控制和保证互换性的基础。
(二)误差与公差的关系图1由图1可知,零件误差是公差的子集,误差是相对于单个零件而言的;公差是设计人员规定的零件误差的变动范围。
(三)公差术语及示例图2以图2为例:基本尺寸——零件设计中,根据性能和工艺要求,通过必要的计算和实验确定的尺寸,又称名义尺寸,图中销轴的直径基本尺寸为Φ20,长度基本尺寸为40。
实际尺寸——实际测量的尺寸。
极限尺寸——允许零件实际尺寸变化的两个极限值。
两个极限值中大的是最大极限尺寸,小的是最小极限尺寸。
尺寸偏差——某一尺寸(实际尺寸,极限尺寸)减去基本尺寸所得到的代数差。
上偏差=最大极限尺寸-基本尺寸,用代号(ES)(孔)和es(轴)下偏差=最小极限尺寸-基本尺寸,用代号(ES)(孔)和es(轴)尺寸公差——允许尺寸的变动量尺寸公差=最大极限尺寸-最小极限尺寸公差带零线——在极限与配合图解中,标准基本尺寸是一条直线,以其为基准确定偏差和公差。
公差分析讲义

RSS
用于 制作模具的设计图纸出图前, 即 已收集到工程数据时 使用. RSS 公差分析方法 根据部品的变化量来 决定系统不良的可能性 根据RSS进行 6σ 设计时, 预想会发生 4.3ppm 不良
μ 1 + μ2 + μ3 + μ4
如果两部品的尺寸相互独立, 平均和标准偏差的共分散就是 “0”, 所以只进行加减计算即可
μx+y= μx + μy μx-y = μx – μy σ2x+y = σ2x + σ2y σ2x-y = σ2x + σ2y (X + Y)的平均 (X - Y)的平均 (X + Y)的分散 (X - Y)的分散
+
A
Block Box(右侧) Gap
B1 Block 1 的 大小
B2 Block 2 的 大小
B3 Block 3 的 大小
B4 Block 4 的 大小
Gap = A – B1 – B2 – B3 – B4
Gap比 0.0 小时, 会出现干扰. 平均Gap: μgap= μe - μ1+2 = 80.0 - 79.0 = 1.0mm Gap的标准偏差:
gap gap
e 1 2
2 2
2
0 . 3408
2
0 . 2032
2
0 . 1270
2
gap 0 . 3877
理想的 6σ 水平的设计是 :
- 确认是否满足顾客要求 - 确认标准偏差
公差分析简介及实例分析
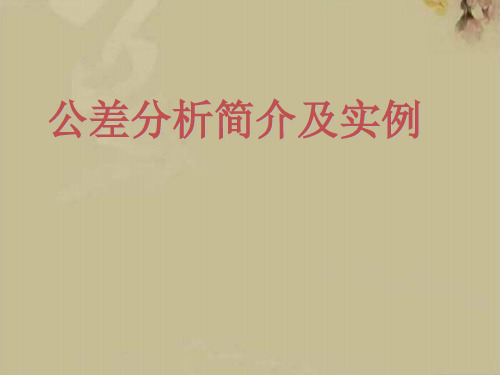
缺点:易产生过于保守的设计 导致制造成本提高
共面度=0.
求尺寸链上各尺寸的基本尺寸及极限偏差
对于呈非正态分布之零件组合
如果想得到合理的零件工差分布,就必需了解其实际的制程能力.
共面度: 须靠平时对工艺知识的不断累积
3481 0.
SHIELDING 36 0. 474 0.
SHELL
=HOUSING高+CONTACT高-SHELL高
* 3.产品开发设计的需要 产品设计一般分为 原形设计 和 二次生产设计
不进行公差分析意味着将在制造时冒很大的风险
二 公差分析的作用及分类
1设计时利用公差分析可合理分配各零件的公差.达到可制造 性的要求.
2.制造时可用以校核公差组合可否满足产品功能要求
3.降低制造成本 针对不同的状况 使用不同的公差分析方法
3σ=3 0.0032+0.02522+0.00172+0.00132+0.005482+0.003852 =0.0756
Z=(0.10-0.0319)/0.0252=2.702
查表得:P1=0.34%
小 结:
1.如果想得到合理的零件工差分布,就必需了解其实际的制程能力.须靠平时对工 艺知识的不断累积
2.631
0.326
0.476 0.014 3.36 0.038
2.619 2.625
0.250 0.298
0.470 0.009 3.34 0.021 0.474 0.012 3.3481 0.029 0.0017 0.0013 0.00548 0.00385
0.003
0.0252*
X0=(2.625+0.298)+(0.474+0.012)-(3.3481+0.029)=0.0319
第4部分:公差分析指南

22
DFMA
谢 谢 !
23
3.当公差分析的结果不满足要求时:
DFMA
减少尺寸链的长度; A为54.00±0.20,C为25.00±0.15,D为28.50±0.15
优化的设计
18
四. 公差分析指南
3.当公差分析的结果不满足要求时:
DFMA
使用定位特征; 好处:
定位特征可以提供较精密的尺寸公差 定位特征的尺寸可以放置于比较容易进行尺寸管控的区域 使用定位特征时可以减少和避免对其他尺寸的公差要求,只需严格管控定 位特征的相关尺寸,就可以满足产品设计要求 因为定位特征精度高,使用定位特征有利于减少零件之间的尺寸公差累积
DFMA
制造工艺能力决定了公差分析中公差的设定; 二维图纸中公差标注与公差分析中的公差一致; 对公差分析中的尺寸需要进行制程管控;
制造工艺 能力
公差分析中 公差的设定
二维图样零 件公差标注
零件尺寸 制程管控
15
四. 公差分析指南
3.当公差分析的结果不满足要求时: 不推荐的做法:
DFMA
调整尺寸链中的尺寸公差大小; 降低目标尺寸判断标准;
100±0.20
3
一. 公差分析的介绍
2.公差的本质:
DFMA
公差是产品设计和产品制造的桥梁和纽带,是保证产品以优异的质量、 优良的性能和较低的成本进行制造的关键。
设计 功能 性能 外观 可装配性 设计限制 稳健性设计 设计意图 产品质量 客户满意
公差
制造 制造费用 装配费用 制造方法选择 机器 夹具 检验 不良率 返工率
推荐的做法:
减少尺寸链的长度; 使用定位特征;
公差分析 ppt课件
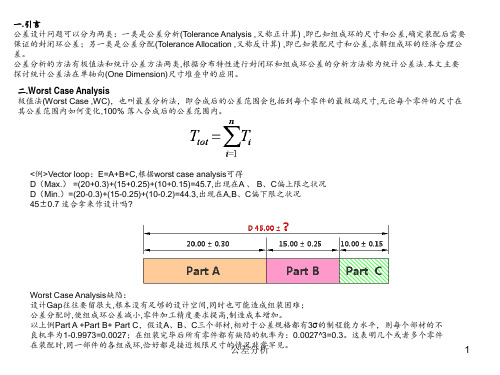
<例>Vector loop:E=A+B+C,根据worst case analysis可得 D(Max.) =(20+0.3)+(15+0.25)+(10+0.15)=45.7,出现在A 、 B、C偏上限之状况 D(Min.)=(20-0.3)+(15-0.25)+(10-0.2)=44.3,出现在A,B、C偏下限之状况 45±0.7 适合拿来作设计吗?
Worst Case Analysis缺陷:
设计Gap往往要留很大,根本没有足够的设计空间,同时也可能造成组装困难;
公差分配时,使组成环公差减小,零件加工精度要求提高,制造成本增加。
以上例Part A +Part B+ Part C,假设A、B、C三个部材,相对于公差规格都有3σ的制程能力水平,则每个部材的不
一.引言 公差设计问题可以分为两类:一类是公差分析(Tolerance Analysis ,又称正计算) ,即已知组成环的尺寸和公差,确定装配后需要 保证的封闭环公差;另一类是公差分配(Tolerance Allocation ,又称反计算) ,即已知装配尺寸和公差,求解组成环的经济合理公 差。 公差分析的方法有极值法和统计公差方法两类,根据分布特性进行封闭环和组成环公差的分析方法称为统计公差法.本文主要 探讨统计公差法在单轴向(One Dimension)尺寸堆叠中的应用。
良机率为1-0.9973=0.0027;在组装完毕后所有零件都有缺陷的机率为:0.0027^3=0.3。这表明几个或者多个零件
公差分析基本知识
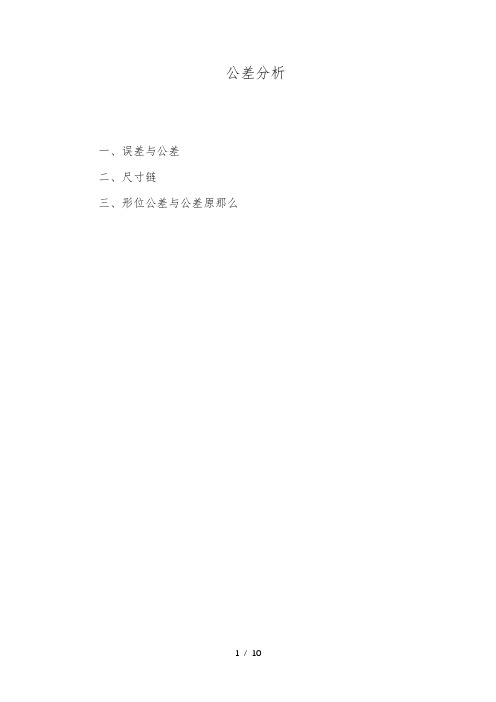
公差分析一、误差与公差二、尺寸链三、形位公差与公差原那么一、误差与公差〔一〕误差与公差的根本概念1. 误差误差——指零件加工后的实际几何参数相对于理想几何参数之差。
〔1〕零件的几何参数误差分为尺寸误差、形状误差、位置误差与外表粗糙度。
尺寸误差——指零件加工后的实际尺寸相对于理想尺寸之差,如直径误差、孔径误差、长度误差。
形状误差〔宏观几何形状误差〕——指零件加工后的实际外表形状相对于理想形状的差值,如孔、轴横截面的理想形状是正圆形,加工后实际形状为椭圆形等。
相对位置误差——指零件加工后的外表、轴线或对称面之间的实际相互位置相对于理想位置的差值,如两个面之间的垂直度,阶梯轴的同轴度等。
外表粗糙度〔微观几何形状误差〕——指零件加工后的外表上留下的较小间距和微笑谷峰所形成的不平度。
2. 公差公差——指零件在设计时规定尺寸变动围,在加工时只要控制零件的误差在公差围,就能保证零件的互换性。
因此,建立各种几何公差标准是实现对零件误差的控制和保证互换性的根底。
〔二〕误差与公差的关系零件误差公差零件误差图1由图1可知,零件误差是公差的子集,误差是相对于单个零件而言的;公差是设计人员规定的零件误差的变动围。
〔三〕公差术语与示例图2以图2为例:根本尺寸——零件设计中,根据性能和工艺要求,通过必要的计算和实验确定的尺寸,又称名义尺寸,图中销轴的直径根本尺寸为Φ20,长度根本尺寸为40。
实际尺寸——实际测量的尺寸。
极限尺寸——允许零件实际尺寸变化的两个极限值。
两个极限值的是最大极限尺寸,小的是最小极限尺寸。
尺寸偏差——某一尺寸〔实际尺寸,极限尺寸〕减去根本尺寸所得到的代数差。
上偏差=最大极限尺寸-根本尺寸,用代号〔ES〕〔孔〕和es〔轴〕下偏差=最小极限尺寸-根本尺寸,用代号〔ES〕〔孔〕和es〔轴〕尺寸公差——允许尺寸的变动量尺寸公差=最大极限尺寸-最小极限尺寸公差带零线——在极限与配合图解中,标准根本尺寸是一条直线,以其为基准确定偏差和公差。
公差分析常用方法
公差分析常用方法
公差分析是一种用于研究产品或系统各种要素之间相互连锁关系的方法。
它可用于确定导致产品或系统性能差异的主要因素,并寻找改进的机会。
下面是一些常用的公差分析方法:
1. 传递函数法:传递函数法是一种将产品或系统的总体公差在各个部件或要素上分配的方法。
通过将总体公差按照一定的比例分配给各个部件,以满足产品或系统性能的需求。
2. 采用最小二乘法(Least Square Method):最小二乘法是一种通过最小化观测值和理论值之间的差异平方和,来确定最接近真实值的方法。
在公差分析中,可以使用最小二乘法来评估产品或系统的总体公差和各个部件之间的关系。
3. 驱动因子公差分析(Driver Factor Analysis):驱动因子公差分析是一种通过识别产品或系统的主要性能驱动因子,来优化公差分配的方法。
通过将更多的公差分配给主要驱动因子,可以显著改善产品或系统的性能。
4. 公差优化:公差优化是一种通过最小化总体公差,以满足产品或系统性能要求的方法。
通过分析各个部件之间的相互关系,可以确定最佳的公差分配方案。
5. 敏感度分析:敏感度分析是一种评估产品或系统对公差变化的敏感程度的方法。
通过分析不同参数的变化对产品或系统性能的影响,可以确定哪些部件或要
素对总体公差的变化最为敏感。
以上是常用的公差分析方法,具体选择哪种方法取决于产品或系统的特点和分析目的。
公差分析基本知识
公差分析一、误差与公差二、尺寸链三、形位公差及公差原则一、误差与公差(一)误差与公差的基本概念1. 误差误差——指零件加工后的实际几何参数相对于理想几何参数之差。
(1)零件的几何参数误差分为尺寸误差、形状误差、位置误差及表面粗糙度。
尺寸误差——指零件加工后的实际尺寸相对于理想尺寸之差,如直径误差、孔径误差、长度误差。
形状误差(宏观几何形状误差)——指零件加工后的实际表面形状相对于理想形状的差值,如孔、轴横截面的理想形状是正圆形,加工后实际形状为椭圆形等。
相对位置误差——指零件加工后的表面、轴线或对称面之间的实际相互位置相对于理想位置的差值,如两个面之间的垂直度,阶梯轴的同轴度等。
表面粗糙度(微观几何形状误差)——指零件加工后的表面上留下的较小间距和微笑谷峰所形成的不平度。
2. 公差公差——指零件在设计时规定尺寸变动范围,在加工时只要控制零件的误差在公差范围内,就能保证零件的互换性。
因此,建立各种几何公差标准是实现对零件误差的控制和保证互换性的基础。
(二)误差与公差的关系由图1(三)公差术语及示例图2以图2为例:基本尺寸——零件设计中,根据性能和工艺要求,通过必要的计算和实验确定的尺寸,又称名义尺寸,图中销轴的直径基本尺寸为Φ20,长度基本尺寸为40。
实际尺寸——实际测量的尺寸。
极限尺寸——允许零件实际尺寸变化的两个极限值。
两个极限值中大的是最大极限尺寸,小的是最小极限尺寸。
尺寸偏差——某一尺寸(实际尺寸,极限尺寸)减去基本尺寸所得到的代数差。
上偏差=最大极限尺寸-基本尺寸,用代号(ES)(孔)和es(轴)下偏差=最小极限尺寸-基本尺寸,用代号(ES)(孔)和es(轴)尺寸公差——允许尺寸的变动量尺寸公差=最大极限尺寸-最小极限尺寸公差带零线——在极限与配合图解中,标准基本尺寸是一条直线,以其为基准确定偏差和公差。
通常,零件沿水平方向绘制,正偏差位于其上,负偏差位于其下,如下图。
图3公差带图解公差带——在公差带图解中,由代表上极限偏差和下极限偏差的两条直线所限定的一个区域。
公差分析
为什么为产生公差?
加工制程的变异: 材料特性的不同 设备或模具的精度 加工条件的不同 操作员的不熟练 模具磨损
DFMA
组装制程的变异: 组装设备的精度 工装夹具的错误
10
二. 公差分析
DFMA
1.公差的概念:
正态分布
一般认为,零件尺寸分布是正态分布
按照某种制造工艺制造如图所示的零件,对于25.40mm零件长度长度尺寸, 从一批零件中任取100件检测,测得它们的实际尺寸如下:
DFMA
3.宽松的零件公差要求
A.设计合理的间隙
设计合理的间隙,防止零件过约束,避免对零件尺寸的不必要的公差要 求,不合理的零件间隙设计会带来对零件不合理的公差要求
合理间隙
零件A 零件B
零件C
20
二. 公差分析
DFMA
B.简化产品装配关系,缩短装配尺寸链
对于重要的装配尺寸,在产品最初设计阶段就要重点加以关注,简化产 品的装配关系,避免重要装配尺寸涉及更多的零件,从而减少尺寸链中 尺寸的数目,达到减少累积公差的目的,产品设计于是能够允许零件宽 松的公差要求
内容:
一.常见的公差分析做法 二.公差分析 三.公差分析的计算步骤 四.公差分析的计算方法 五.公差分析的三大原则 六.产品开发中的公差分析
DFMA
2
一. 常见的公差分析做法
DFMA
1. 产品详细设计完成后,在design review时,针对O-ring的压缩量进行
公差分析;分析如下:
3
一. 常见的公差分析做法
TX = TA2 + TB2 + TC2 + TD2 + TE2
= 0.202 + 0.102 + 0.102 + 0.152 + 0.102
公差分析基本知识
公差分析基本知识公差分析一、误差与公差二、尺寸链三、形位公差及公差原则一、误差与公差(一)误差与公差的基本概念1. 误差误差——指零件加工后的实际几何参数相对于理想几何参数之差。
(1)零件的几何参数误差分为尺寸误差、形状误差、位置误差及表面粗糙度。
尺寸误差——指零件加工后的实际尺寸相对于理想尺寸之差,如直径误差、孔径误差、长度误差。
形状误差(宏观几何形状误差)——指零件加工后的实际表面形状相对于理想形状的差值,如孔、轴横截面的理想形状是正圆形,加工后实际形状为椭圆形等。
相对位置误差——指零件加工后的表面、轴线或对称面之间的实际相互位置相对于理想位置的差值,如两个面之间的垂直度,阶梯轴的同轴度等。
表面粗糙度(微观几何形状误差)——指零件加工后的表面上留下的较小间距和微笑谷峰所形成的不平度。
2. 公差公差——指零件在设计时规定尺寸变动围,在加工时只要控制零件的误差在公差围,就能保证零件的互换性。
因此,建立各种几何公差标准是实现对零件误差的控制和保证互换性的基础。
(二)误差与公差的关系由图1可知,零件误差是公差的子集,误差是相对于单个零件而言的;公差是设计人员规定的零件误差的变动围。
(三)公差术语及示例图2以图2为例:基本尺寸——零件设计中,根据性能和工艺要求,通过必要的计算和实验确定的尺寸,又称名义尺寸,图中销轴的直径基本尺寸为Φ20,长度基本尺寸为40。
实际尺寸——实际测量的尺寸。
极限尺寸——允许零件实际尺寸变化的两个极限值。
两个极限值的是最大极限尺寸,小的是最小极限尺寸。
公差零件误差零件误差图1尺寸偏差——某一尺寸(实际尺寸,极限尺寸)减去基本尺寸所得到的代数差。
上偏差=最大极限尺寸-基本尺寸,用代号(ES)(孔)和es(轴)下偏差=最小极限尺寸-基本尺寸,用代号(ES)(孔)和es(轴)尺寸公差——允许尺寸的变动量尺寸公差=最大极限尺寸-最小极限尺寸公差带零线——在极限与配合图解中,标准基本尺寸是一条直线,以其为基准确定偏差和公差。
- 1、下载文档前请自行甄别文档内容的完整性,平台不提供额外的编辑、内容补充、找答案等附加服务。
- 2、"仅部分预览"的文档,不可在线预览部分如存在完整性等问题,可反馈申请退款(可完整预览的文档不适用该条件!)。
- 3、如文档侵犯您的权益,请联系客服反馈,我们会尽快为您处理(人工客服工作时间:9:00-18:30)。
求尺寸链上各尺寸的基本尺寸及极限偏差
用于设计时的公差分配
A)等公差法 B)等精度法
缺点:易产生过于保守的设计 导致制造成本提高
B.统计公差分析(大数分析法)
1..正态分布
标准差
σ=
Σ(Xi- X0 )2 n
-3σ 3σ
样本标准差
σn -1=
Σ(Xi- X)2 n-1
± σ ± 2σ ± 3σ ± 4σ
小 结:
1.如果想得到合理的零件工差分布,就必需了解其实际的制程能力.须靠平时对工 艺知识的不断累积 2.在满足产品功能的前提下.公差的极限应尽可能的宽 以免造成不必要的浪费.高昂的 制造成本!
则有:
2 2 T0=1/K0 Σ§ iKi Ti
K0,Ki :相对分布系数 § I :传递系数
关于公差分析及其他
1熟悉各种零件的加工工艺水平即制程能力.是成功设定 公差的关键
2.目前的CAD技术无法完全取代公差分析
Rear Socket for CardBus G2
HOUSING CONTACT
* 3.产品开发设计的需要 产品设计一般分为 原形设计 和 二次生产设计 不进行公差分析意味着将在制造时冒很大的风险
二 公差分析的作用及分类
1设计时利用公差分析可合理分配各零件的公差.达到可制造 性的要求. 2.制造时可用以校核公差组合可否满足产品功能要求 3.降低制造成本
针对不同的状况 使用不同的公差分析方法
P=0.682 P=0.9544 P=0.9973 P=0.99936
理论依据:
1.大部分零件在其公差限制范围内.呈正态概率分布 2. 如果两个或有限多個随机变量均呈正态分布.且互相独立 (不相關)那么它们之间相互迭加的结果也呈正态分布
即:
T0=σ0= σ12+σ22+σ32+...+σn2
对于呈非正态分布之零件组合
SHIELDING SHELL
共面度须在 0.10mm范围以ING SHELL
CONTACT
对产品平面度影响之相关零件尺寸
HOUSING : DIM 0.30± 0.10 DIM 2.60+0.05/-0.00 SHIELDING: DIM 3.35± 0.05 SHELL DIM 0.00+0.05/-0.00
公差分析简介及实例
报告大纲:
1.使用公差分析的必要性 2.公差分析作用 3.公差分析的分类及用法 4.REAR SOCKET平面度公差分析(例) 5.结束
一 使用公差分析的原因及必要性
* 1工业化时代的需要 国际化的制造业趨勢.生产技术的专业化 公司企业有时需在别的国家或地区寻求合理伙伴 * 2市场竟争的需要 交期.品质.成本…...
=0.00+0.25/-0.35mm
使用统计分析进行的公差分析
1.以相关各尺寸之设计中心值作为平均值X 2.以相关各尺寸之设计公差范围作为其对应标准偏差6σ 3.依公式进行计算 分别得出配合后共面度中心值及其偏差范围 计算得: X = (0.30+2.625)+(0.45+0.05)-(3.35+0.025)=0.05mm 3σ= 0.102+0.0252+0.052+0.0252+0.052+0.052 =0.136mm 合计: 共面度=0.05± 0.136mm (0.186~-0.086) 查表得: Z1 =3*(0.10-0.05)/0.136=1.103
P=0.00048+(1-0.86433)=13.6%
实际制程能力统计分析
0.10 2.60+0.05/-0.000.30± MAX MIN X σn-1 2.631 2.619 2.625 0.326 0.05 0.00+0.05/-0.00 0.45± 0.05 0.00+0.10/-0.00 3.35± 0.476 0.470 0.250 0.474 0.298 0.0252* 0.012 3.3481 0.029 0.014 0.009 3.36 3.34 0.038 0.021
分类:
极端情况公差分析V.S.统计分析 (完全互换法) (大数互换法)
A极端情况公差分析
即在建立好的一條尺寸链上 保証各环(尺寸)公差均向一个 方向上累积.也仍然滿足封闭環的装配性及功能要求
方法分类:
a.正计算: 已知尺寸链上各尺寸的基本尺寸及极限偏差 求封闭环的尺寸及极限偏差用于校核功能性 b.反计算: 已知封闭环尺寸的基本尺寸及极限偏差
0.0017 0.0013 0.00548 0.00385
0.003
X0=(2.625+0.298)+(0.474+0.012)-(3.3481+0.029)=0.0319 3σ=3 0.0032+0.02522+0.00172+0.00132+0.005482+0.003852 =0.0756 Z=(0.10-0.0319)/0.0252=2.702 查表得:P1=0.34%
CONTACT: DIM 0.45± 0.05 DIM 0.00+0.10/-0.00
使用极端情况进行的 一般公差分析
共面度: =HOUSING高+CONTACT高-SHELL高 =[(0.30± 0.10)+(2.60+0.05/-0.00)] +[(3.35± 0.05)+(0.00+0.05/-0.00)] -[(0.45± 0.05)+(0.00+0.10/-0.00)]