风扇叶模具设计
风扇叶片注塑模CAD/CAM/CAE一体化技术的应用

零 件壁 厚 05 mm
然 而 采 用 CAD CAM/ / CAE 体 化 技 术 流 程 , - 始 终 以 塑料 件 的 3 模 型 为 中心 ,模 具 设 计 、CAE D
警
幽 1
模拟分析 、模具CNCJI ,以及模具C J I MM ( 三坐
标 )检 测 、塑 料 件 C M检 测 都 完 全 基 于 这 些 塑 料 M 件3 D模 型 的 传 递 ,从 而 消 除 了 二 维 图传 递 几 何 信 息 的不 准 确 性 ,使最 终 生 产 的 塑料 件 和 设计 者 的意 图 保持 高 度 一 致 。还 使 得 整 个生 产 流 程 易 于 实现 自 动化 生 产 ,从 而 大幅 度 降 低 了技 术 工 人 的 工作 量 ,
本
图2 注 塑模生产流程
参磊
冷工 加
榭
6 1
拦旦圭挠i 誊玲
齿轮磨削加工快换夹具的广泛应用
德 国柯尼 格有 限公 司 费 永新
对 于 现 代 化 的 机 床 来 说 ,加 工 任 务 变 得 越 来 越 复 杂 ,加 工的 产 品 也 变得 越 来 越 多样 化 , 因此 相
d
风扇叶片注塑模C D C M C E A /A /A 体化技术的应用
一
湖北省 十堰市 技师学 院 (4 0 0 何 4 20 )
军
冯方根
赵道 明
李
图 1 示 为 一 电 风 扇 图形 ,零 件 厚 度 05 所 . mm, 材料 AB ,年产 1万 件 。需 对 其 进行 注 塑 模具 设 计 S 5
性运行的前提条件 。
I 问题 的提 出 .
有 别于 大 规 模 的 汽车 齿 轮 加 工 ,我 们所 面 对 的 越 来越 多 的 齿 轮加 工 厂 ,都是 针 对 不 同 行业 所 需 而 生 产相 应 规 格 的 齿轮 , 因此 势 必要 求 生 产 厂 家必 须 面 临一 个 小 批 量 ,多 品种加 工 的现 实 问题 ,如 果 加 工 主 要 是 依 靠 一些 高 效 率 的进 口磨 齿 机 床 的话 ,在 保 证 加 工 高 质 高效 的 前 提 下 ,厂 家 就 必 须要 在 工 装 ( )CAD 数 化 技 术 便 于 建 立 基 于 注 塑 模 具 5 参 的统 一 数 据 库 ,提 供 了模 具 开 发平 台 。 ( )利 用CA 6 M软 件 进 行C 高 速加 工技 术 , NC 与传 统 放 电加 工相 比 ,省 去 电极 制 造 一 环 ,缩 短 了 模 具 加 工 周期 ,提 高模 具 加 工精 度 。
下面首先介绍电脑风扇上壳模具设计,其三维模型图如图1-1 …
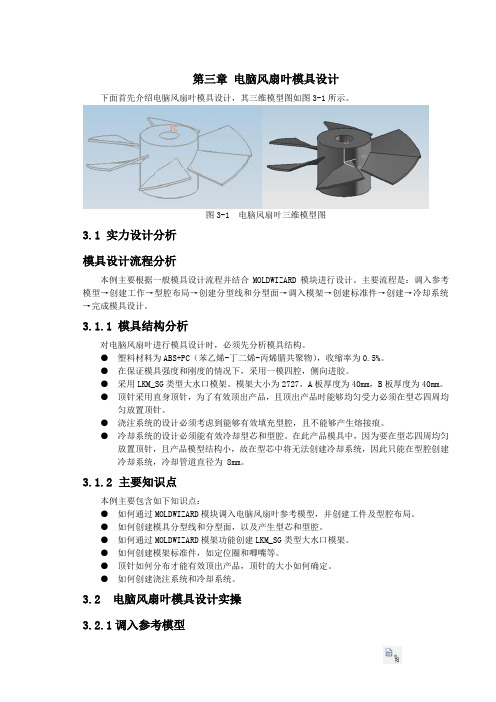
第三章电脑风扇叶模具设计下面首先介绍电脑风扇叶模具设计,其三维模型图如图3-1所示。
图3-1 电脑风扇叶三维模型图3.1 实力设计分析模具设计流程分析本例主要根据一般模具设计流程并结合MOLDWIZARD模块进行设计。
主要流程是:调入参考模型→创建工作→型腔布局→创建分型线和分型面→调入模架→创建标准件→创建→冷却系统→完成模具设计。
3.1.1 模具结构分析对电脑风扇叶进行模具设计时,必须先分析模具结构。
●塑料材料为ABS+PC(苯乙烯-丁二烯-丙烯腈共聚物),收缩率为0.5%。
●在保证模具强度和刚度的情况下,采用一模四腔,侧向进胶。
●采用LKM_SG类型大水口模架。
模架大小为2727,A板厚度为40mm,B板厚度为40mm。
●顶针采用直身顶针,为了有效顶出产品,且顶出产品时能够均匀受力必须在型芯四周均匀放置顶针。
●浇注系统的设计必须考虑到能够有效填充型腔,且不能够产生熔接痕。
●冷却系统的设计必须能有效冷却型芯和型腔。
在此产品模具中,因为要在型芯四周均匀放置顶针,且产品模型结构小,故在型芯中将无法创建冷却系统,因此只能在型腔创建冷却系统,冷却管道直径为 8mm。
3.1.2主要知识点本例主要包含如下知识点:●如何通过MOLDWIZARD模块调入电脑风扇叶参考模型,并创建工件及型腔布局。
●如何创建模具分型线和分型面,以及产生型芯和型腔。
●如何通过MOLDWIZARD模架功能创建LKM_SG类型大水口模架。
●如何创建模架标准件,如定位圈和唧嘴等。
●顶针如何分布才能有效顶出产品,顶针的大小如何确定。
●如何创建浇注系统和冷却系统。
3.2电脑风扇叶模具设计实操3.2.1调入参考模型(1)调入参考模型。
在【注塑模向导】工具条中单击【项目初始化】按钮,弹出【打开部件文件】对话框,然后根据图3-2所示操作过程进行操作。
图3-2【调入参考向导】操作过程(2)系统经过自动计算并调入参考模型,如图3-3所示。
图3-3 调入参考模型(3)接下来我们就来看看这套模具在GUS里的具体具体做法。
solidworks案例教程《风扇叶片建模》
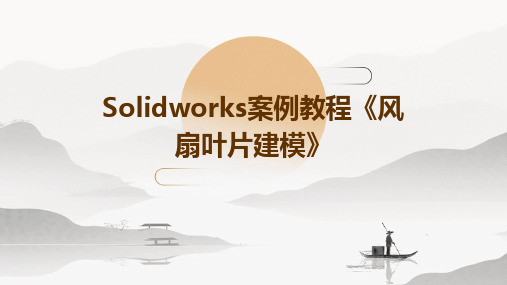
目录
• 引言 • Solidworks基础操作 • 风扇叶片设计理念 • 风扇叶片建模过程 • 风扇叶片后处理与优化 • 课程总结与展望
01
引言
课程背景
风扇叶片作为机械设备中的重要组成部分,其设计质量和加工精度直接影响设备 的性能和安全性。
随着计算机技术的发展,CAD(计算机辅助设计)软件在机械设计领域得到了广泛 应用,其中SolidWorks是一款功能强大、易学易用的CAD软件,广泛应用于各种机 械设计领域。
06
课程总结与展望
本课程学习重点回顾
风扇叶片设计原理
Solidworks基本操作
理解风扇叶片的工作原理和设计要求,以 便更好地进行建模。
掌握Solidworks的基本操作,如草图绘制 、特征创建、装配体设计等。
参数化设计
优化设计
学习如何使用Solidworks的参数化设计功 能,提高设计效率和准确性。
倒角
在实体的边角上添 加倒角,使实体更 加坚固。
实例操作:简单零件建模
打开Solidworks软件, 新建一个零件文件。
执行拉伸命令,将矩 形拉伸成一个长方体。
在草图绘制模式下, 绘制一个矩形,作为 拉伸特征的基础。
实例操作:简单零件建模
在长方体的顶部绘制一个圆形 草图,作为旋转特征的基础。
执行旋转命令,将圆形草图旋 转成一个圆柱体。
提供常用命令的快速访 问按钮,方便用户操作。
显示当前零件的结构和 特征,方便用户进行编
辑和修改。
绘图区域
用于显示和编辑零件的 三维模型。
基础命令介绍
拉伸
将草图沿着一个方 向拉伸,形成三维 实体。
风扇叶片三维模型的绘制思路。
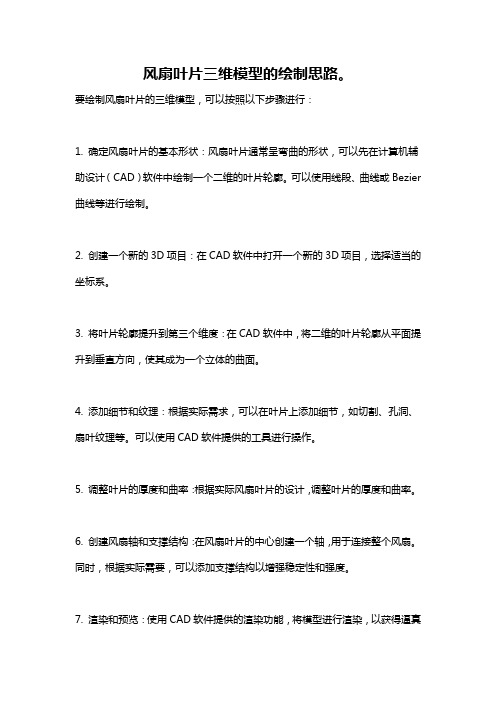
风扇叶片三维模型的绘制思路。
要绘制风扇叶片的三维模型,可以按照以下步骤进行:
1. 确定风扇叶片的基本形状:风扇叶片通常呈弯曲的形状,可以先在计算机辅助设计(CAD)软件中绘制一个二维的叶片轮廓。
可以使用线段、曲线或Bezier 曲线等进行绘制。
2. 创建一个新的3D项目:在CAD软件中打开一个新的3D项目,选择适当的坐标系。
3. 将叶片轮廓提升到第三个维度:在CAD软件中,将二维的叶片轮廓从平面提升到垂直方向,使其成为一个立体的曲面。
4. 添加细节和纹理:根据实际需求,可以在叶片上添加细节,如切割、孔洞、扇叶纹理等。
可以使用CAD软件提供的工具进行操作。
5. 调整叶片的厚度和曲率:根据实际风扇叶片的设计,调整叶片的厚度和曲率。
6. 创建风扇轴和支撑结构:在风扇叶片的中心创建一个轴,用于连接整个风扇。
同时,根据实际需要,可以添加支撑结构以增强稳定性和强度。
7. 渲染和预览:使用CAD软件提供的渲染功能,将模型进行渲染,以获得逼真
的效果。
可以调整光照、材质和背景等参数。
可以预览和检查模型是否符合预期。
8. 导出模型:完成风扇叶片的绘制后,将其导出为常见的3D文件格式,如.STL、.OBJ等,以便在其他软件中使用或进行进一步的处理和制造。
以上是风扇叶片三维模型的绘制思路,具体操作过程可以根据所使用的CAD软件进行调整和优化。
电风扇叶片塑料模具设计说明

第1章注射模可行性分析1.1注射模设计的特点塑料注射模塑能一次性地成型形状复杂、尺寸精确或嵌件的塑料制品。
在注射模设计时。
必须充分注意以下三个特点:(1)塑料熔体大多属于假塑料液体,能剪切变稀。
它的流动性依赖于物料品种、剪切速率、温度和压力。
因此须按其流变特性来设计浇注系统,并校验型腔压力及锁模力。
(2)视注射模为承受很高型腔压力的耐压容器。
应在正确估算模具型腔压力的基础上,进行模具的结构设计。
为保证模具的闭合、成型、开模、脱模和侧抽芯的可靠进行,模具零件和塑件的刚度与强度等力学问题必须充分考虑。
1.2注射模组成凡是注射模,均可分为动模和定模两大部件。
注射充模时动模和定模闭合,构成型腔和浇注系统;开模时定模和动模分离,取出制件。
定模安装在注射机的固定板上,动模则安装在注射机的移动模板上。
根据模具上各个零件的不同功能,可由一下个系统或机构组成。
(1)成型零件指构成型腔,直接与熔体相接触并成型塑料制件的零件。
通常有凸模、型芯、成型杆、凹模、成型环、镶件等零件。
在动模和动模闭合后,成型零件确定了塑件的内部和外部轮廓尺寸。
(2)浇注系统将塑料熔体由注射机喷嘴引向型腔的流道称为浇注系统,由主流道、分流道、浇口和冷料井组成。
(3)导向与定位机构为确保动模与定模闭合时,能准确导向和定位对中,通常分别在动模和定模上设置导柱和导套。
深腔注射模还须在主分型面上设置锥面定位,有时为保证脱模机构的准确运动和复位,也设置导向零件。
(4)脱模机构是指模具开模过程的后期,将塑件从模具中脱出的机构。
(5)侧向分型抽芯机构带有侧凹或侧孔的塑件,在被脱出模具之间,必须先进行侧向分型或拔出侧向凸模或抽出侧型芯。
1.3塑料风叶设计与分析风叶是利用一定空间曲面的叶片,通过主体的高速旋转产生风能。
以前,大都是采用金属片材,经过模压制成风叶片。
然后与风叶主体固定安装成风叶。
由于模压叶片和装配等方面的原因,往往风叶的静、动平衡难以达到设计要求。
电风扇叶注塑模设计

4 电风扇叶注塑模设计4.1 注塑模设计的基本流程传统方法的注塑模设计是在二维环境下进行,从图4.1中可以看出,传统的模具制造工艺路线只是典型的串行流程,任何其中一部分没有完成都会影响下面的工作,相互之间的制约性太大,这样的结果就是生产周期的延长,人工进行的工作量非常大,而且做工粗糙、精度不高,在CAD/CAM技术高速发展的今天,传统方法终将被取而代之。
基于UG 的注塑模具的设计是在三维环境下进行的,这用方法的采用不仅提高了生成型芯和型腔零件的速度和准确度还可以进行造型设计,还能完成模具的总装配,大大缩短了模具设计周期并及时发现模具设计中的错误,有效地避免工人重复劳动[16]。
图4.1传统方式的注塑模具设计过程图4.2 基于UG的注塑模设计工程4.2 注塑模具的基本结构设计4.2.1 扇叶材料的分析风扇为人们日常生活常用品,需大批量生产,又与人们紧密接触,所以扇叶的材料必须无毒无害,同时考虑没有很高的强度要求,收缩率方面也无特殊要求,故选择ABS材料进行注塑生产。
ABS具有良好的成型加工型,制品表面光洁度高,且具有良好的涂装性和染色性,可电镀成多种光泽[17]。
塑料ABS具有以下性能:(1)冲击强度极好,耐磨性优良,尺寸的稳定性好。
(2)从热学性能上来看热变形温度为85℃左右,制品经退火处理以后还可提高10℃左右。
在-40℃时仍能表现出一定的韧性,可在-40℃到85℃的温度范围内长期使用。
(3)ABS的电绝缘性较好,并且几乎不受温度、湿度和频率的影响。
(4)ABS流动性好,易溢料,具有优良的化学稳定性、不吸水,是易成型加工的材料可用于注塑。
4.2.2 分型面的选择分型面是指上、下两模芯互相接触的表面,而分型面的设计在电风扇叶的注塑模设计中是非常重要的。
分型面一般是在确定浇注位置或被称为进料口的位置后再选择。
但在分析各种分型面方案的优缺点之后,也有可能需要重新调整浇注位置。
分型面选择原则有两个,首先要考虑到是塑件在开模时尽可能留在动模部分,同时由于塑件有曲面扇叶,所以也要尽可能留在动模部分。
风扇叶片及其模具快速反求设计和制造

1 测量数据 的获取
1 1 测量 装置 ,
采用 英 国的 3 C D S ANNE S高速激 光三 维扫描 系统 .该系 统包 括 R vra激 光扫 描头 、 pi R e es Re l a独 c
立扫 描 台 、 S AN 操 作软件 三个主要 部分 .各 部分 的主要 功能是 : RIC
的档 案 , 配台反 向工 程软 件( S r cr或一 般 C 如 uf e) a AD/ AM 系统( UG I, r. C 如 PoE或 C ADD 5等 ) 便 S , 可直接 应用 于产 品设计开 发 、模具制 造 、 快速 原 形 、广告 动画及 医学等 用途 .
该扫 描 头 的扫 描宽度 2 5mm, 距长 ( 1 0mm, 焦 z) 0 重复 精度 ( 5 I , z) 0 n
精 度 ( ± 2 u 解 析 度 1 u ,轴 最 小 点 距 6 m,高 精 度 扫 描 速 度 z) 0. m, 0. n r 0p 1 0 / , 0 0点 s 激光 束宽 6 m,外形 : 9 5 0g 18mm×8 2mm×7 0mm.
I } 2 R pi / 0 0S RVO 独立扫 描 台 . . e l a 1 0 E c
实践证 明 , 该方 法是一种切实 可行 的质量高 、精度高 、
关键词 : 反求 工程 ;激光襁 量 ; 『 三维重掏 模具
中图分类号 : T 3 I 5 P 1 .2
文献标识工 程 ( e es n ier g 是 根 据 现有 实物 模 型 的 测量 数 据 演绎 出零 件 的设 计 概 念 和 C R v reE gn ei ) n AD
摘
要 : 目的
根据某汽车冷却风扇叶片实物快 速实现该叶 片及其模具 的设 计制造.方法
风扇叶片模具设计论文
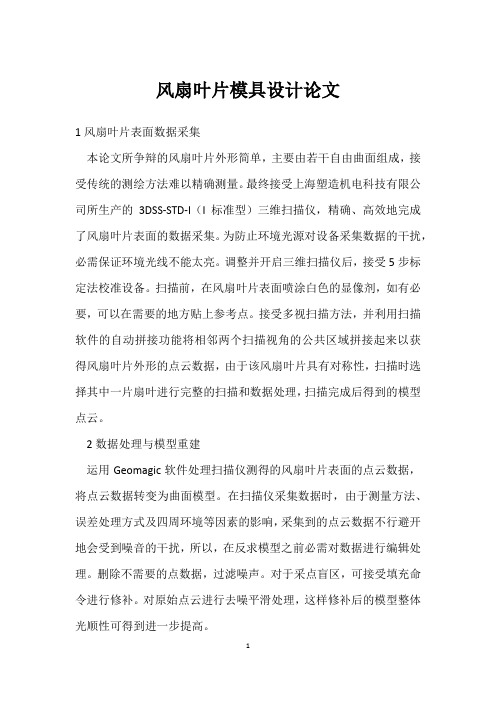
风扇叶片模具设计论文1风扇叶片表面数据采集本论文所争辩的风扇叶片外形简单,主要由若干自由曲面组成,接受传统的测绘方法难以精确测量。
最终接受上海塑造机电科技有限公司所生产的3DSS-STD-I(I标准型)三维扫描仪,精确、高效地完成了风扇叶片表面的数据采集。
为防止环境光源对设备采集数据的干扰,必需保证环境光线不能太亮。
调整并开启三维扫描仪后,接受5步标定法校准设备。
扫描前,在风扇叶片表面喷涂白色的显像剂,如有必要,可以在需要的地方贴上参考点。
接受多视扫描方法,并利用扫描软件的自动拼接功能将相邻两个扫描视角的公共区域拼接起来以获得风扇叶片外形的点云数据,由于该风扇叶片具有对称性,扫描时选择其中一片扇叶进行完整的扫描和数据处理,扫描完成后得到的模型点云。
2数据处理与模型重建运用Geomagic软件处理扫描仪测得的风扇叶片表面的点云数据,将点云数据转变为曲面模型。
在扫描仪采集数据时,由于测量方法、误差处理方式及四周环境等因素的影响,采集到的点云数据不行避开地会受到噪音的干扰,所以,在反求模型之前必需对数据进行编辑处理。
删除不需要的点数据,过滤噪声。
对于采点盲区,可接受填充命令进行修补。
对原始点云进行去噪平滑处理,这样修补后的模型整体光顺性可得到进一步提高。
3风扇叶片注塑模具设计在逆向工程的基础上,在UG注塑模具设计(MoldWizard)模块中,对该风扇叶片进行了注塑模设计。
模具设计的基本流程如下:导入制件三维实体模型;对设计项目进行初始化,加载实体模型,确定材料及收缩率;分析实体模型出模斜度及分型状况;确定模具的分型面、型腔布局、推杆、浇口和冷却系统等;修补开方面,定义分型面;生成型芯、型腔等工作部件;加入标准模架、推杆、滑块等部件;设计浇注系统、冷却系统;完善设计图纸等。
依据该塑件外观质量及尺寸精度要求,选用模具为一模一腔单分型面模具。
结合分型面的选择原则,选取单分型面垂直分型。
避开了顶杆端部与叶片的接触,保证产品外观的完整性。
- 1、下载文档前请自行甄别文档内容的完整性,平台不提供额外的编辑、内容补充、找答案等附加服务。
- 2、"仅部分预览"的文档,不可在线预览部分如存在完整性等问题,可反馈申请退款(可完整预览的文档不适用该条件!)。
- 3、如文档侵犯您的权益,请联系客服反馈,我们会尽快为您处理(人工客服工作时间:9:00-18:30)。
11.7.1 创建定模部分冷却管道
• 定模部分冷却管道主要由型腔冷却管道和定模板 冷却管道构成。 • 1. 型腔冷却管道设计 • 2. 定模板冷却管道设计
11.7.2 创建动模部分冷却管道
• 动模部分冷却管道也由型芯冷却管道动模板冷却 管道构成。 • 1. 型芯冷却管道设计 • 2. 创建动模板上的冷却管道
• 由于“模架管理”对话框无模架的平移变换功能, 所以只能调整模腔。调整模腔过程包括模具坐标 系的重定义和工件的参数编辑。操作步骤如下:
11.4.3 创建空腔
• 模架加载后,为了便于后续的设计,需先创建出 模腔在动、定模板上的空腔。操作步骤如下:
11.5 创建浇注系统
• 风扇叶模具的浇注系统组件包括主流道、分流道 和浇口。但由于模具采用的是单点浇口进料,因 此不设分流道。
• 使用“注塑模向导”工具条上的“腔体”工具在 模具定模部分中创建出浇注系统组件的空腔。
11.6 创建顶出系统
• 本例产品无内、外侧凹或侧孔特征,所以顶出系 统的创建仅仅是加载并修剪顶杆。
11.6.1 加载顶杆
• 为使制件能平稳地推出,顶杆的分布应尽量均匀。 加载顶杆的操作步骤如下:
11.6.2 修剪顶杆
11.1 设计任务
• • • • • • • • • 本章注塑模具设计实例产品为风扇叶,如图11-1所示。 产品规格:350mm×335mm×51mm。 产品壁厚:最大3mm,最小2mm。 产品设计、生产任务: 材料为ABS+PC; 产品收缩率为0.0045; 单腔模布局; 产量15000个/年; 产品外部表面光滑,无明显制件缺陷,如翘曲、缩痕、凹坑等;
11.4 加载模架
• 由于产品并无复杂的侧凹、侧孔、倒扣等复杂特 征,因此,模架结构可采用简单的二板模,即不 要支承板、卸料板。
11.4.1 加载模架
• 通常,模架的选用是根据具有国家标准的龙记模 架系列来确定的。鉴于本章产品模型较大,所以 选用的是龙记大水口模架。操作步骤如下:
11.4.2 调整模腔
11.2 初始化项目
• 初始化项目过程是MoldWizard克隆模具装配体结 构的复制过程。在NX6.0中,产品的初始化项目过 程包括加载产品和初始化项目。
11.2.1 加载产品
• 在产品模型进ቤተ መጻሕፍቲ ባይዱ初始化项目时,NX6.0与旧版本有所区别的是,必须在打 开的模型文件中显示实体模型。因此,产品的加载是初始化项目过程中不 可缺少的重要步骤。其操作步骤如下: (1)启动UG NX6.0,进入基本环境界面中。 (2)在“标准”工具条上执行“开始>所有应用模块>建模”命令,载 入建模模块,接着调入“特征”工具条、“曲面”工具条、“曲线”工具 条等。 (3)在“标准”工具条上执行“开始>所有应用模块>注塑模向导”命 令,载入MoldWizard模块。 (4)单击“标准”工具条上的“打开”按钮,弹出“打开”对话框。进 入随书光盘中打开Example\ch11\fox.prt产品模型文件,如图11-2所示。
第11章 风扇叶模具设计
• 本章将以塑胶制品—风扇叶为例,将塑料注塑模 具的整个设计流程作详细的介绍,其中包括有产 品设计任务、项目初始化、分模设计、模架加载、 浇注系统设计、顶出系统设计和冷却系统设计。 • 通过本章的风扇叶注塑模设计实例,能使读者对 前面所学内容有更充分的理解和掌握。下面将风 扇叶注塑模设计的整个设计流程介绍如下。 • 随书光盘\Example\ch11\fox.prt。 • 随书光盘 \Example\ch11\fox_mold\fox_top_009.prt。 • 随书光盘\Flash\ch11\fox_mold.avi。
• •
• •
11.2.2 初始化项目
• 产品模型加载后,即可执行初始化项目进程操作,在此进程中可进行项目 路径的更改、项目的重命名、产品材料的选择以及项目单位的设置等操作。 操作步骤如下: (1)在“注塑模向导”工具条上单击“初始化项目”按钮,弹出“初始 化项目”对话框。 (2)在对话框的“材料”下拉列表中选择“ABS+PC”,保留对话框中其 他默认设置,单击“确定”按钮进入初始化项目进程,如图11-3所示。 (3)经过一段时间的初始化项目过程后,完成了模具总装配体的克隆装 配,在装配导航器中可看见模具总装配体结构,如图11-4所示。
11.3.4 抽取区域面及自动补孔
• 产品的MPV模型验证完成后,接着就可以抽取型芯、型腔区 域面和自动修补模型的破孔了。 • 1. 抽取型芯、型腔区域面 • 2. 自动修补破孔
11.3.5 创建型腔和型芯
• • • 虽然前面创建了主分型面,但它并不是MW默认的分型面,因此还 要进行MW分型面的创建,然后才能自动分割出型腔和型芯。 1. 创建MW默认的分型面 2. 创建型腔和型芯
11.3.2 MPV模型验证
• MPV模型验证是MW自动分模设计必须经过的一个过 程。否则,后续的分模设计将无法进行,操作步 骤如下:
11.3.3 主分型面设计
• • • • • • • • 风扇叶的主分型面最好作成碰穿形式,可进行模具精确定位,并有助于减 少开模动作部件之间的摩擦。 1. 创建条带曲面 2. 创建拉伸曲面 3. 拉伸曲面拔模处理 4. 创建延伸曲面 5. 创建另外两片风扇叶的碰穿面 6. 完成主分型面的创建 7. 完成MPV模型验证
11.5.1 创建主流道
• 模具的主流道主要为标准件浇口衬套,同时加载 用于定位注射机机嘴的定位环标准件。 • 1. 加载定位环 • 2. 加载浇口衬套
11.5.2 创建浇口
• 单腔模的浇口多数情况下采用单点浇口或潜浇口, 本例模具采用单点浇口形式。其操作步骤如下:
11.5.3 创建流道与浇口空腔
• 顶杆标准件加载以后,需要将其修剪成型芯部件 上的一部分形状,使产品内部保持原有形状。操 作步骤如下:
11.6.3 创建顶杆的空腔
• 使用“注塑模向导”工具条上的“腔体”工具, 选择型芯、动模板和推件固定板作为目标体,选 择所有的顶杆作为工具体,创建出顶杆的空腔。
11.7 创建冷却系统
• 本例注塑模具的冷却系统分别创建在模具的定模 部分和动模部分。
11.7.3 创建冷却管道空腔
• • 在创建冷却管道空腔时,应先创建出型腔和型芯(已创建)上的 空腔,然后才能创建动、定模板上的冷却管道空腔。 使用“注塑模向导”工具条上的“腔体”工具在模具定模部分创 建的空腔如图11-104所示。在模具动模部分创建的空腔如图11105所示。
• • •
11.3 分模设计
• 产品的分模设计过程包括模具设计准备过程、MPV 模型验证、主分型面设计、抽取区域和自动补孔、 创建型芯与型腔5个设计过程。
11.3.1 模具设计准备过程
• • • • 模具设计准备过程是完成模具设计的前期阶段,同时也是极为重要的设计阶段。 模具设计准备过程包括模具坐标系的设置、创建自动工件和模腔布局。 由于本章风扇叶模具为单模腔设计,也就不再进行模腔布局设计了。 1. 设置模具坐标系 2. 创建自动工件