管壳式换热器的工艺设计
孙兰义教授新作《换热器工艺设计》第3章 管壳式换热器ppt

特性
适用范围
ϕ25×2.5
325~1Байду номын сангаас00
2,4
3,6
ϕ19×2 ϕ25×2.5
△
浮头 式
GB/T 28712.1 —2012
325~1900
2,4, 3, 4.5, 6, ϕ19×2 6 9
◇
ϕ25×2.5
3.1 管壳式换热器的特点
管壳式换热器的主要组合部件
TEMA标准中规定的管壳式换热器的主要组合
图3-3 GB/T 151-1999 管壳式 换热器中的主要部件和部件代号图
⑤ F型壳体用于需要多壳体的工况,它可起到两台或多 台串联换热器的作用,并允许换热器温度交叉的出现。
3.1 管壳式换热器的特点
前端管箱和后端管箱
前端管箱有封头管箱和平盖管箱两种基本型式。封头管箱(B)最常用,一 般是在管侧流体较清洁的情况下使用。平盖管箱可以是可拆式(A)也可以与 管板做成一个整体(C)。对于水冷却器,当管侧需要定期清洗且管侧设计压 力小于1 MPa时,前封头可选A型,对于高压换热器前封头宜选择D型。各管箱 详细介绍见书p6~p7。 可参考的一般选型指导:
(a)竖缺形折流板
(b)横缺形折流板
图3-11 折流板缺口方向
3.2 管壳式换热器结构参数选择
折流板换热器间隙 折流板管孔与管壁之间的间隙 根据TEMA标准,对于未受支承的管子的最大长度为36 in(914.4 mm)
或更小,或者对于外径大于1.25 in(31.8 mm)的管子,该孔隙为1/32 in (0.80 mm);对于未受支承的长度超过36 in,外径为1.25 in或更小的 管子,该孔隙为1/62 in(0.40 mm)。
管壳式换热器的分类及工艺设计应用概述

中 图分类 号 : T Q 0 5 1 . 5
文 献标 志码 : C
文章 编号 : 1 0 0 8 — 1 2 6 7 ( 2 0 1 3 ) 0 4 — 0 0 6 0 — 0 3
( 2 ) 管、 壳程温差不大 , 压力 较高的工况 ; ( 3 ) 壳程 1 管 壳式 换热器 的主 要结构 型 式及使 用 条 况 ; 介 质干净 ; 或虽 会结 垢 , 但 通过 化学 清洗能 去除 的工 件
该换热器的特点是结构简单 、 紧凑、 没有壳程密
封的问题 , 而且往往是管板兼做法兰。
其适用于 : ( 1 ) 管、 壳程温差较大 , 压力不高的工
¨
收 稿 日期 : 2 0 1 2 — 1 1 -1 2
-
一 一
+
- - - + 一- +
一 — — 一 - - + 一 - — - ● 一一 十 一 — + 一 - — — 一 +
1 . 1 管壳 式换热 器 的分类
况; f 4 ) 布管 多 , 锻 件少 , 一次性 投 资低 的工况 。
常见 的管壳 式换 热器 ( 以下 简称 换热 器 )主要 有: ( 1 ) 固定管 板 式换 热器 ; ( 2 ) 浮 头式换 热 器 ; ( 3 ) u形 管式 换热 器 ; ( 4 ) 釜式重沸 器 ; ( 5 ) 填料 函式换 热器 。
差 的情况 。
4 . 3 采取 不 同地基
4 地下室不均匀沉降
解决不均匀沉降问题大致有以下几种方法 。
4 . 1 沉 降 缝
在设计 中不设沉降缝 ,而采取一定 的措施 , 调
整 地 基反 力 ,尽 量减 少不 同部分 的 地基 反 力差 , 从 而减少 沉降差 。 这 是所谓 “ 调” 的方 法 。 如: 裙 房部 分 采 用 天然 地基 , 主楼 部分 采用 复 合地 基 或 桩基 。裙 房 和 主楼 部分 采 用不 同的基 础形 式 , 主楼 采用 筏 基 或 箱基 , 裙房 采用 独立基 础或 条形基 础 。
管壳式换热器的设计
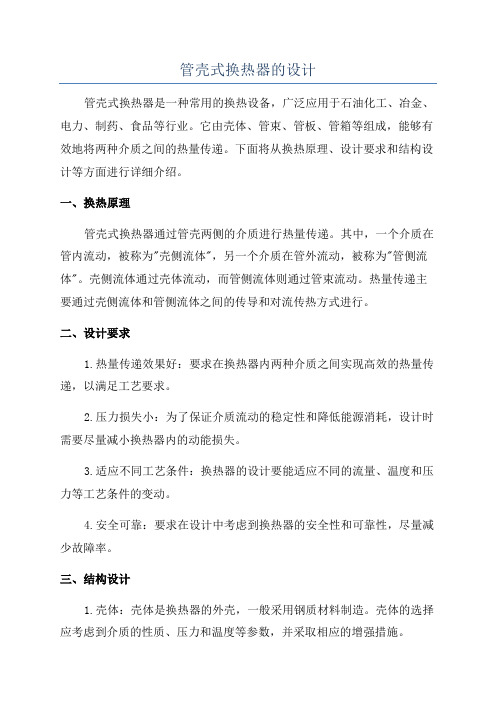
管壳式换热器的设计管壳式换热器是一种常用的换热设备,广泛应用于石油化工、冶金、电力、制药、食品等行业。
它由壳体、管束、管板、管箱等组成,能够有效地将两种介质之间的热量传递。
下面将从换热原理、设计要求和结构设计等方面进行详细介绍。
一、换热原理管壳式换热器通过管壳两侧的介质进行热量传递。
其中,一个介质在管内流动,被称为"壳侧流体",另一个介质在管外流动,被称为"管侧流体"。
壳侧流体通过壳体流动,而管侧流体则通过管束流动。
热量传递主要通过壳侧流体和管侧流体之间的传导和对流传热方式进行。
二、设计要求1.热量传递效果好:要求在换热器内两种介质之间实现高效的热量传递,以满足工艺要求。
2.压力损失小:为了保证介质流动的稳定性和降低能源消耗,设计时需要尽量减小换热器内的动能损失。
3.适应不同工艺条件:换热器的设计要能适应不同的流量、温度和压力等工艺条件的变动。
4.安全可靠:要求在设计中考虑到换热器的安全性和可靠性,尽量减少故障率。
三、结构设计1.壳体:壳体是换热器的外壳,一般采用钢质材料制造。
壳体的选择应考虑到介质的性质、压力和温度等参数,并采取相应的增强措施。
2.管束:管束是由多根管子组成的,一般采用金属材料或塑料制造。
管束的设计要考虑到介质对管材的腐蚀性、温度和压力等参数,同时也要考虑到换热面积的要求。
3.管板:管板位于管束两端,起到支撑和固定管束的作用,一般采用钢质材料制造。
管板的设计要考虑到壳侧和管侧流体的流动特性,并采用合适的孔洞布置,以保证流体的均匀流动。
4.管箱:管箱是安装在管板上的设施,主要用于集流壳侧流体并将其引导出换热器。
管箱的设计应考虑到壳侧流体的流动特性和流量等参数,以实现流体的顺畅流动。
在设计过程中,需要进行换热器的热力计算和结构力学计算,以确定壳体、管束和管板等部件的尺寸和选材。
同时,还需要根据不同工艺和使用条件的要求,进行热交换面积的计算和确定。
管壳式换热器工艺设计说明书
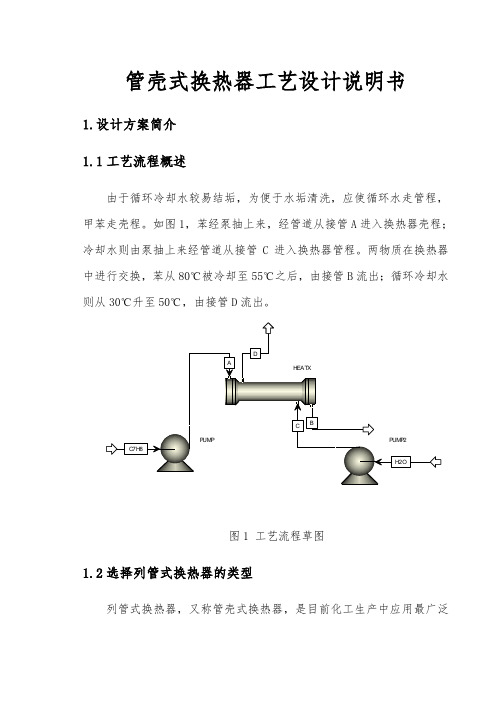
管壳式换热器工艺设计说明书1.设计方案简介1.1工艺流程概述由于循环冷却水较易结垢,为便于水垢清洗,应使循环水走管程,甲苯走壳程。
如图1,苯经泵抽上来,经管道从接管A进入换热器壳程;冷却水则由泵抽上来经管道从接管C进入换热器管程。
两物质在换热器中进行交换,苯从80℃被冷却至55℃之后,由接管B流出;循环冷却水则从30℃升至50℃,由接管D流出。
图1 工艺流程草图1.2选择列管式换热器的类型列管式换热器,又称管壳式换热器,是目前化工生产中应用最广泛的传热设备。
其主要优点是:单位体积所具有的传热面积大以及窜热效果较好;此外,结构简单,制造的材料范围广,操作弹性也较大等。
因此在高温、高压和大型装置上多采用列壳式换热器。
如下图所示。
1.2.1列管式换热器的分类根据列管式换热器结构特点的不同,主要分为以下几种:⑴固定管板式换热器固定管板式换热器,结构比较简单,造价较低。
两管板由管子互相支承,因而在各种列管式换热器中,其管板最薄。
其缺点是管外清洗困难,管壳间有温差应力存在,当两种介质温差较大时,必须设置膨胀节。
固定管板式换热器适用于壳程介质清洁,不易结垢,管程需清洗及温差不大或温差虽大但壳程压力不高的场合。
固定板式换热器⑵浮头式换热器浮头式换热器,一端管板式固定的,另一端管板可在壳体内移动,因而管、壳间不产生温差应力。
管束可以抽出,便于清洗。
但这类换热器结构较复杂,金属耗量较大;浮头处发生内漏时不便检查;管束与壳体间隙较大,影响传热。
浮头式换热器适用于管、壳温差较大及介质易结垢的场合。
⑶填料函式换热器填料函式换热器,管束一端可以自由膨胀,造价也比浮头式换热器低,检修、清洗容易,填函处泄漏能及时发现。
但壳程内介质有外漏的可能,壳程中不宜处理易挥发、易燃、易爆、有毒的介质。
⑷U形管式换热器U形管式换热器,只有一个管板,管程至少为两程,管束可以抽出清洗,管子可以自由膨胀。
其缺点是管内不便清洗,管板上布管少,结垢不紧凑,管外介质易短路,影响传热效果,内层管子损坏后不易更换。
管壳式换热器胀管工艺
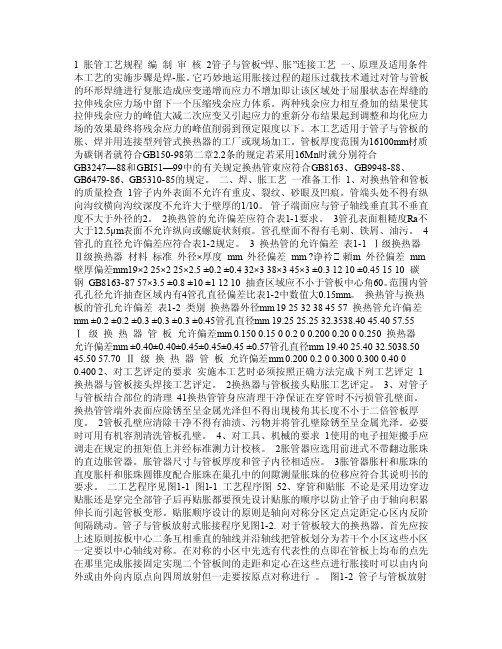
1 胀管工艺规程编制审核2管子与管板“焊、胀”连接工艺一、原理及适用条件本工艺的实施步骤是焊-胀。
它巧妙地运用胀接过程的超压过载技术通过对管与管板的环形焊缝进行复胀造成应变递增而应力不增加即让该区域处于屈服状态在焊缝的拉伸残余应力场中留下一个压缩残余应力体系。
两种残余应力相互叠加的结果使其拉伸残余应力的峰值大减二次应变又引起应力的重新分布结果起到调整和均化应力场的效果最终将残余应力的峰值削弱到预定限度以下。
本工艺适用于管子与管板的胀、焊并用连接型列管式换热器的工厂或现场加工。
管板厚度范围为16100mm材质为碳钢者就符合GB150-98第二章2.2条的规定若采用16Mn时就分别符合GB3247—88和GBI51—99中的有关规定换热管束应符合GB8163、GB9948-88、GB6479-86、GB5310-85的规定。
二、焊、胀工艺一准备工作1、对换热管和管板的质量检查1管子内外表面不允许有重皮、裂纹、砂眼及凹痕。
管端头处不得有纵向沟纹横向沟纹深度不允许大于壁厚的1/10。
管子端面应与管子轴线垂直其不垂直度不大于外径的2。
2换热管的允许偏差应符合表1-1要求。
3管孔表面粗糙度Ra不大于12.5μm表面不允许纵向或螺旋状刻痕。
管孔壁面不得有毛刺、铁屑、油污。
4管孔的直径允许偏差应符合表1-2规定。
3 换热管的允许偏差表1-1 Ⅰ级换热器Ⅱ级换热器材料标准外径×厚度mm 外径偏差mm ?诤衿 頼m 外径偏差mm 壁厚偏差mm19×2 25×2 25×2.5 ±0.2 ±0.4 32×3 38×3 45×3 ±0.3 12 10 ±0.45 15 10 碳钢GB8163-87 57×3.5 ±0.8 ±10 ±1 12 10 抽查区域应不小于管板中心角60。
完整版HTRI管壳式换热器设计基础教程讲解
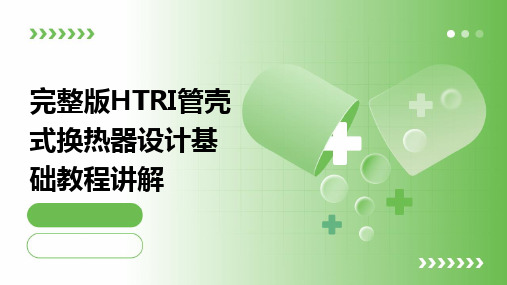
市场前景
随着科技的不断进步和工业的快速发展,管 壳式换热器的应用领域将不断扩大。同时, 随着环保意识的提高和节能减排政策的实施, 高效、节能、环保的管壳式换热器将成为未
来市场的主流产品。
02
HTRI软件简介及功能
HTRI软件发展历程
01
初始开发阶段
HTRI软件最初由美国Heat Transfer Research Inc.公司开发,专注于管
04
HTRI在管壳式换热器设 计中的应用
工艺流程模拟与优化
工艺流程建模
使用HTRI软件对管壳式换热器工艺流程进行 建模,包括输入工艺参数、物性数据和设备尺 寸等。
模拟计算
通过软件内置的算法和模型,对工艺流程进行模拟计 算,得出各物流的温度、压力、流量和物性变化等关 键参数。
优化设计
根据模拟结果,对换热器的结构、尺寸和布局 等进行优化设计,以提高换热效率和降低能耗。
换热器类型选择依据
传热方式
根据工艺要求选择合适的传热方式,如并流、逆 流或错流。
操作条件
根据操作压力、温度、流量等条件选择合适的换 热器类型。
ABCD
流体性质
考虑流体的物理性质(如密度、粘度、比热容等) 和化学性质(如腐蚀性、结垢性等)。
经济性
在满足工艺要求的前提下,考虑换热器的制造成 本、运行费用和维修费用等因素。
壳式换热器的热工水力设计计算。
02
逐步完善阶段
随着技术的发展和用户需求的变化,HTRI软件逐步增加了新的功能模
块,如振动分析、腐蚀预测等,并不断优化算法以提高计算精度和效率。
03
广泛应用阶段
目前,HTRI软件已成为全球范围内广泛应用于石油、化工、制冷等领
浅析管壳式换热器工艺设计
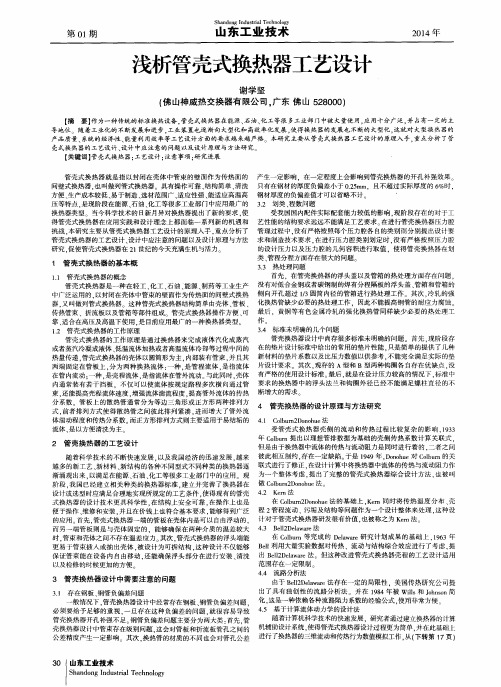
管壳式换热器制造工艺

两道冷压和一道热压 水压机,冲头,温度 900-1000
100%射线探伤 立车坡口加工,钻床钻孔
2-20 椭圆封头尺寸
2.筒体 材料为 16MnR,展开的坯料尺寸为 9850X8325X16 (mm),拼接图如图 2-69
所示。它的制造过程列于表 2-19 2-19 筒体的制造过程
液化石油气储罐示意图一储罐主要构件的加工制造板材成型前的通用工艺流程列于表217序号工作内容要求加工方法加工内容或设备原材料复验外观几何尺寸和理化检验及钢板的超声波探伤钢印标记小于5毫米的板材用风刻电刻和不退色的墨水标记边缘加工气割或等离子弧坡口用机加工方法进行边缘加工二主要受压元件的成型和焊接工艺该封头为标准椭圆形封头材料为16mnr
许偏差分别列于表 2-25 和表 2-28。
3. 折流板等
下图为最常用的 20%DN 圆缺高度的弓形折流板,为保证加工精度和效率,常将圆板
坯以 8~10 块为一叠进行钻孔和切削加工外圆,折流板孔的允许偏差列于表 2-26。
4. 管子 换热器的管表面就是传热面积。常用管子外径 10~57 (mm);其长度一般用 2000、 3000、6000(mm)等。管子应作下列试验:以管子数的 5%,且不少于 2 根作拉力、硬度 和扩口等抽样检验;进行水压试验(试验压力为设计压力的(1.5~2)倍,合格者才可使 用。 如采用胀接,管子两端应作软化退火处理,使管端的硬度低于管板硬度;另外,还 应对管端两倍于管板厚度的长范围内进行打磨,打磨后的粗糙度,钢管为
<0.5%DN
<5
<7
壳体内径过大或圆度误差会引起壳程介质短路而降低换热效率。
壳体的直线度误差会影响管束的抽装,对其要求列于表 2-24。
- 1、下载文档前请自行甄别文档内容的完整性,平台不提供额外的编辑、内容补充、找答案等附加服务。
- 2、"仅部分预览"的文档,不可在线预览部分如存在完整性等问题,可反馈申请退款(可完整预览的文档不适用该条件!)。
- 3、如文档侵犯您的权益,请联系客服反馈,我们会尽快为您处理(人工客服工作时间:9:00-18:30)。
管壳式换热器的工艺设计
芮胜波李峥王克立李彩艳
兖矿鲁南化肥厂
芮胜波:(1974-),山东枣庄人,工程师,工程硕士,从事煤化工项目研发及建设工作。
第一作者联系方式:山东滕州木石兖矿鲁南化肥厂项目办(277527),电话:0632-2363395
摘要:管壳式换热器在各种换热器中应用最为广泛,为了使换热器既能满足工艺过程的要求,又能从结构、维修、造价等方面比较合理,在设计中要从各个方面综合考虑。
本文着重从换热器程数的选择以及如何降低换热器的压力降方面进行了比较详细的论述,对于换热器的工艺设计起到一定的指导作用。
关键词:管壳式换热器,程数,压降
在化工、石油、动力、制冷以及食品等行业中,换热器都属于非常重要的工艺设备,占有举足轻重的地位。
随着我国工业的不断发展,对能源利用、开发和节约的要求不断提高,因而对换热器的要求也日益加强,特别是换热器的设计必须满足各种特殊工况和苛刻操作条件的要求。
大致说来,随着换热器在生产中的地位和作用不同,对它的要求也不同,但都必须满足下列一些基本要求:首先是满足工艺过程的要求;其次,要求在工作压力下具有一定的强度,但结构又要求简单、紧凑,便于安装和维修;第三,造价要低,但运行却又要求安全可靠。
许多新型换热器的出现,大大提高了换热器的传热效率。
比如板式换热器和螺旋板式换热器具有传热效果好、结构紧凑等优点,在温度不太高和压力不太大的情况下,应用比较有利;板翅式换热器是一种轻巧、紧凑、高效换热器,广泛应用于石油化工、天然气液化、气体分离等部门中;此外,空气冷却器以空气为冷却剂在翅片管外流过,用以冷却或冷凝管内通过的流体,尤其适用于缺水地区,由于管外装置了翅片,既增强了管外流体的湍流程度,又增大了传热面积,这样,可以减少两边对流传热系数过于悬殊的影响,从而提高换热器的传热效能。
尽管各种各样的新型换热器以其特有的优势在不同领域得以应用,但管壳式换热器仍然在各种换热器中占有很大的比重,虽然它在换热效率、设备的体积和金属材料的消耗量等方面不占优势,但它具有结构坚固、操作弹性大、可靠程度高、使用范围广等优点,所以在工程中仍得到普遍使用。
目前我们在各种工程中应用最多的换热器就是管壳式换热器,其中又以固定管板式为最常见,除了波纹管换热器等可选用标准系列产品外,其它光管换热器都由工艺专业自行设计,尽管专用计算软件HTFS的应用使设计人员从繁琐的手工设计计算中解脱出来,但是为了使设计出来的换热器能更好的满足各种要求,仍然有许多方面需要在设计时充分加以考虑。
首先,程数的选择。
管程程数的选择:关键要比较管程与壳程的给热系数,如果单管程时管程流体的给热系数小于壳程流体给热系数,则可选用双管程,管程给热系数会因此显著增大,并且总传热系数也会有大幅提高。
例如,有一台单管程换热器,管程给热系数为990W/(m2.℃), 壳程给热系数为5010 W/(m2.℃),总传热系数为794 W/(m2.℃),在换热器的外形尺寸保持不变的情况下改为双管程后,管程给热系数变为1680 W/(m2.℃),增大了70%,,总传热系数变为1176 W/(m2.℃),增大了48%,显然此时选用双管程换热器有利。
反之,如果单管程时管程的给热系数大于壳程给热系数,虽然改用双管程时,管程给热系数也会显著增大,但是总传热系数则增幅不明显,例如,一单管程换热器,管程给热系数为2276 W/(m2.℃), 壳程给热系数为2104 W/(m2.℃),总传热系数为1040 W/(m2.℃),在换热器的外形尺寸保持不变的情况下
改为双管程后,管程给热系数变为4147 W/(m2.℃),增大了82%,,总传热系数变为1280 W/(m2.℃),只增大了23%。
另一方面,由于双管程换热器中分程挡板的存在,减少了换热管的排管数量,所以,有时传热系数增大的幅度尚不足以补偿因换热管的减少而损失的换热面积,所以这种情况下就更不宜采用双管程结构了;同时从结构上看,双管程要比单管程复杂,制造难度大,所以即使在换热面积相当的情况下,仍然考虑单管程换热器为首选。
壳程程数的选择:应从两个方面考虑,首先,对于换热管很长的换热器,如果为了减少占地面积,可以采用双壳程结构以减短换热管长度,例如一台单管程、单壳程的换热器外形尺寸为φ1000×6000,若改用双管程双壳程结构,则φ1400×3000可满足要求,长度方向减少了一半,从占地角度考虑是很有意义的。
其次,如果壳程流体流量较小,造成壳程给热系数较小,单纯靠扩大壳体直径虽然会增大传热面积,但是由于流速降低而导致总传热系数的减小,甚至不能补偿增大的传热面积,此时,除了可以选用几台小直径的换热器串联外,也可以考虑选用双壳程结构。
但是双壳程设计需要在壳程设置纵向隔板,大大增加了换热器本身结构的复杂性,增加制造成本,而且壳程介质容易发生短路而降低换热效率,一般推荐采用。
第二,压力降的设计。
换热器的压力降不仅受到动力消耗的限制,有时工艺过程也要求压力降不能太大,例如热虹吸式再沸器,其工作原理就是靠再沸器与塔之间的静压差,使工艺物料在蒸馏塔与再沸器之间构成循环,如果工艺流体流经再沸器的压力降过大,会使静压差不足以克服压力降从而导致精馏塔不能正常操作。
影响压力降的因素很多,其中物料流速关系较大,增加物料流速,可增大传热系数,使换热器结构紧凑,但增加流速同时增大了换热器的压力降。
管程压力降的减小主要就是靠减小流体流速即增大换热管的流通面积,如减少管程数、选用大直径的壳体从而增加换热管数等措施。
壳程压力降除了与壳体直径有关外,换热器的内部结构比如折流板的形式及切口宽度、换热管的间距及排列方式等也会对压力降造成不同程度的影响,如果选择得当,将会大大降低壳程的压力降,壳程为气相冷凝时常遇到这种情况。
为了提高壳程流体的流速,往往在壳体内安装一定数目与管束相垂直的折流挡板,这样可使流体沿规定路径多次横向流过管束,增加湍流程度,提高管间对流传热系数。
常用的折流板有以下两种形式:1)圆缺形折流板,大部分换热器采用此种形式。
又可分为单圆缺和双圆缺,单圆缺形折流板的缺口宽度可为直径的15~45%,其在卧式壳程内的放置形式有两种,一种是上下方向排列,可造成液体剧烈扰动,以增大传热系数,另一种是左右方向排列,当设备中伴随有气相冷凝时,就必须采用左右方向排列,便于冷凝液与气体的流动。
对双圆缺形折流板,每块圆缺的缺口宽度可为直径的15~25%;2)环盘形折流板,此种折流板允许通过的流量大,压降小,但传热效率不如圆缺形折流板,因此这种折流板多用于要求压降小的情况。
对于壳程为气相冷凝的冷凝器,折流板的具体形式对壳程压降有很大影响,为了减小压降,在满足换热效果的前提下,可以增大单圆缺折流板的切口宽度,也可以选用双圆缺折流板或者环盘形折流板。
此外调整折流板之间的间距以及第一块折流板与管板之间的距离,也会减小壳程压降。
一般情况下,对同一台换热器,我们都习惯于采用相同切口宽度的折流板,对壳程没有相变的换热器来说,这样做没有问题,但是对壳程为气相冷凝的冷凝冷却器来讲,就会存在一定的弊病,如果采用较小的圆缺切口宽度,则在壳程进口处的几块折流板处必然会产生较大的压降;反之,如果为了减小压降而采用很大的圆缺切口宽度,那么经过一定数量的折流板后,大部分气体冷凝造成流体体积急剧减小,从而导致液体通道相对太大而影响换热效果。
实际上,为了解决这个问题,我们可以对壳程进口处的几块折流板采用较大的切口宽度,而后逐渐减小切口宽度,这样既能满足压降的要求,又能使冷凝液也能有较大的传热系数,但是HTFS计算软件中没有提供这种计算模式,所以,折流板的切口宽度将如何渐
变,渐变后壳程内不同部位流体的给热系数如何分布,计算起来将比较复杂,有待于在实际工作中进一步寻求经验。
此外,在管壳式换热器的设计中,还有一些常规问题需要考虑。
比如在物流的安排上,一般应遵循以下原则:(1)不洁净或易于结垢的物料应流经易清洗的一侧;(2)需要提高流速以增大对流传热系数的流体应当走管内;(3)具有腐蚀性的物料走管内;(4)压力高的物料走管内,以使外壳不承受高压,降低设备成本;(5)温度很高(或很低)的物料走管内,以减少热量(或冷量)的散失,如果为了更好地散热,则应让高温物料走壳程;(6)蒸汽一般通入壳程,以便于排除冷凝液,而且蒸汽较清洁,其对流传热系数又与流速关系较小;(7)粘度大的流体[μ>(1.5×10-3—2.5×10-3)Pa.s]一般走壳程,因为在设有挡板的壳程中流动时,流道截面和流向都在不断改变,在低Re数(Re>100)下即可达到湍流,有利于提高管外流体的对流传热系数。