8D报告培训教材教程
纠正行动(8D)报告培训教程
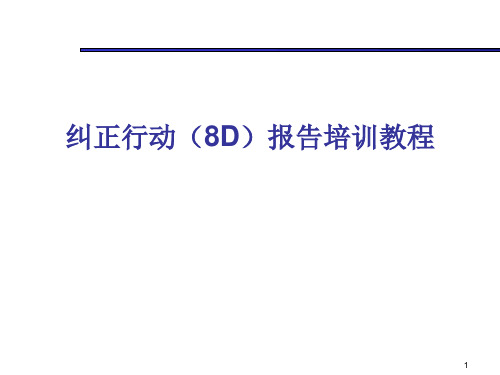
8D的特点
4
8D中常用的工具
第二步:明确问题 第四步:分析/验证根本原因
第五步:制定/实施纠正措施
甘特图
第七步:实施预防措施(文件化)
5
公司所用8D格式
公司使用
此表格均适用于被动式改善,即问题已出现时的改善。
6
8D的第一步:建立改善小组
建立合适的改善小组是成功的一半。
建立改善小组时常犯的错误
12
8D的第二步:明确问题
流程图绘制的提示
13
8D的第二步:明确问题
流程图的层次
14
8D的第二步:明确问题
流程图实例
15
8D的第二步:明确问题
流程图实例
16
8D的第二步:明确问题
陈述问题的标准
17
8D的第二步:明确问题
陈述问题的例子
18
8D的第二步:明确问题
D1: 改善小组(由责任部门填写) 组长: 成员:
D2:问题描述:(由责任部门填写)
将问题描述填在你们的CAR中,时间5分钟。
19
8D的第三步:制定/实施围堵措施 ---围追堵截
20
8D的第三步:制定/实施围堵措施
D2:问题描述:(由责任部门填写)
D3:围堵措施(由责任部门填写)
完成时间
责任人
将围堵行动填在你们的CAR中,时间5分钟。
21
8D的第四步:分析/验证根本原因 ---寻根问底
发生日期/时 间:Mar17,08
发生地点: 钻房IPQC检查
要求回复时间: Mar 17,08
QE经理批准:
不符合(潜在不合格)情况描述(由发出部门填写) IPQC全检XXXXX,Lot号 12345,批量数量100Panel,检验数量100Panel,发现20Panel 出现 2.0+/-0.075mm的孔孔大问题,
8D报告培训教材经典课件
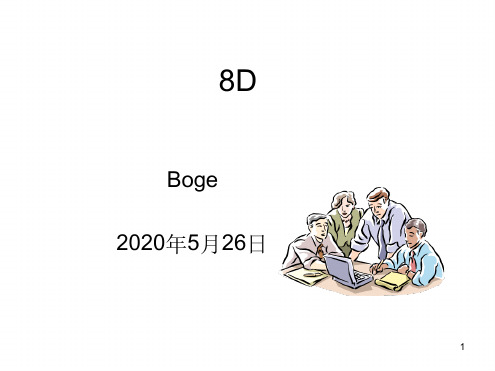
?小组成员的 人数控制在4到 10个之间
?选择具有相 应技能、知识、 资源、权力等 的人作为团队 成员
?各类成员之 间职责、任务 合理搭配
?按需要调整 团队成员
11
四. 8D步骤—D2问题描述
以客户的角度和观点详细描述其所感受到的问题现象, 将所遭遇的问题,以量化的方式,明确出所涉及的人, 事,时,地,为何,如何,多少。
33
五.8D改善案例 D1.成立小组
? 按问题涉及范围确定小组成员: ? 责属单位:生管部、业务部、仓储部、品管部 ? 责属人员:
34
五.8D改善案例
D2.问题描述
? 何时 : 20099年11月4日; ? 何人 : 众盛精密机械厂—品管部; ? 何地 : 众盛精密机械厂—包装车间; ? 何事 : 包装ALT-5 检测器; ? 如何 : 使用的20μMHT机用膜一拉就断; ? 为何 : 机用膜卷端口破损; ? 多少 : 20卷中目前发现6卷有问题。
效果确认 实事求是,以事实和数据为依据,对数据用统计工具处 理后得出相应的结论,不应未做对比分析即判定效果。
16.00% 14.00% 12.00% 10.00%
8.00% 6.00% 4.00% 2.00% 0.00%
slot1
slot2
改善前
slot3
slot4
改善后
slot5
数据点多按日期来建议走势图,数据点少可用上面的柱状图
析和方案策划。
9
四. 8D步骤—D1建立小组
建立一个小组来解决问题和执行纠正计划, 小组成员应具有过程和/或产品知识、分配的 时间、权威和需要的技能。
建立小组需要考虑的要素:
?小组的领导: 谁来推动? ?小组的资源: 谁提供支持? ?小组的成员: 合作及分工? ?人员的数量: 多少为宜?
8D报告培训教材

2.
描述 问题
实施
和验证
3.
临时
(限制)行动
4.
寻找潜在原因
选择可能 原因
N 潜在原因 是根本 原因吗?
Y
寻找可能的 解决方法
验证
5. 改进行动
实施
6.
永久性
改进行动
7.
预防
问题重现
8.
祝贺你的 小组
2021/5/27 确利达—创造企业新动力!
8
我们是谁?
我们都是同事、领导者、教练和 导师。
我们互相依赖,我们是公司的脊 梁。
2021/5/27 确利达—创造企业新动力!
50
确定和分析可能的原因
评价所有现有的有关问题的信 息和数据。 在问题被发现的同时,评价正 在发生的事件。 是什么导致了质量水平的不同?
运用分析工具:
运用数据
为了有效地解决问题 有必要对已确定的所
&
有可能原因进行调查?
先前提到的工具 因果分析图 FMEA 和控制计划 图表 过程图
验证
5. 改进行动
实施
6.
永久性
改进行动
7.
预防
问题重现
8.
祝贺你的 小组
33
请 分 析:
纠 正…… 纠正措施…… 预防措施……
2021/5/27 确利达—创造企业新动力!
34
纠正 为消除已经发现的不合格所采取的的措施 可涉及:返修,返工或降级
2021/5/27 确利达—创造企业新动力!
35
纠正措施
2021/5/27 确利达—创造企业新动力!
31
3D
实施和验证
临时(限制)行动
2021/5/27 确利达—创造企业新动力!
2024年8D报告培训教材教程

8D报告培训教材教程1.引言8D报告是一种广泛应用于质量管理和问题解决的方法,其名称来源于8个解决问题的步骤(Disciplines)。
本教材旨在为您提供关于8D报告的全面培训,帮助您掌握8D报告的编写和应用技巧。
2.8D报告的背景和目的8D报告起源于汽车行业,并逐渐被其他行业所采用。
其主要目的是系统地解决问题,防止问题再次发生,并提高产品和服务的质量。
8D报告通常用于处理客户投诉和内部问题,以及推动持续改进。
3.8D报告的8个步骤3.1步骤1:建立团队在开始编写8D报告之前,需要建立一个跨部门的团队,团队成员应具备相关领域的专业知识和经验。
团队应由一名负责人领导,负责协调和推动整个解决问题的过程。
3.2步骤2:问题描述问题描述是8D报告的核心部分,需要清晰地描述问题的现象、影响和发生的时间。
问题描述应尽量具体、准确,并使用数据和事实来支持。
3.3步骤3:临时措施在找到根本原因之前,需要采取一些临时措施来减轻问题的影响。
这些措施应尽快实施,并在报告中详细说明。
3.4步骤4:根本原因分析根本原因分析是解决问题的关键步骤,需要运用各种工具和技术来找到问题的根本原因。
常用的工具包括鱼骨图、5个为什么等。
3.5步骤5:制定行动计划根据根本原因分析的结果,制定详细的行动计划来解决问题。
行动计划应包括具体的行动步骤、责任人和完成时间。
3.6步骤6:实施行动计划按照行动计划,组织资源并实施解决方案。
在实施过程中,需要监控进度,并及时调整计划以确保问题得到有效解决。
3.7步骤7:效果验证在实施解决方案后,需要对效果进行验证,以确保问题得到根本解决。
验证可以通过数据分析、客户反馈等方式进行。
3.8步骤8:预防措施和持续改进为了防止问题再次发生,需要制定预防措施,并对整个问题解决过程进行总结和反思,提出改进建议。
4.8D报告的编写技巧4.1结构清晰8D报告应遵循一定的结构,包括引言、问题描述、临时措施、根本原因分析、行动计划、实施结果、效果验证、预防措施和持续改进等部分。
8DReport培训教材

3 – 为什么?
4 – 为什么? 4 – 为什么?
32
5 – 为什么? 5 – 为什么?
5Why分析公司近期案例
2品0全11年部8停月线2日。,(铜运陵5W锐H展Y解反决馈方,法我司为7什月么份会所发供生的Q?J1为00什3产么品没,有出检现测气出门来环?带为间什隙么无会法出调厂配?,)产 从法(试验、检验、探测)方面分析(为什么该问题没有被检测到)
四问:为何吃早餐晚了?
答:因为起床晚了;
五问:为何起床晚了?
答:因为忘了上闹钟了……
15
课程内容
5Why质量工具简介 5Why工具应用方法 5Why问题解决方式 5Why经典案例解析
16
5 why质量工具简介
丰田生产方式创始人大野耐一总是爱在车间走来走去,停下来向 工人发问。他反复地就一个问题,问“为什么”,直到回答令他满意, 被他问到的人也心里明白为止——这就是后来著名的“五个为什么”。
恰当地定义问题。
不断提问为什么前一个事件会发生,直到回答“没有好的理由”或直 到一个新的故障模式被发现时才停止提问。
解释根本原因以防止问题重演。
文件中所有带有“为什么”的语句都会定义真正的根源(通常需要至 少5个“为什么”)
总体5个为什么图表
问题
1 – 为什么?
1 – 原因
2 -为什么?
2 -原因
2
什么是8D?
在撰写8D报告的时候,务必要保证下面的问题被清 楚准确有理有据地回答:
D2-问题是什么? D3~D6-问题如何解决? D7-将来该问题如何预防
3
什么是8D?
务必保证以下的问题被如实回答: 1.对零件的知识进行了充分的论证 2.完全确定了根本原因并聚焦于该原因 3.遗漏点已经被识别 4.确定与根本相匹配的纠正措施 5.纠正措施计划的验证已经被确定 6.包括了实施纠正措施的时间计划 7.有证据显示供方将把纠正措施纳入整个系统。
质量管理8D报告培训(经典教材)含案例分析_2022年学习资料
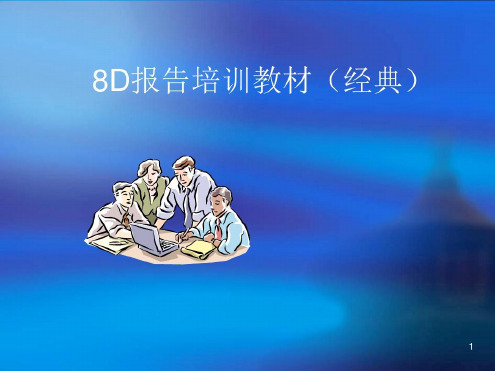
四.8D聚一D3临时对策-定义、验证和执行临时控制行动,保证在永-久纠正措施实施前,将问题与内外部顾客隔。-需要考虑的问题:-1.防止继续产生不-2减小产生的不良和-良品(减少不良品产-后续可能产生不良对-客户 影响。-14
∥NEWASIA-折-亚州州-四.8D步骤一D3临时对策-确定并执行应先采取的临时措施,以遏制外界/内部客 户问题的扩大。-临时措施的确定应考虑从供应商零件库存--供应商零件-在途品-内部零件/材料一生产制程一仓库 存一交付在-途品一客户端减少和降低(消除)后果的产生。-临时措施一直要持续实施至后续的永久对策的执行有效,方可撤消-临时措施实施中,应及时跟踪和验证其效果-15
D1--成D步骤D1建立小组-选择小组成员的准则-■选择具有相-■小组成员的-■各类成员之-■按需要调整技能、知识、-人数控制在4到-间职责、任务-团队成员-资源、权力等-10个之间-合理搭配-的人作为团队-1
四.8D素一D2问题描述-以客户的角度和观点详细描述其所感受到的问题现象,-将所遭遇的问题,以量化的方式, 明确出所涉及的人-事,时,地,为何,如何,多少-什么是问题??-期望-目标-现实-12
四.8D斐聚一D4原因分析-鱼骨图分析-员工品质意识淡薄-机-手工喷涂-标准执行-力差-人员变动大-杜邦油 性能-不良-车顶饰条附着力不良-素材表面-输送链台车-要打磨-漆渣太厚-复押半成品-喷涂房-表面粒点-环境 -未对半成品-进行检验-法-料-21
四.8D斐聚一D4原因分析->人人员相关信息是否有变更->机-设备维修保养记录-5M1E->料物料更改记录 主料、辅料)->环-温湿度记录-法工艺更改记录,-生产原始记录->测-检测条件方法人员-常用方法-1.对操 员现场询问2.现场观察-3.模拟试验-4.DO试验-5.异常记录-22
8d报告培训教材
六.結論:
• 8D格式用于監控解決問題的過程,它不是 一個詳盡的報告或複雜的分析,描述工具, 而是一個包含了解決問題的每個步驟的 集合,因而可從其中找到經提煉的基本信 息.
七. 8 D steps 8D步驟
• (1) Team: Composition of the team in charge of solving the problem
8D 方法
一.范圍:
該方法适用于解決各類可能遇到的簡單或 複雜的問題. 8D 方法就是要建立一個体系,讓整個團 隊共享信息, 努力達成目標. 8D本身不提供成功解決 問題的方法或途徑, 但它是解決問題的一個很有用 的工具.
二.目標
• 提高解決問題的效率,積累解決問題的經 驗.
• 提供找出現存的与質量相關問題的框架, 杜絕或盡量減少重復問題出現.
七. 8 D steps 8D步驟
• (5)選擇長期糾正措施 • 1) 對將要執行的長期糾正措施在實施前做
進一步的确認,以核對它們是否在實施后能提供 一個合乎期望的結果. 目的是解決問題的根源, 要防止這些糾正措施帶來任何其它的負面影響, 在這种情形下,須採取其它的措施消除負面影響. • 2)選擇或創建一個測量工具,評估在糾正過程中 各項工作的功效.
• 8D格式的原則是針對出現的問題,找出問 題產生的根本原因,提出短期,中期,和長期 對策,並采取相應行動措施.
三.定義:
• (1) 8D (8 Disciplines) 方法包含8個解決問題的步驟. 它基于使用 描述工具,格式化,分析,量化等工具,從而提供徹底解決問題的指引.
• (2)問題: 被發現的具体問題,它包括: • 1) 与正常狀況相比,屬于失常的現象,在這种情況下, 需要予以
8D报告培训教材
8D 方法
一.范圍:
該方法适用于解決各類可能遇到的簡單或 複雜的問題. 8D 方法就是要建立一個体系,讓整個團 隊共享信息, 為努力達成目標. 8D本身不提供成功解 決問題的方法或途徑, 但它是解決問題的一個很有 用的工具.
二.目標
• 提高解決問題的效率,積累解決問題的經 驗. • 提供找出現存的与質量相關問題的框架, 杜絕或盡量減少重復問題出現. • 8D格式的原則是針對出現的問題,找出問 題產生的根本原因,提出短期,中期,和長期 對策,並采取相應行動措施.
四.在下列情形中須提交8D報告:
• • (1)當客戶在工厂現場的稽核中發現不合格項或缺陷時, 對于嚴重 不良,主要不良及重複發生的次要不良須提交8D報告. (2)OQC發現嚴重不良,主要不良及重複發生的次要不良時須提交 8D報告. (3)當市場上發現有重複發生的產品缺陷時須提交8D報告. (4) 當ORT測詴過程中發現缺陷時須提交8D報告. (5)IPQC在同一生產現場連續發現三個相同不良現象或三個相同 不良現象 (6)要對那些需要長期糾正措施來解決的缺陷采取行動時須提交 8D報告. (7)被程序文件定義要求8D報告其他情形.
七. 8 D steps 8D步驟
• (8) 項目完畢 • 1) 關注的問題被解決,确認,核實,和紀 錄被權威人士審核通過.
八.推薦的流程
八.推薦的流程
附圖--1
附圖--2
附圖--3
附圖--4
七. 8 D steps 8D步驟
• (4) 定義和核實原因 • 1) 從問題描述中尋找最有可能的一些原因,若有可 能,做一些測詴幫助尋找原因. • 2) 檢查所有考慮到的可能原因, 將它們會帶來的結 果与觀察到的結果比較, 原因/結果矩陣圖可幫助選擇 优先考慮哪個原因. • 3) 識別問題的种類.(設計,程序,製程,材料,人員技巧). • 4) 探尋可能的解決方案,列出可行性,效果,實施時間 等. • 5) 建立將要實施的那些措施的檢驗標准. • 6) 盡量利用各种圖表
8D报告培训教材
Team Problem description Short term containment actions Define and verify root cause Select permanent corrective actions Implement permanent corrective actions Actions to prevent problem recurrence Problem solved
4.7 Step 7: Actions to prபைடு நூலகம்vent problem Recurrence
•更新整个质量系统 ((Procedures,Guidelines,Specifications and Tools used concerning the problems).
•没有管理层的同意是没有办法执行的, 这是所有措施的第 一步, 然后这些措施必须立即并通过持续改善的计划去执 行。
Quality System, guidelines, procedures, instructions
1 -Team 2 –Problem description
Build the team
No Deterioration ?
Yes Document and describe
the problem
• 用5M 的方法定性并定量的定义问题发生的条件。 ( Man, Machine, Material, Method , Milieu )
• 用5W1H 来详细的描述问题 ( 附表为不同问题描述的建议)
附表:
Product Problem
Process Problem Component Problem Technology Problem
PQE培训教材8D报告课件
•
完成CPK-1.5
•
•
Decreased defect occurrences to zero
•
不良率巳降到零
• Continue containment activities until permanent C/A • actions are verified as being effevtive
Discipline 8: Congratulate Your Team,Case Close. 原則8:結案予參与組員以勉勵
•When shall 8-D be used
The fallout consistently over the DPPM goal. •不良率連續超出DPPM目標值
MEET THE DPPM goal but one failure more than 20% to the fallout
Responsibilities
The originator Initiate the 8-D 發起(開始)8D
Copy the 8-D to all CPQ manufacturing sites(as applicable) 給所有CPQ生產地發送8D
The supplier Provide responses in 8-D format 以8D格式提供結果
PPT文档演模板
PQE培训教材8D报告
• Discipline 6: Verify effectiveness of actions
• • Describe verification results in quantifiable term E.G.: • 描述改善結果
•
Achieved CPK – 1.5
- 1、下载文档前请自行甄别文档内容的完整性,平台不提供额外的编辑、内容补充、找答案等附加服务。
- 2、"仅部分预览"的文档,不可在线预览部分如存在完整性等问题,可反馈申请退款(可完整预览的文档不适用该条件!)。
- 3、如文档侵犯您的权益,请联系客服反馈,我们会尽快为您处理(人工客服工作时间:9:00-18:30)。
12/08 8:25 动力运行金晓 栋从5#动力栋 赶至2#1F现场
12/08 8:31
12/08 8:32
动力运行金晓栋 金晓栋与曹健东手
至屋顶机房复位 动开启电梯轿厢门,
后返回1F现场 14名被困人员解困
12/08 8:50 签约单位 维修人员 赶至现场
过程持续10min
过程持续2小时
12/08 8:22 动力运行值班室 2664接到安环监 控中心5119报电 梯故障
1W
2W
3W
4W
5W
WHY 问题
WHY 中间原因
WHY 中间原因
WHY 中间原因
四. 8D步骤—D4原因分析
5-WHY分析案例1
状态1 一辆汽车出了故障不能行驶(WHY1)
状态2-原因1 引擎故障(WHY2)
状态3-原因2
火花塞不点火(WHY3)
状态4-原因3
火花塞潮湿沾水(WHY4)
状态5-原因4
2. 运行异常启动 限位后停车运 行保护:OK
电梯保护功 能启用:OK
电梯故障应急预案中无 5119安抚要求:NG
1.线路问题(无) :OK
2.感应器问题(未 提供运行方向信 号):NG
3.主机问题(参数 重新灌入,运行 正常):OK
1.电梯安装公司按规 定实施季/月维修 保养:OK
2.梯按周期维保:OK
D1—四成.立8工D步作团骤队—D1建立小组
小组成员的 人数控制在4到 10个之间
选择具有相 应技能、知识、 资源、权力等 的人作为团队 成员
各类成员之 间职责、任务 合理搭配
按需要调整 团队成员
四. 8D步骤—D2问题描述
以客户的角度和观点详细描述其所感受到的问题现象, 将所遭遇的问题,以量化的方式,明确出所涉及的人, 事,时,地,为何,如何,多少。
此过程尽量获取内部 和外部的问题信息、 数据、进行初步的分
析和方案策划。
四. 8D步骤—D1建立小组
建立一个小组来解决问题和执行纠正计划, 小组成员应具有过程和/或产品知识、分配的 时间、权威和需要的技能。
建立小组需要考虑的要素:
小组的领导:
小组的资源: 持小?组的成员:
人员的数量:
谁来推动? 谁提供支 合作及分工? 多少为宜?
改善前
改善后
数据来源:
数据点多按日期来建议走势图,数据点少可用上面的柱状图 时 间:
关键点一 :改善前后对比,数量及比例。 关键点二: 结果收集的数据来源要说明。
四. 8D步骤-D7效果确认及标准化
标准化
标准化是把企业所积累的技术、经验,通过 文件的方式进行规范。
标准化的目的:
技术储备、 提高效率、 防止再发、 教育训练。
D3:应急措施
(Interim Containment Action )
临时对策1:解救被困人员 临时对策2:关闭该电梯 ,等待维修单位
D4: 鱼刺图原因剖析
(5M1E)
Environment 电梯轿厢受到冲击,引起 光电感应器信号故障:NG
电梯轿厢受到冲击 1. 轿厢受外力晃动,比如扔水桶
管理方面: 对策1:鉴于电梯已经运行超过10年,经与电梯公司讨论,对方同意轿厢光电感应器点检频率由原来 1季度点检改为1个月点检; 对策2:鉴于电梯已经运行超过10年,经与电梯公司讨论,对方同意警铃和三方通话设备的点检频率 由1个月点检改为半月点检; 对策3:修改应急预案,增加服务功能:一旦发生电梯关人,监控中心值班人员必须利用电梯三方通话 功能与被困人员保持联络直至被困人员获救; 对策4:轿厢内张贴电梯乘用提示语。
1. 报警按钮未启动三方通话联系到监控中心:NG 2. 事后报警按钮测试(第一次正常,第二次不正常,拆
开后检查发现触点接触不良):NG 3. 警铃不响 电梯只有三方通话功能(国标无强制要求
需警铃鸣响功能) :OK 4. 话筒铃声及功能正常(事后测试):OK
1. 光电感应器位置偏离 导致无信号输出:NG
四. 8D步骤-D7效果确认及标准化
效果确认 实事求是,以事实和数据为依据,对数据用统计工具处 理后得出相应的结论,不应未做对比分析即判定效果。
16.00% 14.00% 12.00% 10.00%
8.00% 6.00% 4.00% 2.00% 0.00%
slot1
slot2
slot3
slot4
slot5
. 8D步骤
原因分析
0 问题初步了解
4
确定可能原因
5
长期对策
1
建立小组
2
问题描述
3
临时对策
选择最可能原因
NO
最有
可能的原因
是否是根本
原因?
YES
确定根本原因
6 预防再发对策
7 效果确认及标准化
8
恭贺小组
四. 8D步骤—D0问题初步了解
问题初步了解(立项和准备工作)
– 鉴定是否有进行8D 的必要; – 立项和确定主题; – 收集资料。
什么是问题???
问期题望
期望 目标
现实
四. 8D步骤—D2问题描述
问题描述方法:5W/2H
WHO
WHAT
WHEN WHERE WHY HOW
5W2H 谁
什么
何时 何地 为什么 怎么样
解释 识别那一个客户(内/外部)在抱怨 问题的症状,无法用文字描述清楚的,借助 于数字或图片将问题表达清楚
记入问题发生的日期 记入问题发生的场所 识别已知的解释 在什么的模式或状态这问题会发生
• 确定并执行应先采取的临时措施,以遏制外界/内部客 户问题的扩大。
• 临时措施的确定应考虑从供应商零件库存---供应商零 件在途品--内部零件/材料—生产制程—仓库储存—交 付在途品—客户端减少和降低(消除)后果的产生。
• 临时措施一直要持续实施至后续的永久对策的执行有 效后,方可撤消。
• 临时措施实施中,应及时跟踪和验证其效果。
:NG(送水公司) 2. 轿厢受力不均匀,比如货物集
中堆放:NG(各部门)
Material
电气元件使用寿命: 未指定,损坏后更换
Man
维保人员按维保要 求进行维保:OK
对应人员按应急预 案流程处置:OK
1. 感应器损坏后更换:OK 2. 按钮功能不良更换:NG
(保洁人员使用碧丽珠擦拭 电梯控制面板引起按钮接触 不良)
需要考虑的问题:
1.确定并执行预 防再发对策, 并应注意持续 实施监控,以 确定根因已经 消除。
2.待步入生产阶 段,应即监视 纠正措施之长 期效果,并于 必要时采行补 救措施。
3.验证 预防再发 对策有效 后,可以 停止临时 措施。
四. 8D步骤-D7效果确认及标准化
验证预防再发对策并监控长期的效果。 水平展开,以防同一问题及类似问题再 度发生。将相关对策形成书面文件(管 理制度、程序文件、作业指导书、表单、 技术文件、工程图纸等)。
四. 8D步骤—D4原因分析
鱼骨图分析
机
手工喷涂
员工品质意识淡薄
人
标准执行 力差
人员变动大
杜邦油漆性能 不良
素材表面
输送链台车
要打磨
漆渣太厚
喷涂房
环境差
未对半成品
环
法
进行检验
料
复押半成品 表面粒点
车 顶 饰 条 附 着 力 不 良
四. 8D步骤—D4原因分析
人--人员相关信息是否有变更 机--设备维修保养记录,
四. 8D步骤—D5长期对策
选取最佳的的长期对策来解决根本原因。 同时也选取最佳的长期对策来控制根本原 因的影响。
需要考虑的问题:
1. 一定是针对根本原 因来制定措施,一个 原因可能有几条措施。
2.必要时对已 经明确的措 施进行验证。
3.措施 尽量具
体化。
四. 8D步骤—D6预防再发对策
计划和执行选取的预防再发对策。去除 临时行动。
5M1E 分析
常用方法
料--物料更改记录(主料、辅料)
环--温湿度记录 法--工艺更改记录,生产原始记录, 测--检测条件方法人员
1.对操作员现场询问 2.现场观察 3.模拟试验
4.DOE试验
5.异常记录
四. 8D步骤—D4原因分析
5-Why 分析
当一个原因被发现时,不停地问为什么、为什么、为什么、 为什么、为什么,一直到无法拆解下去 。
四. 8D步骤-D8恭贺小组(结案)
恭贺小组的每一成员,问题解决完成,对小 组成员的努力予以肯定。
对所有积极参与的小组成员 进行适当的承认
对小组的效益进行沟通和文件化
四. 8D步骤
注意事项 上述各项步骤,不一定必须完全依序进行,各步骤之顺 序可因个别问题而异。
五.8D改善案例
D0:发生时间线
(Time-Line)
四. 8D步骤—D4原因分析
深入明 确问题
团队协 作: 列出所 有可能 的疑点
进一步明确问题 (不良解析)
从流程分析 (流程图)
质量问题5M1E分析 (鱼翅图分析)
各个可疑原因排查
对现场人机料环法
测进行观察测量,
有历史数据的对数据
疑
进行初步分析
点
验
关键原因确认
证
统计分析
DOE验证
机理分析
关键原因-是否为根本原因 5-WHY分析
一.什么是8D
此方法以团队运作导 向以事实为基础,避 免个人主见之介入, 使问题之解决能更具 条理。
面对问题应群策群力, 互相帮助、相互提拔、 如此才能彻底解决问题。
3
二.为什么要推行8D
三. 何时采用8D
重复发生,一直没有解决的问题 比较重大的制程品质问题 客户要求回复的品质投诉