模压制品缺陷及解决办法
SMC模压常见缺陷、原因与解决办法

不良现象
可能原因
解决方法
模压时有先胶化的区域 表 面 多 孔 性
SMC熟料熟成粘度太低 模压太低 熟料配方中硬酯酸锌用量过高 SMC摆料干掉(苯乙烯单体挥发掉)
●降低模温 ●配方中多加些抑制剂 ●增长贮存时间或贮存在较高温处以增加 其熟成 ●配方中增加增粘剂量 ●增加模压 ●降低配方中之硬酯酸锌用量 ●SMC熟料经可防止苯乙烯单体挥发的塑胶膜包装 ●在模压前不要准备太多的熟料 灼烧(Burning)
可能发生之原因
颜料的比重太小 成形前颜料即分离 成形流动时颜料分离
改善对策
●改用无机颜料之色料 ●加速SMC初期的增粘 ●增高SMC熟料之熟成粘度 ●增高SMC熟料之熟成粘度 ●加快合模速度
上 硬 厚 在厚内处产生内压力造成层间之剥离 凸呈化肉 起 圆 表 部 在流动距离大之处,单方向强度减少(玻璃 形 面 份 纤维定向作用)
摆料面积太大,流动距离太短,空气无法逸 ●减少摆料面积或加小面积摆料于较大 出 面积摆料之上 ●降低初期膏状物的粘度 表面多孔性 ●增大SMC机器的压合力量 熟料中玻璃纤维合浸不佳 ●改变合浸较佳的纤维
部份不完全硬化,由于太弱,不易顶出而 ●增加模温 损坏 变形(Warpage) ●配方使用低收缩或不收缩树脂 成形品轻微 由于硬化及冷却时,流动及收缩不均匀而 ●调整模具的温度差 翘曲 翘曲 ●检查顶出系统的正确动作
成形品严重 由于熟料过度的流动,造成玻璃纤维的定向 ●增加摆料面积以缩短流动距离或使用低收缩、不 翘曲 作用(orientation) 收缩树脂 ●使用低收缩或不收缩树脂 ●增加压力,缩短切断纤维的长度,改变模具 设计,更改摆位置,减少剪切边间隙 成形品的厚度和加强肋深,宽间的比例不适 ●调整至最适当的比例 当 波形表面(wavy surface) 在大多数情况不能完全消除改进方法: 成形品的形状不适当或复杂设计,妨碍均匀 ●增大模压 流动 ●改变模具的设计 ●改变摆料位置 摆料重量太低(摆料不足填满模子,合模时 ●增加摆料 不能产生正压(podditive pressure)熟料以乱 心摆放熟料,并降低合模速度 流流动 成形品收缩率太大 收缩率太大(光泽不均匀) 材料 苯乙烯单体量过多 低收缩剂量过多 ●改变配方,使苯乙烯量适中 ●改变配方中低收缩剂量使适中 ●使用低收缩或不收缩熟料 光泽不良,光泽不均匀 ●小
橡胶模压常见质量问题及解决方案

橡胶模压常见质量问题及解决方案模压制品:是指在平板硫化机上用模具成型和硫化的中小型橡胶制品。
橡胶模压中出现的反映在不同制品的同一类问题,如:缺胶、鼓包等。
由于橡胶材料的种类、批次、产地不同、机台、操作者不同、只能具体情况具体分析。
1.缺胶表现为表面(全部或局部)疏松、麻面或有空洞,产生的原因和防止方法:(1)加料量不足为保证每穴制品不缺胶,应准确确定用料量,加足料量并反映在工艺文件内;(2)压力不足,胶量不能充满模腔,应适当增加压力。
(3)胶料流动性太差。
在制品性能允许的情况下,可调整胶料配方,增加可塑性。
工艺上适当增加压力或者在模具表面涂洒一层硬脂酸锌、硅油一类的润滑剂。
(4)模具温度过高,胶料部分焦烧,流动性降低。
应适当降低装料时的模具温度,但不应过多,否则模温在规定时间内升不到硫化温度而使整模胶料报废。
硅橡胶可在较低温度下装料。
(5)胶料的焦烧时间太短应改进配方,提高胶料的耐焦烧性能。
(6)装料合模速度太慢,引起焦烧,应提高操作技术。
(7)坯料安放位置不当,使得胶料不易充满模腔。
(8)模具结构不合理,也会使胶料不易充满模腔如:对于狭长制品,应便于制品长度方向与加压方向垂直。
(9)加压太快,胶料在未充满模腔之前就被挤出模外,使飞边增厚而制品缺料,应减慢加压速度,是胶料在压力下缓缓流入模腔。
2.对合线开裂表现为啓模后在模具对合处制品开裂,有时飞边内缩现象(俗称抽边),产生原因及防止方法:(1)压力不足或压力波动使硫化过程中胶料模腔内部压力大于硫化压力。
而使模具稍稍涨开,引起制品开裂,应检查压力或者检查压力波动原因。
(2)硫化压力过大胶料被严重压缩,启模时,压力急剧下降,硫化胶体积增大,制品其它部分受模具限制无法膨胀,而模具对合模线处则可自由膨胀,因膨胀不均造成的内应力就会导致对合线开裂,应使硫化压力调整到合适的状态,防止过大过小。
如果降压后飞边增厚,可酌情减少加料量或加大流胶槽。
(压力下冷却后出模)。
SMC模压常见缺陷、原因与解决办法

摆料方式不佳或因使用贮存过期熟料造成 ●改善摆料的方式,并使用未过期的熟料 流动不足
可能发生原因
改善对策
熟衬重量过低 ●增加熟料重量直到材料填满模边 模边少数部 合模前熟料散溢 ●熟料摆放位置要更注意或熟料放少些 份未填满 剪切边(Sheal Adge)间隙太大,使熟料发 ●用焊接或镀铬方法减少剪切边间隙 生散溢现象 有模 凹边 凸已 点填 发满 生但 熟料重量过低 空气无法由模具间逸出 加强肋(Rib)或凸栓(Boss)部份有空气存在 致模压时气体无法逸出 ●增加熟料重量 ●重新安排摆料方式,避免空气捕捉之缺点。或使 熟料在流动时,可将成形品内之空气驱除 ●适当处钻引机,使空气排出,若情况不严重,增 加压力,可能有帮助 ●事先压缩去除熟料及熟料间的空气 硬 化 后 的 表 面 呈 现 半 圆 状 凸 起 SMC熟料中及熟料层间存在的空气或气体 ●减少摆料面积或改变摆料方式使空气易于逸出
空气/苯乙烯混合气体存在于未填满部份, ●选用无包覆(trap)空气,流动时可驱走空气之熟料 模压件未完 被压缩后引起混合气体着火烧焦成形品 全填满之处 成型品的形状不适当 有暗棕色或 ●降低合模速度 黑烟表面 合模速度太快 ●改变摆料方式使模压时,气体容易逸出 摆料方式不当 离型不良,脱模不良 模温过低 硬化周期太短 苯乙烯单体挥发,造成部分硬化不完全 内脱模剂太少 成形品难以 取出,在若 新模具或长时间未使用致使模具不能开 干处材料粘 模具表面不良 在模具上表 摆料面积太大,流动距离太小,致使空气无 面有胞孔或 法逸出而包覆的空气延缓硬化反应 疤痕 不正确的顶出系统 模具有倒角(Undercut) SMC的收缩性能 ●增高模温 ●增长硬化时间 ●直至使用时,保持SMC熟料密封于薄膜中 ●配方中增加内脱模剂量 ●在最初数次模压时,涂用外部脱模剂 ●改善模具面 ●减少摆料面积,且在较大摆料上面增放小摆料 ●检查水平顶出动作,在加强肋(Rib) 区域或添顶出梢以防止卡住 ●使用不同收缩等级的熟料 裂痕(Crack) 熟料熟成粘度过低,流动时,树脂与玻璃纤 维分离 ●增设熟料熟成粘度
模压成型工艺实验报告现象分析总结怎么写

模压成型工艺实验报告现象分析总结怎么写引言模压成型工艺作为一种常见的加工方法,广泛应用于塑料制品、橡胶制品等领域。
本文通过对模压成型工艺实验的现象分析总结,旨在探讨实验中可能出现的问题和解决方法,以期提高生产效率和产品质量。
实验条件描述实验中我们选用了标准的模压设备和塑料原料,设定了适当的温度、压力和时间参数进行成型。
模具设计合理,包括了产品的形状、尺寸以及凹凸平整度等要求。
实验过程中,我们发现了以下几个现象:1.成型不完整:部分产品出现了成型不完整的情况,主要表现为产品表面凹凸不平或者有空洞存在。
2.产品变形:有些产品成型后发生了形状变形,与设计要求不符,造成产品无法使用。
3.色差问题:成型后的产品出现了一些色差,与预期颜色不一致。
现象分析成型不完整成型不完整的现象可能由以下原因引起:1.模具问题:模具表面存在划痕、损伤等情况,导致产品表面不平整。
2.温度设置不当:温度过高或过低都会影响塑料的流动性,导致成型不完整。
3.压力不均匀:压力分布不均匀会造成部分区域成型不完整,出现空洞。
解决方法: - 定期检查模具的表面情况,及时保养和更换受损模具。
- 调整温度至适宜范围内,确保塑料材料可以均匀流动。
- 调整压力均匀分布,避免空洞产生。
产品变形产品变形可能是由以下原因引起:1.冷却不均匀:产品在冷却阶段受到外部环境温度影响不均匀,导致变形。
2.材料质量:原料质量差、成分不均匀等因素可能导致产品变形。
解决方法: - 调整冷却设备,保证产品整体受热冷却均匀。
- 定期检查原料质量,选用优质原料,并保持原料成分稳定。
色差问题产品出现色差问题可能由以下原因引起:1.原料选择问题:选用了不同批次或不同品牌的原料可能导致颜色不一致。
2.温度控制:温度波动大或不稳定会影响颜色的稳定性。
解决方法: - 统一选用同一批次、同一品牌的原料,确保颜色一致。
- 稳定温度控制在设定值范围内,避免温度波动。
总结通过对模压成型工艺实验中出现的成型不完整、产品变形以及色差问题进行分析,我们可以看出,影响成型质量的因素是多方面的,需要从多个角度进行改进和优化。
某公司橡胶模压制品常见缺陷及解决方法

橡胶模压制品常见缺陷及解决方法喷霜混炼胶或硫化胶内部的液体或固体配合剂因迁移而在橡胶制品表面析出形成云雾状或白色粉末物质的现象。
这是由于硫、石蜡、某些防老剂、软化剂的使用量超出了它们在橡胶中的溶解度而引起的。
为防止喷霜,上述各种配合剂用量要适当,对常见的硫黄喷霜可采用不溶性硫黄加以防止。
在橡胶中适当加入松焦油,液体古马隆等可增加胶料对上述配合剂的溶解度,以减少喷霜现象。
喷霜-定义和由来喷霜又名喷出(blooming),是橡胶加工过程中常见的质量问题,它是指未硫化胶或硫化胶中所含的配合剂迁移到表面并析出的现象。
有时,这种喷出物呈霜状结晶物,故习惯上称“喷霜”。
较多见的喷霜物为硫,因为硫黄是通用橡胶中应用最广泛的硫化剂,且在橡胶中的溶解度低因而容易产生喷霜。
其实从喷出物外观来看,也未必都呈霜状,也有呈油状(软化剂、增塑剂)或粉粒状(多为填充剂、防老剂、促进剂等)的物质喷出,甚至炭黑喷出也有所见。
喷霜-防霜剂硅胶也会有喷霜现象,采用双二四硫化剂(通常用在挤出成型工艺)高温分解后会产生低分子量的酸性物质,其与硅橡胶不相容,在存放过程中会转移到硅胶表面结晶从而出现喷霜。
防霜剂主要成分为碱性物质,通过酸碱中和反应来达到防霜的目的。
高硬度的硅胶往往加入比较多的内脱模剂,遇水也会喷白,水的酸性对此有遏制作用硅橡胶模具制作方法及注意事项模具是快速模具里的一种最为简单的方法,一般是用硅胶将RP原型进行复模,但寿命很短,只有10-30件左右!他具有很好的弹性和复制性能,用硅橡胶复制模可不用考虑拔模斜度,不会影响尺寸精度,有很好的分割性,不用分上下模可直接进行整体浇注。
再沿预定的分模线进行切割取出母模就可以了!室温硫化硅橡胶又分为加成型和缩合型两种!原料及配方采用专用模具硅橡胶,该品系以双包装形式出售,A组份是胶料,B组份是催化剂。
配制时要考虑室温、模具的强度和硬度,以此来确定AB组份的重量配制比例。
室温在20-25度时,A:B=100:1.5。
橡胶制品外观缺陷及解决方案

橡胶制品外观缺陷及解决方案篇一:橡胶模压制品常见缺陷及解决方法喷霜混炼胶或硫化胶内部的液体或固体配合剂因迁移而在橡胶制品表而析出形成云雾状或白色粉末物质的现象。
这是由于硫、石蜡、某些防老剂、软化剂的使用量超出了它们在橡胶中的溶解度而引起的。
为防止喷霜,上述各种配合剂用量要适当,对常见的硫黄喷霜可采用不溶性硫黄加以防止。
在橡胶中适当加入松焦油,液体古马隆等可增加胶料对上述配合剂的溶解度,以减少喷霜现彖。
喷霜-定义和由来喷霜又名喷出(blooming),是橡胶加工过程中常见的质量问题,它是指未硫化胶或硫化胶中所含的配合剂迁移到表面并析岀的现彖。
有时,这种喷岀物呈霜状结晶物,故习惯上称“喷霜”。
较多见的喷霜物为硫,因为硫黄是通用橡胶中应用最广泛的硫化剂,且在橡胶中的溶解度低因而容易产生喷霜。
其实从喷出物外观来看,也未必都呈霜状,也有呈油状(软化剂、增塑剂)或粉粒状(多为填充剂、防老剂、促进剂等)的物质喷岀,甚至炭黑喷出也有所见。
喷霜-防霜剂硅胶也会有喷霜现象,采用双二四硫化剂(通常用在挤出成型工艺)高温分解后会产生低分子量的酸性物质,其lword版与硅橡胶不相容,在存放过程中会转移到硅胶表面结晶从而出现喷霜。
防霜剂主要成分为碱性物质,通过酸碱中和反应来达到防霜的目的。
高硬度的硅胶往往加入比较多的内脱模剂,遇水也会喷白,水的酸性对此有遏制作用硅橡胶模具制作方法及注意事项模具是快速模具里的一种最为简单的方法,一般是用硅胶将RP原型进行复模,但寿命很短,只有10-30件左右!他具有很好的弹性和复制性能,用硅橡胶复制模可不用考虑拔模斜度,不会影响尺寸精度,有很好的分割性,不用分上下模可直接进行整体浇注。
再沿预定的分模线进行切割取出母模就可以了!室温硫化硅橡胶又分为加成型和缩合型两种!原料及配方采用专用模具硅橡胶,该品系以双包装形式岀售,A组份是胶料,B组份是催化剂。
配制时要考虑室温、模具的强度和硬度,以此来确定AB组份的重量配制比例。
模压制品缺陷及解决办法
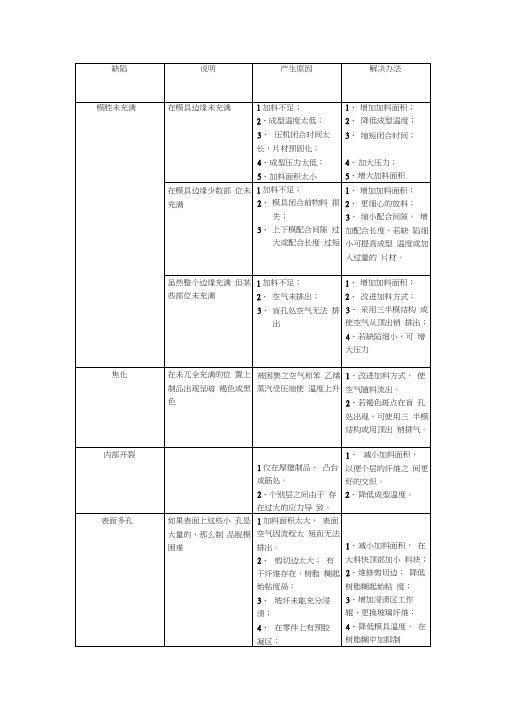
6、增加SMC片材熟
7、零件固化不完
化程度;
全。
7、增加固化周期或 升高模具温度。
在厚制品的表面上
1、在特厚制品中,
1、减小加料面积,
有半圆形鼓起
内应力使个别层间
使各层纤维更好的
扯开;
交织,降低固化温度
2、沿熔接线存在薄
或延长固化时间;
弱区;
2、改变加料方式缺陷
说明
产生原因
解决办法
模腔未充满
在模具边缘未充满
1加料不足;
2、成型温度太低;
3、压机闭合时间太 长,片材预固化;
4、成型压力太低;
5、加料面积太小
1、增加加料面积;
2、降低成型温度;
3、缩短闭合时间;
4、加大压力;
5、增大加料面积
在模具边缘少数部 位未充满
1加料不足;
2、模具闭合前物料 损失;
3、上下模配合间隙 过大或配合长度 过短
2、降低模压温度:减缓聚 合,降低放热温度。
3、加入惰性填料:降低单 位体积内活性基含量,减 缓放热。
4、加入韧性树脂:降低活 性,增加韧性。
5、减少苯乙烯用量:减少 收缩,降低放热温度。
富树脂(玻纤不足)区, 因树脂集中而造成的应 力,即使是中等活性树脂 也会出现裂纹。
2、降低成型温度。
表面多孔
如果表面上这些小 孔是大量的,那么制 品脱模困难
1加料面积太大, 表面空气因流程太 短而无法排出。
2、剪切边太大; 有干纤维存在,树脂 糊起始粘度咼;
3、玻纤未能充分浸 渍;
4、在零件上有预胶 凝区;
1、减小加料面积, 在大料快顶部加小 料块;
2、维修剪切边; 降低树脂糊起始粘 度;
橡胶模压制品常见缺陷及解决方法

喷霜混炼胶或硫化胶内部的液体或固体配合剂因迁移而在橡胶制品表面析出形成云雾状或白色粉末物质的现象。
这是由于硫、石蜡、某些防老剂、软化剂的使用量超出了它们在橡胶中的溶解度而引起的。
为防止喷霜,上述各种配合剂用量要适当,对常见的硫黄喷霜可采用不溶性硫黄加以防止。
在橡胶中适当加入松焦油,液体古马隆等可增加胶料对上述配合剂的溶解度,以减少喷霜现象。
喷霜-定义和由来喷霜又名喷出(blooming),是橡胶加工过程中常见的质量问题,它是指未硫化胶或硫化胶中所含的配合剂迁移到表面并析出的现象。
有时,这种喷出物呈霜状结晶物,故习惯上称“喷霜”。
较多见的喷霜物为硫,因为硫黄是通用橡胶中应用最广泛的硫化剂,且在橡胶中的溶解度低因而容易产生喷霜。
其实从喷出物外观来看,也未必都呈霜状,也有呈油状(软化剂、增塑剂)或粉粒状(多为填充剂、防老剂、促进剂等)的物质喷出,甚至炭黑喷出也有所见。
喷霜-防霜剂硅胶也会有喷霜现象,采用双二四硫化剂(通常用在挤出成型工艺)高温分解后会产生低分子量的酸性物质,其与硅橡胶不相容,在存放过程中会转移到硅胶表面结晶从而出现喷霜。
防霜剂主要成分为碱性物质,通过酸碱中和反应来达到防霜的目的。
高硬度的硅胶往往加入比较多的内脱模剂,遇水也会喷白,水的酸性对此有遏制作用硅橡胶模具制作方法及注意事项模具是快速模具里的一种最为简单的方法,一般是用硅胶将RP原型进行复模,但寿命很短,只有10-30件左右!他具有很好的弹性和复制性能,用硅橡胶复制模可不用考虑拔模斜度,不会影响尺寸精度,有很好的分割性,不用分上下模可直接进行整体浇注。
再沿预定的分模线进行切割取出母模就可以了!室温硫化硅橡胶又分为加成型和缩合型两种!原料及配方采用专用模具硅橡胶,该品系以双包装形式出售,A组份是胶料,B组份是催化剂。
配制时要考虑室温、模具的强度和硬度,以此来确定AB组份的重量配制比例。
室温在20-25度时,A:B=100:1.5。
室低时(但不能低于10度)则适当增加B组份0.1-0.3份。
- 1、下载文档前请自行甄别文档内容的完整性,平台不提供额外的编辑、内容补充、找答案等附加服务。
- 2、"仅部分预览"的文档,不可在线预览部分如存在完整性等问题,可反馈申请退款(可完整预览的文档不适用该条件!)。
- 3、如文档侵犯您的权益,请联系客服反馈,我们会尽快为您处理(人工客服工作时间:9:00-18:30)。
表面波纹
在与流动方向成直 角长的。垂直的溥壁 表面上产生波纹,或 由于其它不利的流 动条件(壁厚差大) 可能产生的不规则 表面波纹
制品复杂设计妨碍 材料均匀流动。
在大多数情况下不 能消除,但可以用下 列方法改进:增加压 力;改变模具设计; 改换装料位置;使用
LPA或LSA。
缩孔标记
在表面或筋,凸起部 背面的凹陷(发亮或 发暗点)
1、 按模具设计介绍 的方法改进;
2、 提高模具温度;
3、 加大加料面积, 缩短流程;
4、 改进模具导向。
预成型胚制品常见缺陷及解决方法
缺陷
说明
可能的原因
解决方法和建议
起泡
表面上的半圆形 鼓起(模塑物中的 离层)
固化不完全,泡延伸的范 围较大。
延长模压时间,提高引发 剂用量。
湿气、溶剂、被困集的空 气膨胀或烝发。
1加料不足;
2、 模具闭合前物料 损失;
3、 上下模配合间隙 过大或配合长度 过短
1、 增加加料面积;
2、 更细心的放料;
3、 缩小配合间隙。 增加配合长度,若缺 陷细小可提高成型 温度或加入过量的 片材。
虽然整个边缘充满 但某些部位未充满
1加料不足;
2、 空气未排出;
3、 盲孔处空气无法 排出
1、 增加加料面积;
2、 降低模具温度;
3、 延长固化时间;
4、 降低树脂糊粘度, 在浸渍区安装更多 的工作辊,是浸渍辊 加热,更换玻璃纤 维;
5、 更仔细低清理模 具内毛刺;
6、 增加SMC片材熟 化程度;
7、 增加固化周期或 升高模具温度。
在厚制品的表面上 有半圆形鼓起
1、 在特厚制品中, 内应力使个别层间 扯开;
成型过程中不均匀 收缩。
1、 配方中使用LPA或LSA;
2、 增加上下模温差
5-6C;
3、 加大压力,缩短 纤维短切丝长度,改 变模具设计,变换加 料位置,采用狭小的 上下模配合间隙。
模具剪切边磨损
在施力方向金属损 伤
导柱不够精确或太 弱。
1、 提供精确的模具 导向;
2、 强化导柱;
3、改进加料位置, 以使侧推力最小。
片状模塑料制品的缺陷及解决办法
缺陷
说明
产生原因
解决办法
模腔未充满
在模具边缘未充满
1加料不足;
2、 成型温度太低;
3、 压机闭合时间太 长,片材预固化;
4、 成型压力太低;
5、 加料面积太小
1、 增加加料面积;
2、 降低成型温度;
3、 缩短闭合时间;
4、 加大压力;
5、 增大加料面积
在模具边缘少数部 位未充满
2、 改进加料方式;
3、 采用三半模结构 或使空气从顶出销 排出;
4、 若缺陷细小,可 增大压力
焦化
在未兀全充满的位 置上制品出现呈暗 褐色或黑色
被困集之空气和苯 乙烯蒸汽受压缩使 温度上升
1、 改进加料方式, 使空气随料流出。
2、 若褐色斑点在盲 孔处出现,可使用三 半模结构或用顶出 销排气。
内部开裂
表面发暗
表面没有足够的光 泽
1、 压力太低;
2、 模温度太低;
3、 模具表面不理 想。
1、 加大压力;
2、 提高模具温度;
3、 模具镀铬。
流动线
表面上有局部波纹
1、 模具闭合不当或 损坏;
2、 模具温度太低;
3、 纤维在极长流程 或不利流程中发生 取向;
4、 由于在一边缘过 度的压力降低引起 模具移动。
3、 用增加加料面积 的方法缩短流程;
(1) 去除切口;
(2) 增加顶出面
积;
(3) 增加顶出销数 量;
(4)见“粘模”项; (5)增加固化时间
或温度。
粘模
制品难以脱模,材料 某些部位粘在模具 上
1、 模具温度太低;
2、 固化时间太短;
3、 料卷打开外包装 时间太长;
4、 使用新模具或长 期未用的模具又未 经开模处理;
2、 沿熔接线存在薄 弱区;
3、 极长的流程存在 某方向上强度的下 降(纤维取向);
4、 脱模过程中损坏
(1) 形成切口;
(2) 顶出销面积过 大;
(3) 顶出销数量不 够;
(4) 粘模;
(5) 未完全固化
1、 减小加料面积, 使各层纤维更好的 交织,降低固化温度 或延长固化时间;
2、 改变加料方式, 增加加料面积缩短 流程;
5、 用防渗透膜包裹SMC料,成型时不可 备料过多;
6、、增大片材熟化程 度;
7、 增加成型压力;
8、 调整配方,减少 用量。
鼓泡
在已固化制品表面 半圆形鼓起
1、 片材困集空气;
2、 温度太高;
3、 固化时间太短;
4、 有干纤维存在;
5、 模内有毛刺;
6、SMC太软;
7、 零件固化不完 全。
1、 用预压法除去层 间空气,减小加料面 积,以利于空气的排 出;
预成型胚充分干燥,避免 树脂中的气泡。
裂纹
树脂细微开裂,可 从表面伸向内部 甚至贯穿整个零 件。
咼不饱和度的树脂固化 快,放热温度咼。在刚性 树脂中固化收缩和热膨 胀,即便在玻璃纤维均匀 填充区域也会引起裂纹。
1降低引发剂浓度:稍微 延长固化时间,以降低放 热温度。
5、 模具表面太粗糙
1、 增加模具温度;
2、 延长固化时间;
3、 使用前料卷要始 终保持密封;
4、 头几模使用外脱 模剂;
5、 表面抛光。
已固化的制品难以 脱模,在某些部位材 料粘在模具上,同时 制品表面出现微孔 和伤痕
加料面积过大,空气 未能排出,而空气阻 碍固化。
减小加料面积,在大 料块顶部加小料块间由于 存在过大的应力导 致。
1、 减小加料面积, 以便个层的纤维之 间更好的交织。
2、 降低成型温度。
表面多孔
如果表面上这些小 孔是大量的,那么制 品脱模困难
1加料面积太大, 表面空气因流程太 短而无法排出。
2、 剪切边太大; 有干纤维存在,树脂 糊起始粘度咼;
3、 玻纤未能充分浸 渍;
1、 减小加料面积, 在大料快顶部加小 料块;
2、 维修剪切边; 降低树脂糊起始粘 度;
3、 增加浸渍区工作 辊,更换玻璃纤维;
4、 在零件上有预胶 凝区;
5、SMC料发干;
6、SMC料发软;
7、 压力不足;
8、SMC中ZnSt用量
过大。
4、 降低模具温度, 在树脂糊中加抑制 剂;
模具磨损
在已固化制品表面 上有暗黑斑点
模具磨损
模具镀烙
翘曲
制品稍有翘曲
1、 由于在硬化和冷 却过程中的收缩产 生翘曲;
2、 一半模具比另一 半模具热的多。
1、 制品在夹具中冷 却。加LPA或LSA。
2、 减小模具温差。
制品严重翘曲
由于特别长的流程 引起玻璃纤维取向, 产生翘曲。
增加加料面积,缩短 流程。在配方中加入