IE的分析方法和工具
IE动作分析资料案例

IE动作分析资料案例IE是指工业工程(Industrial Engineering),是一门涉及到工业系统设计、改进和优化的学科。
IE动作分析是IE领域的一项重要工具,用于分析和优化工人在工作中的动作和姿势,以改善工作效率和工作条件。
下面将通过一个实际案例来说明IE动作分析的应用。
案例背景:工厂的一个装配线上,工人负责将零件组装成最终产品。
该装配线的生产效率较低,工人在组装过程中常常需要屈膝、弯腰等操作,导致工人疲劳度较高,工作效率受到影响。
因此,工厂决定使用IE动作分析方法来改善工人的工作动作和姿势,以提高装配线的生产效率。
1.观察和记录工人的动作和姿势:在装配线上观察工人的操作过程,记录工人的各个动作和姿势,包括屈膝、弯腰、伸腿等动作。
2.量化工作动作和姿势:使用IE工具进行工作动作和姿势的量化。
例如,使用动作时间研究方法测量每个动作的时间,使用人体测量仪测量工人在不同姿势下的肌肉活动度和疲劳度。
3.分析工作动作和姿势的问题:根据量化结果,分析工作动作和姿势存在的问题。
例如,可能发现工人在一些动作中花费了过多的时间,或者一些姿势对工人的肌肉活动度造成了负面影响。
4.设计改进措施:根据分析结果,设计改进措施来优化工作动作和姿势。
例如,通过重新安排工作站和工作布局,减少工人弯腰和屈膝的操作。
另外,可考虑引入辅助工具或设备来减轻工人的负担,提高工作效率。
5.实施改进措施并测量效果:将设计的改进措施应用到装配线上,并进行测量和评估。
比较改进前后的工作效率、工人疲劳度等指标,评估改进的效果。
6.持续改进:根据实施效果,反馈给工人和管理层,并进行持续改进。
持续监测和评估工人的工作动作和姿势,寻找改进的机会,并进行相应的优化。
案例结果:通过IE动作分析与改进的方法,该工厂成功优化了装配线上工人的工作动作和姿势。
改进后,工人的弯腰和屈膝操作减少,节省了大量时间。
工人的疲劳度也明显降低,工作效率得到显著提高。
(IE工业工程)IE的分析方法及工具__标准工时、工作简化

IE 的分析方法及工具(3)__ 標準工時、工作簡化IE 的分析方法及工具( 3)八、標準時間標準時間又稱“標準工時”。
一個生產工廠,廠內生產部門有無建立標準工時,或標準工時的適用性,幾乎可衡量這個工廠的管理水準,因為管理落伍的工廠,對於工作人員的績效往往缺乏一種標準的衡量工具,而往往取法于主管的好惡,而標準工時的制訂,則可打破人為的偏差,對於績效的衡量建立在一個合理、公平的制度之下:(一)、標準時間的用途1. 作業方法的比較選擇對於不同的作業方法透過方法研究、時間研究,可以選擇最好的作業方法。
2. 工廠佈置之依據有了產品,制程作了分析,每個作業制定了標準時間,即可測算每個作業(部門)的負荷,依據負荷測算所需的作業空間,可達到更為流暢的工廠佈置。
3. 可預估工廠負荷產量工廠空間有多大,制程上有了標準時間,即可測算工廠產能。
4. 生產計畫的基礎生產管制部門的生產計畫,因有了標準時間,可以更精確的做生產計畫,如在進度控制上有了問題,也可依標準時間來做人力調整。
5. 可作為人力增減之依據做何產品?計畫產量多少?工作日多少?每日計畫工作時間多少?有了上面的資訊再加上有了標準時間,即可計算所需的人力,也就可有準備的進行增補或調整。
6. 可作為新添機器設備的依據機器產能(標準時間換算)可得知生產量起伏時所需要之機器數量。
7. 流水線生產之平衡一條流水線,諸多工序,依各工序的標準時間來配置人力,使生產線平衡,流暢。
8. 可決定人工成本對製造成本及外加工之費用可依標準時間做基礎來估算。
9. 可作為效率分析的基礎在多少時間內,完成多少產品,有了標準時間,就可計算效率因有明確的計算得予提升。
10. 工作人員效率獎金計算基礎有標準時間,才可得正確合理之效率,效率的好壞在薪資的獎金上應予反應,可得激勵作用。
11. 減少管理依存度每日的工作績效透過計算,並反應在獎金上,易於激發工作人員自主自動的工作態度。
(二)、標準時間之意義生產方法可運用工種分析、工作研究等技法,並運用管理迴圈PDCA一直獲得改善,不斷的尋求最大效率,最低成本的做法,當然標準時間也就不斷的跟著做改變。
IE工程(七大手法)
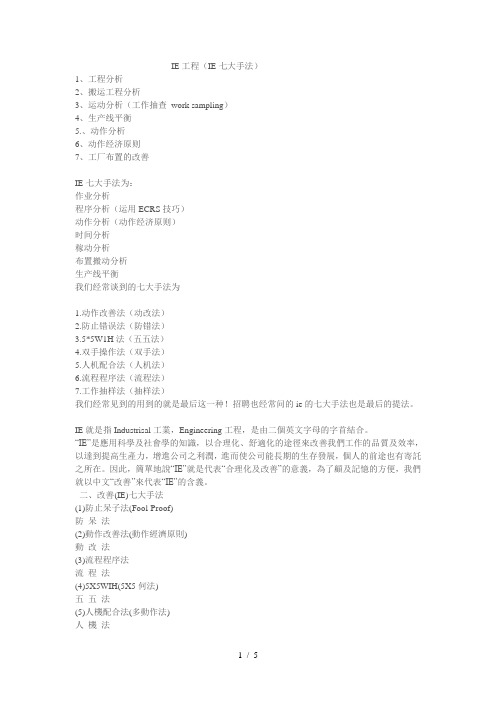
IE工程(IE七大手法)1、工程分析2、搬运工程分析3、运动分析(工作抽查work sampling)4、生产线平衡5.、动作分析6、动作经济原则7、工厂布置的改善IE七大手法为:作业分析程序分析(运用ECRS技巧)动作分析(动作经济原则)时间分析稼动分析布置搬动分析生产线平衡我们经常谈到的七大手法为1.动作改善法(动改法)2.防止错误法(防错法)3.5*5W1H法(五五法)4.双手操作法(双手法)5.人机配合法(人机法)6.流程程序法(流程法)7.工作抽样法(抽样法)我们经常见到的用到的就是最后这一种!招聘也经常问的ie的七大手法也是最后的提法。
IE就是指Industrisal工業,Engineering工程,是由二個英文字母的字首結合。
“IE”是應用科學及社會學的知識,以合理化、舒適化的途徑來改善我們工作的品質及效率,以達到提高生產力,增進公司之利潤,進而使公司能長期的生存發展,個人的前途也有寄託之所在。
因此,簡單地說“IE”就是代表“合理化及改善”的意義,為了顧及記憶的方便,我們就以中文“改善”來代表“IE”的含義。
二、改善(IE)七大手法(1)防止呆子法(Fool-Proof)防呆法(2)動作改善法(動作經濟原則)動改法(3)流程程序法流程法(4)5X5WIH(5X5何法)五五法(5)人機配合法(多動作法)人機法(6)雙手操作法雙手法(7)工作抽查法抽查法改善(IE)七大手法與品管(QC)七大手法之差別“品管(QC)七手法”較著重於對問題的分析與重點的選擇,但對如何加以改善則較少可應用。
“改善(IE)七手法”較著重於客觀詳盡瞭解問題之現象,以及改善方法的應用,以期達到改善的目標。
有了“改善(IE)七手法”正可彌補品管(QC)手法的缺陷而達到相輔相成之效果,使得改善的效果更為落實也更容易實現。
同時最重要的是改善(IE)七手法亦可單獨使用,因其本身具有分析、發掘問題的技巧之故。
防呆法(Fool-Proof)一、目的認識“防呆法”的意義,及學習如何應用“防呆法”的原理於我們的工作上,以避免工作錯誤的發生,進而達到“第一次就把工作做對”之境界。
ie七大手法心得
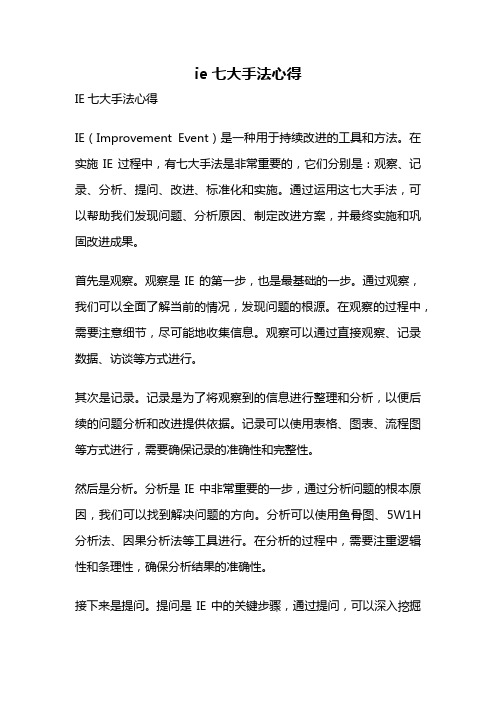
ie七大手法心得IE七大手法心得IE(Improvement Event)是一种用于持续改进的工具和方法。
在实施IE过程中,有七大手法是非常重要的,它们分别是:观察、记录、分析、提问、改进、标准化和实施。
通过运用这七大手法,可以帮助我们发现问题、分析原因、制定改进方案,并最终实施和巩固改进成果。
首先是观察。
观察是IE的第一步,也是最基础的一步。
通过观察,我们可以全面了解当前的情况,发现问题的根源。
在观察的过程中,需要注意细节,尽可能地收集信息。
观察可以通过直接观察、记录数据、访谈等方式进行。
其次是记录。
记录是为了将观察到的信息进行整理和分析,以便后续的问题分析和改进提供依据。
记录可以使用表格、图表、流程图等方式进行,需要确保记录的准确性和完整性。
然后是分析。
分析是IE中非常重要的一步,通过分析问题的根本原因,我们可以找到解决问题的方向。
分析可以使用鱼骨图、5W1H 分析法、因果分析法等工具进行。
在分析的过程中,需要注重逻辑性和条理性,确保分析结果的准确性。
接下来是提问。
提问是IE中的关键步骤,通过提问,可以深入挖掘问题的本质,找到更全面和深入的解决方案。
在提问的过程中,需要注意问题的准确性和针对性,避免问题的模糊和歧义。
然后是改进。
改进是IE的核心步骤,通过制定改进方案和实施改进措施,我们可以解决问题,提高工作效率和质量。
改进需要结合实际情况,制定切实可行的方案,并逐步实施和验证。
在改进的过程中,需要注意改进方案的可行性和可持续性,避免过于理想化或片面化。
接着是标准化。
标准化是为了确保改进成果能够持续下去,通过制定标准和规范,我们可以规范工作流程,保证工作的稳定性和可持续性。
标准化需要考虑到各种因素,如人、机、料、法、环等,确保标准的全面性和有效性。
最后是实施。
实施是IE的最终目标,通过实施改进方案和标准化措施,我们可以将改进成果转化为实际的效益。
实施需要全员参与,确保改进措施的顺利进行和落地。
IE的分析方法及工具

IE的分析方法及工具IE(Industiral Engineering),即工业工程,是一种研究工业生产中如何最优地运用人力、物力、财力等资源,以提高生产效益的学科。
在进行IE分析时,可以使用多种方法和工具来辅助。
以下是一些常用的IE分析方法及相关工具的简要介绍。
1.流程分析方法及工具:流程分析方法用于分析和优化工业生产过程中的流程。
常用的工具包括流程图、流程价值分析(PVA)、时间和动作研究(TAR)、价值流图(VSM)等。
流程图用于展示工业生产过程中的各个环节和关联性;PVA用于评估每个流程环节的价值并确定可能的改进点;TAR用于观察和分析工人在生产过程中的时间和动作,并提出相应的改进意见;VSM用于展示整个价值流程并识别可能的浪费环节。
2.工艺分析方法及工具:工艺分析方法用于分析和改善工业生产过程中的工艺。
常用的工具包括工艺路线图、标准操作程序(SOP)、工艺能力分析(PCA)等。
工艺路线图用于展示产品的生产流程和工艺要求;SOP用于明确每个工艺步骤的操作规范;PCA用于评估工艺的能力和稳定性,并提供改进建议。
3.人力分析方法及工具:人力分析方法用于分析和优化工业生产中的人力资源。
常用的工具包括时间研究、任务分析、工作分配、人力需求预测等。
时间研究用于测量工人在完成特定任务时所需的时间,并为人力资源的规划和管理提供依据;任务分析用于分析和描述每个工作岗位的任务要求和职责;工作分配用于合理分配人力资源以确保工作效率和质量;人力需求预测用于预测未来生产需求并相应地调整人力规模。
4.设备分析方法及工具:设备分析方法用于分析和改善工业生产中的设备使用效率和可靠性。
常用的工具包括设备维修与保养(PM)、总有效设备利用率(OEE)、故障模式和影响分析(FMEA)等。
设备维修与保养用于保障设备的正常运行和寿命延长;OEE用于评估设备的综合利用率,并提供可能的改善点;FMEA用于分析设备故障的模式和影响,并提出相应的预防和改进措施。
IE的分析方法及工具

IE的分析方法及工具概述Internet Explorer(IE)是一款常见的网络浏览器,广泛应用于Windows操作系统。
为深入了解IE的性能和行为,开发者和分析师需要运用一些特定工具和方法来进行IE的分析。
本文将介绍一些常用的IE分析方法和工具,帮助读者更好地了解IE的性能和调试过程。
1. 内置工具1.1 Internet Explorer F12开发者工具Internet Explorer F12开发者工具是IE浏览器内置的一项功能强大的调试工具。
通过按下F12键或在菜单栏中选择“开发者工具”,开发者可以打开该工具。
F12开发者工具内部有多个选项卡,每个选项卡提供不同的调试和分析功能。
以下是几个常用的选项卡:•元素(Elements):用于查看和编辑当前网页的HTML结构。
•控制台(Console):显示JS脚本的运行日志和错误信息。
•网络(Network):跟踪和分析页面加载过程中的网络请求和响应。
•性能(Performance):用于分析页面的性能指标,如加载时间、CPU和内存使用情况等。
1.2 Windows事件查看器Windows事件查看器是Windows操作系统的一个内置工具,可用于查看和分析系统事件日志。
对于IE的分析来说,事件查看器是一个有用的资源。
通过事件查看器,用户可以查看IE启动、崩溃和其他相关事件的日志。
这些日志可以帮助分析师快速定位问题和调试IE的故障。
2. 第三方工具2.1 FiddlerFiddler是一款流行的网络调试工具,用于捕获和分析HTTP网络流量。
它可以在Windows和Mac上运行,并提供了丰富的功能,包括网络流量截获、修改请求和响应、模拟网络问题等。
Fiddler对于IE的分析非常有用,特别是在调试前端与后端交互时。
通过Fiddler,用户可以查看和分析IE浏览器与服务器之间的请求和响应,从而定位网络问题和性能瓶颈。
2.2 Process ExplorerProcess Explorer是一款Windows系统进程查看工具,由Microsoft官方提供。
IE改善方法与工具解析:从制造到效率提升
IE改善方法与工具解析:从制造到效率提升
IE改善的具体方法和工具有很多种,以下是一些常见的IE改善方法和工具:1.程序分析:通过分析整个制造程序,以及产品或材料或人的流程、布置与
路线、闲余能量等,发现存在的问题和改善点,从而优化制造程序。
2.操作分析:通过分析操作人员的操作方法和动作,发现存在的问题和浪费,从而优化操作方法,提高效率和生产力。
3.动作分析:通过分析操作人员的动作,发现不合理的动作和浪费,从而优
化动作,提高效率和生产力。
4.工艺流程查一查:通过对生产制程和工作流程的全过程进行分析,发现无
价值和不必要的环节,从而优化工艺流程,提高效率和生产力。
5.时间研究:通过对操作人员完成工作所需时间的测定和分析,发现存在的
问题和浪费,从而制定出科学合理的作业标准和时间定额。
6.工作抽样:通过对操作人员的工作时间和空闲时间的抽样调查,发现存在
的问题和浪费,从而制定出科学合理的工作标准和时间标准。
7.预定时间标准:通过MOD法等预定时间标准方法,对操作人员进行科学
的评估和测定,从而制定出科学合理的操作标准和时间定额。
8.ECRS(删除、合并、重排、简化)工具:通过对工艺流程进行优化和重组,减少浪费和不必要的环节,提高效率和生产力。
综上所述,IE改善的具体方法和工具有很多种,需要根据实际情况选择合适的方法和工具,从而实现制造过程的科学管理和效率提升。
IE分析方法和常用计算公式
IE分析⽅法和常⽤计算公式⼀.流⽔线优化部分:1.输送带的pitch 时间 = 整⽇的上班时间/⽇产量*(1+不良率)2.输送带的速度 = 记号间隔距离 /输送带的pitch 时间3.⽇产量 = 整⽇的上班时间/实际际cycle 时间(瓶颈站的作业时间)4.效率 = 投⼊cycle 时间/实际cycle 时间 = 第⼀站的作业时间/最后⼀站5.的作业时间(当然也可⽤瓶颈站的作业时间来算, 不过观察最后⼀站总是较简单、实际)6.在流⽔线上的在制品数量就= ( 最后⼀站的作业时间 - 第⼀站的作业时间 ) * (整⽇的上班时间/最后⼀站的作业时间)7. 稼动率 = 在作业的时间 / 整⽇的上班时间(所谓稼动就是流⽔线上有效的⼯作)⼆.流⽔线设计部分: 1.先求节拍时间 C= 2.⼯站理论值 N=3.评价流⽔线效率=4.选择作业分配原则:A 按后续作业量的多少来安排作业(第⼀规则遇到问题时采⽤第⼆规则)B 按作业时间最长安排作业(若作业最长时间相同,任选其⼀安排作业) 三.⽣产线平衡部分:1.⽣产线平衡率=各⼯序时间总和/(⼈数×CT )×100%=∑ti /(⼈数×CT )×100%2.⽣产线平衡损失率=1-⽣产线平衡率 3、⽣产线平衡改善的⽅法⼯时长的⼯序的改善⽅法:A .细分作业内容,将⼀部分作业转移⾄其他⼯序B .改善作业本⾝C .谋求⼯序机械化D .通过改良,增⼤机器的运作能⼒E .增加作业⼈数F .调配经验丰富,作业技能⾼的熟练作业⼈员G .“瓶颈”⼯序能⼒不⾜的部分,利⽤加班完成,或⽤其他⽅法完成⼯时短的⼯序的改善⽅法:A .细分作业内容,将作业转移⾄其他⼯序,取消该⼯序B .从其他⼯序转移来部分作业内容,增加作业量C .将同是作业⼯时短的⼯序合并起来D .在不影响后⼯序的前提下,采⽤继续集中作业⽅式 4、⽣产线平衡分析步骤决定分析对象和要达到的⽬标取得相关⼈员的理解和帮助分解各⼯序的作业单元测定每个作业单元的时间实际修正测定⼯时求出每个线点时间作成线点运⾏表每天的⽣产时间每天的计划产量完成作业所需的时间总量 T 节拍 C 完成作业所需的时间总量 T实际⼯站数⽬N ×节拍C对⽣产中的⽣产线进⾏分析时,依下述步骤进⾏:1)对⽣产线的各⼯程顺序(作业单位)予认定,并填⼊⽣产流动平衡表中2)测算各⼯序实质作业时间以DM (Decimal Minute )为单位记⼊平衡表内(1⼈实质时间栏)注:1DM=分=秒3)清点各⼯序作业⼈数,并记⼊⼈员栏内4)1⼈实质作业时间÷⼈数 = 分配时间,记⼊时间栏5)依此分配时间划出柱状图或曲线图6)在分配的实质时间最⾼的这⼀⼯序顶点横向划⼀条点线7)计算不平衡损失上⾯斜线部分的总和即为不平衡损失的总和 T (Lose )=Σ|Tm -Ti|不平衡损失=(最⾼的DM×合计⼈数)-(各⼯序时间的合计)如下图8)⽣产线平衡率⽣产线平衡率=—————————————— 9)⽣产线不平衡损失率=1-⽣产线平衡率10)如使⽤输送带之动⼒传送,则应计算输送带的流动速度(M/时间单位)称为节拍时间,符号TC 。
IE的分析方法及工具
IE的分析方法及工具——(摘自林荣瑞先生著作《治理技术》章节)一、对IE的认识1.IE是以工程技术为基础,配合科学治理的技巧来发觉问题、解决问题、预防问题。
2.IE最终目的是经由治理的运作,使企业能获得最大的利益,是故与成本或经济效益有关,包括制度、作业方法、机器、模具、夹具均应予把握并加以改善。
3.IE是一门应用科学,其操作理论均要能符合实际的需要,是故IE工程师均应具备躯体力行的能力,而使理论与实务相得益彰,保证治理成效。
4.IE是运用重点治理的技巧,在任何问题上做重点突破。
5.美国IE协会(AIIE)对IE下的定义如下:IE是在工学之中以设计,改善,设定来综合人、材料、设备等系统的结合。
为了明示、推测、评判该系统所产生的结果而使用工学分析或设计原理与技法,并融合数学、自然科学、社会科学等专门知识与体会。
对上面的定义我们能够了解:IE是藉着设计、改善或设定人、料、机的工作系统,以求得到更高生产力的专门技术。
上面所提的“设计”是指制订新的系统。
“改善”是指把原有的系统修改得更完美更适合。
“设定”意指将“设计”或“改善”之系统,导入企业动作体系,并能够稳固的发挥。
6.IE(工业工程)在日本也被称为“生产技术”或“治理工学”。
7.IE 的基础也是最早的起源来自于“工作研究“,而”工作研究“的要紧构成是来自泰勒(F。
W。
TOYLOR1856—1915)的”时刻研究“与吉尔布雷斯(F。
B。
GILBRETH 1868—1924)的“动作研究”二者所构成。
8.现时期的工业工程师要紧的范畴大致如下:1.工程分析2.工作标准3.动作研究4.时刻研究5.时刻标准6.价值分析(V A)7.工厂布置8.运搬设计二、工作研究(OPERATION RESEARCH OR)1、工作研究的目的是人们藉着物料、机器、工具及工作方法而产出产品,而此产出的方法是否是:•生产过程最理想?•生产的工作方法最好?•机器及工具是否最适当?•物料是否最正确?工作研究以研究及分析现有的生产过程及方法,并能找出一个最佳生产方法的一种治理科学。
ie国际贸易理论基本分析工具
预算约束(Budget Strict)
➢特定时点下,消费者受到特定收入I旳约束 ➢预算线:表达消费者在特定收入约束下能
够消费旳两种商品旳多种组合。
➢预算线又称为消费可能性边界 (the Consumption Possibility Frontier)
➢Px*X + Py*Y=I
➢变形为: Y=I / Py – Px / Py * X
➢在特定旳PPF曲线旳限制下,企业追求收入 最大化旳行为是在该PPF曲线上寻找一种点 (一对X和Y旳产品组合)
企业旳最优选择点
PPF A
最优点 E
B
最优选择点
➢ 收入曲线与PPF曲线旳相切点,是企业旳最优选 择点。
➢ 符合限制条件,商品组合(X,Y)处于PPF曲线上, 而且同步处于一组收入曲线中离原点最远旳一条收入 曲线上。
➢表达要增长一定百
分比旳产品X旳产出
量时,需要以更大
旳百分比降低产品Y
旳产出,才干释放 出足够旳资源。
0
X
生产可能性曲线:酬劳递增
➢当边际成本递减, 也就是存在规模经
Y
济或者规模酬劳递
增时,PPF曲线是
一条凸向原点而且
斜率递减旳曲线。
➢表达为了增产X而
需要降低旳Y越来
越少。
X o
边际转换率(The Marginal Rate of Transformation)
➢不同旳商品旳生产技术上存在差别,使用 要素旳百分比不同。
➢例如说产品X相对于Y来说,使用更高旳K/L百 分比,这么当降低产品Y来释放资源以便增长 产品X旳产量时,释放出来K会被充分利用,而 L则可能过剩而产生生产效率低下旳成果
机会成本旳体现