精轧区设备
精轧机区设备标定规程
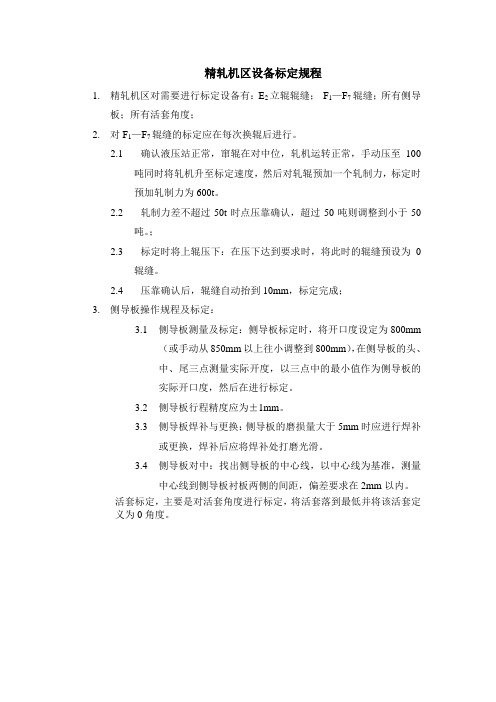
精轧机区设备标定规程
1.精轧机区对需要进行标定设备有:E2立辊辊缝;F1—F7辊缝;所有侧导
板;所有活套角度;
2.对F1—F7辊缝的标定应在每次换辊后进行。
2.1确认液压站正常,窜辊在对中位,轧机运转正常,手动压至100
吨同时将轧机升至标定速度,然后对轧辊预加一个轧制力,标定时
预加轧制力为600t。
2.2轧制力差不超过50t时点压靠确认,超过50吨则调整到小于50
吨。
;
2.3标定时将上辊压下:在压下达到要求时,将此时的辊缝预设为0
辊缝。
2.4压靠确认后,辊缝自动抬到10mm,标定完成;
3.侧导板操作规程及标定:
3.1侧导板测量及标定:侧导板标定时,将开口度设定为800mm
(或手动从850mm以上往小调整到800mm),在侧导板的头、
中、尾三点测量实际开度,以三点中的最小值作为侧导板的
实际开口度,然后在进行标定。
3.2侧导板行程精度应为±1mm。
3.3侧导板焊补与更换:侧导板的磨损量大于5mm时应进行焊补
或更换,焊补后应将焊补处打磨光滑。
3.4侧导板对中:找出侧导板的中心线,以中心线为基准,测量
中心线到侧导板衬板两侧的间距,偏差要求在2mm以内。
活套标定,主要是对活套角度进行标定,将活套落到最低并将该活套定义为0角度。
粗轧中精轧

机械制造业
机械制造业对精度要求较 高的金属零部件有很大需 求,这些零部件往往需要通 过粗轧和精轧工艺制造。 如齿轮、轴承等关键零件 都依赖于精密的轧制加工 工艺。
粗轧与精轧的发展趋势
自动化生产
粗轧与精轧工艺正朝着更高的自动化和 智能化发展,利用先进的控制系统实现 高效无人操作。
技术创新
新型轧机设备和工艺不断涌现,提高生 产效率、降低能耗,满足更高的材料性 能要求。
环保节能
粗轧与精轧工艺正朝着绿色、环保、节 能的方向发展,减少对环境的影响。
粗轧与精轧的工艺优化
优化设备性能
定期维护保养粗轧机和精轧机 设备,提升其运行效率和可靠 性,确保工艺稳定。
优化能源利用
采用节能技术,如余热回收利 用、智能控制等,降低能源消 耗,提高整体能源利用效率。
优化工艺参数
根据不同材料特性,调整轧制 温度、压下量和轧制速度等参 数,实现最佳轧制效果。
个人防护装备
确保员工佩戴劳动防护用 品,如安全帽、防护眼镜、 防护手套等,切实保护好自 身安全。定期检查维护,确 保防护装备处于可靠状态 。
应急预案管理
制定完善的应急预案,明确 各种可能发生的事故类型 和应对措施。定期组织应 急演练,提高员工的应急处 置能力,最大程度地减少事 故发生。
粗轧与精轧的人员培训
应用先进的在线检测技术, 如光学检测、超声波检测 等,实时监测和控制产品质 量。
粗轧与精轧的行业标准
1 标准体系
建立包括原材料、制造工艺、产品检测等方面的全面标 准体系,确保产品质量稳定可靠。
2 国内外标准
紧跟国内外行业标准的制定与更新,及时将最新标准引 入到生产和管理中。
3 测试方法
完善产品各项性能指标的测试方法,采用先进的检测设 备和手段,提高检测精度。
轧钢主设备

由于连铸机改变连铸板坯宽度的能力较小,不能满足热轧带钢轧机的各种宽度规格,由粗轧机的立辊根据热轧带钢轧机需要的各种宽度规格的板坯宽度进行控制。热轧带钢轧机发展了立辊轧机,定宽压力机等形式的板坯宽度侧压设备。
5、精轧机组
精轧机组是成品轧机,布置在粗轧机组中间辊道或热卷箱的后面,是带钢热连轧线的核心设备。精轧是决定产品质量的主要工序,带钢的力学性能主要取决于精轧机终轧温度和卷取温度。
2国内的情况
1978年12月投产的武汉钢铁公司1700mm热连轧机计算机系统,是我国引进的第一套带钢热连轧计算机控制系统热带轧机。1989年宝钢2050mm热连轧机的建成投产,使我国热轧宽带钢轧机的生产技术和技术装备又上了一个新的高度。
3带钢热连轧生产工艺流程
原料准备→称重→加热→除鳞→定宽→粗轧→(调头尾)→保温(补热)→剪头尾→除鳞→精轧→层流冷却→卷取→热轧卷(检查、打捆、喷印、包装) →平整→热轧卷→精整→纵切→窄带钢→横切→钢板→酸洗→酸洗卷
四我国热连轧带钢生产采用的先进技术与特色技术
目前国内的热轧宽带钢轧机约有4类,其特色分别如下:
1传统热轧宽带钢轧机
(1)连铸坯热装和直接热装。该技术要求炼钢和连铸机稳定生产无缺陷板坯;热轧车间最好和连铸机直接连接,以缩短传送时间;在输送辊道上加设保温罩及在板坯库中设保温坑;板坯库中要具有相应的热防护措施,以保证板坯温度。应设有定宽压力机,减少板坯宽度种类。加热炉采用长行程装料机,以便于冷坯与热坯交换时可将高温坯装入炉内深处,缩短加热时间。精轧机后2机架采用轧辊轴向串动技术,以增加同宽度带钢轧制量。采用连铸、炼钢、轧钢生产计划的计算机一体化管理系统,以保证物流匹配。
第3阶段,这个阶段实际上是近1~2年开始的,是以提高效益、调整品种结构、满足市场需要和提高企业竞争能力为目的的发展阶段。由于近年国家经济快速发展,对钢材需求不断增加,因此除国营大中型企业外,中小型企业,甚至民营企业都把生产宽带钢作为今后发展的重点,或引进或采用国产技术,或建设传统热连轧宽带钢轧机或建设薄板坯连铸连轧生产线。这个阶段以鞍钢1700mm、2150mm(国产),唐钢1780mm薄板坯和1700mm(国产)、马钢1700mm薄板坯和2250mm、涟钢1700mm薄板坯、莱钢1500mm(国产)、本钢薄板坯、济钢1700mm(国产)、新丰1700mm(国产)、宝钢1800mm、首钢2250mm、武钢2250mm、太钢2250mm轧机为代表。同时,这个阶段对引进的二手轧机和原技术较落后的国产轧机进行了全面技术改造,使其达到了现代化水平。
轧钢机械设备(DOC)

轧钢机的定义狭义的定义:直接轧制钢材的机械设备广义的定义:用于轧制钢材所需的全部设备轧钢机械设备的组成主要设备:直接使轧件产生塑性变形的设备--轧钢机主机列,包括:工作机座、接轴、齿轮机座、减速机、联轴节、主电机辅助设备:主设备以外的各种设备,包括:加热炉、剪切机、辊道、矫直机、包装机等各种设备轧钢机分类(主设备)按用途分类<1> 开坯机:将钢锭轧成钢坯(方坯、板坯、圆管坯)<2>型钢轧机:将方坯轧成型材<3>热轧板带轧机:将板坯轧制各种厚度的板材<4> 冷轧板带轧机:将热轧板轧成冷轧板<5>钢管轧机:将圆管坯轧制成无缝钢管<6>特种轧机:特殊用途的轧机按结构分类<1> 二辊式可逆:初轧机、轨梁轧机、中厚板不可逆:型钢连轧机<2> 三辊式:走上下两条轧制线<3> 三辊劳特式:中辊浮动<4> 四辊式:由两个工作辊和两个支承辊构成<5> 多辊式:由两个工作辊和多个支承辊构成,主要用于冷轧板带钢<6> 行星式:<7> 立辊式:<8> 万能式:立辊+平辊<9> H型钢轧机<10>斜辊式按布置分类(1)单机座式优点:轧机少,易操作缺点:成本相对较高(一个电机、一个减速机、一个齿轮机座带一个轧机)(2)横列式主要用于型钢轧机,一个电机带多个轧机优点:(1)设备成本低;(2)可采用大规格原料,降低轧材成本;(3)头尾温差小,轧材尺寸教精确。
缺点:(1)后架轧辊的速度不能与增长的轧件长度相匹配;(2)轧件要横移,需设移钢机。
(3)纵列式一个电机分别带一个轧机,每架轧机轧完后进入下一架轧机。
优点:(1)产量高;(2)轧辊速度与轧件长度相匹配缺点:(1)厂房细长;(2)机械投资大(4)连续式一个电机分别带一个轧机,轧件同时进入每架轧机,常用于冷轧。
热轧区域设备精度要求 (2)
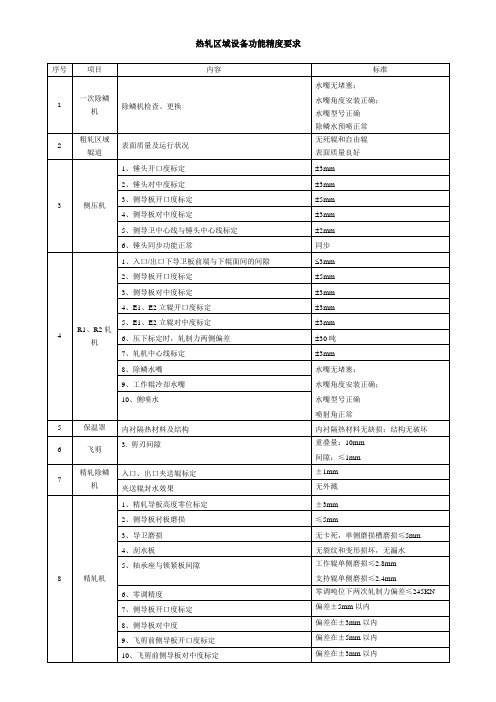
6、锤头同步功能正常
同步
4
R1、R2轧机
1、入口/出口下导卫板前端与下辊面间的间隙
3mm
2、侧导板开口度标定
5mm
3、侧导板对中度标定
3mm
4、E1、E2立辊开口度标定
3mm
5、E1、E2立辊对中度标定
3mm
6、压下标定时,轧制力两侧偏差
30吨
7、轧机中心线标定
3mm
8、除鳞水嘴
水嘴无堵塞;
水嘴角度安装正确;
5mm,入口>出口
对中度偏差
3mm
13
溜槽
与下夹送辊间隙
0.8~1.8mm
14
夹送辊
辊缝偏差
2mm
15
助卷辊
操作侧与传动侧偏差
0.5mm/m
辊缝实测值与显示值偏差
0.5mm
助卷辊和卷筒的平行度
两侧偏差0.1mm
16
卷筒
涨缩实测值与显示值偏差
1mm
11、F1E立辊开口度标定
偏差在±3mm以内
12、F1E立辊对中度标定
偏差在±3mm以内
13、轧机的中心线标定
3mm
9
精轧机冷却水
1、WRC
12.5bar:压力偏差±0.5bar;最大流量:F1~F2:894m3/h;F3:874 m3/h;F4:750m3/h;F5:600 m3/h;F6~F7:564m3/h;流量偏差±50 m3/h
水嘴型号正确
喷射角正常
9、工作辊冷却水嘴
10、侧喷水
5
保温罩
内衬隔热材料及结构
内衬隔热材料无缺损;结构无破坏
6
飞剪
3.剪刃间隙
重叠量:10mm
精轧区设备简介

精軋機F-1至F-4為連結驅動方式,而F-5至 F-7設計為齒輪箱連接軋機,精軋機F-1至 F-7 設計有十字型式萬向接頭 ,在工輥換輥時一對 工輥被機動式換輥小車拖出 ,快速更換工輥設 備為側移器型式安裝在每一軋機前方 ,下背輥 軸承箱如雪橇型式安裝連接著液壓缸,背輥更 換時一對背輥被坐落在上下軸承箱間的液壓缸 退回。
14個
10,860 mm 0/132 m/min
連結器
潤滑 Aprons
齒輪式連結器
中央系統油脂潤滑輥輪頸部軸承 焊接鋼格板形式的 aprons安裝在工作台樑上
剪切機入口側邊導器(Crop Shear Entry Side Guide)
剪切機入口側邊導器是設計來導正(T-Bar)進入剪切 機作業,採用液壓缸推動邊導器並預先設定寬度。
F1
剪切機入口側工作台(Crop Shear Entry Table)
剪切機入口工作平台位於捲取箱和剪切機間, 具有獨立式驅動型式滾輪並裝有格子型式 aprons , 捲取箱 出口側的夾送輥位在此工作台上。
型式 滾輪尺寸 獨立式馬達驅動 直徑350 mm x長 1,800 mm
滾輪數量
工作台長度 工作台速度
剪切機餘料槽坐落於剪切機的漥坑底部
,剪
切機餘料槽是使用天車做搬運更換。 IHI的雙齒輪式剪切機有利於延長維持上下彎 曲切刀平行度。 切刀的更換和間隙調整作業為停機狀態模式 下完成作業。 生產鋼帶厚度在 (16 to 32 mm)經剪切機分切 後送至平板堆疊機完成堆疊並由天車運至儲 區儲存。
190/530 rpm
F-4 6,500 kW 190/530 rpm F-5 6,500 kW 190/530 rpm 01:01 1000 1132 01:01.9 636 724
(完整版)热轧1450轧机设备组成及原理简介

• (2)、点检:主要检查锁紧螺栓的紧固情况、液压缸工 作情况以及牌坊内侧滑板开口度尺寸(一般测量周期为1 个月,单侧滑板尺寸磨损超过0.5~1.5mm,需更换。)
精轧机主传动
• 1、主传动:(如图)
• ⑴、组成:电机、电机联轴器、减速机、主联轴器(带中间 筒轴,需做动平衡)、齿轮机座、鼓形齿接轴。
精轧机主传动
• ⑵、电机联轴器与主联轴器均采用鼓形齿轮与直齿内齿圈 传动。减速机采用斜齿轮传动,靠偏心套调整齿面接触与 侧隙。齿轮机座采用人字齿轮,也采用偏心套。
精轧机压下装置
• 3、上阶梯垫装置:
• 位于AGC液压缸与上支承辊之间,通过螺栓把合在AGC液 压缸上。每架轧机有1套上阶梯垫装置,阶梯垫窜动液压缸 安装在传动侧(行程600,一级行程150),2块阶梯垫中间 通过连杆铰接。4级高差,F1-F6高差80(F5-F6最后一级高 度(最厚一级)不采用,故而实际使用高差60)。
• 位于下支承辊与牌坊下横梁之间,用于调整轧机下辊系标 高,均采用液压缸驱动。抬升缸将下支承辊抬起到最高, 阶梯垫移动缸移动垫架到需要的位置,然后放下支承辊。 在阶梯垫下方设有测压仪,用来测量轧制力。共15级,每 级高差10,最后一级高度差5。
精轧机下阶梯垫
• (d+D)/2( d为下工作辊直径; D为下支承辊直径)与 下阶梯垫垫板厚度及液压缸行程的关系见下表:
精轧机主传动
• ④、鼓形齿接轴连接螺栓松动、接轴有裂纹,产生原因为 螺栓无防松,轧机堆钢及轧生钢时产生过大的扭转应力, 超过接轴许用应力产生的破坏。
精轧机工作原理
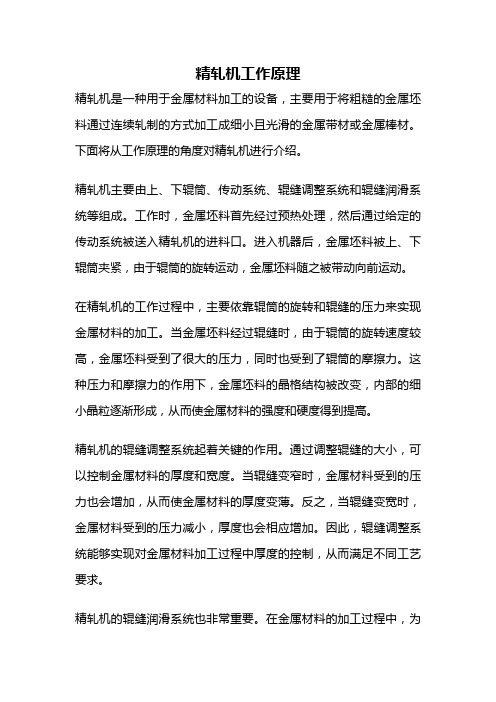
精轧机工作原理精轧机是一种用于金属材料加工的设备,主要用于将粗糙的金属坯料通过连续轧制的方式加工成细小且光滑的金属带材或金属棒材。
下面将从工作原理的角度对精轧机进行介绍。
精轧机主要由上、下辊筒、传动系统、辊缝调整系统和辊缝润滑系统等组成。
工作时,金属坯料首先经过预热处理,然后通过给定的传动系统被送入精轧机的进料口。
进入机器后,金属坯料被上、下辊筒夹紧,由于辊筒的旋转运动,金属坯料随之被带动向前运动。
在精轧机的工作过程中,主要依靠辊筒的旋转和辊缝的压力来实现金属材料的加工。
当金属坯料经过辊缝时,由于辊筒的旋转速度较高,金属坯料受到了很大的压力,同时也受到了辊筒的摩擦力。
这种压力和摩擦力的作用下,金属坯料的晶格结构被改变,内部的细小晶粒逐渐形成,从而使金属材料的强度和硬度得到提高。
精轧机的辊缝调整系统起着关键的作用。
通过调整辊缝的大小,可以控制金属材料的厚度和宽度。
当辊缝变窄时,金属材料受到的压力也会增加,从而使金属材料的厚度变薄。
反之,当辊缝变宽时,金属材料受到的压力减小,厚度也会相应增加。
因此,辊缝调整系统能够实现对金属材料加工过程中厚度的控制,从而满足不同工艺要求。
精轧机的辊缝润滑系统也非常重要。
在金属材料的加工过程中,为了减小辊筒与金属材料之间的摩擦力,增加金属材料的延展性,必须保证辊缝处有足够的润滑剂。
润滑剂能够形成一层薄膜,减小辊筒与金属材料之间的接触面积,从而减小摩擦力。
同时,润滑剂还能起到冷却作用,防止金属材料因为摩擦而过热。
精轧机是一种通过连续轧制来加工金属材料的设备。
它主要依靠辊筒的旋转和辊缝的压力来实现金属材料的加工,通过辊缝调整系统和辊缝润滑系统的配合,能够实现对金属材料厚度和宽度的控制。
精轧机的工作原理简单明了,但在实际应用中,还需要根据具体的金属材料和工艺要求进行参数的调整和控制,以确保加工质量的稳定性和一致性。
- 1、下载文档前请自行甄别文档内容的完整性,平台不提供额外的编辑、内容补充、找答案等附加服务。
- 2、"仅部分预览"的文档,不可在线预览部分如存在完整性等问题,可反馈申请退款(可完整预览的文档不适用该条件!)。
- 3、如文档侵犯您的权益,请联系客服反馈,我们会尽快为您处理(人工客服工作时间:9:00-18:30)。
概述:
精轧除鳞机:除鳞箱的上盖是用液压缸开闭,使除鳞喷咀维修容易。
入口夹送辊
有将带钢从精轧内拖出的作用,出口夹送辊兼给切头剪提供切尾速度信号。
F1E 立辊轧机:为了进一步提高板宽精度,并使中间坯对中于轧制中心线,在F1
轧机入口侧设置立辊轧机。
工作辊轴向窜动的HCW 轧机:轧机通过工作辊轴向窜动,加上强力液压弯辊,可以改变轧辊的凸度,从而保证板形质量并延长轧辊的使用寿命。
F1-F7 全部采用HCW 轧机。
F1-F7 全部采用全液压H—AGC。
F1-F7 全部采用强力液压弯辊。
F1-F7 设工艺润滑水。
F1-F7 之间采用带钢冷却(F1-F3 强冷)。
F1-F7 采用氧化铁皮抑制。
F1-F7 采用轧辊分段冷却。
F1-F7 采用水压除尘。
F1-F7 轧机间采用液压活套。
F1-F7 采用横移列车式的快速换工作辊。
3.1. 精轧除磷机(051112050)
用途:用以清除板坯二次氧化铁皮,并对板坯测速。
型式:夹送辊式高压水除鳞箱。
结构特点:
精轧除机箱体是由两片机架通过横梁连接而成。
正常工作时,用液压缸辊缝设定将带材送入
精轧机中,当发生事故时,用液压缸将带材从轧机中拉出。
上辊有飞剪切尾速度检测功能。
高压水喷嘴纵向交错布置,使喷射区域相互补充,避免出现水痕。
控制及联锁要求:
1. 所有辊子速度应与飞剪精轧立辊轧机速度相匹配.
2. 前后夹送辊正常工作时,液压缸处于夹紧状态; 事故时,前夹送辊液压缸工作,后夹送辊液压缸打开.。
3. 后夹送辊上辊具有飞剪切尾测速功能.
4. 前后夹送辊辊缝预先设定, 除鳞过程中不再动作.
5. 带钢进入除鳞机前,喷嘴开始喷水,带钢出夹送辊之后,停止喷水。
6. 换集水管时,上盖缸驱动至上盖与水平成900 后,换集水管,维修完成后。
驱动缸回落。
集水管维修后,送入除鳞机体内。
3.2. F1E 立辊轧机(051112051)
用途:将中间坯正确导入精轧机并对中间坯边部进行轧制。
型式:吸附型、上传动式(不可逆轧制)。
结构特点:
在精轧除鳞机的出口侧,F1 轧机的入口侧,配置附着式的立辊轧机(F1E),
机架装配、侧压装置等部件组成,辊缝的予设定是通过被分别设在立辊轧机的操作侧、传动侧的液压压下缸来完成的。
控制联锁要求:
1.F1E 立辊与F1 水平辊轧机进行微张力控制。
2.两台主传动电机进行电气同步控制。
3.侧压开口度精度0.5-1mm。
4.两侧侧压液压同步精度1mm。
5.辊时接近开关发信号,主传动准确停车,使扁头方向与轧制方向平行。
左右侧压下及平衡装置带动立辊至接轴垂直位置;用接轴提升缸将接轴收缩570mm 与轧辊脱开,这时轧辊的扁头与接轴的叉头分开;继续用侧压缸将轧辊推至靠近轧机中心;用专用吊具吊出轧辊。
另一侧的换辊与以上步骤相同。
新辊的装入与换辊程序相反。
6.接轴:主传动电机准确停车,左右侧压下及平衡装置带动立辊至接轴正下方;打开接轴与叉头之间的把和螺栓;用C 型钩将接轴托起,并用螺栓把住,这时叉头留在轧辊扁头上;打开主传动减速机上的保护罩;将接轴从主传动减速机的孔中由上部吊走;再用C 型钩吊走叉头。
装入新接轴的程序与换下旧接轴的程序相反。
3.3. 精轧机组(061108054-60)
用途:将中间坯轧至成品带钢。
型式:四辊不可逆HCW 轧机。
结构说明:
该套精轧机是四辊不可逆式轧机,由7 架轧机组成。
F1-F7 机架上设置工作辊轴向窜动HCW,上下工作辊在液压缸作用下轴向窜动。
F1-F3 的上下工作辊是通过主联轴节、主减速机、中间轴、齿轮机座,鼓形齿接轴用直流电机驱动的。
F4-F7 的上下工作辊是通过主接轴、齿轮机座、鼓形齿接轴用直流电机驱动。
轧机的辊缝调整和板厚控制均由全液压AGC 实现。
用阶梯垫补偿辊径变化。
更换工作辊:
1)停机、轧辊扁头准确停在铅垂位置,关闭各冷却水;
2)导卫装置中的上、下导板于打开状态;
3)侧向压紧缸活塞杆退回到机架牌坊里通过液压系统保证其活塞杆退回位置; .
4)液压AGC 活塞杆退回至上换辊位置,上阶梯垫厚度处于最薄状态,通过上支承辊平衡上的行程检测装置发高度信号;通过上阶梯垫移动缸内位移传感器显示阶梯垫厚度信号;
5)下工作辊平衡缸活塞退回,工作辊换辊提升缸上升至换辊位置;
6)下接轴定位装置上的液压缸动作使夹紧夹头处于抱紧状态,工作辊与换辊小车自动挂钩;
7)下工作辊轴端挡板打开状态;
8)换辊小车动作使下轧辊轴向拉出300mm;
9)液压AGC 及上支承辊平衡不动,上工作辊平衡缸泄压,上工作辊下降定位销到位;
10)上接轴定位装置上的液压缸动作使夹紧夹头处于抱紧状态;
11)上工作辊轴端挡板打开状态;
12)换辊小车将旧辊拉出结束并脱开挂钩;换辊小车具体动作;
13)工作辊换辊机-横移装置动作将成对新辊对准机架,根据辊径的变化适当调整垫垫厚度和配辊,保证换辊后轧制标高控制在820±7.5;
14)换辊小车动作将一对新辊推入轧机;
15)上工作辊轴端挡板闭合、上接轴夹紧缸打开发信号;
16)上工作辊平衡缸活塞杆伸出电气延时保证;
17)下工作辊轴端挡板闭合发信号;下接轴夹紧缸打开;
18)工作辊换辊轨道提升缸下降至极限;
19)换辊小车动作退回;
20)上、下导板处于接通状态,新辊换辊结束;
21)打开冷却水,开机调整辊缝。
更换支承辊
1)首先换出工作辊;
2)下支承辊轴端挡板打开状态;支承辊换辊机液压缸活塞杆退回,将下支承辊拉出机
架;
3)在下支承辊轴承座放上换辊支架,再将下支承辊推入机架;
4)液压AGC 不动,上支承辊平衡缸泄压至换辊位置(通过上支承辊平衡上的行程检测
装置发信号);
5)上支承辊轴端挡板打开状态;拉出旧支承辊;
6)吊走旧支承辊,换新辊。
根据新的辊系直径调配机架下部垫板,使轧辊标高控制在
820±7.5;
7)支承辊换辊机液压缸活塞杆前进,将上支承辊拉入机架;上支承辊轴端挡板合上,
上支承辊平衡缸升起回原位;根据新的辊系直径调配机架上部阶梯垫;
8)支承辊换辊机活塞杆退回到原始位置,取下换辊支架,支承辊换辊机液压缸活塞杆
前进,将下支承辊推入机架;下支承辊轴端挡板合上;新辊换辊结束。
3.4. F1-F7 轧机间导卫及活套(061108064)
用途:导卫用于板带的顺利导入导出,活套用于控制各机架间张力。
型式:入口侧导板:液压驱动式。
结构特点:
在F2-F6 机架的入口侧设置可调侧导板,各精轧机机架间设活套,各精轧机机架的出口侧设出口导卫装置。
在入口导板架体及出口导卫装置架体上设有工作辊分段冷却集水管,氧化铁皮抑制集水。