精轧区设备简介
轧钢设备介绍

1.3.2 按结构分类:根据轧辊在机座中的布置形式 1.3.2.1轧辊水平布置 (1)二辊式轧钢机
(2)三辊式轧机
三辊劳特式轧机
(3)四辊轧机
(4)多辊式轧机
泰勒 轧机
六辊 轧机
HC
HC 轧机
(偏)(八)辊轧机
偏八
偏十
双偏八
十二辊轧机
二十辊轧机
三十二辊轧机
三十六辊轧机(成品厚度:0.0007~0.0008mm )
目的:降低轧制时主电机尖峰负荷,增加空载时的主电机 负荷,从而使负荷均匀化。
储存能量:
适用范围(1)轧制时间〈间隙时间;(2)轧辊不可逆。
Ⅰ主电机;Ⅱ传动机构(装臵);Ⅲ工作机座
主电机:为轧辊旋转提供动力的设备
传动机构:通常由减速机、齿轮座、连接轴和连轴器等部件组成
工作机座(1)机架:在其窗口内安装轧辊的轴承 (2)轧辊:轧件在其间被轧制(压缩变形) (3)轧辊轴承:用于轧辊的支承和定位 (4)轧辊调整装臵及上辊平衡装臵:前者用于调整轧辊间的距离,后者用来消除上轴承 座与压下系统间的间隙 (5)导位装臵:用来使轧件按照规定的位臵、方向和状态准确进出孔型
(2)横轧机
1.2.3按轧钢机的布臵形式分类
(1)单机座式轧机
(2)横列式轧机
(3)纵列式轧机
(4)半连续式轧机
(5)连续式轧机
(6)串(顺)列往复式(跟踪式、越野式)轧机
(7)布棋式轧机
(8)复二重式轧机
1.4 主机列的构成及各部分的作用
二辊冷轧机
飞轮:轧制时,冲击负荷作用下,系统减速,负载的一部 分有飞轮放出储存的动能来克服。轧件轧出后(空载), 负载突减,主电机带动飞轮加速,飞轮储存能量。
精轧区设备

概述:精轧除鳞机:除鳞箱的上盖是用液压缸开闭,使除鳞喷咀维修容易。
入口夹送辊有将带钢从精轧内拖出的作用,出口夹送辊兼给切头剪提供切尾速度信号。
F1E 立辊轧机:为了进一步提高板宽精度,并使中间坯对中于轧制中心线,在F1轧机入口侧设置立辊轧机。
工作辊轴向窜动的HCW 轧机:轧机通过工作辊轴向窜动,加上强力液压弯辊,可以改变轧辊的凸度,从而保证板形质量并延长轧辊的使用寿命。
F1-F7 全部采用HCW 轧机。
F1-F7 全部采用全液压H—AGC。
F1-F7 全部采用强力液压弯辊。
F1-F7 设工艺润滑水。
F1-F7 之间采用带钢冷却(F1-F3 强冷)。
F1-F7 采用氧化铁皮抑制。
F1-F7 采用轧辊分段冷却。
F1-F7 采用水压除尘。
F1-F7 轧机间采用液压活套。
F1-F7 采用横移列车式的快速换工作辊。
3.1. 精轧除磷机(051112050)用途:用以清除板坯二次氧化铁皮,并对板坯测速。
型式:夹送辊式高压水除鳞箱。
结构特点:精轧除机箱体是由两片机架通过横梁连接而成。
正常工作时,用液压缸辊缝设定将带材送入精轧机中,当发生事故时,用液压缸将带材从轧机中拉出。
上辊有飞剪切尾速度检测功能。
高压水喷嘴纵向交错布置,使喷射区域相互补充,避免出现水痕。
控制及联锁要求:1. 所有辊子速度应与飞剪精轧立辊轧机速度相匹配.2. 前后夹送辊正常工作时,液压缸处于夹紧状态; 事故时,前夹送辊液压缸工作,后夹送辊液压缸打开.。
3. 后夹送辊上辊具有飞剪切尾测速功能.4. 前后夹送辊辊缝预先设定, 除鳞过程中不再动作.5. 带钢进入除鳞机前,喷嘴开始喷水,带钢出夹送辊之后,停止喷水。
6. 换集水管时,上盖缸驱动至上盖与水平成900 后,换集水管,维修完成后。
驱动缸回落。
集水管维修后,送入除鳞机体内。
3.2. F1E 立辊轧机(051112051)用途:将中间坯正确导入精轧机并对中间坯边部进行轧制。
型式:吸附型、上传动式(不可逆轧制)。
精轧区功能说明速度活套V2.0解剖

首钢1580热轧带钢精轧区主速度活套控制器功能说明北京北科麦思科自动化工程技术有限公司目录1.1主速度活套控制器功能说明 (3)1.1.1F1E立辊轧机 (3)1.1.1.1F1E立辊轧机的功能 (3)1.1.1.2F1E立辊轧机的技术参数 (3)1.1.1.3F1E立辊轧机的速度控制 (4)1.1.1.4F1E立辊轧机的操作 (5)1.1.1.5F1E立辊轧机的状态显示 (6)1.1.2F1-F7精轧机 (6)1.1.2.1F1-F7精轧机的功能 (7)1.1.2.2F1-F7精轧机的技术参数 (7)1.1.2.3F1-F7精轧机的速度级联 (9)1.1.2.4F1-F7精轧机的速度控制 (12)1.1.2.5F1-F7精轧机的主轴定位控制 (15)1.1.2.6F1-F7精轧机的操作 (15)1.1.2.7F1-F7精轧机的状态显示 (15)1.1.3活套 (16)1.1.3.1活套的功能 (16)1.1.3.2活套高度及张力控制 (16)1.1.3.2.1活套机构的基本方程 (16)1.1.3.2.2活套张力控制方法 (19)1.1.3.2.3活套高度调节原理 (20)1.1.3.3活套的技术参数 (20)1.1.3.4活套的控制 (20)1.1.3.5活套的操作 (21)1.1.3.6活套的状态显示 (22)1.2精轧区模拟轧钢功能 (22)1.2.1区域模轧 (22)1.2.2全线模轧 (23)1.3精轧区主速度通讯 (23)1.3.1精轧区主速度与传动系统通讯 (23)1.3.2精轧区主速度与精轧区压下控制系统通讯 (25)1.3.3精轧区主速度与精轧区板形控制系统通讯 (25)1.3.4精轧区主速度与卷取控制系统通讯 (25)1.1 主速度活套控制器功能说明主速度活套控制器控制F1E立辊轧机,F1-F7精轧机和L1-L6活套。
其中主轧机和活套是精轧区域的最核心设备。
1.1.1 F1E立辊轧机F1E立辊轧机由主传动装置、立辊机架装配、左右侧辊缝调整装置、轧辊轴承、吊具、配管及平台等部件组成。
设备参数

中板厂轧钢车间:1#、2#加热炉参数:有效尺寸:5.0×26.448=132.24㎡。
生产能力:75t(坯料)/h。
加热钢种:普碳钢、低合金钢、合金钢。
坯料进炉温度:常温。
坯料出炉温度:1100~1200℃。
燃料种类和发热值:焦炉煤气,16314kJ/h。
空气预热温度:350~400℃。
加热坯料厚度:170~240mm。
加热坯料宽度:800~1500mm。
加热坯料长度:1200~2200mm。
冷却方式:全炉汽化冷却。
加热炉还有助燃风机、空气预热器、汽化冷却装置、烟筒加热炉检测设备等辅助设备。
3#蓄热式加热炉的参数:有效尺寸:5.0×26.448㎡。
生产能力:75t/h。
加热钢种:普通碳素钢、低合金钢、合金钢。
坯料装炉温度:常温。
坯料出炉温度:1100~1200℃。
燃料种类和发热值:焦炉煤气,16314kJ/h。
空气预热温度:≥1000℃。
单位燃料消耗:1.2GJ/t(坯)加热钢板尺寸:厚度:100~240mm,宽度:800~1500mm,长度:1200~2200mm。
冷却方式:800mm还有加热炉风机、汽化冷却装置、烟筒、加热炉检测设备、30吨板坯升降台、3吨推钢机、炉前和炉后辊道等辅助设备。
主要设备及参数:二辊可逆式粗轧机1、轧机,最大轧制力:25000KN(2550t),最大传动力矩:1764KN.m(180t.m),最大轧制力矩:1275KN.m(130t.m),轧制速度:0~2.51m/s~5.03m/s.2、轧辊,轧辊转速:0~±40r/min~±80r/min,轧辊直径:Φ1200~Φ1000mm,轧辊材质:65GrNiMo,轧辊单重:33t,工作时上辊最大提升高度:350mm(工作)、600mm(设计)。
除轧机外,粗轧部分还有油膜轴承、压下装置、回松电机、机架辊、工作辊道、主电机、连接机、推床等辅助装置。
粗轧机的布置:粗轧机到一号加热炉的中心距:18031mm,粗轧机到精轧机中心距:39585mm。
热轧1450精轧机设备组成及原理简介

精轧机压下装置 • 3、上阶梯垫装置:
• 位于AGC液压缸与上支承辊之间,通过螺栓把合在AGC液 压缸上。每架轧机有1套上阶梯垫装置,阶梯垫窜动液压缸 安装在传动侧(行程600,一级行程150),2块阶梯垫中间 通过连杆铰接。4级高差,F1-F6高差80(F5-F6最后一级高 度(最厚一级)不采用,故而实际使用高差60)。
AdwF5-F6= h+(D F5-F6/2+ dF5-F6)-625
• 例 如: F1-F4 下工作辊 直径 720mm , 下支承辊 直径 1351mm 时,(d+D)/2=1395.5mm,按上表用第9阶梯垫, h=170mm。 • 下工作辊上辊面标高 : • AdwF1-F4=170+1395.5-755=+810.5mm
• 轧线标高的确定 轧线名义标高为+815mm,允许偏差为 ±5mm,标高A在+820~+810范围内(即下工作辊上辊面标 高),其参考点为车间地平面为±0。
精轧机下阶梯垫
• 轧线标高Adw与下阶梯垫厚度h、工作辊直径d和支承辊直 径D的关系为:(见上页附表)
• F1-F4
• F5-F6
AdwF1-F4= h+(D F1-F4/2+ dF1-F4)-755
精轧机压下装置
• 主要补偿工作辊重磨量,支承辊磨损后的调节靠人工在承 压垫板底部加垫板(垫板共3种,厚度分类:20、40、 50)。另上阶梯垫可以实现快速换辊(直接达到最薄厚度)
支承辊直径 1450~1410 1410~1370 1370~1330 1330~1300 垫板厚度 0(不采用垫板) 20 40(20+20) 50(20+20+10)
轧钢自动化设备

轧钢自动化设备轧钢自动化设备是指在钢铁生产过程中使用的自动化设备,用于实现钢材的轧制和加工。
这些设备通过自动化控制系统,可以实现钢材的精确轧制和高效加工,提高生产效率和产品质量。
一、设备概述轧钢自动化设备通常包括轧机、输送设备、控制系统等部份。
1. 轧机:轧机是轧钢自动化设备的核心部份,主要用于将钢坯进行轧制和加工。
根据不同的轧制工艺和产品要求,轧机可以分为热轧机和冷轧机两种类型。
热轧机主要用于热轧钢材的生产,冷轧机主要用于冷轧钢材的生产。
轧机通常由辊道、辊轴、辊缸、辊座等部份组成,通过辊轧的方式将钢坯进行塑性变形,实现钢材的轧制和加工。
2. 输送设备:输送设备用于将钢坯从一工序输送到另一工序,实现生产线的连续运行。
常见的输送设备包括输送机、皮带输送机、辊道输送机等。
这些设备通过传动装置将钢坯从一个位置转移到另一个位置,确保生产线的顺畅运行。
3. 控制系统:控制系统是轧钢自动化设备的核心,用于对设备进行自动化控制和监测。
控制系统通常包括PLC(可编程逻辑控制器)、人机界面、传感器等部份。
PLC负责对设备进行逻辑控制,实现自动化生产过程的各个功能。
人机界面用于人机交互,操作员可以通过触摸屏或者键盘等设备对设备进行操作和监测。
传感器用于采集设备运行状态和产品质量等数据,反馈给控制系统,实现对设备的实时监测和控制。
二、设备特点轧钢自动化设备具有以下特点:1. 高效生产:轧钢自动化设备通过自动化控制系统,实现了设备的高效生产。
自动化控制系统可以根据生产需求进行智能调度,实现设备的自动化运行和优化控制,提高生产效率。
2. 精确轧制:轧钢自动化设备通过精确的控制系统,可以实现钢材的精确轧制。
控制系统可以对辊轧力、辊间距、辊轴转速等参数进行精确控制,确保钢材的尺寸和质量符合要求。
3. 产品质量稳定:轧钢自动化设备通过自动化控制系统,可以实现对钢材质量的实时监测和控制。
控制系统可以采集钢材的温度、尺寸、硬度等数据,根据设定的控制策略进行调整,确保产品质量的稳定性。
F1-F7精轧机组机械设备设备使用说明书

F1-F7精轧机组机械设备设备使用说明书
使用说明书
(包括功能、安装、操作、维护)
13272.302.00SM
13272.304.00SM
13272.305.00SM
13272.306.00SM
13272.307.00SM
(机械部分)
中国二重(德阳)重型装备责任有限公司
设计研究院
2006年3月25日
使用说明书13272.302.00SM 13272.304.00SM 13272.305.00SM 13272.306.00SM 13272.307.00SM
F1-F7精轧机组设
备
共88 页第7 页
1. 概述
F1-F7精轧区设备为1750mm热轧带钢工程的核心设备,位于热卷箱飞剪区之后、输出辊道和层流冷却区之前,包含精除鳞箱(13272.301.00)、F1-F7精轧机(13272.302.00)、精轧机(F1-F7)主传动装置(13272.303.00)、F1-F7机上配管(13272.307.00)、工作辊换辊小车(13272.305.00)、F1-F7快速换辊装置(13272.304.00)、F1-F7侧导板及导卫、活套装置(13272.306.00)。
其中主要设备F1-F7精轧机位于精除鳞箱后,可完成从中间坯料轧制到成品带钢的全轧制过程。
F1-F7精轧机由六台全液压压下、带串辊、正弯辊板型控制的四辊不可逆轧机(F1-F7)组成, 每两台轧机之间间距为5500mm,由于装有液压AGC装置、正弯辊及工作辊水平串辊等装置,提高成品钢带的厚度精度和板型精度。
热轧1450精轧机设备组成及原理简介共30页文档
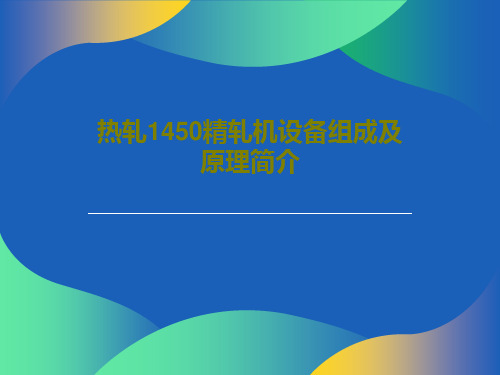
45、法律的制定是为了保证每一个人 自由发 挥自己 的才能 ,而不 是为了 束缚他 的才能 。—— 罗伯斯 庇尔
谢谢你的阅读
❖ 知识就是财富 ❖ 丰富你的人生
71、既然我已经踏上这条道路,那么,任何东西都不应妨碍我沿着这条路走下去。——康德 72、家庭成为快乐的种子在外也不致成为障碍物但在旅行之际却是夜间的伴侣。——西塞罗 73、坚持意志伟大的事业需要始终不渝的精神。——伏尔泰 74、路漫漫其修道远,吾将上下而求索。——屈原 75、内外相应,言行相称。——韩非
- 1、下载文档前请自行甄别文档内容的完整性,平台不提供额外的编辑、内容补充、找答案等附加服务。
- 2、"仅部分预览"的文档,不可在线预览部分如存在完整性等问题,可反馈申请退款(可完整预览的文档不适用该条件!)。
- 3、如文档侵犯您的权益,请联系客服反馈,我们会尽快为您处理(人工客服工作时间:9:00-18:30)。
精軋機F-1至F-4為連結驅動方式,而F-5至 F-7設計為齒輪箱連接軋機,精軋機F-1至 F-7 設計有十字型式萬向接頭 ,在工輥換輥時一對 工輥被機動式換輥小車拖出 ,快速更換工輥設 備為側移器型式安裝在每一軋機前方 ,下背輥 軸承箱如雪橇型式安裝連接著液壓缸,背輥更 換時一對背輥被坐落在上下軸承箱間的液壓缸 退回。
14個
10,860 mm 0/132 m/min
連結器
潤滑 Aprons
齒輪式連結器
中央系統油脂潤滑輥輪頸部軸承 焊接鋼格板形式的 aprons安裝在工作台樑上
剪切機入口側邊導器(Crop Shear Entry Side Guide)
剪切機入口側邊導器是設計來導正(T-Bar)進入剪切 機作業,採用液壓缸推動邊導器並預先設定寬度。
F1
剪切機入口側工作台(Crop Shear Entry Table)
剪切機入口工作平台位於捲取箱和剪切機間, 具有獨立式驅動型式滾輪並裝有格子型式 aprons , 捲取箱 出口側的夾送輥位在此工作台上。
型式 滾輪尺寸 獨立式馬達驅動 直徑350 mm x長 1,800 mm
滾輪數量
工作台長度 工作台速度
剪切機餘料槽坐落於剪切機的漥坑底部
,剪
切機餘料槽是使用天車做搬運更換。 IHI的雙齒輪式剪切機有利於延長維持上下彎 曲切刀平行度。 切刀的更換和間隙調整作業為停機狀態模式 下完成作業。 生產鋼帶厚度在 (16 to 32 mm)經剪切機分切 後送至平板堆疊機完成堆疊並由天車運至儲 區儲存。
190/530 rpm
F-4 6,500 kW 190/530 rpm F-5 6,500 kW 190/530 rpm 01:01 1000 1132 01:01.9 636 724
F-6
6,500 kW
250/530 rpm
01:01
1000
1132
F-7
6,500 kW 250/530 rpm
815 mm
頭端: 80 m/min,尾端:40-120 m/min. 1.驅動齒輪單元以集中供油系統強迫給油 2. Drum頸部軸承以集中供油系統供油脂 經液壓缸將drum收回(滑軌型式) 瀉槽型式 兩個可傾導型式
剪切機設計說明:
剪切機被設計可以精確的與自動地事先決定
T-bar頭尾端的剪切長度。 剪接機被設計可徹底將鋼帶殘餘部分切除。 每一個冷卻噴頭將被提供冷卻圓鼓。 剪切鋼帶板形量測裝置位於剪切機前端。
剪切機
精軋機
精軋區主要區分二大部份: 一、剪切機(Crop
Shear): 當解捲作業時T-Bar(transfer bar )的頭端將被 剪切機自動切除,彎曲切刀將提供T-Bar的頭 端具備平坦形狀以利穿過精軋機。 T-Bar的尾端被另一個相對方向彎曲切刀切除 以提供鋼帶較佳生產品質。
剪切機(Crop Shear)
剪切機坐落在機軋機入口側,用來剪切T-bar的頭 和尾端,剪切機設備為圓鼓式框架具有兩個齒輪與彎 曲切刀型式,由輥輪軸承上鑄鐵襯墊支撐,剪切機機 架焊接固定在基礎上並支撐圓鼓襯墊。 兩個齒輪單元同時結合在操作側和驅動側兩側是 以獲得良好剪切形狀,當剪切鋼板時彎曲切刀間隙將 被圓鼓的固定反向扭轉力維持著,同時圓鼓將被坐落 在牌坊襯墊上由液壓缸固定著,在圓鼓的操作側上下 齒輪單元連接彈簧補償齒輪所受反衝力。
01:01
1000
1132
精軋機設備說明:
精軋機( F-1) 進料輥
軋機出口側滾輪 工輥更換
1個直徑 350 mm. x長 2,230 mm
2個直徑 300 mm x長 1,800 mm在精軋機 ( F7) 出口側 馬達驅動運輸小車, 邊移動由液壓運轉型式
背輥更換
每座軋機
液壓操作(雪橇型式)
澆鑄鐵 每站大約7,200cm2 (F1~F4) 每站大約 6,000cm2 (F5~F7) 牌坊窗口的鋼板襯墊 Welded steel 上隔離板為鍛接鋼鐵
精軋機除銹器(Finishing Scale Breaker)
精軋機除銹器將噴灑出高壓水將T-bar上下表
面二次銹皮除去,精軋機除銹器蓋板的設計是 防止除銹水波灑濺出,蓋板有類似(蝸牛形狀) 排水溝以收集噴灑出的除銹水並流至清渣溝。 獨立式驅動輸送輥道位於夾送輥進出口側,是 以進口上方夾送輥為驅動型式,精軋機除銹器 輸送輥面較其他輸送輥道長是為防止軸承箱被 噴灑出的水浸入。
在更換切刀時位於液壓缸操作側將牽引著機座外的
圓鼓框架,切刀更換時設定於停機環境下作業,軋 延作業時調整切刀間隙是不必要的。 在剪切機的圓鼓更換是用手動方式解開齒輪的連結 器和襯墊板保持裝置,切刀的間隙是由切刀背後金 屬墊板來做適當調整。 兩個螺旋狀齒輪機座平台由滾輪軸承支撐並安裝焊 接於齒輪箱,齒輪箱將有足夠強度來承受剪切時所 受衝程負載,兩個量測滾被精確使用在量測T-bar速 度,當量測輥偵測到鋼板頭端被剪切時,捲取箱搖 輥將被啟用,而精軋機除銹器的輥輪將被使用當成 剪切鋼板尾端量測輥。
牌坊
軋機參數 臺板 背輥平衡 工輥平衡和彎曲
大約. 550 ton/mm (F1~F4) 大約 520 ton/mm (F5~F7) 輥座底下沉重鋼鐵 4個液壓缸建造在液壓缸箱上 高工輥液壓平衡和彎曲的液壓缸安裝在牌坊上軸承箱上可增大冠 工輥移轉是備裝置是安裝在 精軋機(F1 to F7)
工輥移轉是備裝置
型式
開度 汽缸 邊導器長度 移動速度 齒輪條和齒輪機械設備運轉液壓缸並 操作側和驅動側結合 750 – 1,800 mm (最大) 由伺服閥控制液驅動壓缸 約9m 100 mm/sec (兩側一起作動)
邊導器襯墊
潤滑 位置感應器 邊導器滾輪
可替換式鋼板
集中系統式提供ad cell 坐落在下背輥兩側軸承箱底下 ,液壓缸的 衝程調整工輥直徑改變和輥子安置間隙,用以增補填 充墊板方式完成補償上背輥直徑的變化,裝填墊板坐 落固定底層墊板的方式來完成補償下背輥的直徑改 變,上背輥平衡是利用以坐落在液壓缸箱的上輥平衡 裝置液壓缸來完成,平衡上下工輥的强而有力液壓缸 坐落在液壓缸箱,軋機牌坊的樁表面在焊接在不銹鋼 襯墊面上,軋機每一站具有入口邊導器和出口邊導 器 ,這些邊導器可在輥子更換同時縮回,精軋機 F-1 入口側和 F-7 出口側具有進料輥,伸張力保持器設備 位於軋機間其驅動型式為低惰性引導。
軋機馬達能力和 軋機速度:
軋機 主馬達規格 轉速比 滾輪速度 m/min.
min
F-1 6,500 kW 01:05.5 221
max
251
190/530 rpm
F-2 6,500 kW 190/530 rpm F-3 6,500 kW 01:03.0 405 461 01:04.5 270 307
精軋區範圍 (15~20柱)
簡介內容:
一、精軋區慨要(General): 二、設備介紹: 剪切機入口側工作台(Crop Shear Entry Table) 剪切機入口側邊導器(Crop Shear Entry Side Guide) 剪切機(Crop Shear) 精軋機除銹器(Finishing Scale Breaker) 機軋機(Finishing Mill)
精軋機除銹器噴頭介紹:
噴頭 噴頭型式 凸輪 支撐和螺栓 除銹壓力 兩個上/下噴頭 不銹鋼材質 碳鋼材質 17.6 MPa min.
精軋機除銹機設計說明:
液壓缸的蓋板為傾斜方式以防止銹皮和噴灑水流出。 上夾送輥將扮演具有檔水功能。 噴嘴將被設計能保證完全地除銹並具有冷卻鋼帶功能,以 防止銹皮缺陷產生和避免增加熱鋼帶生產的造成問題。 兩個主要噴水閥被設計為前後兩列型式。 每列噴水孔被設計為交叉排列型式。 蓋板被設計可有效將側邊噴灑水轉向。 除銹水系統容積的設計能足夠滿足粗軋區和精軋區除銹用 水。 所有管件將被強而有力鐵箍或固定器固定著以防止移動。
1支 (直徑350 mm x長 2,160 mm)
1支 (直徑406 mm x長 2,160 mm) AC 52 kw 0/550 rpm AC 25 kw 0/120 rpm 齒輪式連結器 1.集中系統油脂潤滑 2.萬向接頭與齒輪連結器(手動油脂潤滑)
機軋機(Finishing Mill)
F1至 F7 軋機: 精軋機由七座軋機串聯組合程(tandem mill) ,片 狀軋機牌坊為上封閉型式,軋機牌坊坐落在底板上並 牢固的固定在基礎上,每個軋機的工輥被設計備有可 轉移式機械設備,F-1至 F-6軋機由數個輥輪連接結合 。工輥坐落在多列楔形型式滾柱軸承上,而背輥坐落 在無間隙型式Morgoil 油膜軸承上,其潤滑方式由潤 滑系統的分配器供油潤滑,不具有下壓螺桿( screwdown )機械設備設計方式 ,液壓缸設備坐落在上背輥 與軋機牌坊間,其設計條件為了輥子間隙設定與自動 厚度控制系統(AGC)。
二、精軋機(Finishing Mill): T-bar經由機軋機入口側除銹裝置做三次銹皮的除 銹後接著送入精軋機軋延 。 各站精軋機的軋輥間隙和軋輥速度由電腦系統自 動設定控制。 F-1 到 F-7的主馬達由 AC 高速度反應驅動模式控 制。 軋輥間隙設定的控制由自動量測控制模式液壓缸 運行。 精軋機各站具有AGC液壓缸機械設備,不使用馬 達驅動壓下螺桿(screw down)機械裝置。
油液壓缸控制移動位置 移動行程 +/- 150 mm
至 F7 精軋機具有强而有力工輥bending 系統和工輥轉移系統以提供鋼板板形控制和 軋輥排程控制。 為獲得最佳鋼板的厚度和寬度,機軋機(F-1 至F-7)各站間具有低慣性伸張力保持器及高 反應速度控制和高速度的 (AGC)機械設備 。 工輥更換機械裝置是另一個重要因素,軋機 上下一對的工輥使用馬達式換輥小車取出, 在軋機前的側移器設備將更換新的一對工輥 並推進軋機內。