精益生产教材(学员版)
精益生产培训教材

21/52
四、多技能工训练,提升员工技能
22/52
五、通过防呆技术,降低员工劳动复杂性
1、常见的防呆构造
不需要注意力,即使有人 因为疏忽也不会发生错误 的构造。
不需要经验与直觉, 即使是外行人来做也 不会做错的构造。 • 例如: 电脑的接线插头。
不需要专门知识与高度的技 能,不管是谁或在任何时候 工作都不会出现差错的构造。 • 例如: 模具自动夹紧装置,一 个按键就能完成模具的 自动夹紧。
6/52
五、精益的基本思想:人性尊重
创造出以产品制造为核心的附加值
挑战
长期志向
沉思熟虑和决断
智慧与改善
改善
建立起简朴而紧凑的系统
有组织地进行彻底的学习 实践主义、完成任务的志向
现地实物
改善 尊重人性 现地实物
尊重利益享有者 公司与职员的相互信任的相互负责 尊重个人人性的发辉团队的缩合力量
12/52
八、组织工作时间
维护与改进
改进:活动对提高现行标准
在“精益”组织工作
事情 如何 变得 更好: 宏和大型流程改进 工艺改进
• 高管理
• 高管理
• 中层管理
• 中层管理
•监事
•监事
•运营商
•运营商
0
25
50
75
100
0
25
50
75
100
%的总工作时间
13/52
%的总工作时间
第二部分:工具篇
当重要责任。
11/52
七、精益倡导模式
自我实现需求
1
人是公司最重要的资源,培养善于观察和思考的员工
2
把从事改善的积极性,作为选拔人才的一项重要考核指标
精益生产预览培训教材

某企业精益生产推广案例
企业背景:某大型制造企业,生产多种产品 推广原因:提高生产效率,降低成本 推广过程:成立精益生产小组,进行培训和实施 推广效果:生产效率提高20%,成本降低15%,产品质量提升
精益生产未来发展
智能化精益生产
智能化技术:利用人工智能、大 数据等技术提高生产效率
智能化管理:通过信息化手段实 现生产过程的实时监控和管理
持续改进
建立持续改进的文化和氛围 制定持续改进的计划和目标 定期评估和改进生产流程 鼓励员工提出改进建议和参与改进活动 持续改进的成果分享和激励机制
精益生产案例分析
某企业精益生产实施案例
企业背景:某汽车制造企业 实施时间:2015年 实施目标:提高生产效率,降低成本
实施过程:引入精益生产理念,优化 生产流程,提高员工素质
构成:价值流图通常包括原材料、生产过程、成品、客户等环节,以及信息流、物料流、 时间流等信息。
作用:价值流图可以帮助企业发现生产过程中的瓶颈、浪费和不合理之处,从而进行优 化和改进。
绘制方法:绘制价值流图时,需要按照生产过程的实际流程,将各个环节和信息进行梳 理和绘制,并标注出关键数据,如生产时间、库存量等。
目视化管理
目视化管理的定义:通过视觉信号来传递信息,使员工能够快速、准确地了解生产状况和问题 目视化管理的作用:提高生产效率、降低成本、提高产品质量、减少浪费 目视化管理的工具:看板、信号灯、颜色标记、图表等 目视化管理的应用:生产现场、仓库、办公室等
精益生产实施步骤
制定实施计划
制定计划:根据目标和现状 制定实施计划,包括时间、 人员、资源等
培训目标:提高员工对精益 生产的理解和应用能力
培训方式:理论讲解、案例 分析、实践操作
精益生产培训教材
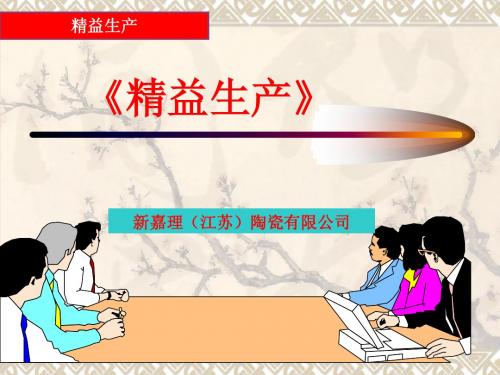
《精益生产》
新嘉理(江苏)陶瓷有限公司
精益生产
精益生产理念
第一部分
精益生产理念与浪费
企业经营的基本理念是什么?
为什么要实行精益生产?
精益生产的理念思想是什么? 企业的运营目的是什么?
成本的结构是什么?
工作和干活有什么不同? 现场七大浪费
课程内容
现场管理训练
精益生产理念
企业的基本经营理念
• 为股东创造利润(维持企业生存) • 向社会提供好的产品(占领市场空间) • 企业和员工共同发展
业
附加价值
• 等待 • 寻找 • 保管 • 重新整理 • 打开包装
现场管理训练
现场浪费
现场七大浪费
浪费
1. 过量生产 2. 库存
3. 搬运
4. 作业本身
5. 等待
6. 多余动作
7. 不良
现场管理训练
现场浪费
1、过量生产
•生产多于下游客户所需 Making More Than Needed •生产快于下游客户所求 Making Faster Than Needed
自働化
自 働 化
好处:
提供下列视觉和听觉帮助: - 目前生产状态 - 库存情况 - 设备状态 - 质量状态 - 需求援助状态 - 按节拍生产状态
支持小组的 快速反应
提高运行能力
现场管理训练
自働化
如何有效的自働化
1. 限制作业不良影响他人的限制位置 2. 防止不合格加工的动作防止 3. 防止装配漏件的监控装置 4. 快速处理问题的系统
有附加值的作业
无附加值的作业
工人的 动作
浪费
现场管理训练
现场浪费
所谓附加价值作业就是把产品或部件改变成某种形态的作业。 作业者的动态 作
精益生产培训教材(上)可编辑

大量生产方式的 三个发展阶段
萌芽期
19世纪中叶,美国制造业已具有劳动分 工、零件的互换性和专用机器等特点,具 备大量生产的雏形。
形成与发展期
1913年后福特公司为降低成本、提高质 量,采用流水作业进行生产,建立了世界 上第一条汽车装配流水线,推出了改变世 界的T型车。
全盛期
二战之后,大规模生产作为一种成熟的
调整时间 客户需变
长
动
短暂待机
生产力 问题
之三:搬运浪费 搬运不会产生附加价值。 原因:搬运会增加物料在空间的移动时间,多耗费人力,占用
搬运设备与工具,在搬运过程中因碰撞等原因造成不良品等
之四:加工浪费 超过需要的作业。
分为两种: 质量标准过高的浪费。 作业程序过多的浪费。→ECRS四原则方法进行改善。
高 低 高 物资缺乏、供不应 求
精益生产方式 品种多样化、系列化
柔性高、效率高 较粗略、
多技能、丰富 多技能
低 更低 更高 买方市场
1.2 精益生产理念
一、经营思想
在价格,成本和利润的关系中,有三种不同的思考方法: 成本主义、售价主义和利润主义。
成本中心型:以计算或实际的成本为中心,加上预先设定的利 润,得出售价。
计算公式: 成本=售价-利润
经营理念: 不断消除浪费 降低成本 积极进取
按照“利润中心型”的 思想经营,企业就可以
在竞争中立于不败之地。
二、浪费概念与类型
浪费概念:指超出增加产品价值所必需的绝对最少的物料、机器和 人力资源、场地和时间等各种资源的部分。
包含两个层面
一切不增加价值的活动都是浪费。 尽管是增加价值的活动,但所用的资源超出“绝对最少”
管理范式成为世界工业的主导生产模式, 并对美国及战后世界经济发展起了巨大推 动作用。
TPS精益生产5S学员版
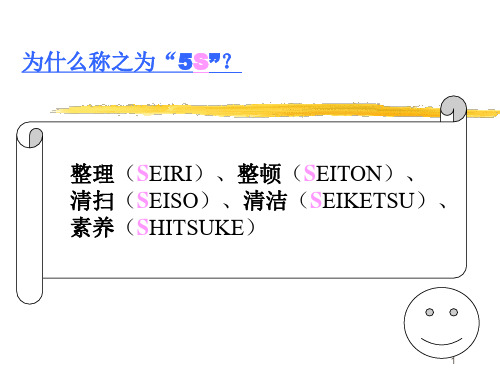
清扫
清洁
41
5S定义
日本企业不论是大工厂还是办 公室,都按区域设有卫生责任 者,任何时间都能保持窗亮几 净。
3.清扫
将工作场所内看得见与看不见的地方清扫干净,
保持工作场所干净、亮丽的环境。
目的:
·培养全员讲卫生的习惯 ·创造一个干净、清爽的工作环境 ·使人心情舒畅
这里有灰
注意点:责任化、制度化
42
放置方法 ○易取 ○在放置方法上多下工夫(照片84)
标识方法 ○放置场所和物品原则上一对一表示(停车场)
○现物的表示和放置场所的表示 (机场货)
○某些表示方法全公司要统一
○在表示方法上多下工夫(例:1季度1种颜色)
(ห้องสมุดไป่ตู้更换、活用颜色等)
30
整顿的“3定原则”: 定点、定容、定量
定点:放在哪里合适 定容:用什么容器、颜色 定量:规定合适的数量
备注:
(副)王华 确认时间 17:00
序号 名称 规格 QTY 5. 6. 7. 9.
25
◆显示板
◎吊挂式
△△零件置场
◎钩式
◎台式
26
◆定位置标示
◎影绘表示(形迹管理)
◎连接线标识
27
整顿的流程
设定整顿的对象场所
按3要素进行分析 按3定原则进行分析
整顿的实施 实施结果的评价
和改进
整顿对象的优先考虑场所 ·会出现较好效果的地方 ·在较短期间内可实施的地方 ·给顾客留下不好印象的地方
人的品质得以提升。 5
5S--现场管理之基石
生 品 企 员高 产 质 业 工效 管 管 形 满率 理 理 象 足里
5S
不没 起有 大牢 风固 大基 浪础 。的
精益生产培训教材

.36666666666666666666第1讲企业组织生产的价值(VSM)分析(一)【本讲重点】1.JIT诞生背景2.价值流程图(VSM)分析两个流程3.流程分析案例JIT生产方式的产生生产经营方式是指生产者对所投入的资源要素、生产过程以及产出物的有机有效组合和运营方式的一种通盘概括,是对生产运作经管中的战略决策、系统设计和系统运行经管问题的全面综合。
到目前为止,制造业的生产方式经历了一个从手工生产、批量生产到精益生产的演变过程。
传统生产方式的优缺点1.传统生产方式的优点20世纪初,美国福特汽车创始人亨利•福特创立了以零部件互换原理、作业单纯化原理以及移动装配法为代表的批量生产方式,由此揭开了现代化大生产的序幕。
几十年来,随着制造业产品越来越复杂,自动化技术以及各种加工技术的发展,这种生产方式在形式和内容上都不断增添新的内容,成为目前最为传统的生产方式。
图1-1 传统生产方式的特征如图1-1所示,在消费需求旺盛、商品相对供应不足的时代,企业生产的产品品种单一,通过大批量生产就可达到降低成本的目的。
一旦成本得到降低,企业就可以进一步扩大生产规模,形成“大批量—低成本”的循环模式。
因此,传统生产方式实际上是一种“以量取胜”的生产方式。
2.传统生产方式的缺点在商品紧缺的年代,传统的生产方式获得了巨大的成功。
但是,随着商品经济的发展,顾客不再满足于使用单一的商品,开始追求与众不同的多样化产品。
由于少品种、大批量的传统生产方式忽视了顾客的个性化需求,因而越来越不能适应市场的需求。
此外,当前的工业产品具有一个显著特征:价格越来越便宜。
在这种情况下,传统生产方式本来具备的优点变成了缺陷:在传统生产方式下,企业制造出的产品形成大量的库存。
由于产品价格不断降低,这些库存处于持续贬值的过程中。
这给企业带来了巨大的损失。
因此,商品经济的发展呼唤小批量、多品种的生产方式。
JIT生产方式的产生20世纪后半期,兼备手工生产及大量生产两者的优点,又能克服两者缺点的一种高质量、低成本并富有柔性的新的生产方式在战后崛起的日本丰田公司应运而生,即JIT(just in time)生产方式,也被称为“丰田生产方式”,在国内被译为“精益生产方式”。
精益生产培训教材(共 38张PPT)
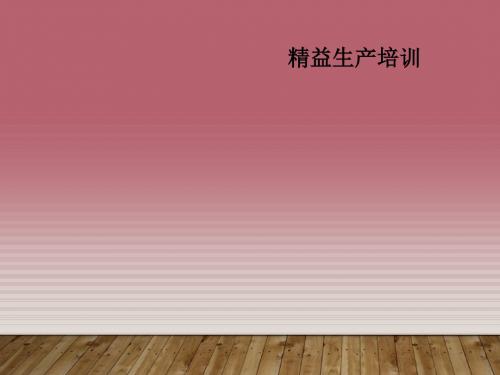
柏拉图
柏拉图
28
• 改善效果之确认
(元)
25000
改善前
(%)
100 75
(元)
25000
改善後 效果
支 出 金 額
20000 15000 10000 5000 0
累 計 比 率
支 出 金 額
20000 15000 10000 5000 0
50 25 0
伙 零 水 教 交 其 食 用 電 育 際 他 費 錢 瓦 費 費 斯 費
经过取消、合并、重排后的必要工序,应 采用最简单的方法或设备替代,以节省人
作业改善压缩
分割转移
作 业 时 间
作 業 改 善
作 业 时 间
工序
1
2
3
4
5
工序
2
3
并行作业,增加人员
拆解去除
1人 作业 作 业 时 间 作 业 时 间
2人 作业
工序
1
2
3
4
5
工序
1
2
3
作业改善后合并
重排
作 业 时 间
作 业 时 间
伙 零 水 教 交 食 用 電 育 際 費 錢 瓦 費 費 斯 費
29 柏拉图
• 效果确认的柏拉图制作要决
1. 2. 3. 4. 必须两个柏拉图并排,分为改善前与改善后。 收集数据的期间和对象必须一致。 季节性的变化应列入考虑。 对於改善项目以外的要因也要加以注意。
3.多能工培养
多能工是指掌握多个岗位作业技
21
QC手法——鱼骨图
开车人数增加
交通事故多
道路施工
收入提高 生活品质提高 虛榮心作祟休闲增加 休息日多 活动地点多 货车任意卸貨 购物商圈 停车位少 等候停车对伍长 收費速度慢
精益生产概念理论培训教材
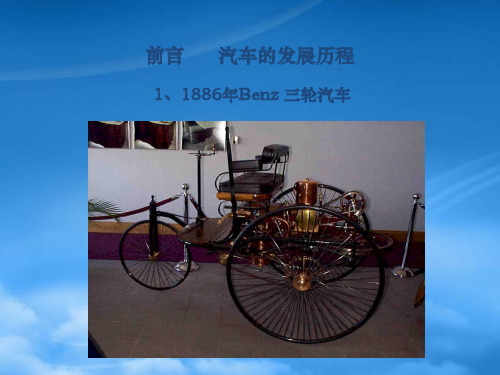
前言 汽车的发展历程
2、1890年,Sakichi Toyoda 获得了木制纺织的专利,由于市场 竞争的压力及需要,改善(KAIZEN)这种哲学思想应运而生。“没有任何机器或生产流程是不可以被改善和提高的” - Sakichi Toyoda
3、1894年Benz四轮汽车
4、1899年法国Quadricycle
5、1901年美国 Oldsmobile
6、1908年,亨利福特发明了移动式汽车装配流水线,并且将工人的 工资提高到每天5美元,这大大的提高了生产率和员工积极性。自 此,一种连续型的生产模式诞生了。 “ 我们要让所有的东西动起来,也就是让东西沿着人移动, 而不是让人随着东西运动,这就是我们最基本的观念,流水线的传 送带仅仅是众多的手段之一。 - 亨利福特:“今天和明天”
手工、大批量、精益三种生产方式的比较
序号
生产方式项目
手工生产方式
大批量生产方式
精益生产方式
1
产品特点
完全按顾客ห้องสมุดไป่ตู้求
标准化品种单一
品种多样、系列化
2
设备和工装
通用、灵活、便宜
专一、高效、昂贵
柔性高、效率高
3
分工与作业内容
粗略、丰富多彩
细致、简单、重复
较粗、多技能、丰富
4
操作工人
懂设计制造、具有高操作技艺
四、精益生产的核心
五、手工、大批量、精益三种生产方式比较
1、在精益生产方式诞生前,存在过手工生产方式及大批量生产方式。 ■ 19世纪末,法国巴黎Panhard-Levassor机床公司制造汽车,它采用的是一种 典型的手工生产方式。几乎没有两辆车是相同的! ■ 第一次世界大战后,以美国福特汽车公司为代表的大批量生产方式逐步取代以 欧洲企业为代表的手工生产方式; ■ 第二次世界大战之后,以日本丰田汽车公司为代表的精益生产方式又逐渐取代 大批量生产方式(福特公司长达10年时间只生产T型车。它的生产设备没有柔 性,如果改变品种,不仅耗资巨大,而且要停产1年!)。2、如此看来,任何一种生产方式都有一个产生、发展与衰退的过程。每种生产方式 有其特点,也有其缺陷。当社会发展到具备使某种生产方式的优势得以充分发挥 的条件时,该生产方式就占统治地位;当条件发生了变化,其优势得不到发挥或 得不到充分发挥,而缺陷成为适应市场变化的主要障碍时,这种生产方式就会衰 退。3、发展是永恒的,大批量生产方式否定了手工生产方式;精益生产方式又否定了大 批量生产方式。比较三种生产方式,精益生产方式综合了手工生产方式和大批量 生产方式的特点,克服了两者的缺点,成为新形势下最有生命力的生产方式。