脱硫增效剂说明书-OEM版
脱硫增效剂说明书

烟气脱硫增效剂(HP-525)湿法烟气脱硫工艺(FGD)是燃煤电厂控制SO2污染的主要技术,由于脱硫、除尘同时兼顾,适用性强,运行可靠,已成为我国燃煤电厂环保的主流配置。
但FGD投运以来,也暴露了一些问题:1、电煤资源紧张,煤种变化大,含硫量偏离设计值,直接影响脱硫率,甚至导致超环保限值排放。
2、因脱硫剂溶解物性差,维持浆液循环需用电量较高,在煤价上升和脱硫电价无法保本的情况下,运行成本居高不下。
3、特别因系统易结垢堵塞,被迫切换旁路,甚至发生增压风机喘振,造成运行可靠性下降。
HP-525 产品特性我公司研发的烟气脱硫增效剂(HP-525)可显著提高烟气石灰石-石膏湿法脱硫效率,实现高硫煤烟气达标排放,并较大幅度降低运行成本,延缓结垢,改善系统运行可靠性,为长周期运行提供技术支持。
该产品主要特点如下:特点运行意义脱硫效率高在不做设备升级的前提下,较大幅度提高脱硫率,并可实现中、高硫煤SO2达标。
经济性能好无须另行投资或增加设备,在各项措施选择中,有明显优势。
节能降耗相同脱硫率下:可以通过调整浆液循环泵投用配置,降低用电量,明显降低运行成本。
环保时效性水溶性好,低挥发,无害,化学稳定性好,无二次污染,不影响硫酸钙品质。
运行可靠,维护简便工艺流程精炼,简洁,无需停机检修,易掌握,易运行,运行和维护人员能快速操作。
产品组成本制剂是由复合多元酸、膦酸基高分子化合物、活性剂、助溶剂等组成的复杂混合物。
复合多元酸:在吸收塔浆液环境中提供缓冲,加快气、液膜之间的传质过程,提高反应速度;膦酸基高分子化合物:含有阻垢的活性基团,干扰晶体成长或形成疏松型多环螯合物;活化剂:降低液膜阻力,改变固、液相界面湿润性,提高界面传质效率;助溶剂:加速石灰石的溶解速度。
外观:白色结晶或粉末PH值(1%水溶液):≤6.0水不溶物含量(%):<0.1总Fe含量(mg/L):≤10产品使用方法1、将石灰配制成一定浓度的石灰石浆液,并加入一定量本制剂,机械搅拌均匀,经石灰石浆液泵打入脱硫反应塔内;或将本制剂加入地坑中,用滤液、循环液或工业水溶解,经地坑泵打入脱硫塔内。
ZC-001 脱硫增效剂

ZC-001脱硫增效剂(脱硫添加剂)一、前言在众多燃煤电厂烟气脱硫技术中,湿法烟气脱硫一直占据着主导地位,目前在世界上已经建成的脱硫装置中,湿法脱硫装置约占80%;由于石灰石价廉易得,因此在湿法烟气脱硫过程中广泛应用作为脱硫吸收剂。
尽管湿法脱硫技术的工艺成熟,脱硫效率高,但是它也存在着初期投资大(占发电机组投资的10%~30%)、运行费用高(约占发电成本的10%~20%)、容易结垢等不足。
同时由于吸收剂石灰石的溶解度小,导致液相传质差,脱硫过程中脱硫浆液的pH值波动剧烈,严重影响石灰石的利用和脱硫效率。
而且随着煤炭大量的开采和使用,煤炭品质逐渐降低,电站煤粉锅炉的烟气含硫量逐渐升高,使某些已经投运的脱硫设备即使在其设计脱硫效率下也很难达到日益严格的SO2排放标准。
因此在不对原有脱硫设备进行增容改造的前提下,合理选用ZC-001脱硫增效剂来提高设备的脱硫效率,既能达到国家节能减排的要求,又能为电厂节省投资、创造效益。
二、ZC-001脱硫增效剂产品简介ZC-001脱硫增效剂(或称脱硫添加剂,脱硫催化剂)执行标准Q/BZC001-20081、产品用途ZC-001脱硫增效剂是由不成盐氧化物与丁醇发生羰基反应而成,再配以活化剂、催化剂等而组成的高效复合增效剂,用于强化石灰石湿法FGD脱硫工艺系统中,促进石灰石浆液对SO2的吸收,显著提高烟气脱硫率:1)若电厂因掺烧高硫煤导致脱硫系统不能达标排放,加入本产品后短时间内能提高脱硫率5~10个百分点,使脱硫效率和净烟气的排放浓度达到国家规定的标准。
2)若电厂的烟气脱硫率已达到国家的排放标准,使用本产品,也同样可以实现节能减排的目的:如原本需要使用三台浆液循环泵,使用该产品后可以停用一台浆液循环泵,这样节省的厂用电和降低石灰石的消耗等综合节能费用,是药剂加入成本的一倍以上。
3)在部分脱硫设备出现异常情况时,使用该产品,能减轻或弥补因设备问题导致的烟气脱硫率下降不能达标排放,石膏氧化效果不佳、脱水困难等问题。
脱硫增效剂说明书-OEM版

脱硫增效剂产品说明书脱硫增效剂简介技术背景石灰石-石膏湿法烟气脱硫工艺因其技术成熟、脱硫效率高,吸收剂来源丰富,价格低廉,副产品可利用等特点而被广泛采用,成为目前燃煤电厂烟气脱硫应用最广泛的方法。
由于石灰石本身的性质及工艺限制,石灰石-石膏湿法烟气脱硫工艺也存在着能耗、效率等等问题。
针对以上情况,我们开发了脱硫增效剂(NOFON-FGD01型),用于优化脱硫过程,提高FGD系统的脱硫性能,使其能适应各种含硫量的煤种,降低系统能量损耗,给电厂带来良好的经济和社会效益。
脱硫增效剂的主要成份脱硫增效剂主要成份有:CaCO3表面活化剂、反应催化剂、化学隧道形成剂。
★表面活化剂:改变固液界面湿润性,提高界面传质效率;★反应催化剂:降低反应能,提高反应速度;★化学隧道形成剂:形成CaCO3的微球内部化学隧道,将反应从平面推向立体,进一步提高吸收剂利用效率和加快反应速度。
脱硫增效剂原理在脱硫过程中,石灰石与硫的反应速度受控于CaCO3的溶解速度,CaCO3在水中的溶解度较小,克服或改善CaCO3在水中的溶解问题,将会对整个脱硫工艺有较大的改善提高。
由于CaCO3在水中的溶解度较小,在吸收塔中大量的CaCO3是以微小颗粒状存在的,经研究发现,在这些微球表面,存在着双膜效应,严重影响了液体中硫的传质,采用针对CaCO3表面物性的活性剂和催化剂来减弱和消除双膜效应,同时配合化学隧道形成剂来渗透进入CaCO3的微球表面遍布的微孔和裂纹,制造无数的从微球体表面到内部的隧道,使得液体中硫的传质从这些微孔和裂纹顺利引入,大大加快了石灰石与硫的反应速度。
电镜照片:CaCO3 微颗粒形状电镜照片:CaCO3 表面的固液界面脱硫增效剂的应用效果★提高脱硫效率添加脱硫增效剂在一般情况下可提高烟气脱硫效率10%左右,这对一直达不到设计脱硫效率的机组是一种很好的解决办法。
★减少浆液循环强度在不降低脱硫效率的同时,添加脱硫增效剂后可降低浆液循环强度四分之一到三分之一,降低系统的液气比,显著降低脱硫系统能耗,并能减少烟气带出水滴对减轻后级设备的结垢堵塞有一定好处。
脱硫增效剂效果说明及经济分析

POLYTE®4080A脱硫增效剂作用效果说明1)提高脱硫效率,满足环保排放要求。
添加适当浓度POL YTE®4080A脱硫增效剂,一般情况下,可使存在超标排放的系统脱硫效率提升5%-20%。
可代替或减小脱硫系统改造,经济效益非常明显。
简单讲原有脱硫效率在80%左右,一般可提升6~15%,原有效率在90%左右,可提升3~6%,即相当于1~2台浆液循环泵处理能力。
2)提升系统处理能力,可提高燃煤硫份,降低经营成本。
添加适当浓度POL YTE®4080A脱硫增效剂,一般情况下,可使脱硫系统燃煤硫份适应范围提升20%-40%,根据目前煤炭市场硫份差价,此项可为电厂带来几千万收益。
3)大幅降低系统所需液气比,节能降耗。
在不降低脱硫效率的前提下,添加适当浓度POLYTE®4080A脱硫增效剂,一般情况下,可使系统所需液气比降低30%-50%,即可停运一到两台浆液循环泵。
此项可显著降低脱硫系统电耗(降低厂用电率0.12~0.20%)。
4)提高石灰石活性,减少石灰石损耗。
试验室数据表明添加POLYTE®4080A脱硫增效剂可缩短石灰石半消溶时间溶50%以上,大幅提升了石灰石活性。
同时,石灰石损耗一般可减少0.5%-3%。
5)提高系统氧化、结晶速率,改善吸收塔浆液及石膏品质。
POL YTE®4080A脱硫增效剂可对于吸收塔浆液中一系列化学反应起到催化作用,加快反应进行。
特别在燃烧高硫煤,原有的氧化系统及处理能力无法满足要求时,作用效果体现更加明显。
系统氧化、结晶速率提升,浆液及石膏品质得到明显改善。
6)减少系统腐蚀、结垢POL YTE®4080A脱硫增效剂不仅不会对系统产生任何副作用,而其可在一定程度上减少系统腐蚀、结垢。
通过不同材料挂片的动态模拟实验表明各种材料的腐蚀、结垢具有不同程度的减少。
其中以碳钢减少的幅度最大,腐蚀与结垢速度分别减少74%和79%。
脱硫增效剂的使用说明及脱硫工艺流程图

一、增效剂的首次加入,加入点可选两种方案:1、增效剂的首次加入点选在吸收塔地坑(吸收塔排水坑或废水收集坑):加入方式:打开搅拌,加水,同时倒入计量的脱硫增效剂,搅拌5分钟,继续加水至高位时,开启地坑泵(提升泵)打入吸收塔;每次加入脱硫增效剂300~500KG,根据总加入量,分2~5次投加。
2、增效剂的首次加入点选在滤液池或滤液水箱(低位2m)加入:加入方式:检查滤液池或滤液水箱上的搅拌处于开启状态;在进入滤液池或滤液水箱的水沟中加入,此时应保证水沟中有较多的滤液正在流入滤液池或滤液水箱;边按一定速度加入增效剂,边搅拌,再通过滤液泵打入吸收塔。
二、基础加药量及首次加药控制:首次使用时,浆液中增效剂的浓度按1000ppm左右控制:吸收塔浆液池体积=3.14×(吸收塔直径φ/2)2×浆液高度=V(m3)根据吸收塔浆液池体积计算增效剂使用量约为:吸收塔浆液池体积×1000PPM/1000=V (公斤)。
将增效剂分2~5次,每次加入量约300~500公斤,两次加药间隔2~4小时,每次加药前应将PH值调整至运行PH的上限后再加入。
三、增效剂的补加1、从滤液水箱加入:检查滤液池或滤液水箱上的搅拌处于开启状态;在进入滤液池或滤液水箱的水沟中加入,此时应保证水沟中有较多的滤液正在流入滤液池或滤液水箱;边按一定速度加入增效剂,边搅拌,再通过滤液泵打入吸收塔。
2、从吸收塔地坑加入:有浆液及其它水流入地坑时,边倒入脱硫增效剂边搅拌,继续加水至高位时,自动或手动开启地坑泵(提升泵)打入吸收塔。
当地坑容积较小、地坑液位上涨较快且脱硫增效剂加量较大时,可在30~120min内分2~4次加入。
3、后续加药规程:第一天投加基础量的脱硫增效剂后,根据机组及负荷的大小,以后每天投加一次,投加量约为80~240公斤,并根据脱硫效率的变化情况进行调整。
四、加药运行中的参数控制:PH值的控制范围(实测值):5。
脱硫添加剂
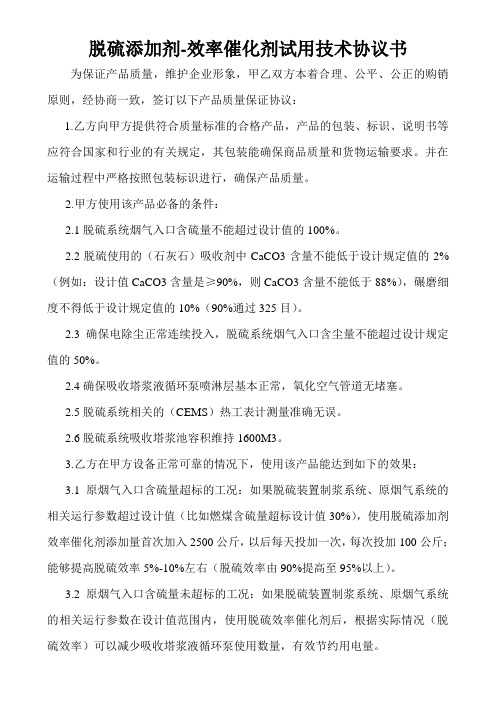
脱硫添加剂-效率催化剂试用技术协议书为保证产品质量,维护企业形象,甲乙双方本着合理、公平、公正的购销原则,经协商一致,签订以下产品质量保证协议:1.乙方向甲方提供符合质量标准的合格产品,产品的包装、标识、说明书等应符合国家和行业的有关规定,其包装能确保商品质量和货物运输要求。
并在运输过程中严格按照包装标识进行,确保产品质量。
2.甲方使用该产品必备的条件:2.1脱硫系统烟气入口含硫量不能超过设计值的100%。
2.2脱硫使用的(石灰石)吸收剂中CaCO3含量不能低于设计规定值的2%(例如:设计值CaCO3含量是≥90%,则CaCO3含量不能低于88%),碾磨细度不得低于设计规定值的10%(90%通过325目)。
2.3确保电除尘正常连续投入,脱硫系统烟气入口含尘量不能超过设计规定值的50%。
2.4确保吸收塔浆液循环泵喷淋层基本正常,氧化空气管道无堵塞。
2.5脱硫系统相关的(CEMS)热工表计测量准确无误。
2.6脱硫系统吸收塔浆池容积维持1600M3。
3.乙方在甲方设备正常可靠的情况下,使用该产品能达到如下的效果:3.1原烟气入口含硫量超标的工况:如果脱硫装置制浆系统、原烟气系统的相关运行参数超过设计值(比如燃煤含硫量超标设计值30%),使用脱硫添加剂效率催化剂添加量首次加入2500公斤,以后每天投加一次,每次投加100公斤;能够提高脱硫效率5%-10%左右(脱硫效率由90%提高至95%以上)。
3.2原烟气入口含硫量未超标的工况:如果脱硫装置制浆系统、原烟气系统的相关运行参数在设计值范围内,使用脱硫效率催化剂后,根据实际情况(脱硫效率)可以减少吸收塔浆液循环泵使用数量,有效节约用电量。
3.3不管实际原烟气参数是否超过设计值,如果脱硫系统运行正常,在使用脱硫添加剂-效率催化剂后,能够提高脱硫效率5%以上(脱硫效率由90%提高至95%以上),能够有效提高石灰石利用率。
3.4脱硫装置设备不稳定时(异常故障)在浆液中加入脱硫添加剂-效率催化剂可以提高脱硫效率5%以上(脱硫效率由90%提高至95%以上),满足环保要求,避免排放不达标事件发生。
脱硫增效剂技术要求

脱硫增效剂技术要求脱硫增效剂成分:纳米高分子聚合物钠盐分子式:C x H y(COOH)m[COONa]n缩写NaR性状:白色结晶体粉末PH值:6-7.5密度:1.1—1.3一、产品用途脱硫增效剂专用于电厂,它能有效避免介质对设备的腐蚀,强化传质,提高总反应速率、设备的稳定性和适应性。
它不但能降低表面张力并减小系统介质的粘度,增强设备中介质的分散性,而且能有效地降低介质沉降速率,从而降低介质对系统设备的的腐蚀,提高设备的利用率,减少设备的维护费用,延长设备使用寿命。
二、产品数据三、产品特点脱硫增效剂NaR的共聚物是一种粉末固体物质,溶于水后能适用于各种设备及材料。
它含有亲水官能团(-COOH)和憎水官能团(-CH3、-CH2CH3、-CnHm),所以它本身就具有一定的表面活性和良好的缓冲性能,所以脱硫增效剂NaR是一种廉价、高效的添加剂。
四、技术要求鹤壁丰鹤发电有限责任公司2×600MW机组烟气脱硫工程,采用石灰石-石膏湿法、一炉一塔脱硫装置,不设GGH,由浙江浙大网新机电工程有限公司总承包,于2008年1月投产。
2013年3月对原系统进行扩容改造,采用单塔双循环脱硫工艺,一级吸收塔浆池容积1847 m3,二级吸收塔浆池容积1462 m3。
2016年先后完成两台机组脱硫系统超低排放改造,改造后BMCR工况下,燃煤硫份为3498 mg/Nm3,脱硫出口二氧化硫排放浓度小于35mg/Nm3,脱硫效率≥99%。
脱硫增效剂使用时,机组负荷600MW时,硫份3498mg/Nm3,保证脱硫系统出口SO2排放浓度小于35 mg/Nm3的前提下可以减少一台浆液循环泵运行;当燃煤硫份达到4000 mg/Nm3时,仍能保证SO2排放浓度小于35 mg/Nm3。
如不能达到要求,则扣除本批次货款。
使用脱硫增效剂后,不能对设备内壁的衬胶或玻璃鳞片产生腐蚀,各种塔内壁、净烟道内壁、流体管道以及烟囱内壁没有点蚀的情况出现。
巴克曼脱硫增效剂介绍

案例2:石膏湿式脱硫(600MW机组)
某电厂1#机组主要的经济效益 :
• 脱硫系统状况 • 日常采用3台浆液循环泵,运行电流55A,能耗较高 • 没有备用循环泵,当发生设备故障时,无法保证脱硫系统正常运行 • 遇到突发情况被迫提高高硫煤的使用比例时,脱硫率无法达标 试验结论:
• 脱硫效率在添加BLX13735时,可停一台浆液泵而安全运行
3.506 3.638 3.791 3.969 4.211 4.357 4.752 1.869 2.209 2.388 2.565 2.606 9 10 11 12 13 14 15 16 17 18 19
效果案例二:某电厂1#机组600MW
600MW机组湿法脱硫系统 1、脱硫塔浆液容量在 1100~1300 2、浆液循环泵:3台,每台的循环量在6000~7500,一般情况开3台,循 环泵的电流在55~85安培之间
4.催化剂强化石灰石-石膏湿式脱硫 效果案例一:某电厂1#和2#机组600MW*2
燃煤状况: 入炉煤含硫量0.51~2.0%,当燃煤含硫量大于0.63%时,脱硫 效率下降,并随燃煤含硫量增加而降低,脱硫塔出口烟气含硫量能够大于 100 mg/m3,超出环保要求。 其中含硫量低于0.63%的燃煤约占15%,含硫量在0.63~1.3%的燃煤约 占总煤量的80%,含硫量超出1.3%的燃煤不足5%。
7.加药方式及加药量
不需要增加任何硬件设备,可利用吸收塔区域浆池 (也称:地坑),将药倒入坑中,加入部分回收 水,启动搅拌器,使之完全溶解后,启动区域浆池 泵将溶解后的药剂打入浆中。首次加药量较大,一 次打入
投加量一般为500至800mg/l(相对石膏出量),初次 投加800~1000mg/l(相对脱硫塔浆液保有量积量)
- 1、下载文档前请自行甄别文档内容的完整性,平台不提供额外的编辑、内容补充、找答案等附加服务。
- 2、"仅部分预览"的文档,不可在线预览部分如存在完整性等问题,可反馈申请退款(可完整预览的文档不适用该条件!)。
- 3、如文档侵犯您的权益,请联系客服反馈,我们会尽快为您处理(人工客服工作时间:9:00-18:30)。
脱硫增效剂产品说明书
脱硫增效剂简介
技术背景
石灰石-石膏湿法烟气脱硫工艺因其技术成熟、脱硫效率高,吸收剂来源丰富,价格低廉,副产品可利用等特点而被广泛采用,成为目前燃煤电厂烟气脱硫应用最广泛的方法。
由于石灰石本身的性质及工艺限制,石灰石-石膏湿法烟气脱硫工艺也存在着能耗、效率等等问题。
针对以上情况,我们开发了脱硫增效剂(NOFON-FGD01型),用于优化脱硫过程,提高FGD系统的脱硫性能,使其能适应各种含硫量的煤种,降低系统能量损耗,给电厂带来良好的经济和社会效益。
脱硫增效剂的主要成份
脱硫增效剂主要成份有:CaCO3表面活化剂、反应催化剂、化学隧道形成剂。
★表面活化剂:改变固液界面湿润性,提高界面传质效率;
★反应催化剂:降低反应能,提高反应速度;
★化学隧道形成剂:形成CaCO3的微球内部化学隧道,将反应从平面推向立体,进一步提高吸收剂利用效率和加快反应速度。
脱硫增效剂原理
在脱硫过程中,石灰石与硫的反应速度受控于CaCO3的溶解速度,CaCO3在水中的溶解度较小,克服或改善CaCO3在水中的溶解问题,将会对整个脱硫工艺有较大的改善提高。
由于CaCO3在水中的溶解度较小,在吸收塔中大量的CaCO3是以微小颗粒状存在的,经研究发现,在这些微球表面,存在着双膜效应,严重影响了液体中硫的传质,采用针对CaCO3表面物性的活性剂和催化剂来减弱和消除双膜效应,同时配合化学隧道形成剂来渗透进入CaCO3的微球表面遍布的微孔和裂纹,制造无数的从微球体表面到内部的隧道,使得液体中硫的传质从这些微孔和裂纹顺利引入,大大加快了石灰石与硫的反应速度。
电镜照片:CaCO3 微颗粒形状
电镜照片:CaCO3 表面的固液界面
脱硫增效剂的应用效果
★提高脱硫效率
添加脱硫增效剂在一般情况下可提高烟气脱硫效率10%左右,这对一直达不到设计脱硫效率的机组是一种很好的解决办法。
★减少浆液循环强度
在不降低脱硫效率的同时,添加脱硫增效剂后可降低浆液循环强度四分之一到三分之一,降低系统的液气比,显著降低脱硫系统能耗,并能减少烟气带出水滴对减轻后级设备的结垢堵塞有一定好处。
★适应广泛的煤种
可以适应高硫份的燃煤,当燃煤含硫量超过设计工况时,通过添加脱硫增效剂,使系统能适应燃用高硫煤的运行工况,从而降低发电成本。
脱硫增效剂的使用方法
★脱硫增效剂加入方法
可在浆液循环回路的任意位置加入,根据电厂实际情况提出具体方案。
推荐:首次加入系统从浆液返回管处直接加入吸收塔内;后期补充投加时可在地坑中加入。
★脱硫增效剂的用量
一般首次加入量为500-1000PPM(PPM,百万分之一),由于各厂脱硫系统各不相同,燃用煤种硫份含量不同,添加量需根据实际情况调整。
由于本产品的原理是催化增效,在脱硫反应中并不消耗,产生的损耗基本是浆液水分流失造成的,后续添加量仅考虑出石膏带水等步骤的损失和自身的衰减情况作酌量补充。
脱硫增效剂的用量由两部分组成:一是首次用量,二是补充用量。
首次用量即指在系统中首次使用或者是相隔较长时间再次使用,系统内基本不再含有增效剂的成分时的添加量,建议的添加量为600PPM,具体的范围一般在500-1000PPM之间调整(也就是千分之零点五至千分之一之间)。
一般把浆液池的体积当作总体积来计算,例如:一个600MW机组的脱硫塔浆液池直径为16m,浆液位高12m,它的体积为:
82×3.14×12=2411 m3
按600PPM计算,首次添加量为:
2411×0.6/1000×0.88(调整系数)=1.27(吨)
估算补充量有两个办法,一个是每天定时取样分析脱硫增效剂的含量,计算出每天所消耗的量,然后定时加入补充即可,例如第二天分析测试结果为560PPM,如果还是前例中所述的脱硫系统,这台机组的每天消耗量是:
2411×0.04/1000=0.096(吨)
即96公斤。
按这样的结果,加入96公斤脱硫增效剂就可以了。
还有一个较为简单的办法,就是看脱硫效果粗略的估计,先是按每天加入50公斤的添加量运行,如果脱硫效果保持原样,那就继续按这样的量维持下去,如果脱硫效率有下降,
那就按每天75公斤的量添加,相反如果脱硫效果不断上升,则可减少添加的量,以节约运行成本。
应用实例
⑴ 2010年8月~9月间,由我公司供货的脱硫增效剂分别于湖北华电A电厂及山西大唐B电厂进行了两次系统的脱硫增效剂实验。
①A电厂概况
A电厂机组(2×330MW)采用石灰石—石膏湿法烟气脱硫系统。
一炉一塔单元匹配。
本次实验前脱硫系统三台循环泵必须同时运行且系统PH值达到5.8以上时,系统脱硫效率在87%-93%之间波动,故能耗较高,石灰石用量大,系统设备始终处于满负荷运行。
②B电厂概况
B电厂为2×600MW直接空冷脱硫燃煤发电机组。
根据现场观察及了解可知,因机组设计原因,当入口SO2浓度达到3300 mg/m3 以上时,会造成脱硫系统供浆量严重不足,脱硫效率很难稳定维持在90%以上,从而无法达到环保排放的要求。
⑵实验过程简介
1、在A电厂FGD脱硫系统加入100公斤脱硫增效剂后(使吸收塔内增效剂浓度达到500ppm)和不加前脱硫效率的对比曲线和持续作用时间.
添加增效剂500ppm浓度时脱硫率与作用时间的变化
86
8890929496980.5
4
10
24
时间(小时)
脱硫效率(%)
数据分析
FGD 入口SO2浓度在2100mg/Nm3。
在维持吸收塔原脱硫效率基础上,加入200公斤脱硫增效剂(使吸收塔内增效剂浓度达到500ppm ),配合合理供浆,吸收塔脱硫效率立即快速提升;半小时后,脱硫效率即提高6%以上(对于脱硫效率小于90%的FGD 系统,加脱硫增效剂后脱硫效率或将提高10%以上)。
特别是随着时间的变化,在加入500ppm 增效剂24小时后,仍能够达到较高的脱硫效率。
这说明增效剂的加入,显著提高了脱硫效率,并且能够持续稳定的发挥作用达24小时以上(理论上可维持64小时)。
2、在B 电厂FGD 脱硫系统加入500ppm 脱硫增效剂后和不加前脱硫效率和循环浆液ph 值之间的对比曲线。
数据分析:
FGD 入口SO 2浓
度在3300mg/Nm 3。
塔浆液PH 值对脱硫效率影响显著,随着PH 值增加,脱硫效率增大。
添加增效剂500ppm浓度时对PH值及供浆的影响0
20406080100120
4.8
5.1
5.4 5.7
6
浆液PH值
供浆量/h
加入增效剂后,在保证脱硫效率的前提下,吸收塔浆液PH值保持在5.2-5.8的合理范围内波动,从而减少补浆量,节约大量石灰石。
而且脱硫增效剂的加入,有稳定浆液PH值的作用,从而为脱硫反应提供更好的环境。
结论分析
关于脱硫增效剂,通过数据分析,可以得出以下结论:
1、显著提高FGD系统脱硫效率,提效一般可达6%-10%以上。
这是脱硫增效剂的主要功能,SPRZ-101脱硫增效剂可以加速石灰石反应速度,提高了石灰石利用率,从而提高脱硫效率。
添加30分钟以后即可见效,一次添加持续作用达到24小时以上。
2、促进脱硫系统适应入口二氧化硫浓度的较大变化。
脱硫增效剂的使用,可以适应因煤质等变化引起的入口SO2浓度变化。
3、对浆液PH值具有缓冲作用,减少供浆量,节约石灰石。
脱硫增效剂的使用,可以缓冲气液界面上因SO2 溶解而导致的PH值降低,在保证脱硫效率稳定的前提下,可以减少供浆量,节约石灰石。
4、可促进石灰石的溶解,使CaCO3完全反应,防止设备结垢和堵塞。
脱硫增效剂的使用可以加快CO32-的传质速率,从而加快了石灰石的溶解速率,提高了石灰石利用率,并改变了晶体产物的结构,特别是钙硫比(Ca/S)的降低,使塔浆液浓度也降低,减少了淤积,起到阻垢防腐作用。
5、在保证脱硫系统稳定,效率达标的情况下,可停一台循环泵,降低脱硫塔动力消耗。
经济性分析
使用脱硫增效剂后,节能效果显著。
以某电厂2×330MW机组为例。
(实际机组容量越大,节能越显著。
)
1、平均每天节约石灰石量为32吨,故FGD系统年净节约石灰石费用992800元。
(以石灰石85元/吨计算)
2、平均每天节约水量为30吨,FGD系统年节约水费为13140元。
3、平均停一台循环泵(功率为500KW,按照每天停泵16小时,电价0.3元/度计算),年节电为715400元。
4、FGD系统设备维修年度预期节约维修费89500.00元。
年总节约费用合计:1810840元。
注意:因各个电厂工况不同,此计算仅供参考!
脱硫增效剂的安全因素
脱硫增效剂不燃不爆,对人体无毒无害,储存于阴暗干燥场所,有效期保存期达24个月。
使用操作时要戴口罩、防护眼镜和手套。