压力容器制造工艺卡
压力容器工艺过程流转卡

件号
第
3
页
1
共 13
页
控制 标记
序 号
工序
工艺内容及技术要求
R
1
核查
看 清
有裂纹、凹凸、分层、表面无锈蚀。检验员签字确认后划线下料
2
划线
毛 坯 标
W
3 4 5
检验 定位
记 检 验 对
焊 焊接
拼 对 拼 笔
标
φ
划
2
线
1±1㎜ 错边量
W
6 7
检验
检 验 委
托
H
8
检验
1 )
内表面形状偏差:外凸≤1.25% Di 即≤ 25.00 mm
坡口表面不得有裂纹、分层、夹渣等缺陷,清理坡口两侧不小于20㎜范围内污物,打磨见金属光
泽。
6 滚圆 按要求对钢板进行卷筒制作,要求筒节内径Φ444mm。
7
定位 焊
对卷筒完毕后的件进行定位焊,焊道长度10~20mm,间隔50mm,要求错边量b≤3mm,对接间隙
1±1㎜;
W
8
焊接
对筒节的纵焊缝分别进行焊接,清除焊接熔渣及飞溅物,焊接参数见对应的焊接工艺卡,焊接完 成后,
进行标识移植。
W 4 检验 按图纸及工艺检查下料几何尺寸。
W 5 坡口 进行坡口加工,要求按图加工单边V型坡口,坡口角度35°±2°,钝边高度:1±1mm。 坡口表面不得有裂纹、分层、夹渣等缺陷,清理坡口两侧不小于20㎜范围内污物,打磨见金属光 泽。
6 卷制 按要求对钢板进行卷筒制作,要求卷制零件内径Φ2036mm。
文件编号:ZB2005
产品编号 R20-01
管口位置 共
压力容器制造工艺检验流转卡

铆 工
划线尺寸Φ=
坡口角度α°
坡口钝边P
标记移植
划线尺寸Φ=
坡口角度α°
坡口钝边P
标记移植
E
3
对 接
点 焊
(1)按标号组对。
(2)对坡清理坡口及其两侧各20mm范围内溶渣飞边、除锈 、去污
(3)拼板的对口错边量b不应大于材料厚度δs的10%,且不大于1.5mm。
(4)点固封头拼板。
焊缝代号
A -----筒体及接管等纵缝
B -----筒体及接管等环缝
C-----法兰、平板与筒体及接管等焊缝
D -----接管、凸缘、补强圈等与壳体的焊缝
E -----非受压元件与受压元件的焊缝
BDJL6-03
BDJL6-04
某某
有限公司
容器排版图
名称
压缩空气罐
型号
DN2200
材质
Q345R
编号
R15-0xx
批准手续
返修次数
增探比例
返修结论
批准手续
返修次数
增探比例
返修结论
焊接责任人
签字
E
质控符号:E----检查点H----停止点
筒体制造工艺检验流转卡
BDJL6-06
产品编号
XXXX
材料
Q345R
材料移植号
代用材料
质
控
符号
零部件名称
筒体
规格
DN2200X12
件号
12-2
件数
1
状态
序号
工序
名称
工序内容及工艺要求
质控符号:E----检查点 H----停止点
筒体制造工艺检验流转卡
压力容器制造工艺卡检验过程卡
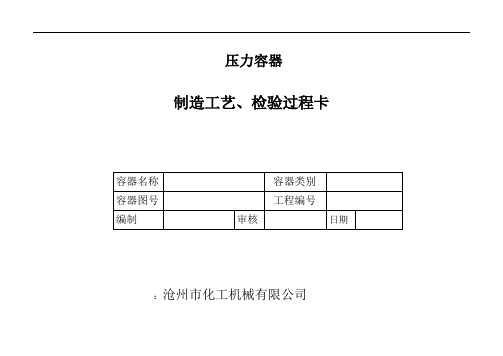
压力容器
制造工艺、检验过程卡
:沧州市化工机械有限公司
GY表3 封头制造工艺、检验过程卡
GY表3 筒节制造工艺、检验过程卡
GY表3 筒节制造工艺、检验过程卡
GY表3 人孔法兰制造工艺、检验过程卡
GY表3 人孔法盖制造工艺、检验过程卡
GY表3 人孔筒节制造工艺、检验过程卡
GY表3 管板制造工艺、检验过程卡
GY表3 容器法兰制造工艺、检验过程卡
GY表3 膨胀节制造工艺、检验过程卡
GY表3 长颈法兰与接管组焊工艺、检验过程卡
GY表3 储存容器总装工艺、检验过程卡
GY表3 储存容器总装工艺、检验过程卡
GY表3 储存容器总装工艺、检验过程卡共2页第2页
GY表3 换热器总装工艺、检验过程卡
GY表3 换热器总装工艺、检验过程卡
GY表3 水压试验工艺、检验过程卡
GY表3 气压试验工艺、检验过程卡
GY表3 气液组合压力试验工艺、检验过程卡
GY表3 气密性试验工艺、检验过程卡
GY表3 氨检漏试验工艺、检验过程卡
GY表3 M36以上(含M36)容器主螺栓制造工艺、、检验过程程卡
GY表3 公称直径≥250接管制造工艺、检验过程卡
GY表3 换热管制造工艺、检验过程卡
GY表3 补强圈制造、检验过程卡
GY表3 产品试板制作、试验、检验过程卡
GY表3 产品酸洗钝化工艺、检验过程卡
GY表3 产品酸洗钝化工艺、检验过程卡
GY表3 除锈、喷漆过程检验卡。
压力容器工艺工序过程卡

产品名称:Ф1200×5104反应釜
产品编号:06WY1—601
编制:王鹉2005年12月14日
校审:2005年12月15日
批准:张中伟2005年12月16日
中国长城铝业公司建设公司
NO.2
产品名称
Ф1200反应釜
压力容器主要零部件制造工艺(工序)过程卡
容器类别
Ⅱ类
件号
1
产品编号
材质、标记
3.实测钢板厚度,用超声波逐张进行检验,Ⅲ级合格。
厚度
二
筒节排料划线
1.按(封头内径+55)×3.14159展开长度划下料线、检查线、加工线,划线公差≯1.5mm,宽误差≯1.5mm,对角线误差≯2mm,长=3943mm,宽=2100mm,对角线=4467mm。
划线尺寸(长)
划线尺寸(宽)
06WY1--601
主材牌号
16MnR
规格
φ1200×55
图号
06WY1--0
部件名称
首节筒体
序号
工序
工艺内容与技术要求
工装
设备
检验项目
自检值
操作者
专检值
检验员
时间
备注
一
领料
检验
1.检查材料表面状况,不允许有裂纹、结疤、折叠、夹渣、分层、麻坑等缺陷。
表面质量
2.核对出厂标记与质量证明书是否一致,打材料标记,填写记录。
2.移植材料标记,打产品编号钢印。
标记移植
3.检查员复验划线尺寸、打确认钢印。
尺寸
4.确认
检验责任工程师确认:
三
下料
按下料线切割下料,清除毛刺、熔渣。
半自动切割机
压力容器焊接工艺过程卡

卷筒
将板材卷成圆筒
卷弯至筒体要求的尺寸
CDW11-8 2500B上调式三辊卷板机
7
装配
将卷制的筒体进行装配,并固定好
无错边,定位精确,坡口间距符合标准约2mm
螺旋拉紧器,夹具
8
纵缝焊接
将装配好的筒节进行焊接
无弧坑、咬边、裂纹等缺陷,焊缝平整、均匀,余高约为1.5mm缝宽约8mm
MAG半自动焊机
9
矫圆
将筒节进行形状矫正处理
筒节横截面符合设计尺寸要求
三辊卷板机
10
检验
对焊缝进行无损检验
符合焊缝质量国家标准Ⅱ级
X射线探伤装置
X射线
压力容器主要受压元件工艺过程卡
产品编号
产品名称
图号
容器类别
零件名称
件号
零件图号或标准号
数量
规格
材质
材料标记
责任师确认
压力容器
筒节
2
序号
工序名称
工作内容
质量要求
加工设备
主要检验工具
检查结果
操作者
检查员
接受人
交检日期
备注
1
材料复检
检验材料是否符合质量要求,选出拟定规格板材
确保材料符合所用的要求1800 6400 12料两块
材料质证书
化学成分实验设备
2
表面预处理
对板材进行机械除锈、喷丸处理等
要求表面无锈迹,且材料达到所要求的强度
GYX-nM预处理装置和喷丸机
3
下料
按排版图尺寸下料
等离子切割机
4
边缘加工
对板材边缘进行刨边,加工出符合要求的V型坡口
坡口表面平整,无裂纹、划痕
工艺卡模板

Q345R正火
编制: 年 月 日 审核: 年 月 日
表:1-4-1
陕 西 化 建 设 备 制 造 公 司
椭圆封头工序流转卡1
产品图号
51-0686-1
产品名称
氮气储罐
件 号
1
产品编号
2019-55-C14
材料及状态
Q345R正火
序
号
工序
部门
工序内容及技术要求
设备
工装
检验数据
操作者
检验员
日期
滚轮架
b=
E=
11
焊接
铆焊
要求同4条。
12
检测
探伤室
按探伤工艺对B类环焊缝分别进行100%检测,按JB/T4703.2-2019 标准,Ⅱ级合格。
射线机
编制: 年 月 日 审核: 年 月 日
表:1-5-2
陕 西 化 建 设 备 制 造 公 司
筒体工序流转卡2
产品图号
51-0686-1
产品名称
氮气储罐
产品编号:2019-55-C14
陕 西 化 建 设 备 制 造 公 司
参加人数:
主持人:
有关图纸名称及图号:
51-0686-1
技术交底内容:
1、本设备的制造、检验、验收按GB150-2019《钢制压力容器》、《固定式压力容器安全技术监察规程》TSG R0004-2009、《钢制压力容器焊接规程》JB/T4709-2000、《钢制化工容器制造技术要求》HG20584-2019进行。
卷板机
e=
7
检测
探伤室
按探伤工艺对A类纵焊缝进行100﹪RT检测,按JB/T4730.2-2019标准,Ⅲ级合格。
压力容器制造工序过程卡
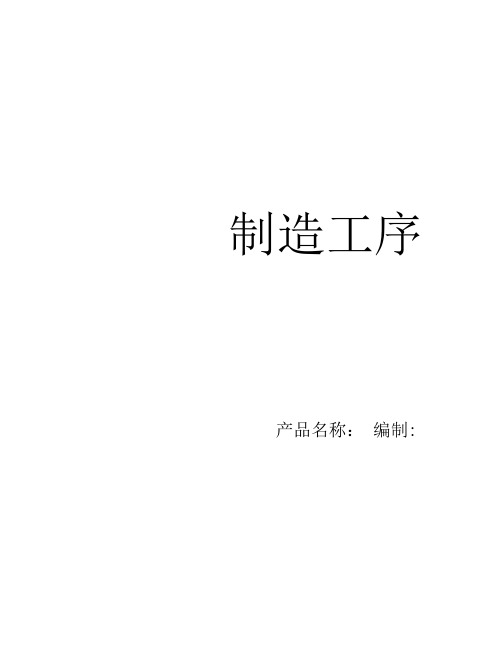
制造工序产品名称:编制:
过程卡制造编号:审核:
制造工序过程卡
注:不锈钢可用等离子体切割编制:年月曰审核:年月日
制造工序过程卡
产品名称:序号:共页第2页
注:不锈钢可用等离子体切割编制:年月曰审核:年月日
序号:共页第4页
产品名称:
编制:年月曰审核:年月日
编制:年月曰审核:年月日
产品名称:序号:共页第7页
编制:年月曰审核:年月日
制造工序过程卡
产品名称:序号:共页第8页
注:不锈钢可用等离子体切割编制:年月曰审核:年月日
序号: 共页第9页
制造工序过程卡
产品名称:
产品名称:序号:共页第10页
编制:年月曰审核:年月日
产品名称:序号:共页第11页
编制:年月曰审核:年月日
产品名称:序号:共页第12页
编制:年月曰审核:年月日
平焊管法兰一览表
编制:年月曰审核:年月日
组装工序过程卡
编制:年月曰审核:年月日
接管安装焊接工序过程卡产品名称:
编制:年月曰审核:年月日
产品名称:序号:共页第页
编制:年月曰审核:年月日
产品名称:序号:共页第页
编制:年月曰审核:年月日
压力容器外观及几何尺寸检验报告产品编号:共页第18页
产品编号: 胀管操作记录: 胀管机型号:
不锈钢产品酸洗钝化处理工艺卡。
压力容器制造工艺卡检验过程卡
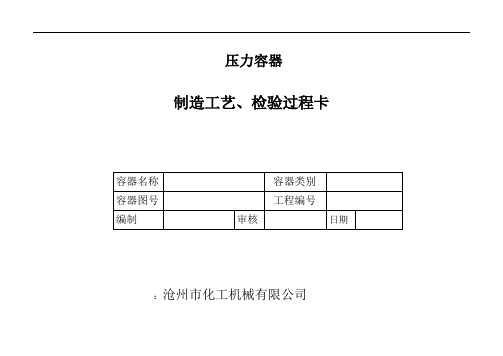
压力容器
制造工艺、检验过程卡
:沧州市化工机械有限公司
GY表3 封头制造工艺、检验过程卡
GY表3 筒节制造工艺、检验过程卡
GY表3 筒节制造工艺、检验过程卡
GY表3 人孔法兰制造工艺、检验过程卡
GY表3 人孔法盖制造工艺、检验过程卡
GY表3 人孔筒节制造工艺、检验过程卡
GY表3 管板制造工艺、检验过程卡
GY表3 容器法兰制造工艺、检验过程卡
GY表3 膨胀节制造工艺、检验过程卡
GY表3 长颈法兰与接管组焊工艺、检验过程卡
GY表3 储存容器总装工艺、检验过程卡
GY表3 储存容器总装工艺、检验过程卡
GY表3 储存容器总装工艺、检验过程卡共2页第2页
GY表3 换热器总装工艺、检验过程卡
GY表3 换热器总装工艺、检验过程卡
GY表3 水压试验工艺、检验过程卡
GY表3 气压试验工艺、检验过程卡
GY表3 气液组合压力试验工艺、检验过程卡
GY表3 气密性试验工艺、检验过程卡
GY表3 氨检漏试验工艺、检验过程卡
GY表3 M36以上(含M36)容器主螺栓制造工艺、、检验过程程卡
GY表3 公称直径≥250接管制造工艺、检验过程卡
GY表3 换热管制造工艺、检验过程卡
GY表3 补强圈制造、检验过程卡
GY表3 产品试板制作、试验、检验过程卡
GY表3 产品酸洗钝化工艺、检验过程卡
GY表3 产品酸洗钝化工艺、检验过程卡
GY表3 除锈、喷漆过程检验卡。
- 1、下载文档前请自行甄别文档内容的完整性,平台不提供额外的编辑、内容补充、找答案等附加服务。
- 2、"仅部分预览"的文档,不可在线预览部分如存在完整性等问题,可反馈申请退款(可完整预览的文档不适用该条件!)。
- 3、如文档侵犯您的权益,请联系客服反馈,我们会尽快为您处理(人工客服工作时间:9:00-18:30)。
5
组焊
铆焊
补强板与壳体紧密贴合后点固,按要求施焊。
6
试验
生产科
补强圈与壳体焊接后,以0.5MPa压缩空气作试漏检查。
空压机
编制 年 月 日 审核 年 月 日
艺表—04
产品编号
补强圈制造卡
共2页
第1页
产品名称
单台数量
产品图号
件号
材料
材料状态
件 号
D
D1δ材料数量产品编号法兰制造卡
共页
第页
产品名称
单台数量
超声仪
7
热处理
生产科
拼接焊缝按热处理工艺作焊后热处理。
8
校平
铆焊
校正法兰上下平面,要求平面度≤±3.0mm,棱角度E≤mm。
9
车
金工
按零件图车成, 要求密封面粗造度 ,厚度mm;作材料标记移植。
10
钻孔
金工
按螺栓孔中心圆直径φmm划线,钻孔φ。要求螺栓孔 中心圆直径偏差 ±1.0mm, 相邻二螺栓孔弦长允差≤±0.5mm,任意二
9
焊接
铆焊
要求同4条。
10
检测
探伤室
按探伤工艺对B类环焊缝进行%RT检测,按 标准 级合格。
射线机
编制 年 月 日 审核 年 月 日
产品编号
补强圈制造卡
共2页
第2页
产品名称
单台数量
产品图号
件号 材 料 材料状态
序 号
工序
承制 单位
工序内容及技术要求
设备 工装
检验数据
操作者
日期
检验员
日期
1
备料
库房
库房备有材质证明书、检验合格的δ=mm,钢板,要求
产品编号
椭圆封头制造卡
共2页
第1页
产品名称
单台数量
产品图号
件号
材料
材料状态
1
备料
库房
库房备有材质证明书、检验合格的δ=mm,钢板,要求材
料表面不得有裂纹、结疤、夹渣、分层等缺陷;核对材料标记,实测钢板厚度。
2
下料
铆焊
按封头理论展开尺寸及排板要求划线,库管员作好材料标记移植,检验员检查确 认后,按线下料。
材料表面不得有裂纹、 结疤、 夹渣、 分层等缺陷; 核对材料标记, 实测钢板厚度。
2
下料
铆焊
按图纸尺寸及排板要求划线,库管员作好材料标记移植,检验员检查确认后,按 线下料。
氧炔
3
煨形
铆焊
按要求滚卷钢板,圆弧部分应与所补强的壳体紧密贴合。
卷板机
4
钻孔 攻丝
金工
在补强板下部、距边缘15mm处划线,钻底孔φ8.4mm,丝锥攻丝M10—7H。
产品图号
件号 材 料 材料状态
序 号
工序
承制 单位
工序内容及技术要求
设备 工装
检验数据
操作者
日期
检验员
日期
1
备料
库房
库房备有材质证明书、检验合格的δ=mm,钢板,要求
材料表面无可见缺陷; 经超声波检测无分层缺陷; 核对材料标记, 实测钢板厚度。
2
下料
铆焊
按图纸尺寸及排板要求划线,内外径预留mm机加余量;分瓣拼焊时 按分 瓣划线。库管员作好材料标记移植,检验员检查确认后,按线下料。
射线机
7
坡口
铆焊/金 工
按零件图要求加工封头端面坡口。
8
酸洗
生产科
不锈钢封头作酸洗钝化处理。
..编制年 月 日 审核 年 月 日
产品编号
筒体制造卡
共页
第页
产品名称
单台数量
产品图号
件号 材 料 材料状态
序 号
工序
承制 单位
工序内容及技术要求
设备 工装
检验数据
操作者
日期
检验员
日期
1
备料
库房
库房备有材质证明书、检验合格的δ=mm,钢板,要求材
氧炔
3
组对
铆焊
按焊接工艺加工坡口,清理坡口两侧30mm范围内污物;拼接焊缝组对错边量b≤mm,棱角度E≤mm。
4
焊接
铆焊
按焊接工艺施焊;清除熔渣及焊接飞溅,补焊凹坑、咬边、弧坑等缺陷并修磨;
打焊工钢印;填写施焊记录;检验员检查外观质量。
6
检测
探伤室
按探伤工艺对拼接焊缝进行100%超声检测,按JB4730标准Ⅰ级合格。
氧炔
3
焊接
铆焊
按焊接工艺施焊;将封头起弧段焊缝余高修磨平,但不得低于母材。
4
外协
供应科
库管员在封头坯料上作原材料钢印标记;工艺员填写封头外协委托单;供应科持 委托单联系外协冲压。
5
入厂 检验
检验科
⑴检查封头合格证内容是否完整;检查封头原材料标记。
⑵检查封头几何尺寸和表面形状:
内表面形状偏差:外凸≤1.25%Di即≤mm,内凹≤0.625%Di即
铆焊
筒体校圆,要求最大最小直径差e≤mm,棱角度E≤mm。
卷板机
6
检测
探伤室
按探伤工艺对纵焊缝进行%RT检测,按 标准 级合格。
射线机
7
理化
理化室
焊接试板进行机械性能试验,拉伸 件,弯曲 件,冲击 件。
试验机
8
组对
铆焊
按筒体布板图要求组对各筒节,定位焊要求同4;筒体B类环缝组对错边量
b≤mm,棱角度E≤mm;筒体直线度≤H/1000即≤mm。
料表面不得有裂纹、结疤、夹渣、分层等缺陷;核对材料标记,实测钢板厚度。
2
下料
铆焊
按实测封头外圆周长计算展开尺寸, 按排板要求划线, 库管员作好材料标记移植, 检验员检查确认后,按线下料;同时下试板、引弧板、灭弧板。
筒体理论下料尺寸为: 。
氧炔
3
卷筒
铆焊
按工艺规程要求滚卷钢板,筒体A类焊缝组对错边量b≤mm,棱角度
≤mm;总深度公差为(-0.2~0.6)%Di即mm;最小厚度不
得小于mm;直边倾斜度向外≤1.5mm,向内≤1.0mm;直边高度公差
为(-5~10)%h即mm;直径公差为mm;外周长公
差为mm;直边部分不得有纵向皱折;封头表面光滑无突变。
⑶作封头入厂检验标记、材料标记移植。
测厚仪
6
检测
探伤室
按探伤工艺对封头拼接焊缝进行100%RT检测, 按标准 级合格。
螺栓孔弦长允差≤±1.0mm。
编制 年 月 日 审核 年 月 日
产品编号
盖制造卡
共页
第页
产品名称
单台数量
产品图号
件号 材 料 材料状态
序 号
工序
承制 单位
工序内容及技术要求
设备 工装
检验数据
操作者
日期
检验员
日期
1
备料
库房
库房备有材质证明书、检验合格的δ=mm,钢板,要求
材料表面不得有裂纹、 结疤、 夹渣、 分层等缺陷; 核对材料标记, 实测钢板厚度。
2
下料
铆焊
按图纸尺寸φmm及排板要求划线,内外径预留mm机加 余量;库管员作好材料标记移植,检验员检查确认后,按线下料。
氧炔
3
车
金工
车外圆到φmm;作材料标记移植; 按凸缘直径φmm车密 封面;要求密封面粗造度 ,厚度mm。
4
钻孔
金工
按中心圆直径φmm划线,钻孔φ。要求螺栓孔中心圆 直径偏差 ±1.0mm,相邻二螺栓孔弦长允差≤±0.5mm,任意二螺栓孔
E≤mm。筒体纵缝延长部位点固试板、 引熄弧板, 定位焊长度20~50mm,
间距150~200mm。
卷板机
4
焊接
铆焊
按焊接工艺要求加工坡口,坡口两侧30mm范围内清理污物,然后按焊接工艺施 焊;清除熔渣及焊接飞溅,补焊凹坑、咬边、弧坑等缺陷并修磨;打焊工钢印; 填写施焊记录;检验员检查外观质量。
5
校圆