不锈钢真空吸滤网冲压工艺及模具设计
冲压成型工艺及模具设计(毕业设计)
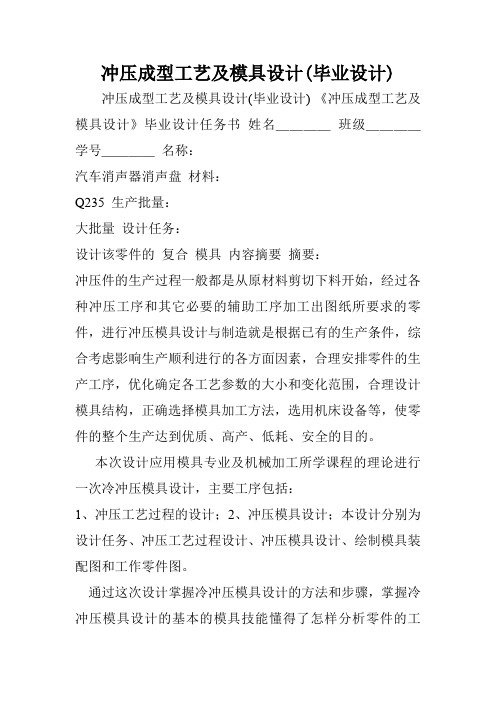
冲压成型工艺及模具设计(毕业设计)冲压成型工艺及模具设计(毕业设计) 《冲压成型工艺及模具设计》毕业设计任务书姓名____班级____学号____名称:汽车消声器消声盘材料:Q235 生产批量:大批量设计任务:设计该零件的复合模具内容摘要摘要:冲压件的生产过程一般都是从原材料剪切下料开始,经过各种冲压工序和其它必要的辅助工序加工出图纸所要求的零件,进行冲压模具设计与制造就是根据已有的生产条件,综合考虑影响生产顺利进行的各方面因素,合理安排零件的生产工序,优化确定各工艺参数的大小和变化范围,合理设计模具结构,正确选择模具加工方法,选用机床设备等,使零件的整个生产达到优质、高产、低耗、安全的目的。
本次设计应用模具专业及机械加工所学课程的理论进行一次冷冲压模具设计,主要工序包括:1、冲压工艺过程的设计;2、冲压模具设计;本设计分别为设计任务、冲压工艺过程设计、冲压模具设计、绘制模具装配图和工作零件图。
通过这次设计掌握冷冲压模具设计的方法和步骤,掌握冷冲压模具设计的基本的模具技能懂得了怎样分析零件的工艺性,怎样确定工艺方案,了解了模具的基本结构,提高了计算能力,绘图能力,熟悉了规范和标准,同时各科相关的课程都有了全面的复习。
此次模具设计目的在于通过自己设计,进行一次完整的过程训练,从模具的设计出发,再到模具主要零件的加工工艺,使自己初步具备综合运用所学专业知识解决工程实际问题的方法能力。
关键词:汽车消声器消声盘汽车消声器消声盘冲压模具设计第二章冲压工艺过程设计 2.1 冲压工艺性分析该零件的外形简单,形状规则,材料为Q235钢板,厚度t=1mm,良好的冲压性能,适合冲裁。
工件结构相对简单,有一个φ22mm的孔和三个φ4.5mm 的孔,最小壁厚为18mm>2t(φ6φ155圆之间的壁厚)。
孔与孔之间的最小距离为a=15mm>2t(φ94圆上的φ6与φ6之间的孔距) 。
工件尺寸全部为自由公差,可看做IT14级尺寸精度较低,普通冲裁完全能满足要求。
机械工程及自动化专业毕业设计论文-超滤机封头的冲压工艺及模具设计

大学毕业设计题目专业班级学生学号指导教师二〇一四年五月五日1前言1.1国内外研究动态和发展趋势:近年来,我国冲压模具制造在质量、技术和能力等方面都有了很大发展,但与国际经济需求和世界先进水平相比,差距仍很大。
随着我国成为世界制造业的中心,电子信息技术中的电子元器件和汽车部件越来越多的成为中国制造,而模具是机械、电子、汽车、家电等工业产品的基础工艺装备,作为工业基础,模具的质量、精度、寿命对其它工业的发展起着十分重要的作用,在国际上称为“工业之母”。
许多先进的模具技术应用不够广泛等等,致使相当一部分大型、精密、复杂和长寿命模具依赖进口。
而模具制造是整个链条中最基础的要素之一,模具制造技术现已成为衡量一个国家制造业水平高低的重要标志,并在很大程度上决定企业的生存空间。
这些年来,虽然中国制造的模具产品,其技术和性能指标等方面接近了世界的高水平,但是还是应该继续努力,逆水行舟不进则退,我们应该更多的运用中国创造来弥补,创国内的世界名牌。
因此,我国冲压设备行业和企业需以战略的思路和有效的措施应对当前的机遇和挑战。
随着科学技术的不断进步和工业生产的迅速发展,许多新技术、新工艺、新设备、新材料不断涌现,因而促进了冲压技术的不断革新和发展。
其主要发展如下:(1)工艺分析计算的现代化。
它将与现代数学、计算机技术相互联系,对加工零件进行计算机模拟和有限元分析,达到预测某一工艺方案对零件成形的可能性与成形过程中可能会发生的问题,供设计人员修改和选择。
(2)模具计算辅助设计、制造与分析(CAD/CAM)的研究和应用将极大地提高模具制造效率,提高模具质量,使模具设计与制造技术实现一体化。
(3)模具的标准化、商品化、机械化及专业化自动生产。
1.2 选题的目的及意义:(1)综合运用冷冲模课程和其它有关先修课程的理论及生产实践的知识去分析和解决模具设计问题,并使所学专业知识得到进一步巩固和深化。
(2)学习模具设计的一般方法,了解和掌握常用模具整体设计、零部件的设计过程和计算方法,培养正确的设计思想和分析问题、解决问题的能力,特别是总体设计和计算的能力。
不锈钢滤芯制作工艺

不锈钢滤芯制作工艺
哎哟喂,说起这不锈钢滤芯的制作工艺,那可真是讲究得很嘞!首先,得选料,得是那种高品质、耐腐蚀的304不锈钢,才能保证滤芯子经久耐用,不生锈,水过起来清爽得很。
选材好了,接下来是切割。
师傅们手艺精,激光切割机一开,唰唰唰,精准得很,那不锈钢片儿跟切豆腐似的,薄厚均匀,边角光滑。
然后嘛,就是冲压成型。
这步关键得很,温度、压力都得拿捏得刚刚好,才能把那不锈钢片儿变成一个个精致的滤网格子,密不透风,又透气透水,玄妙得很。
成型之后,还得清洗、抛光。
用水一冲,油渍污渍全跑光,再用抛光机一打磨,嘿,那滤芯子亮堂堂的,跟镜子似的,看着就舒服。
最关键的一步来了——焊接。
这可是个技术活,得用专门的焊接设备,把滤网格子一个个焊接起来,还不能有漏焊、虚焊,不然漏水了就白搭了。
师傅们都是火眼金睛,焊得严丝合缝,质量杠杠的。
最后一步,就是检测和包装了。
每个滤芯都要经过严格的质量检测,确保没有瑕疵才能出厂。
包装也是精心设计的,防潮防摔,让滤芯安安全全地送到客户手上。
总而言之,这不锈钢滤芯的制作工艺,每一步都马虎不得,只有这样,才能做出让大家都满意的好产品!。
不锈钢薄板高密度小孔冲压加工及模具优化设计策略分析
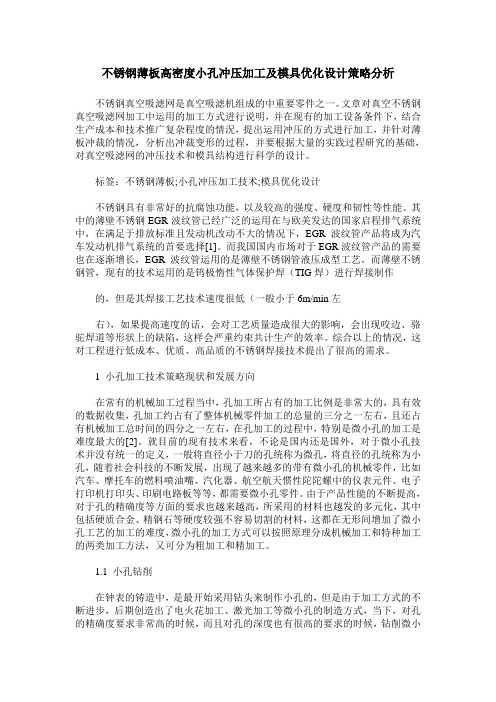
不锈钢薄板高密度小孔冲压加工及模具优化设计策略分析不锈钢真空吸滤网是真空吸滤机组成的中重要零件之一。
文章对真空不锈钢真空吸滤网加工中运用的加工方式进行说明,并在现有的加工设备条件下,结合生产成本和技术推广复杂程度的情況,提出运用冲压的方式进行加工,并针对薄板冲裁的情况,分析出冲裁变形的过程,并要根据大量的实践过程研究的基础,对真空吸滤网的冲压技术和模具结构进行科学的设计。
标签:不锈钢薄板;小孔冲压加工技术;模具优化设计不锈钢具有非常好的抗腐蚀功能,以及较高的强度、硬度和韧性等性能。
其中的薄壁不锈钢EGR波纹管已经广泛的运用在与欧美发达的国家启程排气系统中,在满足于排放标准且发动机改动不大的情况下,EGR波纹管产品将成为汽车发动机排气系统的首要选择[1]。
而我国国内市场对于EGR波纹管产品的需要也在逐渐增长,EGR波纹管运用的是薄壁不锈钢管液压成型工艺。
而薄壁不锈钢管,现有的技术运用的是钨极惰性气体保护焊(TIG焊)进行焊接制作的,但是其焊接工艺技术速度很低(一般小于6m/min左右),如果提高速度的话,会对工艺质量造成很大的影响,会出现咬边、骆驼焊道等形状上的缺陷,这样会严重约束共计生产的效率。
综合以上的情况,这对工程进行低成本、优质、高品质的不锈钢焊接技术提出了很高的需求。
1 小孔加工技术策略现状和发展方向在常有的机械加工过程当中,孔加工所占有的加工比例是非常大的,具有效的数据收集,孔加工约占有了整体机械零件加工的总量的三分之一左右,且还占有机械加工总时间的四分之一左右,在孔加工的过程中,特别是微小孔的加工是难度最大的[2]。
就目前的现有技术来看,不论是国内还是国外,对于微小孔技术并没有统一的定义,一般将直径小于刀的孔统称为微孔,将直径的孔统称为小孔,随着社会科技的不断发展,出现了越来越多的带有微小孔的机械零件,比如汽车、摩托车的燃料喷油嘴、汽化器、航空航天惯性陀陀螺中的仪表元件、电子打印机打印头、印刷电路板等等,都需要微小孔零件。
冲压工艺过程设计与冲压模具设计
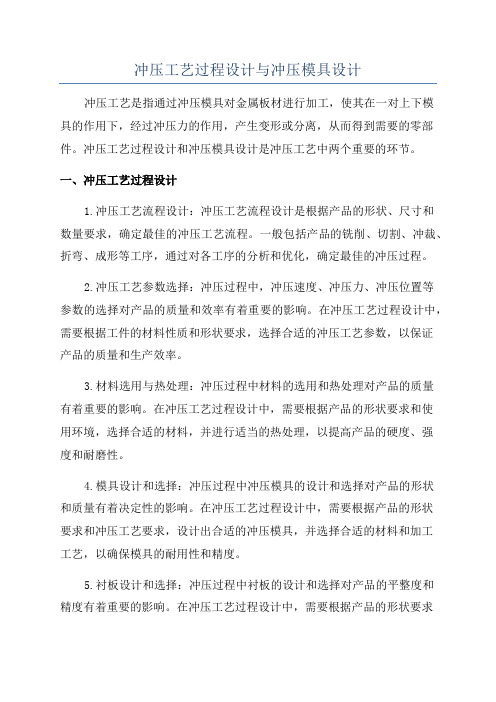
冲压工艺过程设计与冲压模具设计冲压工艺是指通过冲压模具对金属板材进行加工,使其在一对上下模具的作用下,经过冲压力的作用,产生变形或分离,从而得到需要的零部件。
冲压工艺过程设计和冲压模具设计是冲压工艺中两个重要的环节。
一、冲压工艺过程设计1.冲压工艺流程设计:冲压工艺流程设计是根据产品的形状、尺寸和数量要求,确定最佳的冲压工艺流程。
一般包括产品的铣削、切割、冲裁、折弯、成形等工序,通过对各工序的分析和优化,确定最佳的冲压过程。
2.冲压工艺参数选择:冲压过程中,冲压速度、冲压力、冲压位置等参数的选择对产品的质量和效率有着重要的影响。
在冲压工艺过程设计中,需要根据工件的材料性质和形状要求,选择合适的冲压工艺参数,以保证产品的质量和生产效率。
3.材料选用与热处理:冲压过程中材料的选用和热处理对产品的质量有着重要的影响。
在冲压工艺过程设计中,需要根据产品的形状要求和使用环境,选择合适的材料,并进行适当的热处理,以提高产品的硬度、强度和耐磨性。
4.模具设计和选择:冲压过程中冲压模具的设计和选择对产品的形状和质量有着决定性的影响。
在冲压工艺过程设计中,需要根据产品的形状要求和冲压工艺要求,设计出合适的冲压模具,并选择合适的材料和加工工艺,以确保模具的耐用性和精度。
5.衬板设计和选择:冲压过程中衬板的设计和选择对产品的平整度和精度有着重要的影响。
在冲压工艺过程设计中,需要根据产品的形状要求和冲压工艺要求,设计出合适的衬板,并选择合适的材料和工艺,以确保衬板的平整度和精度。
1.冲压模具结构设计:冲压模具的结构设计是根据产品的形状要求和冲压工艺要求,设计出合适的模具结构。
一般包括上模、下模、导柱、导套、导向件等部分,通过对这些部分的设计,实现产品的冲裁、折弯、成形等工艺要求。
2.冲压模具材料选择:冲压模具的材料选择对模具的寿命和精度有着重要的影响。
在冲压模具设计中,需要根据模具的使用环境和要求,选择合适的材料,并进行适当的热处理,以提高模具的硬度、强度和耐磨性。
冲压工艺与模具设计的内容及步骤
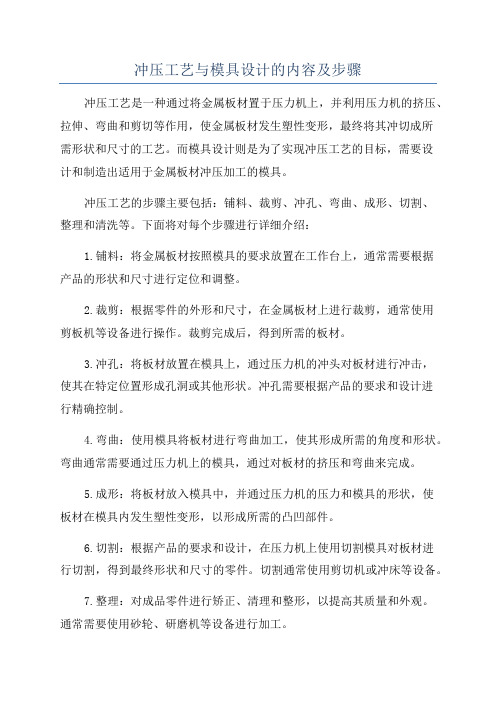
冲压工艺与模具设计的内容及步骤冲压工艺是一种通过将金属板材置于压力机上,并利用压力机的挤压、拉伸、弯曲和剪切等作用,使金属板材发生塑性变形,最终将其冲切成所需形状和尺寸的工艺。
而模具设计则是为了实现冲压工艺的目标,需要设计和制造出适用于金属板材冲压加工的模具。
冲压工艺的步骤主要包括:铺料、裁剪、冲孔、弯曲、成形、切割、整理和清洗等。
下面将对每个步骤进行详细介绍:1.铺料:将金属板材按照模具的要求放置在工作台上,通常需要根据产品的形状和尺寸进行定位和调整。
2.裁剪:根据零件的外形和尺寸,在金属板材上进行裁剪,通常使用剪板机等设备进行操作。
裁剪完成后,得到所需的板材。
3.冲孔:将板材放置在模具上,通过压力机的冲头对板材进行冲击,使其在特定位置形成孔洞或其他形状。
冲孔需要根据产品的要求和设计进行精确控制。
4.弯曲:使用模具将板材进行弯曲加工,使其形成所需的角度和形状。
弯曲通常需要通过压力机上的模具,通过对板材的挤压和弯曲来完成。
5.成形:将板材放入模具中,并通过压力机的压力和模具的形状,使板材在模具内发生塑性变形,以形成所需的凸凹部件。
6.切割:根据产品的要求和设计,在压力机上使用切割模具对板材进行切割,得到最终形状和尺寸的零件。
切割通常使用剪切机或冲床等设备。
7.整理:对成品零件进行矫正、清理和整形,以提高其质量和外观。
通常需要使用砂轮、研磨机等设备进行加工。
8.清洗:将零件进行清洗,去除表面的污垢和油脂,以保证产品的卫生和安全。
模具设计的步骤主要包括:确定产品要求、制定工艺方案、设计模具结构、制定模具工艺和制造模具等。
1.确定产品要求:包括零件的形状、尺寸、材料和数量等方面的要求。
2.制定工艺方案:根据产品要求和实际情况,确定适当的冲压工艺和加工方法,并选择合适的设备和工具。
3.设计模具结构:根据产品形状和要求,设计出合适的模具结构,包括上下模的布局、导向机构、定位装置、脱模装置等。
4.制定模具工艺:根据模具结构和产品要求,制定模具的冲压顺序、冲头形状和尺寸、冲孔位置和尺寸等。
不锈钢笼屉的冲压工艺及模具设计论文_学位论文

1 前言冲压是生产中应用相当广泛的一种加工方法,但冲压加工必须制备相应的模具,而模具是技术精密型产品,起制造属单间小批量生产,具有加工难、精度高、技术含量高、生产成本高的特点。
所以,只有在冲压零件大批量生产的情况下,冲压加工的优点才能充分显现出来。
当前我国模具工业发展迅速,模具技术是先进制造技术的重要代表,模具工业已成为高薪技术产业的一个重要组成部分。
经过几十年的发展,我国的冲压模具总量位居世界第三位,加工技术装备基本已与世界先进水平同步。
以汽车覆盖件为代表的大型、复杂、精密冲压模,用C A D /C A M / C A E软件进行三维设计和模拟,靠高速、精密的加工设备生产,用新型研磨或抛光代替传统的手工研磨抛光,提高模具质量。
标志冲模技术先进水平的多工位级进模和多功能模具,是我国重点发展的精密模具品种。
有代表性的是集机电一体化的铁芯精密自动阀片多功能模具,已基本达到国际水平。
但总体上和国外多工位级进模相比,在制造精度、使用寿命、模具结构和功能上,仍存在一定差距。
钣金冲压模具的水平也有了显著的提高,很多新型材料的冲压的模具的制造得到了实践。
我国钣金冲压模具无论在数量上,还是在质量、技术和能力等方面都已有了很大发展,但与国家经济需求和世界先进水平相比,差距仍很大。
随着与国际接轨的脚步不断加快,市场竞争的日益加剧,人们已经越来越认识到产品质量、成本和新产品的开发能力的重要性。
对于钣金冲压模具的设计和制造,结合所需加工的材料进行分析和优化,通过我们的不懈努力,提高我国制造业的水平。
不锈钢钣金冲压件作为最常见的现代电子和家庭用品的消费品,显示了不锈钢冲压件模具生产的重要性,生产的零件的综合种类很多,用途很广,因此不锈钢钣金的冲压模具会有很大的市场,尤其对于电子产品和家庭日用品。
我觉得外国的电子产品的设计加工主要还是零部件冲压模具的精密性决定的,要占领消费市场,在提高产品设计的同时,必须提高钣金冲压模具的设计和加工工艺。
毕业设计(论文)-五格不锈钢餐盘冲压工艺及模具设计(全套图纸)

第1章绪论1.1冲压技术的现状冲压技术的真正发展,始于汽车的工业化生产。
20世纪初,美国福特汽车的工业化生产大大推动了冲术的研究和发展。
研究工作基本上在板料成形技术和成形性两方面同时展开,关键问题是破裂、起皱与回弹,涉及可成形性预估、成形方法的创新,以及成形过程的分析与控制。
但在20世纪的大部分时间里,对冲压技术的掌握基本上是经验型的。
分析工具是经典的成形力学理论,能求解的问题十分有限。
研究的重点是板材冲压性能及成形力学,60年代是冲压技术发展的重要时期,各种新的成形技术相继出现。
尤其是成形极限图(FLD)的提出,推动了板材性能、成形理论、成形工艺和质量控制的协调发展,成为冲压技术发展史上的一个里程碑。
全套图纸,加153893706随着对发展先进制造技术的重要性获得前所未有的共识,冲压成形技术无论在深度和广度上都取得了前所未有的进展,其特征是与高新技术结合,在方法和体系上开始发生很大变化。
计算机技术、信息技术、现代测控技术等冲压领域的渗透与交叉融合,推动了先进冲压成形技术的形成和发展。
工业发达国家对冷冲压生产工工艺的发展是很重视的.不少国家(如美国、日本等)模具工业产值己超过机床工业。
从这些国家钢材构成可以看出冷冲压的发展趋势。
钢带和钢板占全部品种的67%,充分说明冲压这种加工方法己成为现代工业生产的重要手段和发展方向。
1.2冲压技术的发展趋势随着与国际接轨的脚步不断加快,市场竞争的日益加剧,人们已经越来越认识到产品质量、成本和新产品的开发能力的重要性。
而模具制造是整个链条中最基础的要素之一,模具制造技术现已成为衡量一个国家制造业水平高低的重要标志,并在很大程度上决定企业的生存空间。
近年许多模具企业加大了用于技术进步的投资力度,将技术进步视为企业发展的重要动力。
一些国内模具企业已普及了二维CAD,并陆续开始使用UG、PRO/E ngineer、I-DEAS、Euclid-IS等国际通用软件,个别厂家还引进了Moldflow、C-Flow、DYNAFORM、Optris和MAGMASOFT等CAE软件,并成功应用于冲压模的设计中。
- 1、下载文档前请自行甄别文档内容的完整性,平台不提供额外的编辑、内容补充、找答案等附加服务。
- 2、"仅部分预览"的文档,不可在线预览部分如存在完整性等问题,可反馈申请退款(可完整预览的文档不适用该条件!)。
- 3、如文档侵犯您的权益,请联系客服反馈,我们会尽快为您处理(人工客服工作时间:9:00-18:30)。
F ——凸模所受总压力 (N )。
对于圆凸模, J = Πd4 64, 取 n= 3, 代入式 (1) 可
得圆凸模有导向时最大允许长度为
L max≤270 d 2
(2)
F
凸模所受总压力 F 一般按下式计算:
F = K L tΣ
(3)
式中: L ——冲裁周边长度 (mm ) ;
22
进行锻造处理, 经过多次锻打后, 改进材料的致密 度, 流线方向和碳化物分布状况, 使组织均匀, 改善 机械性能, 提高热处理质量和使用寿命, 以保证在冲 裁、振动的环境中保持刚性, 避免因变形而使精度受 到 影响。 另外, 凸凹模经热处理后要求硬度达到 HRC58~ 62, 从而提高模具的使用寿命。
采用浮动式模柄, 浮动模柄在上模座的固定位置和 模具压力中心一致, 避免压力机精度不足对冲压的 影响, 从而保证冲压过程中的同心度。 (4) 卸料装置及退料 为保证吸滤网冲制过程中不变形, 模具中设置 同时起导向、压料与卸料作用的卸料板。冲压吸滤网 的时候, 卸料顶杆在橡皮的弹力作用下与卸料板先 将料压紧, 再进行冲压, 因此剪切断面质量较高, 工 件平整。为此, 同一模具上的卸料顶杆加工时要求几 件尺寸公差协调一致, 同时保证卸料板一般比凹模 平面高出约 012mm。 特别指出, 如凸凹模内积存有废料, 则对凸凹模 胀开力就会增大, 而且容易胀开刃口, 因此, 在较小 壁厚的情况下, 为安全起见, 应避免凸凹模内积存废 料。另外, 由于吸滤网薄而轻, 在冲裁的过程中, 因模 具的微振动常会出现因油或真空使废料或冲制出的 零件上跳而吸附在凸模或凹模上, 从而造成零件报 废, 严重时引起模具的损伤。 为此, 规定冲制前手工 用干净棉布将钢带上的油污擦拭干净, 冲制过程中 采用压缩空气退料, 以保证冲裁精度及保护模具。
3 工艺分析与模具的设计
冲压零件质量的好坏与模具的结构、模具的精 度、凸模和凹模的状况, 材料的状态、料厚、润滑条 件、设备精度、冲裁速度、压边力和顶件力等因素有 关[2]。 因此, 根据吸滤网的形状、尺寸及材料从以下 几个方面来分析考虑模具的结构与加工。 (1) 模具结构形式, 见图 2。 (2) 凸、凹模设计 凸模和凹模是冲模中的关键零件, 它的形状和 尺寸直接影响模具的刃口间隙和冲压零件剪切面的 粗糙度, 它的强度直接影响模具的寿命。 a1 凸、凹模材料的选择 吸滤网材料的硬度为维氏硬度HV 486~ 600, 硬度较高, 模具在工作过程中要承受强压和很大的 冲击, 凸模和凹模刃口部分易出现断裂, 而显得尤其 严重。另外, 冲压模的使用中常因磨损而使工作部分 尺寸发生变化, 所以要求模具工作部分有良好的耐 磨性, 以保证模具的寿命和冲压件的质量。通过分析 比较, 凸、凹模的材料均采用 C r12M oV 钢, 其硬度 高, 耐磨性强, 为进一步提高材料的工作性能, 对其
4 结束语
经验证, 本项小孔冲制工艺可行, 模具设计成 功。在小批量生产中, 采用该模具冲制出的吸滤网尺 寸精度高, 基本无变形, 表面质量高 (微小毛刺经研 磨后即可去除) , 达到了设计要求, 质量稳定。
参Байду номын сангаас文献:
[ 1 ] 罗益旋 1 最新冲压新工艺新技术及模具设计实用手册 [M ]1 长春: 吉林出版发行集团, 20041
图 2 模具结构 11 下模座 21 凹模垫板 31 凹模固定板 41 凹模 51 下模小导 柱导套 61 卸料板 71 上模小导柱导套 81 模柄 91 凸模 101 弹力件 111 拉紧螺钉 121 凸模固定板 131 上模座 141 限位柱 151 两端垫铁 161 滚珠导向件
b1 凸、凹模配合间隙设计 冲孔件的尺寸取决于凸模尺寸, 故冲孔模应先 决定凸模尺寸, 用增大凹模尺寸来保证合理间隙。吸 滤网的材料薄而且尺寸精度要求高, 冲裁间隙的选 择不但影响零件的剪切面的形状 (包括毛面斜度、塌 角、毛刺等) 而且也影响零件的尺寸精度。 在查阅了 有关资料和进行多次实验后, 将凸凹模配合间隙设 计为0103mm 左右。这样在冲裁的过程中, 可有效抑 制剪切过程中裂纹的产生, 使得冲裁件的断面质量 和尺寸精度都有所提高。对冲制薄材料工件的模具, 其凸、凹模通常采用配合加工的方法。此方法是先做 凸模或凹模中的一件, 然后根据制作好的凸模或凹 模的实际尺寸, 配做另一件, 使它们之间达到最小合 理间隙值。 在这里, 我们先做凸模, 并以它作为基准 配做凹模, 保证最小合理间隙。 c1 凸模强度计算 凸模的设计是整个设计的关键, 要提高凸模的 强度和刚性, 可以采取两种办法: 一是保护凸模, 也 就是说增加凸模的约束; 另一种办法是减小凸模有 效工作部分长度。 小孔凸模折断主要是凸模受弯曲 力矩作用发生失稳而造成。 凸模有导向时, 相当于一端固定, 另一端铰支的 压杆, 凸模不发生失稳弯曲的最大长度L max 可由下 式确定[3 ]:
作者简介: 纪永 (1977—) , 男, 吉林省人, 硕士研究生, 研究方向: 机电控制及自动化。 收稿日期: 2006- 02- 06
21
Equ ipm en t M anufactu ring T echno logy N o 11, 2006
不正或冲孔重叠, 造成零件报废。
2 加工工艺方案的确定
冲压工艺学指出, 冲孔的最小尺寸由板料的抗 剪强度和板材厚度决定。 同样厚度的板, 若材质不 同, 允许最小冲孔直径也不同。 因而, 各种材质的板 都存在一个允许冲孔的最小尺寸。 根据资料公布的
实践数据, 冲孔的最小孔型尺寸值见表 1[1]。
表 1 无保护套凸模冲孔最小值 ( t 为板材厚度)
t——材料厚度 (mm ) ;
Σ——材料抗剪强度 (M Pa) ;
K —— 系数, 考虑在实际生产中, 模具间隙值
的波动和不均匀、刃口的磨损、板料力学性能和厚度
波动等因素而给出的修正系数, 一般取K = 113。 奥氏体不锈钢 (304 或 316) , 抗剪强度 Σ取约为 460M Pa, 而冲裁周边长度L = Πd , d = 016mm , t= 014mm , 代入式 (3) 中, 可得 F≈ 450N , 再把结果代 入式 (2) , 可得凸模的极限长度约为 416mm。 冲孔时, 凸模除了受冲裁力引起的压应力外, 还 要受到卸料时的拉应力, 因此, 凸模要承受很强烈的 拉伸、压缩交变载荷。 此外, 凸模刃口处通常存在较 大的应力集中现象, 所以凸模也经常出现疲劳破坏。 因此, 在凸模热处理规范选用时, 必须同时兼顾硬度 和韧性两个方面的综合性能[ 4 ]。
材料及抗剪强度 (M Pa)
Σ> 700
圆孔 直径 d ≥115 t
方孔 边长 a ≥1135 t
长圆孔 宽a
≥111t
长方孔 宽a
≥112t
钢 Σ= 400~ 700
≥113t ≥112t ≥019t ≥t
Σ< 400
≥t
≥019t ≥017t ≥018t
黄铜、铜
≥019t ≥018t ≥016t ≥017t
不锈钢高密度真空吸滤网是制糖业中真空吸滤 机 (主要用于泥汁的过滤) 中的关键零件, 该零件的 长×宽×厚为 3000mm ×600mm ×014mm , 在此区 域内均匀密布着约 120 万个孔径小且密度大的圆 孔。 在不锈钢的超长钢板上用冲压方法加工出上百 万个极小孔, 在国内确属罕见。 我国现用的不锈钢高密度真空吸滤网均靠进 口, 价格昂贵。国外把加工这种密集小孔薄板的技术 列为专利, 我们很难得到他们的冲孔模具和冲压工 艺。因此, 如何解决在不锈钢薄板上冲制高密度微孔 的难题, 填补国内空白, 有着非常现实的意义。
1 零件的工艺分析
根据制糖业要求, 真空吸滤网材料采用 304 或 316 奥氏体不锈钢板加工, 厚度为 014mm , 板上的小 孔排列见图 1。
图 1 小孔分布图
在图 1 可见, 相邻孔间距 0198mm , 孔径大小为
016mm , 孔径接近板厚, 因此, 按照冲压工艺学的观 点, 这种小孔的尺寸已经达到常规冲裁的极限值, 小 孔是极限小孔。
《装备制造技术》 2006 年第 1 期
工艺与工装
不锈钢真空吸滤网冲压工艺及模具设计
纪 永, 王小纯, 曾盛绰 (广西大学机械工程学院, 广西 南宁 530004)
摘要: 不锈钢真空吸滤网是真空吸滤机的关键零件, 它具有网孔小、分布密集、材料冲压性能差 等特点, 成为国内冲压工艺研究亟待解决的一个难题。 本文在大量实践研究的基础上, 对真空 吸滤网的冲压工艺和模具结构进行了合理的设计, 在小批量生产中, 获得了较好的使用效果。 关键词: 真空吸滤网; 冲孔模; 工艺分析 中图分类号: T G38512 文献标识码: A 文章编号: 1672- 545X (2006) 01- 0021- 03
由上述分析, 根据现有设备情况, 我们确定此零 件在J 92K 系列数控冲模回转头压力机上加工, 由于 相邻孔间距小, 若同时冲制, 相邻凸模将相互干扰, 故我们采用分步跳冲的方法加以解决。 ( 1) 该压力机 X、Y 方 向 的 工 作 行 程 分 别 是 1250mm ×2500mm。 在 2500 mm 方向上, 具有多次 自动移位功能, 即便是很长的工件, 在理论上也可通 过反复移位而实现超长部分的冲孔加工。 (2) 机床除送进步距精度高外, 被冲工件可以在 X、Y 方向上同时准确移动, 按之字形方向送进, 这 就完全有把握按照预先编制的加工程序, 制造出合 格的网板。 (3) 压力机最高冲孔频率达 300 次 m in, 是一般 压力机速度的 6~ 10 倍, 这就提供了用冲头数少且 结构小的模具高速度冲制大量小孔零件的可能。 (4) 机床通过数控指令, 在每一次冲孔之前, 压 料装置事先将冲孔区四周部分的板料牢牢压紧, 而 后冲孔, 这就大大减少了冲孔变形量, 这对提高和保 证吸滤网的质量大为有利。
Punch ing Techn ics and M old D esign for Sta in less Steel Vacuum F ilter Sieve