公司零件检验情况分析报告表
MSA分析报告

MSA分析报告MSA分析报告XXX公司计量型MSA分析报告⽇期:实施⼈:评价⼈:仪器名称:仪器编号:分析结论:合格不合格审核:批准:XX/840 -004B №:L202017年2⽉23⽇陈秋凤、雷丽花、欧阳丽敏张志超数显卡尺(中间检验)XXX计量型MSA分析报告⽬录稳定性………………………………………………………………………………………1偏倚………………………………………………………………………………………4线性………………………………………………………………………………………7重复性和再现性………………………………………………………………………………………9备注: 对于有条件接收的项⽬应阐述接受原因.第⼀节稳定性分析1.1 稳定性概述在经过⼀段长时间下,⽤相同的测量系统对同⼀基准或零件的同⼀特性进⾏测量所获得的总变差,即稳定性是整个时间的偏倚变化。
1.2 试验⽅案2017 年 02 ⽉份,随机抽取⼀常见印制板样品,让中间检验员⼯每天的早上及晚上分别使⽤数显卡尺对样品外形尺⼨测量5次/组,共测量25组数据,并将每次测量的数据记录在表1。
1.3 数据收集测量结果/单位:__mm__测量时间第1次第2次第3次第4次第5次时段1 65.23 65.23 65.23 65.24 65.23 时段2 65.23 65.23 65.23 65.23 65.23 时段3 65.24 65.23 65.23 65.24 65.24 时段4 65.24 65.24 65.24 65.23 65.24 时段5 65.23 65.24 65.23 65.23 65.23 时段6 65.24 65.24 65.24 65.24 65.24 时段7 65.24 65.23 65.24 65.24 65.24 时段8 65.24 65.23 65.23 65.24 65.23 时段9 65.23 65.24 65.23 65.23 65.23 时段10 65.23 65.23 65.23 65.23 65.23 时段11 65.24 65.23 65.23 65.24 65.24操作者陈秋凤测量⽇期2017-02-04~2017-02-20测量结果/单位:__mm__测量时间第1次第2次第3次第4次第5次时段12 65.24 65.24 65.24 65.24 65.23 时段13 65.24 65.23 65.23 65.24 65.23 时段14 65.23 65.23 65.23 65.23 65.23 时段15 65.24 65.24 65.23 65.23 65.24 时段16 65.23 65.23 65.24 65.23 65.23 时段17 65.23 65.24 65.23 65.23 65.23 时段18 65.24 65.24 65.24 65.24 65.23 时段19 65.24 65.23 65.23 65.23 65.23 时段20 65.24 65.24 65.24 65.24 65.24 时段21 65.23 65.23 65.24 65.23 65.23 时段22 65.24 65.24 65.23 65.24 65.24 时段23 65.23 65.24 65.24 65.23 65.23 时段24 65.23 65.24 65.24 65.24 65.24 时段25 65.23 65.23 65.23 65.23 65.231.4 测量系统稳定性可接受判定标准1.4.1 不允许有超出控制限的点;1.4.2 连续7点位于中⼼线同⼀侧;1.4.3 连续6点上升或下降;1.4.4 连续14点交替上下变化;1.4.5 连续3点有2点距中⼼的距离⼤于两个标准差;1.4.6 连续5点中有4点距离中⼼线的距离⼤于⼀个标准差;1.4.7 连续15点排列在中⼼线的⼀个标准差范围内;1.4.8 连续8点距中⼼线的距离⼤于⼀个标准差。
过程分析工作表-典型汽车零部件企业
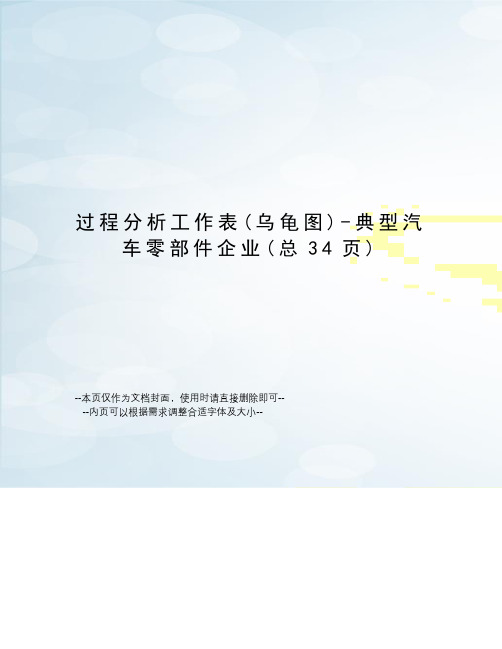
过程分析工作表(乌龟图)-典型汽车零部件企业(总34页)--本页仅作为文档封面,使用时请直接删除即可----内页可以根据需求调整合适字体及大小--过程分析工作表(乌龟图)23过程分析工作表(乌龟图)4过程分析工作表(乌龟图)56过程分析工作表(乌龟图)78过程分析工作表(乌龟图)过程分析工作表(乌龟图)1011过程分析工作表(乌龟图)1213过程分析工作表(乌龟图)14过程分析工作表(乌龟图)1516过程分析工作表(乌龟图)过程分析工作表(乌龟图)1819过程分析工作表(乌龟图)20过程分析工作表(乌龟图)2122过程分析工作表(乌龟图)2324过程分析工作表(乌龟图)2526过程分析工作表(乌龟图)2728过程分析工作表(乌龟图)2930过程分析工作表(乌龟图)3132过程分析工作表(乌龟图)33过程分析工作表(乌龟图)34过程分析工作表(乌龟图)3536过程分析工作表(乌龟图)3738过程分析工作表(乌龟图)39过程分析工作表(乌龟图)40过程分析工作表(乌龟图)4142过程分析工作表(乌龟图)过程分析工作表(乌龟图)4445过程分析工作表(乌龟图)46过程分析工作表(乌龟图)4748过程分析工作表(乌龟图)4950。
叉车定期检验分析报告

合格
42
(1)
货叉限位装置
符合
合格
43
B9
(2)
蓄电池叉车总电源应急断电装置
符合
合格
44
安全
(3)
护顶架
符合
合格
45
保护
(4)
步行式车辆安全换向器
符合
合格
46
(5)
车轮的防护装置
符合
合格
47
(1)
货叉架自然下滑量、门架倾角变化量
符合
合格
48
B10
(2)
货叉两叉尖高度差
符合
合格
49
工作
(3)
货叉或属具在叉架上的固定
叉车定期检验分析报告
报告编号:2009-02-CT5-67
叉车定期检验报告
使用单位:台州市正康木业有限公司
检验机构:台州市特种设备监督检验中心
检验日期:2009年02月23日
国家质量监督检验检疫总局制
叉车定期检验报告
报告编号:2009-02-CT5-67
共1页第4页
使用单位
台州市正康木业有限公司
制造单位
浙江杭叉工程机械股份有限公司
设备注册代码
出厂编号
叉车规格型号
CPC3L-C
额定重量
3T
发动机功率
4.5KW
检验依据:
1.《特种设备安全监察条例》(国务)
2.《厂内机动车辆安全检验技术要求》(GB/T16178-1996)
3.《前移式和插腿式叉车
稳定性基本试验》(GB/T5142-2005)
4.《前移式和插腿式叉车
符合
合格
34
(7)蓄电池叉车的制动连锁装置
2产能与品质验厂评分表
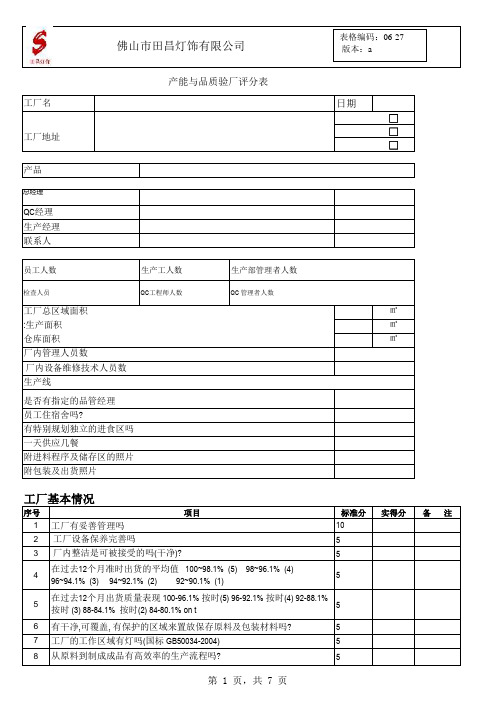
日期□□□生产部管理者人数QC 管理者人数㎡㎡㎡序号标准分实得分备 注11025354555657585员工住宿舍吗?QC 工程师人数有特别规划独立的进食区吗一天供应几餐附包装及出货照片附进料程序及储存区的照片在过去12个月出货质量表现 100-96.1% 按时(5) 96-92.1% 按时(4) 92-88.1%按时 (3) 88-84.1% 按时(2) 84-80.1% on t有干净,可覆盖, 有保护的区域来置放保存原料及包装材料吗?工厂的工作区域有灯吗(国标 GB50034-2004)工厂有妥善管理吗生产线厂内管理人员数厂内设备维修技术人员数工厂地址总经理产品仓库面积员工人数是否有指定的品管经理从原料到制成成品有高效率的生产流程吗?工厂设备保养完善吗厂内整洁是可被接受的吗(干净)?工厂名生产工人数检查人员:生产面积工厂总区域面积产能与品质验厂评分表联系人QC 经理生产经理项目在过去12个月准时出货的平均值 100~98.1% (5) 98~96.1% (4)96~94.1% (3) 94~92.1% (2) 92~90.1% (1)产能与品质验厂评分表产能与品质验厂评分表产能与品质验厂评分表产能与品质验厂评分表11、产能评估(打星号得分为时,本公司不满意)产能与品质验厂评分表12.一般员工相关事项任何有"F"的问题若被打零分,验厂认证将不被通过, 假产能与品质验厂评分表日期 :_________________批准 :________________这是一个计算机生成的报告。
不需要签名。
项目实得分=(总标准分-不适合分)总分 = ———————————————————— x 100。
VDA 过程审核检查表及打分表—

日期:发现/背离等级生产 (工序 2 - 10)退火6.1.人员/素质6.1.1.是否对员工委以监控产品质量/过程质量的职责和权限?10查:明确授予了操作人员、车间主任的质量职责及质量管理员的过程监控职责6.1.2.是否对员工委以负责生产设备/生产环境的职责和权限?10查:球化退火炉,设备编号完好,标识牌上明确责任人为卜科平6.1.3.员工是否适合于完成所交付的任务并保持其素质?8查:现场记录与作业指导书相符6.1.4.是否有包括顶岗规定的人员配置计划?8查:有员工技能矩阵图及人员能力评价记录6.1.5.是否有效地使用了提高员工工作积极性的方法?10查:有员工奖罚制度,行政部能提供奖励及处罚记录。
6.2.生产设备/工装6.2.1.生产设备/工装模具是否能保证满足产品特定的质量要求?10查:能提供设备保养规程、保养计划、保养记录、维修记录;查:能提供工装管理规定、保养记录、精度检查记录。
关注易损零件/易损部位的定期更新记录。
查:能提供设备履历、工装履历等。
查:能提供工装验收记录并与工装设计文件比较。
包括易损件/部位的更换/维修周期的规定及实施。
6.2.2.在批量生产中使用的检测,试验设备是否能有效地监控质量要求?10查:提供《2017年检测设备外校检定证书台账》、《2017年计量器具外校检定计划》、《计量器具内校计划》及校准台账查:现场使用是千分尺,编号:45186,合格证上的校准日期为:2017/5/19,有效期为2018/5/18;6.2.3.生产工位,检验工位是否符合要求?8查:根据生产流程制定生产、检验工位,符合要求6.2.4.生产文件与检验文件中是否标出所有的重要技术要求,并坚持执行?10查:09118-08015《控制计划》与《作业指导书》该工序,没有特殊特性要求。
6.2.5.对产品调整/更换是否有必备的辅助器具?8查:配备有相关的辅助器具,如提升机等6.2.6.是否进行批量生产起始认可,并记录调整参数或偏差情况?10查:35K退火工艺记录参数符合《作业指导书》规定6.2.7.是否按时落实要求的纠正措施并检查其有效性?10查:质量目标未达标,每天在QRQC会议通报,并进行原因分析、制定改进措施,在后续会议中汇报实施结果日期:日期:日期:日期:6.1.1.是否对员工委以监控产品质量/过程质量的职责和权限?查:明确授予了操作人员、车间主任的质量职责及质量管理员的过程监控职责6.1.2.是否对员工委以负责生产设备/生产环境的职责和权限?查:设备标识是完好、正确有效,明确了设备责任人6.1.3.员工是否适合于完成所交付的任务并保持其素质?查:员工对本岗位作业指导书能理解和执行(首件记录、设备点检、工装服役档案等),符合。
实验分析报告 形位公差

实验报告形位公差————————————————————————————————作者:————————————————————————————————日期:2目录实验一零件形状误差的测量与检验实验1—1直线度测量与检验实验1—2平面度测量与检验实验1—3圆度测量与检验实验1—4圆柱度测量与检验实验二零件位置误差的测量实验2—1 平行度测量与检验实验2—2 垂直度测量与检验实验2—3 同轴度测量与检验实验2—4圆柱跳动测量与检验实验2—4—1圆柱径向跳动测量与检验实验2—4—2圆柱全跳动测量与检验实验2—5端面跳动测量与检验实验2—5—1端面圆跳动测量与检验实验2—5—1端面全跳动测量与检验实验2—6 对称度测量与检验实验三齿轮形位误差的测量与检验实验3—1齿圈径向跳动测量与检验实验3—2齿轮齿向误差测量与检验实验一零件形状误差的测量与检验实验1—1直线度测量与检验一、实验目的1、通过测量与检验加深理解直线度误差与公差的定义;2、熟练掌握直线度误差的测量及数据处理方法和技能;3、掌握判断零件直线度误差是否合格的方法和技能。
二、实验内容用百分表测量直线度误差。
三、测量工具及零件平板、支承座、百分表(架)、测量块(图纸一)。
四、实验步骤1、将测量块2组装在支承块3上,并用调整座4支承在平板上,再将测量块两端点调整到与平板等高(百分表示值为零),图1-1-1所示。
图1-1-1 用百分表测量直线度误差2、在被测素线的全长范围内取8点测量(两端点为0和7点,示值为零),将测量数据填入表1-1-1中。
表1-1-1:单位:μm 测点序号0 1 2 3 4 5 6 7 计算值图纸值合格否两端点连线法最小条件法3、按图1-1-1示例将测量数据绘成坐标图线,分别用两端点连线法和最小条件法计算测量块直线度误差。
图1-1-1 直线度误差数据处理方法4、用计算出的测量块直线度误差与图纸直线度公差进行比较,判断该零件的直线度误差是否合格。
机械零件常规检测方案及专用检具设计

2.1
该支撑架零件的材料为HT200灰口铸铁,在大批量生产的情况下,根据《GB-T 6414-1999铸件尺寸公差与机械加工余量》表1、表2、表A1、表B1取毛坯的加工余量等级为G,公差等级为12,从而确定毛坯各待加工表面的加工余量,画出毛坯图如下所示:
附图2:支撑架毛坯图
由于砂型铸造的特点,除 、 两大孔外,其他的小孔都不铸造,采用机加方式。
[4]吕天玉张柏军主编《公差配合与测量技术》.大连理工大学出版社.2012
[5]王先逵.《机械加工工艺手册》第1卷(工艺基础卷)[M].北京:机械工业出版社,2006.
[6]杨叔子.《机械加工工艺师手册》[M].北京:机械工业出版社,2001年.
[7]黄如林.汪群.《金属加工工艺及工装设计》[M].北京:化学工业出版社,2006年.
工序V:铣端面,钻铰孔,倒角
卧式加工中心XH754,以铣平面夹具固定,铣端面,保证66;倒C3;钻绞孔 ,保证24、110±0.05,倒C1.5;钻绞孔2×φ5,保证40,划90°、φ11。
工序VI:成品检验,入库
三、确定检验方案
3
从已知图样中得知,支撑架零件除了 、 两个大孔有尺寸公差和形位公差外,其他部位尺寸都为自由公差。
4.
根据国家对检测量规标准的相关规定(GB/T1957-2006)对该塞规制定出相应的制造技术精度(2级精度)要求。
根据公式:
计算出塞规的基本尺寸,通过查阅量规制造公差表,最后求证出塞规的制造尺寸精度及公差要求。
通端:
止端:
根据《检、量具设计》表3-3可查出该量规测头和总长尺寸为:L=136mm,L1(D)=18mm,L2(d)=14mm,R=1.5。
其他部位尺寸无公差要求,可采用通用量具检验。
质量管理表格大全
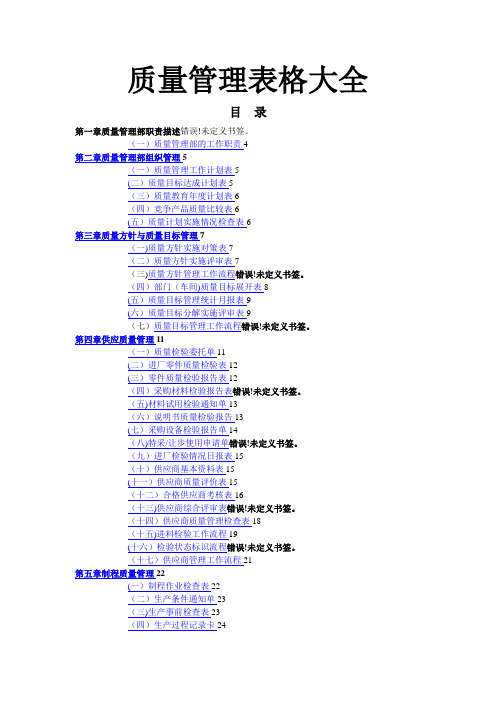
质量管理表格大全目录第一章质量管理部职责描述错误!未定义书签。
(一)质量管理部的工作职责4第二章质量管理部组织管理5(一)质量管理工作计划表5(二)质量目标达成计划表5(三)质量教育年度计划表6(四)竞争产品质量比较表6(五)质量计划实施情况检查表6第三章质量方针与质量目标管理7(一)质量方针实施对策表7(二)质量方针实施评审表7(三)质量方针管理工作流程错误!未定义书签。
(四)部门(车间)质量目标展开表8(五)质量目标管理统计月报表9(六)质量目标分解实施评审表9(七)质量目标管理工作流程错误!未定义书签。
第四章供应质量管理11(一)质量检验委托单11(二)进厂零件质量检验表12(三)零件质量检验报告表12(四)采购材料检验报告表错误!未定义书签。
(五)材料试用检验通知单13(六)说明书质量检验报告13(七)采购设备检验报告单14(八)特采/让步使用申请单错误!未定义书签。
(九)进厂检验情况日报表15(十)供应商基本资料表15(十一)供应商质量评价表15(十二)合格供应商考核表16(十三)供应商综合评审表错误!未定义书签。
(十四)供应商质量管理检查表18(十五)进料检验工作流程19(十六)检验状态标识流程错误!未定义书签。
(十七)供应商管理工作流程21第五章制程质量管理22(一)制程作业检查表22(二)生产条件通知单23(三)生产事前检查表23(四)生产过程记录卡24(五)过程控制标准表24(六)产品质量标准表24(七)产品质量检验表25(八)质量因素变动表25(九)操作标准变更通知单25(十)生产过程检验标准表26(十一)产品质量抽查记录26(十二)制程质量管理工作流程26(十三)质量分析统计工作流程27(十四)质量指标报告工作流程28(十五)制程质量异常处理工作流程29(十六)工序质量分析表30(十七)工序质量评定表31(十八)工序质量跟踪卡错误!未定义书签。
(十九)工序控制点明细表32(二十)工序质量审核记录表32(二十一)检验工序作业指导书32(二十二)工序质量检验评定表33(二十三)工序操作标准通知单33(二十四)工序质量异常报告表34(二十五)工序质量控制工作流程错误!未定义书签。