三坐标测量机的测头半径补偿与曲面匹配
三坐标测量机测量误差分析及补偿方法的研究

三坐标测量机测量误差分析及补偿方法的研究摘要:20世纪60年代初,三坐标测量机(CoordinateMeasuringMachine,简称CMM)首次面市,这是一种精密的高效测量仪器。
三坐标测量级的技术基础是计算机,数控,电子技术的极大发展。
需求来源是由于数控机床以及零件形状复杂化而产生的配套测量设备的需求。
时至今日,三坐标测量机已经由简单的配套设备转变为加工控制设备。
在现如今的航天航空、汽车、机加工等行业中被广泛应用。
已成为现代工业检测和质量控制不可缺少的测量设备。
因此,使用好CMM,使其在生产中发挥其应有的作用,显得至关重要。
测量误差在工程实践中不可避免,让测量人员了解三坐标测量过程中的误差来源及如何消除误差,使测量值更接近于实际值,具有较强的工程实践意义。
关键词:三坐标测量机;测量误差;补偿方法作为精密测量仪器,三坐标测量机在产品设计、加工制造、检测等领域得到广泛的应用与推广。
但在实际的测量过程中,仍然会有测量误差的产生,如测头测针磨损、测量路径选择不当等因素。
因此,分析误差源并采取合适的补偿方法,是提高测量精度行之有效的途径。
1三坐标测量机误差分类根据误差特性的不同,可将误差分为准静态误差和动态误差。
准静态误差是指由于外界因素和自身结构引起的误差,而动态误差引起的原因是多方面的,会随时间变化而变化。
2三坐标测量机误差源分析2.1准静态误差源分析三坐标测量机静态误差的原因是多方面的,如测量环境的温度、湿度、振动、机导向机构的运动、测头磨损,以及测量方法等不确定因素造成的。
2.2动态误差源分析三坐标测量机是一个由机体、驱动部分、控制系统、导轨支承、侧头部分、计算机及软件等组成的整体。
测量速度会随着测量任务的变化而经常性的变化,在测量过程中,会受到较大的惯性力。
由于三坐标测量机的运动部件和导轨是弱刚度性,因此运动部件会在惯性力的作用下产生偏转,测针会偏离正交位置并产生动态误差。
由于三坐标测量机的导轨支承的运动精度会随着三轴的移动速度变化而变化,在此过程中会伴随着测头接触力、测头等效半径和冲击力的变化,导致三坐标测量机的移动速度和逼近距离产生偏差,动态误差随之产生。
三坐标测量机的误差分析及其补偿

收稿日期: 1996- 03- 06 © 1994-2006 China Academic Journal Electronic Publishing House. All rights reserved.
46
沈 阳 工 业 学 院 学 报 1997 年
1. 2 三坐标测量机测头位置误差表达式
式 (1) 对坐标平移和旋转的坐标变换可应用到三坐标测量机中各滑台的平移和转动误差 向绝对坐标系的转换.
图 3 坐标系 向坐标系 的变换
图 4 三坐标测量机的坐标变换示意图
在图 1 中的 X 、Y、Z 的滑尺上分别建立三个坐标系 、 、 , 且使三坐标测量机的测头
xp
y=
- ex y + A - M y m - ey y + A -
- ezy + A -
yp
(3)
z
- ex z
- ey z
zm - ezz
zp
式 (3) 中的各误差项均是以绝对坐标系原点为起点, 在单一运动方向上测量的, 其误差评定基
准是理想的坐标轴方向. 因此, 式 (3) 中的误差分量包含三个滑尺运动方向的相互垂直度误差.
48
沈 阳 工 业 学 院 学 报 1997 年
x = x m - ex x - ey x - y m Ηx z (5)
y = y m - ex y - ey y
工作台数显装置为光栅尺, 误差测量装置和坐标值检定用双频激光干涉仪. 实验数据如表
2 所示.
表 2 测量数据
从实验中看出补偿后坐标值更接近于坐标检定值, 显示误差分别为 exm = 010479 mm , eym = - 010039 mm , 而补偿后坐标定位误差为 ex = 010038 mm , ey = 010005 mm.
在三坐标测量机上测量曲线_曲面的方法和误差分析
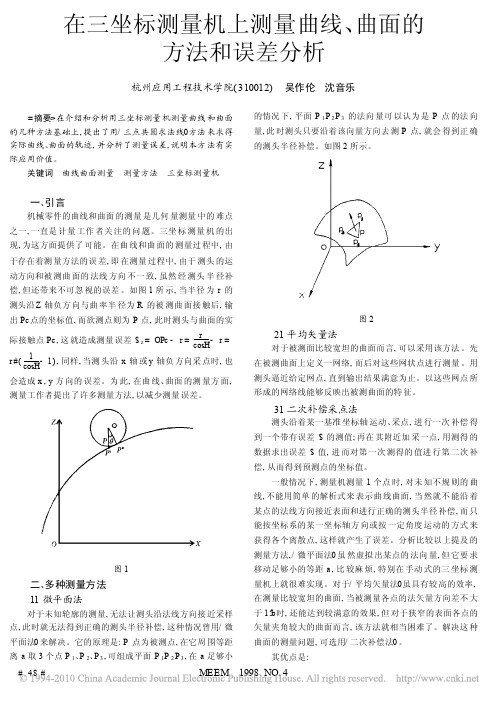
的情况 下, 平面 P 1P 2P 3 的法向 量可 以认为 是 P 点 的法 向 量, 此 时测头只要沿着该向量方向去 测 P 点, 就会 得到正 确 的测头半径补偿。如图 2 所示。
一、引言
机械零件的曲线和曲面 的测量 是几何 量测量 中的 难点
之一, 一直是 计量 工作 者关 注的 问 题。三坐 标 测量 机 的出
出 Pc 点的坐标值, 而欲测点则为 P 点, 此时测头与曲面的实 际接触点 Pc , 这 就造成测量 误差 $ z = OPc - r = corsH- r = r #( co1sH- 1) , 同样, 当测 头沿 x 轴 或 y 轴负 方向采 点时, 也 会造成 x , y 方 向的 误差。为 此, 在曲 线、曲面 的测 量方 面, 测量工作者提出了许多测量方法, 以减少测量 误差。
图4
六、测量实例和数据处理
根据以上提出的/ 三点共圆求 法线法0, 对我院 数控机床 加工的叶片, 在 DEA 三坐标 测量机上进行采样, 并用本方法 求得实际的曲线的离散点, 并用样条插 值函数拟合 成实际曲 线, 其结果还是令人满意的, 当然也可以将多个截面上计算得 到离散点, 用孔斯曲面表示, 现将其截面测量所得测头中心的 坐标值( y, z ) 和通过/ 三点共圆 求法线0得出 实际曲线上的点 坐标( yc , zc ) , 如表 1 所示, 叶片曲线如图 4 中的实线所示。
到一个带有误差 $ 的测值; 再在 其附近加 采一点, 用测得 的
数据求出误差 $ 值, 进 而对第 一次 测得的 值进 行第 二次 补
偿, 从而得到预测点的坐标值。
一般情况下, 测量机测量 1 个点 时, 对未 知不规 则的 曲
线, 不能用简单 的解析式来 表示曲 线曲面, 当 然就不 能沿 着
三坐标测量机测头半径补偿的新方法
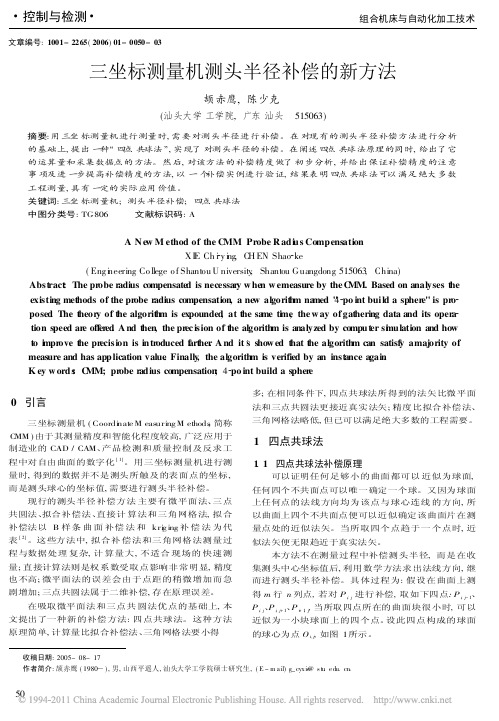
2 精度分析
为了对四点共球法进行 精度分析, 作者利用三维 绘图软件 U G 的二次开发工具 U G /O pen GR IP 将此方 法作为一个菜单嵌入到 U G 软件中, 以便在 U G 中对解 析曲面进行仿真分析。
具体如下: 在 U G 中构造一椭球面, 方程为: x2 / 1002 + y2 /1302 + z2 / 1002 = 1。考虑到对称性, 截取处在第一 象限的 1 / 8椭球面作为被测曲面进行仿真分析。按照一 定规律截取 m 个垂直于 y 轴的截面, 在每个截面上按等 弧长构造 n个曲面上的点作为模拟测量点, 记为 Q i, j ( i = 0, 1, , m - 1; j = 1, , n )。然后为每个测量点构造 对应的测头中心点 (取测头半径 R 的值为 1mm ), 并在 第 m 行后扩充一行, 在每一行的首末各扩充一列, 共得 到 m + 1行 n + 2列点, 记为 Pi, j ( i = 0, 1, , m; j = 0, 1, , n + 1), 作为模拟测量数据。再用四点共球法对 P 1, , n) 进行测头半径补偿, 将补偿后的点 记为 Q i, j ( i = 0, 1, , m - 1; j = 1, , n )。最后将 Q i, j 和 Q i, j 比较, 以偏差 e = | Q i, j - Q i, j | 为 指标考察四点共球法的精度。
解。
( 3) 补偿矢量及补偿公式: 补偿矢量N i, j 的坐标表 达式为 O i, j 的 x、y、z 值分别减去 Pi, j 的 x、y、z 值。设单位 化后的补偿矢量为ni, j, 测头半径为 R, 则可以推出被测 点 Q i, j 的坐标公式, 即测头补偿公式为 (本公式按坐标 分量进行计算 ):
三坐标测量机测量误差分析及补偿方法

三坐标测量机测量误差分析及补偿方法发布时间:2021-01-12T05:24:05.499Z 来源:《中国科技人才》2021年第1期作者:田晓春[导读] 为了更好地对三坐标测量机测量的误差进行分析和研究,所以本文首先主要对三坐标测量机的含义以及测量原理进行了明确,其次,在多方面对三坐标测量机的测量误差展开分析,这样能够有效地提高分析的效果。
中车齐齐哈尔车辆有限公司黑龙江齐齐哈尔 161002摘要:为了更好地对三坐标测量机测量的误差进行分析和研究,所以本文首先主要对三坐标测量机的含义以及测量原理进行了明确,其次,在多方面对三坐标测量机的测量误差展开分析,这样能够有效地提高分析的效果。
与此同时,在对三坐标测量机误测量误差展开分析时,主要从以下三个方面展开:第一是环境温度误差,第二是光栅误差,第三是装配误差,这三方面都能够有效的对测量误差进行分析,并且能够取得较好地效果。
本文还针对三坐标测量机测量误差的补偿方法展开了研究,在研究过程中,主要从两方面开展,第一是温度补偿法,第二式动态误差补偿法。
关键词:三坐标测量;误差分析;补偿1 三坐标测量机的含义及测量原理三坐标测量机是属于当前时代发展背景下的新型高精度的测量仪器,相比传统的测量以及三坐标测量机,能够更加稳定地提高测量的效果,防止出现测量失误,并且能够提高测量的精准程度。
与此同时,本文针对三坐标测量机的测量原理也展开了研究和分析,可以明显地发现,三坐标测量机主要是通过坐标测量的原理来进行实物测量,首先,在生活中寻找需要测量的物体,并且将物体当中的几何元素提取出来,明确几何元素中的具体测量坐标,根据所寻找到的坐标展开集中测量。
在进行测量时,应当按照严格的测量标准来进行,主要测量几何元素的具体尺寸以及形状大小等。
截至目前,三坐标测量机已经逐渐广泛地应用在各大车间的测量过程中,并且取得了较好的效果,突破了传统测量方式的限制,在测量精准程度上做出了很大的提升。
用三坐标测量机进行曲面测量的方法

用三坐标测量机进行曲面测量的方法毫题报遵用三坐标测量机进行曲面测量的方法在汽车生产制造中,许多零部件具有的高精度三维曲面和曲线轮廓度需要用三坐标测量机进行测量,经过多年摸索实践,归纳总结出该类测量问题的规范流程,操作起来比较方便实用.1确定曲线,曲面上检测点的方法三坐标测量曲线和曲面必须通过测量点的法向矢量进行打点,否则在三坐标机数据处理及测头半径补偿时将产生投影余弦的误差如何得到测量点的法向矢量数据信息主要有2条途径.一是从三坐标机测量软件平台直接获取见图1.在测量软件亚台读^披测件的CAD数模■存零件标系毒输入测量点的警标值.或用MUOSE手工在被则露直接取点+I直接对被测件取点进行测量}'+'输出测量结累:有数据文件报告也可以设鼹为带测量点数据框的图形报告图2图1二是利用CAD软件平台获取,见以上2种取点方法具有不同特需检查加工出来的产品待机床稳定后,也只需抽检~部分产品.在线检测量仪的应用使得原来100%的检查变为抽检工作量及操作失误减少了.机床控制性能提高了同一上海萨克斯动力总成部件系统有限公司陈其伟{在eAD软件平台上读八祓测件的cAo数模l●●II属外形曲面}I属型腔曲面J上'1L上利用CAD的编辑功图纸指定测量点坐标图纸无指定测爱点坐标能,加截面得交线输八指定测量点坐与技术开发部商定测在交线上设置均匀标值,并找到点量点的位置和数量或按疏密要求取点●在CAD软件中打开几伺元素程性点的Information信息框.选中全部数据并储存为aa文件,然后打开事先用VB语言编制通用的数据转换程序"FormUG2"fAutoLisp App!icationSOUFC8类型)文件,转换为AA.T×T文件进入三坐标机,编制测量程序..程序中育事先用VB语言编制的"blade(VisualBasic Module类型)文件.读AA TXT,自动打点.并梅测璧结果文件储存在指定目录下进人Excel平台,读入测爨结果数据文件,用VB软件编制的文件对数据进行处理后输出某截面的啦线图形报告点.方法一,因为是在三坐标测量机的测量软件平台上读取被测零件的CAD数模,在CAD数模上取点后获得测量点的坐标值和矢量值,因此可直接测量,不需要考虑数据时废品率也随之降低.为用户加工出更高精度的合格产品.通过实际应用.我们认为在线检测量仪可以很好地解决毛坯及人工检查带来的诸多问题.在线检测量仪的应用最图2从CAD到测量软件的转化问题.但是三坐标测量机软件的CAD数模的编辑功能不如普通CAD的编辑功能不能任意地加截面,加直线.取点时的条件设置功能也不如普通CAD所以难以取得有规则的某终得到了用户的认可,同时也提高了该自动线的自动化程度和技术含量.使得装备公司在组合机床测量与控制方面的技术达到了国内领先~'-7-.圃8I汽车工艺与材料AT&M2009年第12期考题撩追些点.另外.当需要取点数量较多时所用时间较多.故影响三坐标机的测量利用率,所以该方法适用于CAD数模上取点比较简单,随机且测量点数不多的情况.方法二,因为CAD软件本身具有强大的编辑功能,在选择各不同曲面时.可对图形曲面.尤其是内腔曲面加些截面,得到交线后需要按设置点数均匀取点,或需要按曲面曲率大小不同取疏密不同的点时都比较方便.如果被测曲面大.需要加若干个截面.取点数多,就越体现其优势.但问题是从CAD平台到测量平台之间需要数据转换.要有数据接IZI.为此我们用VB语言编制了通用性的FormUG2数据转换接口程序,针对UG2输出点的几何属性信息框中的数据格式.取出需要的X,y,Z,f,J,K数据.按TXT文件格式排列,而且可以不受取点数量限制.在测量平台中为了读取TXT 文件中的数据.并能自动打点,我们又用VB语言编制了通用性的blade 程序,即自动读取测量点,在被测件坐标系内自动测量的程序,也不受打点数量限制,并将测量结果文件储存在指定的目录.这样,在CAD数模上取点方便.编程测量也比较流畅且简单可行.2二类不同被测曲面的不同检测方法当被测件本身可以找到特征元素用于建立零件坐标,坐标系原点在被测件上.完全可用上述流程操作,例如车灯,内饰件,发动机气缸体的气道型腔等可以通过安装孔或定位点的测量来建立零件坐标.汽车发动机零件"下进"的气道曲面和液力变矩器中重要零件"导轮"的叶片都有明确的基准,通过测量夹具定位能直接建立零件坐标然后测量曲面.见图3.当被测件本身找不到特征元素可以用于建立零件坐标时,如液力变矩器中的涡轮叶片.零件坐标原点是叶片的回转中心,不在零件上,为了测量叶片的面轮廓度.就需要插入另外一段流程.汽车液力变矩器中的涡轮叶片,被测件本身可以通过测量某要素来建立零件坐标加上复杂曲面和边缘的加工误差,其正确定位有困难.见图4,图5.首先必须设计测量夹具.在CAD中将被测件安装定位到夹具上.并建立零件坐标系与夹具坐标系的转换关系(①对夹具的定位可靠性必须进行MSA分析合格.②因为夹具制作存在误差.被测件定位点加工也会有误差使得实际夹具定位及坐标转换后与理论坐标之间还会存在不可忽略的误差,所以必须进行数次最佳拟台,在测量软件中运用"Bestfit"功能修正由于定位的偏差而造成的坐标转化的偏差),同样可以按上述流程获取测量点的TXT文件.然后在编制测量程序时,首先对夹具测量建立夹具坐标系,按转换关系转换到零件坐标系.再执行通用性的blade程序,即可打点测量曲面,并自动输出测量结果.3输出曲线,曲面检测数据结果的图形报告在曲面测量的流程中还有一个重要特点是被测曲面与指定截面交线的测量结果图形输出报告,见图6.图6是我公司为SGM配套的液力变矩器其中的一个泵轮壳冲压成形时测量回转体曲面轮廓度的部分图形报告.因为泵轮壳是回转体,所以过回转中心的2个垂直截面与曲面相交的曲线进行测量.得到4个曲线组成的1份报告.该报告是用VB语言编制的接口,将测量数据文件转换到Excel平台然后利用Excel的绘图功能,画出理论,上/下公差及实际测量结果4条曲线.为了能在1份报告中放入4个图形,又能把误差明显地表达出来,我们采用上,下公差和实际测量结果3条曲线均在各个点的法向矢量上放大5O倍.得到上述图形报告.在图形中有超差点的状态,又有轮廓度数值.经过数年的实践.无论是新产品试制.还是批量生产过程的监控.都获得一目了然的效果.根据图形报告结合现场加工的信息,能分析出各种缺图4图3图52009年第12期汽车T艺与材料A T&Mj9 毫题撮厘'—5—1O一15—2O一25-30-35-40轮廓(1):0.45},}/,',,/\~-,:—5—10—15-20-25-30-35-40轮廓(2):0.47 一●''//—l,r50556065707.58085909510010511011512O125130505560657075808590951001051 10115120I25130-5—1O~15-20-25-30—35—40轮廓(3):056,'i/./,—,:\,—:505560657075808590951.o105"011512.125130 陷.如冲压压力不足的图形特点模具个别弹簧断裂的图形特点;钢板屈服极限造成的材料局部堆积增厚的图形特点等.测量结果图形输出报告是快速初步判断,进而采取措施的重要依据.在排除隐患后可得出如图7所示的合格产品质量图形报告.经过多年坚持至今.已经为5O-5—10—15-20-25-30-35-40—455-5—10—15-20-25—30-3,5-40—45轮廓(1】:0.10 图6轮廓《4):050 ●'/.\\=≯—≮过程产品质量保持稳定状态发挥了巨大的作用.图8是液力变矩器重要零件导轮叶片轮廓测量图形报告.图9是发动机"下进"零件气道内腔轮廓测量图形报告在图形上点击其中任一测量点,可立即显示其坐标数据.在三坐标机的软件中有一种形{;~,,,//',矗:,.'5070轮廓《3):01090110130,/,,'\,,\~■,.t~,——'~—,一5O-510 —15 - 20 - 25 —30 - 35 - 40 —45 5 O 一5 —10 —15 - 20 - 25 —3035-40—45式的图形输出报告,即在被测零件的图形上对每个测量点都引出数据框,如图1O是液力变矩器涡轮叶片的测量图形报告,显示每个点的理论值和测量值,当测量点多到一定量时,数据框就会布满整个报告版面.从中要找出有问题的点则感觉不是很容易.所以,我们更改为采轮廓(2):014,./,,,t,_/f\,t~一.,:,~~….一一一.507090110130轮廓{4)=013}_≤,,,.,~~,一-——:一507090110130507090110130图710}汽车T艺与材料AT&M2009年第12期专题报蓬28弦猩21揭{78161420一DffJ—!'kI'{'■jl.I},÷,一}l,,,.,,lj..●豇,{_—七j!lJ——L—_』一.一!~"JSc--i--『f一..二#:-一图8{.■''I~了…Q1g,qq49I图9图10用图11形式的报告.图中既有超差点的状态,又有轮廓度数值且比较直观.图11是以零位线作为理论曲线设立上,下公差线,然后用实际测量点描述的曲线.每枚叶片测量分内,外2条曲线.所以有2幅曲线图.[三三三[三二]羹度测量值mm1号0054/\/\一,——39111】92527293135373941《2号0.05501OO8OO60040O2—002-004-0O6-0.08~01一/t-.,,/,_--^_--..,lr791tt~12.192]_,ig~"25272931∞35373941《''一图11龟涂装祷.薯书||l圃本书是《实用电镀蛛丛书》(第二批)的一个分册.全书系统介绍了-装及涂料方础知识,涂装工艺管理及设备,漆膜弊病及性能测试方法,涂葺用及污水女£瞰术等内容j蕾涂装泳涂装的工程技术人员和管理人员的工作指一;也可作为电泳涂装及设备设计科,el-,电游l-'奢料生产r知豆鼠部特技人员的参考读铂l还可作两夫专院校和专培试龌的敏拣| (wwwco7m8.cn)_02674...元?谱葛登泰亿肆i业电妊娃'盎查询心口.l.ll2009年第12期I汽车工艺与材料AT&MI11i864202468)0OO0OO0O1O00OOOOO—。
三坐标测量机测量误差分析及补偿方法
43工业技术0 引言 作为高精度测量设备,三坐标测量机的误差问题一直存在,使得测量结果出现了可靠性不足的问题,那么为了进一步提高该设备的应用价值,有相关学者针对三坐标测量机的各类误差,提出了相对的补偿方法,理论上可以消除各类误差,得到准确的结果。
1 三坐标测量机常见误差类型 在相关理论基础上,三坐标测量机的误差类型可以分为两类,即静态误差、动态误差,其中静态误差的特点在于其误差值会始终保持在稳定水平,而动态误差则会随着存在时间的增长而增加,所以在误差补偿角度上,应当先对两种误差进行了解,再选择相应的方法。
下文将介绍三坐标测量机静态误差、动态误差的产生原因以及事例表现。
(1)静态误差。
三坐标测量机的静态误差产生原因一般在于:外部因素对设备结构造成了瞬时性影响,此类影响带来的误差因为影响转瞬即逝,所以不容易发生变化,但这一表现不代表静态误差的影响力不大,因为在通常情况下静态误差的误差值要大于动态误差的初始值,乃至动态误差经过一段时间发展后也无法超过静态误差值,所以应当对静态误差保持重视。
在事例上,在三坐标测量机测量当中,其侧头测针存在磨损现象,此时就会形成静态误差[1]。
(2)动态误差。
三坐标测量机动态误差的产生原因有很多,例如温度、灰尘、人工等外在因素,此类误差在大部分情况下都会随着时间的延长而增加误差值,但在特殊情况下会表现出不稳定的动态化表现。
在事例上,在三坐标测量机测量当中,周边的温度、灰尘会随着时间累积而增长,相应引起的测量误差值也会随之增长,这即为动态误差的常规表现;在人工因素下,介于人工不稳定性的特征,其采点测量速度会不平衡,但具体表现却无法预测,由此就形成了不稳定的动态误差表现[2]。
此外,在静态误差与动态误差的综合角度上,静态误差本身虽然不会因为时间增长而发生变化,但在其他因素条件下,其会出现动态性表现,例如侧头测针磨损现象就会在长期应用当中愈发严重,这即为一种动态性表现,针对这一现象,在误差补偿中影响以当前静态误差值为基准来进行计算,以保障计算结果准确性。
三坐标测量机测头半径补偿技术及应用
W ANG n mi Ho g n
( c ol f c a i l n ier g S a d n nvr t o eh o g , io 5 0 9 C S ho o hnc gnei , h n o gU i sy f c n l y Zb 5 4 , HN) Me aE n e i T o 2
还 能进 行形位 误差 的精 确评定 。其 最典 型 的代 表是 三
坐 标 测 量 机 ( oriae Mesr g Mahn s简 称 C odn t aui cie n
表 球心 轨迹 的 曲线 、 面后 , 要 进 行 测 头 半径 补 偿 , 曲 需 求 出与 球心 轨迹 相距 r 的包络 线 、 包络 面 , 而构 建 出 从 所要 求 的 曲线 、 曲面 ¨ 。
Absr c :An i d p h su y o o e s to e h oo y f rp o a i s o o d n t e s rn c i e wa ta t n- e t t d n c mp n ai n tc n lg o r be r d u fCo r i ae M a u g Ma h n s i dn o e,a d t e fa i i t f2 a d 3 c mp n ai n t c noo s a a y e n h e sbl y o D n o e s to e h l g wa n lz d,t erc a a trsi sa i D y h i h r c e tc nd i
Th1 d 工艺 与检 测 en g n co y 0a
三 坐标 测 量 机 测 头 半 径 补偿 技术 及 应 用
三坐标测量机球头测针补偿技术
三坐标测量机球头测针补偿技术*李君波 助理工程师(第七一七研究所)摘 要: 介绍了手动三坐标测量机测头跟踪原理,并分几种情况探讨了使用球头测针进行点位测量时,被测点坐标值的补偿方法及实现途径。
关键词: 三坐标测量机 球头测针 补偿* 收稿日期:1999-11-20。
1 引 言在使用手动三坐标测量机对工件进行多点位测量时,由于被测物体形状各异,工作量很大。
因此,提高硬件测量速度、改进操作流程、增强软件容错性及软件智能性等是提高测量效率的主要手段。
2 测头跟踪机制测头跟踪机制是一种增强软件智能性的技术。
其工作原理如下:图1链队列示意图图2 循环队列示意图每次测量一个点位,无论是重测还是新测,测针都需要运动一段距离,因此可在软件中设置跟踪机制,自动追踪测针的运动轨迹,根据采集到的测针碰触被测点位之前一段距离的坐标值集C OOR-SE T ={node 1,node 2, ,node n}(node n 为跟踪的最后一个坐标值)。
可分析测针从何方位碰触被测点位,再在使用球头测针时自动补偿,而不必在测量之前手动指定测量方位,增强了测量的智能化程度,提高了工作效率。
因为必须保存坐标值集COOR-SET 并且需在测针运动时不断更新数据、加入最新的坐标值、去除最老的坐标值,因此,坐标值集COOR-SE T 构成一个先进先出的队列。
可采用两种方式实现,即链队列和循环队列。
若采用链队列的方式,当加入新的结点P同时删除最老的队头结点时,进行如下操作:new(P); 申请新结点;p->data=xyz data;p->next=NI L;填入数据域,指针域置空;q.rear->next=P;q.rear=P;插入队尾;构成新的队尾结点。
q.front->next=q.front->next->next;free(q.front->next);修改队头指针指向原队列第二个结点,同时释放原第一个结点;注1:xyz data及结点的数据域分别为结构型XYZ DATA和DATA,描述为:struct ZYZ DATA{double x;double y;dou ble z;}struct DATA{double x;double y;double z;}为简单从事,以上语句p->data=xyz data;表示将三维坐标值同时赋值;实际编程时C语言不支持结构型变量的整体赋值。
三坐标测量机误差补偿方法
三坐标测量机的精度提高可通过使用固定补偿模型或自适应补偿模型,或将两者结合起来完成。
固定补偿模型取决于坐标测量机误差的检测结果及所建立的校正表。
例如, 使用激光干涉仪标定的光栅尺校正值表, 可用于坐标测量机光栅尺的线性度补偿。
有研究表明,用三坐标测量机进行测量时,需要对测头半径进行补偿。
在对现有的测头半径补偿方法进行分析的基础上,提出一种“四点共球法”,可以实现对测头半径的补偿。
测量时还能使用自适应补偿模型,这种方法用于正坐标测量机随机发生的几何构成上的变化。
提高坐标测量机精度的成本取决于测量机的重复而不是几何精度。
通过精度提高一般可使几何误差减少80%~ 90% 。
第三种方法是对测量机光栅尺及工件都进行了校正,校正后, 由热膨胀引起的误差可减少80%以上。
温度测量的不确定性及热膨胀系数的变化留下10% ~ 20% 的残差得不到校正。
但当温度迅速变化时, 由于情况变得复杂, 线性温度补偿不能很好地起作用。
- 1、下载文档前请自行甄别文档内容的完整性,平台不提供额外的编辑、内容补充、找答案等附加服务。
- 2、"仅部分预览"的文档,不可在线预览部分如存在完整性等问题,可反馈申请退款(可完整预览的文档不适用该条件!)。
- 3、如文档侵犯您的权益,请联系客服反馈,我们会尽快为您处理(人工客服工作时间:9:00-18:30)。
三坐标测量机的测头半径补偿与曲面匹配李 春 刘书桂(天津大学精密测试技术与仪器国家重点实验室 天津 300072)摘要 在非均匀双三次B—样条函数的基础上,导出自由曲面任意点的法矢量通用算法,进而提出自由曲面测头半径补偿公式;为了更好的消除自由曲面测量中的定位误差,提出了应用单纯形法,对测量原始点进行坐标平移和旋转变换,从而较好的解决了曲面匹配问题。
关键词 自由曲面 测头补偿 曲面匹配The Probe Rad ius Com pen sa tion of Free-form Surface and Surface M a tch i ngL i Chun L iu Shugu i(S ta te K ey L abora tory of P recision M easu ring T echnology and Instrum en t,T ianj in U n iversity,T ianj in300072,Ch ina)Abstract Based on non2unifo rm B2sp lines,a new current algo rithm w ith no rm al vecto r of random free2fo rm surface’s po int is deduced,and mo re,a fo rm ula w ith p robe compensati on is p ropo sed.W e offer a arithm etic nam ed si m p lex m ethod in o rder to eli m inating o rientati on erro r in the p rocess of free2fo rm surface m easurem ent.It can settle surface m atch ing w ell by sh ifting and ro tating the m easuring coo rdinate system.Key words F ree2fo rm surface P robe compensati on Surface m atch ing1 引 言三坐标测量机由于其测量精度和智能化程度较高,广泛应用于制造业的CAD CAM、产品检测和质量控制[1]。
用三坐标测量机的球形测头测量自由曲面时,得到的数据是测头中心轨迹,由于测头总有一定的半径r,因此测得的是与被测曲面相距r的包络面。
为了得到所需的测量表面,需要求出球心轨迹面所构成的包络面,这个过程被称为测头半径补偿。
在实际测量过程中,并不能做到实际曲面和标准曲面完全重合,需要将被测曲面进行旋转、平移等坐标变换,使被测曲面与标准曲面大致重合,从而达到曲面检测的目的,这个过程称之为曲面匹配。
2 测头半径补偿方法用球形测头测量曲面时,测头与被测曲面为点接触,测头半径补偿的关键是确定曲面在接触点处的法矢。
球测头与被测曲面接触时,球心一定在被测点的法线上,而且被测点一定在球心轨迹面过球心点的法线上。
因此不论能否得知被测面的法线方向或是球心面的法线方向,都能对测头半径进行补偿。
本文提出了一种新方法,不在测量过程中补偿测头半径,而只是收集测头中心坐标值,然后应用曲面建模理论,计算出球心各点的法矢量值,继而补偿测头半径。
(1)自由曲面的偏导数求法首先,根据三坐标测量机所得的原始测量点,我们可以反求出双三次B—样条自由曲面的模型[2]:S(u,v)=∑ni=0∑mj=0N i,4(u)N j,4(v)P i,j(1)其中N i,4(u),N j,4(v)为双三次B—样条基函数, P i,j为控制预点。
先求曲面沿u向的切矢量,即对S(u,v)求偏导:S u(u,v)=55u S(u,v)=∑mj=0N j,4(v)u∑ni=0N i,4p(u)P i,j第24卷第4期增刊 仪 器 仪 表 学 报 2003年8月=∑mj=0N j,4(v )55uC j (u )(2)这里,C j (u )=∑ni=0Ni,4p (u )P i,j ,j =0,…,m 为B 样条曲线。
而C ′(u )=∑n-1i=04Ni,3(u )P i+1-P iu i+4-u i+1,所以:S u (u ,v )=∑n-1i=0∑mj=04N i,3(u )N j,4(v )P i+1,j -P i,ju i+4-u i+1(3)同样,我们可以得出:S v (u ,v )=∑ni=0∑m -1j=04Ni,4(u )N j,3(v )P i,j+1-P i,jv i+4-v i+1(4)S u (u ,v )和S v (u ,v )分别为曲面上的点沿u 向和v 向的切矢量。
(2)曲面的测头半径补偿公式被测曲面与测头中心轨迹曲面是法向等距面关系。
测头中心轨迹曲面上的任意点处的单位矢量可以得出:n τ(u ,v)=S u (u,v )×S v (u,v ) S u (u,v )×S v (u,v )(5)其中S u (u ,v )和S v (u ,v )可以由式(3)(4)得出。
根据测头半径值r ,可以推出被测实际曲面的补偿公式为:P (u ,v )=S (u ,v ) rn τ(u ,v )(6)当测头位于被测曲面法矢量所指的一侧时,取“-”号,反之,取“+”号。
(3)计算机仿真结果利用解析曲面进行数字仿真计算,用以考察所述方法的精度。
为了方便计算,我们考虑一个椭球面,方程为x23002+y 25002+z 23002=1。
在第一象限内非均匀的取点P ′i,j ,并用解析方法将其转换为法向等距面上的点S i,j ,模拟测量数据。
应用本论文所述方法对得到的模拟数据进行曲面拟合与测头半径补偿,得到生成曲面上的点P i,j ,将其与原始数据P ′i,j 比较,以偏差e =m ax P ′i,j -P i,j 为指标。
设测头半径r =5mm 。
表1 最大偏差e 的计算结果n u n v m u =10m u =20m u =300.61.26×10-44.28×10-52.24×10-50.78.25×10-53.57×10-51.75×10-50.82.23×10-51.09×10-56.31×10-60.9——1.58×10-58.29×10-6 设测量点数为m u ×m v ,令m u =m v =10,20,30,节点控制数n u =n v =(6 10 9 10)m u ,取得的偏差如下表,可以看出,偏差e 随着测量点数的增大而减小,节点控制数也对偏差有一定的影响。
由此可见,本方法具有一定的计算精度。
3 曲面匹配曲面匹配是曲面误差评价的基础,在曲面检测和逆向工程中,经常要用到曲面匹配。
曲面的匹配实际上是一种受约束的拟合,利用测量点进行拟合的结果是一个其形状与理想轮廓曲面完全相同的曲面。
将测量所得的原始点进行适当的平移和旋转后,理论曲面与测量曲面将“贴合”得相当完美。
(1)坐标系的“旋合”过程假定被测曲面存在M 个原始理论点P ′i (x ′i ,y ′i ,z ′i )(i =1,2,…,M ),被测曲面的拟合模型为:z =f (x ,y )。
将M 个原始理论点P ′i 进行坐标平移和旋转变换,得出一组新的理论点值P i (x i ,y i ,z i )(i =1,2,…,M )。
x i y i z i=A ・x ′i y ′i z ′i+x 0y 0z 0(7)其中:A =co s Αco s Β+sin Αsin Βsin Χsin Αco s Β-co sΑsin Χ+sin Αsin Βco s Χ -sin Αco s Χ+co s Βsin Χco s Βsin Χco s Αco s Β-sin Βsin Αsin Χ+co s Αsin Βco s Χco s Βco s Χx 0,y 0,z 0是三个坐标平移量,Α,Β,Χ是三个坐标旋转量。
当x 0,y 0,z 0,Α,Β,Χ恰好是理论坐标系与测量坐标系之间的旋转平移关系时,M 个新理论点P i (x i ,y i ,z i )与拟合模型z =f (x ,y )最接近。
再定义一个新函数:F (x 0,y 0,z 0,Α,Β,Χ)=∑Mi=1(f (x i,y i)-z i )2(8)经过坐标变换后,M 个新的理论点P i 与拟合模型z =f (x ,y )最接近时,F (x 0,y 0,z 0,Α,Β,Χ)为最小,于是,曲面匹配的问题变成了求:F (x 0,y 0,z 0,Α,Β,Χ)→m in (9)时的x 0,y 0,z 0,Α,Β,Χ的值。
(2)单纯形法的求解思路由于式(9)含有非线性运算(含有正弦、余弦),一般情况是先将它进行线性化,将其展开为泰勒级数形641仪 器 仪 表 学 报 第24卷 式,舍去二次高阶项,这样比较复杂,这里我们应用最优化算法中的单纯形法进行求解。
单纯形法是一种不必计算函数梯度的直接搜索法,它能自动适应函数的局部环境变化,在极值附近内将会收缩。
算法如下:1)令n 维空间的单纯形的n +1个顶点为:x θi (i =1,2,…,n +1)计算函数值F i =f (x θi )(i =1,2,…,n +1),比较大小,并确定:F R =F (x (R ))=m ax 1≤i ≤n+1F i(极大点)F G =F (x (G ))=m ax 1≤i ≤n+1F i(次极大点)F L =F (x (L ))=m ax 1≤i ≤n+1F i(极小点)2)求出最坏点x (R )的对称点 x N =2x F -x (R )式中:x F =1n ∑n+1i=1(x (i )-x (R ))。
3)若F (x N )≥F R ,则将x N 缩小为x M ,x M =(1-Κ)x R +Κx N (0<Κ<1,Κ≠015)如果F (x M )<F (x G ),那么x (R )=x (M ),并重复以上步骤。
如果F (x M )≥F (x G ),那么x (i )=x (i )+x (L )2,并重新开始迭代。
4)若F (x N )<F R ,则将x N 扩大为x E ,x E =(1-Λ)x R+Λx N (Λ>1)如果上述条件满足,并且F (x E )<F (x N ),那么x (R )=x (E ),否则x (R )=x (N ),并重复以上步骤。
上述过程一直继续到∑n+1i=1(F i -F L )2<Ε或F R -F L <Ε F L 为止,其中Ε是预先给定的正数。