坐标测量机测头半径的补偿方法
CMM测量曲面测头半径补偿与路径规划研究

关键词 :三坐标测量机 ;曲面测量 ;测头半径补偿 ;测量路径规划 ;逆 向制造 中图分类号 :T 3 1 P 9 文献标识码 :A 文章编号 :10 —3 8 20 )3— 7 3 0 1 8 1(0 6 05—
Th s a c n P o e Ra i sCo e Re e r h o r b d u mp n a in a d M e s rn a ePln i g o e s t n a u i g Tr c a n n f o Co lx S ra e CM M e s r me t mp e u fc M a u e n WA G Z nqa g I i jn N e gin ,LN Xa u ,R N Jn u o E u x e
测头与 曲面接触点 的坐标成为 了 目前研究热点 。测头 半径补偿的研究成果有¨ s:( )微平面法是在被测 -] 1 点周 围等距离 a取三个点 ,在 a足够小 的情况下 ,三 点构成 的平面法 向量可 以认为是被测点 的法 向量 ,此 时测头只要沿着该 向量方 向去测该点 ,被认为就会得 到正确 的测头半径 补偿 。 ( )平 均矢 量法是针 对被 2 测面 比较宽坦 的曲面而言 ,可 以采用该方法 。先在被 测 曲面上定义一 网格 ,而后对 这些 网状 点进行 测量 。 用测头逼近给定点 ,直到输 出结果满意为止 。这些 网 点所形成 的网格线能够反映 出被测 曲面 的特 征 。 ( ) 3
me s r me t ne t n CMM r b a i sc mp n ain a d me s r g t c l nn r s a c e n tr o i e n d s I a u e n tn i . i o p o e rd u o e s t n a u i a e p a i gwe er e r h d i m f wo df r t o n r n e e t e mo e . t
三坐标测量机的误差分析及其补偿

收稿日期: 1996- 03- 06 © 1994-2006 China Academic Journal Electronic Publishing House. All rights reserved.
46
沈 阳 工 业 学 院 学 报 1997 年
1. 2 三坐标测量机测头位置误差表达式
式 (1) 对坐标平移和旋转的坐标变换可应用到三坐标测量机中各滑台的平移和转动误差 向绝对坐标系的转换.
图 3 坐标系 向坐标系 的变换
图 4 三坐标测量机的坐标变换示意图
在图 1 中的 X 、Y、Z 的滑尺上分别建立三个坐标系 、 、 , 且使三坐标测量机的测头
xp
y=
- ex y + A - M y m - ey y + A -
- ezy + A -
yp
(3)
z
- ex z
- ey z
zm - ezz
zp
式 (3) 中的各误差项均是以绝对坐标系原点为起点, 在单一运动方向上测量的, 其误差评定基
准是理想的坐标轴方向. 因此, 式 (3) 中的误差分量包含三个滑尺运动方向的相互垂直度误差.
48
沈 阳 工 业 学 院 学 报 1997 年
x = x m - ex x - ey x - y m Ηx z (5)
y = y m - ex y - ey y
工作台数显装置为光栅尺, 误差测量装置和坐标值检定用双频激光干涉仪. 实验数据如表
2 所示.
表 2 测量数据
从实验中看出补偿后坐标值更接近于坐标检定值, 显示误差分别为 exm = 010479 mm , eym = - 010039 mm , 而补偿后坐标定位误差为 ex = 010038 mm , ey = 010005 mm.
三坐标测量机测球直径的校正和误差分析

三坐标测量机测球直径的校正和误差分析摘要:三坐标测量机(CMM)以其测量精度高、稳定性好、操作方便快捷的特点广泛的被应用。
但是在使用三坐标测量机测量有些几何要素时,有时测量准确度不是很高。
文章对坐标测量原理进行简述,重点分析三坐标测量机测球直径的校正与误差。
关键词:三坐标测量机;球直径;误差1坐标测量的原理任何形状都是由空间点组成,所有的几何量测量都可归结为空间点的测量,因此精确进行空间点坐标的采集,是评定任何几何形状的基础。
坐标测量机的基本原理是将被测零件放入它已允许的测量空间,精密地测出被测零件表面的点在空间3个坐标位置的数值,将这些点的坐标数值经过计算机数据处理,拟合形成测量元素,如圆、球、圆柱、圆锥、曲面等,经过数学计算的方法得出其形状、位置误差及其他几何量数据。
用CMM进行零件测量,理论上,测头的球半径应为零,测头和工件接触为测头中心。
得到的数据是测头中心的坐标值,而非测头与被测件接触点的坐标值。
但实际上,测头有一半径,从而需要对测头直径进行校正,即进行测头球心轨迹曲面域和测头半径补偿。
2三坐标测量机测量的主要步骤2.1测头选择测头部分是测量机的重要部件,测头根据其功能有:触发式、扫描式、非接触式(激光、光学)等。
触发式测头是使用最多的一种测头。
一般的测头头部都是由一个杆和测球组成。
最常见的测球的材料是红宝石,因为红宝石是目前已知的最坚硬的材料之一,只有极少的情况不适宜采用红宝石球。
高强度下对铝材料制成的工件进行扫描时,选择氮化硅较好;对铸铁材料工件进行高强度扫描,推荐使用氧化锆球。
为保证一定的测量精度,在对测头的使用上,需要注意:(1)测头长度尽可能短:探针弯曲或偏斜越大,精度将越低。
因此在测量时,尽可能采用短探针。
(2)连接点最少:每次将探针与加长杆连接在一起时,就额外引入了新的潜在弯曲和变形点。
因此在应用过程中,尽可能减少连接的数目。
(3)使测球尽可能大:测球直径较大可削弱被测表面未抛光对精度造成的影响。
接触式测头测量中测头半径补偿的研究
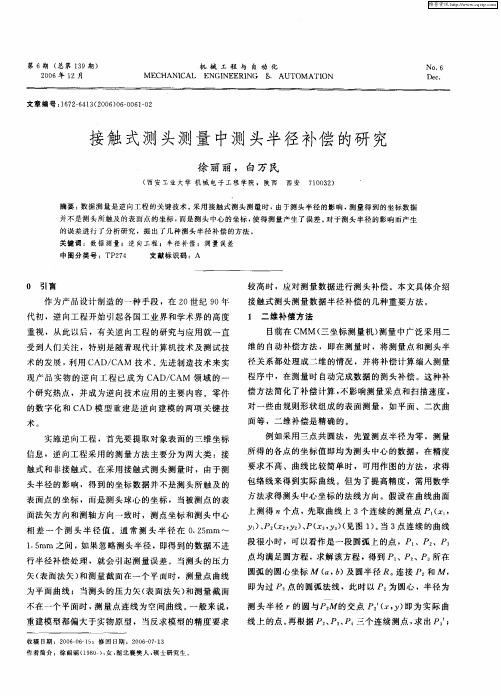
0 引 言
较 高 时 ,应对 测量 数据进 行测 头补 偿 。本 文具 体介 绍
接 触式 测头测 量数 据半径 补偿 的几 种重要 方 法 。 1 二维补偿 方法
作 为产 品设计 制 造 的一 种手 段 ,在 2 世 纪 9 O O年
代初 ,逆 向工程 开始 引起各 国工 业界 和学术 界 的高度
的数 字化 和 C AD模 型重 建 是逆 向建模 的两 项 关键 技
术。
实施 逆 向工程 ,首 先要 提取 对象表 面 的三维 坐标
例 如采用 三点 共 圆法 ,先 置测 点半径 为零 ,测量
信 息 ,逆 向工 程采 用 的测量 方法 主要分 为两 大类 :接
触式 和非接 触式 。在采 用接触 式 测头测 量时 ,由于测 头半径 的影 响 ,得 到 的坐标 数据 并不是 测 头所 触 及 的 表 面点 的坐标 ,而 是测 头球心 的坐标 ,当被测 点 的表 面法矢方 向和测轴 方 向一致 时 ,测点坐 标 和测 头 中心 相 差 一 个 测 头 半 径 值 。通 常 测 头 半 径 在 0 2 mm~ .5 15 . mm 之 间 ,如果 忽略 测头半 径 ,即得 到 的数 据 不进 行 半径补偿 处理 ,就会 引起测 量误 差 。当测 头的 压力 矢 ( 面法矢 ) 表 和测 量截 面在一 个平 面 时 ,测量 点 曲线 为 平面 曲线 ;当测 头 的压力矢 ( 面法 矢) 测量 截面 表 和
个 研究 热点 ,并成 为逆 向技术 应 用 的主要 内容 零件
径 关 系都处理 成二 维 的情 况 ,并将 补偿计 算 编入测 量
程 序 中 ,在测 量时 自动 完成数 据 的测头 补偿 。这种 补
偿 方法 简化 了补 偿 计算 , 不影 响测 量采点 和扫 描速度 ,
曲面测量时球头半径空间补偿

则需要三维的球头半
径补 偿,由 于 补 偿 的
方向难于直接精确得
到,人 们 尝 试 研 究 各
种方法来解决这一问
题。
1 球头半径的空间
补偿法
在对形状复杂的
自由 曲 面 测 量 中, 为
保证测量精度的同时
也为了减少测量工作 量以及后续数据处理
图 1 自由曲面测量中测 头与被测面关系
* 基金项目:山东省高新技术研究发展计划课题支持
可以选择较小,随着采样密度的增加,被测曲面上点
P 处的法矢量与测头中心所决定的曲面( 记为) 在 O1 点处的法矢量34n1 趋于共线,可用34n1 代替式(1) 中
的 n,。这就是空间补偿法的原理。 在34n1 的求解中,过去有“ 微平面法”、“ 平均矢
量法”、“ 三点共圆法” 等[4],这些方法需要大量的
《 机床与液压》2006. No. 3
·49·
工作 量, 测 量 往 往 在 一 次
(或最少次) 装夹中完成,测
头的测量方向无法实现与测点
处法矢方向一致,所以实际测
量接触点 P 一般不在测量平面
内( 图 1 ),而 且 测 量 方 向 与
表面测点处法线的夹角是不定
的,如 果 按 照 简 单 两 维 补 偿
·48·
《 机床与液压》2006. No. 3
自由曲面 CMM 测量中球头半径空间补偿方法的研究*
崔焕勇1,2 ,李兆前1 ,高琦1
(1. 山东大学机械工程学院,山东济南 250061;2. 济南大学机械工程学院,山东济南 250022)
摘要:为解决自由曲面 CMM 测量中测头半径补偿问题,沿用了基于测头中心点所在曲面法矢估算的空间补偿方法, 引入转动惯量法进行测头中心点所在曲面各点处法矢的求解,并解决了边界点补偿的问题。该方法避免了根据离散点构建 样条曲面而进行大量而复杂的计算过程,数据处理简单,并可通过程序实现,具有较高的效率。
三坐标测球半径如何补偿误差以及流程是什么?

三坐标测球半径如何补偿误差?当测针接触到工件时,三坐标测量机接收的的坐标值应是红宝石球头中心点坐标,显然,测量软件将自动沿着测针从接触点回退的方向加上一个测球半径值作为测量值。
但该测量值是一个与测头的机械惯性有关的动态值。
实际上,测量作为一个动态过程,其测量值应该考虑到从测头采点到实际向系统传送该点坐标值时发生的机器空间移动距离。
尽管这个距离极小,但对系统计算动态尺寸有一定影响。
在实际测量时,每测量一个元素,系统都可以自动区分测球半径的补偿方向,计算正确的补偿半径。
在采点开始后,测量软件将在沿着测针接触工件的方向上对测球进行半径补偿。
但被补偿点并非真正的接触点,而是测头沿着测针接触工件方向的延长线上的一个点。
这样就造成了补偿误差,产生误差的大小与测球的半径及该工件被测面与笛卡尔坐标轴的夹角有关,夹角越大,误差越大。
①测球半径r对补偿误差的影响补偿误差δ与测球半径r成正比关系,即测球半径r越小,补偿误差δ也越小。
因此当用三坐标测量机进行点位测量时,应选用尽可能小的测球。
②测针轴线与被测表面法线间的夹角α对补偿误差的影响当测针轴线与被测表面法线间的夹角α等于0时,测球半径补偿误差δ也为0。
因此,测量时要尽可能使测针轴线与被测表面垂直,使测头沿着被测表面的法线方向移动,以最大限度地减小测球半径补偿误差。
在用三坐标测量机测量点元素时,测量软件在自动补偿测球半径过程中会出现测球半径补偿误差。
通过运用参考坐标系找正工件或用CNC模式进行测量,使测头沿着被测表面的法线方向移动采集点的坐标,可以尽量减小测球半径补偿误差,正确进行测球半径补偿,提高测量精度。
三坐标测量仪如何应用在现代设计制造流程的?通过南京三坐标专家前面的一些介绍,我们知道,三坐标因其精确度广泛用于工业工件测量等行业之中,选择适合自己的三坐标有利于测量数据更加精准。
三坐标测量仪测量原理:将被测物体置于三坐标测量空间,可获得被测物体上各测点的坐标位置,根据这些点的空间坐标值,经计算求出被测物体的几何尺寸,形状和位置。
三坐标测量机误差补偿

综合误差补偿
综合硬件和软件补偿
结合硬件和软件补偿方法,通过调整 机械结构、光学元件和优化软件算法 等手段,实现更全面、有效的误差补 偿。
多轴联动误差补偿
针对多轴联动测量机,通过分析各轴 之间的耦合误差,采用多轴联动误差 补偿方法,以提高多轴联动测量的精 度和可靠性。
03 误差补偿实施步骤
误差测量
电气元件误差
测量机的控制系统中的电气元件 ,如传感器、编码器等,由于其 制造和装配过程中存在的误差, 会影响测量机的测量精度。
测量机安装误差
安装水平度误差
测量机在安装过程中,如果工作台面 不水平,会导致测量机在运动过程中 产生误差。
安装位置误差
测量机的安装位置应符合设计要求, 否则会影响测量机的测量范围和精度 。
03
基于机器视觉的误差补偿技术
利用机器视觉技术对测量机进行误差补偿,提高测量精度和效率。
人工智能在误差补偿中的应用
深度学习在误差补偿中的应用
01
通过训练大量数据,建立深度学习模型,对测量结果
进行自动修正。
强化学习在误差补偿中的应用
02 通过强化学习算法,自动调整测量机的参数,以减小
误差。
智能优化算法在误差补偿中的应用
重复性标准差
比较误差补偿前后的重复性标准差, 以量化评估误差补偿的效果。
稳定性分析
分析测量数据的分布情况,判断误 差补偿后测量机的稳定性是否提高。
比较测试
比较测试
将误差补偿后的三坐标测量机与更高精度的测量设备进行比较测 量,以评估误差补偿的效果。
测量数据对比
对比两种设备的测量数据,分析误差补偿后三坐标测量机的测量精 度是否接近或达到更高精度的测量设备。
三坐标测量机测头系统的误差分析与修正

三坐标测量机测头系统的误差分析与修正杜翠翠;徐强;冯旭刚;章家岩【摘要】测头是三坐标测量机的关键部分,其动态性能对测量机最终测量结果有直接的影响。
为了提高三坐标测量机测头的测量精度,以触发式测头系统为主,研究了测头系统动态误差的构成,分析了测头预行程误差来源及影响因素,提出了将测头直径动态标定与微平面补偿法相结合的方法对测头直径进行补偿。
通过对凹轮轮廓进行测量,并在逆向工程软件中对测头直径补偿前后进行对比。
结果表明,该方法对测量机测头直径有较好的补偿效果,具有一定的应用价值。
%As probe is the key component of coordinate measuring machine ( CMM) ,its dynamic per-formance has direct influence on the final measurements.In order to enhance the accuracy of CMM,compo-sition of the probe dynamic error system was studied with focus on introducing the touch triggerprobe.Probe pre-travel error sources and influencing factors were analyzed.The method combining dynamic calibration of probe radius and micro plane compensation was put forward to make compensation for the probe radius.Af-ter measuring the outline of a concave wheel and comparing probe radius before and after the compensation in reverse engineering software,the results showed that the method made better compensation for the probe radius and was worth more applications.【期刊名称】《常州工学院学报》【年(卷),期】2016(029)003【总页数】5页(P33-37)【关键词】三坐标测量机;测头系统;预行程误差;测头直径【作者】杜翠翠;徐强;冯旭刚;章家岩【作者单位】安徽工业大学电气与信息工程学院,安徽马鞍山 243032;安徽工业大学电气与信息工程学院,安徽马鞍山 243032;安徽工业大学电气与信息工程学院,安徽马鞍山 243032;安徽工业大学电气与信息工程学院,安徽马鞍山243032【正文语种】中文【中图分类】TH-9三坐标测量机的测头一直都是学者们的研究热点。
- 1、下载文档前请自行甄别文档内容的完整性,平台不提供额外的编辑、内容补充、找答案等附加服务。
- 2、"仅部分预览"的文档,不可在线预览部分如存在完整性等问题,可反馈申请退款(可完整预览的文档不适用该条件!)。
- 3、如文档侵犯您的权益,请联系客服反馈,我们会尽快为您处理(人工客服工作时间:9:00-18:30)。
坐标测量机测头系统误差分析与补偿方法
【摘要】本文对接触式测头系统在测量过程中和测量方法上存在的误差进
行了详细的分析,并给出了相应的补偿方法。
在测量过程中,从机械结构、测量时逼近速度和逼近距离等几个角度分析了测头误差误差来源;在测量方法上,由于接触式测头测量时所反馈的是测头中心的坐标值, 而不是被测点的坐标值,故必需对测头半径误差进行补偿。
关键词:接触式测头动态误差半径补偿
1、引言
测头被称为坐标测量机的“心脏”[1]。
测头与被测工件直接接触,测量机是用测头来拾取信号的,测量机的功能、工作效率、精度与测头密切相关,没有先进的测头,就没法发挥测量机的功能。
对测量机的精度而言,随着测量机误差补偿技术的广泛应用,使得测头在触测误差在总体误差中占有很大的份额。
测头对测量机精度的影响往往比其他因素要打,不仅在静态或准今天测量中,在动态测量中也是如此。
故对于测头而言,不仅需要对测头系统固有的误差进行分析补偿,对测量过程和测量方法上引起的误差也要给予足够的重视,这样才能使得测头的误差足够小。
现阶段由于扫描式和非接触式测头技术不够成熟,故市面上坐标测量机的大部分测头均为接触式测头,并且相较于扫描式和非接触式测头,接触式测头具有较高的精度,故本文对接触式测头的误差进行分析。
2、测头系统的误差分析与补偿
测头系统的误差主要包括测头机械结构部分误差、测量过程中因逼近速度和逼近距离不同带来的动态误差。
2.1 测头的机械结构误差
测头机械结构误差包括: 机械零件的制造误差和装配误差,如理论测针半径与实际测针半径之间的误差,该部分误差属于静态误差,一般通过测头的校准从而得以消除; 测量过程中的原理误差。
包括以下几项:
(1) 测力引起的测杆及支架的变形误差
根据测头的触发原理,测端在刚刚接触被测件时并不发出触发信号,当测端上的力足够大,它所产生的力足以克服弹簧的力,使一对接触副脱开,测头与工件相对移动一定距离,这一距离称为预行程。
预行程的变化直接影响测头的触发精度,是最大的测头误差源,且它的量值随测杆的长度或触发力的增加而增加。
尽管接触式探针的测量力不是很大,但对于高精度测量来说,测量力使得测杆挠曲变形带来的误差是不可忽视的。
挠曲变形是一个很复杂的物理过程,它受到测力大小、测杆长度、粗细、材质、接触形式等诸多因素影响[1]。
(2) 各向异性带来的预行程变化量误差
测头结构的特点决定了测头在各个方向的预行程大小不同,这会给测头带来预行程变化量误差。
这也是接触触发式测头本身所固有的误差类型[2]。
2. 2 探测速度和逼近距离带来的动态误差
当测头与被测工件表面接触后,克服弹簧预紧力,使处于闭合回路的三对球柱接触副任意一对或一对以上脱开时,数据采集和处理统根据探测器的输出变化而发送触发脉冲。
测头向控制系统发出一个触发信号后,控制系统就向CPU 发出一个中断请求,要求CPU 立即响应,并将测端球心的空间坐标值锁存。
但由于CPU 在执行完当前指令后才能响应中断,必然会带来时间随机误差r t ,同时在中断服务程序中不可缺少的现场保护会产生时间滞后,从而带来系统误差s t 。
因此从测头发出采样信号到CPU 响应中断并锁存数据,存在系统时间延时r s t t +。
若测头与工件接触时的探测速度为v ,则空间坐标的采样误差
()r s l v t t ∆=+
由此可见,若测量机的探测速度大,信号处理及传输的时间长,带来的测量误差也就越大。
在使用过程中,常常给测量设定一个逼近距离,在逼近距离内,降低测头的运行速度,以慢速去触碰工件。
采用这样的方式可以相应减小由于发讯迟滞带来的误差[2]。
3、测头的半径补偿
当测针接触到工件时, 三坐标测量机接收的的坐标值应是红宝石球头中心点坐标, 显然, 测量软件将自动沿着测针从接触点回退的方向加上一个测球半径值作为测量值。
但该测量值是一个与测头的机械惯性有关的动态值。
实际上, 测量作为一个动态过程, 其测量值该考虑到从测头采点到实际向系统传送该点坐标值时发生的机器空间移动距离。
尽管这个距离极小, 但对系统计算动态尺寸有一定影响[3] 。
在实际测量时, 每测量一个元素, 系统都可以自动区分测球半径的补偿方向, 计算正确的补偿半径。
在采点开始后, 测量软件将在沿着测针接触工件的方向上对测球进行半径补偿。
但被补偿点并非真正的接触点, 而是测头沿着测针接触工件方向的延长线上的一个点。
这样就造成了补偿误差[ 7]。
如图
1、图2 所示,产生误差的大小与测球的半径及该工件被测面与笛卡尔坐标轴的夹角有关, 夹角越大, 误差越大。
图1 测量状态图 图2 计算示意图
(1)测球半径r 对补偿误差的影响
由图2中
2222221222cos 2(1cos )4sin 2r r r r α
αα=-=-=(P P )
得: 12P P =2cos
2r α (1) 又因为: 12OP P =2sin 2
r α∠ 122OPP πβ=
-∠ (2)
在12P PP 中,有 12=PP δβ()sin (3) 将式(1)、式(2)代入式(3),故补偿误差为: 212=P P (1cos )2
r αδβα=-()sin =2r sin (4) 式中 :::r δα测球半径补偿误差
测球半径测针轴线与被测表面法线的夹角
由式(4)可以看出,补偿误差δ与测球半径r 成正比关系,即测球半径r 越小,补偿误差δ也越小。
因此当用三坐标测量机进行点位测量时,应选用尽可能小的测球。
(2)测针轴线与被测表面法线间的夹角α对补偿误差的影响
令图2中
'sin r δα=
''cos r δα= (5)
则当'=0δ时,=0α,且此时''0r δ=>。
函数具有极小值。
可见当测针轴线与被测表面法线间的夹角=0α时,测球半径补偿误差δ也为0。
因此,测量时要尽可能使测针轴线与被测表面垂直,使测量沿着被测表面的法线方向移动,以最大限度地减少测球的补偿误差。
随着人们对半径补偿的重视,目前对与半径补偿已有较多的算法,常见 补偿技术分两大类:二维补偿技术和三维补偿技术。
二维补偿技术里主要的补偿方法有:常用二维补偿法和三点共圆补偿法;三维补偿技术里的主要补偿方法有:微平面法、微球面法、曲面拟合法。
4、总结
本文通过对接触式测头的分析详细的介绍了测头在工作过程中各种因素引起的误差,并介绍了相关的消除与补偿方法。
参考文献:
[1]赵静三坐标测量机动态误差源分析与建模研究[D] 合肥工业大学 2005
[2]丁邦宙费业泰三维触发式坐标测量机测头误差分析与性能实验[J] 农业机械学报 2011.11(228-230)
[3]宋开臣等. 三坐标测量机的动态误差补偿研究. 仪器仪表学报, 1999, 20( 1) : 23~ 25
[4] 王毅. 利用电位测量法对曲面测量的测头球头半径的自动补偿. 中国计量测试学会几何量专业委员会1986 年全国年会论文集. 北京: 中国计量测试学会几何量专业委员会, 1986: 204。