10万立大型储罐施工工法
10万立罐基础施工方案

工程镇海基地罐区施工方案1、工程概况1.1本工程为国家储备库工程镇海基地罐区T—01#~18#罐、T—23#~24#罐,共计20台10×104m3罐,位于镇海岚山水库南侧附近。
罐直径为80米(环梁中心线),钢筋混凝土板式基础,底板厚650,底板底标高3.25米,面标高3.90米,基础外侧为800宽钢筋混凝土异型环梁,总高1.60米。
环梁底标高2.70米,顶面标高4.30米,沿罐基直径设置十字型通长后浇带,宽1.0米,后浇带中的承台板筋相连接。
罐基内做法为内填中粗砂垫层最薄处300厚,沥青砂绝缘层100厚(按1.5%找坡)。
1.2本工程罐基主要工程量为钢筋390t,垫层砼为520m3,罐基础为3543m3,砂垫层为2470m3,沥青砂为507m3。
1.3本工程项目砼工程量大,工期短,单罐土建工程从打桩完交付我方施工开始至交付安装,仅70天时间(按罐基础和后浇带养护各7天考虑)。
2、施工部署2.1 5月15日前施工现场生产临设完毕,钢筋车间开始加工制作钢筋。
为便与钢筋二次搬运,减少时间及工作量,故钢筋车间在每个罐基础边就近布置,每台罐钢筋制作完成后随下台罐基础施工位置作相应移位。
详见施工平面布置图。
2.2为提高砼表面的平整度、光洁度,确保结构砼施工质量,达到清水砼要求,故模板采用竹胶板,同时预先拼装制作,现场安装。
2.3砼的浇筑采用炼化公司搅拌站,供应要求供应量不少于60m3/h而且要连续供应至浇筑完毕。
2.4劳动力组织根据工程工期紧的特点,确保各分项工程保质、保量、如期完成,故劳动力的安排从公司劳动人才公司抽调具有10万立罐基础施工经验各专业队伍。
劳动力计划见下表(暂按2台罐平行施工考虑)3、施工进度计划及保证措施3.1本工程实行项目法施工、项目经理全面负责本工程的一切职能。
3.2施工进度计划3.2.1本工程总体施工进度计划根据浙江伊麦克斯公司提供的桩基完成时间进行编制。
3.2.2每台罐土建施工作业时间控制在70天。
十万立罐罐基础施工方案

十万立罐罐基础施工方案1. 引言十万立罐罐基础施工方案旨在为安装和支撑大型立式储罐提供设计的基础施工指南。
本文档涵盖了施工前的准备工作、施工步骤、质量控制和安全措施等内容,以确保施工过程顺利进行并达到预期的效果。
2. 施工前准备工作在进行罐基础施工之前,需要进行以下准备工作:2.1 地质勘察进行地质勘察是为了确定罐基础的支撑力和稳定性。
这包括对土壤属性、地下水位、地震活动等方面进行详细的调查与分析,并根据勘察结果来选择合适的地点进行罐基础施工。
2.2 施工设计根据地质勘察结果和具体的罐体要求,进行罐基础的施工设计。
设计需要考虑土壤承载力、地震抗力、排水设计等因素,并确保施工符合国家相关标准和规范。
2.3 材料准备根据设计要求,准备施工所需的材料。
这包括混凝土、钢筋、膨胀剂、构筑物支撑材料等。
3. 施工步骤3.1 罐基础标志布设根据设计要求,对施工现场进行标志布设。
包括地基中心线、基础平面边界和垂直线等。
3.2 地基开挖按照设计要求,对地基进行开挖。
确保开挖的尺寸和形状符合设计要求,并根据土壤的情况进行必要的加固和处理。
3.3 铺设抗渗层为了防止地基下渗漏水,需要在地基内部铺设一层抗渗层。
这可以使用聚乙烯薄膜或沥青防水卷材等材料。
3.4 浇筑混凝土基础在地基开挖完成后,进行混凝土基础的浇筑工作。
按照设计要求,将混凝土从预先搅拌好的搅拌车中运输到施工现场,并使用泵车或装载机进行浇筑。
确保混凝土均匀填充地基并进行充分的压实。
3.5 钢筋预埋和固定在混凝土未完全凝固之前,将预先加工好的钢筋按照设计要求预埋到混凝土中。
同时,使用固定夹具将钢筋固定在地基上,确保钢筋与混凝土的牢固连接。
3.6 基础养护在混凝土浇筑完成后,进行基础的养护工作。
包括对混凝土进行水养护和覆盖保护,以防止混凝土过早干燥和裂缝的产生。
4. 质量控制施工过程中,需要进行质量控制以确保施工质量符合设计要求。
主要的质量控制项目包括:•地基开挖尺寸和形状的检查;•混凝土强度的检测;•钢筋预埋位置和固定的检查;•基础养护过程的督导和检查。
10万立方储灌施工方案(输油管线站场)
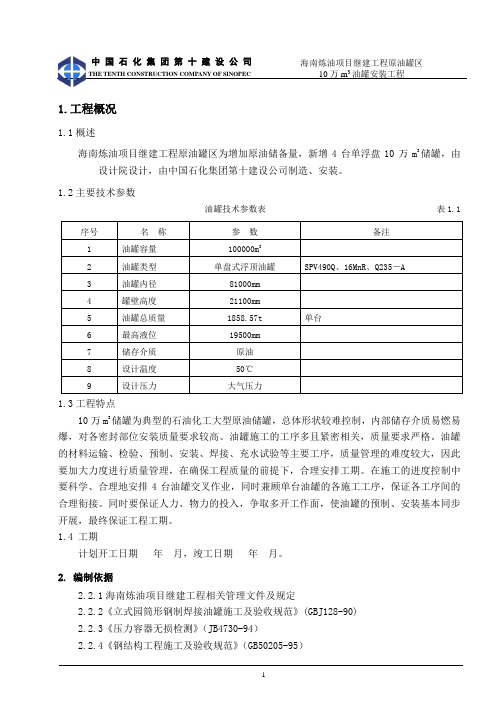
1.工程概况1.1概述海南炼油项目继建工程原油罐区为增加原油储备量,新增4台单浮盘10万m3储罐,由设计院设计,由中国石化集团第十建设公司制造、安装。
1.2主要技术参数油罐技术参数表表1.1 序号名称参数备注1 油罐容量100000m32 油罐类型单盘式浮顶油罐SPV490Q、16MnR、Q235-A3 油罐内径81000mm4 罐壁高度21100mm5 油罐总质量1858.57t 单台6 最高液位19500mm7 储存介质原油8 设计温度50℃9 设计压力大气压力1.3工程特点10万m3储罐为典型的石油化工大型原油储罐,总体形状较难控制,内部储存介质易燃易爆,对各密封部位安装质量要求较高。
油罐施工的工序多且紧密相关,质量要求严格。
油罐的材料运输、检验、预制、安装、焊接、充水试验等主要工序,质量管理的难度较大,因此要加大力度进行质量管理,在确保工程质量的前提下,合理安排工期。
在施工的进度控制中要科学、合理地安排4台油罐交叉作业,同时兼顾单台油罐的各施工工序,保证各工序间的合理衔接。
同时要保证人力、物力的投入,争取多开工作面,使油罐的预制、安装基本同步开展,最终保证工程工期。
1.4 工期计划开工日期年月,竣工日期年月。
2. 编制依据2.2.1海南炼油项目继建工程相关管理文件及规定2.2.2《立式园筒形钢制焊接油罐施工及验收规范》(GBJ128-90)2.2.3《压力容器无损检测》(JB4730-94)2.2.4《钢结构工程施工及验收规范》(GB50205-95)2.2.5《工业管道施工及验收规范》(GB50235-97)2.2.6《现场设备、工艺管线焊接工程施工及验收规范》(GB50236-98)2.2.7《石油化工剧毒、可燃介质管道施工及验收规范》(SH3501-97)2.2.8《工业管道施工及验收规范》(GB50235-97)2.2.9《石油化工钢制通用阀门选用、检验及验收》(SH3064-94)2.2.10《石油化工给水排水管道施工及验收规范》(SH3533-95)2.2.11《石油化工企业设备管道表面色和标志》(SH3043-1999)2.2.12中国石化集团第十建设公司《质量手册》(QG/M44.0000-2001 符合GB/T19001-2000 idt ISO9001:2000)2.2.13中国石化集团第十建设公司《安全、环境与健康管理手册》QG/M4448.00-20002.2.14中国石化集团第十建设公司目前资源状况3. 安装主要工程实物量我公司承建的四台油罐主体安装部分包括油罐罐体及附件。
十万方大型储罐倒装施工方案

十万方大型储罐倒装施工方案在大型储罐倒装施工中,施工方案的合理性和可行性对整个工程的顺利进行至关重要。
本文将针对十万方大型储罐倒装施工提供详细的方案,确保施工过程安全、高效、顺利进行。
一、前期准备工作在施工前,首先需要对施工现场进行详细的勘察和测量,确保施工现场的平整度和承重能力满足倒装工艺的要求。
同时,需要对施工人员进行专业的培训和安全教育,确保他们能够熟练操作施工设备并严格遵守安全操作规程。
二、施工工艺流程1. 现场搭设支撑架首先需要在储罐底部搭设稳固的支撑架,以确保储罐倒装过程中能够保持稳定。
支撑架的选择和布置需要根据储罐的具体结构和重量进行合理设计。
2. 安装起重设备在支撑架搭设完毕后,需要安装起重设备,如起重机械或吊车等。
起重设备的选择需要考虑到储罐的重量和高度,确保能够顺利完成倒装操作。
3. 倒装施工倒装施工过程中,需要严格按照施工方案进行操作。
首先将储罐从基础上分离,并使用起重设备逐步将储罐倒装至预定的位置。
在倒装过程中需要分阶段进行,确保倒装过程平稳、有序。
4. 完工验收储罐倒装完成后,需要进行完工验收。
通过检查储罐的外观和内部结构,确保倒装施工没有造成储罐结构的破坏和泄漏等安全隐患。
同时还需要对施工现场进行清理,确保施工现场的整洁和安全。
三、施工安全措施在进行大型储罐倒装施工过程中,需要严格遵守安全操作规程,保障施工人员和设备的安全。
具体的安全措施包括但不限于: - 施工现场设置安全警示标识,确保施工人员能够清晰了解施工区域的危险区域和安全通道。
- 对施工人员进行岗前安全培训,明确施工操作规程和安全事项。
- 定期对施工设备进行检查和维护,确保设备运行正常。
- 在施工现场设置安全防护网和安全围栏,避免施工人员误入危险区域。
四、施工质量控制为保障施工的质量,需要在施工过程中进行严格的质量控制。
具体的质量控制包括但不限于以下几个方面: - 施工过程中设置监控点,定期对施工进行检查和验收。
10万立大型储罐施工工法
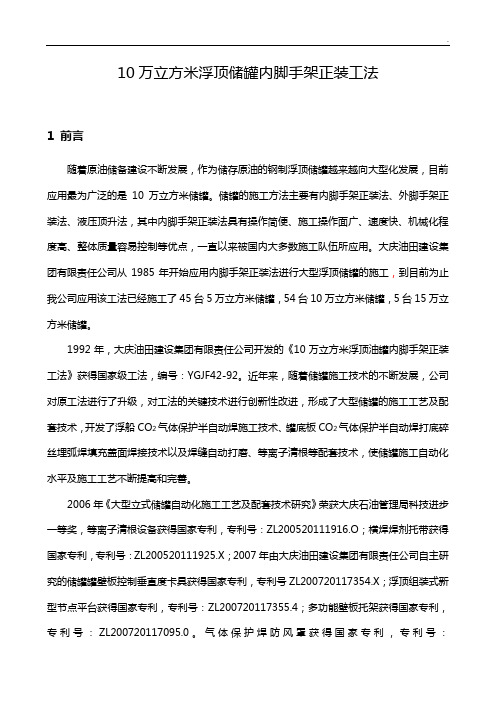
10万立方米浮顶储罐内脚手架正装工法1 前言随着原油储备建设不断发展,作为储存原油的钢制浮顶储罐越来越向大型化发展,目前应用最为广泛的是10万立方米储罐。
储罐的施工方法主要有内脚手架正装法、外脚手架正装法、液压顶升法,其中内脚手架正装法具有操作简便、施工操作面广、速度快、机械化程度高、整体质量容易控制等优点,一直以来被国内大多数施工队伍所应用。
大庆油田建设集团有限责任公司从1985年开始应用内脚手架正装法进行大型浮顶储罐的施工,到目前为止我公司应用该工法已经施工了45台5万立方米储罐,54台10万立方米储罐,5台15万立方米储罐。
1992年,大庆油田建设集团有限责任公司开发的《10万立方米浮顶油罐内脚手架正装工法》获得国家级工法,编号:YGJF42-92。
近年来,随着储罐施工技术的不断发展,公司对原工法进行了升级,对工法的关键技术进行创新性改进,形成了大型储罐的施工工艺及配套技术,开发了浮船CO2气体保护半自动焊施工技术、罐底板CO2气体保护半自动焊打底碎丝埋弧焊填充盖面焊接技术以及焊缝自动打磨、等离子清根等配套技术,使储罐施工自动化水平及施工工艺不断提高和完善。
2006年《大型立式储罐自动化施工工艺及配套技术研究》荣获大庆石油管理局科技进步一等奖,等离子清根设备获得国家专利,专利号:ZL200520111916.O;横焊焊剂托带获得国家专利,专利号:ZL200520111925.X;2007年由大庆油田建设集团有限责任公司自主研究的储罐罐壁板控制垂直度卡具获得国家专利,专利号ZL200720117354.X;浮顶组装式新型节点平台获得国家专利,专利号:ZL200720117355.4;多功能壁板托架获得国家专利,专利号:ZL200720117095.0。
气体保护焊防风罩获得国家专利,专利号:ZL200720117358.8。
2008年《10万立方米浮顶储罐施工配套技术研究》荣获中国石油和化学工业协会科技进步三等奖。
10万立罐基础施工方案

国家储备库工程镇海基地罐区施工方案1、工程概况1.1本工程为国家储备库工程镇海基地罐区T—01#~18#罐、T—23#~24#罐,共计20台10×104m3罐,位于镇海岚山水库南侧附近。
罐直径为80米(环梁中心线),钢筋混凝土板式基础,底板厚650,底板底标高3.25米,面标高3.90米,基础外侧为800宽钢筋混凝土异型环梁,总高1.60米。
环梁底标高2.70米,顶面标高4.30米,沿罐基直径设置十字型通长后浇带,宽1.0米,后浇带中的承台板筋相连接。
罐基内做法为内填中粗砂垫层最薄处300厚,沥青砂绝缘层100厚(按1.5%找坡)。
1.2本工程罐基主要工程量为钢筋390t,垫层砼为520m3,罐基础为3543m3,砂垫层为2470m3,沥青砂为507m3。
1.3本工程项目砼工程量大,工期短,单罐土建工程从打桩完交付我方施工开始至交付安装,仅70天时间(按罐基础和后浇带养护各7天考虑)。
2、施工部署2.1 5月15日前施工现场生产临设完毕,钢筋车间开始加工制作钢筋。
为便与钢筋二次搬运,减少时间及工作量,故钢筋车间在每个罐基础边就近布置,每台罐钢筋制作完成后随下台罐基础施工位置作相应移位。
详见施工平面布置图。
2.2为提高砼表面的平整度、光洁度,确保结构砼施工质量,达到清水砼要求,故模板采用竹胶板,同时预先拼装制作,现场安装。
2.3砼的浇筑采用炼化公司搅拌站,供应要求供应量不少于60m3/h而且要连续供应至浇筑完毕。
2.4劳动力组织根据工程工期紧的特点,确保各分项工程保质、保量、如期完成,故劳动力的安排从公司劳动人才公司抽调具有10万立罐基础施工经验各专业队伍。
劳动力计划见下表(暂按2台罐平行施工考虑)3、施工进度计划及保证措施3.1本工程实行项目法施工、项目经理全面负责本工程的一切职能。
3.2施工进度计划3.2.1本工程总体施工进度计划根据浙江伊麦克斯公司提供的桩基完成时间进行编制。
3.2.2每台罐土建施工作业时间控制在70天。
10万立大型储罐施工工法要点
10万立大型储罐施工工法要点随着现代工业的快速发展,大型储罐的需求也在日益增长。
10万立大型储罐作为一种重要的储存设备,广泛应用于石油、化工、燃气等领域。
本文将介绍10万立大型储罐的施工工法要点,包括施工前准备、罐体预制、基础施工、罐体安装、焊接与密封、压力试验以及安全措施等方面。
一、施工前准备在开始施工前,需要进行充分的准备工作。
要确定施工方案和工艺流程,明确施工目标和计划。
要进行现场勘查和清理,确保施工场地安全、平整、无障碍物。
同时,还要进行人员组织和技术交底,确保参与施工的人员了解施工方案和工艺要求。
二、罐体预制10万立大型储罐的罐体通常采用钢材焊接而成,因此需要在施工前进行预制。
在预制过程中,需要注意以下几点:1、钢材选择:根据设计要求选择符合规格和质量的钢材。
2、焊接工艺:采用合适的焊接工艺和焊接材料,确保焊接质量和安全性。
3、尺寸精度:在预制过程中要控制好尺寸精度,避免出现误差。
4、防腐处理:预制完成的罐体需要进行防腐处理,以提高使用寿命。
三、基础施工10万立大型储罐通常采用钢筋混凝土基础,基础深度和强度需根据储罐容量和使用要求进行设计。
在基础施工过程中,需要注意以下几点:1、基础设计:根据储罐容量和使用要求进行基础设计,包括基础深度、强度、稳定性等方面。
2、施工工艺:按照施工工艺要求进行基础施工,确保施工质量。
3、混凝土养护:混凝土浇筑完成后需要进行适当的养护,确保基础强度。
4、基础验收:完成施工后需要进行基础验收,确保基础质量和安全性。
四、罐体安装在完成基础施工后,可以进行罐体的安装。
在安装过程中,需要注意以下几点:1、吊装设备:选择合适的吊装设备,确保吊装过程的安全性和准确性。
2、安装定位:将罐体放置在基础上,调整好位置和高度,确保安装精度。
3、焊接固定:将罐体与基础进行焊接固定,确保储罐的稳定性和安全性。
4、无损检测:完成安装后需要进行无损检测,确保焊接质量和安全性。
五、焊接与密封焊接与密封是10万立大型储罐施工的关键环节之一。
10万立储罐倒装法施工技术总结
目录1.工程概况 (2)2.施工遵循的标准、规定和原则 (5)3.施工方案优化 (5)4.储罐施工主要设备、机具明细 (10)5.施工作业条件 (11)6. 10万立方米储罐建安施工程序及施工方法 (12)7. 10万立储罐施工劳动组织 (14)8.投入与发展 (17)9.施工中遇到的问题和处理方法 (18)10.新技术的应用 (18)11.总结 (19)第1页共20页1.工程概况1.1工程特点1.1.1建设地点范围xxx石化千万吨炼油及百万吨乙烯项目-50万立方米原油商业储备库工程位于克拉玛依市xxx区独石化公司化工新区西部。
我公司承建两台10万立方米双盘式浮顶罐T-001和 T-004的罐体制安工程。
罐区东西长度为250m,南北宽度为120m,占地面积为30000m2。
1.1.2建安工程量以下为单台储罐实物量汇总表:1.1.3施工工期项目开工时间:2007年6月21日项目竣工时间:2008年7月30日1.1.4工序流程及设备特点第2页共20页1.1.4.1施工程序流程第3页共20页1.1.4.2 10万立方米双盘式浮顶罐特点a. 10万立方米储罐,是我公司目前为止所承接的大型储罐制安工程当中,容量最大的大型储罐。
其内壁直径达80m,罐体总高22m;壁板厚度范围10〜32mm。
b.浮顶结构为双盘式浮顶,主要由底板、顶板、外边缘板、桁架和隔板组成。
浮顶底板与顶板组对形式为搭接。
浮顶密封由1、2次密封结构和刮蜡机构组成。
c.罐体材料复验繁杂。
罐壁板包括多种材质:Q235B、16MnR和12MnNiVR。
其中高强钢12MnNiVR 的各项性能要求较高,其化学成分、力学性等能都须进行严格的复验,且逐张进行超声波检验。
d.涉及高强钢的焊接(连续焊、定位焊),焊前必须进行预热,预热温度须达到125〜130℃;环境温度低于0℃ (含0℃),不允许高强钢的焊接。
e.无损检测量大。
10万立储罐对其安装质量要求十分严格,无损检测量非常大,如所有罐底焊缝底层焊道和成形后焊道表面分别做渗透和磁粉检验。
十万方大型储罐倒装施工方案
十万方大型储罐倒装施工方案一、施工背景二、施工准备1.确定施工场地,并对场地进行平整、清理,确保没有障碍物和杂物。
2.对施工现场进行测量,确定施工机械的位置和储罐倒装的具体要求。
3.调集所需的施工机械和设备,如起重机、吊车等。
4.安排人员到场施工,包括机械操作人员、安全员等。
三、施工步骤1.检查储罐的结构完整性和表面的光洁度,确保储罐没有任何损坏和污染。
2.准备好大型起重机,并将其稳定固定在施工现场。
3.将储罐放置在起重机下方,并使用吊车将储罐抬升至合适的高度。
4.将储罐倾斜至适当的角度,并进行固定。
5.检查储罐的安全固定,确保不会出现任何移动和倾斜的情况。
6.检查施工现场的安全措施,确保施工人员和机械的安全。
7.完成储罐倒装施工后,进行清理和整理现场,确保没有遗留杂物和施工垃圾。
四、安全措施1.施工现场要设置专门的警示标识,并采取必要的封闭措施,防止外来人员进入。
2.在施工现场设置专门的交通指示牌,指示人员和机械的行进方向,确保施工现场的交通畅通。
3.施工人员要佩戴个人防护用品,包括安全帽、防护服、防护手套等。
4.机械操作人员要经过专门培训,并具备相应的资格证书。
5.施工过程中,要定期检查机械设备的完好性和安全性能,确保其正常运行。
六、施工效果评估通过以上步骤的施工,储罐的倒装工作能够顺利进行,施工现场秩序井然,施工人员和机械的安全得到了保障。
七、总结十万方大型储罐倒装施工方案的制定和实施,为大型储罐倒装施工提供了具体的指导,保障了施工的顺利进行和人员、设备的安全。
但在具体施工过程中,仍需根据实际情况进行具体操作,并严格遵守相关的安全规范和操作规程。
10万立方油罐正装法施工方案
10万立方油罐正装法施工方案目录一、工程概况二、编制依据三、工程特点四、施工流程框图五、施工方案1、施工部署2、储罐施工:(1).施工准备;(2).材料检验(3).基础验收(4).储罐预制一般要求(5).罐壁板预制(6).罐顶板预制(7).构件预制3、储罐主体安装工艺措施(1).罐地板组装(2).罐壁组装(3).罐顶盖的组装(4).附件安装;(5).焊接施工(6).焊接顺序4、充水试验5、防腐工程6、绝热工程7、施工机械及机具六.安全管理与安全保障七;安全技术管理措施八.主要施工用手段用料10万立方油罐安装方案一、工程概况1.简述本工程为新增2台100000m3油罐,本工程在2009年月日开工,计划于2009年月日竣工,单台罐重量约为2100吨。
本施工方案针对承担两台罐施工的工况进行编制。
本次施工新建 2 台 100000立方汽油罐制作安装;油罐顶板及底板(除边缘板)均为搭接,罐底边缘板、罐壁立缝、环缝为对接。
其主体结构形式为立式油罐,该结构的主要特点是,焊接量大、焊接质量要求高、焊接变形控制要求严,因此要求施工人员严格按照施工方案、施工技术交底卡进行施工。
确保油罐优质、高效、按期完成。
二、编制依据1 设计施工图;2 合同、招标文件;3 GBJ128-90 《立式圆筒钢制焊接油罐施工及验收规范》;4 GB50235-97 《工业金属管道工程质量验收规范》;5 GB50236-98 《现场设备、工业管道焊接工程施工验收规范》;6 SH3501-1997 《石油化工剧毒、可燃介质管道施工及验收规范》;7 JB4730-94 《压力容器无损检测》;8 SH3046-923 《石油化工立式圆筒形钢制焊接储罐设计规范》;9 SH3048-1999 《石油化工钢制焊接储罐设备抗震设计规范》;10 Q/HD0026-1995 《立式圆筒钢制焊接储罐铠装式外防腐保温工程施工及验收规范》;11 GB4053.2-1993 《固定式钢斜梯》;12 GB8923-88 《涂装前钢材表面锈蚀等级和除锈等级》;13 SH3530-93 《石油化工立式圆筒形钢制储罐施工工艺标准》;14 公司质量管理手册及程序文件15罐体基本参数16工程施工总工期:2台10×104m3双盘浮顶油罐个月。
- 1、下载文档前请自行甄别文档内容的完整性,平台不提供额外的编辑、内容补充、找答案等附加服务。
- 2、"仅部分预览"的文档,不可在线预览部分如存在完整性等问题,可反馈申请退款(可完整预览的文档不适用该条件!)。
- 3、如文档侵犯您的权益,请联系客服反馈,我们会尽快为您处理(人工客服工作时间:9:00-18:30)。
10万立方米浮顶储罐脚手架正装工法1 前言随着原油储备建设不断发展,作为储存原油的钢制浮顶储罐越来越向大型化发展,目前应用最为广泛的是10万立方米储罐。
储罐的施工方法主要有脚手架正装法、外脚手架正装法、液压顶升法,其中脚手架正装法具有操作简便、施工操作面广、速度快、机械化程度高、整体质量容易控制等优点,一直以来被国大多数施工队伍所应用。
油田建设集团有限责任公司从1985年开始应用脚手架正装法进行大型浮顶储罐的施工,到目前为止我公司应用该工法已经施工了45台5万立方米储罐,54台10万立方米储罐,5台15万立方米储罐。
1992年,油田建设集团有限责任公司开发的《10万立方米浮顶油罐脚手架正装工法》获得国家级工法,编号:YGJF42-92。
近年来,随着储罐施工技术的不断发展,公司对原工法进行了升级,对工法的关键技术进行创新性改进,形成了大型储罐的施工工艺及配套技术,开发了浮船CO2气体保护半自动焊施工技术、罐底板CO2气体保护半自动焊打底碎丝埋弧焊填充盖面焊接技术以及焊缝自动打磨、等离子清根等配套技术,使储罐施工自动化水平及施工工艺不断提高和完善。
2006年《大型立式储罐自动化施工工艺及配套技术研究》荣获石油管理局科技进步一等奖,等离子清根设备获得国家专利,专利号:ZL6.O;横焊焊剂托带获得国家专利,专利号:ZL5.X;2007年由油田建设集团有限责任公司自主研究的储罐罐壁板控制垂直度卡具获得国家专利,专利号ZL4.X;浮顶组装式新型节点平台获得国家专利,专利号:ZL5.4;多功能壁板托架获得国家专利,专利号:ZL5.0。
气体保护焊防风罩获得国家专利,专利号:ZL8.8。
2008年《10万立方米浮顶储罐施工配套技术研究》荣获中国石油和化学工业协会科技进步三等奖。
2009年4月,工法的关键技术通过了中国石油和化学工业协会的科技鉴定,鉴定结论为:该技术创新成果拥有自主知识产权,达到国领先水平,应用前景广阔。
2 工法特点2.1 储罐的罐壁和浮顶可同时交叉施工,工效高。
2.2 罐壁板侧搭设三层临时脚手架及劳动保护,搭设简单、速度快,施工受自然条件限制小,不受水源、大风天气的影响。
2.3施工操作面广,可同时在三层脚手架上进行操作,实现工序间流水化作业,缩短施工周期;并且有充足的检查、返修时间,施工质量容易保证。
2.4壁板组对采用工卡具无活口、无点焊的精密组装技术,对壁板的垂直度、椭圆度、对缝间隙、水平度可进行精密调整,保证质量。
2.5采用自主研制的专用浮顶安装组合平台,平台的刚性和稳定性强,安装、拆卸简单,搭设速度快,不损伤母材,架台可重复利用,节约成本。
2.6罐底中幅板对接焊缝采用半自动CO2气体保护焊与碎丝埋弧焊组合焊接技术,焊接效率高,材料省、变形小,所研制的防风装置获得国家专利。
2.7自主研发的横向埋弧焊剂拖带,具有耐热、耐磨、耐疲劳、耐断裂、焊剂损耗少等优点。
2.8采用自主研制的的横焊缝等离子清根装置,替代了传统碳弧气刨,具有效率高、劳动强度小、材料省、质量稳定等优点。
2.9采用自主研制的的焊缝余高自动修平装置,替代了手工作业,具有加工质量好、工效高、安全可靠等优点。
3 适用围本工法适用于5万立方米到15万立方米浮顶储罐的施工。
4 工艺原理4.1预制罐板现场预制,坡口预制采用龙门式数控火焰切割机进行切割;壁板采用数控滚板机进行滚弧,预制完毕后放在弧形胎具上,在胎具上焊接三角架的挂件及组对卡具的固定件。
4.2安装罐底中幅板施工完毕后,在罐底板上安装浮顶临时架台,在架台上预制、安装浮顶,浮顶施工完毕后,拆除架台并从人孔运出。
罐底边缘板组焊完毕后,组焊底圈罐壁,在底圈罐壁侧挂三角架,通过三角架的支撑铺设跳板及劳动保护,施工人员站在侧脚手架上进行上圈壁板的操作,脚手架共搭设三层,随着壁板不断增高,将最下一层脚手架拆除倒运到上侧搭设,三层脚手架交替往复使用,直至安装完最后一圈壁板。
罐壁外侧的施工借助沿罐壁行走的移动小车进行。
4.2焊接罐底中幅板焊接采用CO2气体保护半自动焊打底、碎丝埋弧焊填充盖面;壁板纵缝焊接采用CO2保护气电立焊;环缝焊接采用自动埋弧横焊;焊缝侧清根使用等离子清根设备;横焊缝侧磨平使用自动修平机。
55.15.2基础验收图5.1 储罐施工工艺流程储罐基础检查验收按GB50128-2005《立式圆筒形钢制焊接储罐施工及验收规》第4章第2节中相关条款要求进行。
1、基础中心标高允许偏差为土20mm 。
2、支承罐壁的基础表面其高差应符合下列规定:有环梁时,每10m 弧长任意两点的高差不应大于6mm ,且整个圆周长度任意两点的高差不应大于12 mm 。
碎石环粱和无环粱时,每3m 弧长任意两点的高差不应大于6mm ,且整个圆周长度任意两点的高差不应大20mm 。
3、沥青砂层表面应平整密实,无凸出的隆起、凹陷及贯穿裂纹。
5.3罐体预制 5.3.1底板、壁板预制1、预制前对屈服强度大于390MPa 的高强度钢板材进行100%超声波检测,合格后进行预制。
2、底板、壁板各边的切割采用数控龙门式自动火焰切割机进行切割(见图5.3.1-1),切割时先进行长边的切割,再进行短边的切割;两长边要同时进行切割以减少变形量。
3、由于纵焊缝收缩,在壁板下料时应提前预留收缩余量,纵焊缝横向收缩总量按下式进行计算:△L=0.27FN/δ (式5.3.1)式中 △L-整圈焊缝的收缩总量mmF-纵焊缝的横截面积mm 2 N-一圈纵焊缝的数量 δ-钢板厚度mm4、边缘板的侧减薄过渡坡口用刨边机进行预制,其余部位用火焰切割机进行切割预制,下料尺寸按边缘板放大后的外径计算尺寸进行预制。
5、壁板弧度加工在滚板机上进行(见图5.3.1-2),其中25mm 以上的厚壁板应滚制9~11遍以充分释放板应力;弧度检查要将板竖起并在无约束的情况下进行。
图5.3.1-1 数控龙门式自动火焰切割机图5.3.1-2 滚扳机滚弧6、第一圈壁板开孔热处理在加工厂进行开孔预制、热处理,热处理温度应符合设计要求。
7、预制好的壁板放在半径与储罐半径相同的弧形胎具上,防止变形。
5.3.2加强圈、抗风圈预制1、加强圈、抗风圈的预制在钢板上搭设的2.5米×12米的平台上进行。
2、切割单块板的侧及两端的坡口。
3、加强圈、抗风圈下料时侧半径应放大2~3mm以预留收缩余量。
4、加强圈、抗风圈每3块组焊在一起,组焊时腹板上的加强型钢统一组焊,并安装吊环便于吊装。
5.3.3浮顶预制1、浮顶预制在临时搭设的架台上进行。
2、浮舱的环板、隔板、桁架在钢板搭设的平台上进行预制,最外侧环舱的隔板、桁架预制时预留适当的收缩余量。
3、浮顶支柱预制时,按其设计高度预留出调整量,充水试验后放水时进行逐根调整。
4、浮舱边缘板预制要对照一、二次密封图纸,提前钻好密封材料使用的固定孔。
5.3.4盘梯预制用0.75mm厚镀锌铁皮放出踏步间外侧板的间隔样板,在外侧板上画线后,组装踏步与外侧板;整个盘梯预制成两段。
5.3.5转动浮梯预制首先在浮顶上安装好浮梯轨道,然后组焊浮梯;浮梯轨道组焊时两个轨道间隔应适当放大。
5.3.6量油管、导向管预制量油管、导向管的预制在浮顶上进行,将钢管沿其轴向接成整根,严格控制其垂直度,并提前钻好取样孔。
5.3.7中央排水管的预制在预制平台上组装好排水管,然后进行压力试验和动态气密性试验,解体后从人孔或搅拌器孔移进罐进行安装。
5.4边缘板铺设与焊接5.4.1画线画出边缘板的外边缘线,外边缘半径应按式5.4.1进行放大:R C=(R+3N/2π)×1/COSarctgA (5.4.1)式中R C:实际放线半径R:图纸设计半径N:边缘板数量A:基础坡度比值5.4.2铺设组对1、铺设前将边缘板的垫板与边缘板点焊固定。
2、用吊车直接铺板,调整对口间隙并点焊固定,点焊长度不小于80mm。
为控制焊接引起的变形,在整条对接焊缝上安装两个反变形卡具(见图5.4.2)。
5.4.3边缘板外侧300mm对接焊缝焊接1、底层边缘板与垫板的结合角处用氩弧焊进行封底焊接。
2、用手工电弧焊进行焊接(见图5.4.3)。
3、焊接时多名焊工沿整个圆周均布,同时焊接。
4、初层焊道进行渗透检测,填充完毕后对外侧300mm打磨平滑后进行磁粉检测和X 射线无损检测,射线检测时间为焊后24小时。
5.5中幅板铺设与焊接5.5.1中幅板铺设、组对1、在罐基础顶面画出垫板铺设线。
2、铺好罐底板垫板,并设置伸缩缝,伸缩缝上下分别插入垫板。
3、用吊车由中心板带向两侧铺设,先铺条形板,后铺带形板。
4、边铺设、边调整对口间隙,将底板与垫板单侧点焊固定。
图5.4.3 边缘板外侧300mm对接焊缝焊接图5.4.2 边缘板卡具安装图5、铺设完毕后,对先焊的焊缝进行调整,调整好间隙后,用连接板进行固定。
6、为防止焊接时引起钢板端部凸起,在T型焊缝处用方销将端部焊缝向上楔起6~8mm(见图5.5.1)。
7、中幅板与边缘板连接处焊接前,中幅板宜搭接在边缘板上至少100mm,且中幅板边缘处于自由状态;待边缘板焊缝和中幅板焊缝焊完后,再切割中幅板的预留量,然后进行组对焊接。
5.5.2中幅板的焊接1、中幅板采用CO2气体自动保护焊封底,碎焊丝填充、自动埋弧焊盖面,其焊接参数见表5.5.2。
中幅板焊接参数表5.5.2焊接部位焊接层次焊接方法填充材料焊接电流(A)焊接电压(V)焊接速度(cm/min)中幅板打底GMAW ER50-6 Φ1.2 245~275 28~34 30~50 填充SAW碎丝H08A 1.0×1.0盖面US-36 Φ3.2 540~580 32~36 25~402、CO2气体自动保护封底焊(见图5.5.2-1)采用分段退焊,焊高5mm。
3、填充碎焊丝自动埋弧焊(见图5.5.2-2),在焊接通长缝时,应采取防变形措施(见图5.5.2-3)。
图5.5.1中幅板反变形图图5.5.2-3 中幅板通长焊缝反变形图4、中幅板焊接顺序见图5.5.2-4。
图5.5.2-4 中幅板焊接顺序图5、中幅板T型焊缝三侧200mm根部采用CO2气体自动保护封底焊,焊后打磨进行渗透检测,采用手工电弧焊填充、盖面。
6、距边缘板1m围焊缝暂留不焊接,在与边缘板组对合格后再焊接。
5.6底圈壁板的组焊5.6.1画线按式5.3.1计算出的周长数据,计算出壁板安装线的放大数值,进行画线并安装挡板,如图5.6.1所示。
5.6.2卡具安装壁板组立前,预先安装好各种组装固定卡具,如图5.6.2所示。
5.6.3调节用吊车将壁板吊装就位,用方销调整并卡紧,安装立缝组对卡具及壁板控制垂直度卡具支撑(见图5.6.3);调节立缝对口间隙、错边量、弧度、垂直度及上口水平度,使之符合图纸及标准规要求。
5.6.4立缝焊接1、焊好立缝的固定龙门板及引弧板。