轧钢技术发展前景
从MPM到PQF---限动芯棒连轧管机回顾及展望

从MPM到PQF---限动芯棒连轧管机回顾及展望作者:李群丁德元来源:河北钢管网0 前言限动芯棒连轧管机是在在浮动芯棒连轧管机的基础上发展起来的。
限动芯棒连轧管机于20世纪60年代中期进行了工艺试验并获得了可喜的成果。
1978年世界上第一套限动芯棒连轧管机(MPM:Multi-Stand Pipe Mill的缩写)在意大利达尔明钢管厂建成投产,将连轧管工艺发展到了一个新的水准;限动芯棒连轧管机在整个轧制过程中对芯棒的运行加以控制,使其以设定的恒定速度前进,轧制过程结束时,由脱管机将荒管与芯棒分离后,荒管被移送到下道工序进一步加工;芯棒则返回,拨出轧制线后,冷却、润滑后循环使用。
MPM使得钢管壁厚偏差得到改善,工具、能耗有所降低,将连轧管机轧制钢管的最大外径由194mm扩大到426mm。
20世纪90年代中期又推出了三辊连轧管机(PQF:Premium Quality Finishing的缩写)技术,2003年世界上第一套三辊限动芯棒连轧管机组(PQF)在中国天津钢管公司建成投产,使连轧管工艺装备跃上了更高的台阶。
经过近30年的发展和应用,世界上目前正在运行和在建的限动芯棒连轧管机超过了20台套。
连轧管机在PQF出现以前,都是两辊式的,即由两个轧辊为一组组成孔型, 两个轧辊相互平行,相邻两个孔型的辊缝相错90°;PQF为三辊式的,即由三个轧辊为一组构成孔型,三个轧辊互成120°,相邻两个孔型的辊缝相错60°;使上一架孔型的槽底对应下一架孔型的槽顶。
图1 连轧管孔型构成本文拟对近30年来限动芯棒连轧管机的发展情况进行一下回顾并展望其前景。
1 1978~1992年,MPM的推广期MPM一经问世,因其在技术、产量、质量、自动化和劳动生产率等诸方面的突出优势,引起了无缝钢管界的广泛关注并得到认同和推崇,目前已使其在除大洋州以外的五大洲得以迅速的推广应用;特别是1978年到1992年间的前15年,受当时石油产业对油井管需求旺盛的影响,促使了MPM技术的飞速发展,相继建成投产了10套限动芯棒连轧管机组,从第二套到第十套仅用了10年的时间。
轧钢专业实习报告3000字

轧钢专业实习报告3000字通过这次专业实习,我对自动化在工业生产中的使用,工艺流程,工作对象,特殊的工程环境,自动化设备等一些自动化专业相关知识有了一个全新的理解和更深的理解,巩固了专业知识的同时,也使我对生产实际有了进一步的认知,增强了我的行业责任感。
在实习的这段日子里,也增进了同学间的友谊,锻炼了大家的团队精神。
现在我将专业实习期间的一些专业理解,所见所闻和一些个人感想分为长钢篇,长虹篇和结语篇三个大的部分总结如下:第一部分长钢篇一长城特种钢材公司概况长城特种钢材公司成立于1965年,当时的国务院副总理李富春为长钢的成立和选址江油市做了很大努力。
在当时的历史条件下,长钢作为西部重要的军工企业,她只有一个代号302,下有四个分厂,代号分别为302-1,302-2,302-3,302-4。
他们分别由上海钢铁五厂,异型钢厂,抚顺钢厂,大冶钢厂的部分设备和员工组建而成,但是,长钢的员工还是绝大部分以转业军人为主。
长钢作为国家布局在西部的重要钢铁军工企业,为当时的国防建设,工业建设作出了卓越的贡献。
改革开放后,长钢由军工企业改为军民两用企业,随着市场经济的冲击,长钢也同其他大型国有企业一样,面临着很多急待解决的问题。
长钢也所以出现过无法正常运营,职工发不起工资等等一些现象。
但是,作为从建国初期走过来的军工大企业便没有就此倒下,坚强的长钢人也没有被重重的困难吓倒,他们而是更加努力,持续开拓创新,为长钢规划新的发展方向,制定新的发展思路。
在党和国家的关怀指导下,二十一世纪初叶,攀钢集团对长钢实行经营性托管,便成功的实行了股份制改革,成立了攀长钢公司。
后不久,攀长钢长城股份在深圳股份交易所上市。
这标志着长钢公司已经从艰难险阻中走出来了,开始迈向新的未来。
当前,长钢公司有四个生产区。
下有特冶中心,核电钢管厂,大型钢材厂,中小型钢材厂,扁平材厂等分厂组成。
长钢现在能够生产碳结、喝结、碳工、合工、弹簧、文秘114网轴承、模具等棒管板、丝、带、锻件等优质钢种。
世界特殊钢棒线材轧机建设近况和前景

世界特殊钢棒线材轧机建设近况和前景王定武Current Situation and Development of Bar and Rod Millsfor Special Steel in WorldWang Dingwu(Beijing Central Iron and Steel Design Institute, Beijing 100053) Current Situation and Development of Bar and Rod Millsfor Special Steel in WorldWang Dingwu(Beijing Central Iron and Steel Design Institute, Beijing 100053)近年来世界各主要产钢国家均新建了一批特殊钢棒线材轧机,并对原有轧机进行全面技术改造。
据统计,1985年以来约新建41台特殊钢棒线材轧机(含单独设立的特殊钢棒材轧机和特殊钢线材轧机),见表1。
表1 1985年以来世界新建部分特殊钢棒线材轧机Table 1 Some special steel bar and rod mills built since 19851 新建特殊钢棒线材轧机的技术特点(1) 冶炼炉配备有多种型式的二次精炼设备以提供优质钢水;日本等国则发展用转炉炼特殊钢。
连铸采用电磁搅拌和保护浇注。
有若干日本钢厂,采用连铸大方坯经开坯后供特殊钢棒线材轧机,最近亦有改用中断面、经大压下量轧机一火成材的趋势,如新日铁室兰厂将原用350 mm×560 mm大连铸坯经初轧开成小方坯供棒线材轧机,改为用220mm×220 mm连铸坯经2道次水平/立式大压下量轧机轧制后径送棒线材连续轧制线的新工艺,另根据特殊钢种配备有锻造开坯、连铸小方坯多种型式设备;有些钢种还需将方坯剥皮后再送轧钢机轧制。
(2) 灵活的、可精密控制的加热设备[1],按不同钢种均匀加热钢坯至需要温度,并保证钢坯表面质量,减少表面氧化、脱碳和擦伤。
冶金专用设备制造行业市场现状分析

冶金专用设备制造行业市场现状分析在现代工业体系中,冶金行业始终占据着举足轻重的地位,而冶金专用设备制造行业则是为冶金生产提供关键技术装备的重要支撑。
随着全球经济的发展和工业技术的不断进步,冶金专用设备制造行业也在经历着深刻的变革和调整。
从市场规模来看,近年来冶金专用设备制造行业总体呈现出稳步增长的态势。
这主要得益于全球钢铁产量的持续上升以及冶金工艺的不断改进和优化。
尤其是在一些新兴经济体,如亚洲的部分国家和地区,基础设施建设和制造业的快速发展对钢铁的需求旺盛,从而带动了冶金设备市场的扩张。
在市场需求方面,高质量、高效率、节能环保的冶金设备成为市场的主流需求。
随着环保要求的日益严格,冶金企业对能够降低能耗、减少污染物排放的设备青睐有加。
例如,新型的节能型电炉、高效的余热回收装置等设备市场需求不断增加。
同时,为了提高生产效率和产品质量,智能化、自动化的冶金设备也备受关注,如具备自动控制和监测功能的轧钢设备、智能化的熔炼设备等。
然而,冶金专用设备制造行业也面临着一些挑战。
首先,市场竞争激烈。
国内外众多企业纷纷涉足这一领域,导致市场竞争白热化。
一些中小企业在技术研发、品牌影响力和资金实力等方面处于劣势,生存压力较大。
其次,技术创新难度大。
冶金设备制造涉及多个学科和技术领域,要实现重大技术突破需要大量的研发投入和长期的积累。
而且,高端设备的核心技术仍掌握在少数发达国家的企业手中,我国企业在技术追赶上面临一定困难。
再者,原材料价格波动和劳动力成本上升也给企业带来了较大的成本压力。
从技术发展趋势来看,数字化、智能化、绿色化是冶金专用设备制造行业的主要发展方向。
数字化技术的应用使得设备的设计、制造和运维更加精确和高效。
通过建立数字化模型,可以在设备研发阶段就对其性能进行模拟和优化,减少实际生产中的调试时间和成本。
智能化则体现在设备能够自主感知、分析和决策,实现自动化生产和远程监控。
绿色化不仅体现在设备自身的节能和环保性能上,还包括整个生命周期中的可持续性,如易于回收和再利用等。
基于新型轧辊技术的轧钢生产发展前景
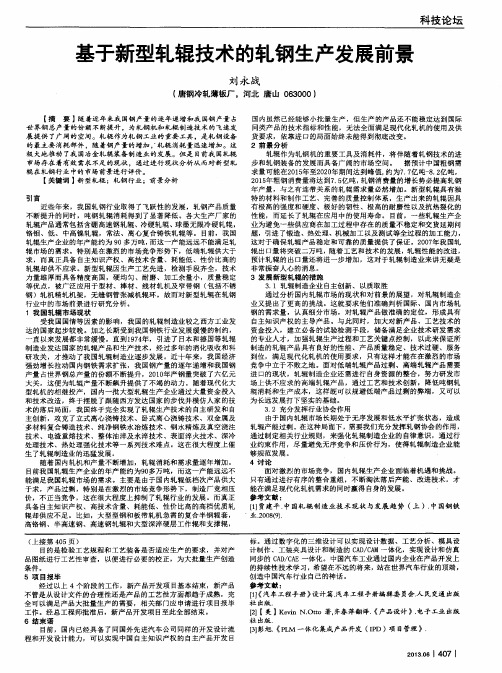
【 关键词 】 新型轧辊 ;轧钢行 业;前景分析
引 言
近些年来 ,我 国轧钢 行业取得了飞跃性的发展 ,轧钢产 品质量 不断提升的 同时 ,吨钢轧辊 消耗得 到了显著降低 各大生产厂家 的 轧辊产品通常包括含硼高速钢轧辊 、 冷硬轧辊、 球墨无 限冷硬轧辊 , 铬钼、低、 中高镍轧辊 ,常法、离心复合铸铁轧辊等 。目前 ,我 国 轧辊生产企业的年产能约为 9 0多万吨 , 而这一产能远远不能满足轧 辊市场 的需求 。特别是在激烈 的市场竞 争形势下,低端轧辊供大于 求,而真正具备 自主知识产权 、高技术 含量、耗能低、性价 比高的 轧辊却供不应求 新型轧辊 因生产 工艺先进 ,检测手段齐全 ,技术 力量雄厚而具备精度高 国,硬均匀 、耐 磨、加工余量小,质量稳定 等优 点 ,被广泛应用于型材 、棒材 、线 材轧机及 窄带钢 ( 包括不锈 钢 )轧 机精 轧 机 架 , 无 缝 钢 管 张 减 机 辊 环 。故 而 对 新 型 轧 辊 在 轧钢 行业 中的市场 前景进 行研 究分析。 1我国轧辊市场现状 受我国国情等因素的影 响,我 国的轧辊制造 业较之西方工业发 达 的国家起 步较晚。加之长期受到我 国钢铁行业 发展 缓慢的制约, 直 以来发展 都非常缓慢。直到1 9 7 4 年 ,引进 了日本和 德国等轧辊 制造业发达 国家 的轧辊产 品和生产技术 ,经过多年 的消化 吸收和科 研攻关 ,才推动 了我 国轧辊制造业逐步发展 。近十年来 ,我 国经济 强 劲 增 长 拉 动 国 内钢 铁 需 求 扩 张 , 我 国 钢 产 量 的逐 年 递 增 和 我 国钢 产量 占世界钢 总产量 的份 额不断提升 ,2 0 1 0 年产钢量 突破 了六 亿元 大关 ,这便 为轧辊产 量不断飙升提供了不竭 的动力 。随着现代 化大 型轧机 的相继投产 ,国内一批 大型轧辊生产企业通过大量资金投入 和技术改造 ,终于摆脱 了跟 随西方发达国家的步伐并模仿人家 的技 术的落后局面 ,我 国终于 完全 实现 了轧辊生产技术的 自主研发和 自 主创新 ,攻克 了立式 离心浇铸 技术、卧式离心浇铸技术 、双金属及 多材料复合铸造技术 、纯 净钢铁 水冶炼技术、钢水精炼及真空浇注 技术、 电渣重熔技术 、整 体油淬及 水淬技术、表面淬火技术 、深冷 处理技术、热处理强化技术等一系 列技 术难 点。这在很大程度上催 生了轧辊制造业的迅猛发展 。 随 着 国 内轧 机 和 产 量 不 断增 加 , 轧 辊 消 耗 和 需 求 量 逐 年 增 加 。 目前我 国轧辊生产企业 的年产 能约 为9 O 多万吨,而这一产能远远不 能 满 足 我 国 轧 辊 市 场 的需 求 。主 要 是 由 于 国 内 轧 辊 低 档 次 产 品 供 大 于求,产品过剩 ,特别是在激烈 的市场 竞争形势下,制造厂竞相压 价,不正当竞争 ,这在很大程度上抑制 了轧辊行业 的发展。而真正 具备 自主知识产权、高技术含量 、耗能低 、性价 比高的高档优质轧 辊却供 应不足 。比如 ,大型型钢和板带轧机 急需的复合半钢 辊套, 高铬钢 、半高速钢、高速钢轧辊和大型深淬硬层 工作 辊和支撑辊,
我国钢铁行业发展瓶颈及对策

◎ 文/ 丘 B 琼
我 国钢铁行 业经过 多年大规模 扩张 ,在 生产能 力、
消 费规模 等方面处于世界领 先水平 ,但 仍面临生产布局
运输 、仓储等物流环 节缺 乏有效衔接 ,导致钢铁流通效
率低 下。钢材 贸易商 在定价权 、渠道 资源等方面与钢铁 生产 企业相 比明显 处于弱势 ,我 国钢铁行 业这种 “ 大生 产 、小流通 ”的格局严重阻碍 了整个钢铁行业 的发展 。 2 . 高产能、次品质 ( 1) 经 过 多年 大规模扩 张 ,继 2 0 0 5 年从钢 铁净进 口国转变为净 出 口国后 ,国家钢铁产业政 策 由总量扩张 逐渐 向结构调整转 变。2 0 0 4 — 2 0 0 7 年钢铁行业平均产能
吨和9 . 5 2 亿吨 ,产 能利用率7 7 %左右 2 0 1 3 年计划 新增 高炉3 2 座 ,涉及产能3 7 0 0 万吨 ,产能利用率 或将下 降到
7 2 %左 右 。
界 总量4 6 . 但平 均规模 不 足1 O 0 万吨 ,钢 铁行业 集 中度 低 ,千万吨 以上 企业钢铁 产 量 占全 国总产量 的5 7 . 2 % ,与 国际水 平有较大差距 。
相 对应 的是 ,钢 铁流通企业 小而分散 ,流 通集 中度低 , 厂商地 位不平等 ,抗风 险能力弱 ,仓储 、代理 、加工 、
配 送 等 增 值 服 务 建 设 不 够 ,加 上 行 业 区 域 布 局 形 成 的
波 动更 为剧 烈 ,总体 呈现 持续上 涨态 势 ,尤其 白2 0 0 3
5 0 k g c e / t( 千克标准煤/ 吨 )。由于我 国铁钢 比高 ,吨钢
综合能耗 比国际先进水平高约1 1 0 k g c e / t 一 2 0 7 k g c e / t 。 ( 3) 能耗 指标低 。我 国大量钢 铁企业 能耗 指标低 于国 家规定 的能耗标准 ,大部 分 中小企业能耗指标低 于 世界 先进水平 1 5 %一 3 0 %。虽然 重点大 中型企业 中能耗
新一代钢铁材料的研究开发现状和发展趋势

高钢材在各个环境的使用效率,研究人员 在钢材的使用性能上做出研究,为找到新 的突破点,研究人员在研究过程当中加入 了微合金元素Ti,该种元素的使用使钢材 在生产过程当中形成阻碍的HZA成分减少, 为钢铁增加了一份在使用环境中的保障。 研究人员通过对稳定Ti元素,解决了钢材 在焊接方面的问题.从而提高了钢材的使 用性能。在材料的强度对比上,钢材的强 度比有色金属的强度更大将钢材的这一优 势结合有色金属的性能,进而研发出双重 性能的新型钢材,便能让钢材在未来市场 竞争中更加强大。
关键词:钢铁材料;新一代钢铁材料;高性能
钢铁材料是人类社会的基础材料,是 社会文踢的标志,新一代钢铁材料的研发 为今年大幅度提升钢材性能拉开了序幕。 新一代钢铁材料大幅度提高了钢铁材料的 使用寿命和使用性能,
全球科技水平不断提高。这是一个长期 进行的任务。它需要和21世纪的;台炼、轧制 技术进步相适应,要协调于我国资源、能源 条件和社会发展的需求。因此本文将对新一 代钢铁材料的发展现状和发展趋势进行讲述。
2.2我国对手新一代钢铁材料的研究 我国在1998年启动了“新一代钢铁 材料重大基础研究”的“973项目”,在5 年内我国国家财政累计投入了25亿万元作 为该项目的研究资金。采用新钢种取代碳 素钢、低合金钢与合金结构,中50%的传 统钢材,方可减少1500万吨钢,直接效益 就可以达到450亿元.而间接效益更加显 著.同时也达到了该项目的目的。我国在 进行该项目中提出了均质化、纯净化、细 晶化的学术思想(建议改为技术路线),先 后在400、800、1500MPa级超级钢的研 究方面取得重大进展,并领先世界进行了工 业化生产和应用.引起了国际上的重视。材 料细晶化是我国“973项目”的重点,该研 究通过对精钢的细化实现了钢铁材料的延 展性增加的目的,在该研发中我国已取得 了很大的突破。不仅如此,“973项目”还 计划成功地开发出了超级钢原型钢.并且 迅速推广了超级钢的工作进展,在2003年 超额实现万吨级的目标后,2004年超级钢 产量超过了30万吨。百万砘超级钢的目标 将很快得以实现。在超级钢的基础上,我 国还参与研究了钢铁材料的复相化。为提
智能轧钢职业规划书范文

一、前言随着我国钢铁工业的快速发展,智能轧钢技术作为钢铁工业的重要组成部分,其重要性日益凸显。
作为一名热爱钢铁行业、对智能轧钢技术充满热情的从业者,我深知职业规划对于个人发展的重要性。
为了更好地实现自我价值,现将我的智能轧钢职业规划如下:二、自我分析1. 个性特点我性格开朗、积极向上,具有较强的学习能力和适应能力。
在团队合作中,我善于沟通、协调,能够迅速融入集体,为团队目标努力奋斗。
2. 专业技能我毕业于某知名大学材料科学与工程专业,主修钢铁材料方向,对钢铁生产工艺、轧钢技术等领域有较深入的了解。
在大学期间,我积极参与科研项目,熟练掌握了CAD、仿真模拟等软件,具备一定的实践操作能力。
3. 优势与劣势优势:(1)扎实的专业基础,对钢铁生产工艺、轧钢技术等领域有深入了解;(2)良好的学习能力和适应能力,能够快速掌握新技术、新知识;(3)较强的团队合作精神和沟通能力,能够与同事、上级有效沟通。
劣势:(1)实践经验相对不足,需要在实际工作中不断积累;(2)在处理复杂问题时,有时会显得过于谨慎。
三、职业分析1. 行业背景随着我国钢铁工业的快速发展,智能轧钢技术逐渐成为行业发展趋势。
智能轧钢技术能够提高生产效率、降低能耗、提高产品质量,是钢铁工业转型升级的重要方向。
2. 职业发展前景随着智能轧钢技术的不断推广,相关人才需求日益旺盛。
从事智能轧钢行业的人员,将有机会在技术创新、项目管理、市场营销等方面发挥重要作用。
3. 职业路径(1)初入职场:从事智能轧钢相关技术岗位,如轧钢工艺工程师、设备维护工程师等;(2)中期发展:担任技术主管或项目经理,负责智能轧钢项目的实施与推进;(3)长期发展:成为行业专家,参与智能轧钢技术的研究与开发,为钢铁工业的可持续发展贡献力量。
四、职业规划1. 短期规划(1-3年)(1)在现有岗位上,努力提高自己的专业技能和综合素质,熟悉智能轧钢生产工艺和设备;(2)积极参与公司组织的培训和学习活动,拓宽知识面,提升个人能力;(3)在工作中,主动承担责任,积极与同事、上级沟通交流,争取更多的发展机会。
- 1、下载文档前请自行甄别文档内容的完整性,平台不提供额外的编辑、内容补充、找答案等附加服务。
- 2、"仅部分预览"的文档,不可在线预览部分如存在完整性等问题,可反馈申请退款(可完整预览的文档不适用该条件!)。
- 3、如文档侵犯您的权益,请联系客服反馈,我们会尽快为您处理(人工客服工作时间:9:00-18:30)。
轧钢技术发展前景世界轧钢工业的技术进步主要集中在生产工艺流程的缩短和简化上, 最终形成轧材性能高品质化、品种规格多样化、控制管理计算机化等。
展望未来, 轧钢工艺和技术的发展主要体现在以下几方面:1.铸轧一体化利用轧辊进行钢材生产, 因其过程连续、高效、可控且便于计算机等高新技术的应用, 在今后相当一段时间内, 以辊轧为特征的连续轧钢技术仍将是钢铁工业钢材成型的主流技术, 但轧钢前后工序的衔接技术必将有长足的进步。
在2O世纪, 由于连铸的发展, 已经逐步淘汰初轧工序。
而连铸技术生产的薄带钢直接进行冷轧, 又使连铸与热轧工序合二为一。
铸轧的一体化, 将使轧制工艺流程更加紧凑。
同时, 低能耗、低成本的铸轧一体化, 也是棒、线、型材生产发展的方向。
2.轧制过程清洁化在热轧过程中, 钢的氧化不仅消耗钢材与能源, 同时也带来环境的污染, 并给深加工带来困难。
因此, 低氧化燃烧技术和低成本氢的应用都成为无氧化加热钢坯的基本技术。
酸洗除鳞是冷轧生产中最大的污染源, 新开发的无酸清洁型(AFC) 除鳞技术, 可使带钢表面全无氧化物、光滑, 并具有金属光泽。
无氧化(或低氧化)和无酸除鳞(氧化铁皮)这两项被称为绿色工艺的新技术, 将使轧钢过程清洁化。
3.轧制过程柔性化板带热连轧生产中压力调宽技术和板形控制技术的应用, 实现了板宽的自由规程轧制。
棒、线材生产的粗、中轧平辊轧辊技术的应用, 实现了部分规格产品的自由轧制。
冷弯和焊管机也可实现自由规格生产。
这些新技术使轧制过程柔性化。
4.高新技术的应用20 世纪轧钢技术取得重大进步的主要特征是信息技术的应用。
板形自动控制, 自由规程轧制, 高精度、多参数在线综合测试等高新技术的应用使轧钢生产达到全新水平。
轧机的控制已开始由计算机模型控制转向人工智能控制, 并随着信息技术的发展, 将实现生产过程的最优化, 使库存率降低, 资金周转加快, 最终降低成本。
5.钢材的延伸加工在轧钢生产过程中, 除应不断挖掘钢材的性能潜力外, 还要不断扩大多种钢材的延伸加工产业, 如开发自润滑钢板用于各种冲压件生产, 减少冲压厂润滑油污染; 开发建筑带肋钢筋焊网等, 把钢材材料生产、服务延伸到各个钢材使用部门。
随着工业的发展和轧钢技术的进步, 轧钢工艺的装备水平和自动控制水平不断提高, 老式轧机也不断被各种新型轧机所取代。
按照我国走新型工业化道路的要求, 轧钢技术发展的重点也转移到可持续发展上, 在保证满足环保要求的条件下, 达到钢材生产的高质量和低成本。
在20世纪末,世界轧钢技术发展迅速。
轧钢生产在自动化、高精度化、连续化方面取得了较大进步。
轧钢生产是将钢锭或钢坯轧制成钢材的重要生产环节和主要方法。
因为用轧制方法生产出的钢材,具有生产率高、生产过程连续性强、品种多、易于实现机械化、自动化等优点,而且比锻造、挤压、拉拔等生产产品,性能更高,成本更低。
目前,约有93%的钢都是经过轧制成材的。
有色金属生产也大量应用轧制方法。
轧钢生产的主要产品为建筑、造船、汽车、石油、化工、国防、矿山等专用钢材。
目前,我国轧钢生产的钢材品种主要有薄钢板、硅钢片、钢带、无缝钢管、焊接钢管、铁道用钢、普通大型材、普通中型材、普通小型材、优质型材、冷弯型钢、线材、特厚钢板、中厚钢板等。
轧钢生产的产品按钢材断面形状分为:钢板、钢管和型钢。
型钢是一种应用范围广泛的钢材。
我国型钢产量占钢材总产量的25%~30%。
型钢按用途分为:普通型钢和专用型钢。
从断面形状又可分为异型断面型钢和简单断面型钢。
从生产方式的角度又可分为焊接型钢、弯曲型钢和轧制型钢。
板带材也是一种广泛应用的钢材,我国的板带材产量占钢材总产量的45%~55%。
板带钢按应用领域分为建筑板、桥板、船板、汽车板、电工钢板、机械用板等。
按照轧制温度的不同又可以分为热轧板带和冷轧板带。
钢板按厚度分为:中厚板、薄板和箔材。
钢管的用途主要有建筑用管和石油管道等。
我国钢管产量占钢材总产量的10%~15%,钢管的规格一般用外形尺寸及壁厚标称。
其断面一般为圆形管,也有多种异型钢管和变断面钢管。
钢管从制造角度划分为无缝钢管、螺旋钢管与直缝钢管、冷轧钢管等。
按断面形状划分为圆形管、异型钢管和变断面钢管。
这些品种齐全、样式繁多的钢管被应用在管道、石油运输,锅炉侧壁、地质钻探、轴承及注射针管等方面。
随着轧钢工艺及轧钢技术的不断发展,钢材的生产范围将不断扩大,产品品种也将不断增多。
近年来我国许多有价值的钢板产量大幅度增长,冷轧硅钢片2003年已达89.6万吨,镀锡板2002年已经达到110万吨,管线钢、石油管、耐火钢板、冷轧不锈钢板产量达55万吨。
轧机的发展史据说在14 世纪欧洲就有轧机﹐但有记载的是1480 年意大利人达' 芬奇(Leonardo da Vinci) 设计出轧机的草图。
1553 年法国人布律列尔(Brulier) 轧制出金和银板材﹐用以制造钱币。
此后在西班牙﹑比利时和英国相继出现轧机。
1728 年设计的生产圆棒材用的轧机为英国设计的生产圆棒材用的轧机。
英国于1766 年有了串行式小型轧机﹐19 世纪中叶﹐第一台可逆式板材轧机在英国投产﹐并轧出了船用铁板。
1848 年德国发明了万能式轧机﹐1853 年美国开始用三辊式的型材轧机﹐并用蒸汽机传动的升降台实现机械化。
接着美国出现了劳特式轧机。
1859 年建造了第一台连轧机。
万能式型材轧机是在1872 年出现的﹔20 世纪初制成半连续式带钢轧机﹐由两架三辊粗轧机和五架四辊精轧机组成。
中国于1871 年在福州船政局所属拉铁厂( 轧钢厂) 开始使用轧机﹔轧制厚15mm 以下的铁板﹐ 6 ~120mm 的方﹑圆钢。
1890 年汉冶萍公司汉阳铁厂装有蒸汽机拖动的横列双机架2450mm 二辊中板轧机和蒸汽机拖动的三机架横列二辊式轨梁轧机以及350/300mm 小型轧机。
随着冶金工业的发展﹐现已有多种类型轧机。
、轧机的分类轧机可按轧辊的排列和数目分类﹐可按机架的排列方式分类﹐也可按生产的产品分类﹐分别列于表 1 轧机按轧辊的排列和数目分类﹑表 2 轧机按机架排列方式分类和表 3 轧机按生产产品分类。
8、轧机的发展现代轧机发展的趋向是连续化﹑自动化﹑专业化﹐产品质量高﹐消耗低。
60 年代以来轧机在设计﹑研究和制造方面取得了很大的进展﹐使带材冷热轧机﹑厚板轧机﹑高速线材轧机﹑H 型材轧机和连轧管机组等性能更加完善﹐并出现了轧制速度高达每秒钟115 米的线材轧机﹑全连续式带材冷轧机﹑5500 毫米宽厚板轧机和连续式H 型钢轧机等一系列先进设备。
轧机用的原料单重增大﹐液压AGC ﹑板形控制﹑电子计算器过程控制及测试手段越来越完善﹐轧制品种不断扩大。
一些适用于连续铸轧﹑控制轧制等新轧制方法﹐以及适应新的产品质量要求和提高经济效益的各种特殊结构的轧机都在发展中。
轧机的主要设备有工作机座和传动装置1)工作机座。
由轧辊﹑轧辊轴承﹑机架﹑轨座﹑轧辊调整装置﹑上轧辊平衡装置和换辊装置等组成。
a.轧辊:是使金属塑性变形的部件。
b.轧辊轴承:支承轧辊并保持轧辊在机架中的固定位置。
轧辊轴承工作负荷重而变化大﹐因此要求轴承摩擦系数小﹐具有足够的强度和刚度﹐而且要便于更换轧辊。
不同的轧机选用不同类型的轧辊轴承。
滚动轴承的刚性大﹐摩擦系数较小﹐但承压能力较小﹐且外形尺寸较大﹐多用于板带轧机工作辊。
滑动轴承有半干摩擦与液体摩擦两种。
半干摩擦轧辊轴承主要是胶木﹑铜瓦﹑尼龙瓦轴承﹐比较便宜﹐多用于型材轧机和开坯机。
液体摩擦轴承有动压﹑静压和静- 动压三种。
优点是摩擦系数比较小﹐承压能力较大﹐使用工作速度高﹐刚性好﹐缺点是油膜厚度随速度而变化。
液体摩擦轴承多用于板带轧机支承辊和其它高速轧机。
c.轧机机架:由两片“牌坊”组成以安装轧辊轴承座和轧辊调整装置﹐需有足够的强度和钢度承受轧制力。
机架形式主要有闭式和开式两种。
闭式机架是一个整体框架﹐具有较高强度和刚度﹐主要用于轧制力较大的初轧机和板带轧机等。
开式机架由机架本体和上盖两部分组成﹐便于换辊﹐主要用于横列式型材轧机。
此外﹐还有无牌坊轧机。
d.轧机轨座:用于安装机架﹐并固定在地基上﹐又称地脚板。
承受工作机座的重力和倾翻力矩﹐同时确保工作机座安装尺寸的精度。
e.轧辊调整装置:用于调整辊缝﹐使轧件达到所要求的断面尺寸。
上辊调整装置也称“压下装置”﹐有手动﹑电动和液压三种。
手动压下装置多用在型材轧机和小的轧机上。
电动压下装置包括电动机﹑减速机﹑制动器﹑压下螺丝﹑压下螺母﹑压下位置指示器﹑球面垫块和测压仪等部件﹔它的传动效率低﹐运动部分的转动惯性大﹐反应速度慢﹐调整精度低。
70 年代以来﹐板带轧机采用AGC( 厚度自动控制) 系统后﹐在新的带材冷﹑热轧机和厚板轧机上已采用液压压下装置﹐具有板材厚度偏差小和产品合格率高等优点。
f.上轧辊平衡装置:用于抬升上辊和防止轧件进出轧辊时受冲击的装置。
形式有﹕弹簧式﹑多用在型材轧机上﹔重锤式﹐常用在轧辊移动量大的初轧机上﹔液压式﹐多用在四辊板带轧机上。
g.为提高作业率﹐要求轧机换辊迅速﹑方便。
换辊方式有C 形钩式﹑套筒式﹑小车式和整机架换辊式四种。
用前两种方式换辊靠吊车辅助操作﹐而整机架换辊需有两套机架﹐此法多用于小的轧机。
小车换辊适合于大的轧机﹐有利于自动化。
目前﹐轧机上均采用快速自动换辊装置﹐换一次轧辊只需 5 ~8 分钟。
2)传动装置由电动机﹑减速机﹑齿轮座和连接轴等组成。
齿轮座将传动力矩分送到两个或几个轧辊上。
3)辅助设备包括轧制过程中一系列辅助工序的设备。
如原料准备﹑加热﹑翻钢﹑剪切﹑矫直﹑冷却﹑探伤﹑热处理﹑酸洗等设备。
4)起重运输设备吊车﹑运输车﹑辊道和移送机等。
5)附属设备有供﹑配电﹑轧辊车磨﹐润滑﹐供﹑排水﹐供燃料﹐压缩空气﹐液压﹐清除氧化铁皮﹐机修﹐电修﹐排酸﹐油﹑水﹑酸的回收﹐以及环境保护等设备。
4、轧机的命名按轧制品种﹑轧机型式和公称尺寸来命名。
“公称尺寸”的原则对型材轧机而言﹐是以齿轮座人字齿轮节圆直径命名﹔初轧机则以轧辊公称直径命名﹔板带轧机是以工作轧辊辊身长度命名﹔钢管轧机以生产最大管径来命名。
有时也以轧机发明者的名字来命名( 如森吉米尔轧机) 。
5、轧机的选择按生产的产品品种﹑规格﹑质量和产量的要求来选定成品或半成品轧机的类型和尺寸﹐并配备必要的辅助﹑起重运输和附属设备﹐然后根据各种因素的要求最后加以平衡选定。
6、轧机动力设施1590 年英国开始用水轮机拖动轧辊﹐直到1790 年还有用水轮机配以石制飞轮拖动四辊式钢板轧机的( 图4 水轮机拖动的钢板轧机) 。
1798 年英国开始用蒸汽机拖动轧机。
现代的轧机均为直流或交流电动机拖动﹐有单机拖动﹐也有通过齿轮成组拖动。