无头轧制技术的发展及展望
ESP无头连铸连轧带钢工艺的创新与展望_张志勤

阿维迪公司 克雷莫纳 厂的 ISP 工 艺路线为 连铸 ※粗轧机 组(3 架)※感 应加热装 置 ※精轧 机组(5 架), 生产线长约 175 m 。 而传统带有隧 道式加热炉的薄板坯 连铸连轧生产线(O TS)长 约为 430 m 。表 2 为 3 种薄 板坯连铸 连轧工艺 对比[ 5] 。
设计
工艺
维迪公司与西门子奥钢联各持股 50 %, 共同投资 兴建总部位于意大利克雷莫纳的合资公司 —克雷 莫纳工程有限公司 , 该合资公司负责这项耗资 3 亿欧元的新生产线的开发与设计 。西门子奥钢联
公司成为克雷莫纳厂工艺和设备制造安装的总承
包商 。 该 ESP 采用单条连铸线 , 目前产能为 200 万
t/ a , 如果提高铸机的拉速 , 在 1 850 m m ESP 生 产线上(单 流)以 7 .5 m/ min 的拉速 进行 无头 轧 制 , 设计产 能可 达 250 ~ 300 万 t/ a[ 2] 。 图 1 为 ESP 生产线示意图 , 表 1 为 ESP 生产线的技术参 数[ 3] 。
1 .2 .2 ESP 工艺技术背景
阿维迪公司克雷莫纳厂 ISP 技术的成熟 , 为 ESP 技术奠定了基础 , 该公司决定采用 ESP 技术 投资兴建 1 条新的 生产线 。 ESP 生产线比 已经 运行在克雷莫纳的 ISP 生产线投资成本更低 。
中国轧钢技术的发展现状和展望

中国轧钢技术的发展现状和展望轧钢技术是指通过各种轧制工艺将钢锭、钢坯或钢材加工成所需形状和性能的产品。
作为钢铁工业的重要组成部分,轧钢技术的发展对于提高钢铁产品质量和降低能耗具有重要意义。
本文将介绍中国轧钢技术的发展现状、取得的成果、未来发展方向以及面临的瓶颈问题。
轧钢技术有着悠久的历史,经历了从初期的手动轧制到现代自动化轧制的发展过程。
中国轧钢行业在近几十年来取得了长足的进步,成为世界上最大的钢铁生产和消费国。
不过,与发达国家相比,中国轧钢技术还存在一定的差距,主要表现在工艺技术水平、装备水平和产品性能等方面。
高效轧制技术:中国已成功研发出了一系列高效轧制技术,如控轧控冷技术、连铸坯热装热送技术等,有效提高了轧钢生产效率和产品质量。
特种钢材开发:中国在特种钢材开发方面取得了重要突破,如高速铁路用钢、汽车用高强度钢等,达到了国际先进水平。
自动化智能化技术:随着自动化和智能化技术的发展,中国轧钢行业积极引进和研发相关技术,实现了生产线自动化、智能化控制,提高了产品质量和生产效率。
工艺技术水平较低:与发达国家相比,中国部分轧钢工艺技术水平还比较落后,如精密轧制、高效矫直等技术有待进一步提高。
装备水平不高:中国轧钢装备整体水平还有待提高,部分设备仍存在精度低、稳定性差等问题。
产品性能差距较大:部分轧制产品的性能与国际先进水平存在一定差距,如高强度钢材、高温合金等。
高效化:全球轧钢技术正在向高效化方向发展,通过提高生产效率、降低能耗来降低生产成本。
自动化智能化:随着人工智能、物联网等技术的发展,轧钢生产的自动化和智能化水平将得到进一步提升。
绿色环保:环保成为全球钢铁行业的共同课题,通过采用环保技术和设备来降低轧钢生产过程中的环境污染。
提升工艺技术水平:加大对高效轧制、精密轧制等技术的研发和应用力度,提高轧钢生产效率和产品质量。
优化产业结构:通过淘汰落后产能、推动企业兼并重组等方式,优化轧钢产业结构,提高产业集中度和竞争力。
轧钢技术的现状和新发展概述
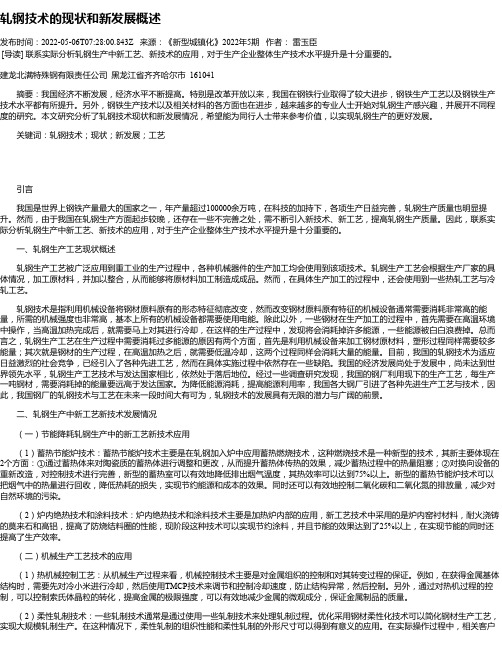
轧钢技术的现状和新发展概述发布时间:2022-05-06T07:28:00.843Z 来源:《新型城镇化》2022年5期作者:雷玉臣[导读] 联系实际分析轧钢生产中新工艺、新技术的应用,对于生产企业整体生产技术水平提升是十分重要的。
建龙北满特殊钢有限责任公司黑龙江省齐齐哈尔市 161041摘要:我国经济不断发展,经济水平不断提高。
特别是改革开放以来,我国在钢铁行业取得了较大进步,钢铁生产工艺以及钢铁生产技术水平都有所提升。
另外,钢铁生产技术以及相关材料的各方面也在进步,越来越多的专业人士开始对轧钢生产感兴趣,并展开不同程度的研究。
本文研究分析了轧钢技术现状和新发展情况,希望能为同行人士带来参考价值,以实现轧钢生产的更好发展。
关键词:轧钢技术;现状;新发展;工艺引言我国是世界上钢铁产量最大的国家之一,年产量超过100000余万吨,在科技的加持下,各项生产日益完善,轧钢生产质量也明显提升。
然而,由于我国在轧钢生产方面起步较晚,还存在一些不完善之处,需不断引入新技术、新工艺,提高轧钢生产质量。
因此,联系实际分析轧钢生产中新工艺、新技术的应用,对于生产企业整体生产技术水平提升是十分重要的。
一、轧钢生产工艺现状概述轧钢生产工艺被广泛应用到重工业的生产过程中,各种机械器件的生产加工均会使用到该项技术。
轧钢生产工艺会根据生产厂家的具体情况,加工原材料,并加以整合,从而能够将原材料加工制造成成品。
然而,在具体生产加工的过程中,还会使用到一些热轧工艺与冷轧工艺。
轧钢技术是指利用机械设备将钢材原料原有的形态特征彻底改变,然而改变钢材原料原有特征的机械设备通常需要消耗非常高的能量,所需的机械强度也非常高,基本上所有的机械设备都需要使用电能。
除此以外,一些钢材在生产加工的过程中,首先需要在高温环境中操作,当高温加热完成后,就需要马上对其进行冷却,在这样的生产过程中,发现将会消耗掉许多能源,一些能源被白白浪费掉。
总而言之,轧钢生产工艺在生产过程中需要消耗过多能源的原因有两个方面,首先是利用机械设备来加工钢材原材料,塑形过程同样需要较多能量;其次就是钢材的生产过程,在高温加热之后,就需要低温冷却,这两个过程同样会消耗大量的能量。
无头轧制技术的发展动态
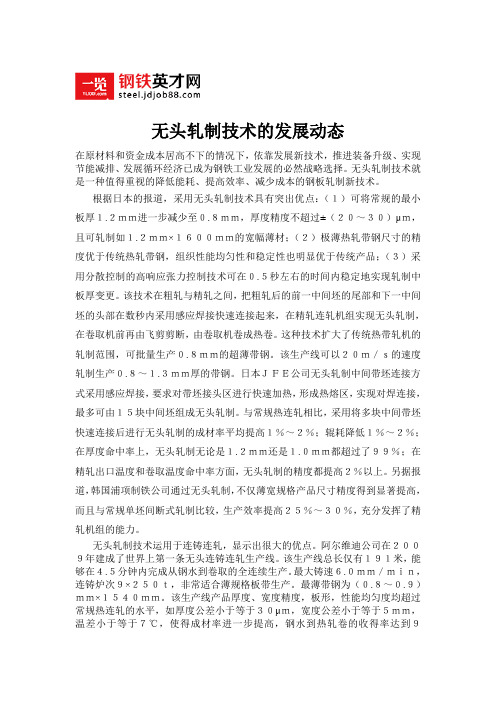
无头轧制技术的发展动态在原材料和资金成本居高不下的情况下,依靠发展新技术,推进装备升级、实现节能减排、发展循环经济已成为钢铁工业发展的必然战略选择。
无头轧制技术就是一种值得重视的降低能耗、提高效率、减少成本的钢板轧制新技术。
根据日本的报道,采用无头轧制技术具有突出优点:(1)可将常规的最小板厚1.2mm进一步减少至0.8mm,厚度精度不超过±(20~30)μm,且可轧制如1.2mm×1600mm的宽幅薄材;(2)极薄热轧带钢尺寸的精度优于传统热轧带钢,组织性能均匀性和稳定性也明显优于传统产品;(3)采用分散控制的高响应张力控制技术可在0.5秒左右的时间内稳定地实现轧制中板厚变更。
该技术在粗轧与精轧之间,把粗轧后的前一中间坯的尾部和下一中间坯的头部在数秒内采用感应焊接快速连接起来,在精轧连轧机组实现无头轧制,在卷取机前再由飞剪剪断,由卷取机卷成热卷。
这种技术扩大了传统热带轧机的轧制范围,可批量生产0.8mm的超薄带钢。
该生产线可以20m/s的速度轧制生产0.8~1.3mm厚的带钢。
日本JFE公司无头轧制中间带坯连接方式采用感应焊接,要求对带坯接头区进行快速加热,形成热熔区,实现对焊连接,最多可由15块中间坯组成无头轧制。
与常规热连轧相比,采用将多块中间带坯快速连接后进行无头轧制的成材率平均提高1%~2%;辊耗降低1%~2%;在厚度命中率上,无头轧制无论是1.2mm还是1.0mm都超过了99%;在精轧出口温度和卷取温度命中率方面,无头轧制的精度都提高2%以上。
另据报道,韩国浦项制铁公司通过无头轧制,不仅薄宽规格产品尺寸精度得到显著提高,而且与常规单坯间断式轧制比较,生产效率提高25%~30%,充分发挥了精轧机组的能力。
无头轧制技术运用于连铸连轧,显示出很大的优点。
阿尔维迪公司在2009年建成了世界上第一条无头连铸连轧生产线。
该生产线总长仅有191米,能够在4.5分钟内完成从钢水到卷取的全连续生产。
轧制设备的发展趋势
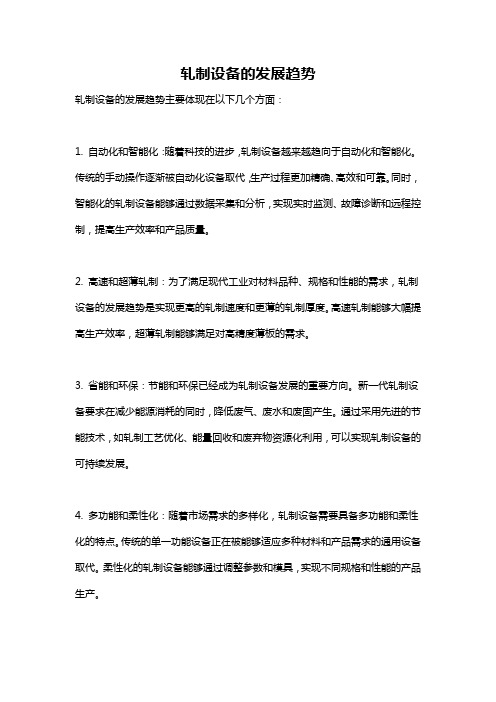
轧制设备的发展趋势
轧制设备的发展趋势主要体现在以下几个方面:
1. 自动化和智能化:随着科技的进步,轧制设备越来越趋向于自动化和智能化。
传统的手动操作逐渐被自动化设备取代,生产过程更加精确、高效和可靠。
同时,智能化的轧制设备能够通过数据采集和分析,实现实时监测、故障诊断和远程控制,提高生产效率和产品质量。
2. 高速和超薄轧制:为了满足现代工业对材料品种、规格和性能的需求,轧制设备的发展趋势是实现更高的轧制速度和更薄的轧制厚度。
高速轧制能够大幅提高生产效率,超薄轧制能够满足对高精度薄板的需求。
3. 省能和环保:节能和环保已经成为轧制设备发展的重要方向。
新一代轧制设备要求在减少能源消耗的同时,降低废气、废水和废固产生。
通过采用先进的节能技术,如轧制工艺优化、能量回收和废弃物资源化利用,可以实现轧制设备的可持续发展。
4. 多功能和柔性化:随着市场需求的多样化,轧制设备需要具备多功能和柔性化的特点。
传统的单一功能设备正在被能够适应多种材料和产品需求的通用设备取代。
柔性化的轧制设备能够通过调整参数和模具,实现不同规格和性能的产品生产。
5. 精密和定制化:随着科学技术的进步,精密轧制设备的发展趋势是实现更高的产品质量和精度要求。
例如,高精度轧制设备可以实现微米级的产品厚度控制和表面粗糙度要求。
定制化的轧制设备能够根据用户的具体需求,进行个性化设计和生产。
总的来说,轧制设备的发展趋势是自动化、智能化、高速化、超薄化、省能环保、多功能柔性化、精密化和定制化。
这些趋势能够推动轧制设备的技术进步和产业升级。
钢铁轧制技术的进步与发展趋势探索

钢铁轧制技术的进步与发展趋势探索摘要:改革开放以来,中国钢铁轧制技术取得了长足的进步。
工业和国民经济的发展,钢材需求量增大,推动了轧钢制造技术的进步与发展。
经过钢铁轧制技术自主创新,中国钢铁轧制技术已经跻身世界先进行列,基本完成了工业化过程。
关键词:钢铁轧制;技术进步;发展趋势近年来,我国钢铁工业在经历了快速发展后,进入了调整结构、转型发展的阶段。
钢铁企业在努力消化引进技术,提高管理与生产操作水平的同时,也在大力进行技术创新,着力开发绿色化、智能化的新技术、新工艺、新装备、新产品,不断增强核心竞争力。
一、中国轧钢技术的发展概况改革开放以来,特别是进入21世纪以来,中国钢铁工业飞跃发展,为中国社会进步和经济腾飞做出了巨大贡献。
作为钢铁工业的关键成材工序,轧钢行业在引进、消化、吸收的基础上,开展集成创新和自主创新,在轧制工艺技术进步、装备和自动化系统研制和引领未来钢铁材料的开发方面实现跨越式发展,为中国钢铁工业的可持续发展做出了突出贡献。
经过改革开放以来的持续发展,中国已经建设了一大批具有国际先进水平的轧钢生产线,比较全面地掌握了国际上最先进的轧制技术,具备了轧钢先进设备的开发、设计、制造能力,一大批国民经济急需、具有国际先进水平的钢材产品源源不断地供应国民经济各个部门,为中国经济与社会发展、人民幸福安康提供了重要的基础原材料。
作为一个发展中的国家,必须尽快掌握世界上的最先进的轧钢技术,引进、消化、吸收是必须的。
改革开放以来,以宝钢建设为契机,中国成套引进了热连轧、薄板坯连铸连轧、冷连轧、中厚板轧制、棒线轧制、长材轧制、钢管轧制等各类轧制工艺技术以及相应的轧制设备和自动化系统,开始了轧制技术的跨越式发展的第一步。
通过引进技术的消化吸收和再创新,中国快速掌握了轧钢领域的前沿工艺技术;通过设备的合作制造以及自主研发,中国掌握了重型轧机的设计、制造、安装的核心技术,逐步具备了自主集成和开发建设先进轧机的能力;利用先进的工艺和装备技术,以及严格科学精细的管理,开发了一大批先进的钢铁材料,满足了经济发展的急需,产品的质量水平不断提高。
中国轧钢技术的发展现状和展望

中国轧钢技术的发展现状和展望一、发展现状1.技术水平提升2.设备自主研发中国轧钢技术的另一个重要进展是设备的自主研发。
过去,中国的钢铁行业依赖于进口设备,但现在情况已经改变。
近年来,中国钢铁企业大力推动设备的自主创新和研发,不断提高设备制造水平,并逐步减少对进口设备的依赖。
3.品种多样化4.绿色环保在技术发展的同时,中国轧钢技术也在积极推动绿色环保。
钢铁行业是一个高能耗、高排放的行业,但随着环保意识的增强,轧钢企业开始重视减少能源消耗和环境污染。
通过技术创新和改进,轧钢工艺不断优化,减少二氧化碳和废气的排放。
二、展望1.技术创新未来,中国轧钢技术将继续加大技术创新力度,提高技术水平和竞争力。
优化工艺流程、提升设备制造水平、加强智能化改造,将成为技术创新的重点。
同时,应加强与科研机构和高校的合作,加强基础研究,掌握核心技术,推动钢铁行业的创新发展。
2.提高产品品质随着轧钢技术的不断进步,未来的发展将更加注重产品品质的提高。
通过提升工艺与材料的结合性能,探索新型合金材料和加工工艺,以提高产品质量和性能。
同时,加强质量控制和监管,推动中国钢材产业向高质量发展。
3.绿色可持续发展未来,中国轧钢技术将继续积极推动绿色可持续发展。
技术创新将聚焦于节能减排和废弃物利用,通过提高能源利用效率、减少废弃物的生成和加强废弃物处理,实现钢铁行业的绿色转型。
4.国际合作总之,中国轧钢技术在过去几十年取得了长足的进步,但仍然面临着很多挑战。
未来,中国轧钢技术将继续发展,通过技术创新、产品品质提高、绿色可持续发展和国际合作,推动钢铁行业向更高水平发展,为中国经济的可持续发展做出更大贡献。
中国轧钢技术的发展现状和展望

中国轧钢技术的发展现状和展望
中国是全球最大的钢铁生产国,并且钢材产量持续增长。
轧钢技术是钢材生产
主要工艺之一,其发展对于提高钢铁生产效率、质量和节能减排具有重要意义。
当前,中国轧钢技术正朝着高效、智能、绿色的方向发展。
一方面,钢厂开始
采用先进的轧机和轧辊,并配合自动化控制系统和在线质检系统,以提高生产效率和品质;另一方面,环保和节能减排成为越来越重要的问题,钢厂开始采用清洁生产技术和新型炉料,例如废钢和可再生能源。
未来,随着工业4.0和数字化技术的普及,轧钢技术将会更加智能化,例如通
过物联网技术实现设备和生产过程的远程监控、预测性维护等。
同时,绿色和低碳依然是轧钢技术发展的重点,包括采用清洁生产技术、绿色制造和再生资源利用等。
总之,随着技术的不断进步和环保意识的加强,中国轧钢技术的未来发展有望实现高效、智能、绿色、低碳等目标。
- 1、下载文档前请自行甄别文档内容的完整性,平台不提供额外的编辑、内容补充、找答案等附加服务。
- 2、"仅部分预览"的文档,不可在线预览部分如存在完整性等问题,可反馈申请退款(可完整预览的文档不适用该条件!)。
- 3、如文档侵犯您的权益,请联系客服反馈,我们会尽快为您处理(人工客服工作时间:9:00-18:30)。
无头轧制技术的发展及展望上世纪60年代以前,传统生产钢材方法是先将钢水模铸成大型钢锭,经加热、轧制成坯,钢坯经冷却、清整后再加热,轧成用户所需断面的成品钢材。
近40多年来经历了三次飞跃式发展:一是将模铸改为连铸,取消开坯机;二是由一般连铸改为近终形连铸,减少加热、轧制次数;无头轧制技术是钢铁加工流程的第三次飞跃,即钢材生产不再是单块的、间隙性的,而是连续进行轧制,然后根据用户需求剪切成所需长度或卷重。
无头轧制的好处是:1.钢材全长以恒定速度进行轧制,生产率有较大提高;2.因对钢材全长施加恒定张力,使钢材断面形状波动减少,钢材质量改善,这点对热轧扁平材生产特别重要;3.由于成品长度不受限制,根据交货状态要求剪切,成品率显著提高;4.由于轧材运行稳定性提高,对热轧带钢来说,有利于生产薄规格带钢;5.和单块轧制不同,钢品啮入次数减少,减小对轧辊冲击,有利于提高轧辊寿命。
在施行无头轧制技术中分扁平材和长材两类,其中又有无头轧制和半无头轧制的区别;就技术类型来说分为焊接型和铸轧型两种,将分别叙述于后。
扁平材的无头轧制1.在传统热连轧带钢机上无头轧制。
第一台全连续无头轧制热连轧带钢机是1996年在日本JFE公司千叶厂投用的。
它的轧机组成是:粗轧机架3台,精轧机架7台,辊身长2030mm,设计最高轧速为25m/s,年产能力为540万t。
连铸坯经加热在粗轧机架轧成最大厚度为50mm中间带坯进人热卷箱,在热卷箱后设有中间带坯剪断机,将带坯头剪平,以便于后面的焊接设备(用对接压合法电磁感应焊接)进行焊接,焊接后的带坯经过带坯边部加热器使带坯温度均匀,然后送入精轧机架轧成所需带钢厚度,由于中间带坯头尾已经焊接,从理论上来讲是可以无限长的,故称为无头轧制。
轧机后卷取机前设有高速带钢剪断机,将高速前进的带钢(最大1200m/min)切断分卷。
在千叶厂3号轧机全连续无头轧制取得成功经验后,日本新日铁公司和韩国浦项公司分别将其大分厂和光阳厂热连轧带钢机改造成能无头轧制的全连续热轧带钢机。
由于中间带坯焊接操作过程比较复杂,对中间坯头尾可搭接性能要求较高,因而这项技术还没有在全球范围内迅速推广。
据对千叶厂考察该轧机的情况介绍,由于市场原因,千叶3#热连轧带钢机实际年产量为300—350万t (设计年产能力540万t的55%-65%),采用无头轧制产品的月产量不足4万t。
随着生产经验的积累和对新技术的掌握和改进,相信这项技术将会发挥更大的作用。
2.薄板坯连铸连轧生产线上半无头轧制。
实现半无头轧制薄板坯连铸连轧生产线的基本设备配置和传统的薄板坯连铸连轧大体相同,但是技术上上有较大变化,即钢水经连铸机浇铸成钢坯后,不需剪切分段直接送人辊底加热炉进行均热,热后即直送轧机轧制,如德国西马克·德马克公司设计的CSP连铸机薄板坯出结晶器时厚63mm,经过液芯压下离开连铸机时铸坯厚48mm,因铸坯不经剪切进入加热炉(传统CSP技术铸坯剪断为40余米),加热炉长达300余米(传统CSP技术为200米左右),铸坯经均热后进入7机架连轧机组轧制成材。
输出冷却辊道分为两段,第一段较短,为30m左右,其中快速水冷却水集管段为10余米,冷却段后为超薄带卷取机(旋转卷取机);第二段为传统的层流冷却和卷取机,主要生产一般规格的热带。
这种类型的生产线以超薄规格薄带为主,其中0.8—3.0mm的带钢占60%以上,高强钢最小厚度为1.2mm,低碳钢可达0.8mm,由于采用该项技术,双流连铸机最大年产量可达240万t,半无头轧制技术利用了连铸坯长的特点,减少了穿带过程中产生的带钢温度降低、厚度不易控制和生产不稳定的问题,极有利于薄规格带钢轧制。
我国华菱集团涟源钢铁公司新建薄板坯连铸连轧生产线即是按上述半无头轧制工艺设计建设的。
由德国西马克·德马克公司供货,投产8个月后即成功创造世界同类型生产线半无头轧制268m长坯的最长纪录以及生产出厚度为0.78mm特薄热轧带卷,涟钢均热炉长291.15m,是目前世界上最长的均热炉。
棒、线材无头轧制棒线材无头轧制技术有三种类型:一是铸轧型无头轧制技术。
将方坯连铸机和热连轧机结合在一条生产线上连铸连轧棒线材的新工艺称为Luna无头铸轧技术。
二是连铸坯焊接型无头轧制技术。
将在步进炉加热好的钢坯进行焊接,成为无头坯送往轧机进行轧制。
三是中间坯焊接型无头轧制技术。
将经粗轧机架轧制后的中间坯(由45mm左右)进行焊接,在中轧、精轧机中实现无头轧制。
1.铸轧型无头轧制技术。
意大利达涅利公司开发成功该项技术并用于意大利乌迪内ABS公司的年产50万t特殊钢棒线材工业性生产厂中,已于2000年8月正式投产。
连铸机和热连轧机配置在一条生产线上,铸机产品为160mm×200mm大方坯,共两流。
连铸机后设有两个淬火箱,其后为125m长辊底式加热炉,加热炉前设有65m长双流隧道式炉以作为工序间缓冲,热缓冲能力约为45t。
生产线能以单流或双流生产,在单流生产时,连铸坯可以是14m以上的任意长度,在连铸和连轧两工序间不进行任何切割,实际上实现了半无头轧制。
当双流生产时,连铸坯要切割成45m长交替送到隧道式炉中,然后送入辊底式加热炉加热和均热。
轧机由18架粗、中轧和预精轧机架及3架三辊RSB减定径机架组成,在精轧机前后装备有控温轧制所需的必要设施,包括在线热处理的淬火及回火(退火)设施。
从技术上来讲,Luna无头铸轧技术给长材轧制工艺带来了一场革命性变化,它实现了从连铸、连轧、在线热处理、表面精整到在线检查的全连续化;全部工序都实现了计算机控制,从订单下达到成品入库全部生产过程不超过4小时。
ABS公司吨钢材成本较常规技术减少约40美元。
工厂产品规格为圆钢Φ20-100mm,圆钢盘卷φ15-50mm和相应规格的方钢。
钢种有碳素钢、表面硬化钢、低合金钢、调质钢、轴承钢、弹簧钢和不锈钢。
2003年1月,ABS公司对其Luna生产线上在线退火装置进行改造,将炉室长度增加一倍,可处理长50m 轧材,原退火炉只能处理长24m轧材,严重制约整条生产线能力的发挥。
2.连铸坯焊接型无头轧制技术。
该技术是连铸方坯经步进式加热炉加热后将前一块钢坯尾部和后一块钢坯头部进行对焊(用闪光焊接),形成无头坯送热连轧机进行轧制,名为EWR(Endlees Welding Rolling)。
自从1998年3月在日本东京高松厂问世以来有了快速的发展,闪光焊机设在加热炉出料端后,焊接过程由计算机控制,并纳入轧钢自动化系统,因而有良好的焊接过程稳定性和可重复性,各种断面形状和钢种的钢坯均能对焊,最大规格可达200x200mm。
我国唐山钢铁公司棒材厂建设的EWR装置对焊165mm方坯所需周期约37-40秒,其中焊接时间约10秒。
由于焊接技术的提高,焊口位置不但不存在内部缺陷,强度指标也不亚于轧件母体。
无头轧制和常规轧制相比,生产效率可提高12%-16%,生产成本降低2.5%-3.0%,棒材定尺率接近100%,金属收得率提高约l%,从轧件品质分析,因为仅有一个头部,所以能明显减少轧制纵向尺寸和性能不均现象。
除新建轧机外,在现有现代化连续棒材轧机上可以新增无头轧制装置,如唐钢棒材厂即属于改造项目,总投资210万美元。
3.中间坯焊接型无头轧制技术。
该项技术系将经粗轧机架轧成的中间坯头尾焊接后送中轧、精轧机轧制,类似传统热轧带钢机装设的无头轧制装置。
新工艺由日本大和钢公司在其所属东部事业所开发成功。
作业时间共30-70秒,其中焊接时间5.5秒,中间坯断面φ45mm,长36m。
该技术开发成功,使东部事业所轧制能力提高约20%,冷坯发生率减少,热坯使用率由75%增到9l%,燃料消耗减少,成材率有较大提高。
展望1.在扁平材无头轧制技术中,以薄板坯连铸连轧生产线中实施半无头轧制较简易可行,我国涟源钢铁公司CSP薄板坯连铸连轧生产线已有良好的开端,特别对生产薄规格带钢具有显著优越性。
传统热连轧带钢机无头轧制技术也有广阔发展前景,但作为一项全新技术有一个继续开发、改进和掌握的过程,是完全可以理解的。
2.在棒线材无头轧制技术中,以连铸坯焊接型无头轧制应用最多,在泰国、马来西亚、墨西哥、西班牙等国若干长材生产厂都得到采用,我国第一家采用该技术的是唐山钢铁公司棒材厂,新疆八一钢铁公司和湖南涟源钢铁公司也采用了该项技术,但在实际生产中出现一些问题和要求,一是提供无缺陷连铸坯是应用此项技术的前提条件;二是钢坯对焊成功率主要取决于对接钢坯端面几何形状的一致性。
目前一些钢厂对焊率不高主要是由于火焰切割的坯料端面不整齐和铸坯断面脱矩造成的,因此该项技术使用率不高,绝大部分仍采用常规轧制。
但无头轧制优越性十分明显,连铸坯焊接型无头轧制新增设备不多,投资额不大,结构和操作不很复杂,具有进一步推广使用的前景。
3.中间坯焊接型棒材无头轧制技术的优点和问题与前述铸坯焊接型大体相同,它的长处还存在于:①中间坯断面小,设备费用少,消耗材料少;②中间坯焊接时产生毛刺少,易于去除。
但其所需设备较多,操作较复杂,目前除日本大和钢铁公司东部事务所外,其他企业应用较少,尚需进一步实践。
4.铸轧型棒线材无头轧制技术实质上是类薄板坯连铸连轧的方坯连铸连轧,在技术上比较成熟,如用于生产普通碳素钢棒材、钢筋和线材,没有特殊钢生产的在线热处理作业,生产将更易掌握。
5.无头轧制和半无头轧制技术具有显著优越性和巨大的经济效益,但总的说来,在生产实践中应用的时间还不长,采用的厂家还不多,属于一种正在发展中、有广阔发展前景的新工艺技术,值得关注、重视并以积极态度去开发和探索。
具体建议:一是在以后新建薄板坯连铸连轧生产线时应重视研究采用半无头制技术的可行性。
特别是当产品要求薄规格带钢品种较多时,应该采用这项技术。
二是在我国适当地点建设一些Luna无头铸轧生产线,这可能会象薄板坯连铸连轧一样,为我国在棒线材生产领域出现一场新的变革作出贡献,三是选择一家新建或现有的传统热连轧带钢机安设无头轧制焊接设施,摸索经验,解决存在的矛盾的问题。
四是认真总结交流已建成连铸坯焊接型棒线材无头轧制的经验教训,不断提高对焊成功率和无头轧制焊接装置的使用率。