螺杆零件加工工艺标准设计
物理微发泡螺杆设计、性能测试及仿真研究

作者简介:Sai Yandamuri,男,硕士,项目工程师,主要从事先进成型技术的研究。
收稿日期:2023-02-02在塑料成型工艺中,物理微发泡注塑成型技术比较常见。
物理微发泡注塑成型有许多优点:(a )能够减轻产品的重量,减少塑料使用量,降低成本。
(b )无需保压阶段,从而缩短了生产周期,提高了生产率。
(c )成型零件翘曲较少,无缩水痕,提高尺寸稳定性。
(d )可以降低锁模力、注射压力等,更节能,为碳中和和碳达峰做出贡献。
现在运用物理微发泡技术的厂家也越来越多。
主流的厂家及技术如下:(1)Cellmould,威猛巴顿菲尔,仅适用于巴顿菲尔机器。
(2)Ku -Fizz,大众/齐默尔曼,适配不同的机器。
(3)MuCell,卓细,与大多数注塑机制造商合作。
(4)Plastinuum,由KIMW 开发,可作为附加系统用于不同的机器。
目前MuCell 应用的最为广泛[1],与之合作的注塑机厂家最多。
市场上现有螺杆具有较短的塑化长度、两个止逆环和一个混合区,导致较低的塑化性能和较高的剪切力。
尤其对于快速塑化或使用剪切敏感材料的应用,与实体工艺相比,现有产品可能会有些不足。
伊之密德国研究所和中国研究院联合开发了自己的螺杆几何结构,以实现相同的发泡质量,而不存在现有产品的缺陷。
物理微发泡螺杆设计、性能测试及仿真研究Sai Yandamuri 1,张雨筱1,施小庆2,陈炽辉2(1.伊之密德国先进成型技术研究所,德国 阿尔斯多夫 52477;2.伊之密股份有限公司,广东 佛山 528306)摘要:自主设计的物理微发泡注塑成型FoamPro 螺杆,对比现有产品,通过多种材料的实验测试及仿真验证,有更高的塑化效率,相当的发泡效果,可用于商业化应用。
关键词:物理微发泡注塑成型;FoamPro 螺杆;更高的塑化效率;相当的发泡效果中图分类号:TQ330.41,TQ320.6文章编号:1009-797X(2023)12-0026-07文献标识码:B DOI:10.13520/ki.rpte.2023.12.0061 螺杆结构实验机器选用伊之密A5系列220 t 三板注塑机,螺杆直径53 mm 。
注塑(注射)螺杆是如何设计

注塑(注射)螺杆是如何设计随着人们对高分子化合物认识的不断深化,注射螺杆有了很大发展。
由于注射螺杆的技术性能是实现优良注射塑化性能的关键,因此对于注射螺杆的合理设计显得尤为重要。
本文分析了注射螺杆主要技术参数及主要结构与技术性能之间的关系,提出了注射螺杆主要技术参数确定的原则,结合作者的设计实际,从理论和实践两方面做了比较具体的分析与研究。
螺杆长径比螺杆长径比是螺杆的一个十分重要的参数,对于常用的通用螺杆而言,尤为重要。
通用螺杆的长径比由13~14,提高到18,现已提高到20~22,甚至达到26。
1、螺杆长径比与注射行程注射行程表达了注射量的大小,是一个重要的技术参数。
注射过程中螺杆填充的物料量基本上是一个很不确定的因素。
注射时,螺杆轴向前移,物料流入螺槽,但不能充满螺槽,因为注射时间不足以满足完全填满螺杆沟槽所需的时间。
由于物料填充稀疏,空气易被吸入,此时空气若不能及时排出,会使塑化质量降低。
通常,计量行程的大小是决定空气能否进入储料缸的主要因素。
多种物料的研究表明,计量行程若大于3D,止回环后面会有夹气产生。
此时如果螺杆长径比小于18(满足3D的计量行程的螺杆长径比),即加料段固体开始熔融的长度太短,则会使固体向压缩段熔体转变时残留在熔体中的固体大量增加,在严重的情况下,甚至可造成输送停止。
因此要想获得超过3D的计量行程,必须增加螺杆的有效长度,使固体料在加料过程中能够有足够的熔融路径进行熔融,以减少熔体中固体含量,使熔体体积的组成与压缩段的体积流组成相匹配,从而实现计量所要求的熔融体积大于螺杆螺槽中的熔融体积。
一般情况下,螺杆长径比达到20~25,可满足计量行程大于3D的要求。
另外为了能够解决由于螺杆长径比的增加而引起的加料夹气问题,在螺杆设计上必须满足塑化时固体塞的速度大于固体床的速度。
现在,随着螺杆设计及加工的进步,一般注塑机的注射行程由3D增加到4.5D~5D,有的甚至达到6.5D,螺杆的长径比也由18增加到20~25,甚至更大,从而提高了塑化机构的经济性。
螺杆机阴阳转子的工艺流程

螺杆机阴阳转子的工艺流程The manufacturing process of screw compressor rotors, also known as male and female rotors, is a critical aspect of producing high-quality screw compressors. The process involves several steps, starting from the design phase and ending with the inspection and testing of the finished rotors. The intricate nature of the rotors and the precision required in their manufacturing make it a complex and challenging process.螺杆压缩机转子的制造工艺是生产高质量螺杆压缩机的关键方面。
该过程涉及多个步骤,从设计阶段开始,到最终对成品转子进行检验和测试结束。
转子的复杂性和制造过程中所需的精密度使其成为一个复杂而具有挑战性的过程。
The first step in the manufacturing process of screw compressor rotors is the design phase. During this phase, engineers and designers create detailed blueprints and specifications for the rotors. This involves determining the exact dimensions, tolerances, and material requirements for the rotors. The design phase is crucial as itlays the foundation for the entire manufacturing process and directly impacts the performance and quality of the screw compressor.螺杆压缩机转子制造过程的第一步是设计阶段。
气门摇杆轴支座机械加工工艺规程设计
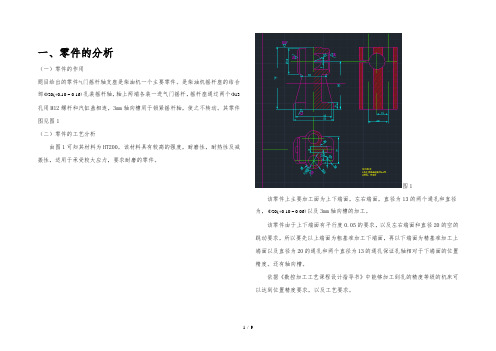
一、零件的分析(一)零件的作用题目给出的零件气门摇杆轴支座是柴油机一个主要零件。
是柴油机摇杆座的结合部)Φ(Φ孔装摇杆轴,轴上两端各装一进气门摇杆,摇杆座通过两个1320+10.0。
16~孔用M12螺杆和汽缸盖相连,3mm轴向槽用于锁紧摇杆轴,使之不转动。
其零件图见图1(二)零件的工艺分析由图1可知其材料为HT200。
该材料具有较高的强度,耐磨性,耐热性及减振性,适用于承受较大应力,要求耐磨的零件。
图1该零件上主要加工面为上下端面,左右端面,直径为13的两个通孔和直径为,).020+Φ以及3mm轴向槽的加工。
(06.0~10该零件由于上下端面有平行度0.05的要求,以及左右端面和直径20的空的跳动要求,所以要先以上端面为粗基准加工下端面,再以下端面为精基准加工上端面以及直径为20的通孔和两个直径为13的通孔保证孔轴相对于下端面的位置精度。
还有轴向槽。
依据《数控加工工艺课程设计指导书》中能够加工到孔的精度等级的机床可以达到位置精度要求,以及工艺要求。
二、确定毛坯(一)毛坯制造方法依据零件材料确定毛坯胚为铸件,因为零件的生产类型为大批量生产,尺寸较大,所以接受砂型机器砂型铸造。
铸件应满足以下要求:(1)铸件的化学成分和力学特性应符合图样规定的材料牌号标准。
(2)铸件的形态和尺寸要求应符合铸件图的规定;(3)铸件表面应进行清砂处理,去除结巴,飞边毛刺,其残留高度应小于或等于1-3mm(4)铸件内部,特别是靠近工作表面处不应有气孔,沙眼,裂纹等缺陷;非工作面不得有严峻的疏松和较大的的缩孔。
(5)铸件应刚好进行热处理。
退火后的硬度小于229HB。
铸件应进行时效处理,消退内应力改善加工性能。
(二)确定毛坯余量接受查表法,查阅《机械制造工艺设计简明手册》表2.2-3该铸造公差等级为CT8-10,MA-H级。
查阅表2.2-4加工表面基本尺寸加工余量等级加工余量数值说明下端面50mm H 4.0 单侧加工上端面48mm H 4.0 单侧加工左端面Φ32mm H 4.0 单侧加工右端面Φ32mm H 4.0 单侧加工,毛坯图三、工艺规程设计(一)定位基准的选择经基准的选择:气门摇杆轴支座下端面既是设计基准又是装配基准所以把它作为精基准满足了基准重合的原则。
滚珠丝杆的设计
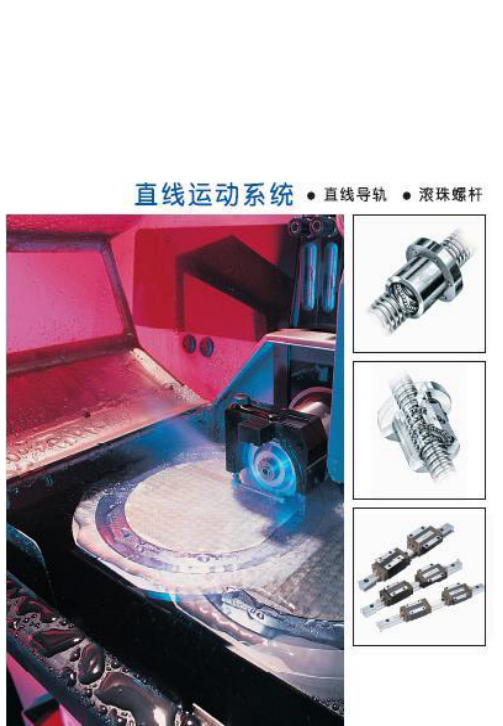
6、定位精度
滚珠螺杆的精度中,导程精度、系统的刚性是主要的影 响因素,其他主要有温度而产生的热变形,安装面的精度等 方面。
弹性变形曲线
6.1 导程精度:
累积基准导程与公称导程相同,但当使用过程中,由于温升所导致螺杆的热膨胀, 或者由于外部负载使螺杆伸缩时,此时可以修正螺杆轴的基准导程负、正向予以补赏。 此时可以将累积导程的目标值提出给本公司,或者由本公司几十年的经验推荐予用户。 另外在补偿螺杆轴的热伸长时,也可以在安装时进行滚珠螺杆的预拉伸。一般以支撑 轴承的负载能力上另加温升2~3 ℃的预拉力。
★1979年研发成功台湾地区第一支研磨级滚珠螺杆 ★1982年引进英国技术外循环研磨级螺杆
★1987年台湾第一支内循环研磨级螺杆 ★1987年台湾第一支高导程研磨级螺杆 ★1990年台湾第一支旋削一般级螺杆 ★1999年台湾第一支7米全程一次热处理螺杆 ★2002年导轨生产线建立 ★2003年台湾第一支9米无焊接一次热处理研磨级螺杆诞生 ★2003年引进日本技术超高精密级直线道轨 ★2004年获台湾精品称号
根据预压力的大小选择相对较薄的垫片 放入螺母之间,施加预压力,由于螺母之间 产生压缩负载,故称:压缩预压。(如下图)
拉伸预压
压缩预压
b.单螺母滚珠螺杆的预压方法: 在滚珠螺杆轴的沟槽种置入比沟槽空 隙空间稍大(1~2μ m)直径的钢珠,使钢珠 与沟槽四点接触产生弹性预压。(如下图)
在螺母中央位置附近的螺纹导程依所需 要的预压量使其偏移。此种预压的方式如同 双螺母,刚性更佳。(如下图)
滚ห้องสมุดไป่ตู้
珠
工
作
图
设
计
各 种
传 动 力
矩
计
算、电
机
螺杆设计质量的标准1
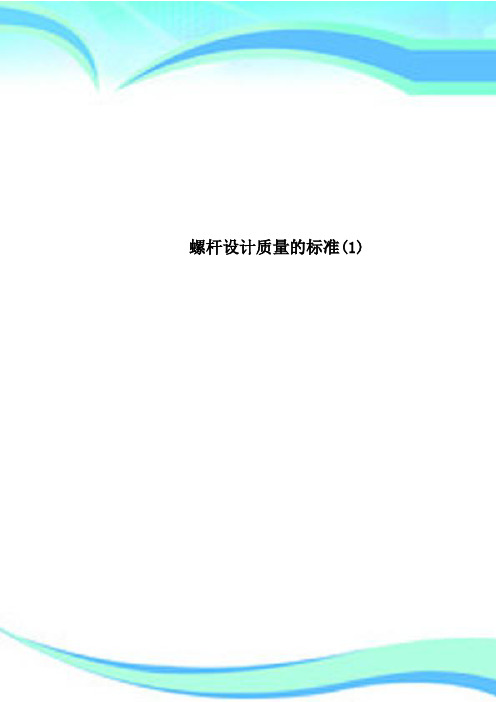
螺杆设计质量的标准(1)————————————————————————————————作者: ————————————————————————————————日期:1.1螺杆设计质量的标准螺杆和料筒组成了挤出机的挤压系统。
为说明挤压系统的重要性,人们通常称之为挤出机的心脏。
塑料(橡胶)正式在这一部分由玻璃态转变为黏流态,然后通过口模、辅机而被做成各种制品的。
由挤出过程分析可以看出,至少应当从以下几个方面评价螺杆:(一)产量所谓产量是指在保证塑化质量的前提下,通过给定机头的产量或挤出量。
如前所述,产量一般用公斤/小时或公斤/转来表示。
一根好的螺杆,应当具有较高的塑化能力。
(生产能力)应当指出,低温挤出是目前的一个发展趋势,它能改善挤出制品的质量(如降低内应力等),防止热敏性物料过热分解,降低能量消耗,减少主辅机冷却系统的负担,提高生产率。
ﻫ(二)塑化质量一根螺杆首先必须能生产出合乎质量要求的制品。
所谓合乎质量要求是指所生产的制品应当合乎以下几个方面的要求:ﻫ 1.具有合乎要求的各种性能。
具有合乎规定的物理、化学、力学、电学性能;2、具有合乎要求的表观质量。
如能达到用户对气泡、晶点、染色分散均匀性的要求等。
3、具有合乎要求的螺杆的塑化质量:(1)螺杆所挤出的熔体温度是否均匀,轴向波动、径向温差多大。
(2)是否有得以成型的最低的熔体温度。
(3)挤出的熔体是否有压力波动。
染色和其它填加剂的分散是否均匀等。
(三)单耗单耗,是指每挤出一公斤塑料(橡胶)所消耗的能量,一般用N来表示。
其中N为功率(千瓦),Q为产量(公斤/小时)。
这个数值越大,表示塑化同样重量的塑料(橡胶)所需要的能量越多,即意味着所耗费的加热功率越多,电机所做的机械功通过剪切和摩擦热的形式进入物料越多。
反之亦然。
一根好的螺杆,在保证塑化质量的前提下,单耗应尽可能低。
(四)适应性所谓螺杆的适应性是指螺杆对加工不同塑料、匹配不同机头和不同制品的适应能力。
螺杆尺寸标准

螺杆尺寸标准螺杆是一种常用的机械传动元件,其尺寸标准对于机械设备的设计和制造具有重要意义。
螺杆尺寸标准的制定是为了保证螺杆在不同设备中的通用性和互换性,同时也是为了保证螺杆的性能和可靠性。
本文将介绍螺杆尺寸标准的相关内容,包括螺杆的基本尺寸、公称直径、螺距、螺杆的精度等方面的内容。
螺杆的基本尺寸包括公称直径、螺距、导程、螺杆长度等。
公称直径是指螺杆的直径,通常用字母D表示,单位是毫米。
螺距是指螺纹上相邻两螺纹峰的距离,通常用字母P表示,单位也是毫米。
导程是指螺杆上相邻两螺纹峰之间的距离,它等于螺距乘以螺纹的数量,通常用字母H表示,单位是毫米。
螺杆长度是指螺杆的有效长度,通常用字母L表示,单位是毫米。
螺杆的公称直径和螺距是螺杆尺寸标准中最基本的参数,也是最常用的参数。
公称直径和螺距的组合可以唯一地确定一个螺纹。
在实际应用中,一般会根据需要选择合适的公称直径和螺距的组合。
螺杆的精度对于机械设备的性能和可靠性有着重要的影响,因此螺杆的精度也是螺杆尺寸标准中的重要内容之一。
螺杆的精度包括两个方面,一个是螺纹的精度,另一个是螺杆的直线度和旋转度。
螺纹的精度包括螺纹的公差等级和螺纹的质量等级。
螺纹的公差等级是指螺纹的尺寸公差的等级,通常用数字表示,数字越小表示公差越小,精度越高。
螺纹的质量等级是指螺纹的表面质量的等级,通常用字母表示,字母越高表示质量越好,精度越高。
螺杆的直线度和旋转度是指螺杆轴线的直线度和旋转度,它们对于螺杆的安装和运行有着重要的影响。
总之,螺杆尺寸标准是保证螺杆在不同设备中的通用性和互换性,同时也是保证螺杆的性能和可靠性的重要依据。
螺杆的基本尺寸、公称直径、螺距、螺杆的精度等方面的内容都是螺杆尺寸标准中的重要内容,对于机械设备的设计和制造具有重要意义。
希望本文能对螺杆尺寸标准有所帮助,谢谢阅读!。
螺杆的功能及选型
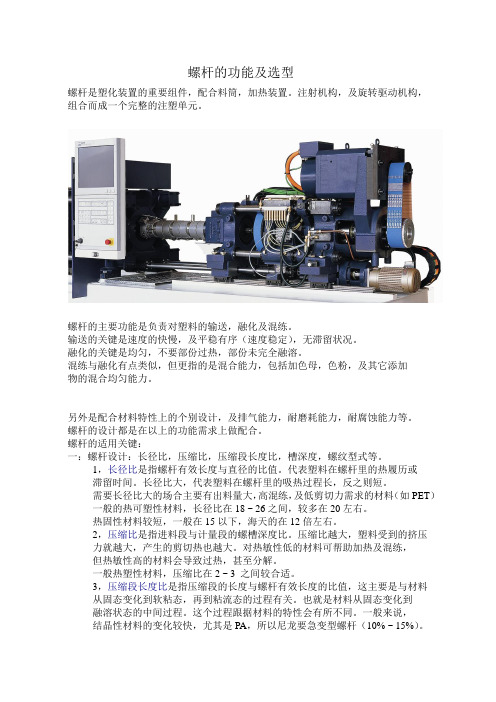
螺杆的功能及选型螺杆是塑化装置的重要组件,配合料筒,加热装置。
注射机构,及旋转驱动机构,组合而成一个完整的注塑单元。
螺杆的主要功能是负责对塑料的输送,融化及混练。
输送的关键是速度的快慢,及平稳有序(速度稳定),无滞留状况。
融化的关键是均匀,不要部份过热,部份未完全融溶。
混练与融化有点类似,但更指的是混合能力,包括加色母,色粉,及其它添加物的混合均匀能力。
另外是配合材料特性上的个别设计,及排气能力,耐磨耗能力,耐腐蚀能力等。
螺杆的设计都是在以上的功能需求上做配合。
螺杆的适用关键:一:螺杆设计:长径比,压缩比,压缩段长度比,槽深度,螺纹型式等。
1,长径比是指螺杆有效长度与直径的比值。
代表塑料在螺杆里的热履历或滞留时间。
长径比大,代表塑料在螺杆里的吸热过程长,反之则短。
需要长径比大的场合主要有出料量大,高混练,及低剪切力需求的材料(如PET)一般的热可塑性材料,长径比在18 ~ 26之间,较多在20左右。
热固性材料较短,一般在15以下,海天的在12倍左右。
2,压缩比是指进料段与计量段的螺槽深度比。
压缩比越大,塑料受到的挤压力就越大,产生的剪切热也越大。
对热敏性低的材料可帮助加热及混练,但热敏性高的材料会导致过热,甚至分解。
一般热塑性材料,压缩比在2 ~ 3 之间较合适。
3,压缩段长度比是指压缩段的长度与螺杆有效长度的比值,这主要是与材料从固态变化到软粘态,再到粘流态的过程有关。
也就是材料从固态变化到融溶状态的中间过程。
这个过程跟据材料的特性会有所不同。
一般来说,结晶性材料的变化较快,尤其是PA,所以尼龙要急变型螺杆(10% ~ 15%)。
而非结晶性材料的变化较慢,例如PMMA,所以PMMA的压缩段要较长(可达50%)。
而一般的通用型螺杆约20% ~ 30%。
压缩段太短会使材料来不及转化,而形成堵塞,产生高压,导致过热烧焦。
太长会形成空洞,混入气体,导致射胶不稳,有气纹等。
4,槽深是指螺顶到螺底的高度。
- 1、下载文档前请自行甄别文档内容的完整性,平台不提供额外的编辑、内容补充、找答案等附加服务。
- 2、"仅部分预览"的文档,不可在线预览部分如存在完整性等问题,可反馈申请退款(可完整预览的文档不适用该条件!)。
- 3、如文档侵犯您的权益,请联系客服反馈,我们会尽快为您处理(人工客服工作时间:9:00-18:30)。
目录序言一零件图的工析 (1)1.1 零件的用途 (1)1.2 零件的工艺分析 (1)1.3 审核主动轴的工艺性 (2)二确定生产类型2.1 计算生产纲领 (3)2.2 确定生产类型 (3)三确定毛坯种类和制造法 (3)3.1 确定毛坯种类 (3)3.2 毛胚的制造方法 (3)3.3确定毛胚尺寸公差和加工余量 (4)四拟定工艺路线 (4)4.1 定位基准的确定 (4)4.2 表面加工方法的确定 (5)4.3 工序的集中与分散 (7)五工序顺序的安排 (7)六确定加工工艺线 (7)七确定各工序加工余量、计算工序尺寸及余量 (9)八选择设备、及工艺装备(刀具、量具) (9)九确定各工序切削用量及时间定额 (9)1 切削用量 (10)2 基本时间 (11)序言机械制造工艺学课程设计使我们在学完大学的全部基础课,技术基础课以及大部分专业课之后进行的。
这是我们在进行课程设计之前对所学各课程的一次深入的综合性的总复习,也是一次理论联系实际的训练。
因此,它在我们四年的大学生活中占有重要的地位。
就我个人而言,我希望能通过这次课程设计对自己未来从事的工作进行一次适应性的训练,希望在设计中能锻炼自己分析问题、解决问题的能力,为自己今后参加祖国的建设打下一个良好基础。
由于能力有限,设计尚有许多不足之处,希望各位老师给予指教。
一零件图分析1.1 零件的用途作用:题目所给的零件是螺杆,螺杆通过锥销孔连接齿轮,起到支撑传递动力等系列作用,在工作中,由于受到弯应力和冲击载荷,因此该零件应具有足够的刚度、强度及韧性,以适应其工作环境的变化技术要求:属于普通零件普通精度。
1.2. 零件的工艺分析零件的工艺分析就是通过对零件图纸的分析研究,判断该零件的结构和技术要求是否合理,是否符合工艺性要求。
(1) 审查零件图纸通过对该零件图的重新绘制,知原图样的视图正确完整,尺寸、公差及技术要求齐全。
(2) 零件的结构工艺性分析该零件比较简单,材料为45#钢,没有较复杂的结构和较高的加工要求,主要的加工有各个外圆表面、端面的车削,磨削等,各个待加工表面的加工精度和表面粗糙度都不难获得。
各主要加工面、精度、偏差如下表1-1:表1-1螺杆零件技术要求表1.3. 审核螺杆的工艺性该零件除主要工作表面加工精度均较低,不需要高精度机床加工。
通过车削的粗加工半精加工等就可以达到加工要求;而主要工作表面虽然加工精度相对不高,可以在正常的生产条件下,由此可见.该零件的工艺性较好.二确定生产类型2.1. 计算生产纲领螺杆年产量为500台,设备品率为3%,机械加工废品率为1%,现制定该螺杆零件的机械加工工艺规程。
N=Q n×m(1+a%)(1+b%)=500×1×(1+3%)(1+1%)=520件/年2.2. 确定生产类型螺杆零件的年产量为520件,现已知该产品属于轻型机械,根据《机械制造工艺设计简明手册》中表1.1—2生产类型与生产纲领的关系,可确定其生产类型为中批量生产。
三确定毛坯种类和制造方法3.1. 确定毛坯种类零件材料45#钢,因为此零件的最大直径尺寸为Φ26mm,与其它直径相差不多,可采用棒料为毛坯。
3.2.毛胚的制造方法由于本零件属于中批生产而且零件的轮廓尺寸不大,查《机械制造工艺设计简明手册》表1.3—1常用毛胚的制造方法与工艺特点,选择模锻制造方法。
从提高生产率,保证加工精度来考虑也是应该的。
3.3. 确定毛坯的尺寸公差和加工余量1)公差等级由动轴的功用和技术要求可以确定该零件的公差等级为普通等级。
2)尺寸及公差该零件的最大直径尺寸为Φ26mm,查《机械制造工艺设计简明手册》表 2.2—36和 2.2—28得毛坯直径尺寸为Φ30mm,公差为±0.30mm,又因两端面只需粗车即可,查《机械制造技术基础课程设计指导教程》表2—16出车外圆余量得余量为5mm,所以长度可定为207mm,毛坯图如下图1-1:图1-1毛坯图四制定工艺路线4.1 定位基准的确定定位基准有粗基准和精基准之分.通常先确定精基准然后再确定粗基准1)精基准的选择:应满足基准重合,基准统一,自为基准,互为基准等原则。
所选的精基准应能保证定位准确,夹紧可靠,夹具简单,操作方便等.本零件是轴类的零件,轴是其设计基准,为避免由于基准不重合而产上的误差,应选轴中心线为定位基准。
在加工中,选择Φ26外圆为夹紧定位基准。
2)粗基准的选择为了保证加工表面与不加工表面之间的位置精度.则应以不加工表面作为定位基准.若工件上有多个不加下表面,应选其中与加工表面位置精度要求高的表面为粗基准。
为保证工件某重要表面的余量均匀,应选重要表面为粗基准。
应尽可能选择光滑平整,无飞边,浇口,或其他缺陷的表面为粗基准,以便定位准确,夹紧可靠。
粗基准一般只在头道工序下使用一次,应该尽量避免重复使用。
在该主动轴的加工中,首先选用左端面为粗基准,对右端面进行粗加工。
保总长206mm留出后面半精加工余量。
4.2 表面加工方法的确定本零件的毛还为棒料待加工面有端面、退刀槽、铣平面、锥销孔等。
材料为45号钢。
公差等级及粗糙度要求参考零件图。
其加工方法的选择如下:1)右端面Φ16圆柱面为未注公差尺寸,根据GB1800-79规定其公差等级按IT14,表面粗糙度为Ra6.3,查《机械制造工艺设计简明手册》表1.4—6得知需进行粗车。
2)右端铣平面为未注公差尺寸,根据GB1800-79规定其公差等级按IT14,表面粗糙度为Ra6.3,查《机械制造工艺设计简明手册》表1.4—6得知需进行粗铣。
3)右端Φ26圆柱面为未注公差尺寸,根据GB1800-79规定其公差等级按IT14,表面粗糙度为Ra6.3,查《机械制造工艺设计简明手册》表1.4—6得知需进行粗车。
4)右端Φ18-0.016圆柱面公差等级为IT8,表面粗糙度-0.034Ra3.2,查《机械制造工艺设计简明手册》表 1.4—6得知需进行粗车—半精车。
5)退刀槽为未注公差尺寸,根据GB1800-79规定其公差等级按IT14,表面粗糙度为Ra6.3,查《机械制造工艺设计简明手册》表1.4—6得知需进行粗车。
6)螺纹表面Φ180-0.033公差等级IT8,表面粗糙度Ra3.2,查《机械制造工艺设计简明手册》表1.4—6得知可用车刀粗车—半精车。
差等级IT8,表面粗糙度7)左端圆柱面Φ12-0.016-0.034公Ra3.2,查《机械制造工艺设计简明手册》表 1.4—6得知可用车刀粗车—半精车。
8)锥销孔Φ4 为未注公差尺寸,根据GB1800-79规定其公差等级按IT14,表面粗糙度为Ra6.3,查《机械制造工艺设计简明手册》表1.4—6得知采用复合钻头钻孔。
4.3 工序的集中与分散选用工序集中原则安排连接轴的加工工序,该主动轴的生产类型为中批生产,可以采用万能型机床配以专用工具、夹具,以提高生产率;而且运用工序集中原则使工件的装夹次数少,不但可以缩短辅助时间,而且由于与一次装夹中加工了许多表面,有利于保证各种加工表面之间的相对位置精度要求。
五工序顺序的安排(1)遵循“先基准后其它”原则,首先加工基准——首先加工螺杆的右端面,保其总长,后车外圆、铣平面。
(2)遵循“先粗后精”原则,先安排粗加工工序,后安排精加工工序。
(3)遵循“先主后次”原则,先加工主要表面——各外圆表面,再加工螺纹表面和钻孔.六确定加工工艺路线在综合考虑上述工序顺序安排的基础上,下表列出了该主动轴的工艺路线,如下表1-2:表1-2主动轴工艺路线及设备的选用七确定各工序加工余量、计算工序尺寸及余量各工序加工余量、计算工序尺寸及余量如下表:表1-3主动轴工序加工余量及工序尺寸八选择设备、及工艺装备(刀具、量具)1.机床设备:车床CA6140 铣床X51 钻床在Z040 切割机。
2.刀具:车刀、铣刀、钻头和切断刀具。
3.量具:结合此轴的结构特点选出所需两种量具:游标卡尺、千分尺。
九确定各工序切削用量及时间定额切削用量一般包括背吃刀量、进给量及切削速度三项。
确定方法是先确定背吃刀量、进给量,在确定切削速度。
9.1 切削用量工序Ⅰ)铣两端面:机床为专用机床,还要有专用夹具(1)背吃刀量:查表得背吃刀量为1mm;(2)进给量:查表得f=50mm/min;(3)计算速度v=πdn /1000=3.14*30*725/1000=68.30mm/min。
工序Ⅱ)粗车:车床为CA6140(1) 背吃刀量:查表得背吃刀量为7mm;(2)进给量:查表得f=0.75mm/s;(3)计算速度v=πdn/1000=3.14*30*900/1000=84.78mm/min。
工序Ⅲ)车螺纹:卧式车床CM6125专用夹具(1)进给量确定由《机械制造技术基础课程设计指导教程》查表的f=0.04mm/r(2)车削速度的计算v=nf=0.04×1000=40mm/min工序Ⅳ)半精车车床为CA6140(1)背吃刀量确定:由《机械制造技术基础课程设计指导教程》得背吃刀量为1mm(2)进给量:查表得f=0.75mm/s(3)计算速度:v=πdn/1000=3.14×26×900/1000=73.48mm/min9.2基本时间(1)铣两端面T j=(L+L1+L2)∕fmz式中L=30mm,L1=0.5(d-√d2-a2e)+(1~3)K r=90°,L1=2mm,L2=0T i=(30+2+0)∕68.30=0.47min(2)粗车外圆T i=(L∕fn)i=(L+L1+L2+L3)i∕fn式中L1=a p∕tgk r+(2~3)K r=90°,L1=2mm,L2=0,L3=0,f=0.75mm∕r,n=1.5r ∕s,i=1T j=(26+2)∕(0.75×1.5)=255(3)车螺纹由T j=(L+L1+L2)i∕fmz式中L=4mm,L1=(1~2)p,L2=2~5则T j=(4+5+6)∕40=0.375min(4)半精车外圆表面由T j=Li∕fn=(L+L1+L2+L3)∕fn式中L=37mm,L1=a p∕tgk r+(2~3)L2=3~5,L3=0则T j=(37+3+4)∕23.48=0.59min我以为爱是窒息疯狂,爱是炙热的火炭。
婚姻生活牵手走过酸甜苦辣温馨与艰难,我开始懂得爱是经得起平淡。